摘要:为研究舱室模型内爆炸载荷下预制孔板的动态响应,实验验证舱室模型内偏置孔板和均匀孔板的变形规律,并与无孔板的变形规律对比,同时建立了一种模拟舱室的仿真模型,进行内爆炸载荷下的数值计算,分析典型测点内爆炸冲击波的分布,研究预制孔板的挠度变形规律。结果表明:预制孔板的局部强度减弱对挠度变形的增益大于泄爆效应的影响,内爆冲击波在舱室模型内部存在反射和汇聚现象,并在毫秒量级后期存在准静态特性,模拟结果与实验结果一致,同时预制孔板不同区域减薄率存在差异。研究结果可以为舱内爆炸冲击波-破片耦合损伤作用的机理分析提供依据。
关键词:舱室模型;预制孔板;内爆冲击波;挠度增益;减薄率
半穿甲反舰导弹是现有大型舰船的主要威胁武器之一,能够穿透舷侧在舱室内部爆炸,导弹战斗部作战效能更高。舱室内爆炸冲击波与空中爆炸冲击波的传播分布显著不同,舱室内爆炸时板架结构的动态响应问题更加复杂。除舱室内爆外,涉及内爆冲击波研究的还有管道内爆[1]、建筑内爆[2]、坑道内爆[3]等。侯海量等[4]采用缩比舱室模型研究舱内爆炸冲击载荷特性;孔祥韶[5]为验证Autodyn的Euler-FCT求解器数值仿真精度,对舱壁有开孔的舱室模型进行了舱内爆炸实验。
Aune等[6]用激波管代替爆炸载荷加载预制孔板,在考虑边界条件下研究孔板的变形和失效;Rakvåg等[7]用可控压力装置,对不同形状的预开孔板进行压力载荷实验,并与数值仿真结合,研究冲击波和破片的耦合作用;蒋建伟等[8]在空爆条件下对预制孔靶板的塑性变形规律开展研究,给出靶板中点挠度预测公式。本研究以参考破片尺寸设计的预制孔板为研究对象,采用Autodyn有限元软件进行内爆数值模拟,并结合舱室模型内爆实验研究预制孔板在冲击波作用下的变形规律。
1 实 验
1.1 实验预制孔板设计
设计实验预制孔板的主要依据为典型反舰导弹战斗部自然破片的飞散规律和预制板的受载面积,即在无孔原始板上打孔,得到预制孔板。以典型100 kg反舰导弹战斗部为例,战斗部壳体爆炸后形成自然破片,根据Mott分布计算自然破片总数和所有破片的平均质量,选取平均质量相当的破片为研究对象。由于破片形状有极大的随机性,根据现有破片形状规律,假设战斗部壳体材料为高强度钢,得到破片的展现面积,从而得出预制孔面积。通过上述方法得到预制孔的形状、数目、分布和大小(孔面积)。
拟定实验药量和舱室模型内装药与预制孔板的爆距,根据比例定律,得出100 kg战斗部和实验装药峰值超压相同时的等效爆距;选择战斗部自然破片合理的飞散角,得到破片整体作用面积和破片单位面积的分布密度,分布密度单位为个每平方米,再确定实验无孔原始板面积,进而得到预制孔数量。考虑实验情况和工程加工的可操作性,选定预制孔的形状和分布,此时在无孔原始板上的打孔方式已明确,最后得到预制孔板。预制孔板设计流程如图1所示。
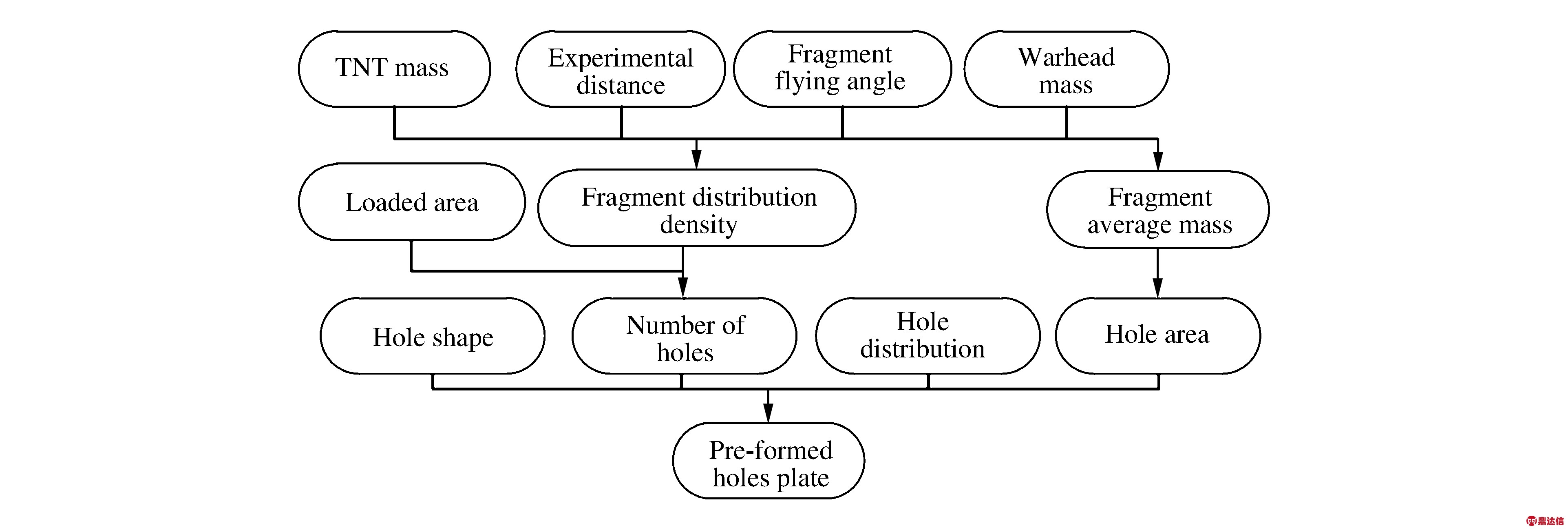
图1 预制孔板设计流程
Fig.1 Design flow of pre-formed holes plate
实验用药为135 g TNT,爆距为500 mm,预制孔板尺寸为680 mm×680 mm,预制孔板实际受载面积为500 mm×500 mm,预制孔形状为圆形,预制孔数量为9个,预制孔分布种类有偏置分布和均匀分布两种,预制孔直径为24 mm。同时预制孔位置避开了目标板的几何中点,当目标板只发生挠曲而没有破口时,这种布置能够方便测量目标板的最大变形挠度。
1.2 实验目标板变形机制分析
实验舱室模型为两端开口型箱体结构,长1 m,开口面积为0.5 m×0.5 m,实际受载体积为1 m×0.5 m×0.5 m。舱室开口处焊有外接法兰板,预制螺栓孔连接目标板,目标板固定在夹板和法兰板中间,夹板内部尺寸保证目标板受载面积和变形区域为0.5 m×0.5 m,周向4个壁面采用10 mm厚的高强度钢板和加强肋板组合的形式,保证小当量装药内爆时,舱室模型整体不变形。目标板厚度为1.8 mm,每组实验左、右两个目标板均一致,实验装药中心放置,从而保证装药到两个目标板的距离相同。第1组实验为左、右两个无孔板,编号为1-1和1-2;第2组实验为偏置孔板,编号为2-1和2-2;第3组实验为均匀孔板,编号为3-1和3-2。实验模型实际作用区域示意图和夹板安装位置分别如图2(a)和图2(b)所示。典型无孔板和预制孔板变形效果如图3所示,目标板侧视图如图4所示。
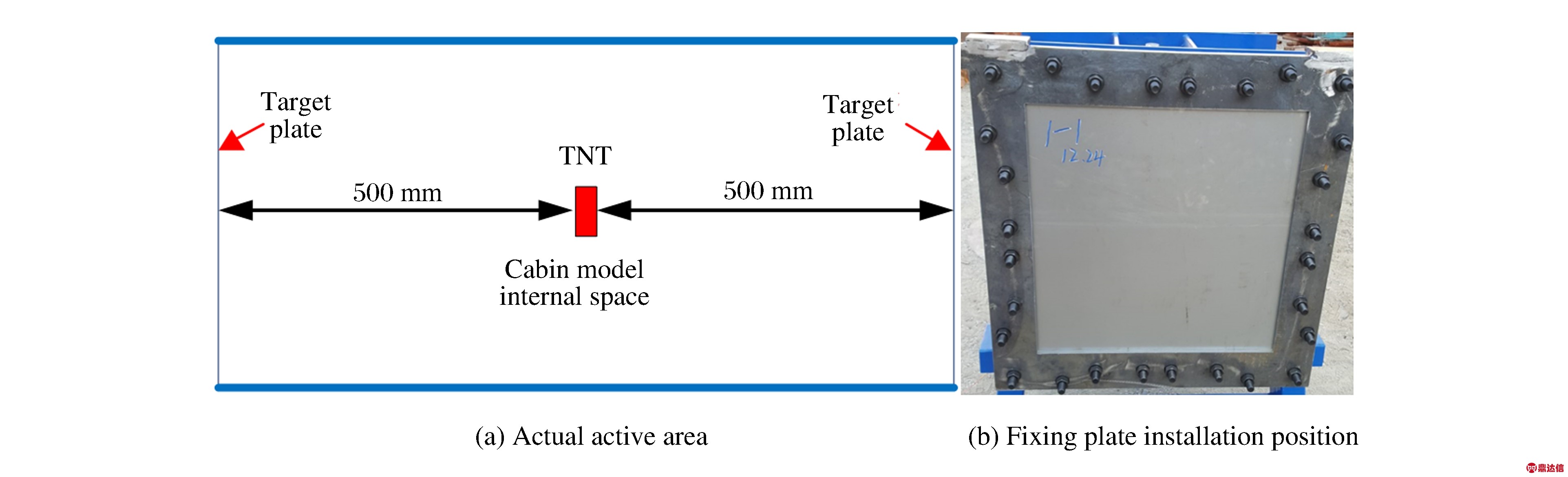
图2 实验模型
Fig.2 Experimental setup
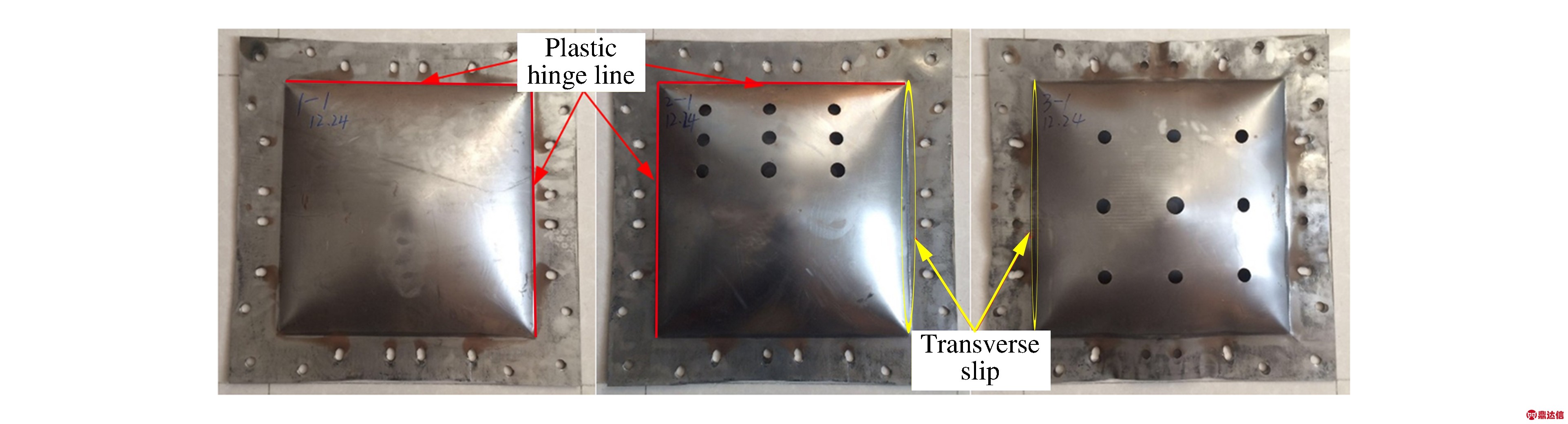
图3 目标板变形效果
Fig.3 Deformation of target plates
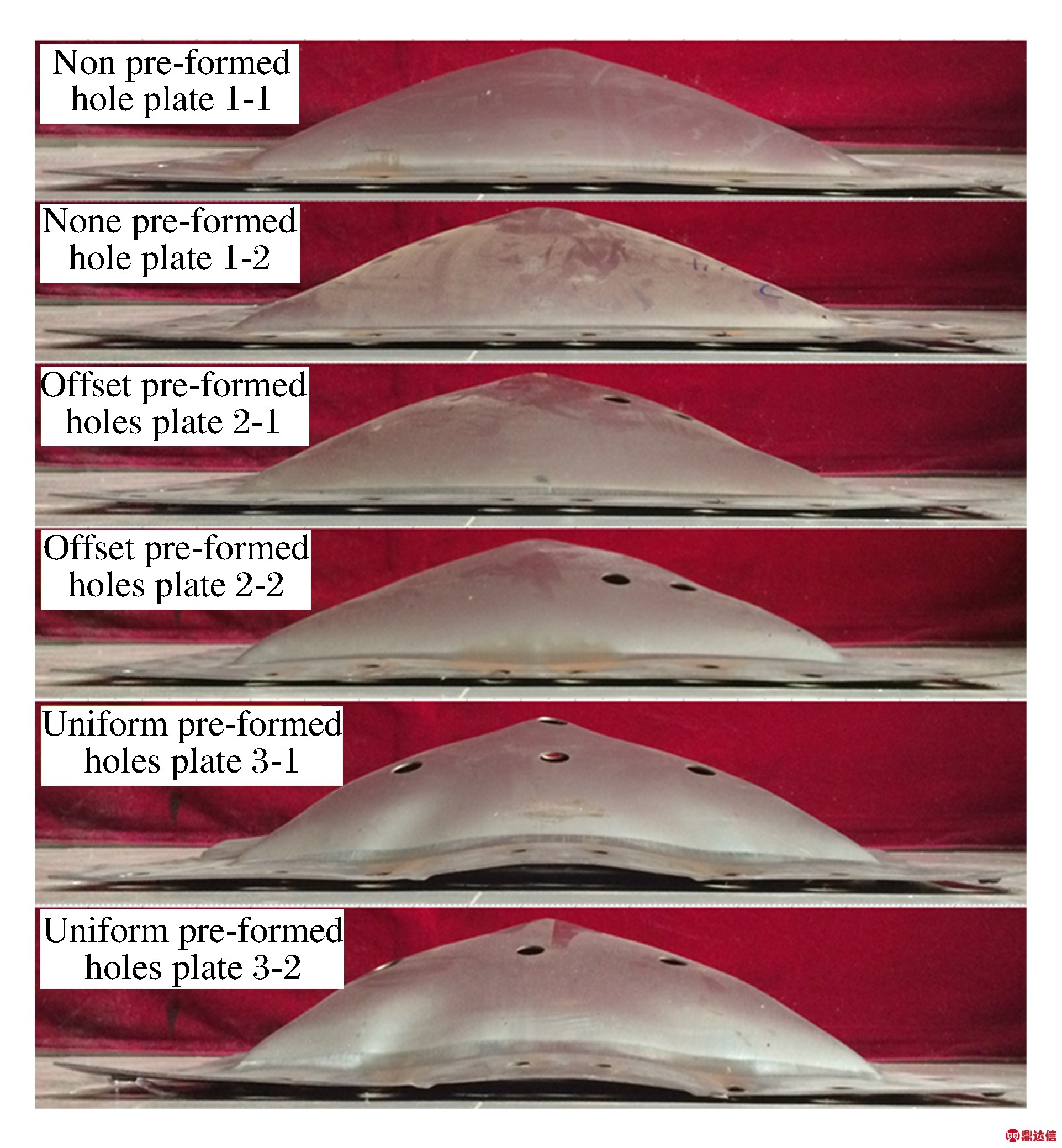
图4 目标板侧视图
Fig.4 Side view of target plates
由图3和图4可知,无孔板和预制孔板未出现结构性破坏,变形表现为夹板与目标板结合处出现塑性铰线,塑性铰线处钢板沿夹板出现横向滑移,横向滑移是以塑性铰线为边界的,目标板和夹板相互作用而产生的一个区域,为突出效果,图3中指示处塑性铰线以线表示,横向滑移以圈表示。目标板有剪切撕裂趋势,钢板受载区域减薄,目标板呈“四坡顶”式[11]变形,最大挠度均出现在平面几何中心处。不难发现目标板横截面均呈平滑式变形,没有出现不规则凹陷或凸起,部分预制孔从最初的圆形被拉伸成椭圆形。另外实验存在边界效应,即螺栓孔被受载区域“牵扯”沿径向变形严重,螺栓孔周围出现由于爆炸物作用而产生的锈蚀现象,边界效应在一定程度上影响了受载区域的变形,导致变形偏大。
统计3组实验共6个目标板的挠度变形数据,实验中心最大变形挠度如表1所示。表中挠度为每组实验两端目标板的最大挠度,3组实验挠度值的获取采用相同的修正方法,考虑因螺栓孔处异常变形、夹板连续使用强度降低等因素引起的偏差,进而获得修正值。
表1中:无孔板变形挠度最小,偏置孔板变形挠度略大,均匀孔板变形挠度最大。无孔板承受爆炸载荷时无泄爆效应,预制孔板则存在泄爆效应。无孔板整体强度均匀;由于孔的存在,预制孔板局部强度会被削弱。泄爆效应会使挠度变形减小,而局部强度弱化会促使挠度变形增大,泄爆和局部强度弱化两种效应同时存在。由实验挠度数据可知,泄爆和局部强度弱化两种效应叠加,局部强度弱化的预制孔板挠度更大,即局部强度弱化对挠度增益更大。
表1 实验最大变形挠度
Table 1 Experimental maximum deformation deflection
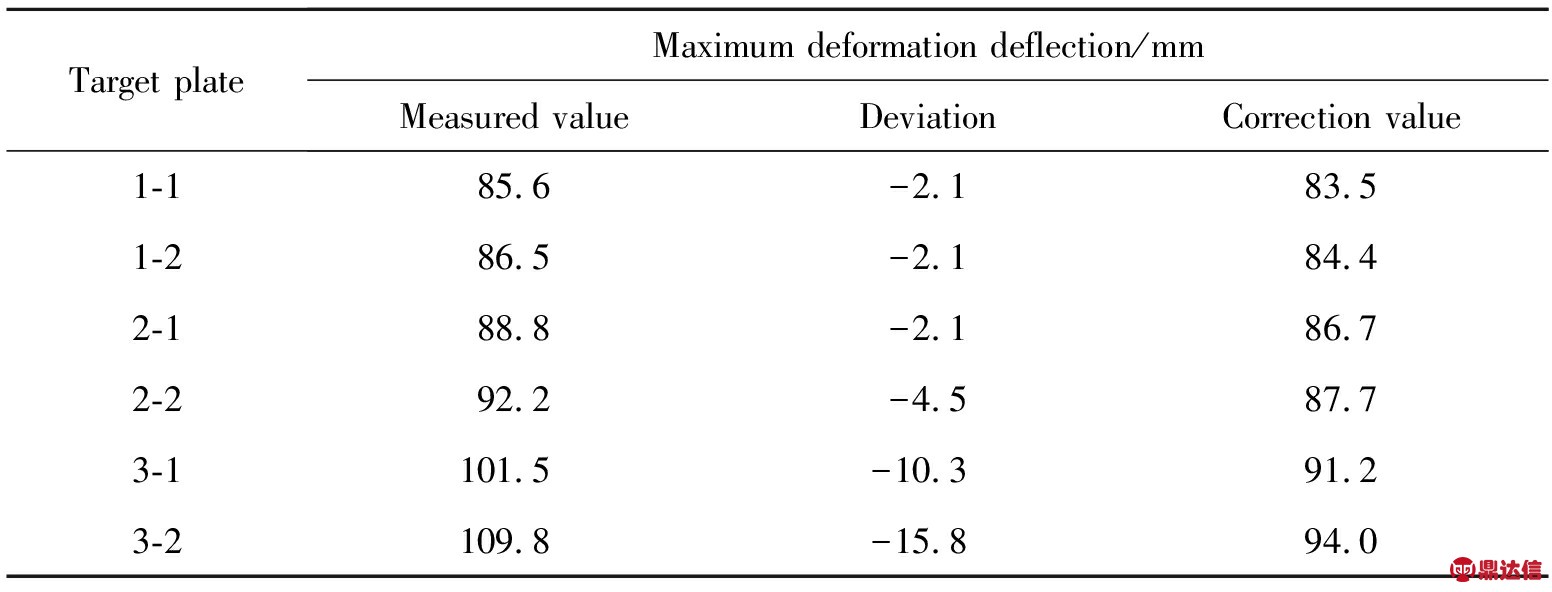
1.3 实验目标板减薄率分析
如图5所示,通过重庆LEEB里博公司的超声波测厚仪,测量3组实验目标板的减薄率:分别选定目标板顶点(挠度最大点)、中间区域典型点和边缘区域典型点进行测量,无孔板区域划分与均匀孔板相同。各区域点实测平均值如表2所示。
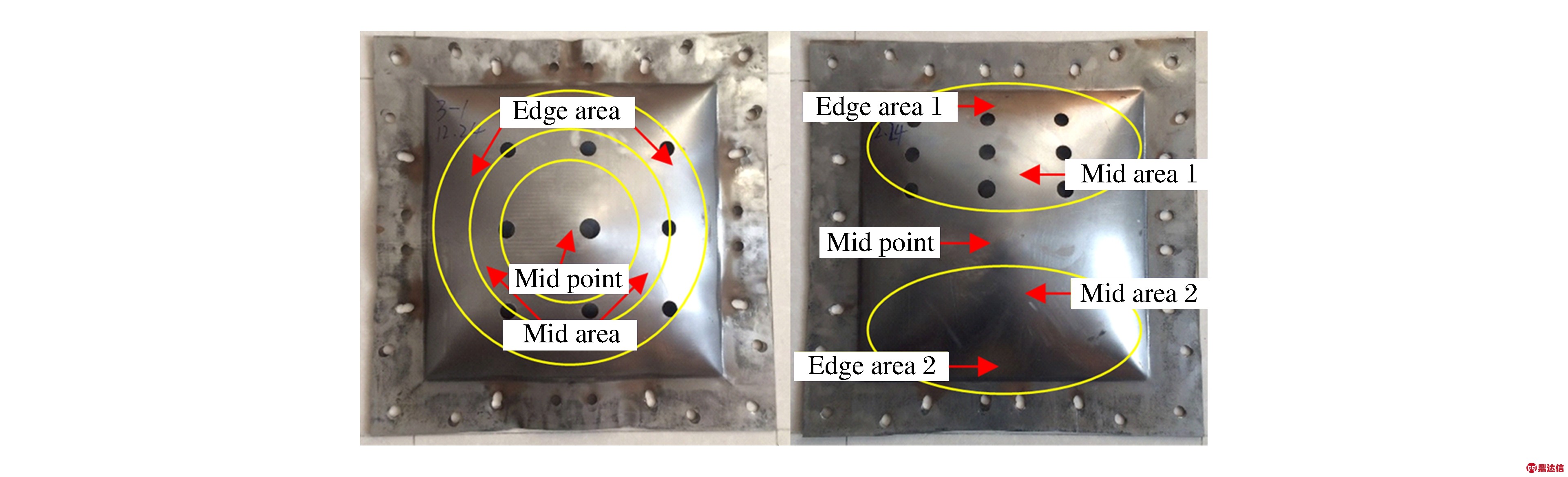
图5 减薄率测试区域划分
Fig.5 Area division of thinning rate tests
表2 减薄率统计
Table 2 Thinning rate statistics
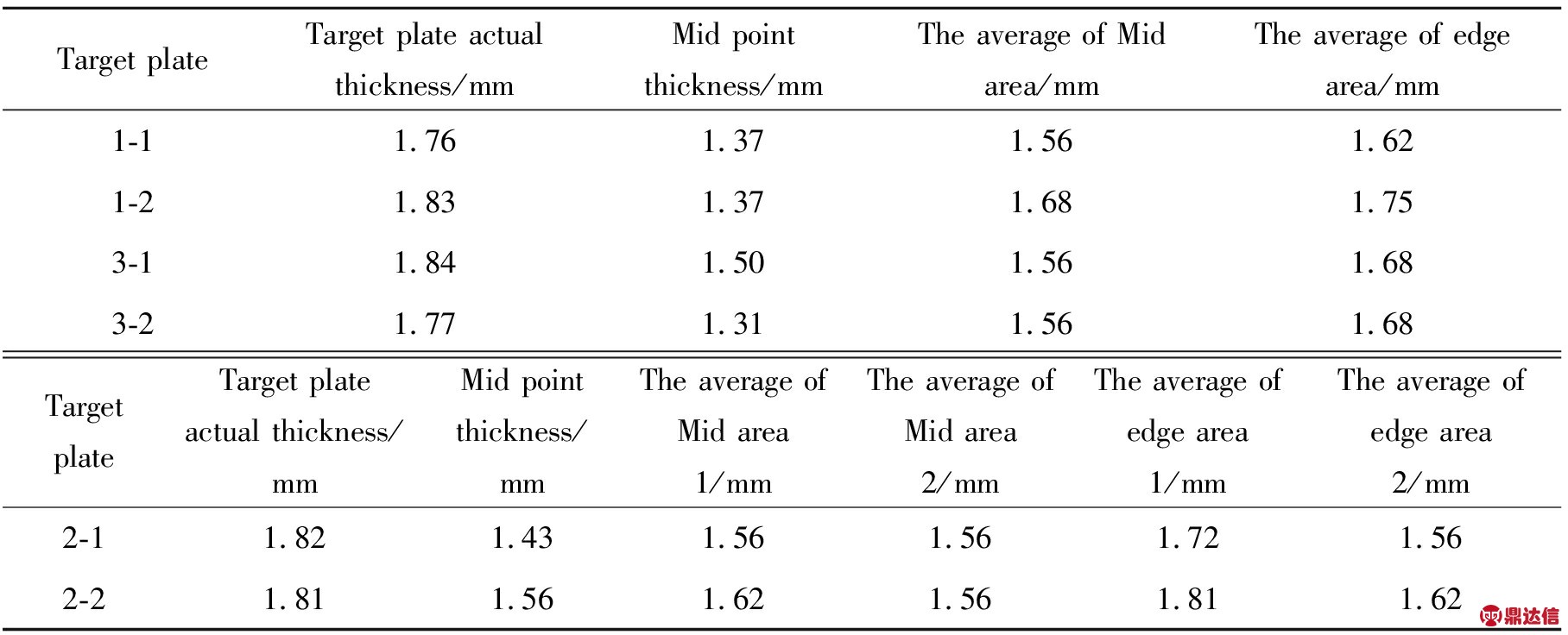
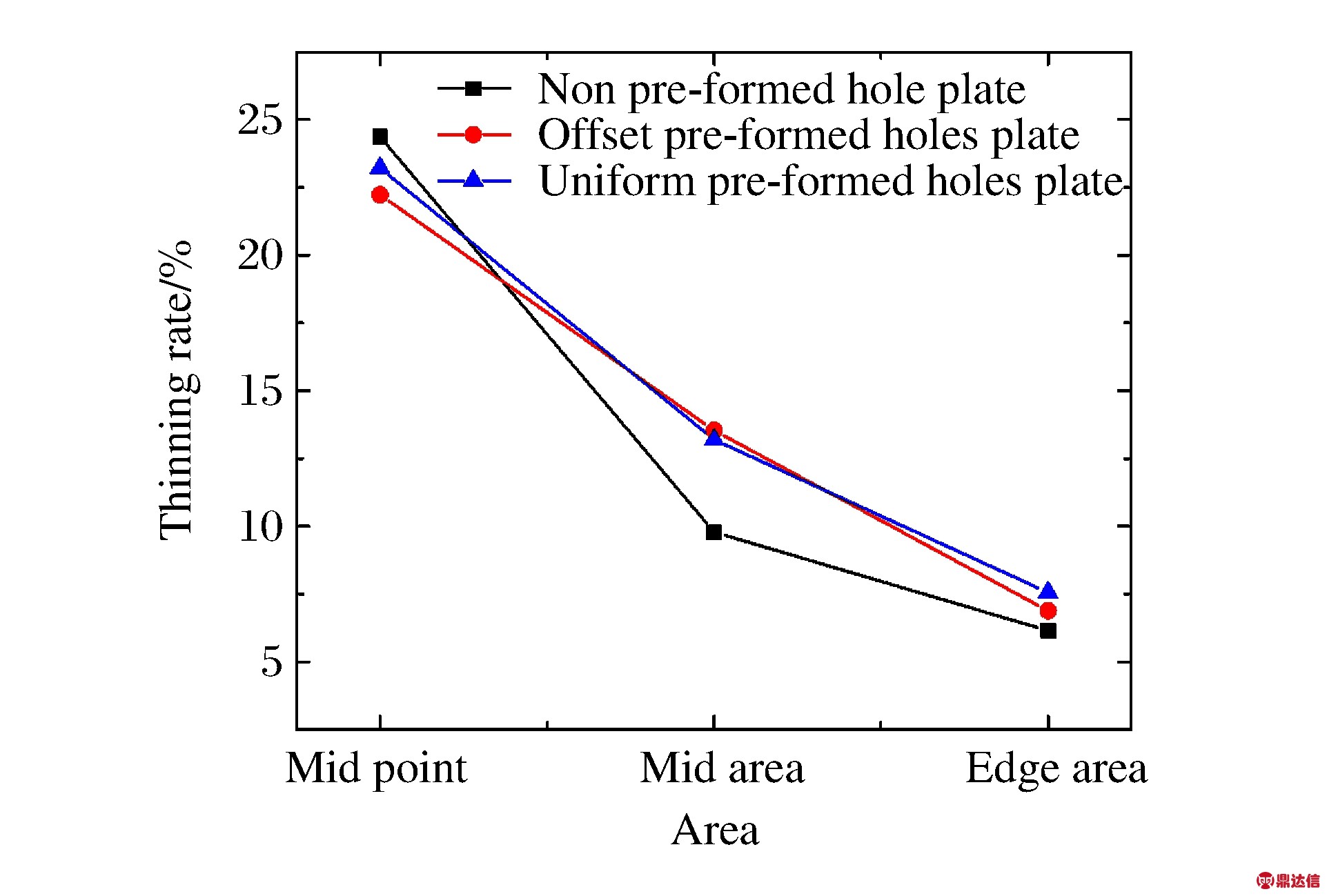
图6 各区域减薄率
Fig.6 Thinning rate in different areas
各区域(点)平均减薄率如图6所示,即将编号2-1和2-2的偏置孔板中间区域和边缘区域点的减薄率求和取平均值。需要注意的是,实际测量时应尽量避开孔边缘区域,主要选取距孔较远的成片区域,以便获得较普遍的规律,同时也方便操作仪器。由图6可知:基于本实验模型,舱内爆炸下的固支目标板在爆炸载荷下,顶点即几何中心点的减薄率最大,中间区域减薄率次之,边缘区域减薄率最低;中间区域减薄率区别较大,预制孔板减薄率大于无孔板,边缘区域无孔板减薄率也略低。
中间区域的减薄率比较典型,以中间区域为例,由于预制孔板板面存在局部缺陷,冲击波作用下容易形成应力集中,应力沿孔边缘分布,孔径被拉大,圆形孔变为椭圆孔,距离孔较远的区域板厚度并没有大幅度减薄;相反无孔板上应力分布较均匀,冲击波作用下没有明显的应力集中。基于这一规律,可以推测:当破片载荷集中且应力集中区连在一起时,板会出现破口或发生结构性损坏。
2 舱室模型和材料模型
2.1 数值计算模型
采用AUTODYN软件进行数值模拟计算,有限元模型由空气域、目标板和炸药组成。通过软件自带的边界特性模拟舱室结构,炸药采用柱形装药,放置于舱室模型中心,数值耦合方式为流固全耦合。由于模型具有对称性,因此采用1/2模型,目标板与空气域接触区域即为实际受载区域,考虑目标板会出现变形,空气域在与目标板接触的另外一侧延伸出100 mm,因此计算模型尺寸为600 mm×500 mm×500 mm,如图7所示。目标板右侧的空气域设置“Flow-out”流出边界;目标板空气域外的部分设置固定边界;目标板内侧空气域边界设置为绝热刚性边界,即Euler默认的边界条件,刚性强,无流动,速度等于零,以模拟舱室模型主体结构。预制孔板计算模型如图8所示。
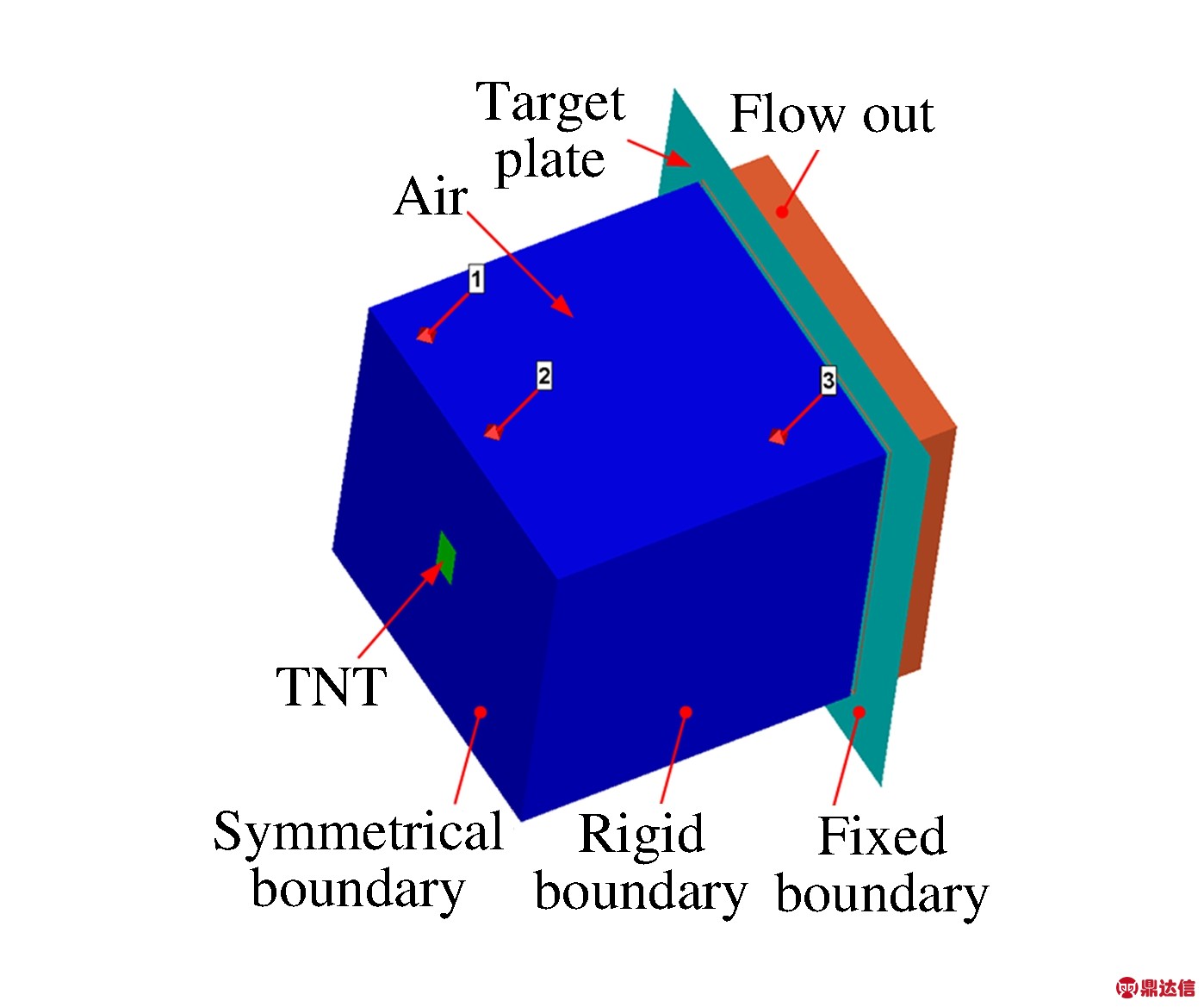
图7 计算模型
Fig.7 Numerical model
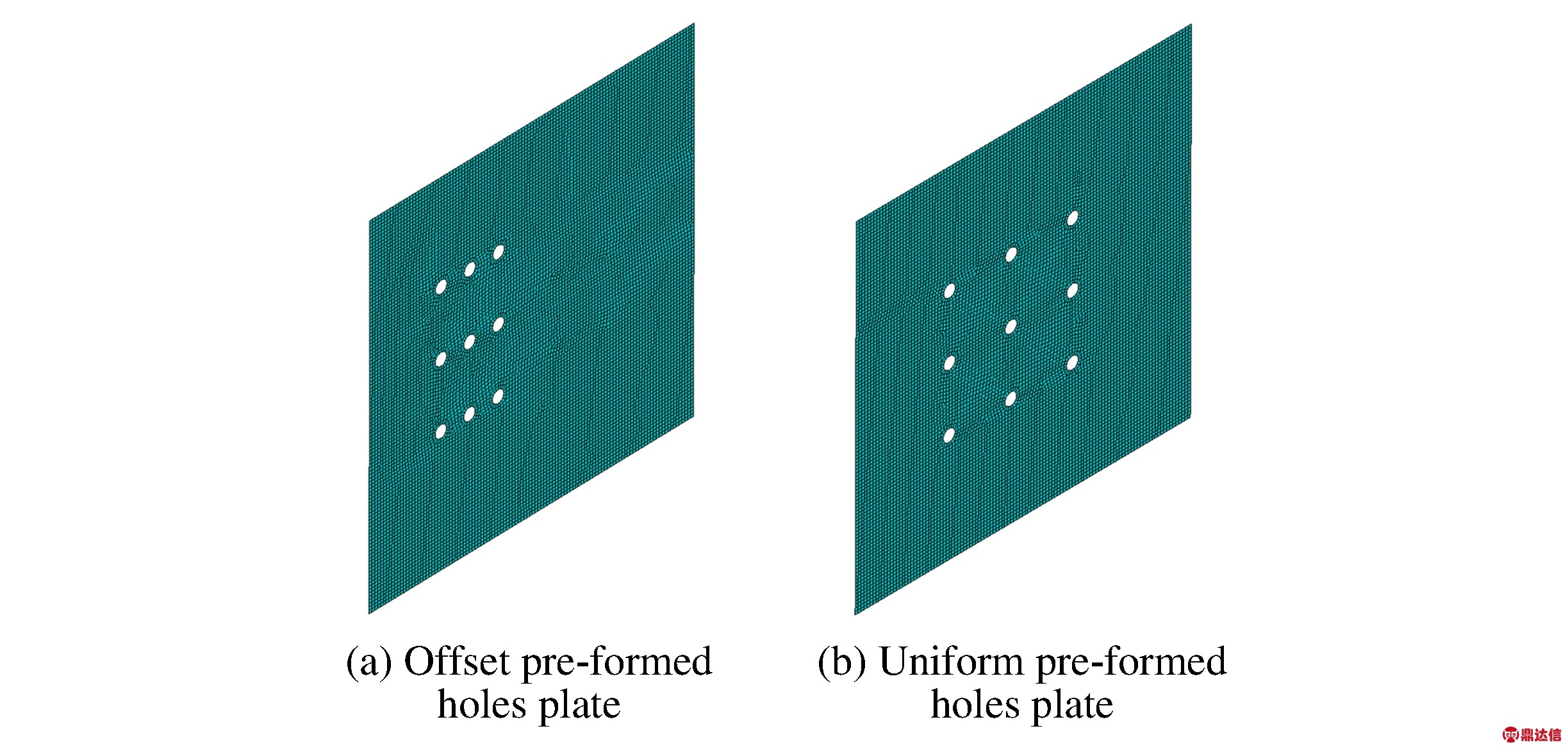
图8 预制孔板计算模型
Fig.8 Numerical model of preformed holes plate
考虑计算速度和精度,最终选定空气网格大小为8 mm,共2.7×105个网格,同时引入无孔板和两种预制孔板(偏置孔板和均匀孔板)做对比,3种目标板采用Shell单元,由外接CAE软件Hypermesh导入。板厚度为1.8 mm,四边形网格的长、宽分别为6 mm。其中无孔板单元为12 769个,偏置孔板单元为12 851个,均匀板单元为12 770个。
2.2 材料参数
空气采用理想气体状态方程,状态方程表述如下

(1)
式中:γ为空气的比热,ρ为空气密度,e为空气内能;该模型中取γ=1.4,ρ=1.225×10-3g/cm3,e=0.2068 J。
装药使用TNT,用JWL状态方程描述。JWL状态方程本质是一个经验公式,其数据来源于一系列的物理实验,能很好地反映产物的体积、压力和能量特性,适用于大多数的高能炸药。爆轰产物的气体压强公式由下式给出

(1)
式中:A1、B1、R1、R2、ω均为实验拟合参数;E0为炸药初始比内能;v=ρ0/ρ,ρ0为炸药初始密度,ρ为爆轰后某一时刻的密度。
预制孔板材料为Q235钢,计算模型中采用Linear状态方程和Cowper-Symonds强度模型来描述,在AUTODYN中对应参数如表3和表4所示。
表3 Q235钢参数
Table 3 Parameters of Q235 steel

表4 Cowper-Symonds强度模型部分参数
Table 4 Some parameters of Cowper-Symonds strength model

3 仿真结果分析
3.1 舱室模型内爆冲击波分析
舱室模型内爆炸冲击波压力云图如图9所示。分析舱室模型内爆全过程可以看到:炸药点起爆后,柱形装药爆炸冲击波逐渐变为球形,冲击波开始在舱室模型内部传播,首先冲击波迅速传播到刚性边界处,即近壁面的4个舱壁上,如图9(a)所示;然后冲击波在近壁面的4个舱壁上形成反射,并在壁面角隅连接处形成汇聚波,两壁面角隅处汇聚波强度大于沿平面传播的反射冲击波,在0.25 ms时,第1次反射冲击波开始到达目标板,如图9(b)所示;在约0.30 ms时,第1次反射冲击波遇到目标板,然后再次发生反射,如图9(c)所示;在冲击波的作用下,进行了能量传递和转化,目标板开始发生变形;随着时间的推移,冲击波在舱室模型内部不断反射和汇聚,来回“振荡”,在毫秒量级的后期,舱内压力逐渐趋于稳定,即演化成准静态压力(Quasistatic pressure),如图9(d)所示。
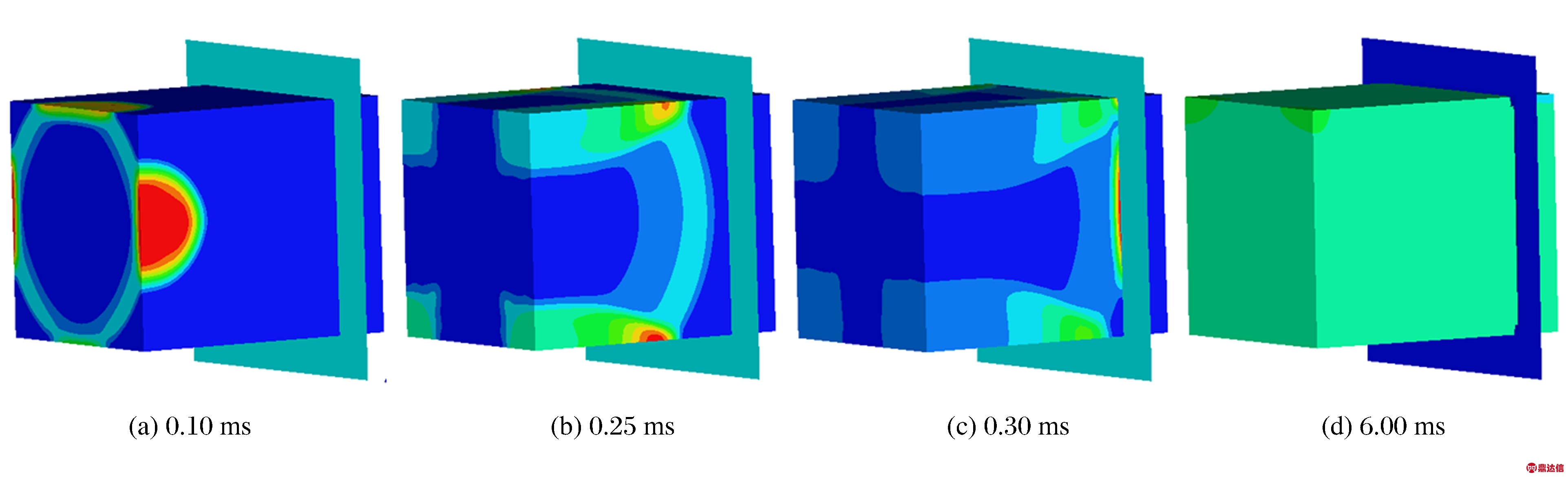
图9 内爆冲击波传播云图
Fig.9 Contour of internal blast shock wave propagation
3.2 典型测点内爆载荷分析
计算模型选取的测点如图7所示。为研究舱室模型内爆冲击波的分布和传播,3个测点分别选取在舱内爆炸典型测点处[10]:测点1设置在靠近两壁面连接处,测点2设置在顶面平面处,测点3设置在三壁面处。各测点冲击波压力时程曲线如图10所示。
由图10可知,舱室模型内部爆炸冲击波存在多次反射现象,后期冲击波呈现准静态特性。测点1和测点2首次反射波峰接近,与空中爆炸类似,近爆载荷下,首次反射波峰和爆距有关。测点2位于舱室模型顶面平面处,在1.1 ms处仍然出现了一个明显的反射波峰,说明在小舱室模型中,各特征区域均会发生反射。测点3反射波峰首次出现时间略微滞后于测点1和测点2,根据空爆冲击波和反射冲击波传播速度规律,反射冲击波波阵面传播速度在近爆点位置受爆距影响较大,首次波峰明显低于测点1和测点2,另外测点3位于三壁面角隅处,后续出现多次反射汇聚波峰,但峰值均没有超过首次波峰。3个测点在1 ms内、2 ms内和6 ms内的总比冲量如表5所示。
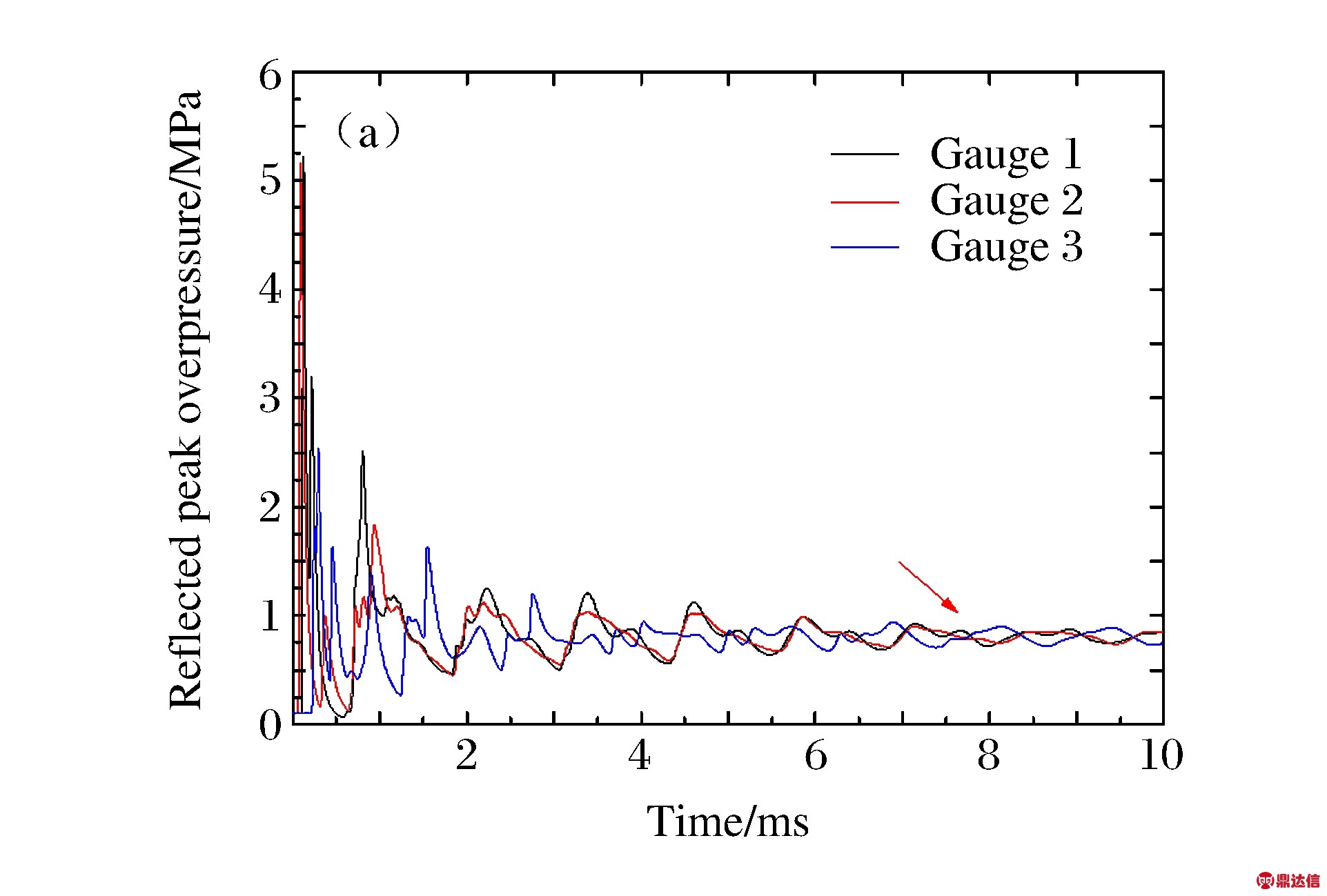
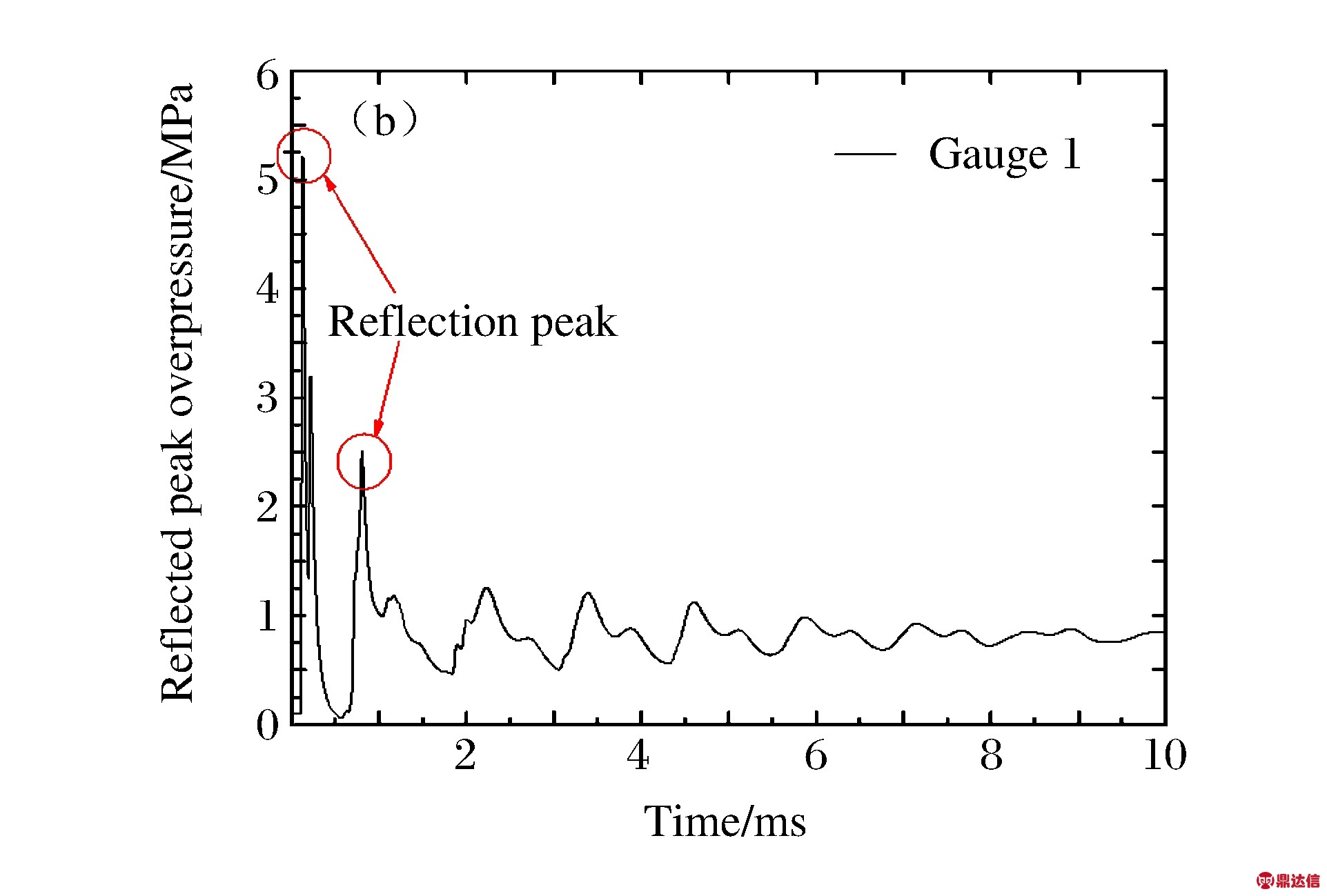
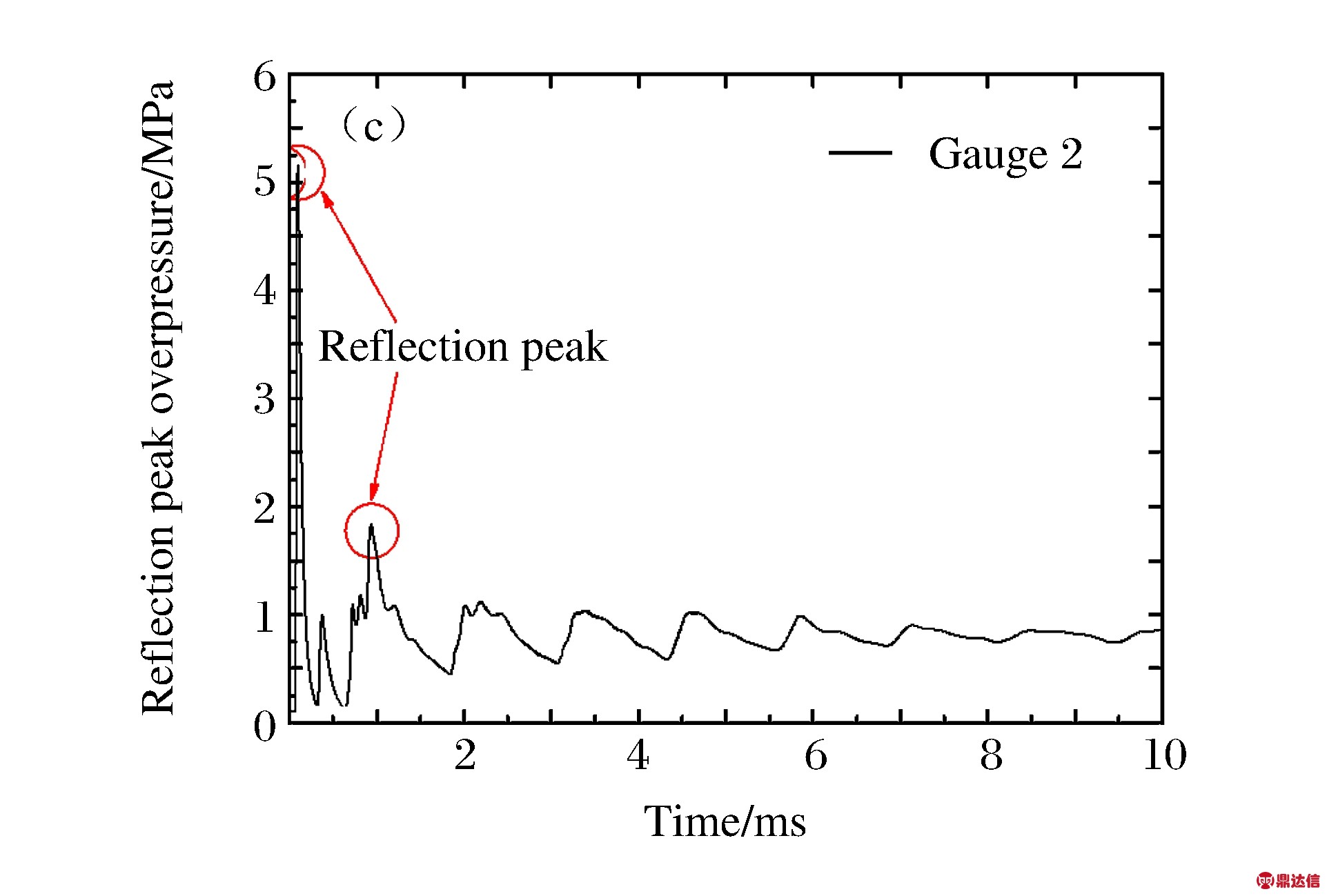
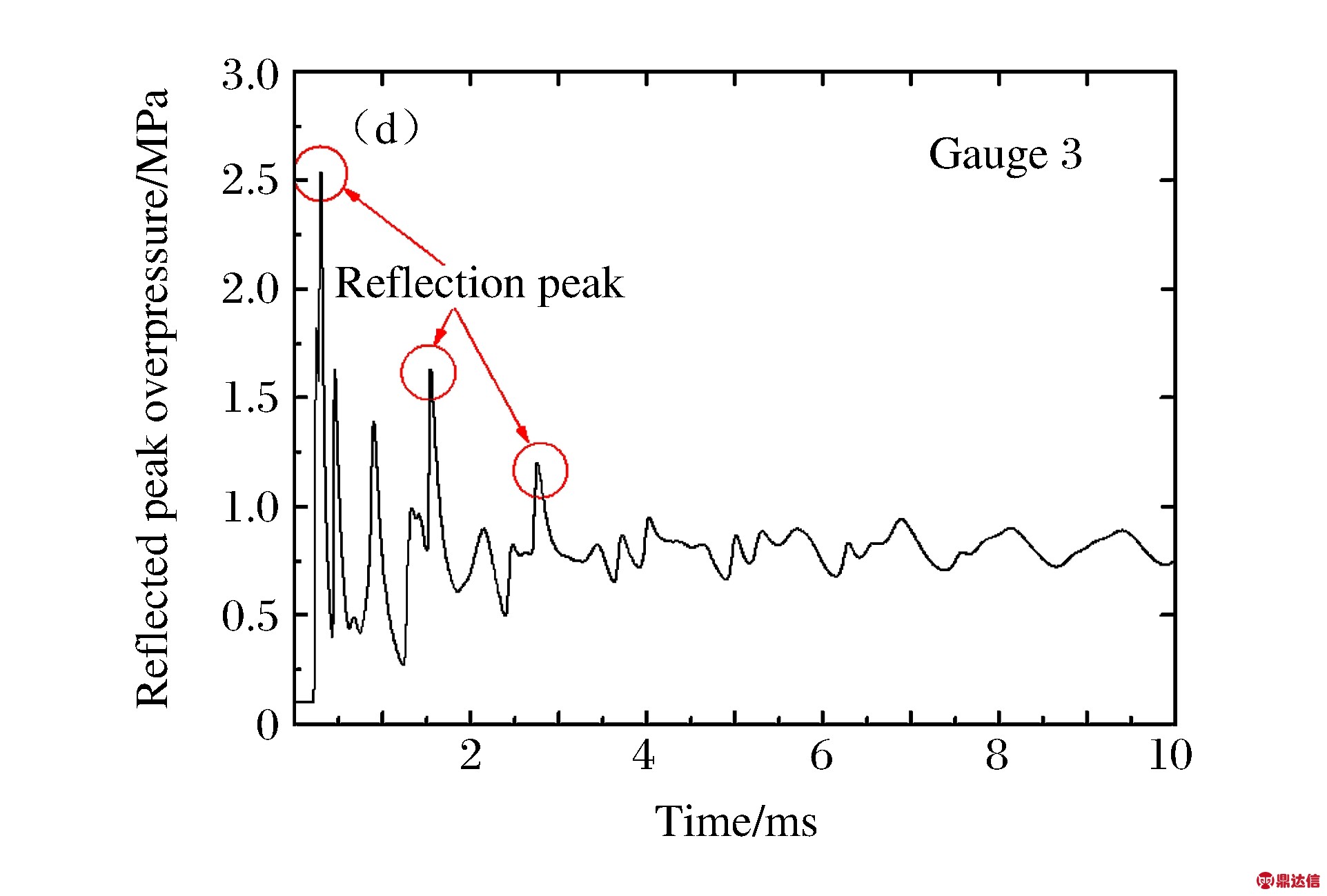
图10 仿真测点上的冲击波压力时程曲线
Fig.10 Shock wave overpressure-time history curves at simulated gauge points
表5 测点冲量对比
Table 5 Impulse comparison between gauge points

由表5可知:同一测点处冲量随时间不断升高,在舱内爆炸冲击波载荷下3个测点所受冲量和爆距有一定关系,测点1和测点2处冲量差异不大,测点3处总冲量略小,冲量大小差异主要在初始阶段产生,后期变化趋于平稳。
3.3 不同目标板在爆炸载荷下的变形机制分析
计算模型中无孔板和两种预制孔板变形情况和最大挠度统计如图11所示,从上至下分别为无孔板、偏置孔板和均匀孔板。3种目标板变形机制均为受载区域平滑式变形,固定边界和受载区域连接处(实验中夹板和目标板结合处)出现明显塑性铰线,但没有撕裂、吹飞。这与文献[10]中舱室模型角隅处先撕裂并向两端扩展的破坏模式不同,说明当固支钢板承受内爆炸载荷,但未能使钢板出现结构破损时,主要变形机制为整体鼓包,边缘大塑性变形,中点变形挠度最大,无孔板挠度最小;,置孔板挠度变形略大,均匀孔板挠度变形最大。数值模拟结果与实验结果呈现良好的一致性。
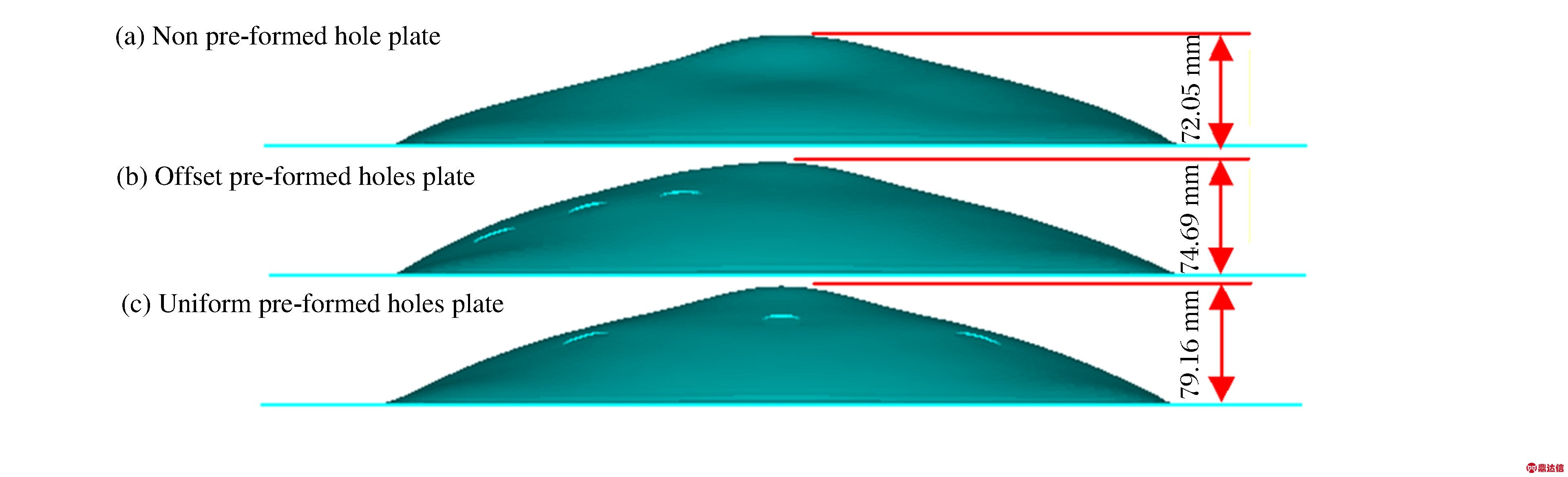
图11 目标板变形和最大挠度
Fig.11 Target plates deformation and maximum deflection
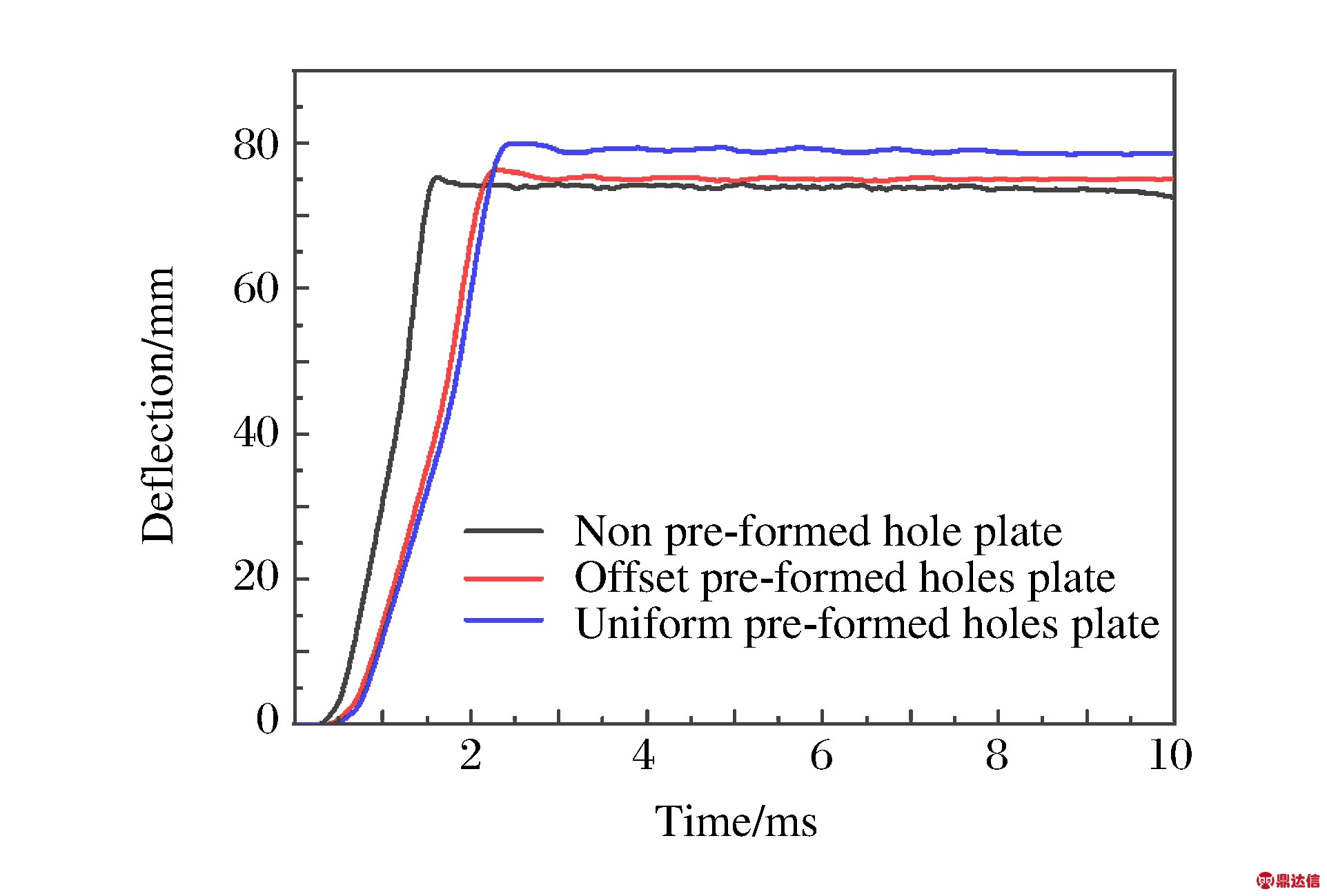
图12 三种目标板中点位移曲线
Fig.12 Midpoint displacement-time curve of three target plates
3种目标板中点位移曲线如图12所示。无孔板没有泄爆效应,最先达到最大挠度,预制孔板达到最大挠度的时间滞后于无孔板。目标板中点最大挠度的数值模拟和实验对比结果如表6所示,实验目标板最大变形挠度为一组实验两个板的挠度平均值。
由表6可知,得到的3种目标板挠度的变化趋势数值仿真与实验呈现较好的一致性,挠度从小到大依次为无孔板<偏置孔板<均匀孔板。模拟挠度较实验普遍偏小,与文献[8]中空爆载荷下预制孔靶板误差更大,说明内爆炸载荷下边界影响更大,除此之外造成误差的因素还有AUTODYN软件自身的原因[12-13],本研究中近场爆炸条件下,模拟网格尺寸限制及模拟软件内置缺陷的影响较大。
表6 挠度对比与误差
Table 6 Deflection comparison and deviation
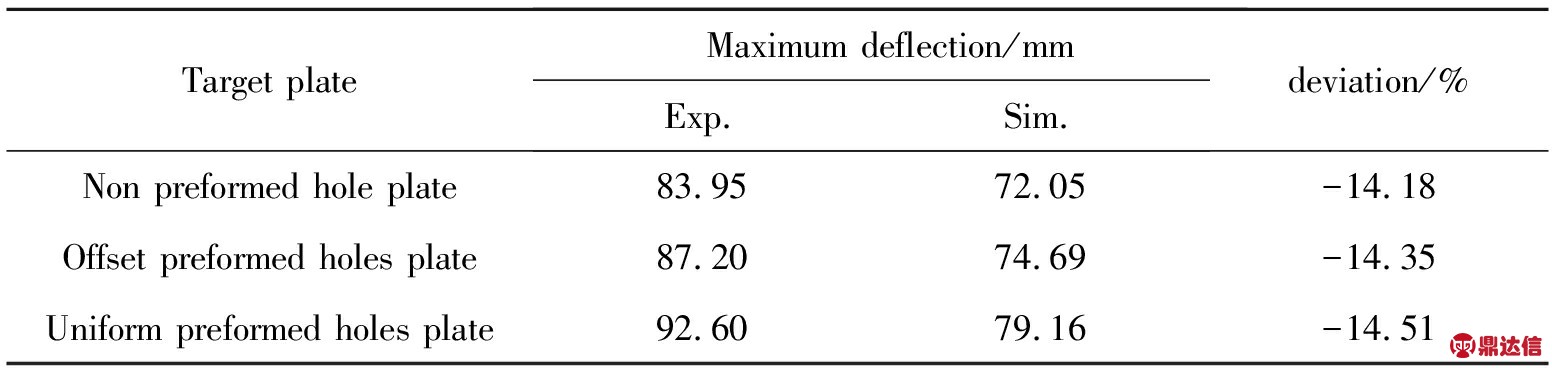
4 结 论
针对舱室模型内爆炸载荷下预制孔板变形规律的研究,通过数值模拟和实验得到以下结论:
(1) 数值模拟方法可行,内爆冲击波在舱室模型内部存在反射和汇聚现象,并在毫秒量级的后期存在准静态特性;
(2) 135 g TNT舱室模型中心起爆时,目标板挠度大小为无孔板<偏置孔板<均匀孔板,预制孔板的局部强度减弱对挠度变形的增益大于泄爆效应的影响;
(3) 实验预制孔板不同区域减薄率存在差异:顶点即几何中心点的减薄率最大,中间区域减薄率次之,边缘区域减薄率最低,中间区域预制孔板减薄率大于无孔板。