摘 要 目的 针对飞机机翼的铝板在正常使用条件下经常出现的切割和冲击两种微损伤类型进行损伤检测.利用超声导波传播过程中衰减小,传播距离远的特点,从而解决传统检测方法的逐点扫描的缺点.方法 采用PZT压电陶瓷作为检测的Lamb波信号的激发和接收传感器,通过Hilbert变换计算监测信号的幅值变化,从而确定信号能量的分布规律,进而研究铝板的损伤程度.结果 切割损伤产生新的边界会产生新的反射波,信号分析过程中可以根据波的传播速度确定损伤的位置,同时根据信号幅值和能量变化确定损伤的程度.结论 冲击损伤可以从回波的Hilbert变换能量变化中检测到,但是信号的解析和确定损伤位置变得复杂得多.该方法可以有效地对超大型铝板进行无损检测.
关键词 航空铝板;Lamb波;PZT;Hilbert变换;损伤识别
结构健康监测(SHM)技术是用于评估结构完整性,发现安全隐患,进而评价结构的健康状态,目前常用的方法有涡流探头、超声波、磁粉测试、X射线、热成像和目视检查等几种[1-3].这些方法都只能对结构进行逐点的扫描,检测速度比较慢.超声导波沿传播过程中衰减很小,可以传播很远的距离,从而克服了逐点扫描的缺点,进而实现长距离、大范围的监测[4-6].
1880年法国物理学家P.居里和J.居里兄弟发现把重物放在石英晶体上,晶体某些表面会产生电荷,电荷量与压力成比例,这一现象被称为压电效应.随即,居里兄弟又发现了逆压电效应,即在外电场作用下压电体会产生形变.研究者们通过压电效应产生的导波在结构中传播的变化来对结构进行健康监测[7].以压电材料制成的PZT传感器是SHM中使用最多的传感器,通过施加很小的电压便可以在便宜的压电材料产生Lamb波.Lamb在波薄板结构中传播能量衰减很少,因此可以对薄板结构的疲劳裂纹、分层裂纹和腐蚀破坏进行健康监测[8-11].
笔者采用Lamb波主动检测技术对飞机机翼板条的超大型铝板结构切割和冲击破坏产生的损伤进行检测,利用Hilbert变换来分析回波信号的能量或幅值变化,研究面波的传播规律并画出波的包络图,进而对航空铝板的损伤进行健康监测.研究结果表明,Lamb波方法不仅可用于飞机机身的铝板损伤检测,也可以用在其他大尺寸的铝板部件,甚至是复合材料构件.该方法填补了目前超声波无损检测领域中超大型铝板检测的空白.
1 理论背景
1.1 Lamb波
当弹性作用力施加到自由边界的薄板表面上便产生了弹性波.弹性波在板的两个上下自由边界上均会发生反射,叠加后就形成了Lamb波[12],或者叫导波(见图1).霍勒斯·兰姆于1917年提出Lamb理论,但是真正在工程上得到应用却是很多年以后.Lamb波在整个薄板体内作椭圆运动传播,由于薄板结构平面所限而形成的纵波与横波组合的Lamb波有对称的S模态 (S0,S1,S2,…)和反对称A模态(A0,A1,A2,…)两种模态(见图2),对称模态(S波,扩展波)Lamb波的特点是沿薄板中心质点作纵向振动,上下表面质点作椭圆运动、振动相位相反并对称于中心.非对称型(A型,弯曲波)Lamb波特点是薄板中心质点作横向振动,上下表面质点作椭圆运动、相位相同,不对称.如果波长和板厚是已知的话便可以计算出波的传播速度 [13-15].

图1 板中导波传播示意图
Fig.1 The schematic in guided wave propagation

图2 Lamb波在航空铝板中的群速度曲线(Al 2024)
Fig.2 Group velocity curve of Lamb waves in an aluminum plate (Al 2024)
1.2 解析信号和Hilbert变换
Hilbert变换是运用Hilbert线性算子把接收到的信号转换成一种解析信号[16].信号经Hilbert变换后,在频域各频率分量的幅度保持不变,用Hilbert变换描述幅度调制或相位调制的包络、瞬时频率和瞬时相位会使分析简便,解析信号xa(t)是真实信号x(t)通过式(1)的Hilbert变换得到[17-18]:
xa(t)=x(t)+iH{x(t)}.
(1)
式中:H{x(t)}是Hilbert算子.
解析信号也可以写成下面极坐标的形式:
xa(t)=re-iθ.
(2)
式中:i和θ分别是半径和分析信号的相位角;r是解析信号的包络最大幅值.
Hilbert算子的定义式为
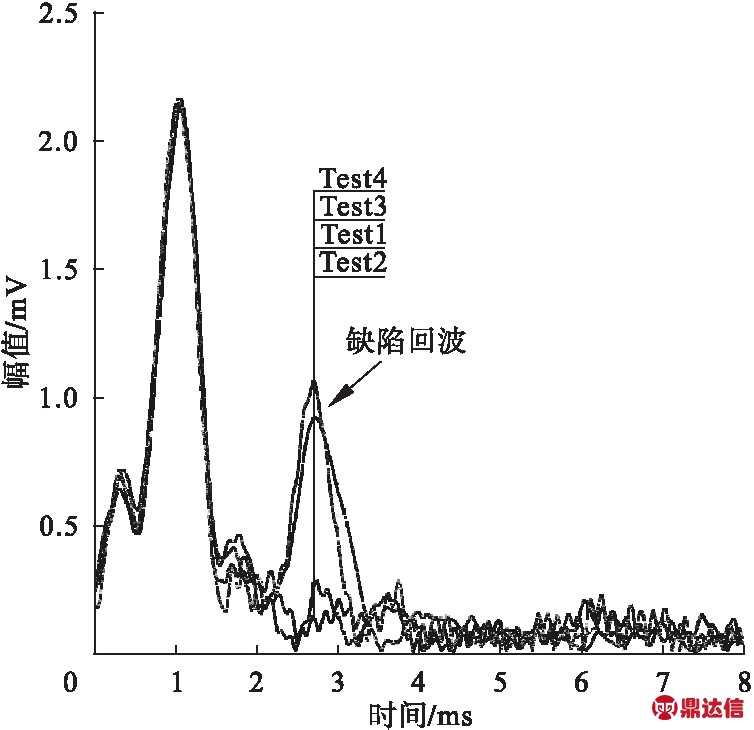
(3)
公式也可以在卷积理论来定义:
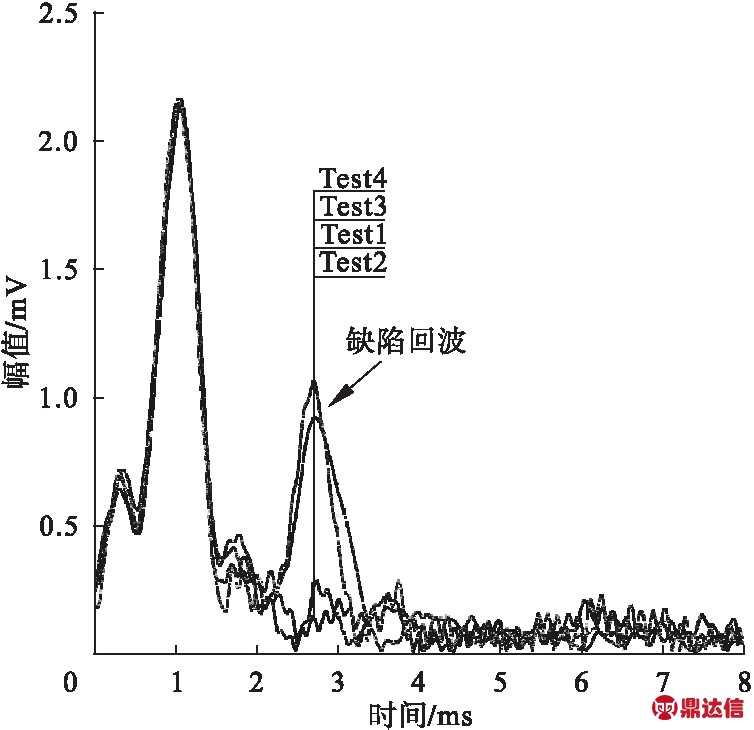
(4)
2 试验装置
波音737飞机机翼由两种不同类型的铝板(Al 2024和Al 7075)制成,通过铆钉连接在一起.Al 2024板为1 mm厚并且用复合蜂窝芯支撑,Al 7075板为2.5 mm厚.
本项研究是模拟飞机机翼受到冲击破坏产生切割和变形两种损伤并进行检测.试验设置如图3所示.
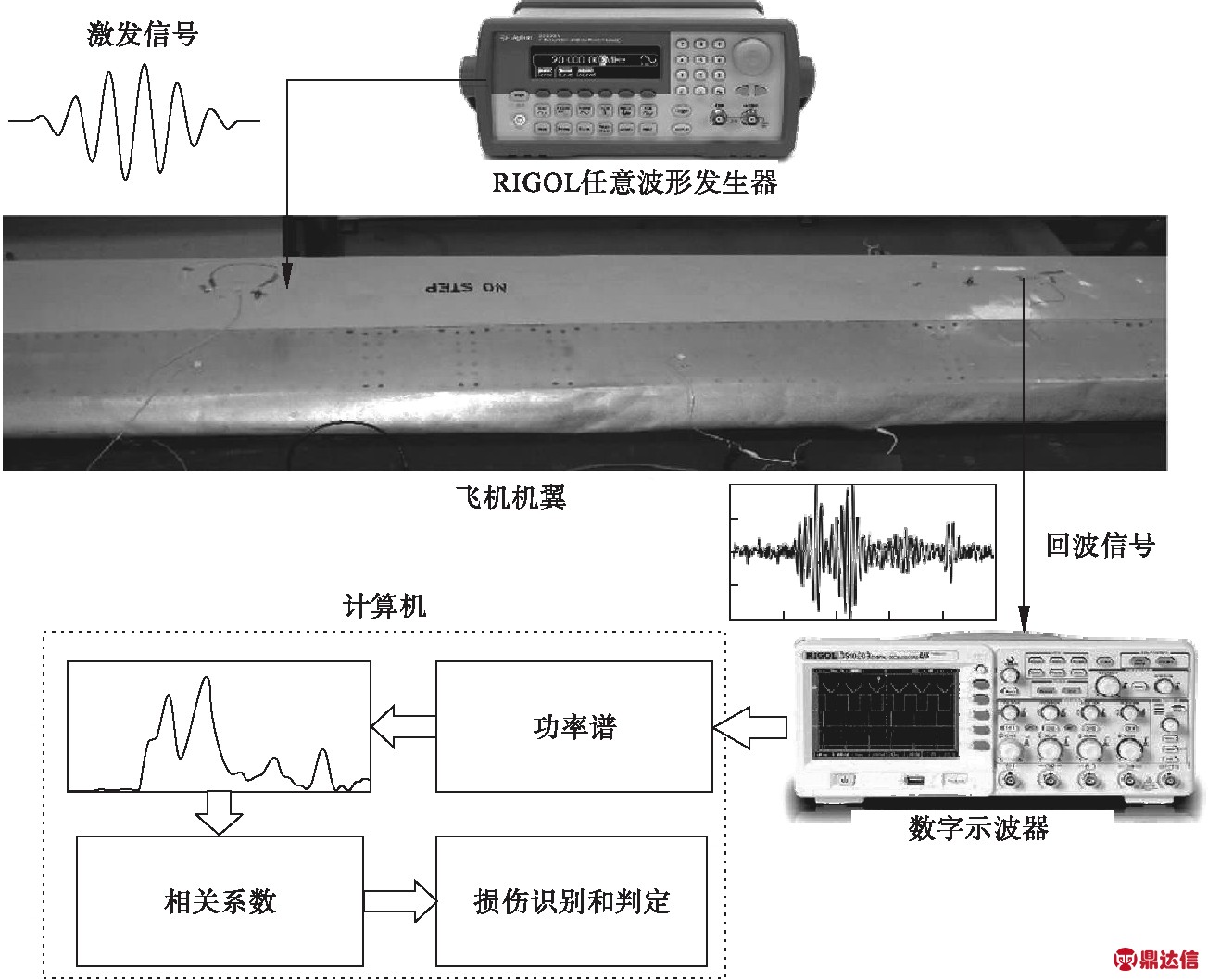
图3 试验装置
Fig.3 Experimental setup
任意波型发生器(AWG)(Agilent 33220A)用于产生经过汉宁窗调制5个循环周期的Lamb波.激发信号的中心频率分别为7 kHz、40 kHz和230 kHz,用于激发出不同模态的Lamb波,激发和接收传感器均为粘结在铝板表面的PZT传感器.Lamb波沿着铝板表面传播被其他的PZT接受传感器接收,通过使用数字示波器(Rigol 1104B)将PZT传感器接收到的信号输出并且数字化移到计算机中.信号的Hilbert变换和分析通过使用MATLAB程序来实现.根据图2的群速度曲线,激发频率确定以后根据群速度可确定出 A0和 S0模态Lamb波.
3 试验过程及结果分析
3.1 Al 2024铝板的截面切割损伤识别
Al 2024铝板的截面厚度为1 mm,并用蜂窝复合结构支撑.如图4、图5、图6所示,在铝板上人工制作三个不同长度的切口以模拟深而严重的微裂缝,其中字母P表示PZT传感器.首先形成18 mm长的切口,具有5 mm宽度.随后,切口的长度增加到55 mm和88 mm.4个PZT传感器粘贴到Al 2024截面的表面.Lamb波由P1激发,激发频率为7 kHz,波沿铝板传播由其他PZT传感器监测接收回波信号.根据铝板的频散曲线可以得出,当激发频率为7 kHz时会激发出A0模式的Lamb波.其他相关的试验参数见表1.
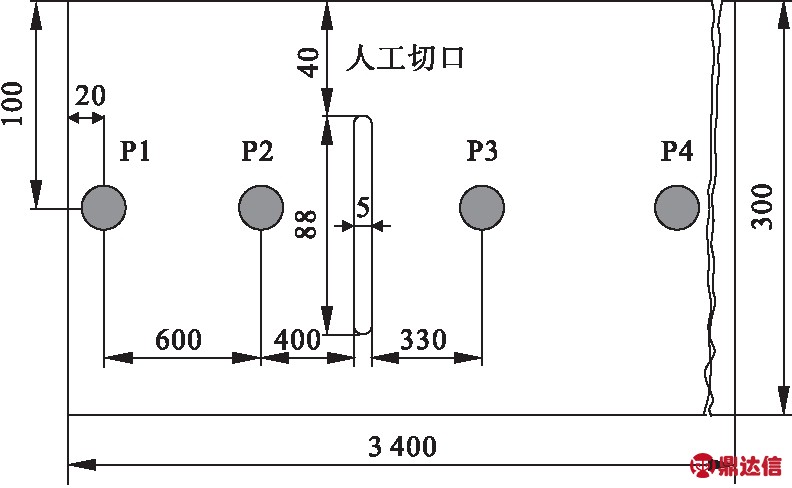
图4 切口损伤试验布置示意图
Fig.4 Schematic plan for cut damages
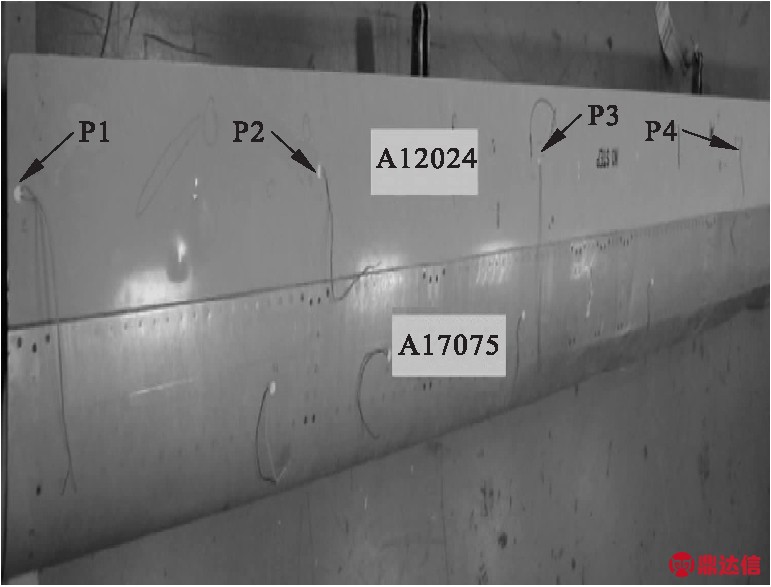
图5 两种不同的铝板制成的飞机机翼
Fig.5 A slat which was made of two different aluminum alloys

图6 切口长度55 mm
Fig.6 Cut with 55 mm length
表1 Al 2024铝板试验参数
Table 1 Al 2024 aluminum test parameters mm
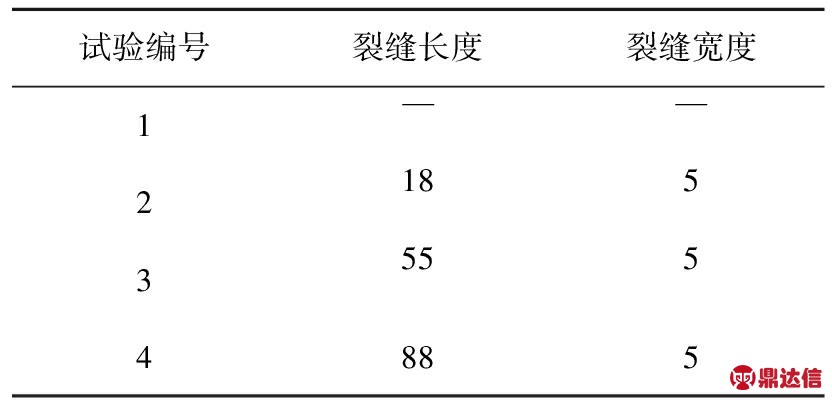
如图7所示,P1传感器激发出Lamb波,理论上经过一定时间延迟会被P2传感器接收到,并继续朝向切口和P3传感器传播然后被接收到.传播过程中如果Lamb波遇到任何边界条件就会产生反射.由于切割损伤产生了新的明确边界,传感器能收到明确的反射信号.实际测试中对信号的分析也证明这一点.
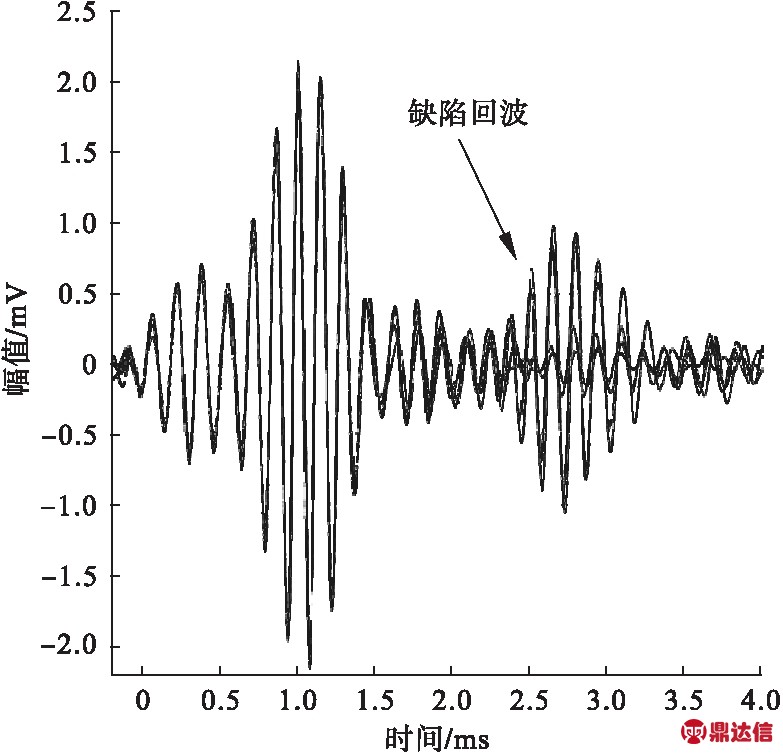
图7 P2接收到的P1激发A0模态信号的回波信号
Fig.7 The signals received from the P2 when the P1 was excited at the A0 mode
为了更好地分析信号,对P2、P3传感器接收到的信号进行Hilbert变换,结果如图8、图9所示.根据图7第一组波的到达时间来计算Lamb波的群速度.波从P1传感器传播到达P2传感器被接收到耗时1.07 ms,P1和P2传感器之间的距离为60 cm.计算Lamb波的速度为561 m / s.切口的位置是通过波在1.07~2.71 ms能够到达和返回的距离来计算确定的.损伤位置经过计算确定为距P2传感器 40.12 cm,计算值与实际值40 cm距离基本一致.
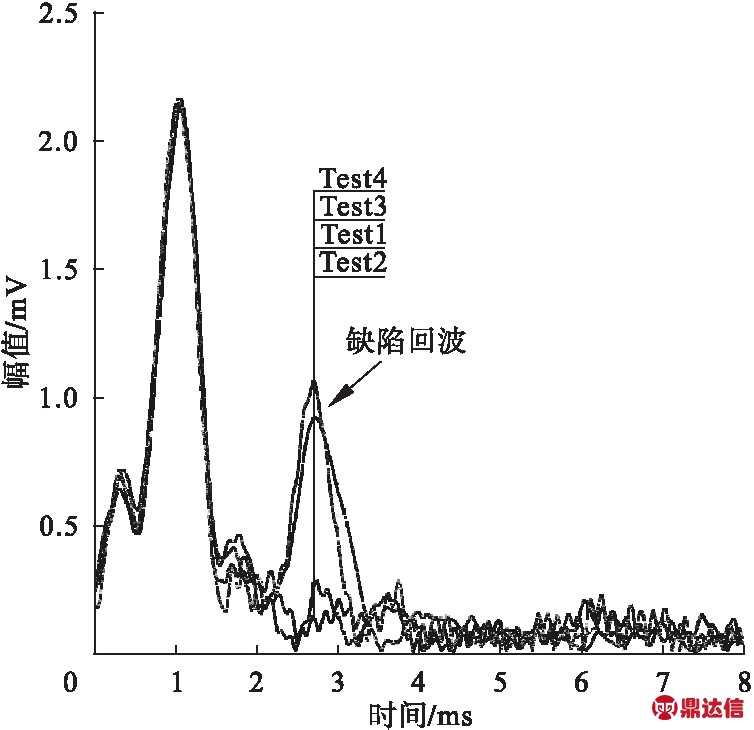
图8 P3信号的Hilbert变换能量(A0模态)
Fig.8 The Hilbert energy of the signals received from P3(A0 mode)
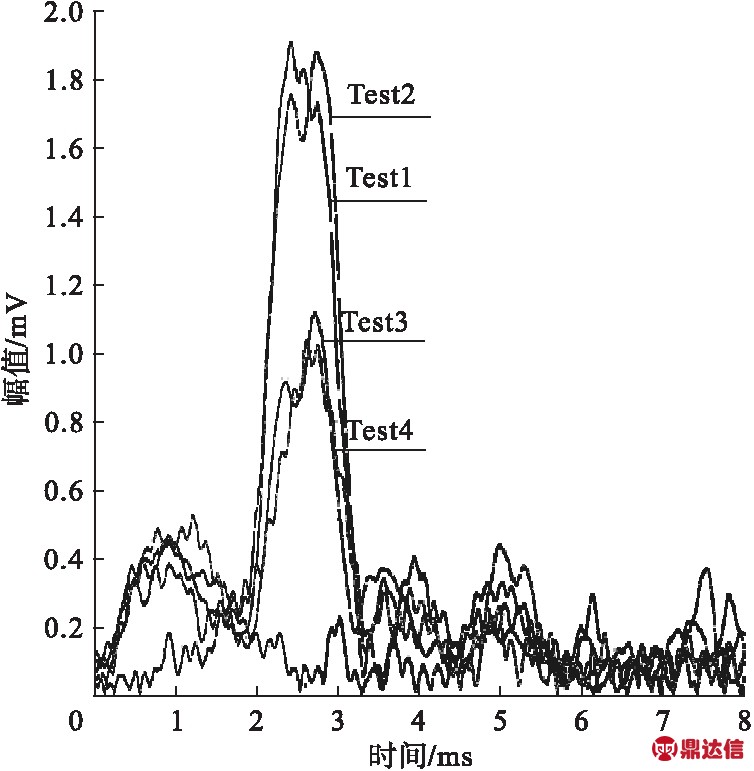
图9 P2信号的Hilbert变换能量(A0模态)
Fig.9 The Hilbert energy of the signals received from P2(A0 mode)
切口损伤尺寸与回波信号能量衰减关系如图10所示.从图10可以看出,P2传感器接收到的信号当没有切口或者切口非常小(小于18 mm)时,单波峰在8 ms内达到P2,当损伤切口长度达到55 mm时,出现第二波峰被P2传感器接收到,当损伤切口达到88 mm时,第二波峰的幅值比切口为55 mm接收到的信号幅值明显增加.P3信号的变化幅值和P2的明显不同,首次到达的信号幅值随着切割长度的增加而减小.无切口时和切口的长度为18 mm第一到达波的振幅具有最大值,当切口长度达到55 mm时,它们的Hilbert能量幅值显著降低,当切口的长度为88 mm时幅值最小.可以解释为由于切口的存在,一部分波的能量被反射回去导致P3传感器接收到的波的能量随着切口尺寸的增大而减少.
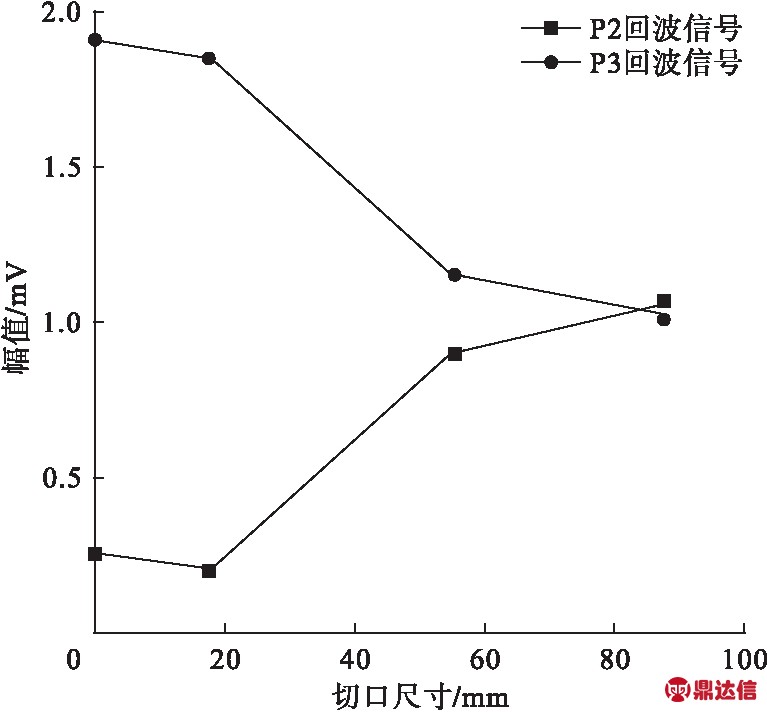
图10 切口损伤尺寸与回波信号能量衰减关系图
Fig.10 The correlation between the Hilbert energy and the cuts size
3.2 Al 7075铝板冲击损伤识别
Al 7075铝板的截面厚度为1 mm,传感器布置如图11、图12所示,铝板上人工制作不同面积冲击损伤见图13,其他试验参数见表2.对Al 7075截面进行检测时,根据图2 Lamb频散分布曲线,确定A0和S0模态激发频率分别为40 kHz和230 kHz,在两个频率处波速几乎没有衰减.在P5传感器激发40 kHz五峰波信号,损伤区域两侧P7、P8传感器接收回波信号并用于分析研究铝板损伤情况.
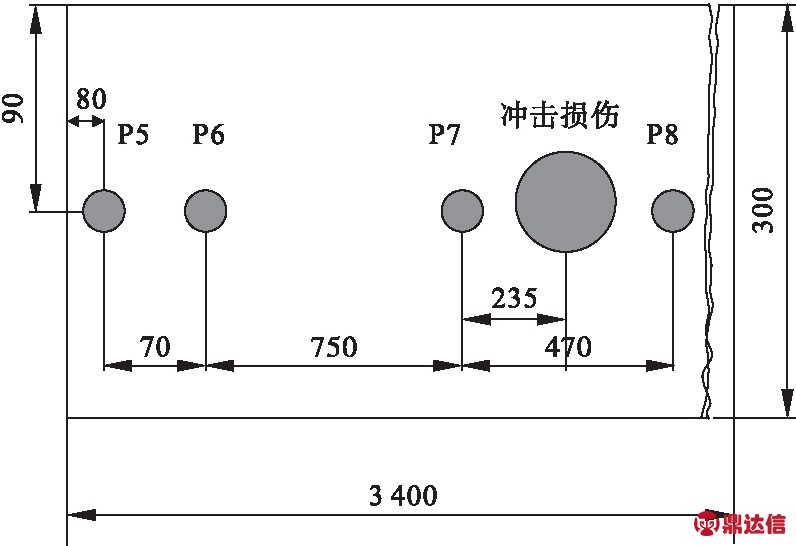
图11 冲击损伤试验布置示意图
Fig.11 Schematic plan for impact damages
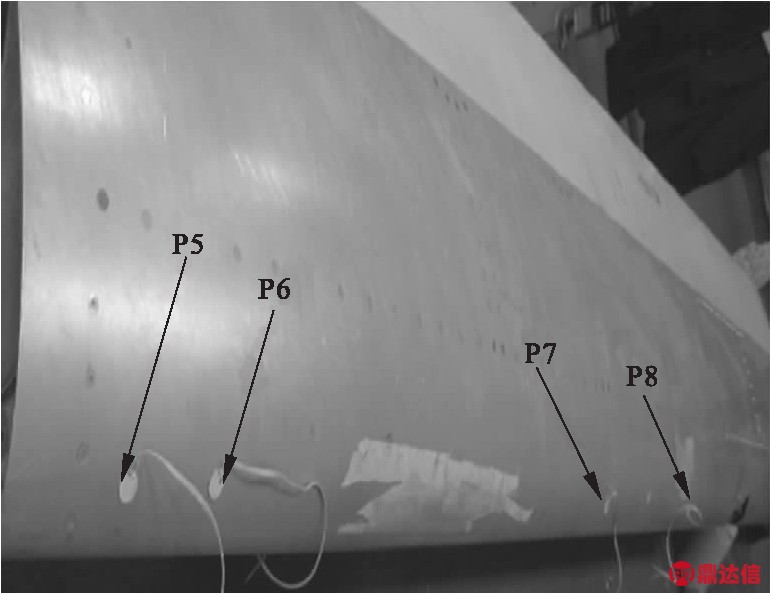
图12 飞机机翼
Fig.12 The slat (P letters shows PZTs.)
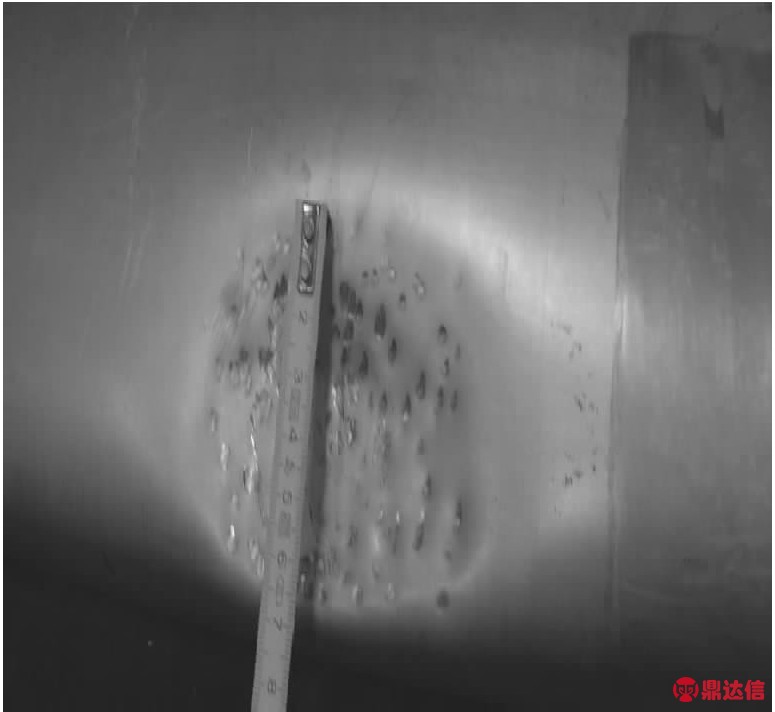
图13 冲击损伤尺寸
Fig.13 Close up view of the damage
表2 Al 7075铝板试验参数
Table 2 Al 7075 aluminum test parameters
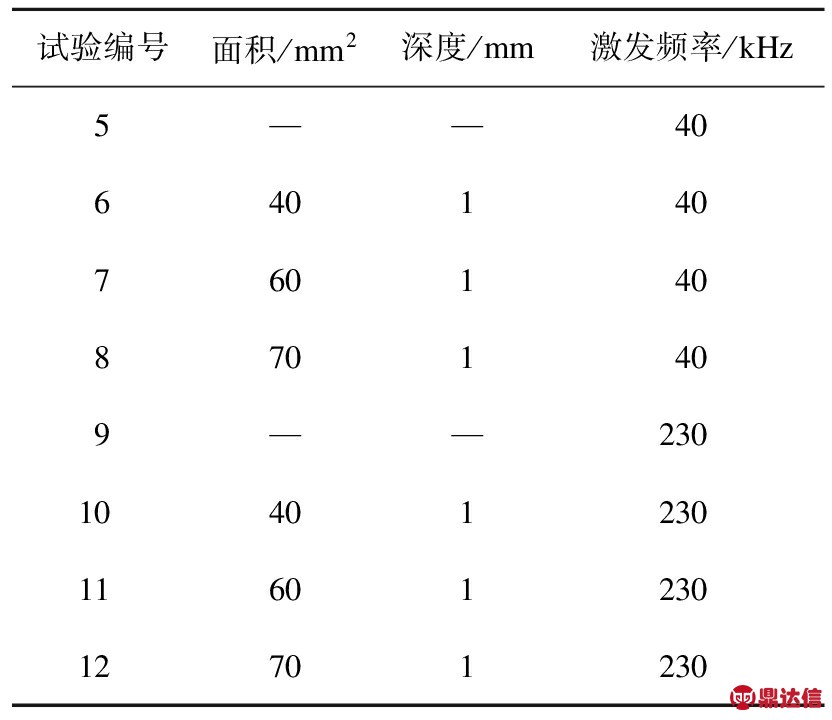
3.2.1 P7传感器接收的A0模态信号分析
P7号传感器接收到的信号如图14所示.对P7接收到的回波信号在1.58~1.68×10-3 s时间段做Hilbert变换.为了研究信号的衰减,图15给出了0.5~2.5 ms时间段信号的Hilbert变换能量衰减情况.根据第一波峰最先到达的时间可以计算出Lamb波的群速度为1 065 m/s.由于波总是以最小的衰减移动,所以它们到达边界以后产生反射在接收信号中会产生附加的波峰.Hilbert变换的特征幅值在冲击损伤后显著变化,然而回波信号并没有出现由冲击损坏区域产生的新的峰值.
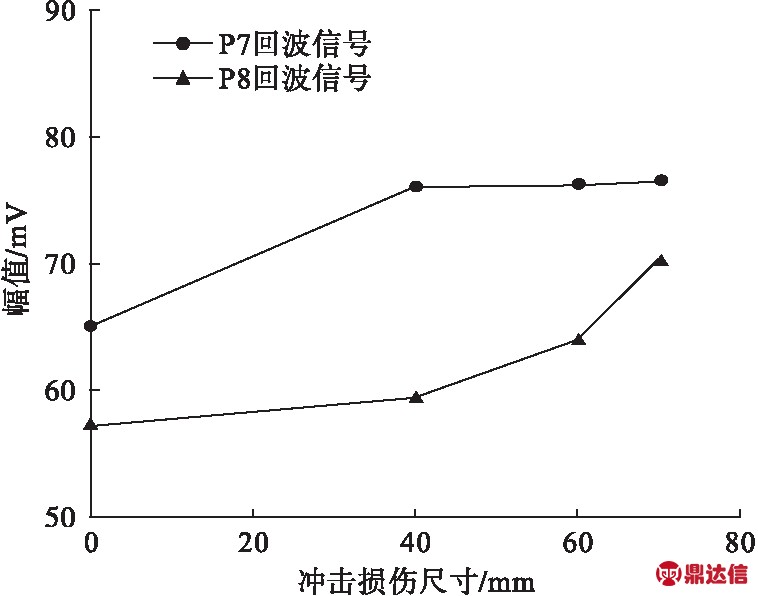
图14 P7接收到的P5激发A0模态信号的回波信号
Fig.14 The signals received from the P7 when the P5 was excited at the A0 mode
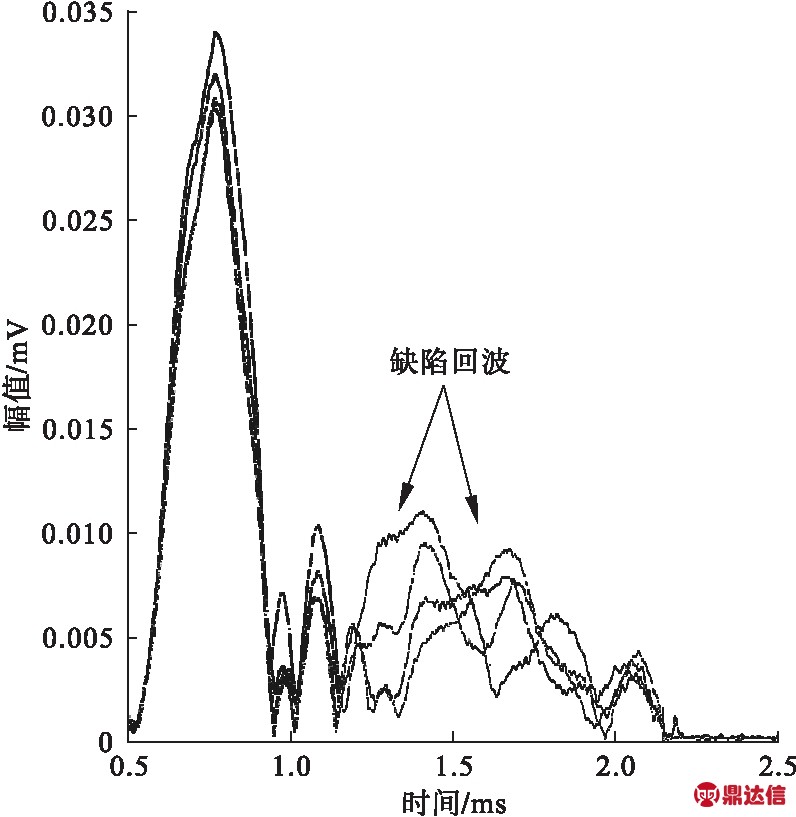
图15 P7信号的Hilbert变换能量(A0模态)
Fig.15 The Hilbert energy of the signals received from P7(A0 mode)
这些结果表明,冲击损伤使表面变形,但没有产生之前切割情况下看到的明显边界条件而产生新的回波峰值.图16为时域信号的幅度和冲击损伤尺寸之间的关系,可以研究信号的衰减和损伤尺寸之间到相关性.从图中可以看出,信号能量的衰减随着冲击损伤尺寸的增加而减小.
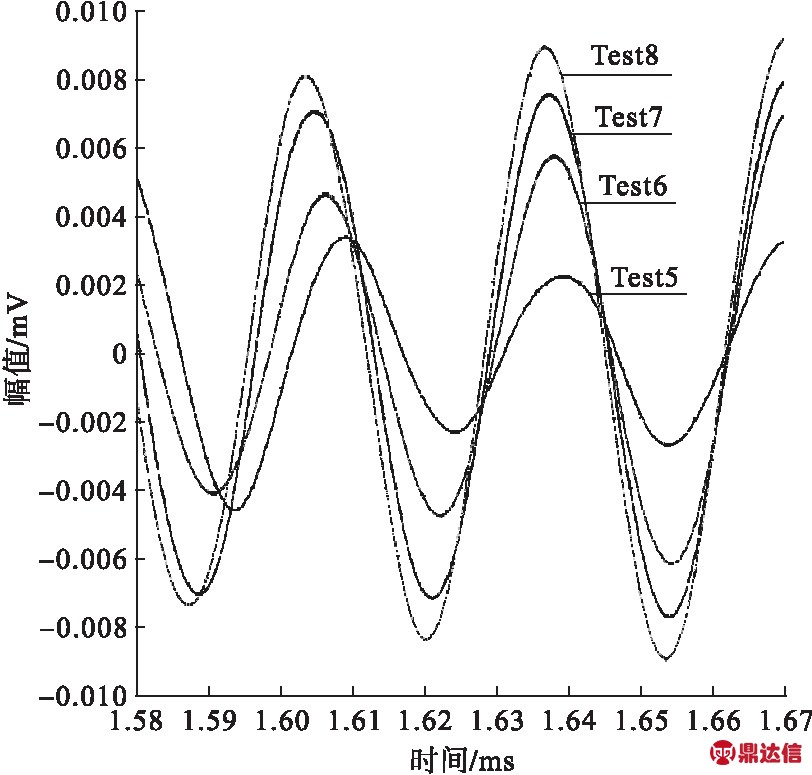
图16 衰减与冲击损伤尺寸关系(P5激发P7接收)
Fig.16 The correlation between the Hilbert energy and the cuts size.(the signals received from the P7 when the P3 was excited )
3.2.2 P7、P8传感器接收的S0模态信号分析
为了进一步验证A0模态检测出的结果,笔者还进行了S0模态的试验.图17、18分别为P7传感器接收到的由P5传感器发出的S0模态信号和Hilbert变换的能量幅值变化关系.0.17 ms延迟时间后第一波峰到达,计算群速度为5 124 m/s.第一个波峰之后的多个波峰是波在边界的反射并且沿着表面以很小的衰减传播形成的,冲击损伤产生后没有产生明确的新的波峰.
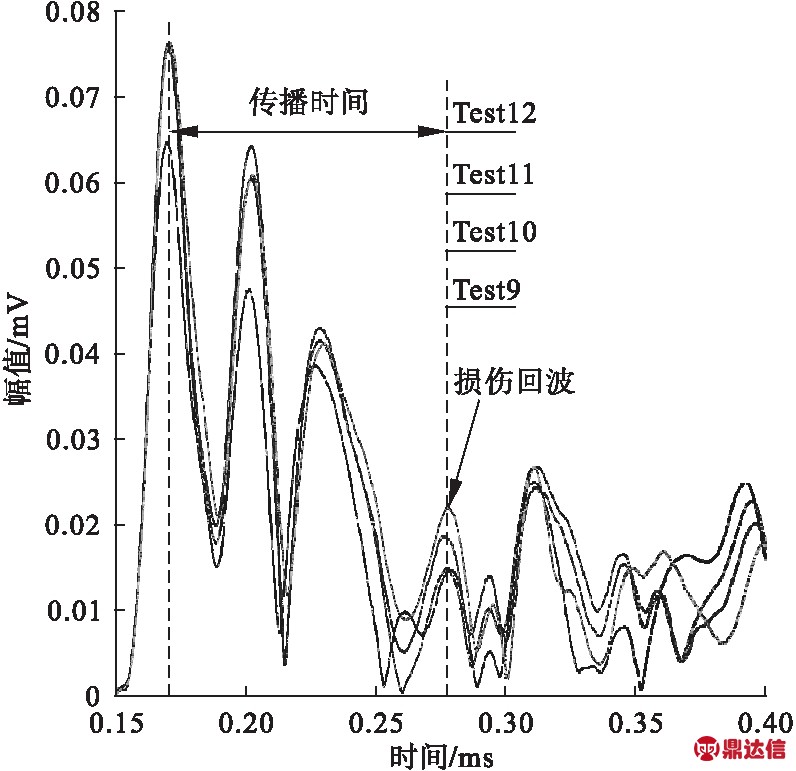
图17 P7信号的Hilbert变换能量(S0模态)
Fig.17 The Hilbert energy of the signals received from P7(S0 mode)
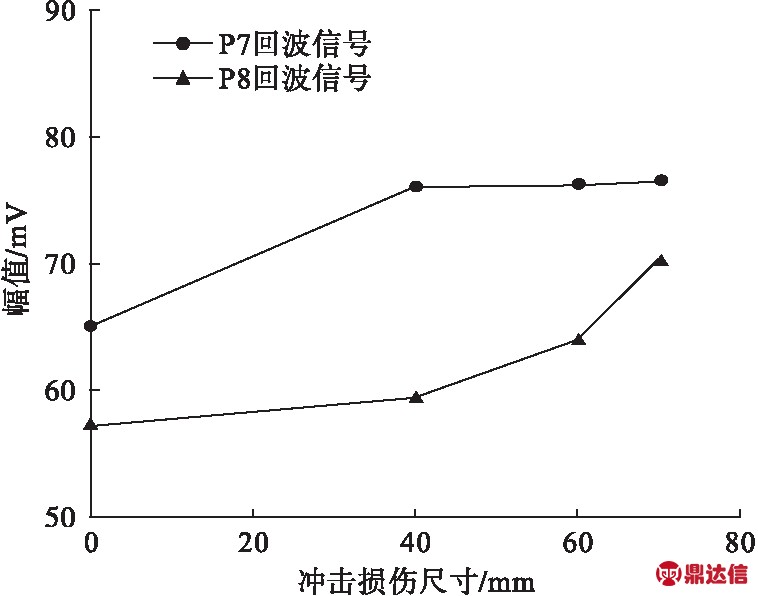
图18 冲击损伤尺寸与回波信号能量衰减关系
Fig.18 The correlation between the attenuation and the impact damage size
图18中的第四波峰的幅值随着损伤面积的增加而增大,表明损伤对波的峰值产生了明显影响.P7接收到的信号能量由于没经过冲击损伤,主波峰能量幅值变化很少, P8接收到的信号能量在冲击损伤尺寸较小的时候幅值缓慢增加(40 mm以下),然后主波峰能量幅值随着冲击损伤尺寸增加而增加.
根据A0和S0模态的研究结果可以得出,冲击损伤不会产生切口损伤那样明显的边界条件,但是可以在损伤部位传递一定的A0、S0模态导波.所以对冲击损伤可以根据能量变化来确定损伤的程度,但是要准确定位还需要进一步的研究.
4 频散曲线和Lamb波传播速度分析
表3是根据试验测到Lamb波传播速度和理论计算的传播速度.从表中可以看出,二者数值符合得很好.
表3 根据试验数据和离散曲线估计Lamb波速度
Table 3 The Lamb wave speeds estimated from experimental data and dispersion curves
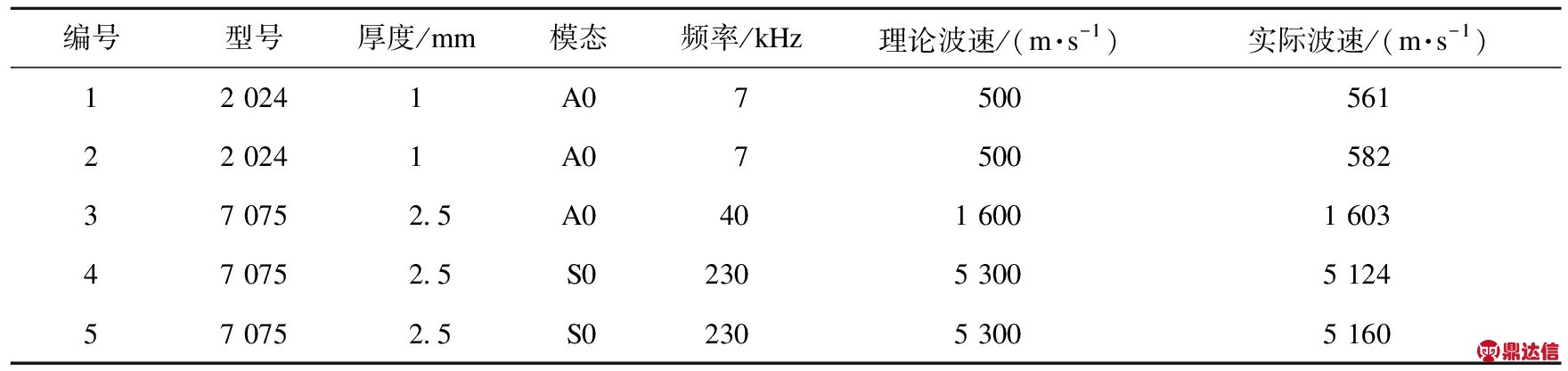
5 结 论
(1)有蜂窝状复合材料芯支撑Al 2024号铝板,随着激发频率的增加波的能量衰减也随之增加.当使用较低的激发频率作为激发频率时或者铝板部分有支撑时,PZT传感器的设置距离应该减小.
(2)在不同尺寸的航空铝板产生切割和冲击损伤两种类型的损伤.切割创建新的边界, Lamb波在新边界产生反射.可以从反射波的到达时间以计算损伤的位置.能量的损失随着切割的长度而增加.
(3)Lamb波经过冲击损坏区域之后没有产生明显的波峰,只有能量衰减损失.可以从Hilbert变换能量特性的变化来检测冲击损伤程度,但是不能估计损伤位置.切割损伤很容易地被检测出,并且可以高精度估计它们的位置.