摘 要:针对目前国内及国外发动机装配线中涂油方式的低效、污染及浪费严重的缺点,开发了全新的全气动控制带有回收功能的自动涂油装置,为发动机生产厂商提供了一种高效节约的零件涂油解决方案。
关键词:涂油装置;全气动控制;发动机装配线
引言
汽车发动机装配过程中,有很多零件带有O形圈等密封件,在装配前需要在密封件表面均匀喷上一层润滑油,从而达到易于装配及避免密封件损伤的目的。由于发动机装配零件中,润滑部分形状不规则,涂油量小且要求精确,无法像传统的涂油设备,如端盖涂油那样,采用复杂的机械结构实现[1]。由于发动机装配线场地要求紧凑,人机工程要求高的特点[2],所采用设备必须要占地小,便于移动。目前大多数国内厂商采用的是海绵擦油的方式,效率低下,浪费严重,涂油效果差。国外厂商如蒂森克虏伯采用的是电动与气动相结合的方式涂油,对电气控制要求极高,机构复杂、维修难度高。针对以上两种方式的优缺点,从纯气动控制方式入手进行了深入研究,研制出此自动涂油装置,解决了以上所有方式的缺点,此装置具有全气动控制,适应性强,移动方便;定量且能形成气液卤化形式;可回收废弃的润滑液,重复使用,不污染环境等众多优点。由于发动机装配零件中带有密封件的零件众多,所以该装置的应用非常广泛,具有良好而广阔的前景。
1 系统构成
本装置由控制箱(如图1所示)和涂油头两部分构成。所有的气动元件都合理的布置在控制箱中 (如图2所示), 通过一个进气口, 一个出气口, 一个进油口及一个回油口与涂油头进行连接。控制箱可根据为
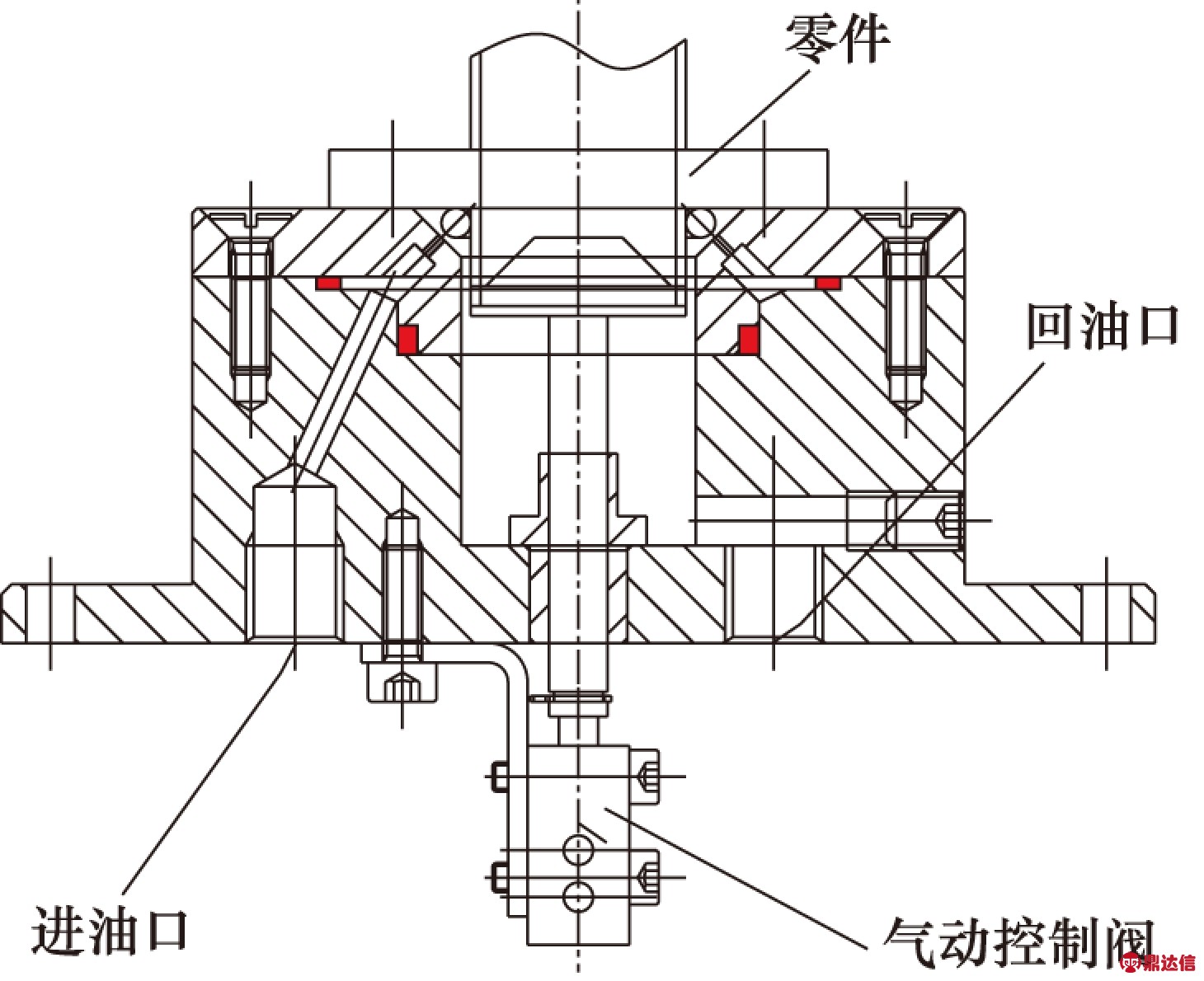
图1 涂油控制箱
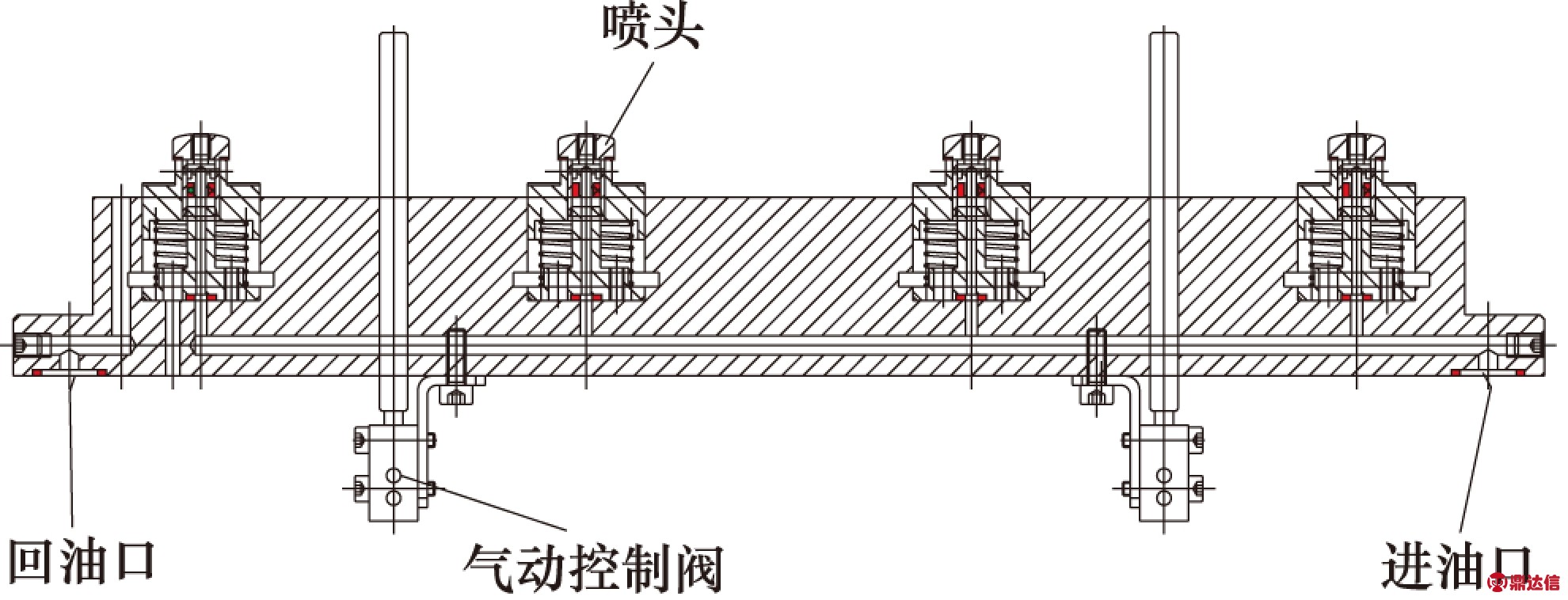
图2 涂油控制箱内部
所需涂油头的数量,分为可带1喷头(如图3所示,适用于零件外径密封圈涂油)、2喷头(适用于同一个工位上两种涂油零件同时涂油)、4喷头(适用于特殊零件,如进气管下体及燃油分配器上O形圈涂油,结构如图4所示)三种规格,而涂油头则需根据零部件涂油要求制作,以适应轴状零件件内径、外径和平面等不同要求。
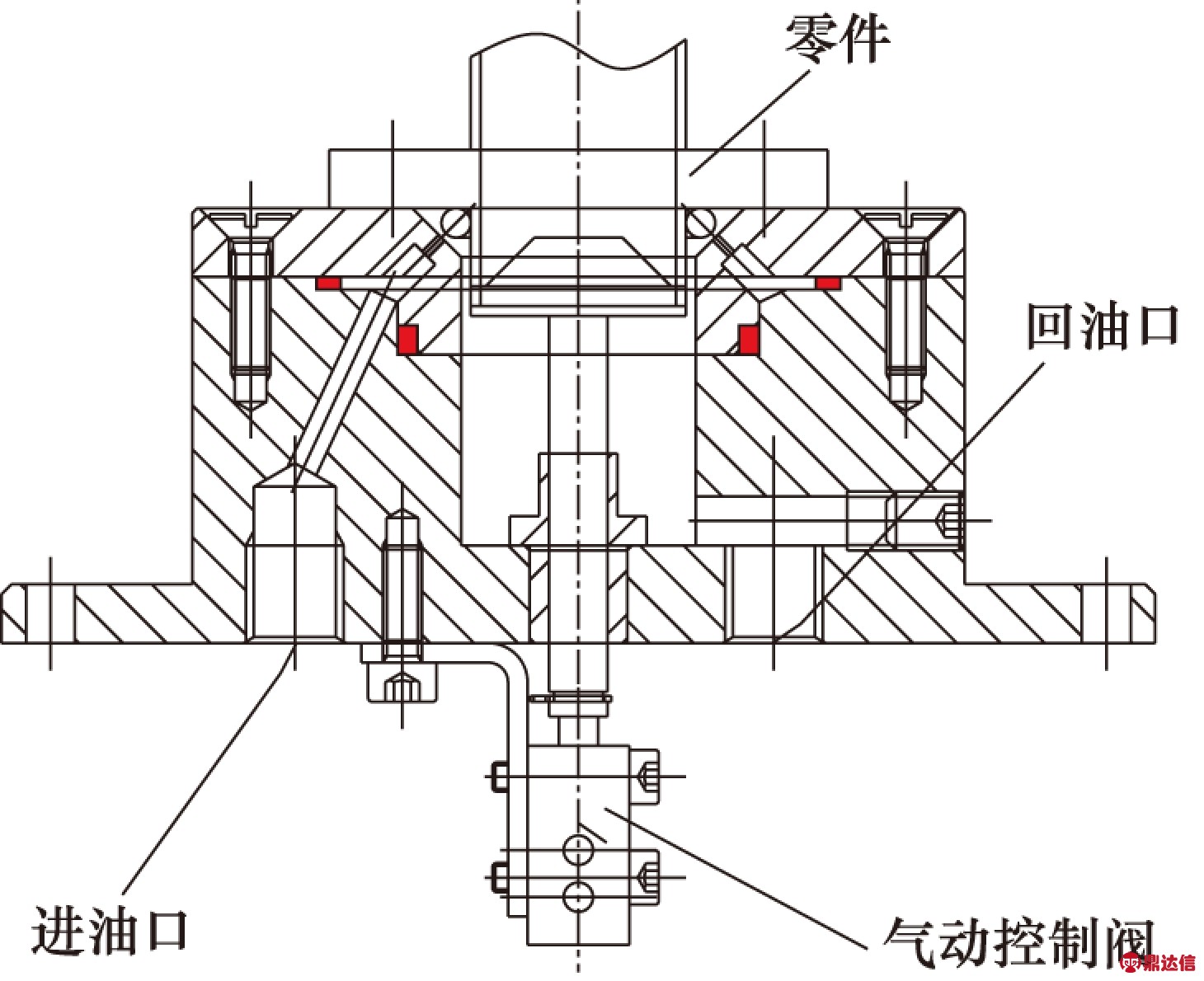
图3 1喷头涂油头
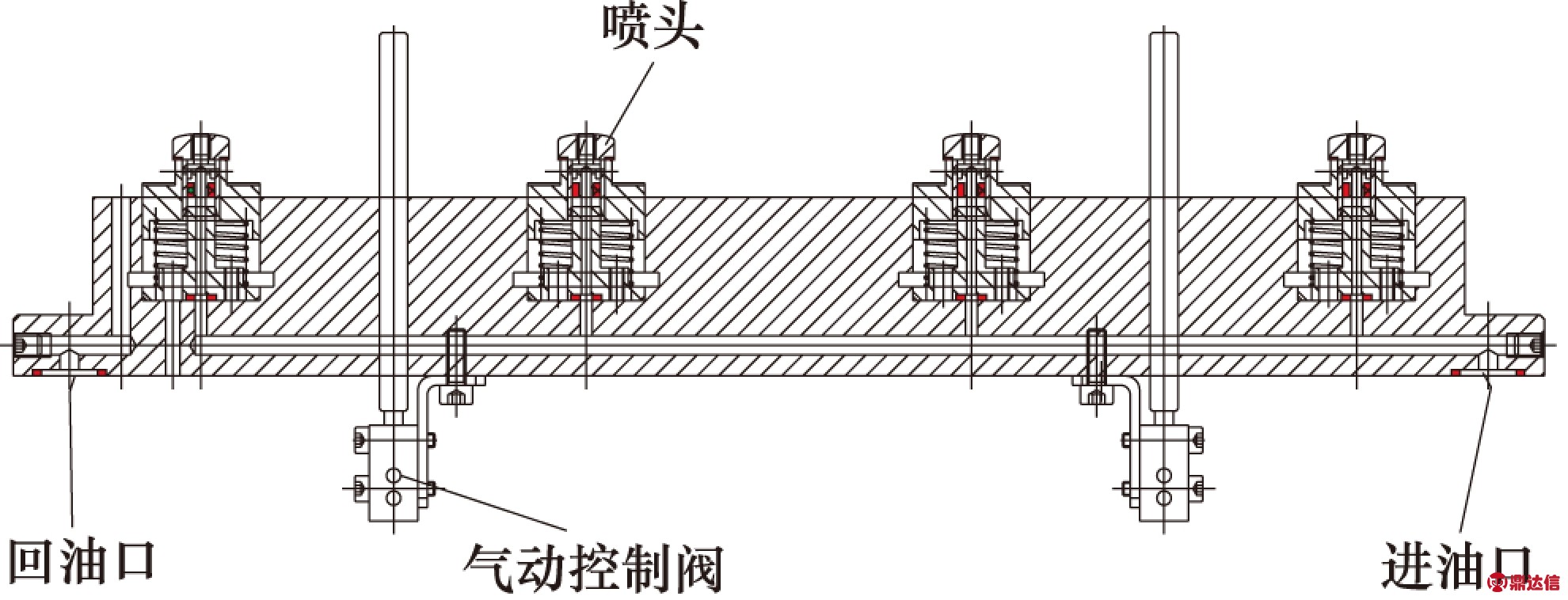
图4 4喷头涂油头
2 工作原理
2.1 涂油及喷油卤化工作原理
如图5所示,压缩空气从气源15,经过气源处理三联件14调整成适当的工作压力,通过手动换向阀2(初始位),经过减压阀1(根据润滑液的粘稠度调整成适当的压力),到达工作罐3。单向阀4处于工作罐3与定量阀10之间起单向隔离作用),此时,定量阀10的柱塞在其弹簧的作用下缩回,工作罐内的润滑液3在罐内压力和定量阀10的柱塞缩回所产生的真空作用下,经单向阀4进入柱塞腔。润滑液进入定量阀10的柱塞腔的多少取决于定量阀10调整的柱塞行程大小。当工件放入涂油头并触动发信阀5,压缩空气通过发信阀5驱动通断阀19和换向阀7换向,同时压缩空气通过快速排气阀18,向可调气容20充气。定量阀10动作,定量阀10的柱塞将润滑液挤入涂油头与通断阀19之间的管道。当工件从涂油头拿出的瞬间,发信阀5断开,通断阀19和换向阀7复位,定量阀10重复吸油过程,与此同时气容中的压缩空气通过排气阀18排气口进入涂油头与通断阀19之间的管道,压缩空气混合挤入涂油头与通断阀19之间的管道内的润滑液一起从涂油头喷出,并喷涂到工件上。
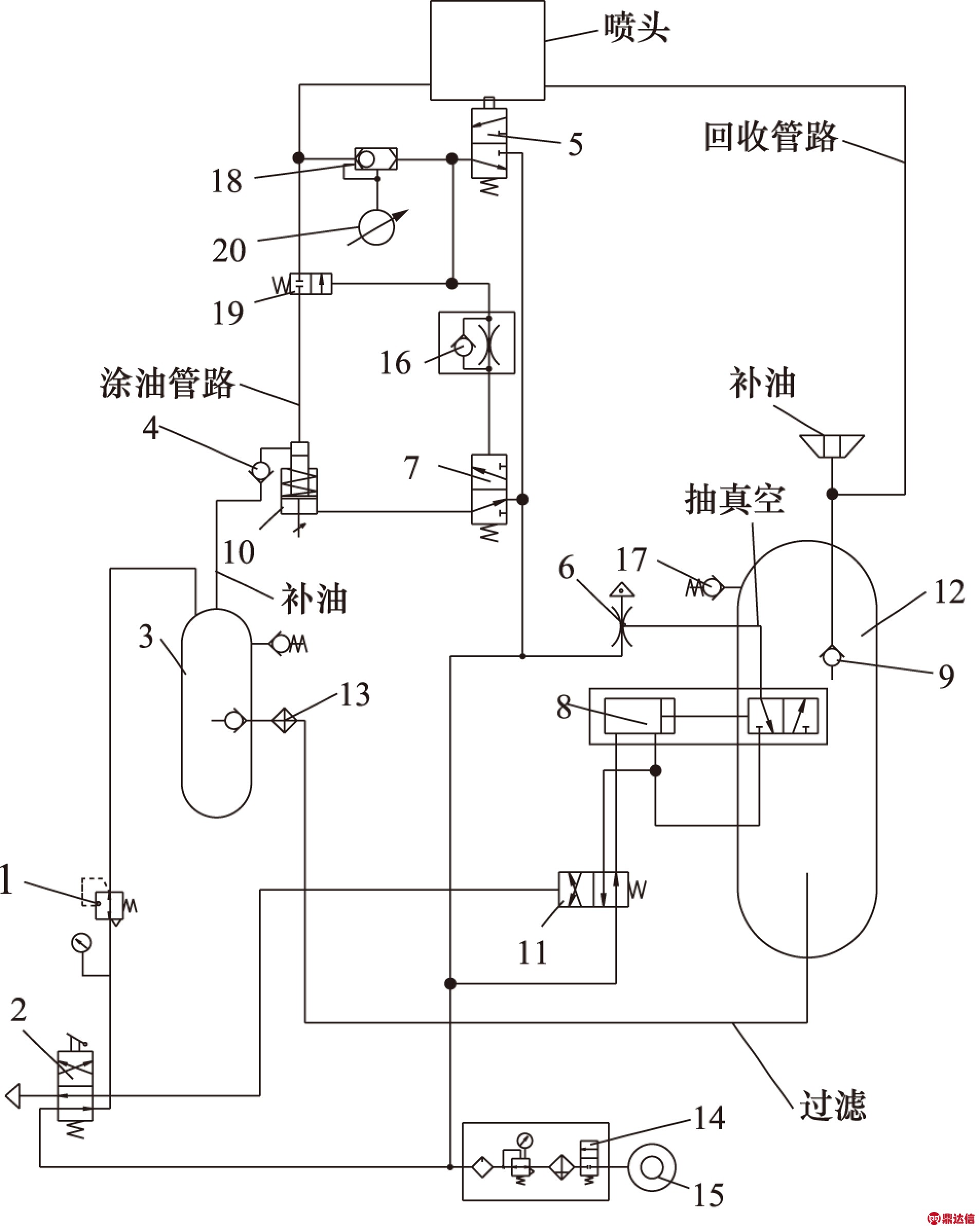
图5 气动原理图(基本型)
2.2 回收工作原理
回收罐12中的空气,经组合阀8,真空发生器6排到大气,使回收罐处于负压状态。涂油头在每次涂有完成后的残油,在涂油头内部收集,并通过回收管道、组合单向阀进入回收罐12。从而实现废液的回收利用。
2.3 回收过滤工作原理
当手动换向阀2被打开时,换向阀11换向,组合阀8动作,真空抽吸管道被切断,同时压缩空气通过组合阀8进入回收罐12,回收罐12中的润滑液通过过滤器13进入工作罐3,使得工作罐3中的润滑液的是补充。
3 应用实例
本系列涂油装置已经广泛应用于一汽大众EA111/EA113/EA211发动机装配线。该装置采用全气动控制,采用定量涂油阀控制涂油的涂油量。其工作过程为:用一气缸推动加压柱塞,使其被涂流体增压并由喷嘴定量喷出到被涂工件表面,气缸活塞处设置有定量调节螺栓,通过限制气缸活塞的移动距离,实现对喷油量的控制。
由于润滑介质的高黏度性,采用气压补油的方案。对工作罐施加以一定的补油压力,以保证涂油定量阀能够及时并充分的汲取润滑油。
考虑到环境保护及喷涂后废液的回收利用,在装置中配置了回收罐及过滤系统。其工作过程为,利用真空阀造成回收罐的一定负压,将喷嘴处的残余润滑油经单向阀吸入回收罐中,(新加注润滑液也在此罐中进行),当需要将补充工作罐润滑液时,可将气压引入回收罐,同时驱动气缸将回收罐进液口封住,此时,回收罐中的润滑液在气压的作用下,经过机油滤、单向阀,过滤后补充到工作罐中。
由于全气动控制及回收技术的使用,大幅减少了润滑油的使用量为,企业节约了大量成本,表1中列出了几种零件使用此装置前后耗油量的对比,节油率都达到了93%以上。
表1 海绵方式与此涂油装置耗油量数据比较(每100件零件)

4 结论
该自动涂油装置针对现有生产线涂油方式的低效、重污染及浪费问题进行的全新的涂油方式的升级,采用全气动控制实现了高效节能的涂油效果。采用此装置后,生产线上润滑油的使用率大幅提高,工人操作强度明显降低,设备维修率及维修难度大幅降低。经过数年的生产现场实践证明,该装置使用方便,完全满足不同规格涂油零件的装配需求,深受现场装配工人的好评,达到预期的设计目的。