摘要:本文使用超声波水浸单探头反射法对不贴紧缺陷进行了检测,根据缺陷反射波的形状及在时域上的位置对缺陷的深度和类型进行了分析评价。使用241Am源59.5 keV的单能窄缝γ射线,对芯体分布的均匀性进行了检测。根据特定检测频率下包壳厚度与涡流阻抗变化的对应关系对包壳厚度进行了分析评价。通过超声、射线和涡流检测方法对板型燃料元件内部缺陷检测并给予评价,保证产品质量。
关键词:板型燃料元件;无损检测;内部缺陷检测;核燃料元件
板型燃料元件是研究试验堆燃料元件的典型类型之一,通过轧制工艺一次成型,燃料板由上包壳、芯体、下包壳3部分组成。制造过程中,通过超声、射线和涡流检测方法对板型燃料元件内部缺陷检测并给予评价,保证产品质量,保证燃料组件安全、高效可靠地运行[1-3]。
采用水浸单探头反射法对包壳与芯体的不贴紧进行检测,该方法可根据缺陷反射波的形状及其在时域上的位置对缺陷的埋藏深度和大致类型进行分析评价,检测灵敏度达到φ1.2 mm平底孔当量。
弥散芯体分布均匀性采用γ射线吸收法,该方法是以Al基体分布完全均匀为前提[4]。该方法结合燃料元件厚度恒定的结构特点[5],利用准直后的241Am源59.5 keV的γ射线进行检测并建立方程组,同时得出检测区域U3Si2、Al的体积百分数,避免了Al分布均匀性假设,提高了U3Si2均匀性检测结果的可靠性。
采用涡流法对板型燃料元件的包壳厚度进行检测,涡流大小与线圈本身因素有关,如在特定信号频率、线圈的形状和尺寸等条件下,涡流阻抗变化仅取决于燃料元件的电导率、尺寸及缺陷等。本文根据特定检测频率下包壳厚度与涡流阻抗变化的对应关系及在时域上的位置对包壳厚度进行实时分析评价。
1 方法原理
1.1 包壳与芯体不贴紧检测
超声波探头发射超声波从一种介质入射到另一种介质时,在两种介质的界面上会发生反射和透射。若是垂直入射,反射波会从原路径返回而被探头接收,透射波会在另一介质中继续传播,当透射波在传播的途径中遇到缺陷时又会有一部分声能从原路径返回被探头接收。根据探头接收到的缺陷反射波能量的大小对缺陷进行描述[6-7]。
图1为单探头反射法原理图。探头发射超声波,当从水中入射到燃料板表面时会发生反射和透射,反射的超声波从原路径返回被探头接收,视为界面波。透射到板中的超声波继续传播,传播到包壳与芯体结合层时,由于芯体材料的声阻抗与包壳材料的声阻抗差别很小,所以可不考虑该层异质界面发生的反射波。若在该结合层有不贴紧,会产生一束能量较大的反射波被探头接收到。

图1 单探头反射法原理图
Fig.1 Schematic diagram of single probe reflection method
1.2 芯体均匀性检测
U3Si2-Al燃料元件的厚度恒定且金属基体和包壳均是由Al金属构成,当使用γ射线进行检测时,每次检测的U3Si2、Al的总体积V恒定,则:
V=VU+VAl
(1)
式中:VU为U3Si2的体积;VAl为Al的体积。
利用体积百分数表征检测区域内U3Si2、Al的含量为:
(VU+VAl)/V=α+β=1
(2)
式中:α为U3Si2的体积百分数;β为Al的体积百分数。
使用γ射线检测时,γ射线的衰减规律可表述为:
I=I0e-μT
(3)
式中:I0为γ射线初始强度;I为γ射线穿透物质后的强度;μ为被检物质的γ射线线吸收系数;T为被检物质厚度。根据式(3),γ射线穿透U3Si2-Al燃料元件的关系式可表述为:
I=I0e-μU-AlTU-Al
(4)
式中:μU-Al为U3Si2-Al燃料元件的γ射线线吸收系数;TU-Al为U3Si2-Al燃料元件厚度。
混合物的γ射线线吸收系数可表示为各组成物质的体积百分数乘以各自的γ射线线吸收系数再求和。假设α+β=1,则燃料元件的γ射线线吸收系数可等效为:
μU-Al=αμU+βμAl
(5)
引入体积百分数的概念后,式(4)可拓展为:
I=I0e-(αμU+βμAl)TU-Al
(6)
在μU、μAl已知的条件下,求解方程(6)可得出各测试点U3Si2、Al的体积百分数α、β,进而可得出其分布状态。
γ射线吸收方法是核辐射射线测量方法,射线计数存在统计涨落现象,因此放射源活度及其计数的统计涨落会给测量结果带来误差[8]。探测器计数分布遵从正态分布,一般情况下取置信度为95%;探测器计数的计数区间为[I0-2,I0+2
],在放射源活度固定的情况下可通过改变测试时间来控制探测器计数区间的波动幅度。
由此可推导出,当置信度为95%、通过样品后探测器强度为I时,面密度D的波动幅度与I0的关系如下:
V+==
(7)
V-==
(8)
式中,V+、V-分别为因统计涨落引起的D变化上、下限。通过计算可得,I0越小,测试误差上、下限越大,I0在0.5×105以上时,波动幅度已接近1%。
1.3 包壳厚度检测
当通以交变电流的线圈靠近金属导体时,由于电磁感应作用,在导体的近表面感应出闭合的涡流,该涡流会产生与原磁场方向相反的交变磁场。涡流磁场与线圈磁场相互作用而使线圈的阻抗发生改变[9-11]。涡流的大小与线圈本身因素有关,如信号频率、线圈的形状和尺寸等。若这些因素一定,则仅与样品特性有关,如样品的电导率、尺寸及缺陷等。因此,根据线圈的阻抗变化就可测量燃料元件的包壳厚度。
2 包壳与芯体不贴紧检测
2.1 回波波形分析
使用Panametrics15P6SJ25DJ探头,水距20 mm对标准伤板无伤位置进行垂直入射检测时波形如图2所示。对下界面φ1.2 mm标准伤垂直入射检测时波形如图3所示。
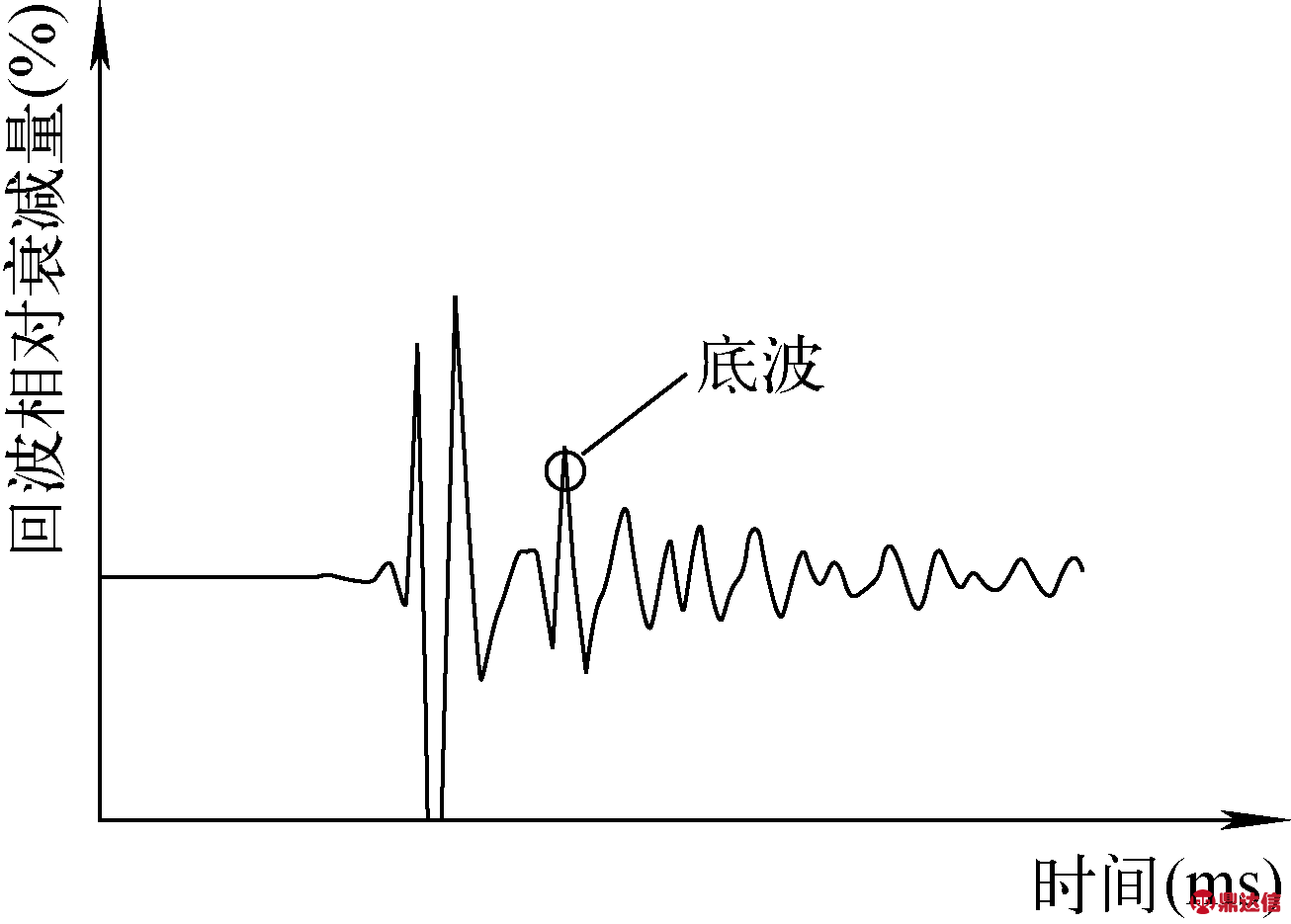
图2 无伤处回波波形
Fig.2 Uninjured echo waveform
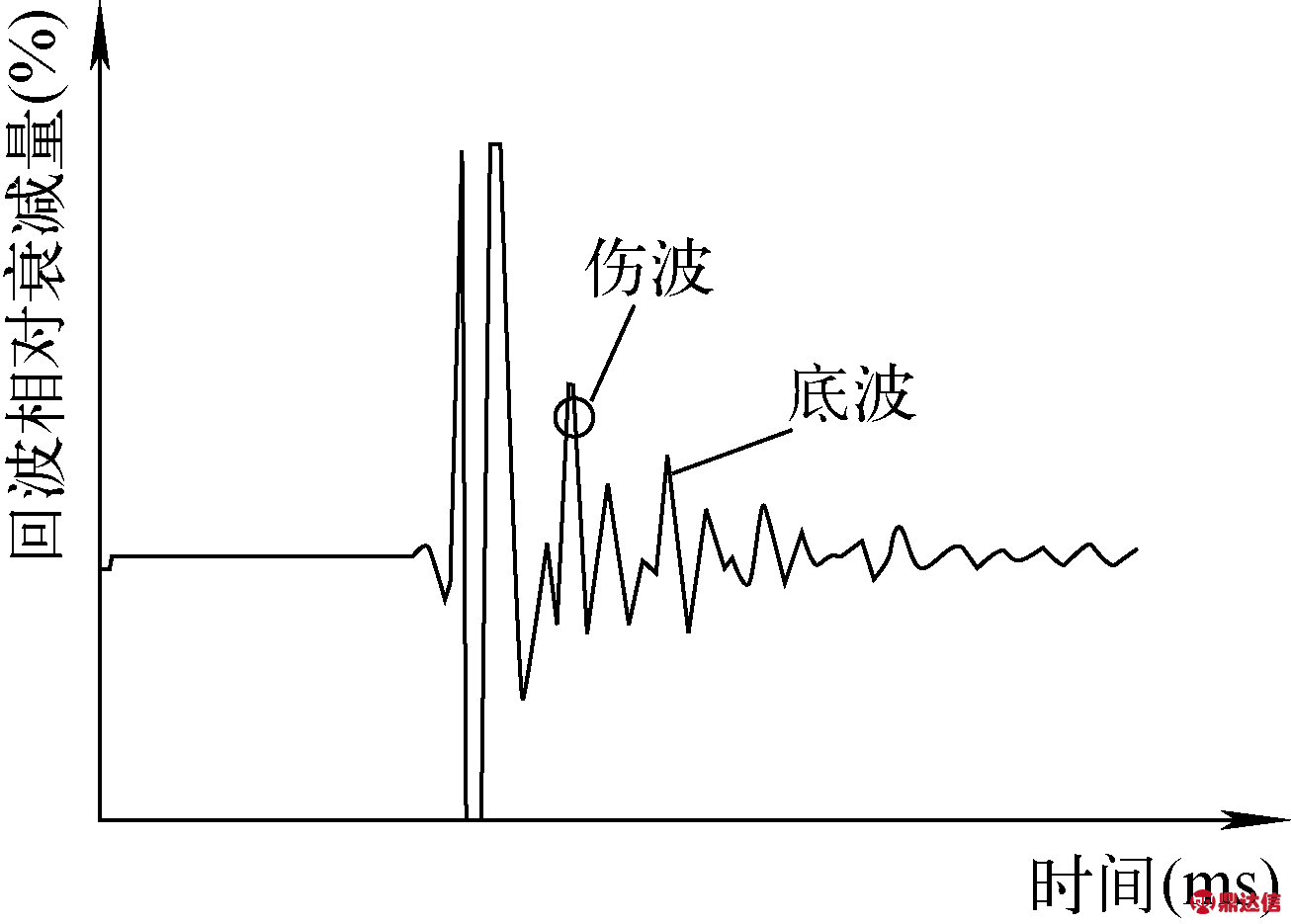
图3 下界面φ1.2 mm标准伤回波波形
Fig.3 Interface φ1.2 mm standard echo waveform
对比图2、3可看出,无伤时界面波与底波之间无反射信号,有伤时底波降低,伤波出现。Al-芯体-Al复合结构各层的声阻抗列于表1。
声压反射公式为:
R=(Z2-Z1)/(Z2+Z1)
(9)
式中:R为声压反射系数;Z1、Z2为声阻抗。
表1 材料声阻抗
Table 1 Material acoustic impedance
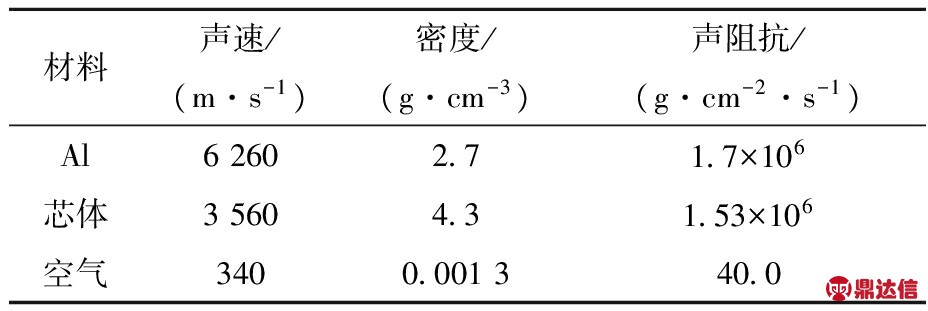
通过测量数据显示,对于能准确表征的超差点,其测量定位精度与实际位置差别不超过±1 mm,缺陷定位精度≤1 mm。
2.2 探伤信号分析
应用单探头反射法分别对8个标准伤进行检测,得出的伤波升高及底波衰减情况列于表2。其中,数据均由KK的15P6SJ20DJ探头测得,水距均为14 mm。
1) 伤孔尺寸对伤信号的影响
实验中标准伤信号上升幅度及该伤处底波下降幅度变化不随被检测孔径的变化而变化,探头焦斑尺寸公式为:
φ=λ
(10)
式中:φ为焦斑直径;λ为介质中波长;f为探头频率;S为探头晶片尺寸。
计算出探头焦斑直径为0.39 mm。因此对最小孔径为1.0 mm的标准伤,实验用探头相当于直射入标准伤孔内,因此不会出现标准伤信号及该处底波降低幅度随被检孔径变化而变化。其变化规律仅随标准伤孔底制作情况及树脂封堵情况而变化。
表2 标准伤幅度对比
Table 2 Comparison of standard injury
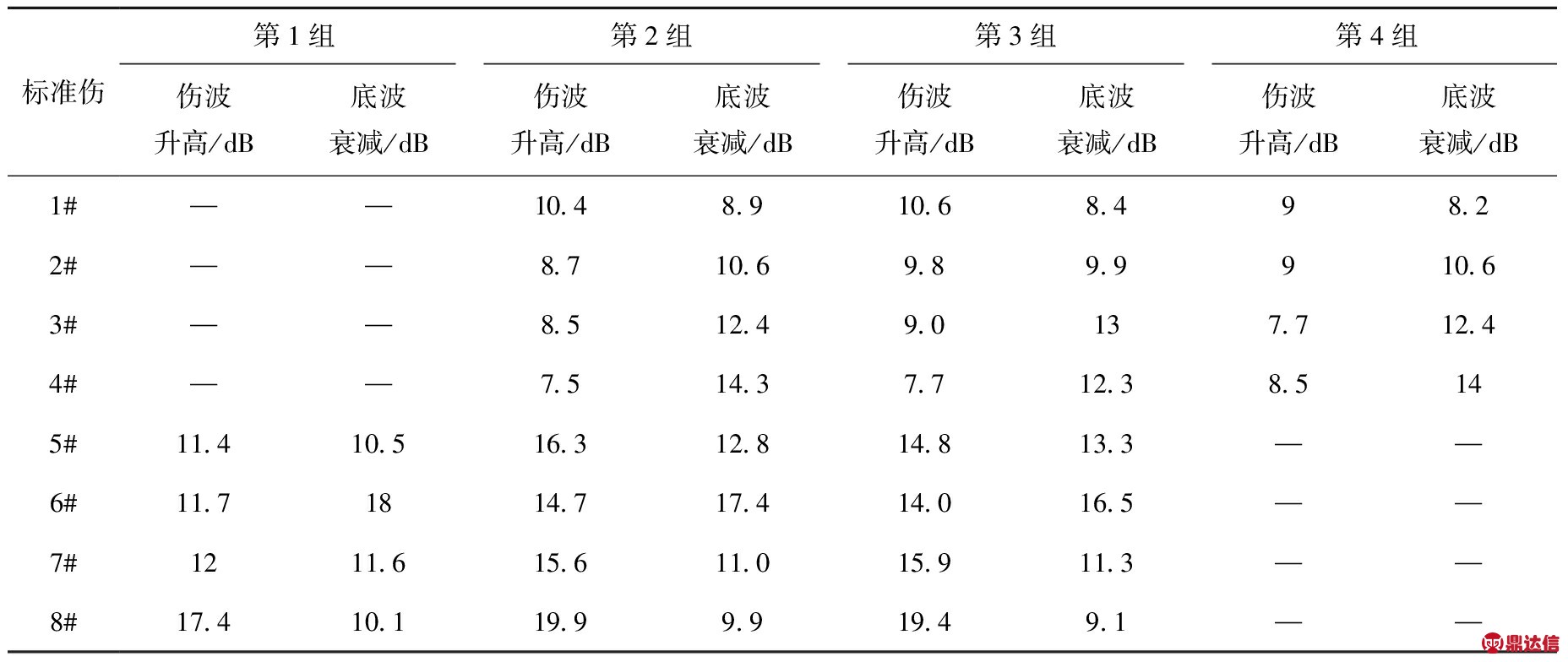
2) 最高底波幅度
实验中通过调整探头与燃料板表面的距离,得出当水距为14 mm时底波反射幅度最高,最有利于观察底波变化情况,而本文将底波变化定义为伤判定的重要依据之一。在不同水距时无缺陷处底波的变化如图4所示。
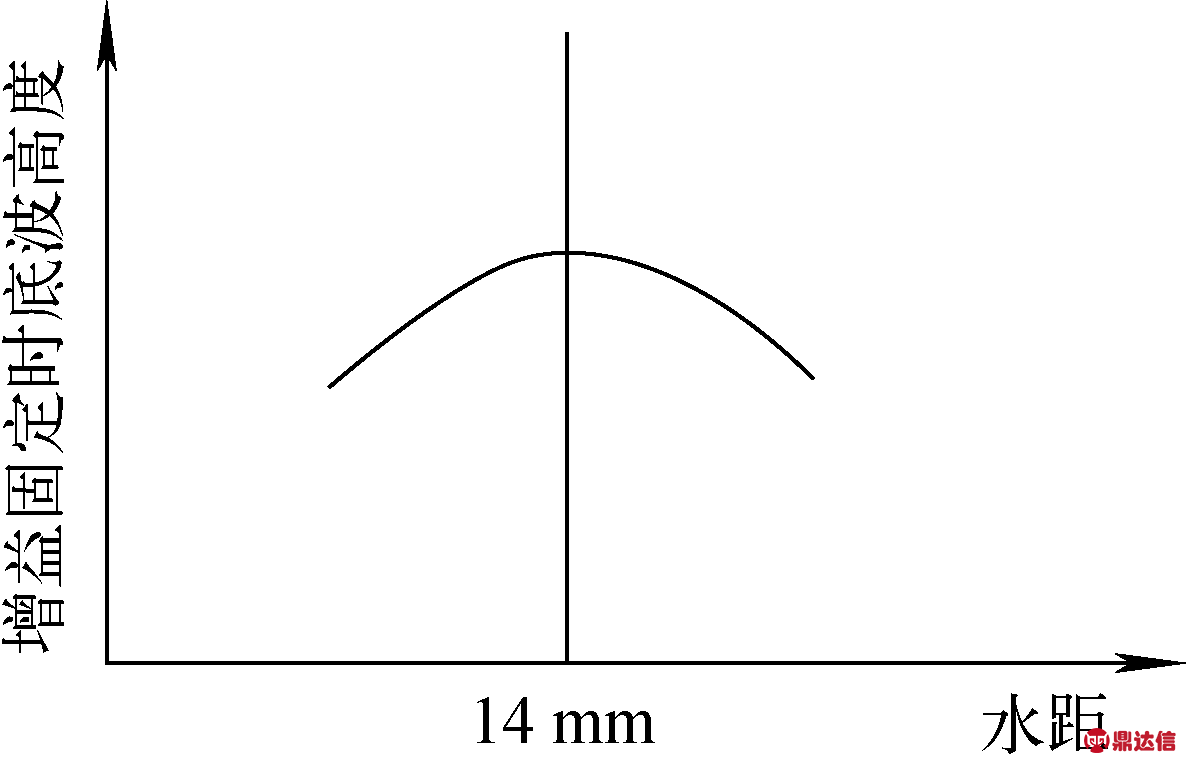
图4 不同水距时无缺陷处底波的变化
Fig.4 Waveform without defect under different water depths
2.3 金相解剖验证
实验中样品1缺陷处靠近上界面出现反射回波,样品2缺陷处靠近下界面出现反射回波,如图5所示。以此推断样品1信号衰减原因为上界面处出现气隙,样品2信号衰减原因为下界面处出现气隙。定点解剖做金相,发现此处有空腔(图6)。
实验证明,通过选取合适的探头,单探头反射法能有效检出φ1.0 mm当量的不贴紧缺陷,区分出不贴紧位于上、下界面的位置,并得到了解剖验证。
2.4 不贴紧位置定量计算
为准确判断不贴紧或空腔位于芯体厚度方向上的位置,实验中钻制直径为1.2 mm,深度分别为0.75、1.05、1.15、1.25 mm的平底孔以模拟不同深度位置的不贴紧,利用钻制的平底孔开展实验,观察回波波形(图7)。
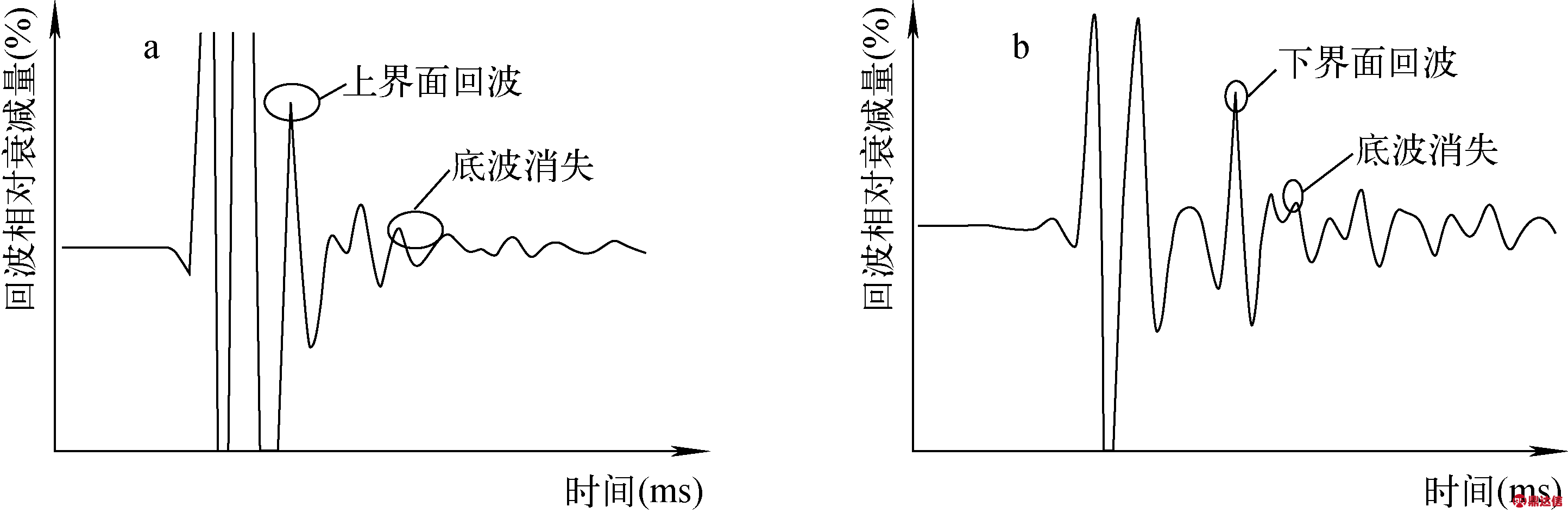
图5 样品1(a)及样品2(b)的缺陷回波
Fig.5 Defect echoes of sample 1 (a) and sample 2 (b)
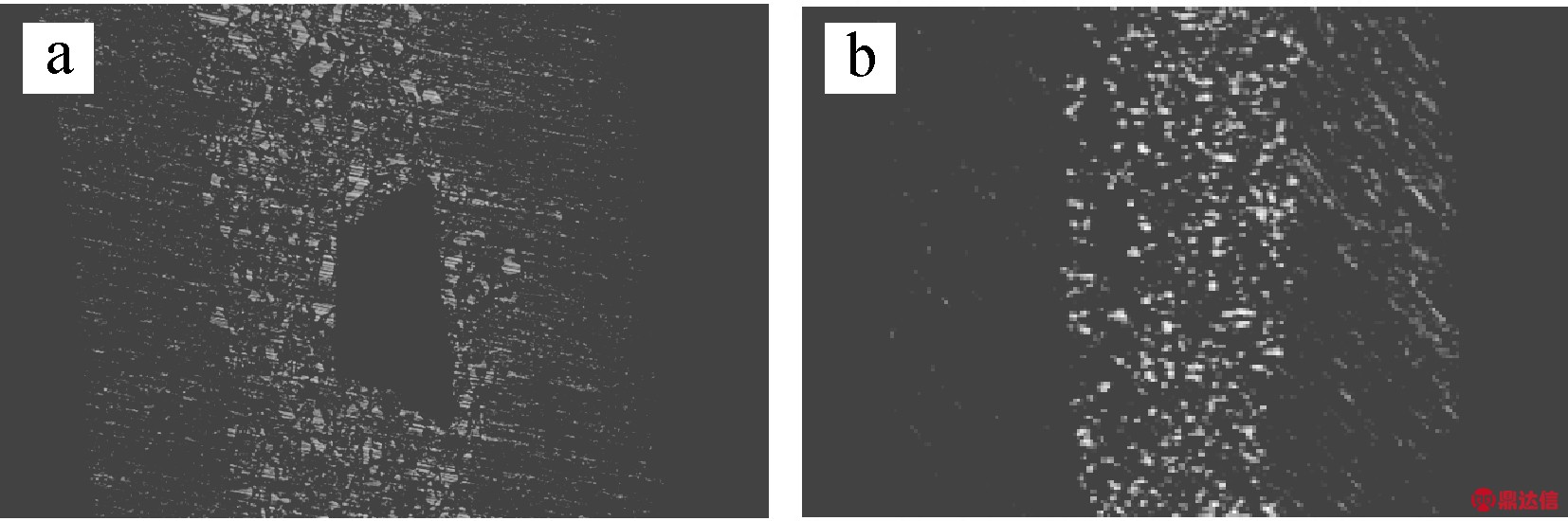
图6 样品1(a)及样品2(b)解剖金相图
Fig.6 Anatomies of sample 1 (a) and sample 2 (b)
图7a为深0.75 mm的平底孔反射回波的第1个振荡周期的上半峰;图7b为深1.05 mm即距外表面埋深0.45 mm平底孔反射回波的第1个振荡周期的上半峰,可看出,该波峰已部分进入到界面波中。图7c为深1.15 mm即距外表面埋深0.35 mm平底孔反射回波的第2个振荡周期的上半峰,与图7a、b相比,图7c的界面波已发生变形,说明反射回波第1个振荡周期已全部进入界面波;图7d为平底孔深1.25 mm即平底孔距外表面埋深0.25 mm时反射回波完全淹没于界面波内,界面波与反射伤波叠加使界面波严重变形。

1——伤波;2——无伤时底波
图7 不同深度平底孔反射回波波形
Fig.7 Reflection echo waveform of different depth flat bottom holes
使用界面波第1个振荡周期上半峰与伤波反射波第1个振荡周期上半峰的峰值间隔的时间t进行深度计算。此处使用的声速v铝=6 260 m/s、v芯体=3 600 m/s,计算得出的深度如下:平底孔深度为0.75 mm时,计算深度为0.56 mm(6次测量均值);平底孔深度为1.05 mm时,计算深度为0.78 mm(6次测量均值)。由于平底孔深度1.15 mm、1.25 mm标准伤的反射回波第1个振荡周期已与界面波叠加,因此计算不出深度值。
3 芯体均匀性检测
3.1 探头阈值参数确定
通过对检测探头能谱的测量可看出,NaI(Tl)探头能量分辨率较高[12],计数亦较高,满足灵敏度要求,将241Am放射源的低能峰纳入上、下阈值范围外,避免低能噪声信号进入探头信号输出而影响检测灵敏度。
3.2 标准样品制作
检测过程中,计数变化转变为铀分布均匀性变化的表征过程是通过标定曲线来完成的。计算机通过分析、比对探头采集计数的变化,进而得到关于燃料元件芯体铀分布均匀性的相关信息。为得到标定曲线,需获得不同等效铀分布均匀性下探头的不同计数。在标样材料及其尺寸、射线类型等影响因素确定的情况下,标样厚度成为直接影响射线穿过后计数发生变化的主要影响因素。
根据实验结果设计加工0.80、0.90、1.00、1.10、1.20、1.30、1.40、1.50 mm厚度紫铜阶梯样板,作为标准样品。标定时比对射线穿过现有标准样品时的计数与穿过标准样品时的计数,根据最小二乘法拟合厚度与计数关系的线性方程。将标准样品计数代入该方程,计算出不同厚度铜板的等效铀分布均匀性值。
3.3 检测精度确定
用现有检测方法测量板型燃料元件芯体均匀性,选取铀分布较均匀的区域,以φ5.6 mm为单位面积在该区域内取点测量,同时对所取点用化学分析方法测量铀总量。由于化学分析具有较高的测量精度,其测量结果更加接近真值。对化学分析结果进行计算,得出对应的铀分布均匀性值。比对化学分析方法与无损测量方法得出的铀分布均匀性值。实验时,对不同次燃料板进行单位铀总量分析,结果显示无损检测方法与化学分析方法之间的差值不超过±3 mg/cm2,吻合性较好,因此射线吸收系数的变化对现有检测方法无显著影响。分析结果列于表3。
表3 化学分析与γ测量数据比对结果
Table 3 Chemical analysis and γ measurement data comparison result
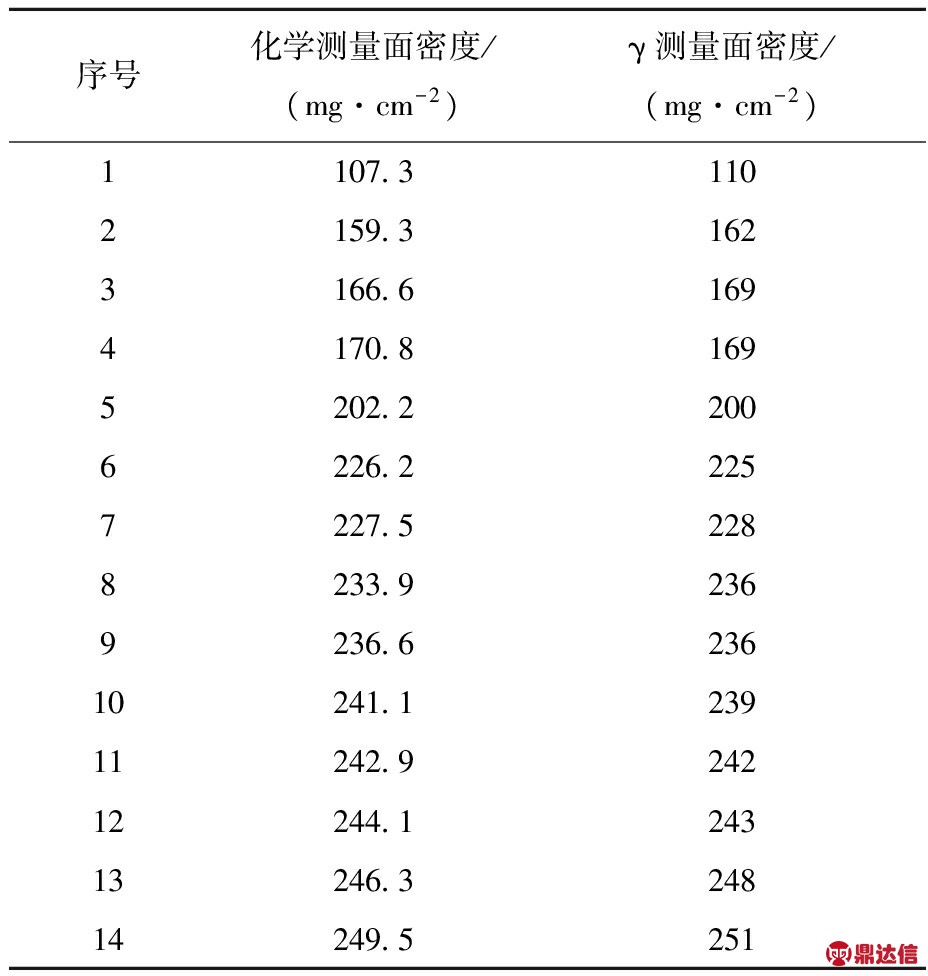
3.4 定位精度
在燃料板上进行人工钻孔,人工伤具体尺寸列于表4。并对该燃料板进行检测,通过观察铀分布均匀性的波动情况,最终确定系统对负超差点的定位能力。
表4 负超差点人工伤信息
Table 4 Negative tolerance point injury information
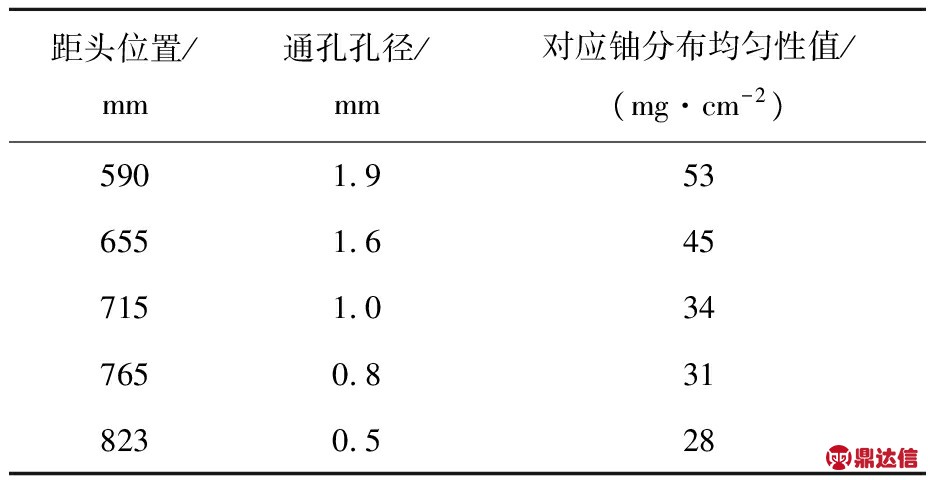
系统可明确区分孔径为1.9、1.6、1.0 mm的通孔位置,定位精度列于表5。
但对孔径为0.8 mm、0.5 mm两点无法明确定位,主要原因为其对应的铀分布均匀性值变化(-14%,-9%)已“淹没”在燃料板自身的铀分布均匀性变化中,无法准确判断其坐标位置。图8为在燃料板上人工钻孔后进行铀分布均匀性检测的结果。
表5 负超差点定位信息
Table 5 Negative tolerance point location information
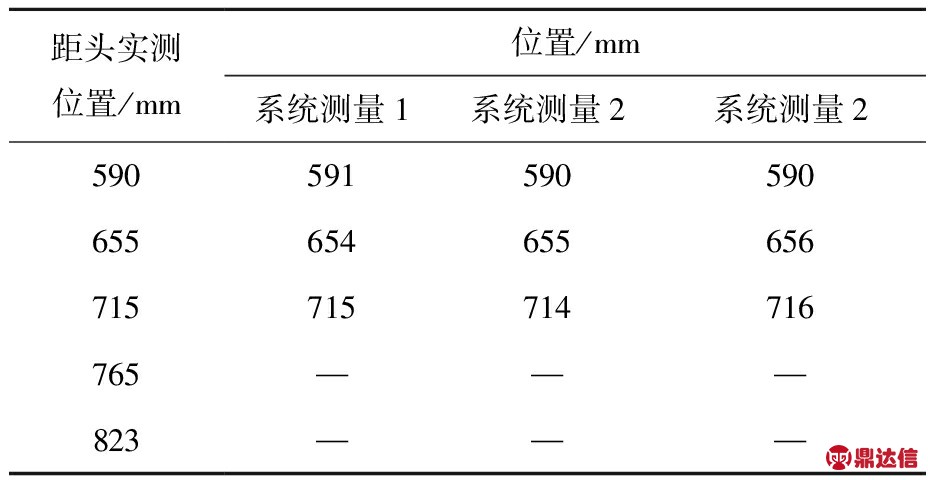
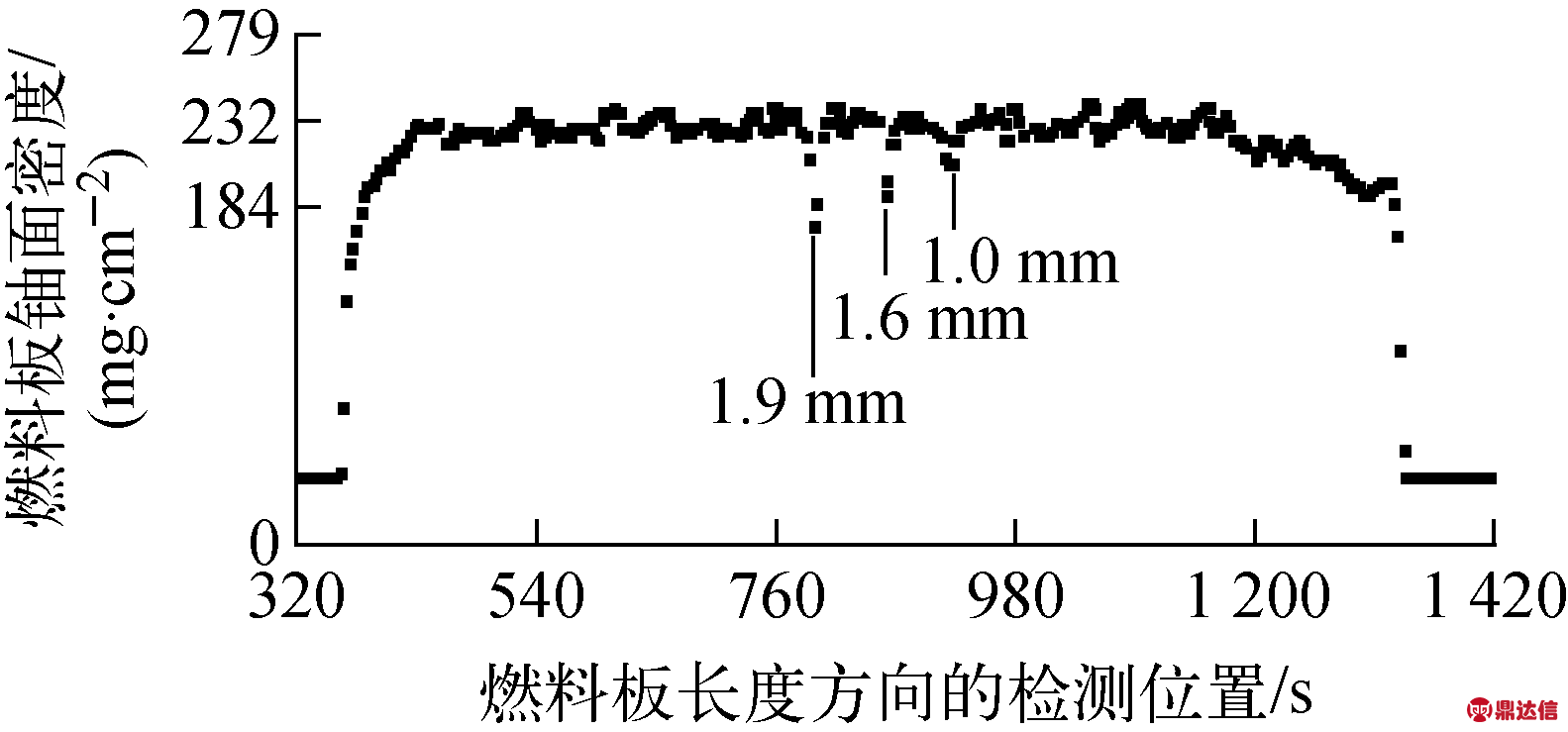
图8 负超差点测量数据
Fig.8 Negative tolerance point measurement data
在燃料板上进行人工增厚,增厚方式为在燃料板上粘贴不同厚度铜箔,人工伤具体尺寸列于表6。对该燃料板进行检测,通过观察铀分布均匀性的波动情况,最终确定系统对正超差点的定位能力。
表6 正超差点人工伤信息
Table 6 Positive tolerance point injury information
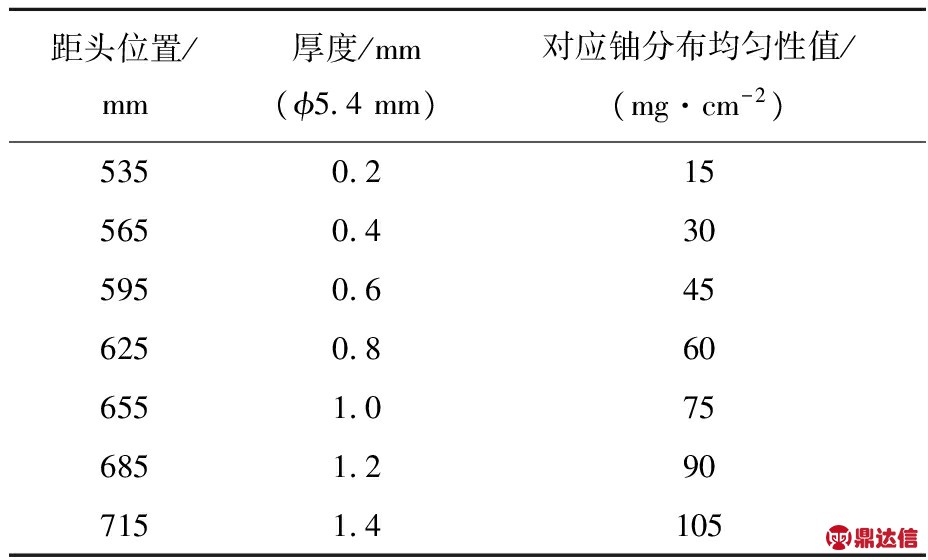
系统可明确区分厚度为0.6、0.8、1.0、1.2、1.4 mm的薄片位置,定位精度列于表7。
表7 正超差点定位信息
Table 7 Positive tolerance point location information
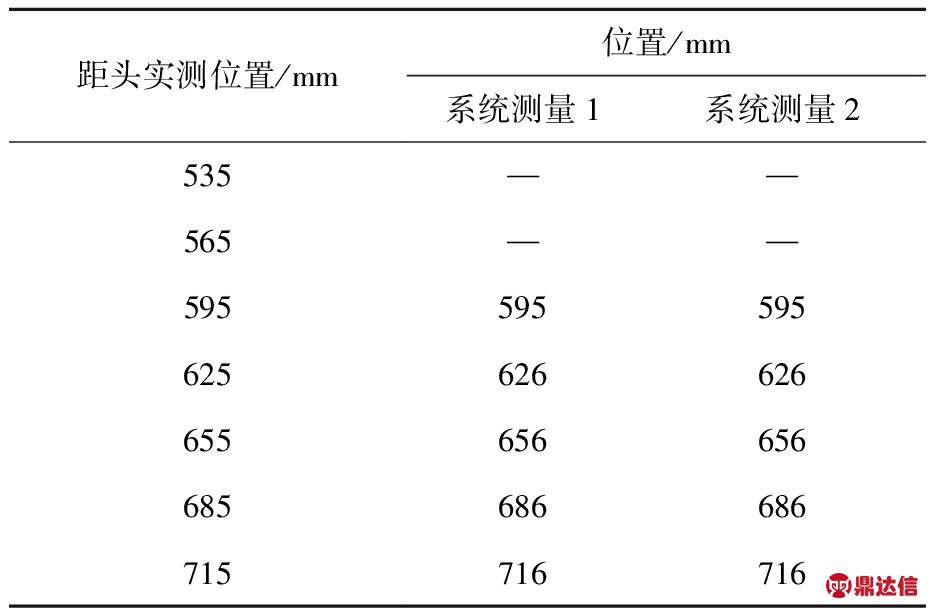
但对厚度为0.2 mm、0.4 mm点无法明确定位,主要原因为其对应的铀分布均匀性值变化已“淹没”在燃料板自身的铀分布均匀性变化中,无法准确判断其坐标位置。图9为在燃料板上粘贴不同厚度铜箔后进行铀分布均匀性检测的结果。
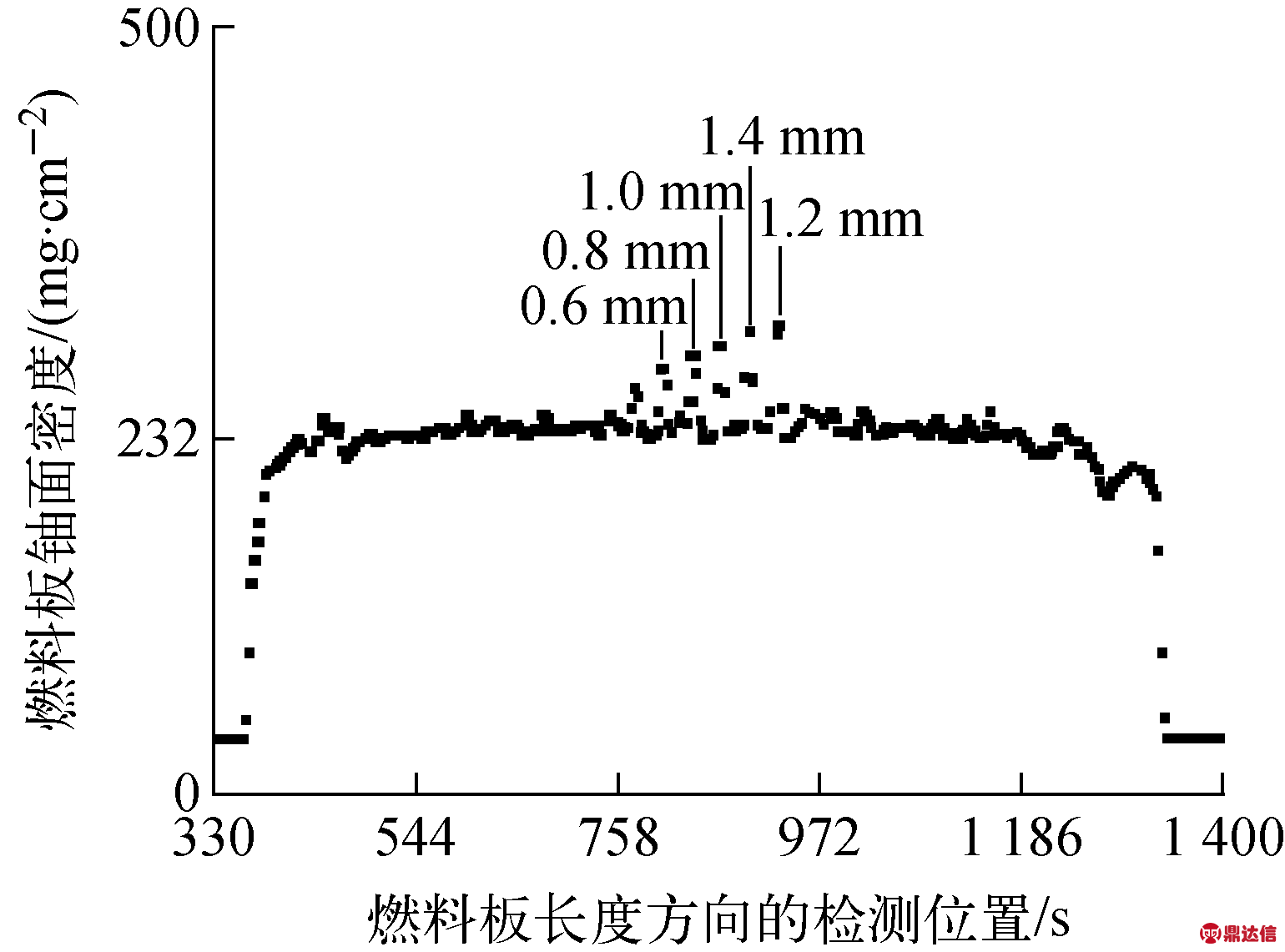
图9 正超差点测量数据
Fig.9 Positive tolerance point measurement data
学生想要查阅资料,不用再到图书馆借阅相关书籍,可利用互联网,随时随地访问学习材料或即时信息。学生将网络学习作为一种学习方式,可节约时间,减少成本投入,找到想要的学习资料;学生也可浏览实时新闻,关注感兴趣的热门话题,发表自己的见解和观点。利用互联网,学生还可与全国优秀教师借助摄像头和耳麦进行“面对面”互动,达到学习交流的目的。如:大规模网络公开课(MOOC课程)、蓝墨云班课等。
4 包壳厚度检测
由式(11)可计算出理论包壳厚度对应的涡流检测频率:
f=
(11)
式中:ρ为材料的电阻率,μΩ·cm;δ为磁导率,H/m;d为燃料板的包壳厚度,cm。
理论计算值检测频率为33 kHz,经实验,当检测频率为30 kHz、增益为30 dB、相位为98°时,涡流检测信号x方向信号水平,噪声最小,且可达到所要求的渗透深度。
为尽量减小由于除包壳厚度以外的其他因素对包壳厚度检测的干扰,元件包壳厚度标准样品是利用与所测样品具有相同包壳材料、热处理状态和生产过程的贫料板加工制成的,其结构如图10所示。
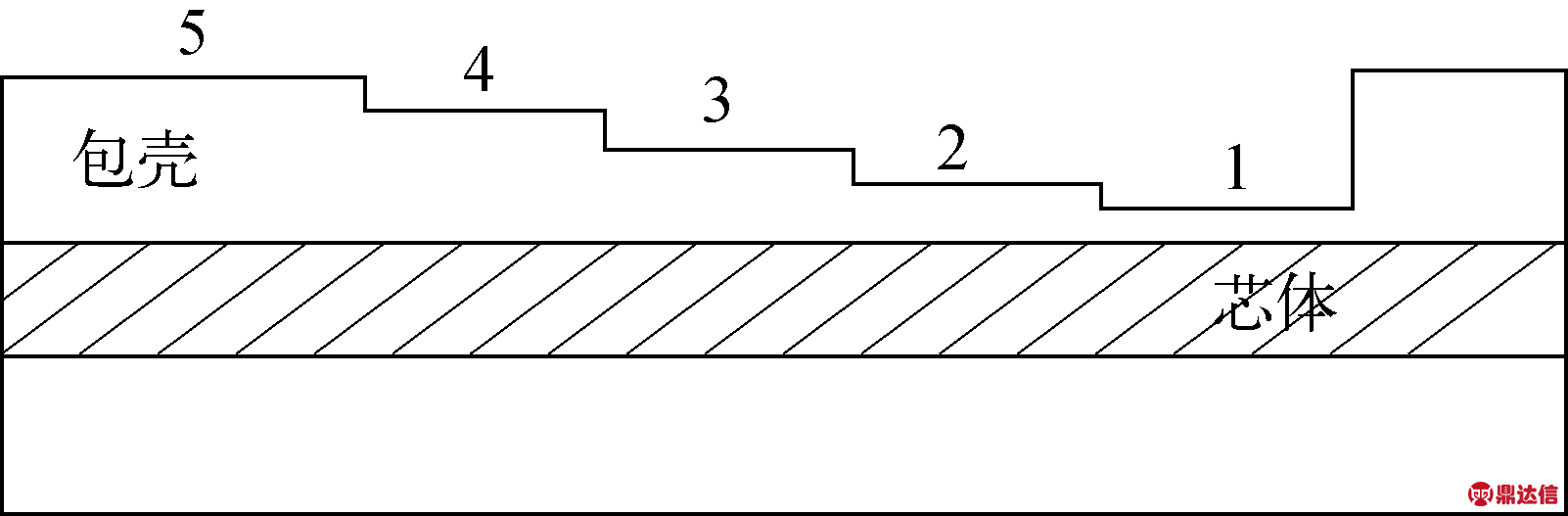
图10 板型燃料元件包壳厚度标样示意图
Fig.10 Sample schematic diagram of shell thickness standard of plate fuel element
经过实验多组参数,最终选取检测频率为30 kHz、相位为117°、增益为30 dB,此参数下的定标阻抗图如图11所示。
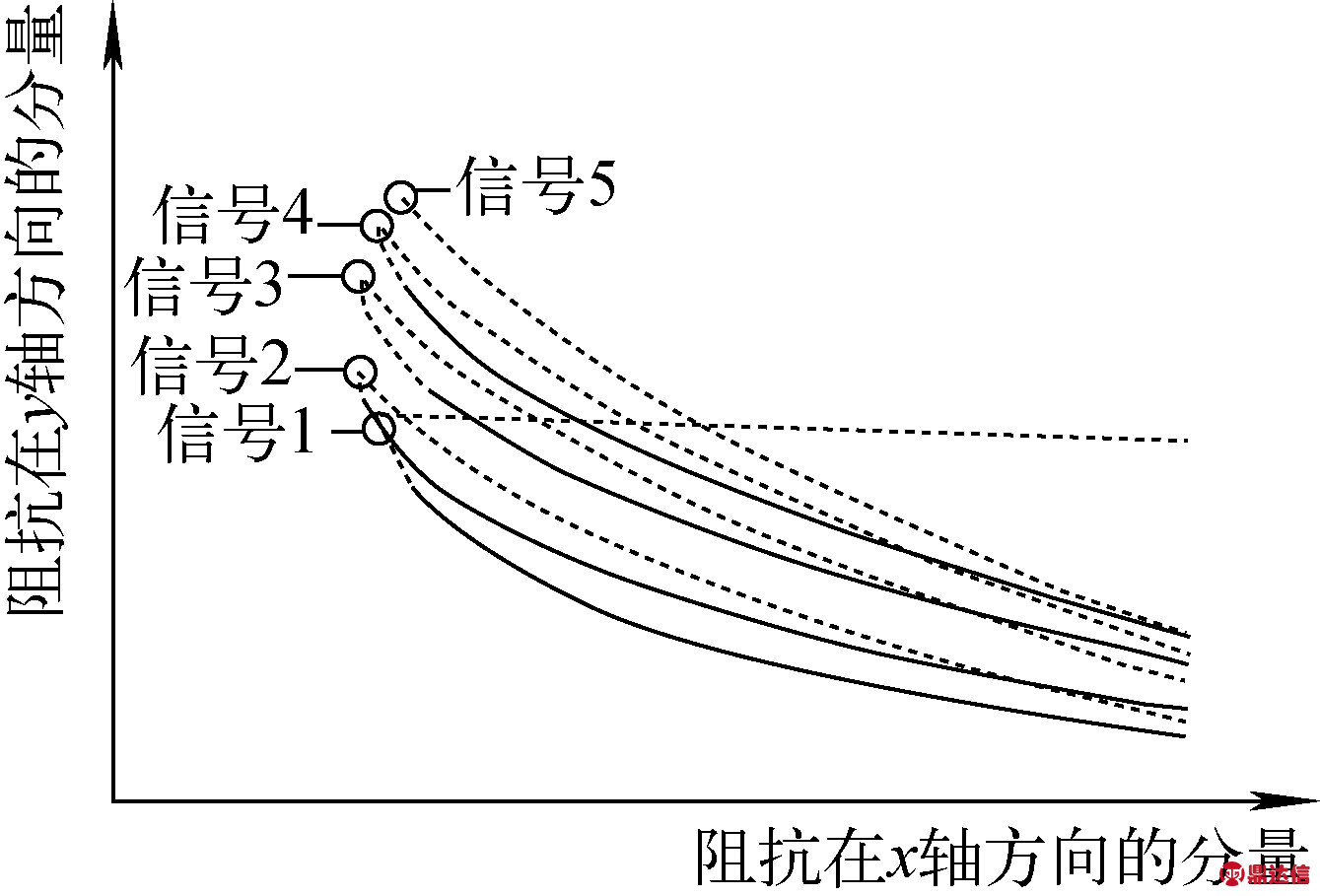
图11 定标阻抗图
Fig.11 Calibration impedance diagram
由图11可见,定标曲线符合要求,因此选取此参数作为检测参数。将标准样品的包壳厚度输入系统中,对系统进行标定。标定后,用系统测量板型燃料元件的包壳厚度a1,a2,…,an,测量结束后对测量位置进行定点解剖,使用金相法测量包壳厚度b1,b2,…,bn。用a1,a2,…,an与b1,b2,…,bn作差,表征检测系统的测量精度,表8为检测精度验证情况。
以金相包壳厚度为真值,板型燃料元件包壳厚度检测误差在-23 μm至19 μm之间,小于30 μm。
表8 检测精度验证
Table 8 Test precision verification
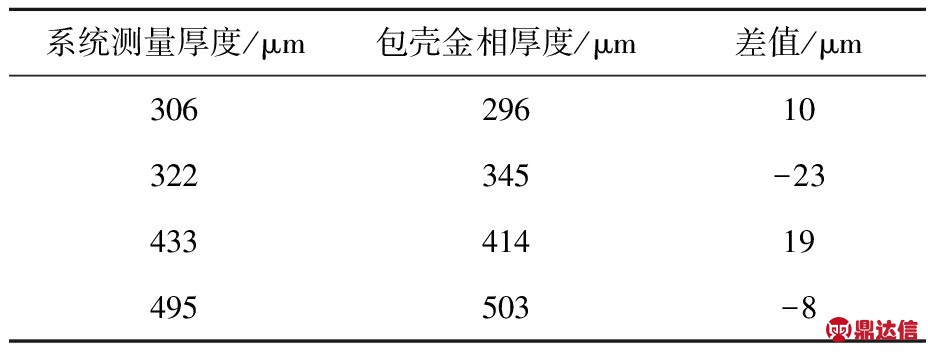
5 结论
本文采用单探头反射法能有效检出板型燃料元件内部φ1.0 mm当量的不贴紧缺陷,平底孔深大于1.25 mm即平底孔距外表面埋深小于0.25 mm时反射回波完全淹没于界面波内,界面波与反射伤波叠加使界面波严重变形,无法准确测量。采用γ射线吸收法检测板型燃料元件铀均匀性,检测精度达±3 mg/cm2,定位精度达±1 mm。采用涡流法对板型燃料元件包壳厚度进行检测,采用与所测样品具有相同包壳材料、热处理状态和生产过程的贫料板作为标准样品,检测精度达±30 μm。通过超声、射线和涡流检测方法对板型燃料元件内部缺陷检测并给予评价,保证产品质量,防止燃料元件在反应堆内破损。