摘 要:本文首先利用AMESim软件针对某轻型载货汽车所采用的双膜片弹簧真空助力制动系统建立了仿真模型,包括制动踏板、真空助力器、制动主缸、制动管路及制动器,并以试验数据为参照验证了仿真模型的有效性。在此基础上,对制动系统进行了静态和动态仿真研究,分析了制动踏板位移与制动力、踏板位移与制动管路油压、踏板位移与制动减速度及踏板力与制动减速度之间的关系,为优化该车制动系统提升制动踏板感觉创造了条件。
关键词:制动系统;真空助力器;制动主缸;制动踏板感觉
汽车制动时,驾驶员可以感受到由制动踏板力、制动踏板位移及制动减速度共同组成的制动踏板感觉,如图1所示。制动踏板感觉是用来评价车辆制动性能、安全性能及舒适性能的重要指标之一,其好坏直接影响消费者对车辆品质的评价。因此,现在汽车制动系统的设计不仅要满足汽车制动安全性的基本要求,还应具有良好的制动踏板感觉。
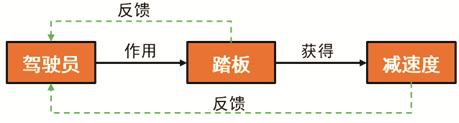
图1 制动踏板感觉关系图
关于制动踏板感觉的研究,早在1994年通用公司的EBERT等提出BFI的概念,首次将主观评价指标转换为客观评价指标 [1] 。泛亚汽车技术中心的石永金等提出用制动感觉指数来评价车辆制动踏板感觉,实现了制动踏板感觉的量化研究 [2] 。王天利等利用AMESim软件建立了带单膜片弹簧真空助力器的制动系统模型并重点研究了制动软管膨胀、制动衬块与制动盘间隙对制动踏板感觉的影响 [3] 。同济大学的孟建德等建立了包含关键结构件、气体和液体的真空助力器-制动主缸系统动力学模型,开展了面向制动踏板感觉的系统特性研究 [4] 。江苏大学的陈燎等提出了一种用于电液复合制动系统的踏板模拟机构,建立了仿真模型 [5] 。吉林大学的刘杨针对电液复合制动系统的制动踏板感觉开展了研究 [6,7]。 北京汽车研究总院的郑素云等提出了一种制动踏板感觉试验数据采集和分析的标准化方法用于不同试验结果的比较 [8] 。奇瑞汽车的张静初针对某自主品牌的产品开发,将制动踏板感觉家族化,提升了产品的可靠性和通用性 [9] 。武汉理工大学的裴晓飞等人应用AMESim软件建立了制动系统的静态/动态仿真模型,采用制动踏板感觉指数评价体系对某试验车的制动踏板进行了客观评价,并提出了优化方案[10]。
本文首先针对某轻型载货汽车制动系统建立了面向制动踏板感觉研究的模型并利用试验数据验证了模型的正确性。之后,针对制动系统开展了制动踏板感觉研究,分析了制动踏板位移与制动力、踏板位移与制动管路油压、踏板位移与制动减速度及踏板力与制动减速度之间的关系。
1 制动系统建模
1.1 制动踏板模型
制动踏板的作用是将施加到踏板上的作用力按照踏板杠杆比成倍放大并输入到后续机构中,并直接反馈踏板感觉。本文车型所采用的吊挂式制动踏板被简化为静力学杠杆模型,忽略了踏板的惯性量。
制动踏板相关参数如表1所示,其中L1为制动踏板输入点到制动踏板支点的距离,mm;L2为制动踏板输出点到制动踏板支点的距离,mm;L3为回位弹簧支点到制动踏板支点的距离,mm;Fs0为回位弹簧预紧力,N;Ks为回位弹簧刚度,N/mm。依据所给参数,在AMESim软件中构件制动踏板仿真模型,如图2所示。图中1为制动踏板输入信号;2为制动踏板臂;3为回位弹簧;4用于模拟制动踏板与真空助力器间隙。
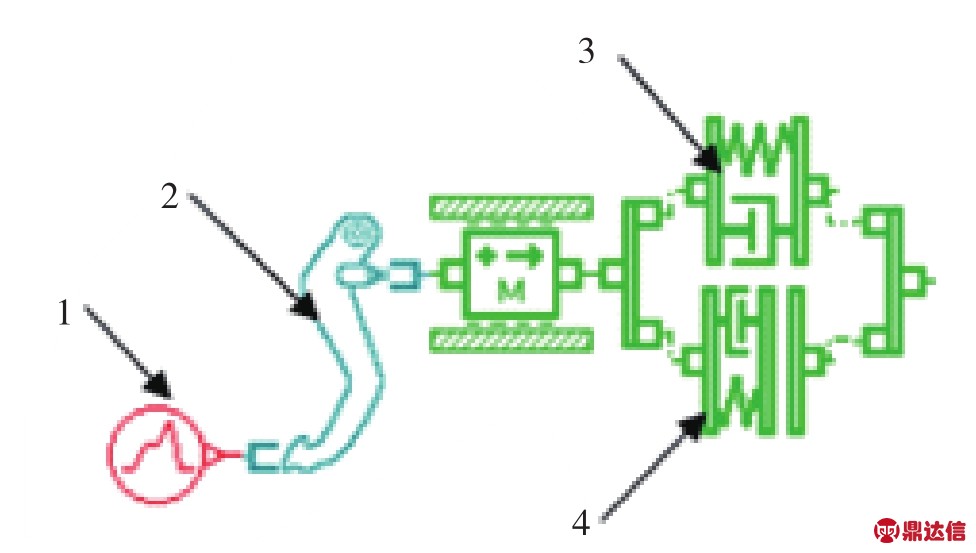
图2 制动踏板仿真模型
表1 制动踏板参数表
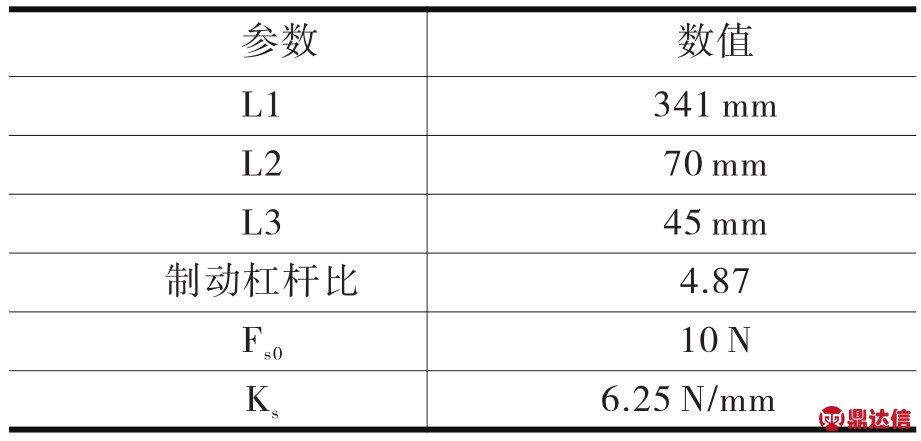
1.2 真空助力器模型
真空助力器主要是由真空助力器控制阀、橡胶反作用盘和膜片前后腔室组成,其性能对制动系统性能影响很大。
真空助力器控制阀门的初始状态是真空阀打开、大气阀关闭,此时膜片前后腔室连通,依据相关标准可知此时前后腔的真空度为66.7±1.3kPa。当输入力抵消真空弹簧和空气弹簧预紧力后,推杆开始向前移动。由于结构中存在间隙,大气阀不能在第一时间打开。随着输入力的不断增加,直到真空阀关闭、大气阀打开,膜片前后腔室开始产生压差,真空助力器才开始起作用。此后,随着输入力的不断增加,真空阀为常闭状态,大气阀不断由开启变为关闭,真空助力器输出力按助力比成倍增加,直到有效助力超过最大助力点后,真空助力器后腔室真空度为零时助力器不再起作用。在AMESim软件中构建的控制阀门仿真模型如图3所示。
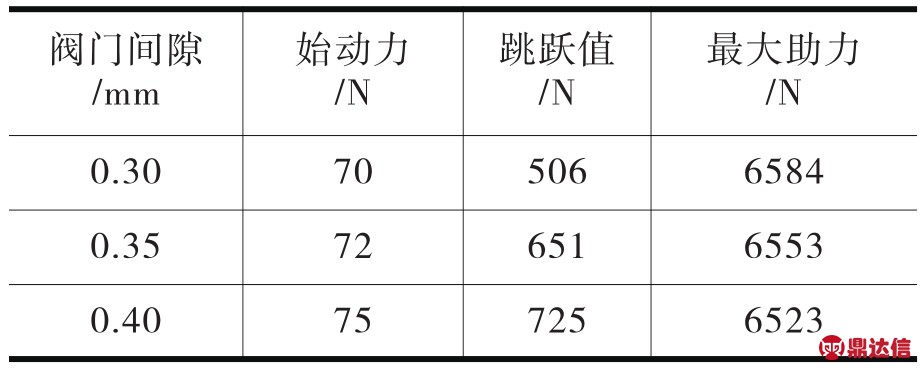
图3 控制阀仿真模型
橡胶反作用盘与相邻部件关系如图4所示。当大气阀们打开时,推杆柱塞与橡胶反作用盘之间的间隙刚好闭合,此时输入力由橡胶反作用盘主面传到副面。由于橡胶反作用盘为不可压缩的柔性材质,可像液体一样传递压力,故可将橡胶反作用盘等效成两个相连的液压缸。橡胶反作用盘的力学模型可见文献[10]。
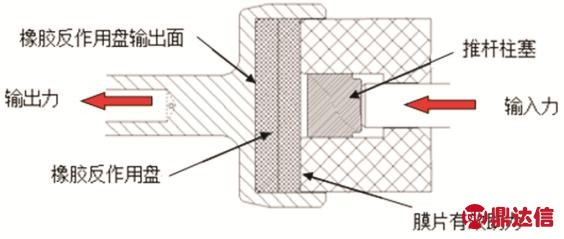
图4 橡胶反作用盘示意图
在AMESim软件中构建的橡胶反作用盘模型如图5所示。通过对两个液压腔元件设置活塞直径和推杆直径,并设置等效弹簧刚度和弹簧预紧力后可输出制动系统的始动力和跳跃值。两液压腔元件横截面积之比即为真空助力器的助力比。
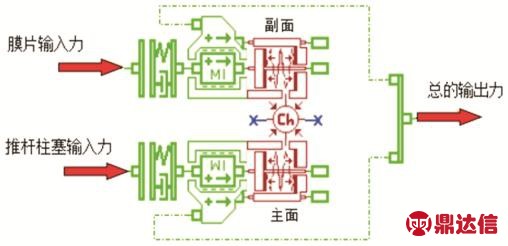
图5 橡胶反作用盘仿真模型
本文所研究的真空助力器为双膜片弹簧设置,故可将结构简化为四个双活塞气压缸,气压缸的活塞等效为两个中间膜片,气压缸的腔室等效为真空助力器的大气腔和真空腔,如图6所示。
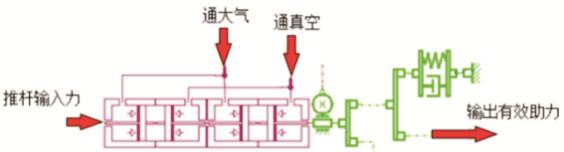
图6 真空助力器腔室仿真模型
真空助力器总成的仿真模型如图7所示,其中柱塞位移传感器和阀门位移传感器用于控制大气阀门的开启和关闭,阀门位移传感器和膜片位移传感器用于控制真空助力器的开启和关闭。真空助力器仿真模型中的关键参数设置如表2所示。
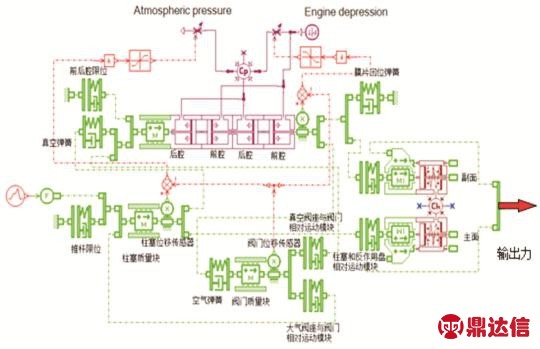
图7 真空助力总成仿真模型
表2 真空助力器仿真模型参数
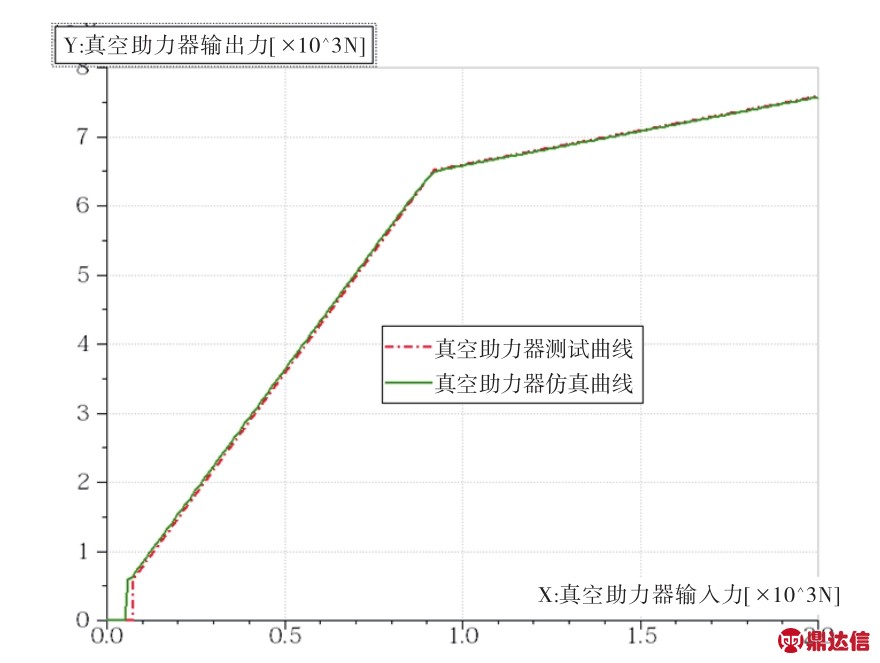
1.3 制动主缸模型
制动主缸几何尺寸对制动踏板感觉有着直接的影响,如主缸直径的大小对踏板行程、制动管路油压特性及制动踏板软硬等均有影响。制动主缸的力学模型可见文献 [10],仿真模型如图8所示。其中端口5为真空助力器输入的力载荷,端口1、2、3、4分别输出液压至四个制动轮缸。
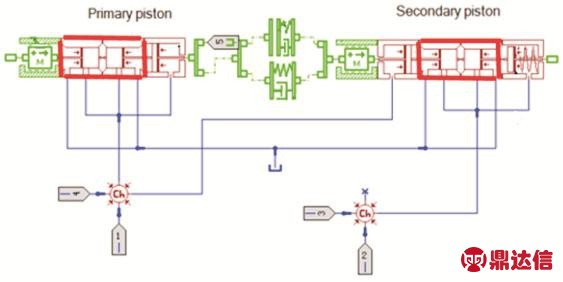
图8 制动主缸仿真模型
参照《汽车液压制动主缸技术条件》中对制动主缸性能的要求来设置制动主缸关参数,如表3所示。
表3 制动主缸参数表
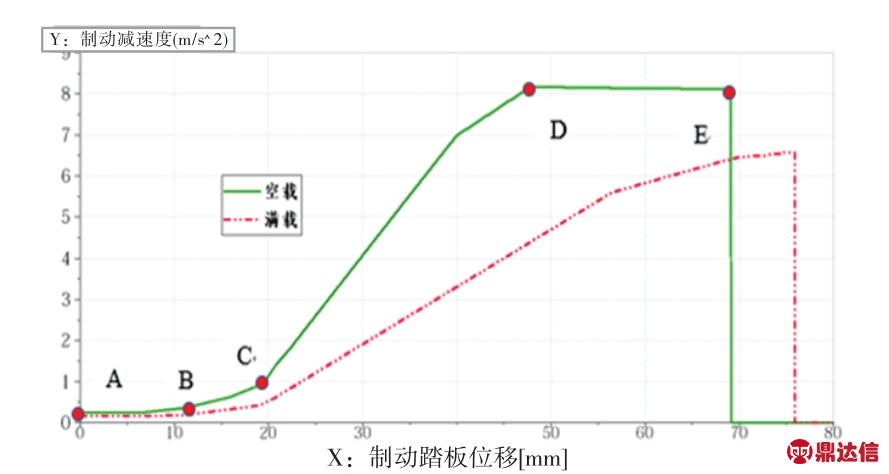
1.4 制动管路模型
汽车制动管路分为制动硬管和制动软管,制动硬管在制动压力变化后体积几乎没有变化,可忽略其对会制动踏板感觉的影响;而制动软管在制动压力变大后直径有较明显的膨胀,对制动踏板感觉有一定的影响。本文所建模型中仅考虑制动软管对制动踏板感觉的影响。
利用Unity3D开发引擎及高通AR插件制作出一个三维可视化的人体模型,并发布到Android系统的手机上进行运行测试。基于高通SDK的良好封装和Unity3D引擎强大的功能支持,最终生成可执行的APK文件。
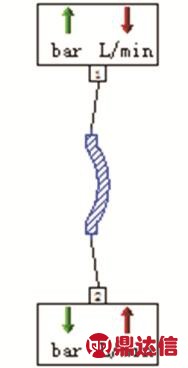
图9 制动软管仿真模型
表4 制动管路参数表
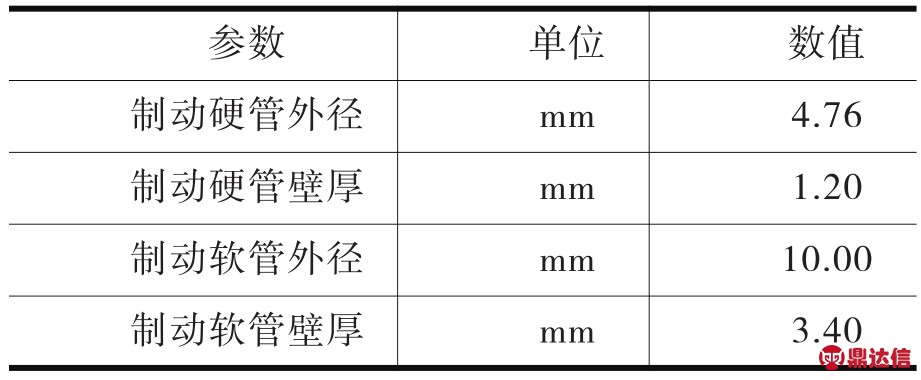
1.5 制动卡钳模型
本研究以浮动钳盘式卡钳为研究对象,制动过程中不考虑钳体的变形,忽略制动块与制动器支架之间的摩擦,同时不考虑钳体内压力损失。
制动卡钳的仿真模型如图10所示,其中端口2用于输入管路油压,端口1用于输出制动力矩。
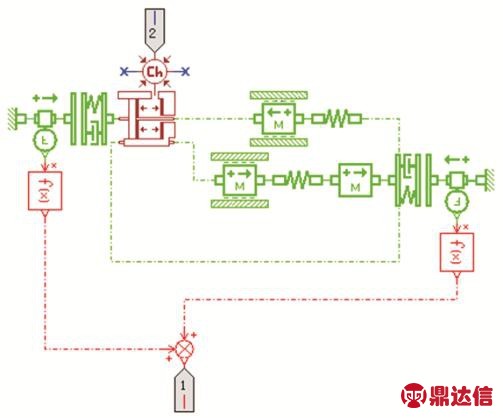
图10 制动卡钳仿真模型
根据《液压制动钳总成性能要求及台架试验方法》中对制动钳参数的要求,本文中所用制动卡钳参数设置如表5所示。
表5 制动卡钳参数设置表
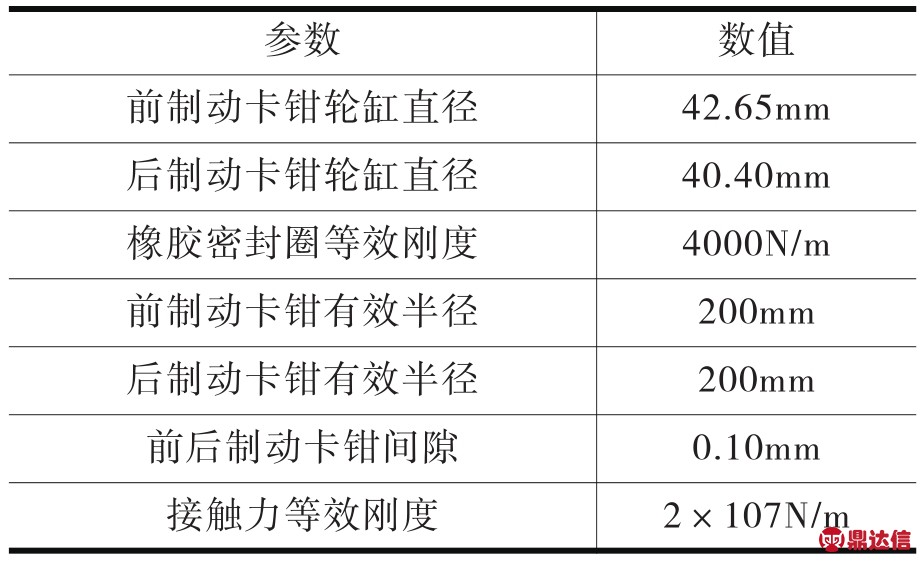
1.6 制动系统仿真模型
基于上述制动系统各组成元件仿真模型的构建,最终形成了制动系统的仿真模型,如图11所示。模型的左侧为双轴车辆仿真模型,右侧为制动系统静态仿真模型。
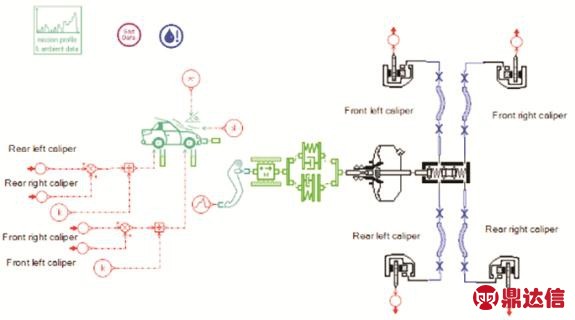
图11 制动系统仿真模型
2 制动系统仿真分析
2.1 真空助力器仿真模型的验证
在AMESim软件中,应用所建真空助力器仿真模型可得到真空助力器输出特性曲线,与台架试验结果对比结果如图12所示。
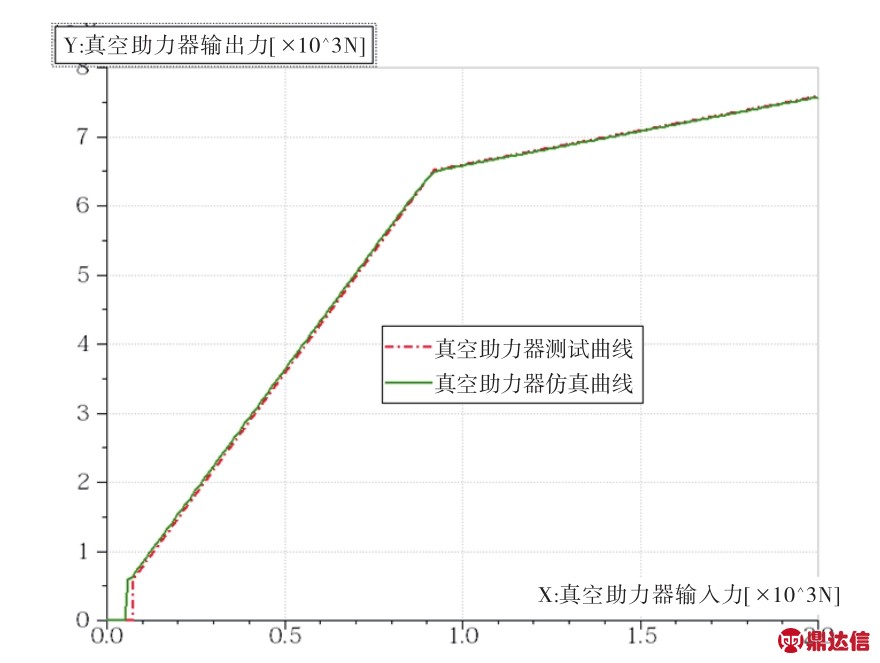
图12 助力器输出特性曲线对比图
由图中可见,仿真模型输出结果与试验结果吻合度很高。通过对各个关键点的相对误差进行计算(如表6所示),仿真结果与试验结果对比最大相对误差仅为6.67%,证明了所建双膜片弹簧真空助力器仿真模型的正确性。
表6 仿真与试验结果对比表
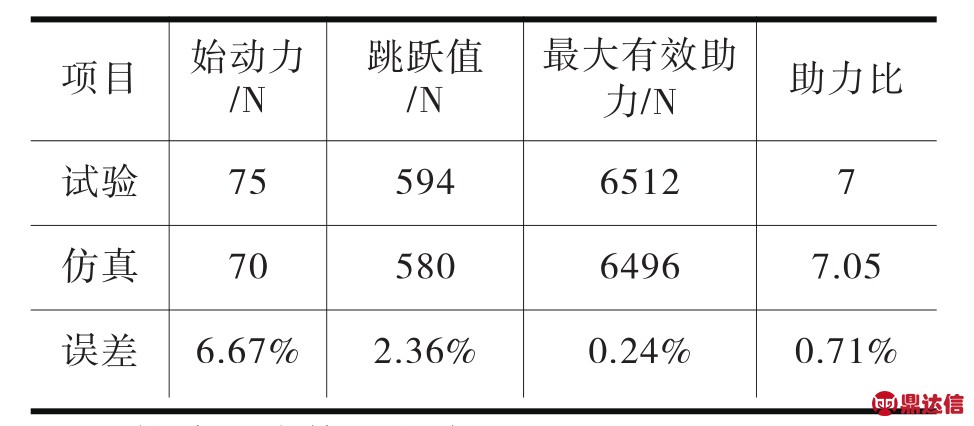
2.2 制动系统静态仿真
《真空助力器技术标准》中施加踏板力的标准为:在助力器的输入推杆上以150N/s~300 N/s的速率连续加载到最大助力点的130% 以上,输入信号时间持续8s,输入力最大从0N连续增加到400N。通过仿真可得到制动踏板位移、制动踏板力和制动管路油压三者的相互关系曲线。
图13为制动踏板力与制动管路油压关系曲线。由图可以看出曲线变化主要是受真空助力器特性曲线的影响。曲线A-B段,真空助力器产生跳跃值,制动管路中油压迅速增加;曲线B-C段,真空助力器产生伺服力,制动管路中的油压快速上升;曲线C-D段,真空助力器已达到最大阻力点,推杆力直接作用在主缸上,油压增速放缓。
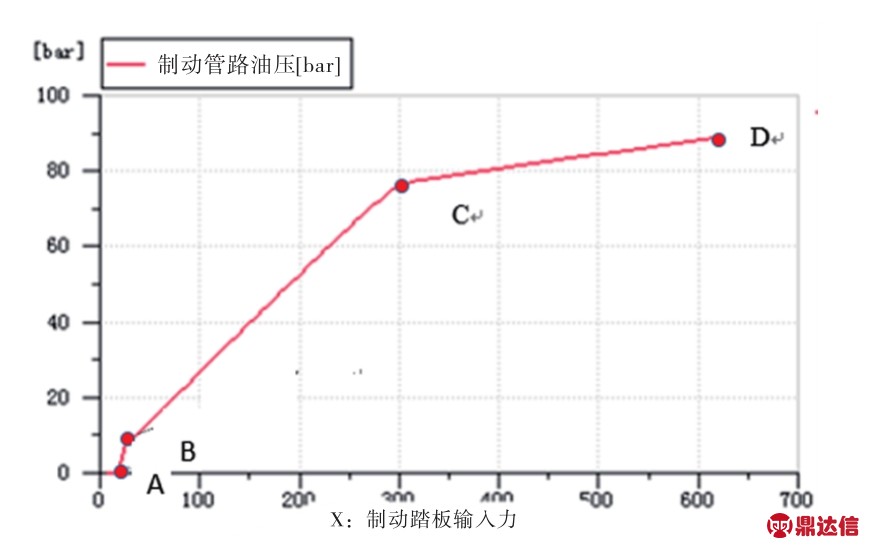
图13 踏板力-管路油压关系曲线
图14为制动踏板位移和制动踏板力关系曲线。曲线A-B段,当制动系统中存在间隙时,随着踏板输入力的增加踏板位移迅速增加,且曲线近似为水平直线;曲线B-C段,真空助力器开始助力,踏板位移随制动踏板力的增加而增加,此时制动脚感偏硬;曲线C-D段,真空助力器已达到最大助力点,制动踏板输入力直接作用在制动主缸推杆,较大的踏板力增加只能引起较小的踏板位移,曲线斜率变大,制动脚感较B-C段更硬。
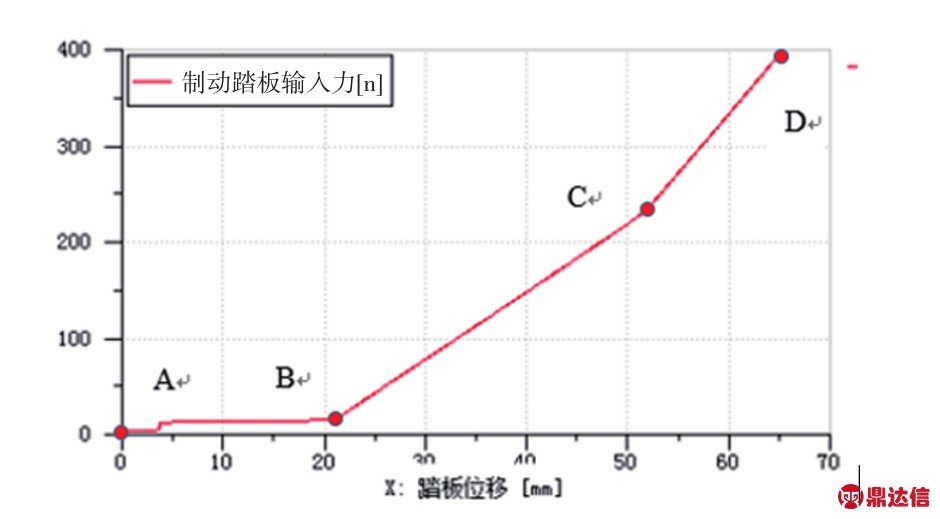
图14 制动踏板位移-踏板力关系曲线
图15为制动踏板位移和制动管路油压的关系曲线。曲线A-B段,制动系统存在间隙时随着制动踏板位移的增加制动管路油压增加缓慢;曲线BC段,此时真空助力器开始助力,制动管路油压随制动踏板位移迅速增加;曲线C-D段,真空助力器已达到最大助力点,较大的制动踏板位移才能使制动管路油压有明显变化,制动管路油压增速减缓。
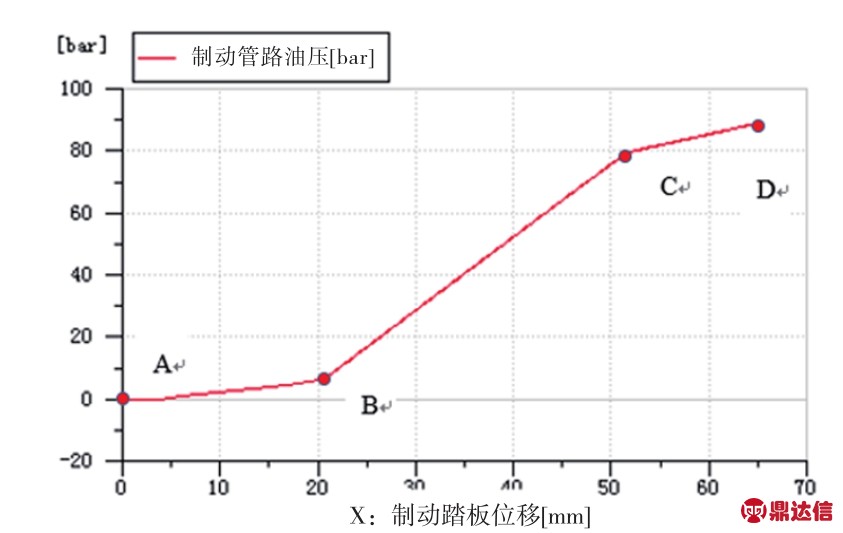
图15 制动踏板位移-管路油压关系曲线
2.3 制动系统动态仿真
图16为空载和满载两个工况下踏板力与制动减速度的关系曲线,实线为空载工况曲线,虚线为满载工况曲线。空载工况时,曲线A-B段,制动管路中还没有建立起油压,车辆属于滑行状态,受到滚动助力和风阻等阻力,有较小的减速度,此时驾驶员几乎感觉不到制动减速;曲线B-C段,真空助力器产生跳跃值,制动减速度有明显的增加,驾驶员开始感觉到车辆的制动减速度;曲线C-D段,制动减速度随着踏板力的增加而持续增加;曲线D-E段,车辆开始滑移,空载情况下制动减速度不能继续增加。图中可以看出,满载工况下车辆没有产生滑移,真空助力器在曲线后部达到最大助力点,制动减速度增速减缓。
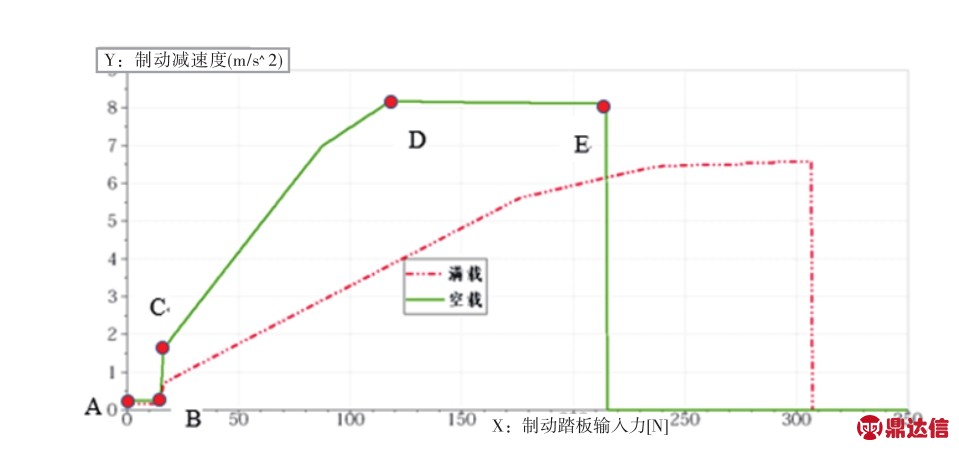
图16 踏板力-制动减速度关系曲线
图17为制动踏板位移和制动减速度关系曲线,其中实线为空载工况曲线,虚线为满载工况曲线。对于空载工况,曲线A-B段,即使制动系统有间隙时制动减速度基本保持不变;曲线B-C段,制动系统产生压力但真空助力器没有达到平衡状态,因此制动减速度增加缓慢;曲线C-D段,真空助力器未达到最大助力点,制动减速度相对制动踏板位移持续增加;曲线D-E段,车辆开始滑移,制动减速度保持稳定。满载工况相较空载工况,曲线趋势基本相同,在曲线后部车辆未出现滑移,此时真空助力器已达最大助力点,踏板力直接作用在主缸上,制动减速度随制动踏板位移的增加而缓慢增加。
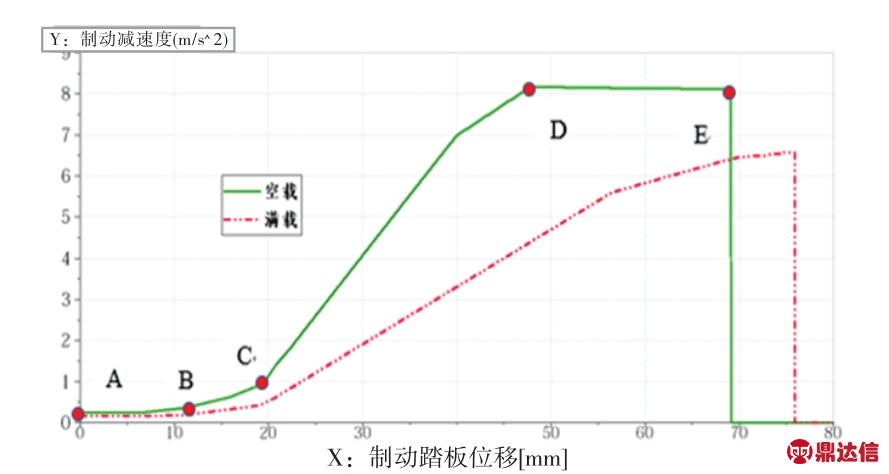
图17 踏板位移-制动减速度关系曲线
2.4 控制阀间隙绝对制动系统的影响
真空助力器控制阀门间隙对真空助力器特性曲线的影响如图18所示。从图中可以看出,真空助力器阀门间隙对始动力、跳跃值和最大助力点均有影响,从图中提取各重要参数点,如表7所示:
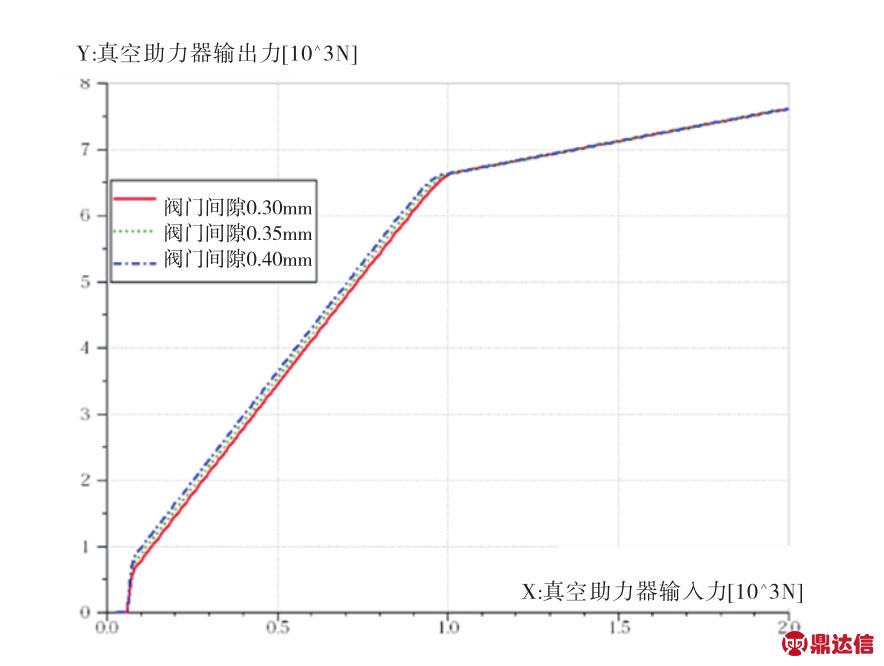
图18 助力器控制阀门间隙的影响
表7 真空助力器重要参数点
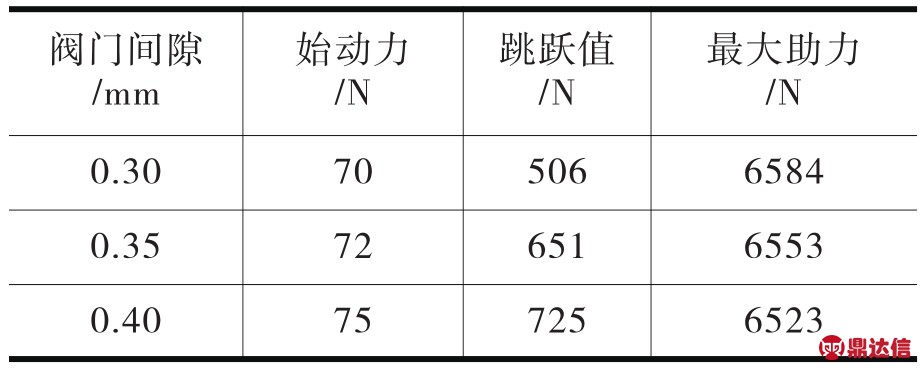
从表中可以看出,随着控制阀门间隙的增大,制动系统始动力有所增加,但影响较小;跳跃值有明显的增加,这将会影响制动初始阶段车辆的制动减速度;而对最大助力的影响可忽略不计。
3 结论
利用AMESim软件建立了整个制动器系统模型,并利用试验数据验证了所建双膜片弹簧真空助力制动器模型的有效性。
在对某轻型载货汽车的制动系统建模仿真后发现该车在满载时,制动系统无法提供足够的制动力,需要对该车的制动系统进行进一步优化,以满足满载时的制动要求。
真空助力器控制阀间隙的增加对制动系统始动力的影响十分有限,而对制动系统跳跃值的影响十分明显,这样对车辆制动初期的减速度产生影响。