摘要:介绍了车载飞轮电池的储能和运行机理,详细分析了飞轮材料、磁悬浮技术、电动/发电机和电力电子转换装置等关键技术的国内外研究现状,探讨了车载飞轮电池的动力学特性及车载飞轮电池的发展趋势。
关键词:车载飞轮电池;飞轮材料;支撑装置;电动/发电机;电力电子转换装置
0 引言
当前,我国汽车保有量已超过1亿辆,而汽车是石油的主要消耗者,也是城市环境恶化的主要因素,而推广电动汽车是目前可行的解决方式。车载动力电池是电动汽车的动力源泉,是制约电动汽车广泛应用的主要因素之一。目前,研究较多的车载动力电池包括化学蓄电池、燃料电池、太阳能电池、超级电容器和车载飞轮电池等。飞轮电池又称机械电池,它利用飞轮高速旋转存储能量。与其他车载动力电池相比,飞轮电池具有比能量大、比功率高、使用寿命长、充电时间短、无环境污染和效率高等优点,存储1kW·h能量成本仅为超级电容器的1/20[1]。先进飞轮电池[2-4]的比能量可达150W·h/kg,比功率为5~10kW/kg,远高于一般的化学电池。在储能一定的情况下,其质量比超级电容更轻、体积更小,更加有利于车载布置及安装。
1 车载飞轮电池的工作原理
一种典型的车载飞轮电池的结构如图1所示。
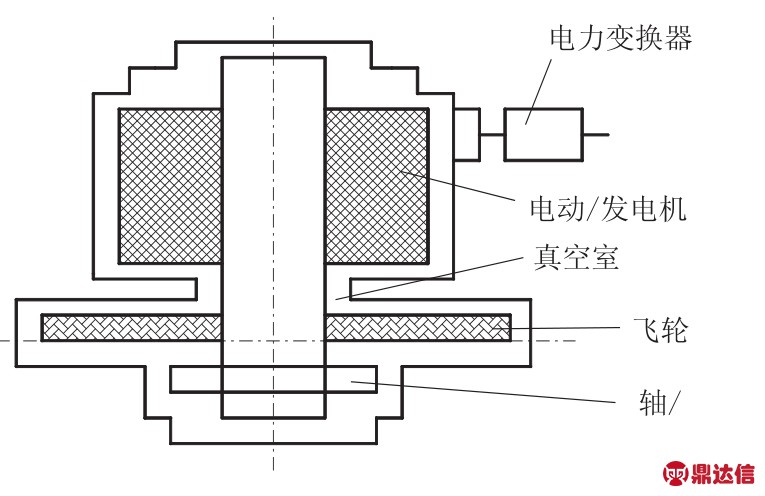
图1 车载飞轮电池的结构
车载飞轮电池储能系统能量流动如图2所示。车载飞轮电池一般有3种运行状态:充电状态、保持状态和放电状态。当汽车停止时,飞轮处于保持状态,电动/发动机处于空载状态;当汽车行驶或爬坡时,电动/发电机处于发电机运行状态,将转子的动能转换为电能输出;当汽车夜间充电时,电动发电机处于电动机运行状态,将外部电能转换为飞轮转子的动能储存起来。另外,当汽车下坡或制动时,电动/发电机和电力电子转换装置可将汽车部分动能转换为飞轮转子的动能。
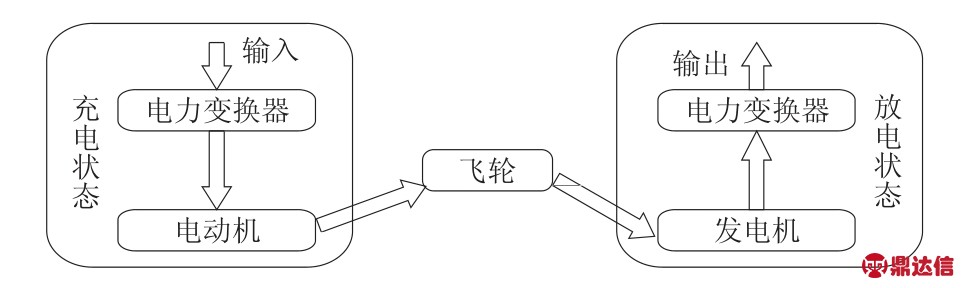
图2 车载飞轮电池储能系统的能量流动
2 车载飞轮电池的关键技术
2.1 飞轮的能量存储
在设计车载飞轮电池时,为减小汽车整体重量,通常在满足高储能量情况下,以体积和质量最小化作为优化目标。飞轮存储的能量为:
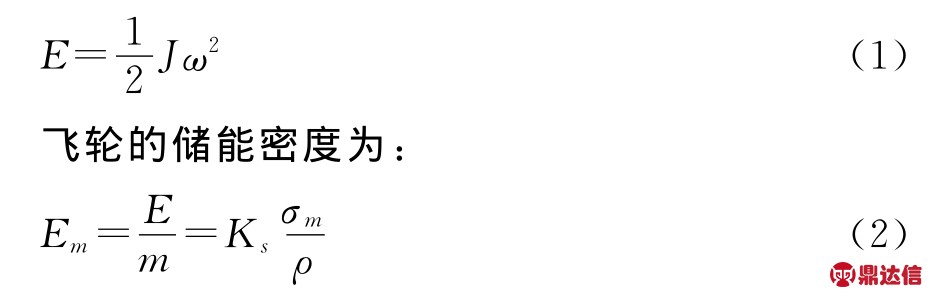
J为飞轮转子轴转动惯量;ω为转子运行角速度;Ks为飞轮的形状系数;σm为飞轮的拉伸强度极限;ρ为飞轮的材料密度。
由式(1)可知,转子的转动惯量和转速决定了飞轮的储能量。提高飞轮的储能量有2个途径:一是增加飞轮的轮缘质量以增大转动惯量,二是提高飞轮的转速。对车载飞轮电池来说,受汽车整体体积和重量的限制,不适合以提高飞轮转动惯量来提高飞轮存储能量;而提高飞轮转速必须要克服飞轮轮缘材料强度约束、轴承发热及摩擦阻力等技术问题。
由式(2)可知,常选用抗拉强度高、密度小的材料来制作飞轮转子,以提高飞轮储能密度。受先进高强纤维的高技术贸易壁垒所限,国内飞轮储能密度的目标是60~80W·h/kg[5]。
由于高转速和高转动惯量的飞轮,其陀螺效应问题不可忽视,因此,其陀螺力矩为:

M为陀螺力矩矢量;ω为飞轮绕惯性主轴旋转的角速度矢量;Ω为基础运动角速度矢量。
2.2 飞轮材料
2.2.1 金属材料
由于金属材料制成的飞轮转速相对较低,存在摩擦损耗大、储能密度低、储能量小、寿命短和体积大等缺陷,且一旦发生故障,破坏性较为严重,因此,逐渐被复合材料所取代。
2.2.2 复合材料
为提高飞轮储能系统的性能,飞轮转子常采用高强度复合材料和高惯量结构,以提高飞轮的极限转速和储能量。常用复合材料的主要性能参数如表1所示。由表1可知,复合材料具有比能量高、比功率大、低密度和高强度等特点,由复合材料制成的飞轮转子线速度达1km/s以上,且存储相同能量的复合材料飞轮几乎要比刚质飞轮轻1个数量级。
表1 几种环形复合材料及钢质飞轮转子的参数
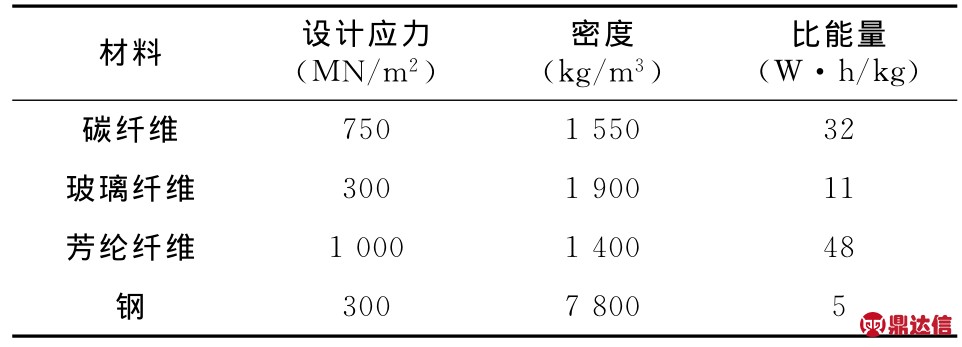
飞轮电池在高转速时的内部应力作用下,易引起转子破裂而失效。在安全防护方面,复合材料制成的飞轮在发生破裂时,造成的事故较小。
2.2.3 飞轮转子的制作工艺
飞轮本体强度不仅与材料强度有关,也与飞轮的制造方法有关。由于高强度复合材料显著的各向异性,导致纤维复合材料缠绕成的飞轮径向抗拉强度低而发生层间脱裂,为使复合材料飞轮储能量更高,必须采用特殊的制作工艺,以克服复合材料的脱层现象。研究表明,多环转子的储能密度远远大于单环飞轮转子的储能密度,且多层复合材料飞轮采用过盈配合,可提高转子的极限角速度,增加储能量,减少了转子重量。
2.3 支撑装置
2.3.1 车载飞轮电池的振动
汽车在行驶时,汽车振动影响车载飞轮电池的稳定运行。考虑车身质心比车身其他地方振动相对较小,因此,常将飞轮电池加载在汽车车身质心上。
由于加工误差使飞轮转子存在不平衡量,当飞轮超高速旋转时引起飞轮振动,同时飞轮转子在临界转速附近运行时振动较大。在车载飞轮电池的振动工程中,针对以上振动的减振措施为:转子动平衡、快速越过临界转速和添加阻尼器等方法。由于汽车振动是多个自由度的振动,磁悬浮转子也将产生多个自由度的振动。而转子的振动激励来源于定子,汽车振动将激励传于定子,定子发生振动,影响转子振动。
2.3.2 轴承支撑技术
轴承除承受飞轮转子自身重量外,还承受飞轮重心偏离引起的离心力和高速旋转飞轮产生的陀螺效应力,因此,它关系到飞轮电池的效率和可靠性。常用的支撑装置有机械轴承和磁悬浮轴承。
机械轴承支撑刚度大,存在极限转速低和摩擦发热严重等问题。目前,机械轴承更多地用于保护轴承,对磁轴承起保护作用。
磁悬浮轴承具有高转速、无接触磨损和使用寿命长等特性。但磁轴承的支撑刚度比机械轴承低1~2个数量级。目前,国内外对磁悬浮轴承的研究较多,主要有电磁轴承、超导磁轴承、永磁轴承及其组合式轴承等。
电磁轴承又称主动磁悬浮轴承,其突出优点在于可对转子进行主动控制,实时在线监测转子的状态,抑制转子振动,使转子稳定运行。电磁轴承主要缺点是其电磁损耗大,目前,国内外对主动磁轴承研究多集中在高性能数字控制电磁磁轴承和降低磁轴承损耗方面。
超导磁轴承主要是利用超导体的迈斯纳效应和磁通钉扎效应,实现飞轮电池转子的稳定悬浮,无控制装置,减小了飞轮电池的体积。由于超导磁轴承必须运行在低温下,要求恒温冷却系统,所以整体费用高。高温超导磁轴承摩擦系数可达到3×10-7。
根据Earnshow著名理论,单靠永磁轴承不可能实现稳定悬浮,常将其与其他轴承合成组合支撑装置。永磁轴承与其他轴承的配合使用,不仅能简化系统结构,降低成本,还能提高系统储能效率。
永磁磁悬浮轴承和超导磁悬浮轴承均为全被动磁轴承,目前以两者组合而成的全被动磁悬浮轴承研究最热,但其悬浮性能还不够稳定,结构复杂并且造价过高,还有待更深的研究。
2.4 电动/发电机
2.4.1 感应电机
感应电机是较早用于飞轮储能系统中的一种电机。感应电机调速控制技术比较成熟,具有结构简单、体积小、成本低、运行可靠、转矩脉动小、噪声低、转速极限高和无位置传感器等优点。但感应电机的转速控制范围小,转矩特性不理想,不适合用于频繁启动和加减速的车载飞轮储能系统中。
2.4.2 开关磁阻电机
开关磁阻电机(SRM)的突出优点为可在较宽转速和转矩范围内高效运行,控制灵活,可四象限运行,响应速度快和成本低。实际应用表明,SRM存在着转矩波动和噪声大、电磁性能较差及需要位置检测器等缺点。近年来,一些学者将轴向叠片各向异性转子应用于开关磁阻电机中,使电机的性能得以提高,其在飞轮电池中的应用研究也逐渐增多。
2.4.3 永磁无刷电机
永磁无刷直流电机转子一般选用钕铁硼永磁材料,使得转子在理想状态下没有能耗损耗,且可使电动/发电机的体积和重量大大减小。永磁同步电动机具有效率高,电机的转速容易控制等优点。永磁电机在各种运行条件下都有较高效率,转速高达200000r/min。
2.5 电力电子转换装置
在电机选定情况下,飞轮电池系统的效率与电力电子转换装置密切相关。
电力变换器是飞轮电池中电能和动能转换的桥梁,是控制整个飞轮电池正常工作的核心组成部件,而飞轮电池的寿命也主要取决于其电力电子器件的寿命。电力电子装置通常是由FET或IGBT组成的双相逆变器和控制电路,它决定了飞轮电池能量的输入输出,而与储能装置外界负载的性质无关。电力变换器是通过控制电动/发电机,实现电能与机械能的相互转换,具有调频、整流和恒压等功能。
2.6 真空室
真空室的主要作用有2个:一是提供真空环境以降低风损,二是屏蔽事故。真空度对系统效率起主要的决定作用,目前国际上真空度一般可达10-5 Pa量级。
英国研究人员用低速运转试验证实:氦气环境有利于减小风损,提高真空度虽能降低风损,但因为稀薄气体环境散热功能减弱,飞轮本体温升较高。
3 国内外车载飞轮电池的研究现状
3.1 飞轮转子技术现状
Active Power公司的240kW/0.8kW·h,Vycon公司的140kW/0.58kW·h和Pentadyne公司的120kW/0.67kW·h的飞轮储能电池,均为大质量金属转子的快速充放电系统。
2011年,Beacon Power公司在纽约Stephen镇完成的世界上最大飞轮储能系统20MW的安装运营,采用世界上最先进的碳纤维复合飞轮转子技术,吸收并释放1MW的电能仅需15min[6]。
2010年,美国波音公司设计的飞轮转子,其复合材料主体部分根据回转受力的不同,采用了3层复合材料装配而成,每层应用不同规格的碳纤维,并用不同的缠绕方式缠绕装配,提高了飞轮的整体强度以及材料的利用率[7]。
北京航空航天大学用于姿态控制和能量存储的飞轮储能系统,采用三环交接的高速碳纤维转子结构,设计的运行转速为50000r/min,储能密度高达36.1W·h/kg[8]。
2008年6月,清华大学工程物理系储能飞轮实验室,对复合材料环向缠绕的高储能密度飞轮转子进行强度试验,达到实验极限转速为54300r/min,轮缘线速度为796m/s,储能密度为48W·h/kg[9]。
3.2 车载飞轮储能支撑装置的研究现状
3.2.1 减小陀螺效应的研究措施
针对飞轮电池高速运转下陀螺效应问题,国内外学者提出了微分交叉反馈解耦控制、比例交叉反馈补偿控制等方法有效地抑制飞轮陀螺效应问题。参考文献[10]提出了一种三轴正交支撑系统,飞轮与支撑环架构成了三自由度系统,使飞轮电池能在以支撑环架中心为圆心的球面内做相对运动,以消除汽车非直线运动时产生的陀螺力矩,非常适合在电动汽车中应用。
为保证飞轮电池的安全运行,在设计车载飞轮储能系统时,常根据汽车经常行驶时的振动特性来合理确定飞轮转子和轴承的安放位置。对于行驶条件是迂回曲折道路的车辆,应尽量避免飞轮轴与地面平行的安置方式;对于行驶条件是起伏不平道路的车辆,应尽量避免采用飞轮轴与地面垂直的安置方式。
3.2.2 车载飞轮电池的轴承技术现状
美国TSI公司研制的基于真空罩的超低损耗机械轴承,摩擦系数只有0.00001[11]。
韩国电力公司研究所开发的35kW·h的超导飞轮储能系统采用由1个高温超导磁轴承,1个角接触球轴承和1个主动电磁阻尼器组成的径向混合轴承套,飞轮最大运行速度为12000r/min。
参考文献[12]以城市轻轨刹车动能再生为背景,研制的20kW/1kW·h的飞轮储能系统采用永磁轴承,卸载约80%的转子重量,大幅度降低摩擦损耗,径向采用滚珠轴承,飞轮设计工转为13500~27000r/min。参考文献[13]采用机械轴承与永磁轴承相结合的支撑形式,省去复杂的电磁轴承以及相关控制部分,飞轮材料为普通碳钢,可实现飞轮在较高转速30000r/min下的稳定旋转,飞轮的效率为85%~95%。
3.3 电动/发电机技术现状
目前,国内外研究较多的电机为永磁无刷电机。从减小电机损耗和提高电机效率出发,参考文献[14]设计了用于飞轮储能系统的高速永磁同步电机,电机功率为30kW,转速为96000r/min。Sychrony公司可生产100kW,60000r/min和400 kW,20000r/min的磁悬浮高速永磁电动机和发电机[5]。
沈阳工业大学、南京航空航天大学及浙江大学合作,研制了磁悬浮轴承支撑的75kW,60000r/min高速永磁电动/发电机试验样机。
3.4 电力电子转换技术现状
参考文献[15]针对电动汽车制动过程中能量损耗问题,采用AC-DC-AC的两级拓扑结构实现电动汽车交流电网、直流母线和飞轮储能系统之间能量传递。
美国BeaconPower公司采用脉冲调制转换器,实现从直流母线到三相变频交流的双向能量转换,飞轮系统具有稳速、恒压功能。Maryland大学开发的“敏捷微处理器电力转换系统”,当飞轮处于充电状态时,其功能为电动机控制器,而飞轮处于放电状态时,其功能为交流转换器。
一些学者也提出将矩阵变换器、PWM变换器和三电平逆变器应用于飞轮电池系统。
电力电子转换装置可以通过再生能量利用,有效地减小了汽车的摩擦损耗,提高汽车整体能量的利用率,增加汽车的行驶里程。研究显示,埃德蒙顿巴士采用飞轮电池可以将每百公里的平均燃油消耗从141.746L降低到104.834L[16]。
参考文献[17]的研究表明,一辆装有3个飞轮电池装置的卡车可以吸收30%的再生制动能量。
广州地铁4号线的制动能-飞轮储能再生模型分析表明,一年可回收292万kW·h[5]。
4 车载飞轮电池的关键技术展望
随着当前电力电子、控制和材料等技术的快速发展,未来新一代的车载飞轮电池必将取代现在的车载飞轮电池。未来飞轮电池关键技术的发展方向及研究热点如下:
a.飞轮转子材料决定飞轮的储能密度。芳纶纤维的理论能量密度可达306W·h/kg,由于技术原因,目前只能达到134W·h/kg,还有很大的潜力。因此开发新型转子材料,改善飞轮转子结构,提高飞轮转子的储能密度已迫在眉睫。近年来出现的应用三维编织技术制作飞轮转子,可有效改善飞轮转子的综合力学性能,有望成为复合材料飞轮加工的主流。
b.寻求新的控制算法或研发新的转子支撑装置,既能简化支撑系统的结构,又能抑制转子的振动,同时最小化飞轮转子的陀螺效应。
c.对电动/发电机来说,高转速、低损耗和高效率是目前电机发展的重点。近年来兴起的无轴承电机结合了磁轴承与电机的双重优点,在超高速旋转方面具有较高的优势,是未来车载飞轮电池理想电机选择之一。
d.电力电子转换装置与飞轮电池整体效率有很大关系。改善电力电子转换装置,提高其效率,有利于提高对车载飞轮电池整体效率,同时提高汽车刹车制动能量的利用。
5 结束语
当前世界性的能源和环境问题愈显突出,汽车的使用是引起这些问题的重要因素之一。电动汽车被认为是高效且符合零排放标准的可用技术。当前,电力电子、控制和材料等技术的快速发展,为电动汽车的研发提供了有力的技术支撑。车载飞轮电池是一种新型“绿色电池”。随着相关技术的发展,车载飞轮电池必将在电动汽车上获得重大发展。