摘 要:利用MoS2真空高温分解高效制备钼粉的工艺特性,提出了真空分解炉的基本结构和工作原理,并采用热平衡法对炉体7个部位的热量损失情况进行了详细计算,为炉体功率的选择提供了理论依据。同时通过对57%的钼精矿进行分解试验,得到了预期的钼粉产品和硫磺产品。
关键词:二硫化钼;真空分解炉;热平衡法;钼粉产品
0 引 言
目前,在工业上以钼精矿为原料生产金属钼粉的传统工艺比较成熟。首先,将钼精矿在焙烧炉中氧化焙烧生成工业三氧化钼。其次,将工业三氧化钼经过硝酸预处理、氨浸、净化、酸沉后制得钼酸铵。第三,将钼酸铵焙解生成纯三氧化钼。最后,将纯三氧化钼在氢气气氛中经两段还原,得到金属钼粉。
从钼精矿到金属钼粉生产的传统工艺采用的是将火法冶金和湿法冶金相结合的联合工艺,其优点是工艺比较成熟,气固两相接触表面分离迅速,容易掌握,设备容易解决,但是,整个钼粉生产的工艺流程长,需要的生产设备多,生产过程中产生大量的废气、废水和废渣,不仅对人们的健康造成威胁,还对环境造成严重污染。而高效制备钼粉是以钼精矿为原料,在真空高温加热的状态下,使钼精矿分解成钼粉产品和粗硫磺,其制备工艺如式(1)所示。该工艺简单可行,减少了钼粉制备过程中的焙烧、酸洗、氨浸、焙解及还原等环节,降低了设备和人力成本,提高了产品生产过程中的可靠性,同时符合环保要求,消除了“三废”引发的环境污染,但是该工艺对设备提出了更高的要求。

(1)
1 分解炉工作原理
用于高效制备钼粉过程中钼精矿的分解系统主要由滑阀真空泵、罗茨真空泵、二级过滤器、一级过滤器、热交换器、电加热器、硫磺收集罐、炉体、炉顶盖、炉底盖、石墨坩埚、丝杠升降机构、限位导轨、变频电源、补偿电容器组、自动控制部分及人机交互平台等组成。其工作原理如图1所示,首先,将钼精矿颗粒平铺在石墨坩埚11中,并使其水平放置在炉体底盖9的正中央,启动滚珠丝杠机构8,使得石墨坩埚11随炉体底盖9做垂直向上运动,直至炉体底盖9和炉体10底部完全封盖,此时钼精矿颗粒完全处于炉体加热区中央,打开真空主阀14,依次启动罗茨真空泵5和滑阀真空泵2,当炉体10内腔体真空度小于10 Pa时,打开炉体的中频加热系统,石墨坩埚和钼精矿颗粒在中频感应的磁力线交换切割下发热变红,达到二硫化钼高温分解温度,生成钼粉颗粒和单质硫磺,钼粉颗粒由于熔点高、比重大,依然平铺在石墨坩埚11内部,而硫磺在445 ℃时就已经以硫蒸气的形式存在,在真空分解温度下,生成的硫磺迅速以气态形式在抽真空装置的辅助下沿管道进入热交换器15中,此时热交换器15的夹层壁内通的是冷却介质,硫磺蒸气遇冷凝结在热交换器的内壁上,当钼精矿完全分解完成后,关闭中频感应加热装置,炉体10开始降温,温度为400 ℃以下时,关闭抽真空系统,降温至室温时,启动滚珠丝杆机构8,使得石墨坩埚11随炉体底盖9一起降至卸料高度,取出钼粉颗粒产品,完成钼粉的制备收集;当关闭真空系统后,同时关闭真空主阀14,启动电加热器13,给冷却介质加热,之前的冷却介质转换成加热介质,此时加热介质流过热交换器15的夹层,附着在热交换器内壁的单质硫磺经热传导加热后熔融成液体硫,液体硫磺在重力作用下沿热交换器15内壁上流入硫磺收集罐6内,硫磺收集结束后,硫磺收集罐6沿限位导轨7运输至操作台,打开收集罐底部盖,取出固体硫磺,完成硫磺的制备收集。
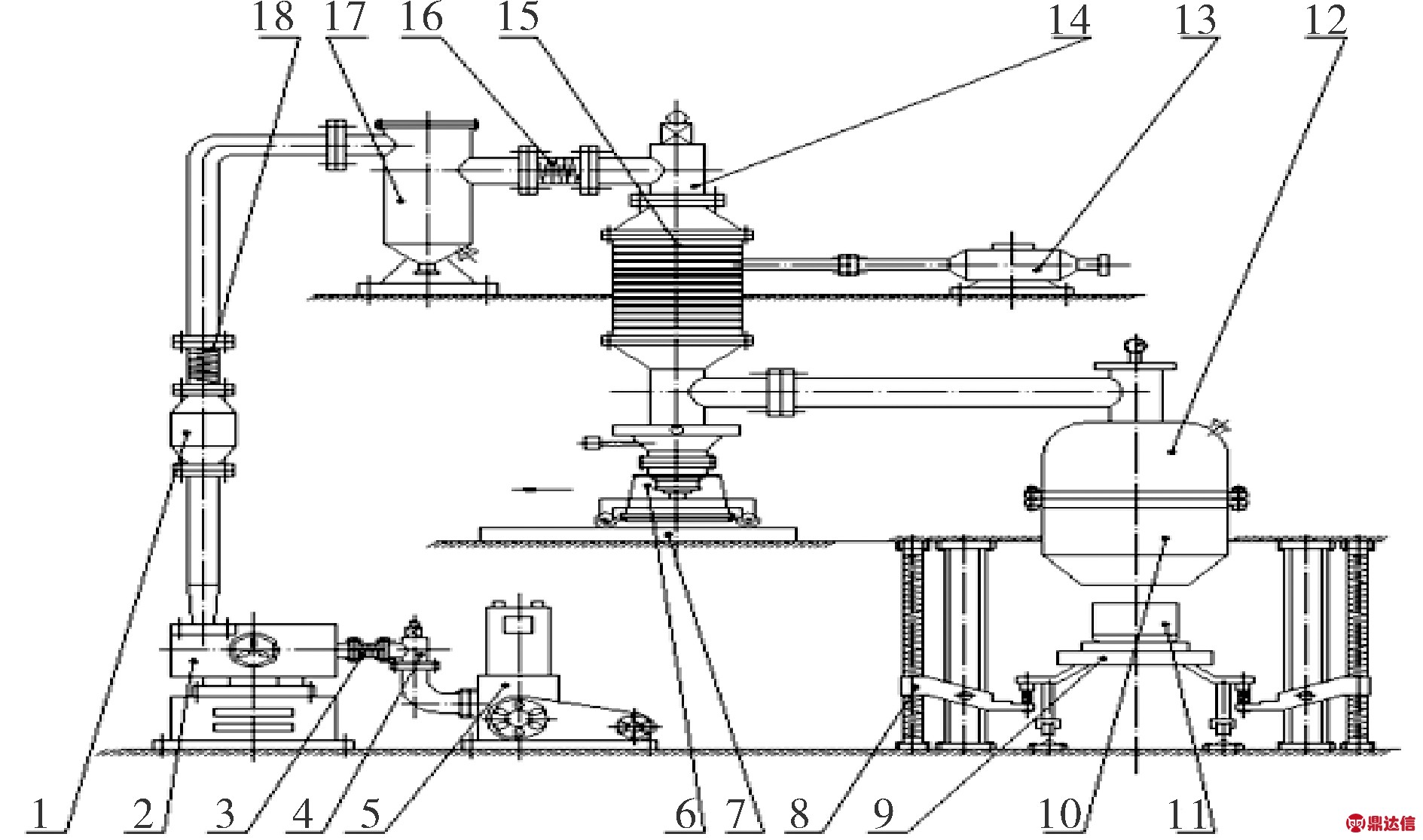
图1 分解炉工作原理
1—二级过滤器;2—滑阀真空泵;3—波纹管1#;4—机组真空阀;5—罗茨真空泵;6— 硫磺收集罐;7—限位导轨;8—滚珠丝杠机构;9—炉底盖;10—炉体;11—石墨坩埚;12—炉顶盖;13—电加热器;14—真空主阀;15—热交换器;16—波纹管2#;17—一级过滤器;18—波纹管3#
2 热工计算
热平衡计算法就是分别计算炉子达到所需设计温度时各项热量的收支情况,并求其热量支出总和,从而计算应供给炉子的总功率[2-3]。根据钼精矿分解工艺要求,所设计分解炉体最高工作温度为1 800 ℃。
(1)MoS2由室温加热至工作温度1 800 ℃所需热量
Q1=G1[(C1t2-C6t1)+ΔH]×0.277 8
式中:G1—分解炉的小时生产能力,5 kg/h;
C1—物料在1 800 ℃下的比热容,0.44 kJ/(kg·℃);
C6—物料在25 ℃下的比热容,1.08 kJ/(kg·℃);
ΔH—MoS2的分解热,1 067 kJ/kg;
t2—最高烧结温度,1 800 ℃;
t1—室温,25 ℃;
则:
Q1=5×[(0.44×1 800-1.16×25)+1 067]×0.277 8=2 540 W
(2)石墨坩埚由室温加热到1 800 ℃所需热量
Q2=G2C2(t2-t1)×0.277 8
式中:G2—石墨坩埚每小时通过t1到t2这一温区的质量,30 kg/h
C2—石墨坩埚的比热容,1.155 kJ/(kg·℃);
t2—最高烧结温度,1 800 ℃;
t1—室温,25 ℃。
则:
Q2=30×0.71×(1 800-25)×0.277 8=10 503 W
(3)氧化铝块由室温加热至工作温度1 800 ℃所需热量
Q3=G3C3(t2-t1)×0.277 8
式中:G3—氧化铝块每小时通过t1到t2这一温区的质量,25 kg/h;
C3—氧化铝的比热容,1.09 kJ/(kg·℃);
t2—最高烧结温度,1 800 ℃;
t1—室温,25 ℃。
则:
Q3=25×1.09×(1 800-25)×0.277 8=13 437 W
(4)抽真空系统和炉体顶部圆形孔的热辐射损失
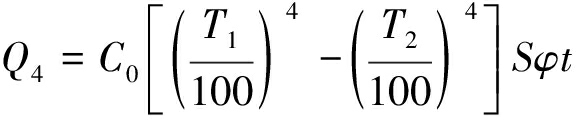
式中:C0—黑体的辐射系数,5.67 W/(m2·K4)
T1—炉体顶部圆形孔内的绝对温度,1 773 K;
T2—炉体顶部圆形孔外部边缘的绝对温度,873 K;
S—开孔面积,0.03 m2;
φ—遮蔽系数[4],0.5;
t—炉门或墙孔开启时间比,1。

(5)冷却水带走的热量
Q5=G5C5(t2-t1)×0.277 8
式中:G5—每小时通过的冷却水量,2 500 kg/h;
C5—水的比热,4.183 kJ/(kg·℃);
t2—流出水的温度,35 ℃;
t1—流入水的温度,25 ℃。
Q5=2 500×4.183×(35-25)×0.277 8=29 051 W
(6)炉壁热损失
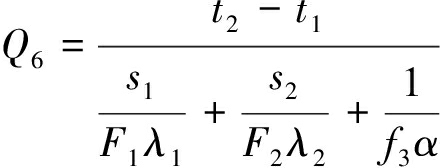
式中:t1—炉体周围空气温度,25 ℃;
t2—炉墙内表面温度,即炉温,1 800 ℃;
λ1—刚玉块的热导率,0.035+0.234×10-6t2W/(m·℃);
λ2—岩棉板的热导率,0.04 W/(m·℃);
s1、s2—分别为刚玉块和岩棉板厚度,0.12 m,0.04 m;
F1、F2—炉墙、炉顶及炉底砌筑材料的几何平均面积,m2;
α—炉墙、炉顶及炉底的传热系数,14.0 W/(m2·℃),16.1 W/(m2·℃),10.8W/(m2·℃)。
其中,分别计算炉墙、炉顶和炉底的几何平均面积,在数值上等于砌筑材料的内面积与散热面积相乘的算术平均值。可得:炉墙热损失862 W,炉顶热损失543 W,炉底热损失684 W。
Q6=Q炉墙+Q炉顶+Q炉底=2 089 W
(7)其他热损失。一般取前6项的10%,则
Q7=10%×Q1~6=10%×88 772=8 877 W
表1 真空分解炉热支出情况
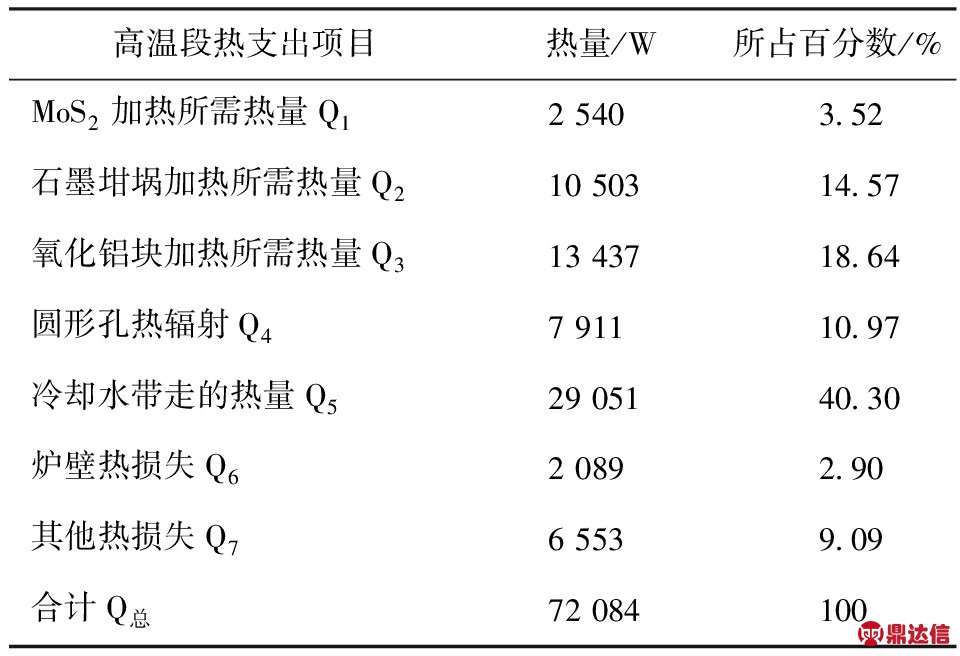
由表1可以看出,在中频感应分解炉加热过程中,热量损耗最大的部分是炉体冷却水带走的部分,其所需加热功率为29.051 kW,占整个炉体加热功率的40.30%,其主要是因为炉体加热过程中,由室温加热1 800 ℃工作温度,炉体温差变化较大,同时还要保证外壁附近空气温度维持在室温状态,这就需要炉体受热部分的冷却水循环速度高,从而增加了每小时冷却水的流量,相应循环水带走的热量就会加大。其次热量损耗较大的部分是氧化铝块加热所需的热量和石墨坩埚加热所需的热量,所需加热功率分别为13.437 kW和10.503 kW,分别占整个炉体加热功率的18.64%和14.75%,其热量情况主要由两部分组成,一部分是通过热传递将热量传导给物料,这部分的热量是有用热量,另一部分是维持自身能量所需的动态热量以及通过多级传递将多余热量由冷却水带走的热量,这部分热量是无用热量。这3个部分的热量损失占整个真空加热炉的73.51%。
3 工艺与产品
3.1 工 艺
高效制备钼粉工艺如图2所示,首先,准备品位为54%的钼精矿粉末30 kg,将有机胶和纯净水按1∶10的比例混合作为钼精矿粉末的粘结剂,把混合好的粘结剂加入到钼精矿粉末中,开始搅拌,待混合均匀后,再搅拌1 h,待钼精矿粘稠后,置于造粒机中造粒,将造好的钼精矿颗粒过筛,取粒径为2~3 mm的钼精矿颗粒,放置在烘箱中烘干,完成钼精矿颗粒的制备。将制备好的钼精矿颗粒置于石墨坩埚内,滚珠丝杠机构旋转,带动炉体底盖上升,将钼精矿颗粒带入到加热炉内,开启罗茨真空泵,打开机组真空阀,待真空度降至2 000 Pa时,打开罗茨真空泵,再打开真空主阀,待炉体真空度降至10 Pa以下时,启动中频电源,给加热炉加热,此时石墨坩埚里的钼精矿颗粒分解。在高温状态下,硫磺蒸气弥散进入热交换器,并与内壁接触遇冷凝结成固体硫磺,待反应结束后关闭中频电源,固体硫磺紧紧的附着在热交换器的内壁上,利用硫磺在150 ℃处于熔融态并且流动性最好的性质,设定好导热介质温度,直接进入热交换器夹套内,导热油将自身携带的热量传递给热交换器内壁上的硫磺,硫磺受热后软化、熔融,最后以液体的形式从热交换器里流出,硫磺直接流入硫磺收集罐内,掉在罐体底盖上,待硫磺收集结束,打开底盖就得到所需的硫磺。对捕集到的硫磺进行荧光全分析检测结果表明,采用钼精矿分解制取的硫磺含硫量可达98%,比市场上销售的高纯硫磺纯度低1.9%,可以将采用本方法制取的硫磺提纯后销售,也可用于制酸。
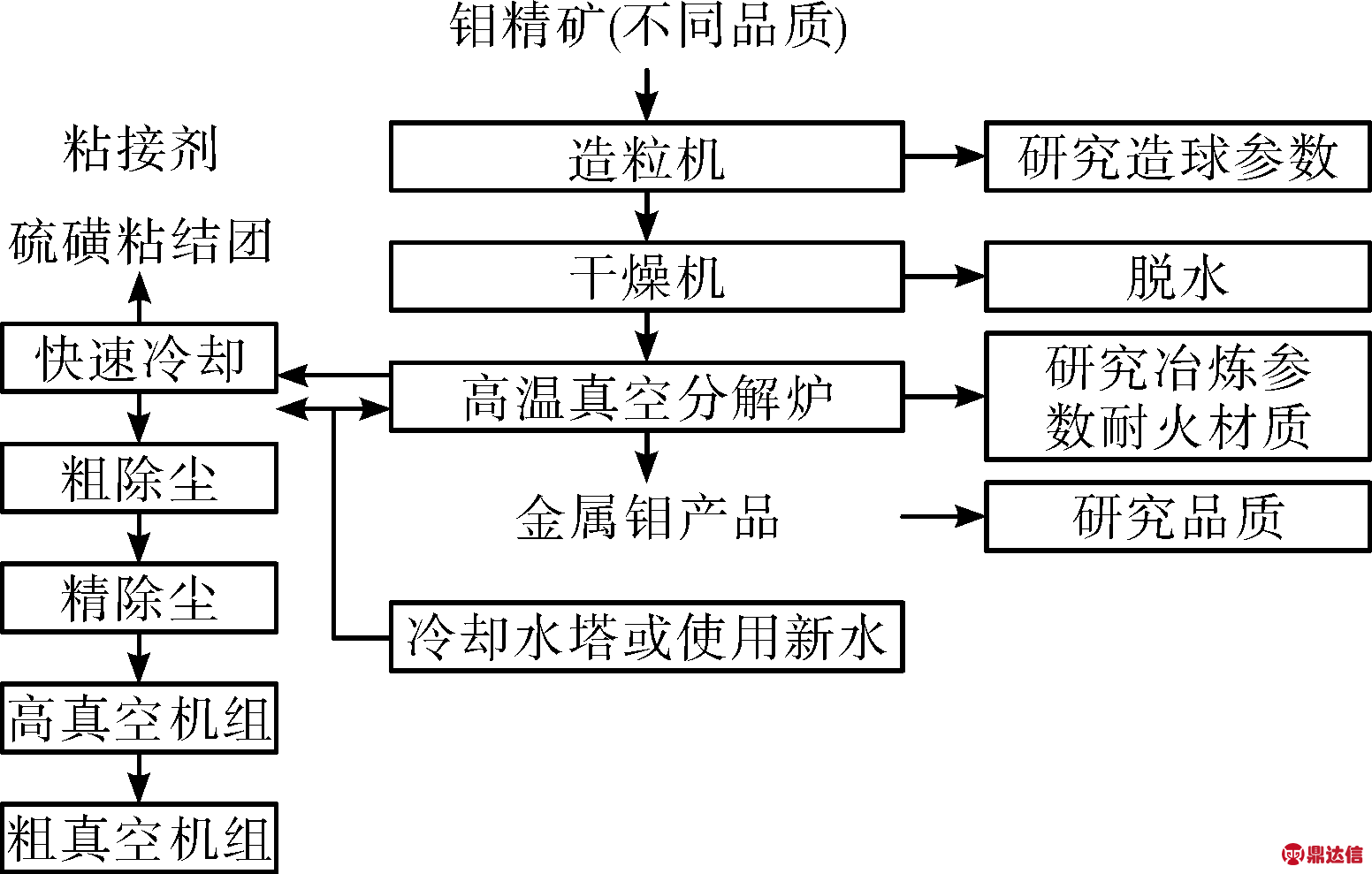
图2 高效制备钼粉工艺流程
3.2 产 品
以牌号为KMo-54的钼精矿为原料,按照高效制备钼粉工艺流程,得到了预期的钼粉产品和硫磺产品,并对其分别完成XRD和化学全分析表征,结果如图3、表2所示。钼粉的含钼量为97.82%,可满足钼粉升华提纯工艺要求,同时也可以进行含钼合金钢的冶炼,硫磺含硫量可达98%,比市场上销售的高纯硫磺纯度低1.9%,可以将采用本方法制取的硫磺经相应工艺提纯[5-6]后销售,也可用于制酸。
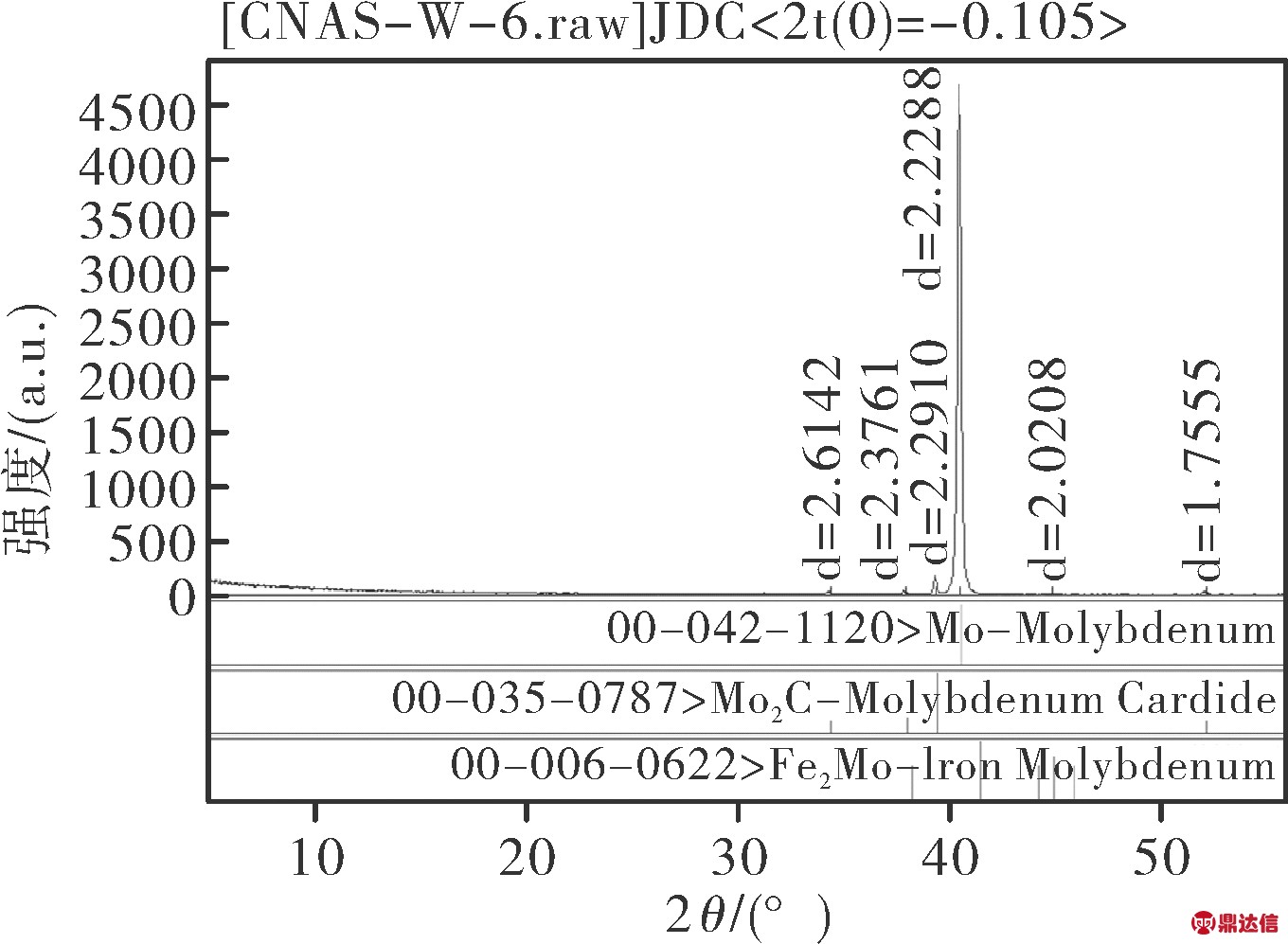
图3 钼粉产品的XRD
表2 钼粉和硫磺产品的化学成分 %(质量分数)
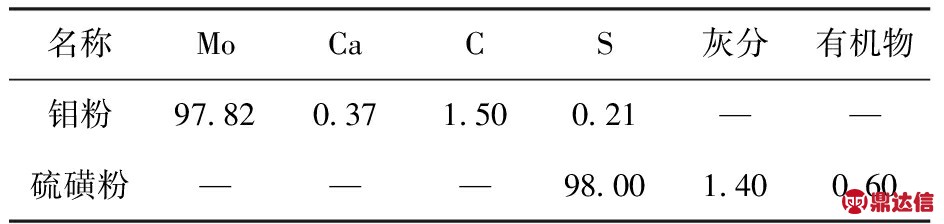
4 结 论
(1)利用MoS2在真空下高温分解成钼和硫的特性,开发出了钼精矿分解系统,该系统只需一步分解就可制备出钼粉产品,其流程短、效率高、可靠性好,极大的降低了“三废”排放污染,符合环保要求。
(2)采用热平衡法,对真空分解炉各个部分热量收支情况进行了详细计算,得出炉体热量损耗最大的部分是炉体冷却循环水带走的热量,达到近30 kW,占整个炉体加热功率的40.3%,为整个炉体设计过程中加热部分功率选择提供了理论依据。
(3)在该系统上,以品位54%的钼精矿为原料,按照制备工艺要求,分解得到了预期的钼粉产品和硫磺产品,其主要成分含量分别为97.82%和98%。