摘 要: 针对空洞层上硅工艺在制作高质量的单晶硅感压膜和真空密封腔上的优势,提出了将其应用于制作电容式绝对压力传感器。应用板壳理论建立了传感器压力检测的理论膜型,对传感器的感压膜进行理论计算和有限元仿真,并利用电容变化模型分析了传感器的灵敏度。给出了基于Pcap01芯片的微电容检测系统的设计,对于半径为100 μm,厚度为1.7 μm的圆形感压膜,初始电容值为0.278 pF,传感器灵敏度为0.86 fF/kPa。
关键词: 空洞层上硅; 电容式; 绝对压力传感器; 有限元仿真
0 引 言
硅微压力传感器中电容式压力传感器具有高灵敏度、能耗低、温度漂移小、信噪比高、响应速度快等优点而广泛使用[1~3]。
在常见微机电系统(micro-electro-mechanical system,MEMS)器件中常用的气密性封装主要是在高真空度(小于0.01 Pa)环境下的阳极键合、共晶键合以及薄膜密封工艺等[4]。阳极键合一般应用于硅—玻璃键合,需要高温、高压环境,使其应用受到较大的限制[5]。共晶键合是采用金属作为过渡层而实现硅—硅键合的一种间接手段,但其密封的效果不佳[6]。薄膜密封技术利用牺牲层方法刻蚀出空腔结构,在真空环境下,薄膜沉积在小孔密封处,完成真空密封,但空腔的真空度受到沉积工艺的限制,同时沉积时的高温环境、薄膜封孔刻蚀工艺也会影响该方法在器件中的应用。常用的电极线引出采用的是基于互补金属氧化物半导体(complementary metal-oxide-semiconductor,CMOS)标准的牺牲层释放工艺来腐蚀掉上下电极之间的氧化物从而引出电极线,但是此种方法受到释放孔尺寸和间距小的限制,容易造成金属引线被损坏[7]。还有一种采用Cr/Au双层金属引线,Cr作为Au的增粘阻挡层,但在深腔结构中,Cr/Au引线容易断裂,同时还会出现Au向Cr中扩散的现象[8]。
Jurczak M等人[9]提出一种将沟道区制备在空洞层上的器件结构,即空洞层上硅(silicon on nothing,SON),日本的Sato T等人提出一种基于硅微结构变换的技术来制备SON器件,通过该技术,可以精确定位形成硅层中的空洞。当ESS连在一起时,形成SON结构。
基于加工工艺简单、提高传感器灵敏度等因素考虑,本文在前期研究的基础上[10],采用的SON工艺为电容式绝对压力传感器的制备提供了一个内嵌的真空腔和可控厚度的感压膜结构。文中首先详细介绍了电容式绝对压力传感器的结构组成和原理,利用板壳理论分析了感压膜的受力变形情况,并用有限元ANSYS对理论计算结果进行分析,同时简单介绍了SON工艺制备压力传感器的流程,最后给出了传感器微小电容的测量方案和测试结果。
1 传感器工作原理
传感器结构示意图如图1所示,上部为固定不动的上极板,下部为利用SON工艺构造形成的感压膜下极板,绝对压力真空腔位于感压膜的下方。
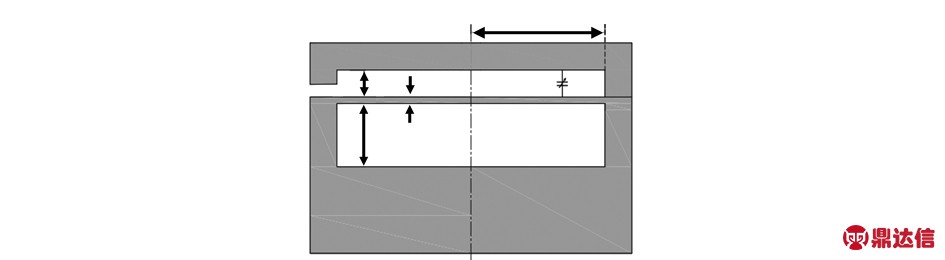
图1 电容式绝对压力传感器结构示意
当感压膜极板受到外界压力的作用时,感压膜将发生形变,上下电极之间的距离会发生变化,导致传感器输出电容值的变化,从而完成了电容信号与压力信号之间的转换,最后通过微电容检测电路对传感器输出电容值进行测量。r为圆形膜片上任意一点与膜片圆心的距离,Cm为感压膜膜和电极之间的电容,g为感压膜和电极之间的距离,感压膜厚度为t,真空腔的高度为d。
弹性力学膜片理论是传感器薄膜结构力学分析的主要方法,基于膜片的物理方程可以求解薄膜在外力作用的形变和应力分布
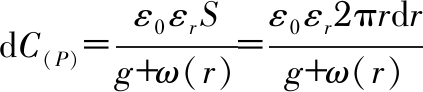
(1)
式中 ω(0)为感压膜的中心挠度,对于圆形感压膜的最大挠度小于膜片的厚度的1/2时,感压膜的变形为小挠度变形。在小挠度的理论中,可以忽略感压膜内的应力对膜的影响,由板壳理论可知[11],小挠度变形方程如下
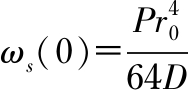
(2)
当挠度大于膜厚的1/2时,中面将发生很大的变形,则其中的应力就不能忽略不计。采用最小能量原理求得
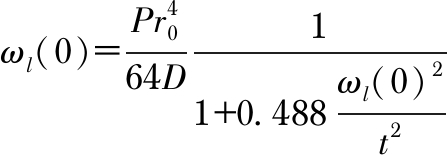
(3)

(4)
式中 D为硅的抗弯曲刚度,E为硅的杨氏模量,ν为泊松比。所以r→r+dr部分的圆环的面积为
S=π(r+dr)2-πr2=2πrdr+πdr2≈2πrdr
(5)
其与上极板组成的电容传感器的容量为
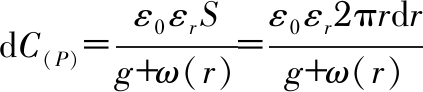
(6)
整个感压膜与上极板所组成的电容,可看作是dC(P)的并联,所以,电容式绝对压力传感器的计算公式为
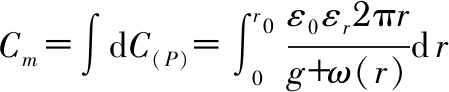
(7)
式中 ω(r)为感压膜任意位置的挠度,ε0为真空的介电常数,εr为空气的相对介电常数。
2 传感器模型的计算与仿真
2.1 感压膜弹性膜片的设计
在0~120 kPa的压力范围下,在相同的尺寸下对小挠度与大挠度理论模型的中心挠度进行计算,计算中单晶硅的弹性模量E取1.65×1011Pa,泊松比ν为0.22,当感压膜半径为100 μm,膜厚为2 μm时,由感压膜的中心形变与压力的关系可知随着外界压力的增加,小挠度模型与大挠度模型下的中心挠度大小的偏差也越大。随着感压膜的半径增大,大挠度模型与小挠度模型的偏差也越大。说明在感压膜半径一定的情况下,小挠度模型只适用于较低的气压范围。
采用SON构造工艺条件的约束下,真腔的高度会受到限制,所以,在受到一定的压力作用下会导致感压膜与真空腔底部发生接触时而导致传感器的失效,为了防止出现类似的情况,在一定的腔体高度和一定的压力范围内,对感压膜采用最大不接触半径对此感压膜的最大挠度进行限制。
由式(3)与式(4)可得小挠度与大挠度模型下的最大不接触半径分别如下

(8)
对上式中的压力采用量程范围内的最大压力P=120 kPa,分别计算d=2 μm与d=4 μm时大挠度与小挠度的曲线,可知,当感压膜的厚度较小时,大挠度的最大不接触半径高于小挠度模型,随着感压膜厚度t的增加,最大不接触半径也随着增加,同时这两种模型的差距也越来越小。从传感器的灵敏度考虑,感压膜的厚度不能制作的太大,故传感器应采用大挠度模型来计算输出的电容值。
根据有限元仿真的求解步骤,在ANSYS 中首先建立半径为r0=100 μm,厚度t=2 μm的几何模型。选择Stastic Structual模块,材料为单晶硅,弹性模量E=1.65×1011Pa,泊松比ν=0.22,感压膜四周固支,在其上表面施加均匀压力载荷,同时开启大形变分析进行仿真。在120 kPa压力作用下的应变云图,可知,感压膜的最大形变量发生在中心部分,边缘部分的变形量最小。
图2给出了膜的中心最大挠度随压力变化的理论计算模型与有限元仿真模型的对比,由图可知0~120 kPa的均匀载荷作用下膜线性形变,传感器具有良好的线性度。
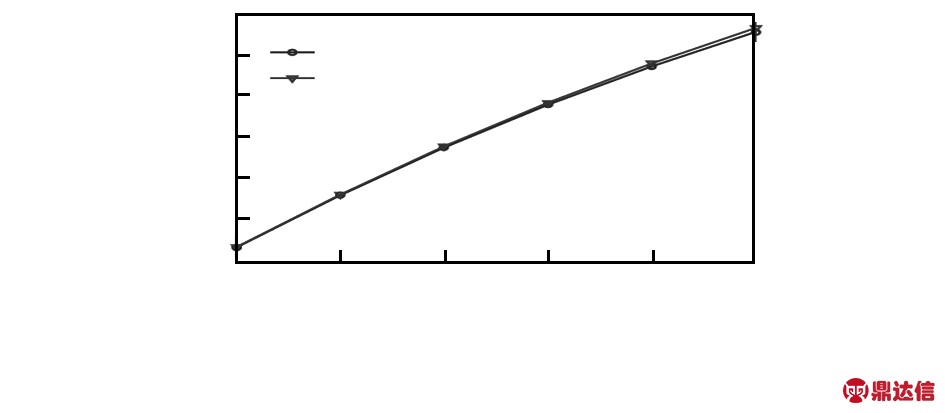
图2 感压膜中心挠度随压力的变化结果
2.2 传感器灵敏度分析
由变间距式电容式压力传感器的表达式(7)可知,其输入输出具有非线性,灵敏度通常是在一个较小的区间用拟合直线的斜率来表示。定义膜片中心最大挠度ω(r)=d的最大压力为Pm,则可得
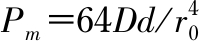
(9)
记r/r0=y,则d r=r0d y,可得膜的挠度公式为

(10)
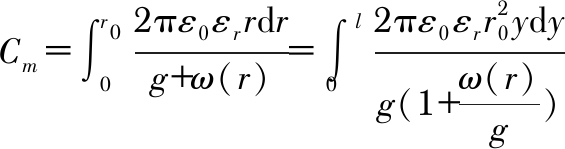
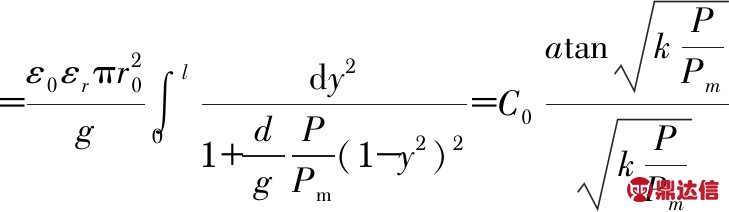
(11)
式中定义电容式压力传感器的灵敏度为
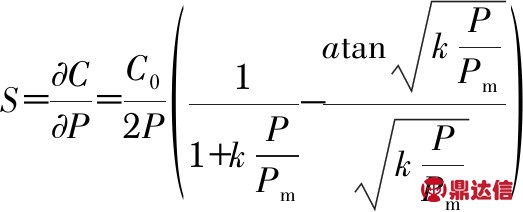
(12)
其中当P=0时,传感器灵敏度为

(13)
由式(13)可知,对传感器灵敏度影响最大的是感压膜的半径r0,其次是膜的厚度t,及膜和电极距离g。基于SON退火加工的工艺,选取了一些传感器的尺寸参数进行优化,传感器的量程选择为0~120 kPa的气压范围,感压膜和电极之间的距离g=1 μm,膜的半径为r0=100 μm,膜厚t分别选取1~3.5 μm,计算在不同的尺寸下传感器的电容输出值,如图3所示。
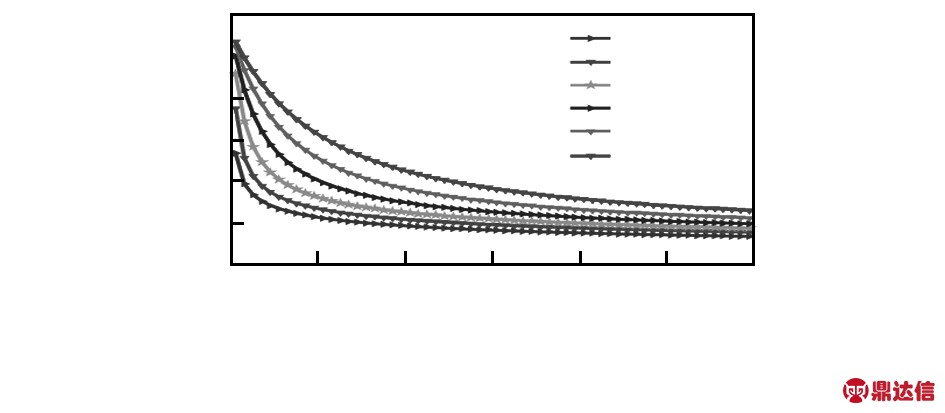
图3 在感压膜半径r0=100 μm,g=1 μm下的电容输出变化量与压力之间的关系
由图3可知,随着压力的增加,传感器输出电容值减小;随着感压膜的膜厚度增加,传感器非线性误差减小但同时其灵敏度也会减小。在其他参数不变的条件下,如果改变感压膜的半径,感压膜的半径从50~300 μm的范围变化时,感压膜的半径越大,传感器输出电容值也越大,灵敏度也越大,但传感器同时会带来较大的非线性误差,这与式(13)的分析结果是一致的。
通过以上分析可知,为了提高电容式压力传感器的灵敏度以及初始输出电容值,需要尽量减小电容传感器的初始间距g,但同时减小g会带来传感器非线性误差的增加,为了保证传感器的线性度,应当限制感压膜的最大挠度,对于本模型最有效的方法增加膜的厚度或采用较小半径的感压膜。综上考虑,为了传感器能够获得较大的信号输出,同时改善传感器的非线性误差,将采用传感器阵列的方式。
3 传感器的制作
传感器的制作流程如图4所示,传感器的SON部分采用的是低电阻率(0.001 Ω·cm)的单晶硅材料,晶向〈100〉、表面抛光。
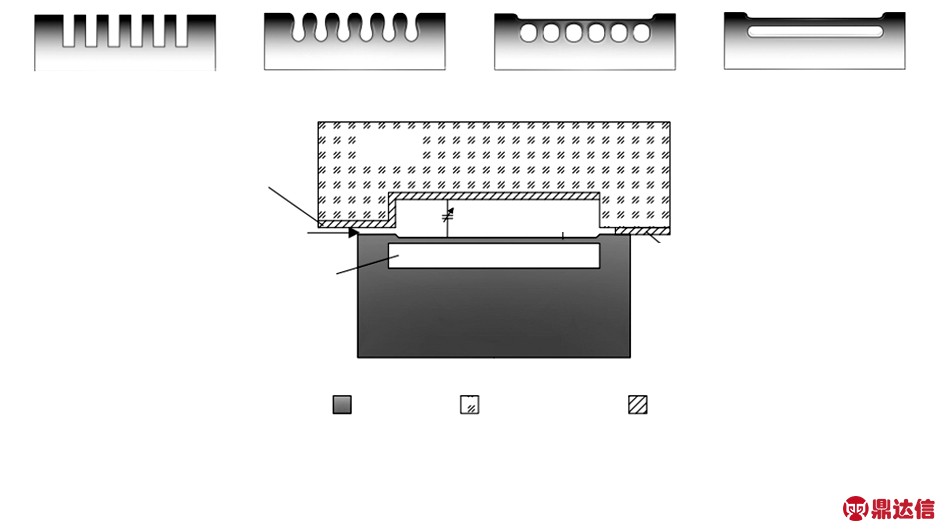
图4 电容式绝压传感器的SON工艺流程
采用 深反应离子刻蚀(deep reactive ion etching,DRIE)工艺在单晶硅衬底上刻蚀等宽的深沟槽阵列(图4(a)),将刻蚀好的硅晶圆衬底在1 100 ℃、氢气、60Torr的环境下进行退火处理(12 min),沟槽上端的硅原子将发生迁移,使得沟槽表面能量最小化。此时,沟槽上的导角开始变圆(图4(b)),之后硅沟槽开始慢慢封闭并形成内嵌真空腔(图4(c)),两边的沟槽深宽比达到一定比例时,沟槽上端的硅原子迁移将使沟槽上端形成完整的硅层,沟槽下端则形成完整的硅层(图4(d)),沟槽下端则留下ESS层(硅层中的空洞),继而形成一个内部带有真空腔的圆孔感压膜的SON结构。在玻璃基底上溅射Ti/Au,并刻蚀出电极,通过静电键合的方法将玻璃电极与SON结构键合,形成最终的电容式绝对压力传感器的结构,并实现了Ti/Au下电极在SON结构上的转移,如图4(e)所示。
4 电容检测系统的设计与测试结果
为了达到压力传感的效果,微小电容检测电路是电容式压力传感器的重要的组成部分。
微小电容的测量方案采用德国ACAM公司的通用电容检测芯片Pcap0l。其测量原理是将传感器的输出电容和参考电容一同连接到芯片内同一个放电电阻,构成一个低通滤波电路,电容被充电到电源电压,然后通过电阻放电到一个可控制阈值电压水平的时间会被芯片内部极高精度的时间芯片数字转换器(time chip digital converter,TDC)记录下来,该芯片测量时间精度能达到μs级[12]。放电时间与传感器的电容值与参考电容的比值关系如下
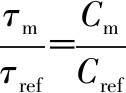
(15)
式中 τm为传感器的放电时间,τref为参考电容的放电时间,Cm为传感器输出电容,Cref为参考电容。芯片的测量精度可以达到fF级,能够满足高精度的微小电容的测量要求。
基于PACPA01芯片与STM32最小系统设计的电容式压力传感器的测试系统如图5所示。选取47 pF的陶瓷电容作为PCAP01芯片最小系统的参考电容。STM32单片机模块通过IIC与PCAP01芯片通信,并将获得的数据打包通过串口发送至上位机模块。该系统无需再进行外部的A/D转换就可以将测量的电容值数据传送至上位机进行处理。
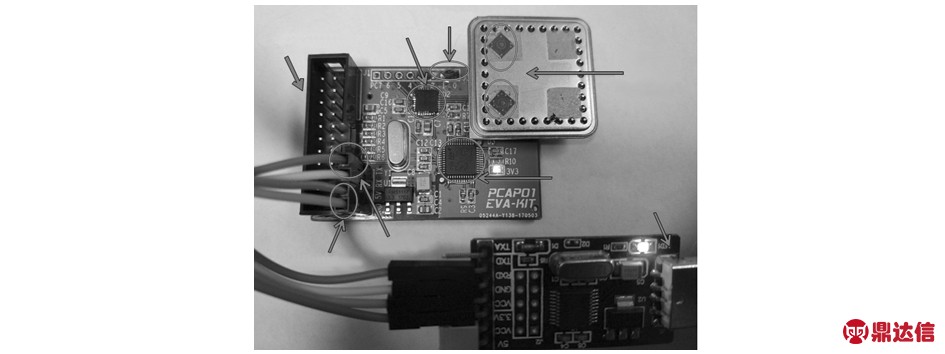
图5 压力传感器的电容检测系统硬件连接实物
对半径为r0=100 μm,t=1.7 μm,g=1 μm的压力传感器进行测试,测试结果与理论计算结果如图6(a)所示,由测试结果可知,该传感器初始电容值为0.278 pF,传感器灵敏度0.86 fF/kPa。若采用传感器采用2×2及3×3的阵列形式,每个电容的结构及尺寸完全相同,每个阵列内的电容之间采用并联的方式进行连接。测试结果如图6(b)所示,采用4个电容并联后整体的灵敏度为3.46 fF/kPa, 9只电容器并联后的整体的灵敏度为7.75 fF/kPa。由前所述,采用较大半径的感压膜,虽然灵敏度增加,但同时传感器会带来非线性误差的增加,若传感器利用SON构造与集成的优势,在相同大小的硅片上同时集成几种相同类型与尺寸的传感器,制成一种阵列的方式可以有效提高传感器整体的性能。
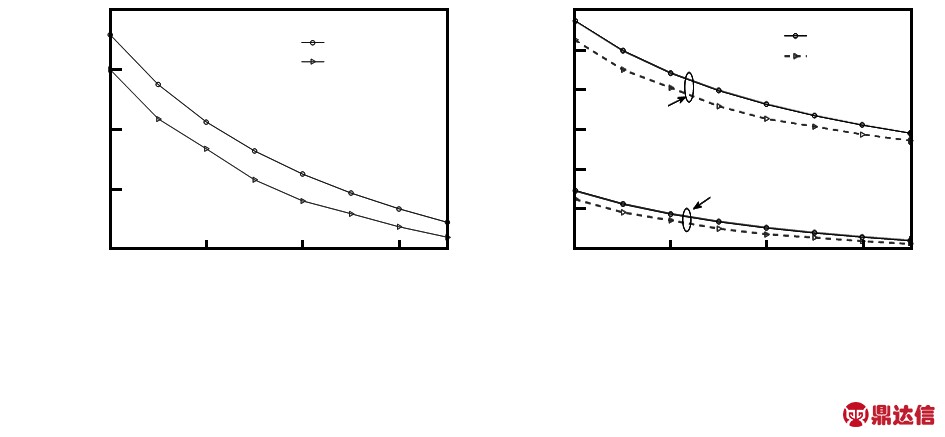
图6 测试结果
5 结 论
本文对电容式绝对压力传感器进行研究,采用大挠度模型对传感器的结构进行计算,并通过ANSYS仿真了感压膜的负载—形变情况,二者有非常一致的结果;用MEMS工艺加工基于SON构造电容压力传感器,无需真空封装工艺,可以实现低应力、长期气密稳定性的电容式绝对压力传感器的制作。最后用高精度的Pcap01芯片对制作的传感器进行性能测试,实验表明:对于半径为100 μm,膜厚为1.7 μm的圆形感压膜,在30~100 kPa的压力范围内传感器灵敏度为0.86 fF/kPa,如果实现阵列形式可以实现更高的灵敏度,并且可以高度稳定、可靠工作。该传感器可以应用于气象监测、智能手机和可穿戴式设备等领域。