摘要:为了评估随机振动载荷下减压阀的安全可靠性,在减压阀振动机制分析基础上,利用有限元分析软件Workbench建立某天然气分输站RMG530减压阀阀体有限元模型,根据现场测得的随机振动载荷对减压阀进行振动响应分析,获得响应功率谱密度,最后依据修正获得的减压阀材料S-N曲线,应用有限元疲劳分析软件NCode,通过时域和频域方法对减压阀进行随机振动疲劳分析,计算阀体关键部位的疲劳寿命。结果表明:减压阀结构设计比较保守,振动载荷下最小寿命发生在进口管段到阀座的拐角处,时域疲劳计算最小寿命为41.79 a,频域疲劳计算最小寿命为38.81 a。
关键词::减压阀; 随机振动; 时域; 频域; 疲劳寿命
RMG530减压阀广泛应用于西气东输和陕京线,减压阀振动决定了减压阀的寿命,直接关系着天然气分输系统的运行可靠性。分输减压阀同与之相连结的各种设备构成了一个完整的机械结构系统,减压阀内流体流动规律十分复杂,加之不同程度的冰屑冲击等影响,易加剧减压阀结构的振动,进而加剧疲劳失效[1]。振动疲劳研究涉及结构动力学、疲劳强度理论以及断裂力学等学科,疲劳寿命估算是在载荷时域或频域分析的基础上,借助材料的S-N曲线计算结构疲劳寿命及其分布。冀亚锋等[2]通过理论分析和有限元分析相结合的方法建立了连续管疲劳寿命预测模型,较好地预测连续管的寿命。刘秀全等[3-6]分别采用频域和时域分析的方法进行了隔水管波激振动及波激疲劳分析计算,研究了深水钻井隔水管波激疲劳失效问题。频域方法较时域方法计算效率高,在结构随机振动疲劳有限元计算方面效果明显。Rahman等[7]采用频域分析的方法,应用有限元计算软件对发动机活塞的振动疲劳寿命进行分析。Claudio等[8]针对双向应力载荷下的机械部件,采用频域方法计算机械部件的疲劳寿命。通过试验方法,Whaley等[9]利用不可逆热力学原理研究了振动疲劳过程中的阻尼变化。Willidal等[10]应用高频共振疲劳试验机对铸钢中片状石墨的数量及大小、共晶体尺寸和基体强度同疲劳强度的关系进行研究。Colakoglu等[11]推导了疲劳裂纹萌生寿命与结构阻尼变化的关系。Damir等[12]通过研究建立结构模态参数同材料疲劳破坏行为的关系,提出了一种非破坏性的分析结构疲劳破坏行为的研究方法。RMG530减压阀阀体材料为1.622 0铸钢,具有良好的低温强度、低温韧性,该减压阀振动具有振动幅值小、频率高的特点,疲劳失效没有明显的塑性形变,属于应力疲劳破坏的范畴。目前国内外尚未见公开发表该减压阀的随机振动疲劳寿命的研究成果。笔者介绍减压阀振动产生原因,就某分输站减压阀的实际监测振动响应数据进行分析,得出减压阀随机振动规律;采用workbench建立RMG530减压阀的有限元精细模型,进行热流固耦合作用下的模态分析。
1 减压阀振动机制
分输减压阀同与之相连结的各种设备构成了一个复杂的机械结构系统,由于减压阀抗振性能差同时受阀内流体脉动引起的激振力的作用,系统容易振动。减压阀是弹簧振子调节系统,阀腔充满弹性的理想可压缩气体,天然气分输过程气体受节流孔开度的影响产生气柱脉动,脉动气流作用在敏感元件上会产生随时间变化的激振力,当激振力的激振频率与系统某一部分固有频率相等时就会造成系统共振,倘若系统阻尼不足以抑制激振力作用,系统振动无法及时衰减,造成减压阀持续振动。脉动气流激振频率一般较小,容易与系统固有频率耦合产生共振,激振力振幅大、衰减慢,对系统危害程度较大。
天然气分输过程流体流动过程复杂,受旋涡冲击和节流过程的影响,容易造成减压阀的高频振动[13-16]。减压阀振动现象是流固耦合作用的结果,节流结束后,在壁面的阻挡和摩擦力共同作用下,在阀笼周围形成数量众多的相同旋向的旋涡,阀套的上下运动与旋涡运动相互作用,容易诱发阀套的高频振动。节流过程中流体流速激增,雷诺数由小变大,旋涡频率出现明显的周期性下降,倘若旋涡频率达到系统的固有频率,容易造成阀套的剧烈振动。同时,阀套升程变化控制节流孔的开度,阀套、阀腔附着流交替反复变化,容易引起气流的高频压力脉动,造成减压阀强迫高频振动[17-19]。
以分输站RMG530减压阀为研究对象,利用YE6280动态数据采集分析系统测量获得秦皇岛天然气分输站工况条件下减压阀随机振动加速度时域历程。减压阀的振动形式主要有横向振动和轴向振动,两种形式的振动振幅和频率并不相同,轴向振动频率低,振幅大,危害大;横向振动频率较,振幅小,危害较小。图1所示为减压阀随机振动时域历程,图2为振动加速度功率谱,减压阀主要振动形式为轴向振动,加速度振动幅值与频率跨度较大,最大加速度振幅约为20 m/s2,振动频率为0~300 Hz,频率为10 Hz的加速度功率谱密度最高。
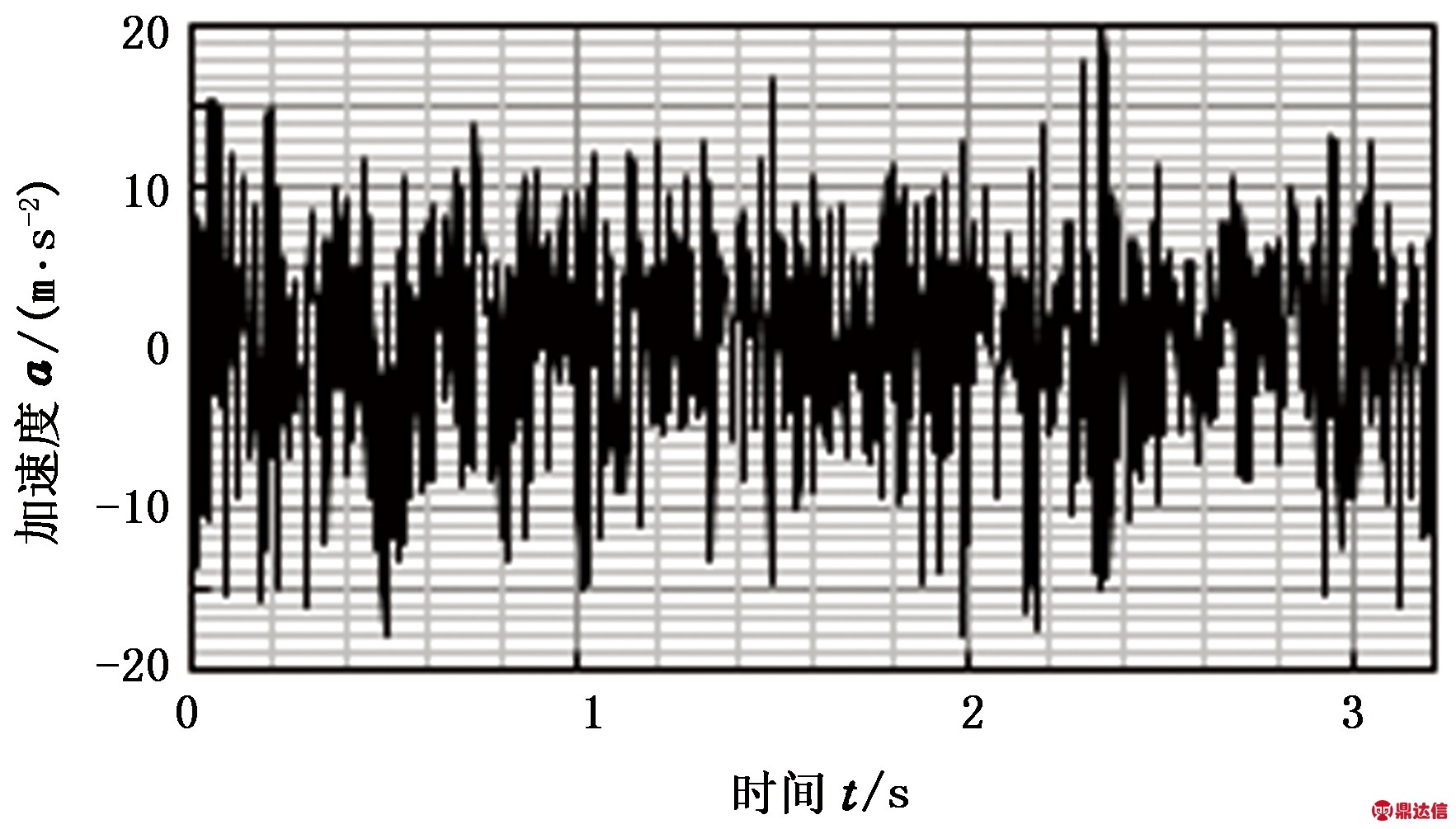
图1 随机振动时域历程
Fig.1 Test results of random vibration acceleration
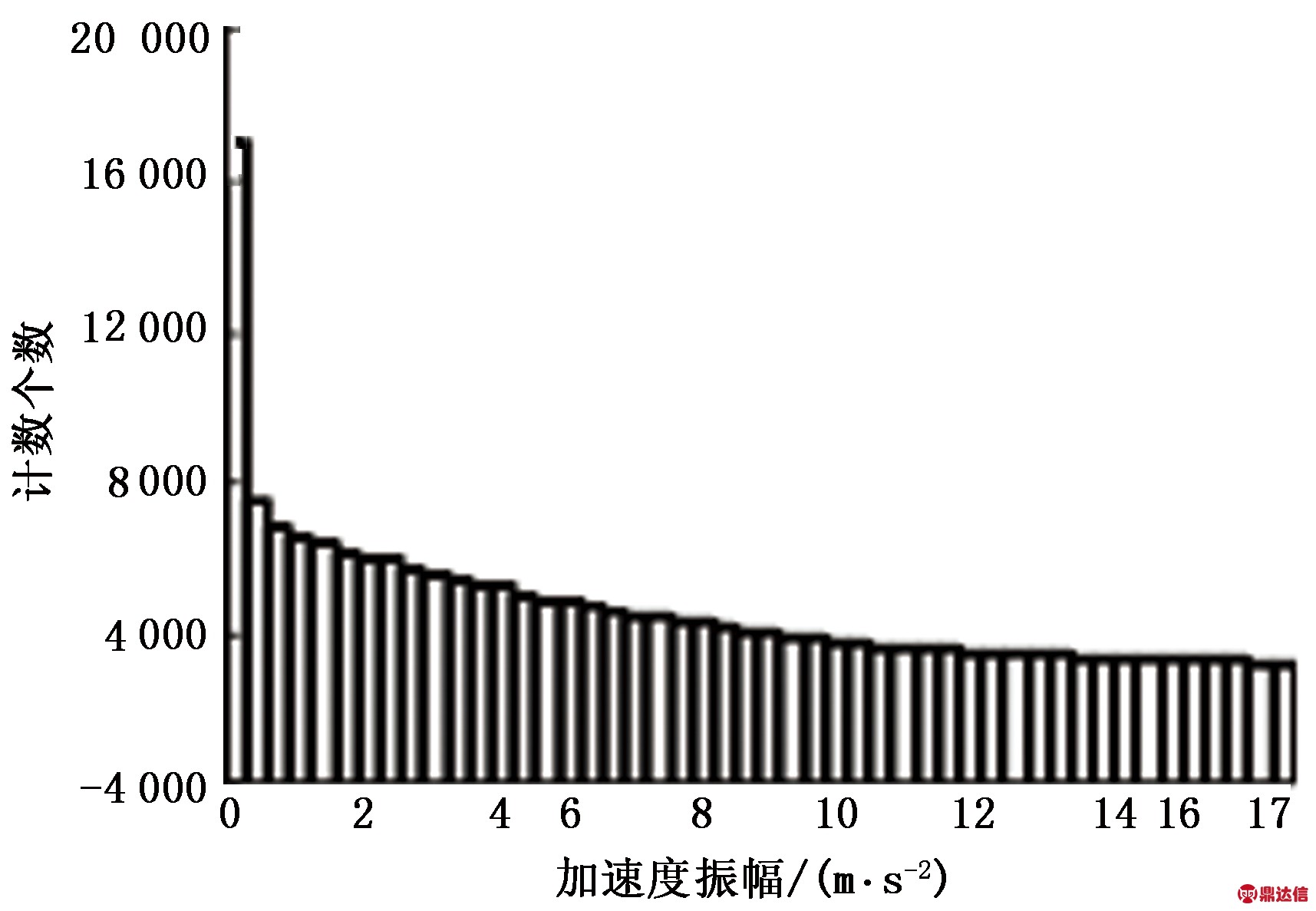
图2 振动加速度功率谱
Fig.2 Vibration acceleration in frequency domain
图3为应用雨流计数法获得的随机振动载荷分析结果。图4为随机振动概率分析结果。
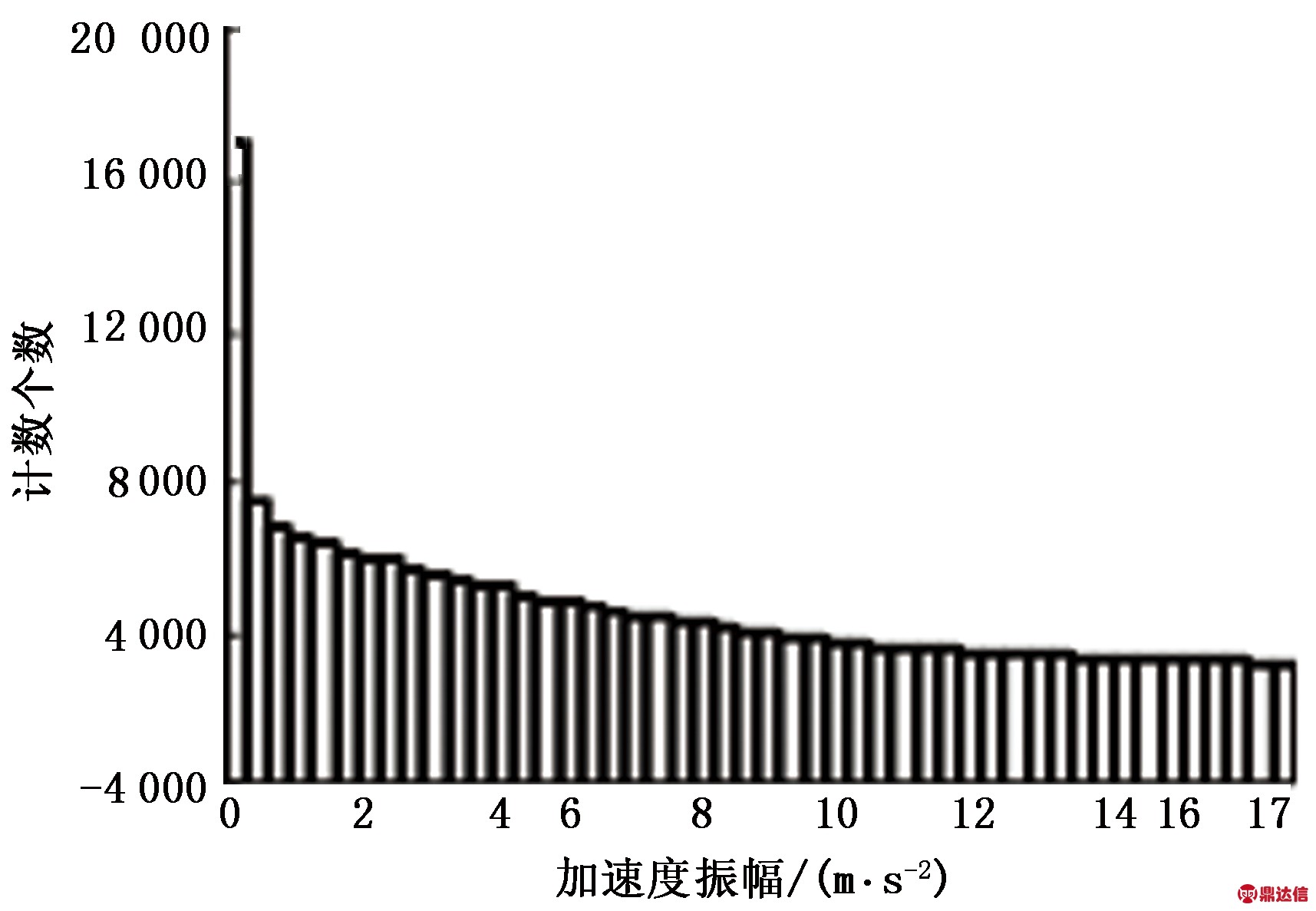
图3 振动载荷雨流法分析
Fig.3 Rain-flow counting of random vibration load cycles
工况条件下加速度振幅变化较大,最小加速度振幅为0.3 m/s2,最大加速度振幅为20 m/s2。1 000 s时间内加速度振幅为0.3 m/s2的振动有17 304次,加速度振幅为10 m/s2的振动有1 148次,加速度振幅为20 m/s2的振动有146次;加速度振幅在0.5 m/s2以内的振动占21.6%,加速度振幅为10 m/s2的振动占1.46%,加速度振幅为20 m/s2的振动只占0.09%。
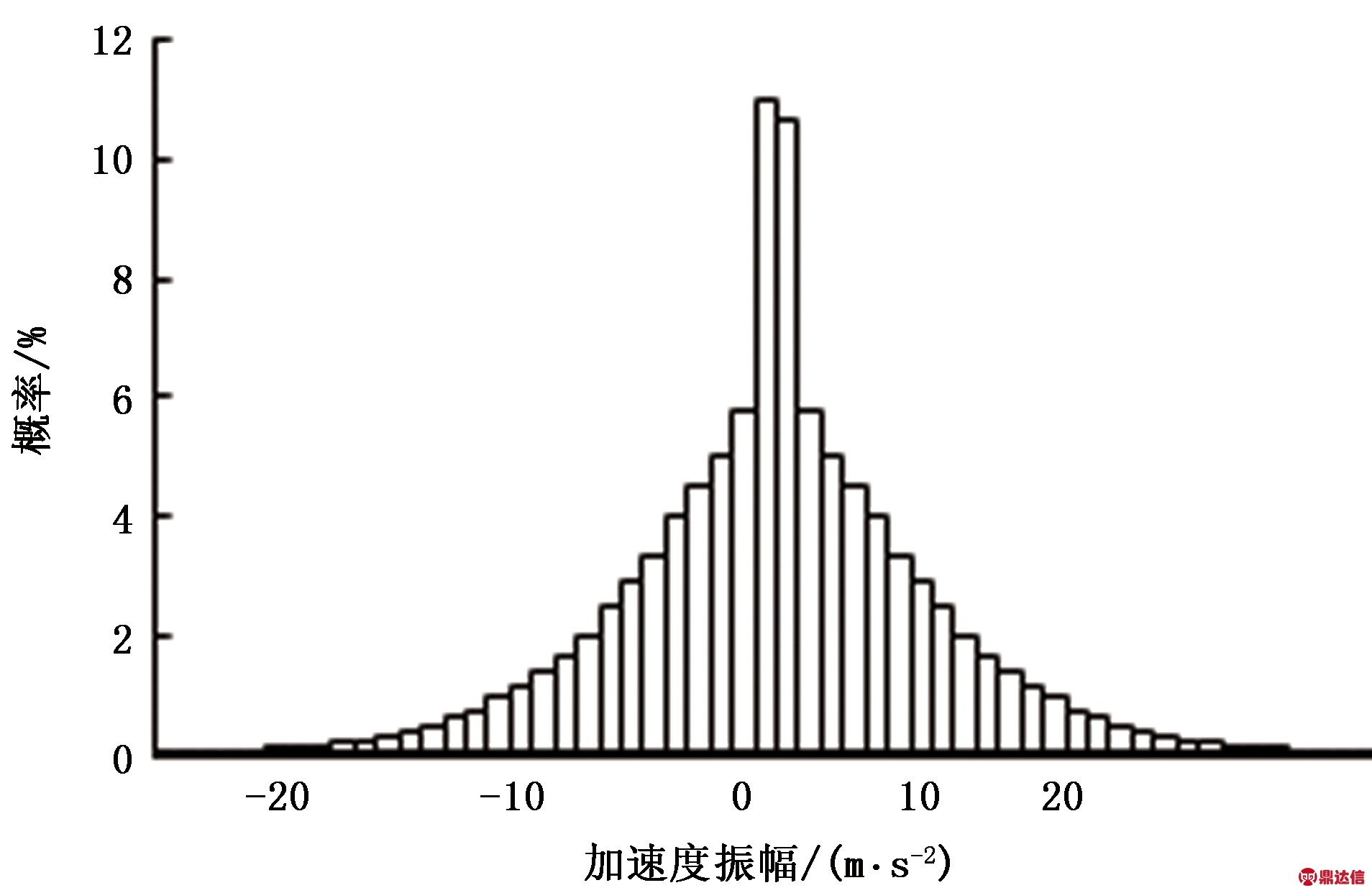
图4 振动载荷概率分析
Fig.4 Probability analysis of random vibration load
2 减压阀模态分析
2.1 减压阀有限元模型建立
根据某天然气分输站RMG530减压阀结构图纸建立等比例阀体模型,减压阀规格为DN150/300,阀体进气端直径为150 mm、出气端直径为300 mm;阀腔内径为380 mm、外径470 mm。上下阀体连接处到下阀体底部高度为600 mm,到上阀体顶部高度为1 100 mm。在Solid Works中建模,利用ICEM对结构进行网格划分,图5为RMG530减压阀几何模型和有限元模型。
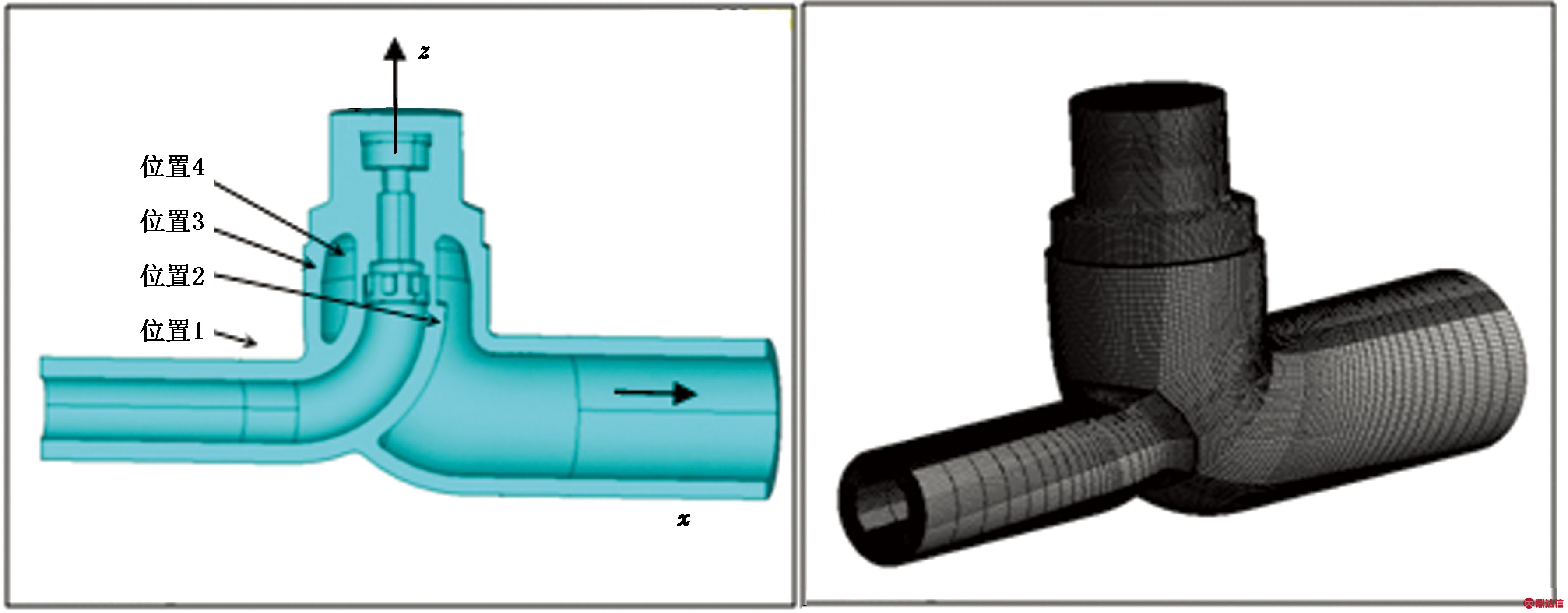
图5 RMG530减压阀几何模型和有限元模型
Fig.5 Geometry model and finite element model of RMG530
2.2 模态分析
模态分析是结构动态响应分析的基础,通过模态分析确定减压阀的固有频率,了解阀体结构对不同方向振动载荷的响应规律。减压阀的振动固有频率本来只与其自身属性和构件特征有关,与外界载荷无关。但当存在温度载荷时,材料性能发生了改变,并且由于热膨胀促使构件存在内部热应力,考虑预应力效应时,固有频率将发生变化。阀体材料为1.622 0铸钢,材料参数为:泊松比μ=0.25,膨胀系数α=1.1×10-5/℃,密度ρ=7 200 kg/m3。材料的弹性模量随温度变化,试验测得低温材料弹性模量的变化规律如图6所示。
模态分析考虑流体压力与温度载荷的影响,图7为入口压力8 MPa,出口压力2 MPa时流体与阀体耦合压力结果。由图7可见,高压腔与低压腔压力载荷较均匀,但阀笼处由于流通面积骤减,流体流通受阻,压力迅速下降。图8为环境温度-10 ℃、加热温度20 ℃时的阀体结构温度场。由图8可见,阀体内部温度分布较均匀,受流体节流温降影响较大的位置温度明显降低,温度最低点出现在阀笼节流孔处,最低温度为-25 ℃。
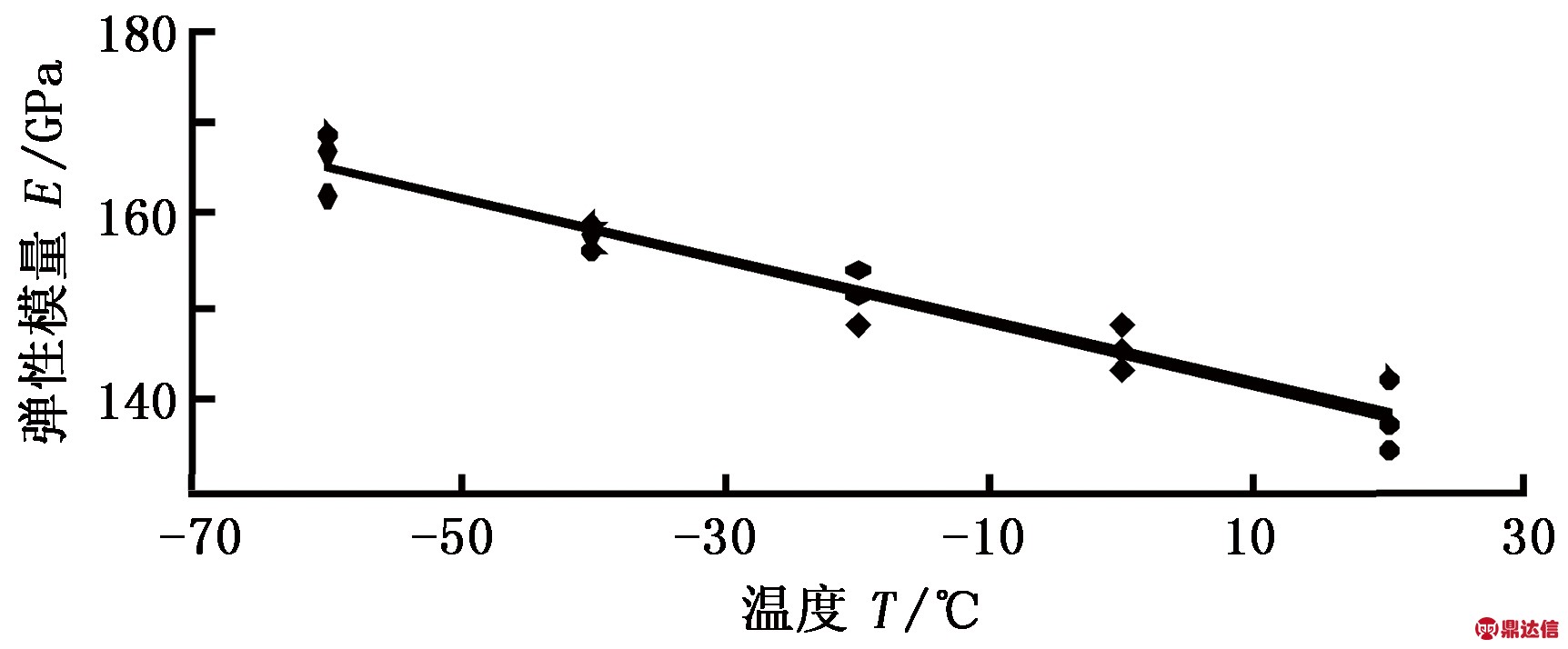
图6 低温下材料弹性模量
Fig.6 Youngs modulus curve at low temperature
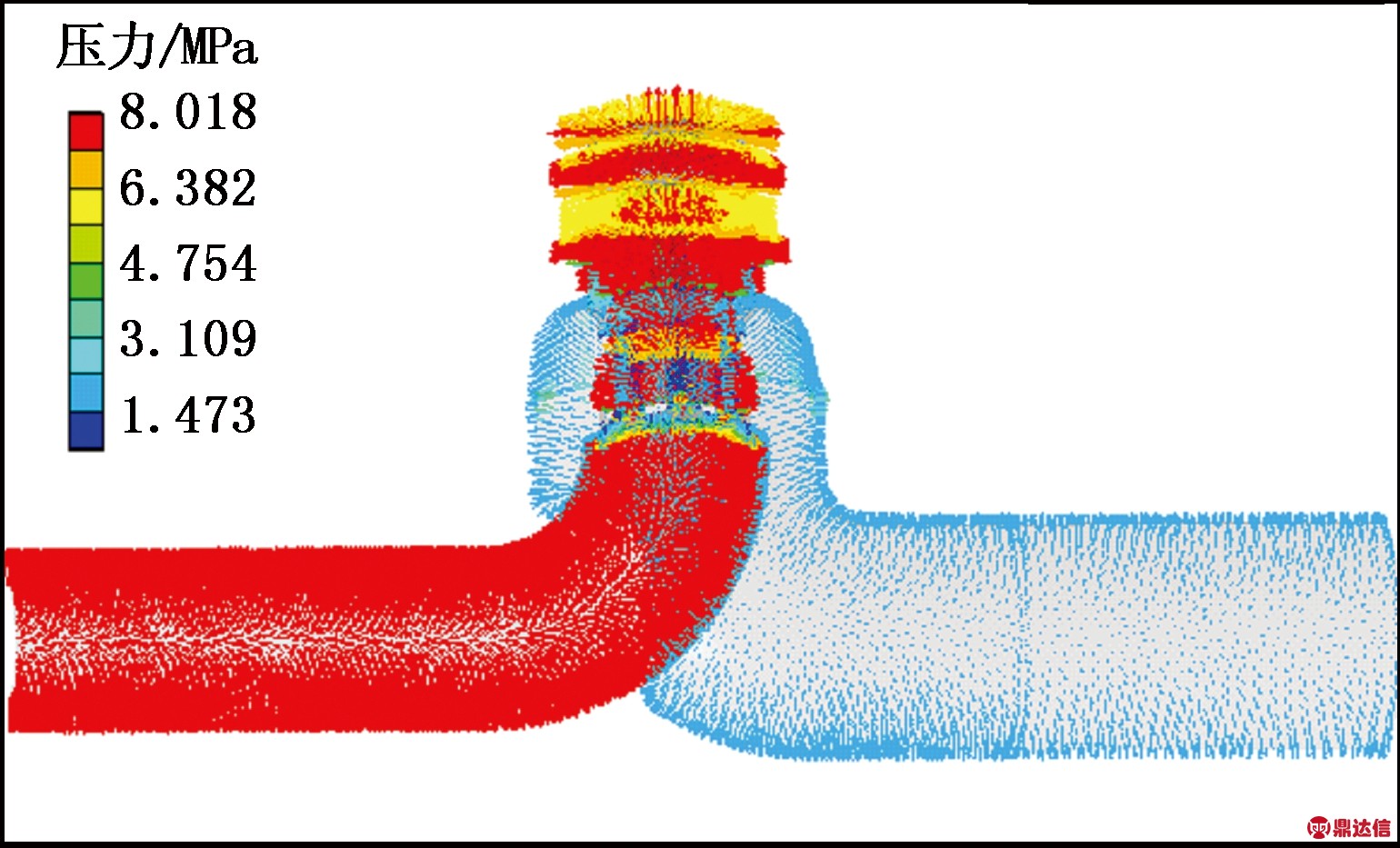
图7 流体压力与阀体的耦合作用
Fig.7 Fluid pressure and coupling effect of value
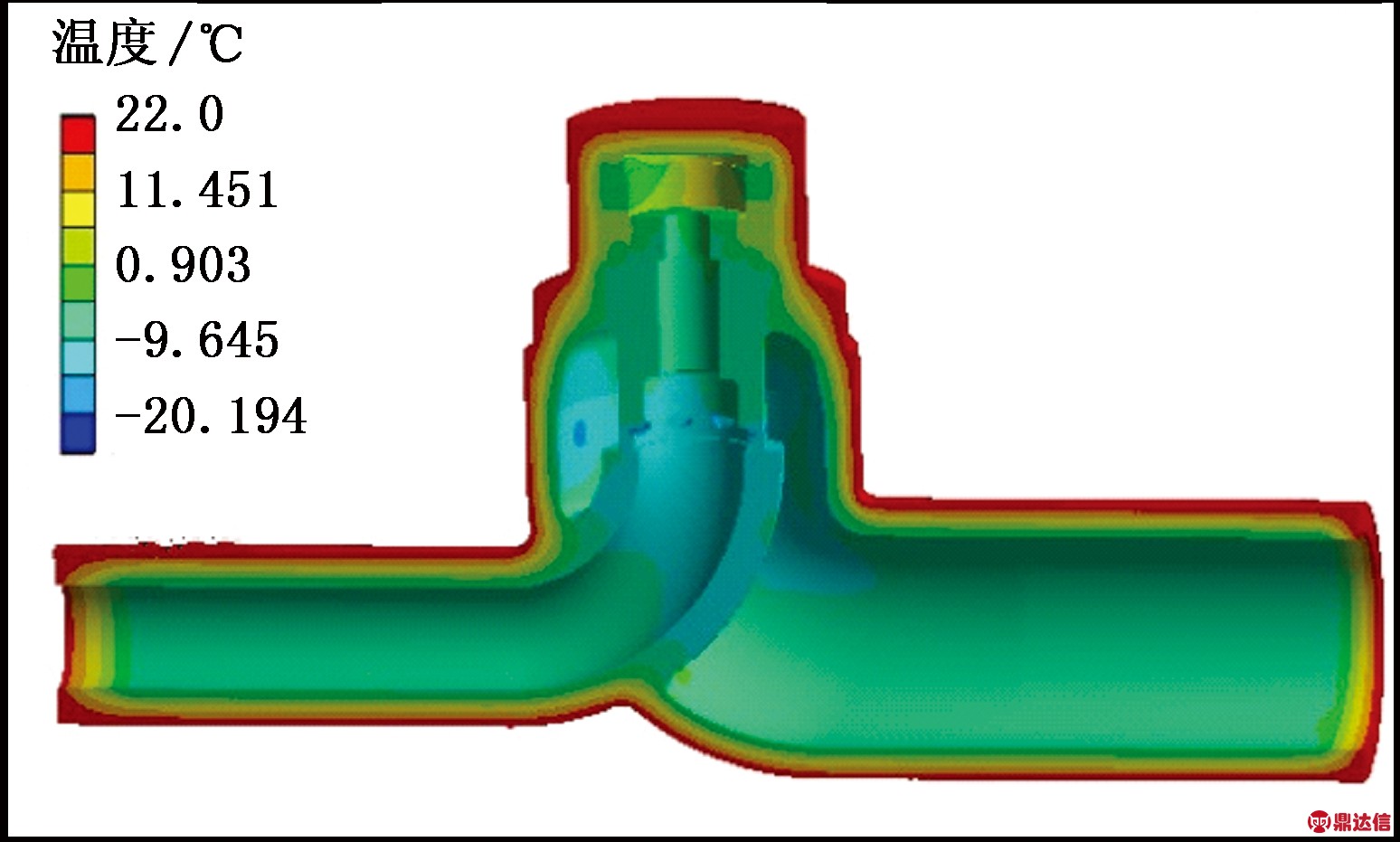
图8 阀体温度载荷
Fig.8 Temperature load of value body
利用Lanzos法计算获得固体重力、流-固耦合作用、热-流-固耦合作用下阀体的前六阶自振频率,频率范围为0~1 300 Hz。减压阀前六阶固有频率计算结果如表1所示。热-流-固耦合作用前六阶固有频率振型如图9所示。数据显示,增加压力载荷,减压阀各阶频率略有增加,但增幅很小。频率增加的原因是流体与壳壁的耦合应力增加了阀体的内部预应力,从而“硬化”了阀体[20-21]。增加热载荷时,各阶频率增长幅度较大,阀体材料的杨氏模量随着温度降低而增大,结构的固有频率也随之升高。同时不均匀温度载荷下,由于材料的热胀冷缩产生较大热应力,使结构进一步“硬化”,固有频率增大[22]。在常温或低温环境下,减压阀的振动固有频率的第一和第二阶都较低,在此频率段有可能引发共振。
表1 减压阀的前六阶固有频率
Table 1 The first six order natural frequency of valve body Hz
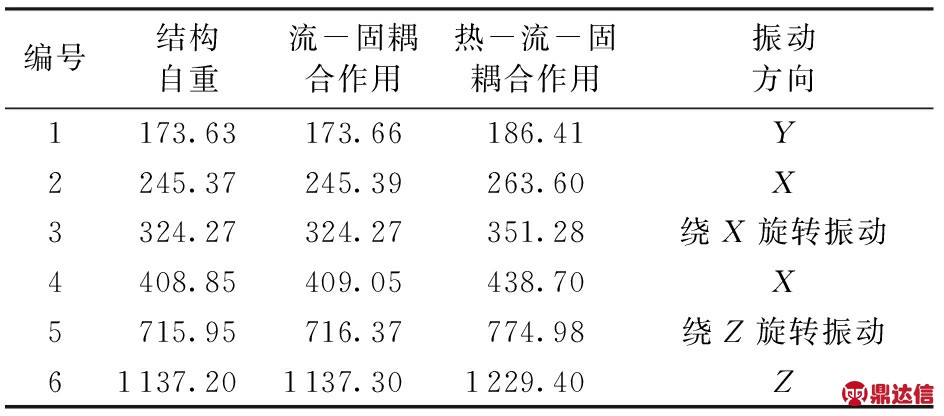
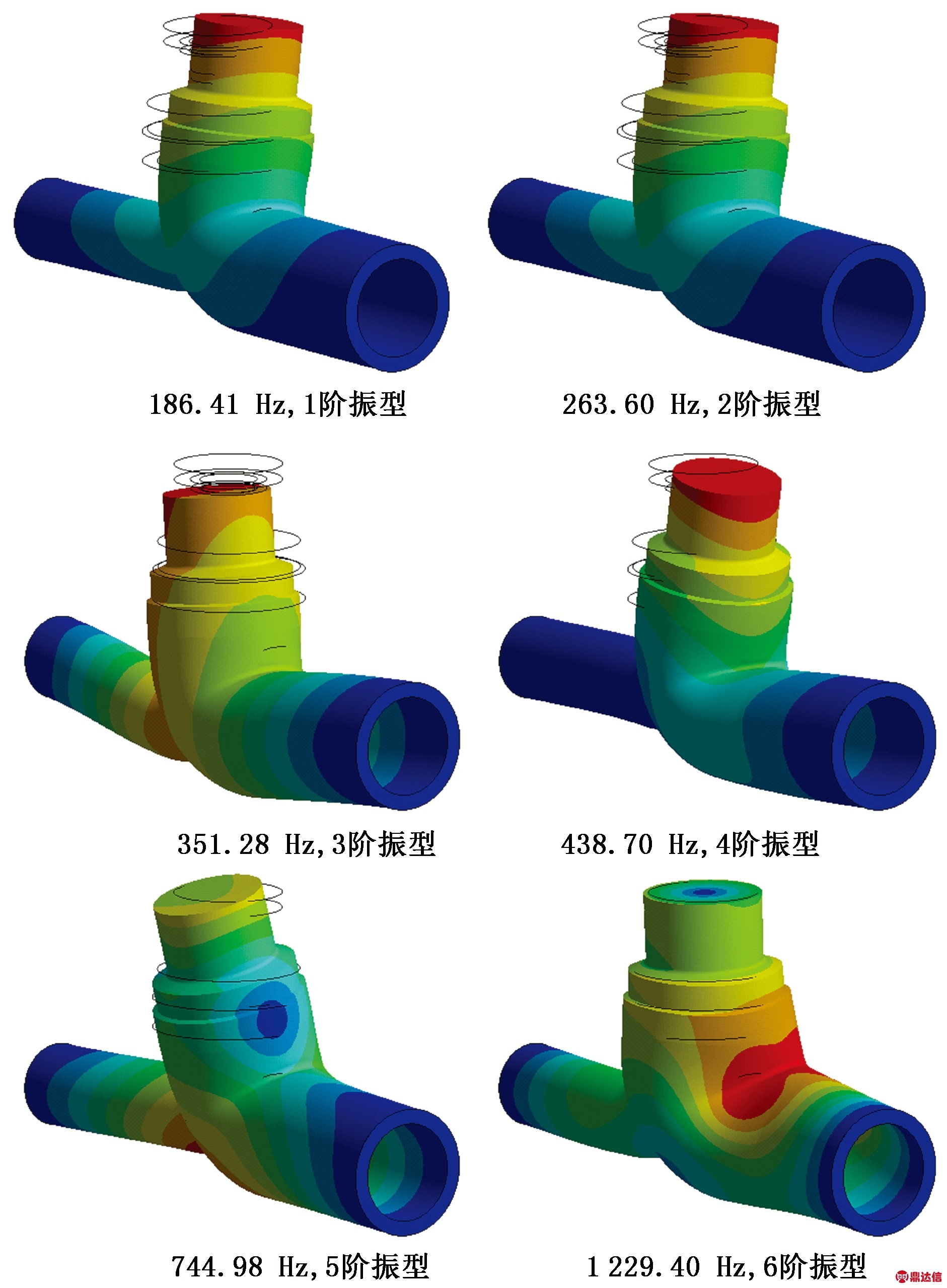
图9 减压阀振型
Fig.9 Mode shapes of valve body
3 材料S-N曲线修正
通常利用材料的抗拉强度和屈服强度并采用最小二乘法拟合获得材料的S-N曲线[23-24]。拟合获得的S-N曲线只能表征标准试样的疲劳性能,阀体结构部件与标准试样存在较大区别,直接利用拟合获得的材料S-N曲线进行疲劳寿命计算,计算误差较大。在拟合获得材料S-N曲线的基础上,分析应力集中、表面状态、载荷类型、微观组织等对疲劳寿命的影响,综合考虑各影响因素,对阀体材料的S-N曲线进行修正。
通过最小二乘法获得材料的S-N曲线,其拟合方程[25-26]为
logN=a+bσ-1.
(1)
其中
,
.
式中,a、b为材料特征常数,由材料的抗拉强度和屈服强度确定;σ-1为材料的屈服强度;σi为材料的抗拉强度。
1.6220铸钢材料的σb为520 MPa,a=33.238 6,b=-11.275 9,屈服σs为196 MPa。ZG08Cr18Ni9材料的σb为496 MPa,a=34.594 1,b=-11.093 9。将材料的特征参数带入式(1)获得材料的S-N曲线。
考虑各影响因素,材料疲劳强度降低系数[27-28]为
.
(2)
其中
kσ=1+q(aσ-1).
式中,kσD为弯曲疲劳强度降低系数;β1为表面加工系数;ε为尺寸系数;kσ为有效应力集中系数;q为敏感系数;aσ为理论应力集中系数。
RMG530减压阀尺寸系数ε为0.671 8,表面加工系数β1为1.5,敏感系数q为0.5,理论应力集中系数aσ为1.5[29-30],代入式(2),计算得出。
根据修正结果,计算获得不同疲劳寿命下对应的疲劳极限值,并得到两种材料的S-N曲线,见图10。
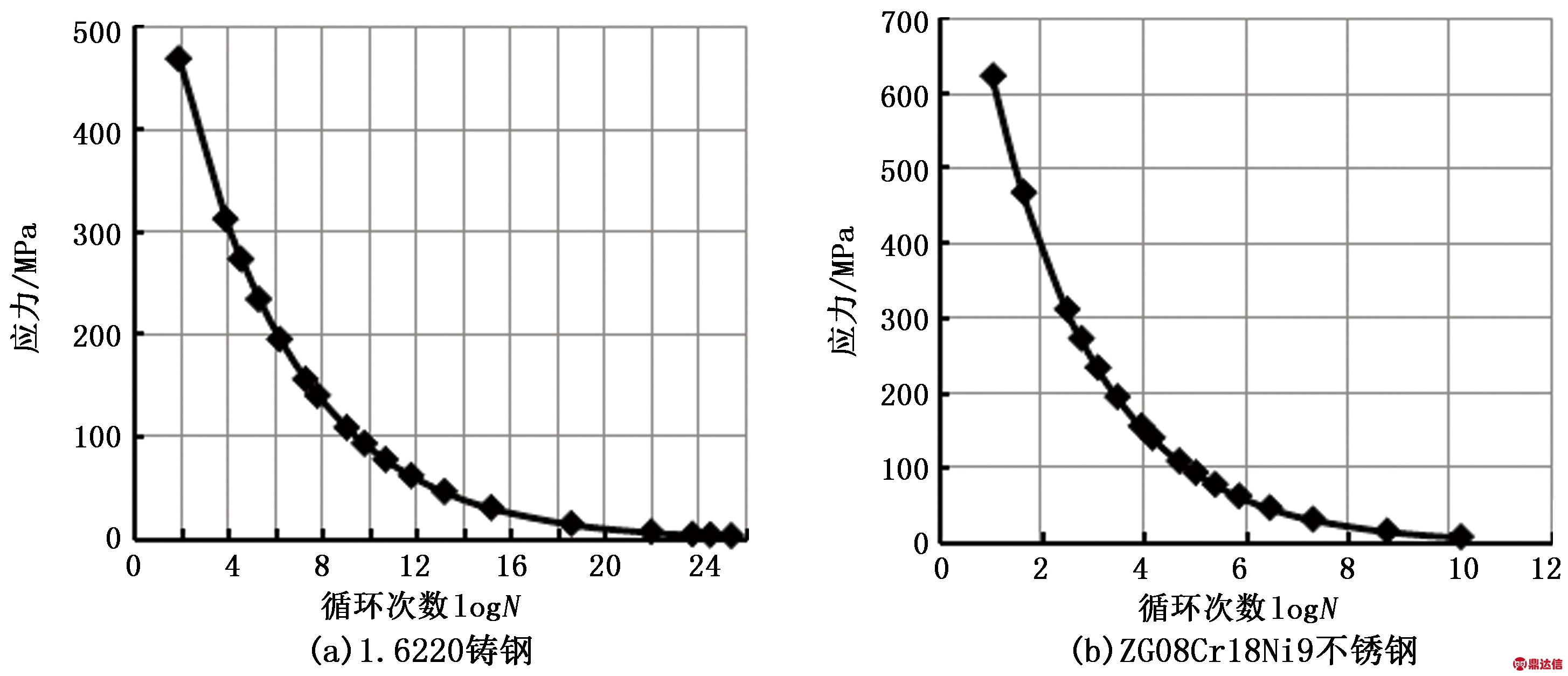
图10 1.6220铸钢及ZG08Cr18Ni9不锈钢S-N曲线
Fig.10 S-N curves of 1.6220 cast steel and ZG08Cr18Ni9 stainless steel
4 随机振动疲劳分析
4.1 时域疲劳分析
将随机振动疲劳寿命的时域法引入到减压阀的疲劳寿命预测中,在阀体上施加Z方向振动加速度载荷,由有限元软件Workbench进行随机振动分析,再依据材料的S-N曲线利用NCode软件进行时域疲劳分析,得到加速度激励下减压阀疲劳寿命分布。图11为减压阀不同位置寿命分布云图。
由表2可知:RMG530减压阀振动载荷下最小寿命发生在进口管段到阀座的拐角处,最小寿命为1.318×106,振动损伤为7.59×10-7;阀笼、阀套处振动载荷下疲劳损伤也较为严重,振动测量周期为1 000 s,阀体和阀笼的振动疲劳寿命分别为1.79 a和60.75 a,阀套的振动疲劳寿命N>100 a,减压阀的振动疲劳寿命大于设计使用寿命30 a,但是,长时间振动作用下仍然容易造成疲劳破坏;因此,减压阀分输过程中须优化节流调压参数,增强减压阀的抗振性能,减小振动疲劳损伤。
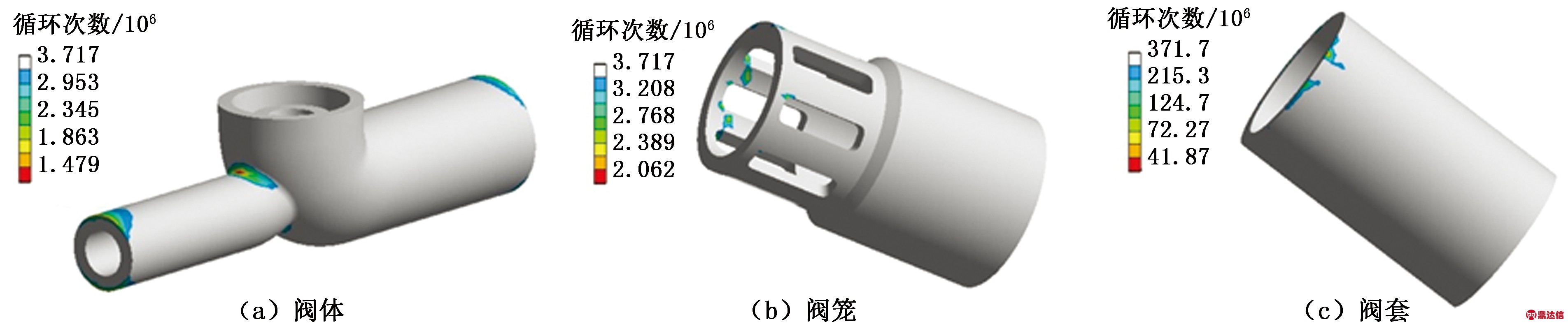
图11 减压阀振动时域疲劳寿命分布云图
Fig.11 Predicted vibration in time domain fatigue life contours
表2 减压阀振动疲劳时域计算结果
Table 2 Vibration fatigue calculation results of flow control valve in time domain
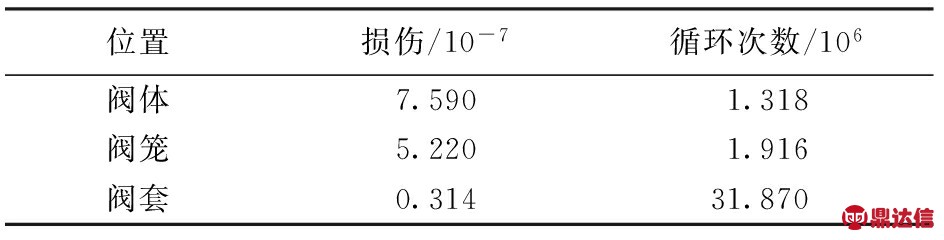
4.2 频域疲劳分析
将随机振动疲劳寿命的频域法引入到减压阀的疲劳寿命预测中,应用有限元分析软件,基于随机振动理论,根据现场测得的随机振动载荷对减压阀进行随机振动响应分析,获得响应功率谱密度,然后根据材料疲劳特性获得阀体结构疲劳寿命及分布。振动激励作用下阀笼、阀套、阀体中腔上部拐角处和进口管段到阀座的拐角处激励位移较大,容易造成振动疲劳,随机振动分析选取这4个位置为观察对象。图12显示在温度场和流场共同作用下减压阀主要位置节点响应的应力功率谱。所有功率谱图的波峰出现在 263.6 Hz位置,这与模态分析获得的第二阶固有频率一致。减压阀主要位置节点响应应力功率谱显示各位置的应力功率谱曲线形态基本一致,但峰值存在较大差异,进口管段到阀座的拐角处响应峰值最大,进口管段到阀座的拐角处的内应力远大于其他位置。
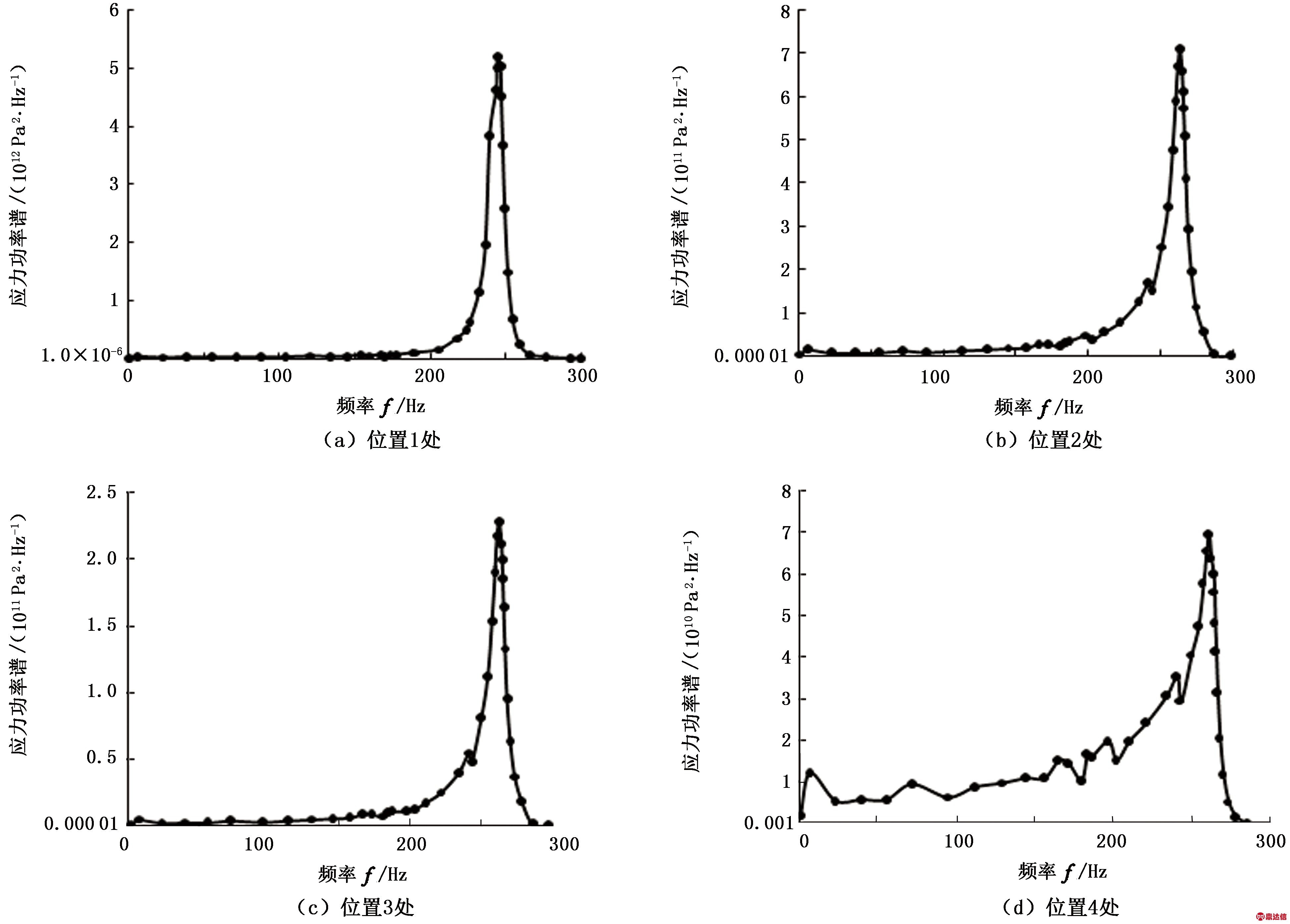
图12 节点应力功率谱
Fig.12 Node stress PSD
基于计算获得的阀体结构应力功率谱结果,利用NCODE软件进行随机振动载荷下阀体结构频域疲劳分析,得到加速度激励下减压阀疲劳寿命结果和分布。图13为减压阀不同位置寿命分布云图。

图13 减压阀振动频域疲劳寿命分布云图
Fig.13 Predicted vibration in frequency domain fatigue life contours
表3为减压阀振动疲劳频域计算结果。由表3可见,RMG530减压阀振动疲劳寿命频域计算结果与时域计算结果存在一定差异,频域计算结果偏安全。随机振动载荷下最小寿命发生在进口管段到阀座的拐角处,最小频域循环次数为1.224×106,振动损伤为8.17×10-7;阀笼、阀套处振动载荷下疲劳损伤也较为严重。阀体和阀笼的振动疲劳寿命分别为38.81和 50.76 a,阀体其他位置的振动疲劳寿命N>100 a,减压阀的整体振动疲劳寿命大于设计使用寿命30 a。
表3 减压阀振动疲劳频域计算结果
Table 3 Vibration fatigue calculation results of flow control valve in frequency domain
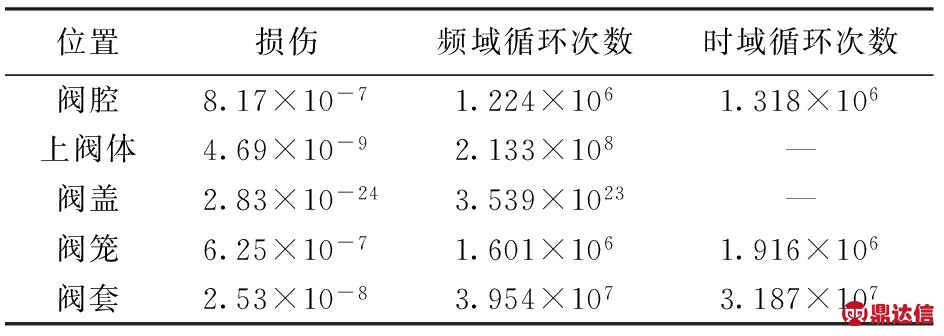
5 结 论
(1)减压阀主要位置节点响应应力功率谱曲线形态基本一致,进口管段到阀座的拐角处响应峰值最大。波峰均出现在263.6 Hz位置,与阀体的第二阶固有频率一致。
(2)RMG530减压阀随机振动载荷下最小寿命发生在进口管段到阀座的拐角处,最小疲劳寿命为41.79 a,阀笼的振动疲劳寿命为60.75 a,阀套的振动疲劳寿命大于100 a。
(3)RMG530减压阀振动疲劳寿命频域计算结果与时域计算结果存在一定差异,频域计算结果偏安全。进口管段到阀座的拐角处为38.81 a,阀笼的振动疲劳寿命为50.76 a,减压阀的振动疲劳寿命大于设计使用寿命30 a。
(4)天然气分输过程中阀体应力响应幅值不大,未引起阀体共振,该阀体有足够的安全裕度。