摘 要:低温流体与常规室温流体冷凝存在显著差异,简述了国内外报道的主要低温冷凝实验装置,指出要准确描述翅片通道内冷凝及两相流动过程,必须借助先进的可视化手段。为解决空分装置中主冷凝蒸发换热器翅片通道内低温流体冷凝热阻大、换热效率低的难题,设计搭建了一套低温冷凝可视化实验装置,实验段采用带光窗的可拆密封设计,便于研究平壁表面及各种型号翅片通道内冷凝换热过程。经初步测试,该实验装置运行稳定,借助高速摄像机可清楚地观察到氮冷凝两相流动的现象。
关键词:空气分离 低温冷凝 可视化 装置设计
1 引言
大规模工业气体应用促进低温空气分离设备向大型化发展,目前世界最大的空分系统规模已达到113 880 Nm3/h[1],空分能耗问题变得日益突出。主冷凝蒸发换热器(简称主冷)是空分装置的关键设备,其结构和性能对空分装置的能耗及效率影响显著。一般情况下,主冷换热温差每降0.5 K,整套空分装置能耗即下降2.46%[2],而温差的降低主要依靠对其内部流体流动与传热机理的深入研究和结构的优化设计。在常温区工作的冷凝蒸发换热器中,流体的沸腾侧热阻往往比冷凝侧热阻大一个数量级,故目前对于沸腾换热的研究远多于冷凝。然而在低温下,沸腾热阻与冷凝热阻大体相当,氢的沸腾热阻甚至小于冷凝热阻[3]。在空分主冷中,冷凝侧热阻大小约为蒸发侧的30%—60%,且随着热流密度增大,两者差别逐渐减小[4]。同时,实际系统中不凝性气体也会显著增大冷凝换热的热阻。主冷运行时,氮气中往往含有少量的氖、氦等不凝性气体,这就导致实际运行的主冷中冷凝热阻增大。综上所述,空分主冷冷凝通道内的换热强化问题不可忽视,但目前仍缺乏对其专门的研究[4-5]。
2 低温流体冷凝的特殊性
低温流体与常温流体(以水为代表)的冷凝都是气体在低于饱和温度的情况下发生液化的现象,本质上是相同的。然而,低温流体冷凝又有其特殊性,这主要是由于低温流体的物性与常温流体的物性(见表1)存在着较大差异。
表1 水和低温流体的物性参数比较(0.101 3 MPa)
Table 1 Comparison of physical parameters of water and cryogenic fluids(0.101 3 MPa)
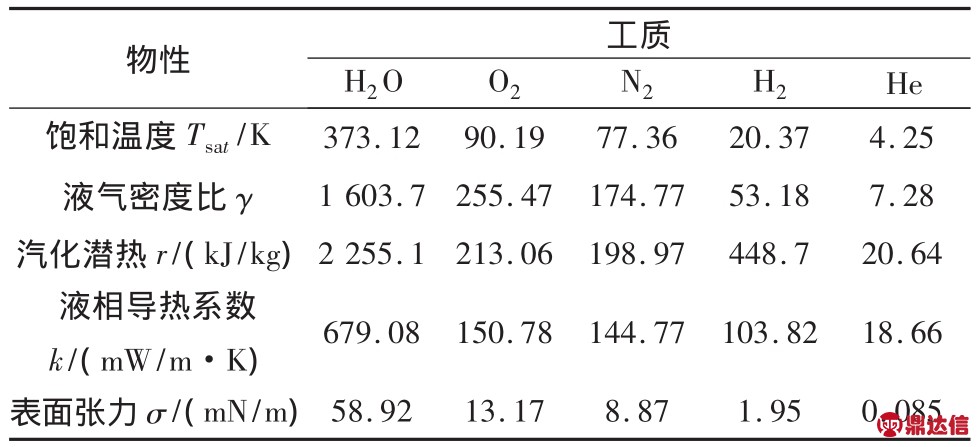
(1)低温冷凝的理论换热系数小。对于理想状态下的膜状冷凝,根据热量平衡,冷凝表面局部的冷凝换热系数应该等于通过该处液膜的导热系数除以液膜厚度。液相导热系数越小,液膜厚度越厚,则冷凝换热系数越小。由表1可知,低温流体液相导热系数均不到水的1/4,这是低温流体冷凝换热系数远小于水蒸气的主要原因;通过Nusselt理论关于液膜厚度的计算式可近似推得,低温流体冷凝的液膜稍厚于水,差别一般不超过30%,这构成低温冷凝换热系数小的次要原因。
(2)低温冷凝的传热强化更加困难。首先,冷凝强化的主要方法是利用延展表面减薄液膜厚度,在这类方法中表面张力促使的液膜减薄起到了主要的强化传热作用,而由于低温流体表面张力不到水的1/4,导致这类方法的强化效果明显降低。此外,表面张力小意味着表面自由能小。根据表面自由能差判据[6],相同的固体表面上,低温流体与固体表面的自由能差较小,更难以形成滴状凝结。即可以使水形成滴状凝结的材料未必能使低温流体形成滴状凝结,使用构造滴状凝结表面的方法强化低温冷凝也相对困难。
(3)低温冷凝两相流的流型变化复杂。低温流体的汽化潜热比水小一个数量级,在相同的冷凝换热量下,沿程干度变化更剧烈,这也就意味着其两相流的流型变化更迅速,流型图转变曲线提前;而低的表面张力也使得重力的影响相对更明显,更倾向于出现环状流及分层流等重力主导的流型。
低温流体与常温流体冷凝存在的上述差异,使得换热器中常温流体冷凝的多数传热、流动关联式以及强化方式不适用于低温流体,必须对其进行专门研究。
3 低温冷凝实验研究综述与讨论
3.1 低温冷凝实验研究综述
对低温冷凝的实验研究大致可分以为两个阶段:第一个阶段的研究大多以管式冷凝蒸发器为背景,通过实验得到低温工质在光管内或光管外冷凝的换热系数,以验证Nusselt理论是否能用于管式冷凝蒸发器的设计。第二个阶段多以板翅式换热器为背景,研究低温流体在微小通道内的冷凝。
Leonard与 Timmerhaus[7]设计了氮气的竖直管外冷凝实验,装置结构如图1所示。使用常压下的液氮作冷源,加热再沸器中的液氮,产生饱和氮蒸气,氮蒸汽上升进入冷凝腔室,在竖直铜管外冷凝,冷凝液向下回流至再沸器中。在铜管壁面内埋设热电偶测量冷凝壁温,通过热流密度与冷凝换热温差直接求得冷凝换热系数。实验结果表明,氮气的冷凝换热系数与Nusselt理论计算值吻合较好,偏差不超过±20%。此外,Haseldon和 Prosad[8]研究了氮和氧的冷凝,实验结果在误差可接受的范围内,氮和氧的冷凝换热系数与Nusselt理论计算结果都相吻合。
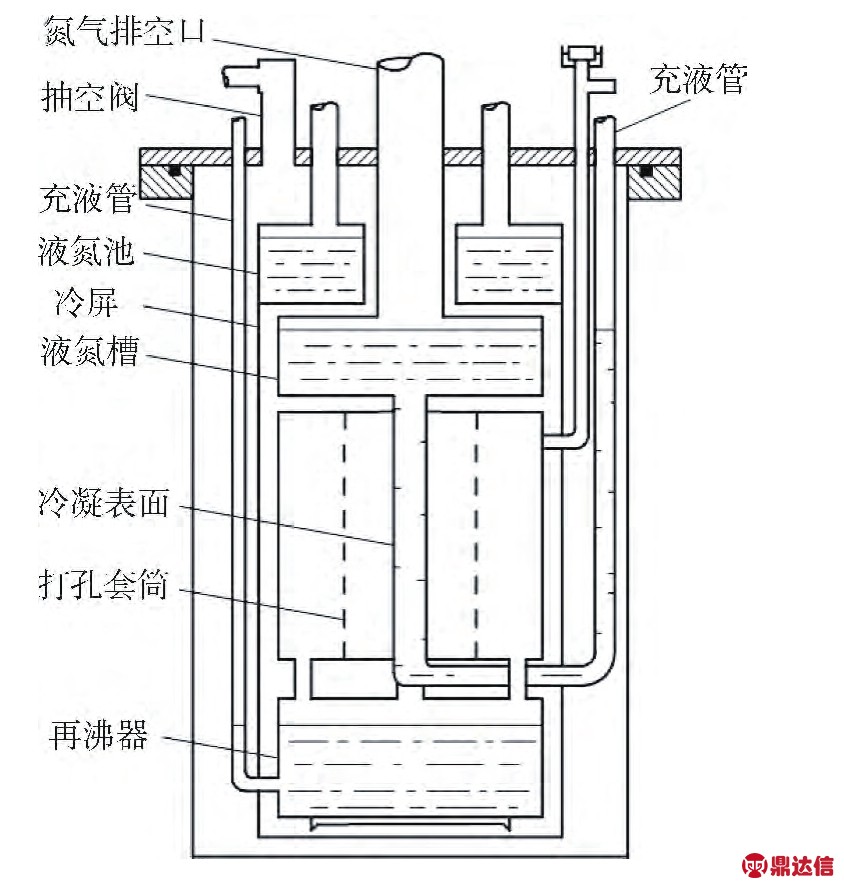
图1 文献[7]实验装置结构示意图
Fig.1 Structural diagram of test apparatus in [7]
Ewald和Perroud[9]设计了氮、氢和氘的可视化冷凝实验。实验装置如图2所示,加热器中加热产生的饱和蒸汽上升进入冷凝室,在冷凝管管外发生冷凝,冷凝液沿输送管流回至加热器中。该装置真空罩与冷凝器外壁均采用Pyrex玻璃制作,可以获得管外冷凝的可视化资料。由于氢和氘冷凝时横跨液膜的冷凝传热温差很小,直接测量困难,文献采用间接处理的方式,用总换热系数和使用核态沸腾的Kutateladze经验关联式估算得到的沸腾侧换热系数,间接得到冷凝换热系数。实验结果表明氮的冷凝换热系数与Nusselt理论吻合较好,而氢和氘的换热系数整体比理论计算值低20%,在低热流密度下甚至低50%以上。
真空杜瓦内部结构如图4所示,液氮上储池与液氮下储池通过管道连接,通过充液管补充液氮。液氮下储池与冷凝实验段焊接成一体,其中的液氮为冷凝实验段中的高压氮气冷凝提供冷量。冷凝实验段与再沸器通过管路连接成封闭的冷凝回路,再沸器底部安装加热棒加热液氮产生氮蒸气,蒸气进入冷凝实验段内,在翅片表面冷凝成液氮,冷凝液下流返回再沸器中,实现自然循环。
空分领域从20世纪50年代开始应用板翅式换热器,如今管式换热器已普遍被紧凑高效的板翅式换热器所取代。学者们针对板翅式换热器中的相变换热进行了很多研究[4-5,11-12],但多以沸腾换热为主,专门针对低温流体冷凝的研究还很少。
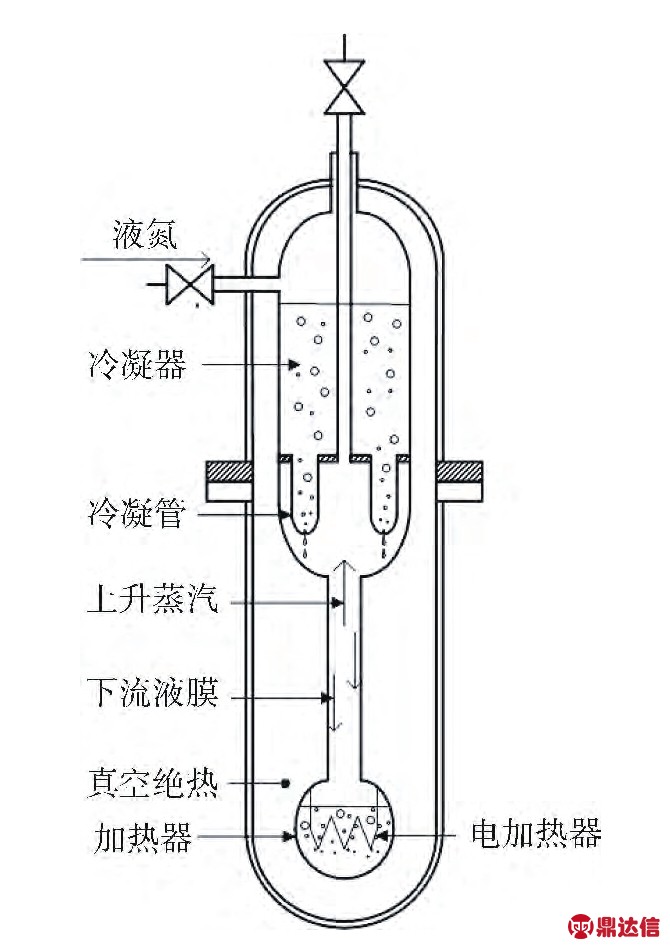
图2 文献[9]实验装置结构示意图
Fig.2 Structural diagram of test apparatus in [9]
刘永忠[4]及陈流芳等[5]研究了板翅式冷凝蒸发换热器单元中的沸腾与冷凝传热特性。制作了3个通道的板翅式冷凝蒸发单元试样,中间为冷凝通道,两侧为蒸发通道。实验结果表明氮气在翅片通道内的冷凝传热系数比Nusselt理论值高50%左右。另外,实验结果显示冷凝热阻约为沸腾侧的一半,且随着热流密度增大,两者差别逐渐减小,在这种情况下,冷凝换热热阻不可忽视。
3.2 低温冷凝实验结果讨论
Nusselt理论运用数学方法推导出冷凝传热问题的解析解,对于一般牛顿流体发生的冷凝,只要符合液膜平整无波动等假设条件,那么其实验结果就应该与理论计算值相吻合。而在蒸汽流速较大、液膜Re较大或液膜波动等情况下的冷凝(如板翅式换热器通道内的冷凝),不再符合Nusselt理论的假设条件,故冷凝换热系数将大于理论计算值。
低温冷凝已有的实验结果见表2,从实验结果来看,氮和氧的实验结果与Nusselt理论计算吻合较好。而氢则存在两种不同的实验结果:文献[9]实验表明,氢的冷凝换热系数整体比理论计算值低20%,并且在低热流密度下低50%以上;而文献[10]的实验表明,氢的冷凝换热系数与理论计算值吻合良好,偏差在±20%以内,低热流密度下也依然如此。由于氢的冷凝换热温差不易测准,文献[9]采用间接方式,通过总传热系数和根据经验关联式估算的核态沸腾换热系数,间接求得冷凝换热系数。所用的经验关联式在应用于液氢的核态沸腾时,可能带入了偏差,使实验结果存在较大的不确定性。文献[10]通过打孔安装高精度的锗电阻温度计测量壁温,直接根据热流密度和冷凝换热温差求得冷凝传热系数,实验结果相对更可靠。应该可以认为,氢的冷凝传热系数也是与Nusselt理论相吻合的。
表2 已有的低温冷凝实验结果
Table 2 Experimental results of cryogenic condensation
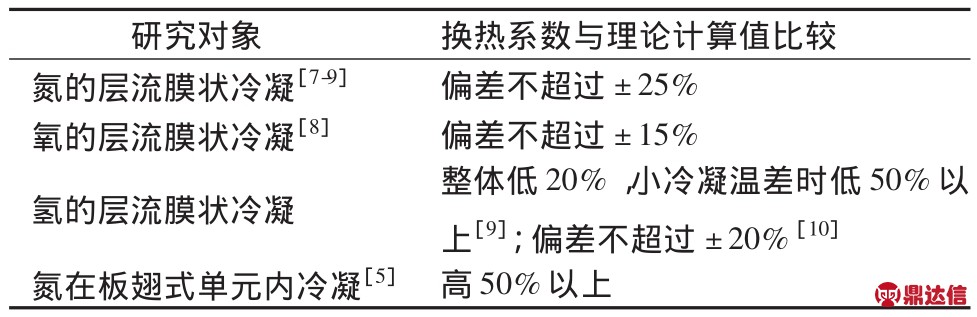
板翅式换热器可以明显地强化低温流体的冷凝换热,而目前尚缺乏描述这一过程的精确关联式。其中的一个重要原因是板翅式换热器翅片通道内的冷凝过程属于微小通道有相变的两相流动,其传热与流动机理复杂多样,且与两相流动的流型直接相关,不同的流型下传热与水力学特性相差很大。而目前极少见到有对翅片通道内低温流体冷凝的两相流型进行可视化观测的研究,导致了空分主冷内两相流动的基础理论不完善,限制了主冷的优化设计和效率提升。
4 低温冷凝可视化实验系统设计
4.1 实验系统结构设计
Ohira[10]研究了氮和氢的冷凝,实验装置以两级G-M制冷机冷头为冷源,将冷凝管固定在制冷机冷头上,冷凝管与下方的再沸器连接,加热产生的蒸汽在冷凝管内壁上冷凝。实验采用直接测量的方式,在距管内壁面0.9 mm处打孔,安装锗电阻温度计,测量与壁面温度极为接近的壁内温度。实验结果表明,氮和氢的冷凝换热系数与Nusselt理论预测的结果偏差不超过±20%。
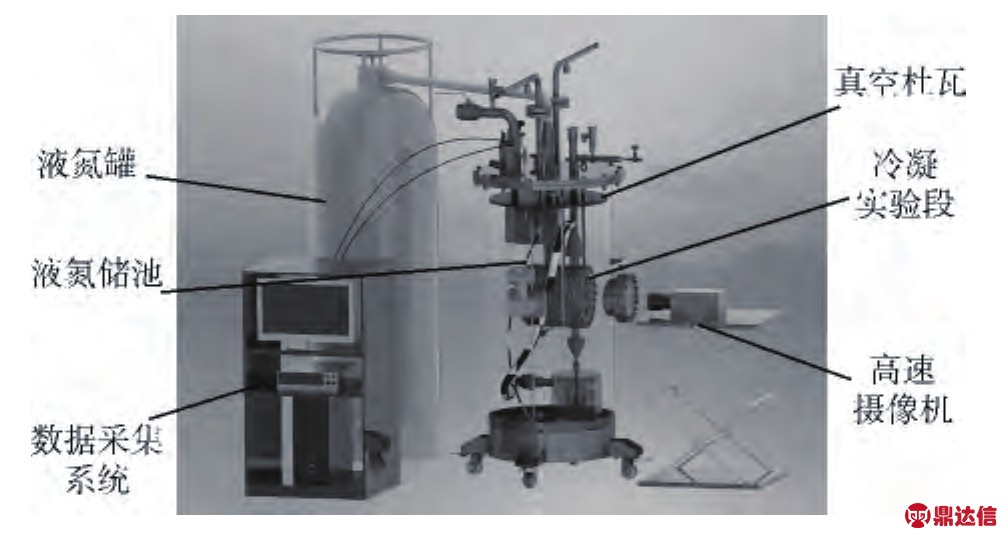
图3 低温可视化实验系统示意图
Fig.3 Schematic diagram of cryogenic visual system
系统的冷量由液氮提供,液氮储存在液氮储池内,通过吸收相邻冷凝实验段内高压氮气的热量使之冷凝。冷凝实验段与真空罩上对应位置均设置可视窗口,整个过程可用高速摄像机拍摄,同时采集相关温度及压力数据。
为了研究低温流体在翅片通道内的冷凝过程,掌握其冷凝两相流动的流型等可视化信息,以得到精确描述该过程的数据与关联式,本文初步建立了一套可用于研究平壁表面及各种型号翅片通道内冷凝过程的可视化实验系统,如图3所示。
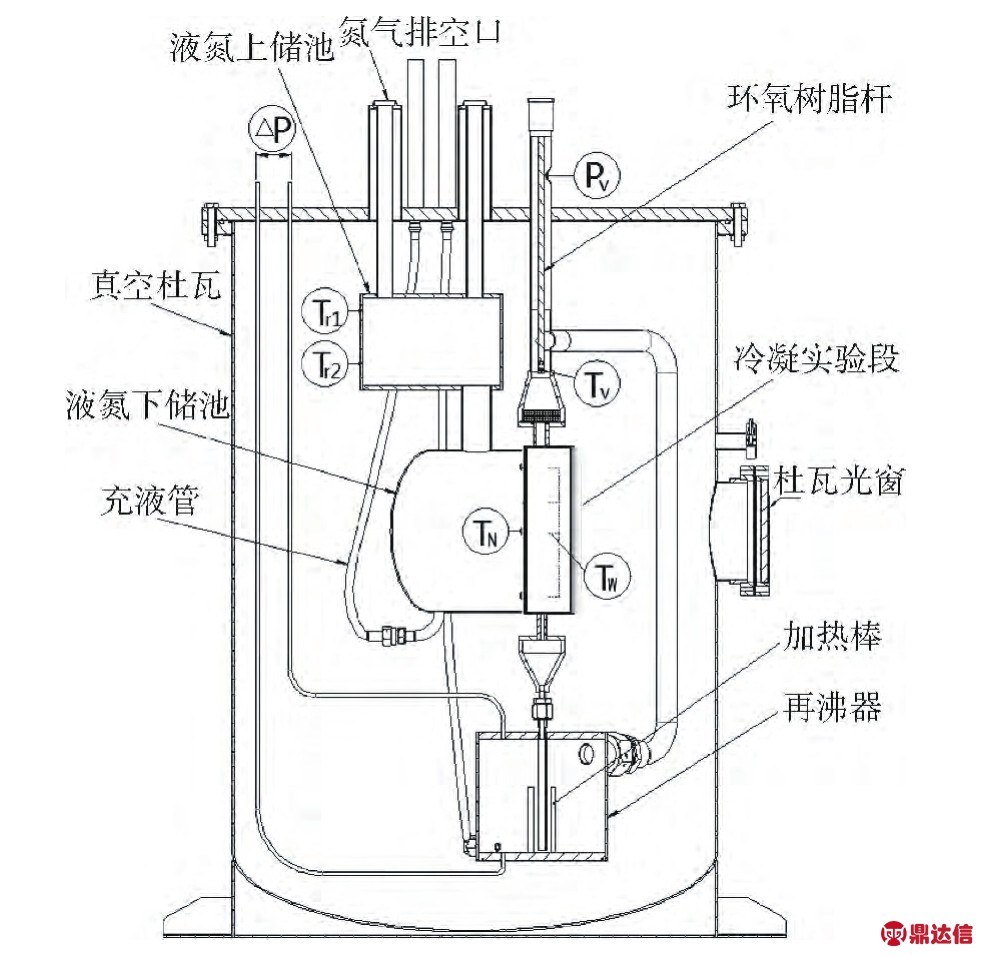
图4 杜瓦内部结构示意图
Fig.4 Structural diagram of cryostat
系统运行时冷凝实验段处于低温环境下,玻璃光窗与金属之间的密封存在一定难度。在液氮温度附近两种材料的热膨胀系数相差一个数量级以上,从室温冷却到低温过程中将产生很大的收缩量差异。采用胶结的方式密封,装置很容易产生局部破裂和泄露,并且不能密封太大的压力;直接采用法兰压紧玻璃密封,玻璃易碎且不易进行表面加工,螺栓预紧力太大容易压碎玻璃,太小会导致泄露;使用可阀合金作为过渡金属焊接玻璃与不锈钢的方式密封效果较好,但对技术要求很高,不易获得,并且焊后不可拆,无法更换。本装置的冷凝实验段在结构上采用可伐合金焊接与法兰密封结合的方式,在不锈钢法兰盖上加工出窗座,光窗玻璃通过可伐合金焊接在窗座上,法兰盖与基座采用刀口密封方式将整个冷凝通道密封起来,以无氧铜做密封垫,既实现了低温下的可靠密封,又满足了拆卸更换内部翅片的需要。
由于存在直达试验段的光学通路,从室温环境到杜瓦内部的辐射漏热较大。为减小辐射漏热,实验装置采用带防辐射屏的真空多层绝热方式,在布置防辐射屏和包覆多层绝热材料时只留出必要的光学通路,并在玻璃表面覆盖反红外辐射涂层。内部各部件采用真空套管和G10杆悬挂固定于法兰上,以减小内部部件向法兰的导热漏热。
4.2 实验数据采集
实验时调节再沸器中加热器的加热量,等待试件回路中压力保持稳定,即再沸器中液位保持不变后,系统达到稳定工况。此时加热器的加热量Qh减去系统漏热量Ql即等于冷凝通道内的冷凝换热量Qc。
如图4所示,实验中的温度测量包括4部分:(1)在冷凝壁背面开孔,孔中布置温度传感器来测量冷凝壁面温度Tw。使用Apiezon真空酯填充孔与温度计之间的缝隙,减小热阻;(2)在液氮下储池内壁上布置温度传感器来测量液氮储池的温度TN;(3)在冷凝实验段入口处通过环氧树脂杆悬挂温度传感器,测量蒸气温度Tv;(4)在液氮上储池筒体外壁布置两个温度计测得温度Tr1、Tr2,以监测液氮上储池中液位。以上所用的温度传感器均为Pt100铂电阻温度计,经过精确标定,在液氮温区精度为±0.1 K,温度数据使用Keithley 2700数据采集器进行采集。
冷凝实验段入口的蒸气压力Pv通过管路引出至杜瓦外进行测量,如图4所示。压力变化范围0.1—1 MPa,压力传感器型号为UNIK5000,测量精度为±0.04%FS。使用差压变送器测量再沸器顶部与底部的压差△P来计算液位,如图4所示。差压变送器型号为 CS3351,测量精度为 ±0.25%FS。
综上所述,已经得到了冷凝壁面的壁温Tw、蒸气温度Tv以及冷凝换热量Qc,而冷凝温度Tsat可通过蒸气压力Pv得到,因此,低温流体在平壁表面或翅片通道内冷凝的平均传热系数可以表示为:
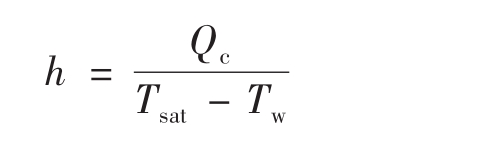
5 试验台初步测试
对试验台进行了测试运行。使用分子泵抽真空后,真空度可达 2.3×10-6Pa,漏率保持 10-10Pa·m3/s。当压力高于0.5 MPa时,刀口法兰的密封性能下降,漏率会有所上升,但仍可保持在10-7Pa·m3/s以下。充液氮后经过5 h预冷降温,试验台内部各测点温度接近液氮温度并保持稳定。启动加热器后,冷凝侧回路内部压力升高,并逐渐平稳,液位计示数先下降后稳定,表明达到稳定工况。调试发现,在冷凝通道内氮气压力达到0.5 MPa左右时可观察到大量的冷凝液下流,并可用高速摄像仪拍摄记录。几组典型的数据见表3,可以看出冷凝通道入口的氮气有一定的过热度,这是因为饱和蒸气从再沸器出口到冷凝通道入口经过约0.5 m长的管路,被管壁加热所致。通过上述测试试验,证明试验台运行稳定,实现了预期功能,为下一步开展翅片微小通道内氮气冷凝过程的研究创造了条件。
表3 试验台的典型运行参数
Table 3 Typical operation parameters of experimental device
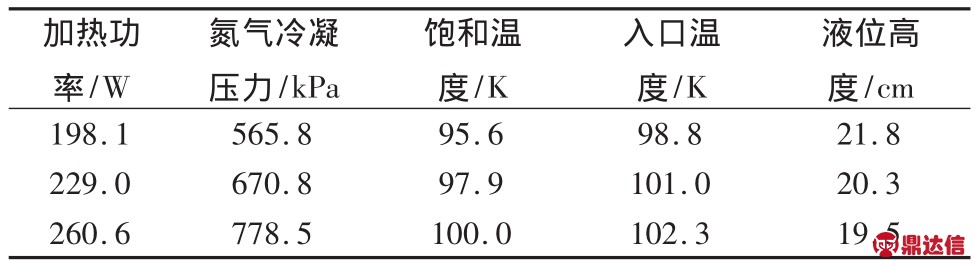
6 结论
(1)空分主冷中低温流体冷凝的热阻较大,影响了主冷效率的提升。与常温流体冷凝相比,低温流体冷凝具有其特殊性,需要进行专门研究。已有的低温冷凝实验大多研究光管壁面的冷凝,缺少对主冷翅片通道内冷凝的研究。为准确描述翅片通道内冷凝侧低温流体的两相流动,需借助可视化的手段获得不同的流型下传热与水力学特性。
(2)初步建立了一套可用于研究平壁表面及各种型号翅片通道内冷凝过程的可视化实验系统。重点解决了低温高压条件下的装置密封以及漏热问题。经测试,实验装置运行稳定,刀口法兰密封良好,辐射漏热较小,可以清楚地拍摄到壁面冷凝液氮的流动,并准确采集相关数据,为进一步研究微小通道内氮的冷凝两相流动提供了参考。