摘要: 为了深入研究电缆附件绝缘材料在电、热和机械等多种应力耦合作用下的破坏机理,以110 kV预制式电缆中间接头用三元乙丙橡胶为研究对象,搭建了模拟电缆附件绝缘界面应力作用状况的多应力耦合试验装置。对交联聚乙烯-乙丙橡胶界面中的橡胶试样施加不同的机械拉伸和电应力,应力作用不同时间后,采用显微观察、机械性能测量、体积电阻率及交联度测试、衰减全反射傅里叶红外光谱和X射线光电子能谱等手段对试样进行了观察及测试。研究结果显示,乙丙橡胶表面分子中的部分原有基团在电应力作用下被破坏并氧化,生成—OH、C=O等氧化基团,机械拉伸应力对上述反应具有一定的协同促进作用,而机械性能、体积电阻率和交联度等反映材料体积特性的参数变化幅度不大。这表明,上述多应力耦合作用对乙丙橡胶的破坏主要停留在表面,并未深入体积内部,原因可能是乙丙橡胶材料中的大量添加物和填料暴露在表面后,阻挡了放电粒子和活性基团对试样内部的进一步破坏。
关键词: 电缆附件界面;三元乙丙橡胶;多应力耦合作用;体积特性;表面破坏
乙丙橡胶广泛应用于电力设备绝缘领域,常用作复合绝缘子、复合套管、电缆绝缘、电缆附件绝缘等。目前,针对乙丙橡胶在绝缘子、复合套管等外绝缘领域应用时的老化特性已开展了大量研究,包括热老化、电晕老化、电弧老化、人工加速老化和运行老化等。根据外绝缘的运行环境和使用要求,研究者常用表面电阻率、泄漏电流、闪络电压、憎水性、机械性能等来评估乙丙橡胶的老化特性,并采用显微观察、热重分析、差式扫描量热分析、光谱及能谱测量等手段探索它的老化机理[1-3]。针对乙丙橡胶在高压电缆及附件中的应用,相关研究主要集中在热老化、电树枝化及界面电痕等方面,对材料在实际运行多应力作用下的特性变化和老化机理仍缺乏深入了解[4-6]。
与外绝缘相比,用作高压电缆附件绝缘的乙丙橡胶具有不同的特性和要求。首先,添加物的种类和含量不同,材料特性有显著差别;其次,老化因子不同,用作外绝缘时环境老化影响不容忽视,而用作电缆附件绝缘时,电、热、机械应力是引起老化的主要因素;最后,使用要求不同,相应的老化特性评估参数应与其匹配。
电缆附件作为连接两根电缆或电缆与其他输配电设备的配件,是电缆系统的重要组成部分,也是可靠性最薄弱的环节[7]。受结构、环境及运行条件影响,电缆附件的绝缘受到多种应力的耦合作用,例如运行电压导致的电应力、传输电流导致的热应力、安装扩径引起的绝缘本体拉伸应力和界面压缩应力等[8]。
电缆附件绝缘本体及界面可能存在缺陷,使局部场强畸变,形成高场强区,从而引发局部放电,从热、紫外辐射、粒子轰击和强氧化物质生成等方面造成材料结构破坏、性能劣化,并最终导致击穿[9-10]。此外,绝缘本体的拉伸应力和界面的压缩应力也会对材料短期及长期性能造成影响,如影响材料的电树枝特性和界面电痕特性等[11-13]。实际运行中,这些因素往往共同作用,导致电缆附件绝缘材料发生老化及劣化。
本文针对三元乙丙橡胶(后文简称乙丙橡胶)在交联聚乙烯(XLPE)绝缘电缆预制式附件中的应用,搭建界面多应力耦合试验装置,模拟交联聚乙烯-乙丙橡胶绝缘界面上橡胶同时受到机械拉伸和电应力作用的情况。以应力作用时间和机械拉伸率为变量,对乙丙橡胶试样进行电-机械应力作用下的不同老化,然后对试样进行扫描电子显微镜(SEM)观察,获得老化前后样品微观形貌的变化规律。根据电缆附件绝缘材料的使用要求,重点对老化前后乙丙橡胶的机械强度、体积电阻率参数进行评估。最后,采用交联度测试、衰减全反射傅里叶变换红外光谱(ATR-FTIR)和X射线光电子能谱(XPS)等分析手段,研究乙丙橡胶在电-机械应力作用下的老化机理。
1 试验样品及试验方法
1.1 试验样品
本文以110 kV预制式电缆中间接头用三元乙丙橡胶绝缘材料为研究对象,按照实际生产工艺将原料热压成型,制备成150 mm×100 mm×2 mm的薄片试样。制备时,将原料放置在温度为155~165 ℃的平板硫化机上一次硫化30 min之后,再将试样放置在温度为150~160 ℃的高温试验箱中二次硫化2 h。试样中除含三元乙丙橡胶分子外,还添加了白炭黑、石蜡油、防老剂、偶联剂、结构控制剂等,用于改善材料的加工和使用性能。
交联聚乙烯试样采用110 kV XLPE电缆用粒料在温度为175 ℃、压力为8.4 MPa的平板硫化机上热压12 min制备而成,整体为100 mm×100 mm×2 mm的正方形薄片,在试样一面的中部人为制造了一个长方体凹槽,尺寸为40 mm×40 mm×0.5 mm。
1.2 试验方法
1.2.1 试验平台搭建 为开展电缆附件中乙丙橡胶绝缘的老化特性研究,搭建了模拟交联聚乙烯-乙丙橡胶界面上橡胶绝缘受电-机械应力耦合作用的试验平台。该平台由电应力施加装置和拉伸应力施加装置两部分组成,配合使用,可同时对乙丙橡胶试样施加电应力和机械拉伸应力。
电应力施加装置如图1所示,包含上、下两个完全相同的不锈钢电极,直径为65 mm,厚度为10 mm,分别用作高压电极和接地电极,带有凹槽的XLPE试样和乙丙橡胶试样放置于两个电极之间。在外加电压下,XLPE和乙丙橡胶界面上的气隙内场强集中,在高场强下发生放电,对乙丙橡胶试样表面产生放电应力。本文采用内部气隙放电模型,模拟存在气隙缺陷时电缆附件界面的放电应力,同时该气隙尺寸较大,目的是在乙丙橡胶试样表面上形成相对均匀的较大面积老化区域,以满足相关测量对试样尺寸的要求。
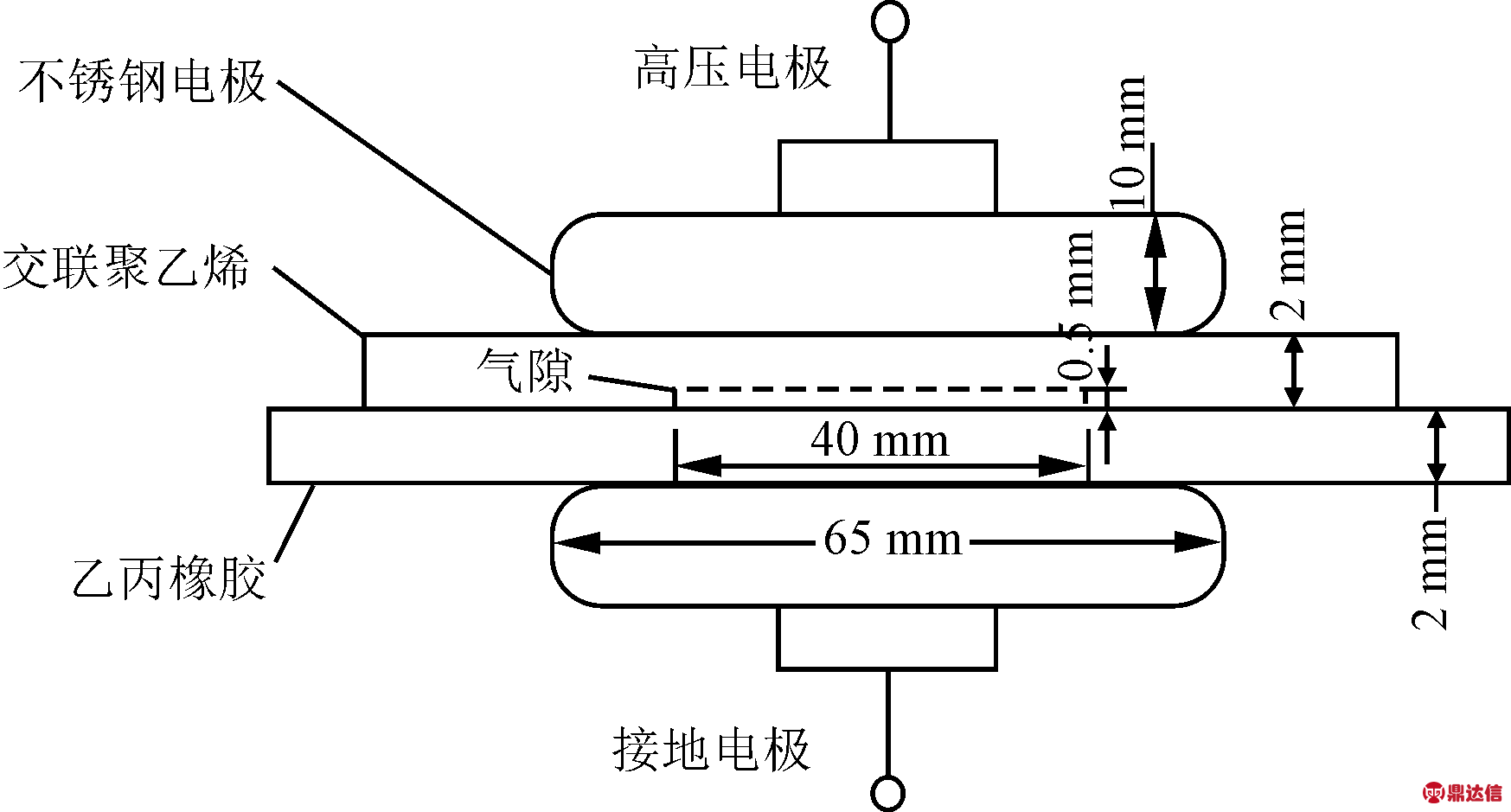
图1 电应力施加装置示意图
拉伸应力施加装置为对称结构,由固定支架和可水平移动的夹具构成,如图2所示。两个完全相同的夹具放置在固定支架内,与穿过固定支架两侧板的拉伸螺杆相连接,可在拉伸螺杆的作用下水平移动,侧板外的螺母将螺杆有效固定。
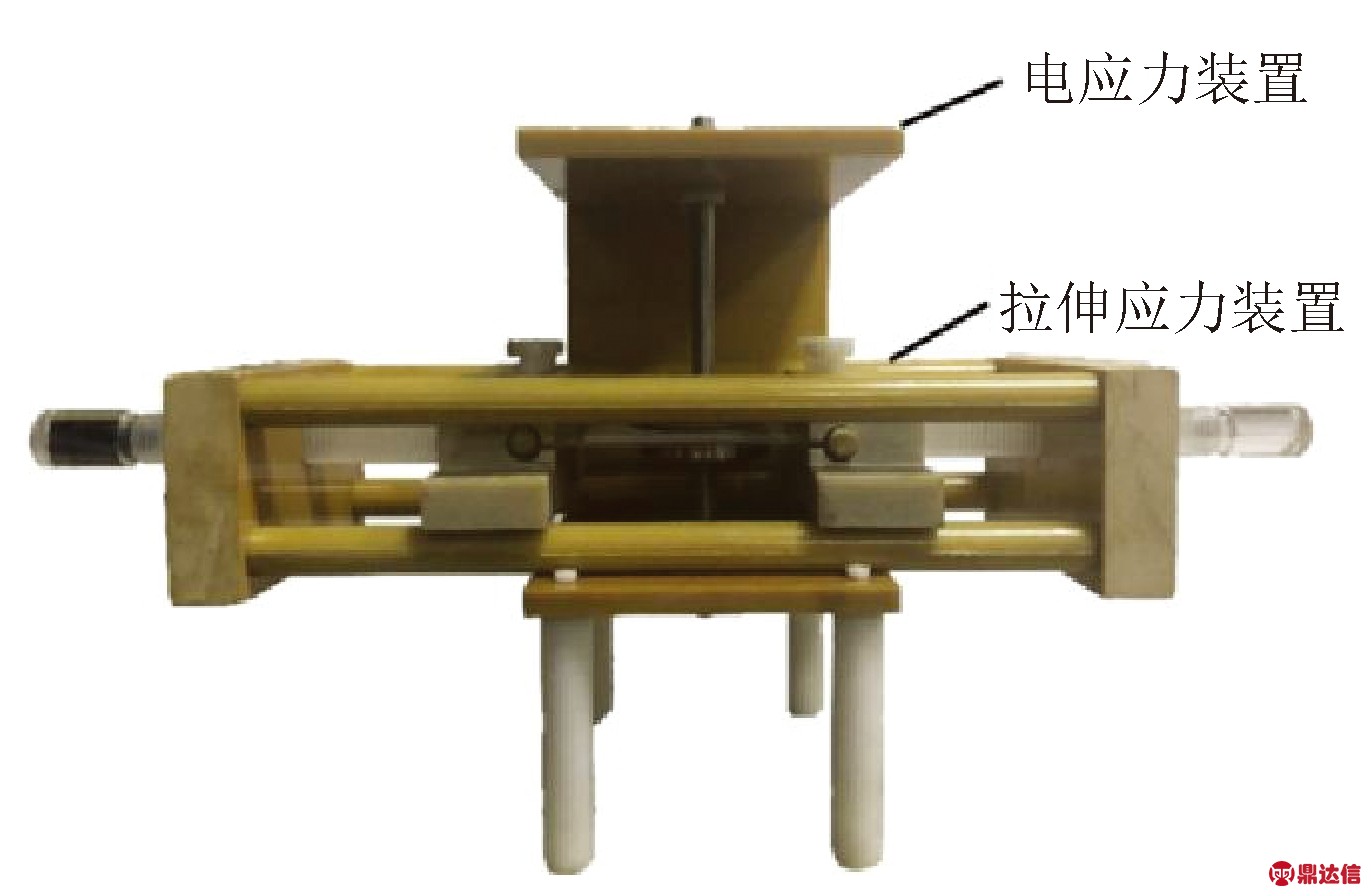
图2 电-机械应力耦合试验装置实物图
试验时,先用夹具将橡胶试样沿长边均匀拉伸至预设位置并固定;将XLPE试样放置在橡胶试样上,使XLPE试样带凹槽面和经拉伸的橡胶试样上表面紧贴,构成带气隙的界面;将两者一起置于高压电极和接地电极之间,并调节电极架,使试样与电极良好接触,如图2所示。在高压电极上加电压,将接地电极与接地线连接,既可在XLPE和橡胶界面上施加电应力,又可对橡胶试样施加机械拉伸应力。
1.2.2 试验方案设计 本文以应力作用时间和试样拉伸率为变量,设计乙丙橡胶的电-机械应力老化试验。定义拉伸率为试样拉伸后的长度增量与原长度的比值,并设定0%、35%和65% 3个试验拉伸率水平,其中35%的拉伸率对应于110 kV预制式电缆中间接头安装后的扩径率,65%的拉伸率对应于安装之前的工厂或现场扩径率。
探索试验发现,在乙丙橡胶未拉伸且加压使气隙中平均场强约为11.5 kV/mm时,可观察到明显的气隙放电,且50 h后橡胶表面有显著老化痕迹。本试验保持气隙中平均场强不变,将老化时间设置为0、50 和100 h。
对试样分组试验,每组6片,在规定的试验条件下对试样老化处理后,将其中3片用于体积电阻率的测试,3片用于机械性能测试、表面外观形貌观察和化学分析。采用“拉伸率-老化时间”的形式对试样命名,其中,老化时间是指电-机械应力共同作用的时间,例如“35%-50 h”指在橡胶试样被拉伸35%的同时施加电压,两者共同作用50 h。为研究机械应力单独作用对试样性能的影响,设置了“35%-0 h”和“65%-0 h”两组试验,将橡胶试样在拉伸率为35%及65%的状态下保持50 h,不加电压。未经任何处理的原始试样标注为“新试样”。
1.2.3 理化特性分析 本文对不同条件老化后的乙丙橡胶试样进行了扫描电镜观察、机械性能测试和体积电阻率测量,并采用交联度测试、ATR-FTIR和XPS测试对试样进行化学特性分析。
将试样切成外径约为3 mm的圆片并对表面喷金处理后,采用VE-9800S型扫描式电子显微镜在放大倍数为1 000倍下进行显微观察。
参照GB/T 528—2009的要求[14],将试样裁剪为标准哑铃形,采用CMT-4503型拉力试验机进行机械性能测试,拉伸速率为500 mm/min。
按照GB 1410—2006的要求[15],对试样进行表面喷金处理后,采用Keithley 6517B型高阻计测量体积电阻率,测试时环境温度为(26±3) ℃,相对湿度为(55±15)%,测量电压为1 kV。
参照JB/T 10437—2004的要求[16],采用二甲苯萃取法在室温为(23±2) ℃、相对湿度为(50±5)%的标准实验室大气环境下进行交联度测试。
将试样切成外径约为10 mm的圆片状,采用Nicolet iZ1型红外光谱仪进行ATR-FITR测试,光谱范围为4 000~600 cm-1,精度为8 cm-1。
采用型号为ESCALAB Xi+的X射线光电子能谱仪进行XPS测试,分辨率为0.8 eV,分析结果以C1s结合能为284.8 eV为基准进行荷电校正。
2 试验结果
2.1 表面微观形貌观察
不同条件老化后乙丙橡胶试样的表面微观形貌如图3所示,试样标注为拉伸率和作用时间,从图中可以看到,原始试样表面有压片产生的划痕。在机械应力单独作用下,乙丙橡胶表面变得粗糙,有颗粒物析出;在35%拉伸率下,析出的颗粒物较小,粒径在5 μm以下;拉伸率增加到65%时,析出的颗粒物尺寸增大,最大粒径可达8 μm。
电应力单独作用50 h后,试样表面有条状物质生成,产生小颗粒物,尺寸在25 μm左右,且颗粒物周围有裂纹产生;当电应力作用至100 h,试样表面生成颗粒物尺寸变大并产生聚集,最大粒径可达50 μm以上,且出现粉化痕迹。
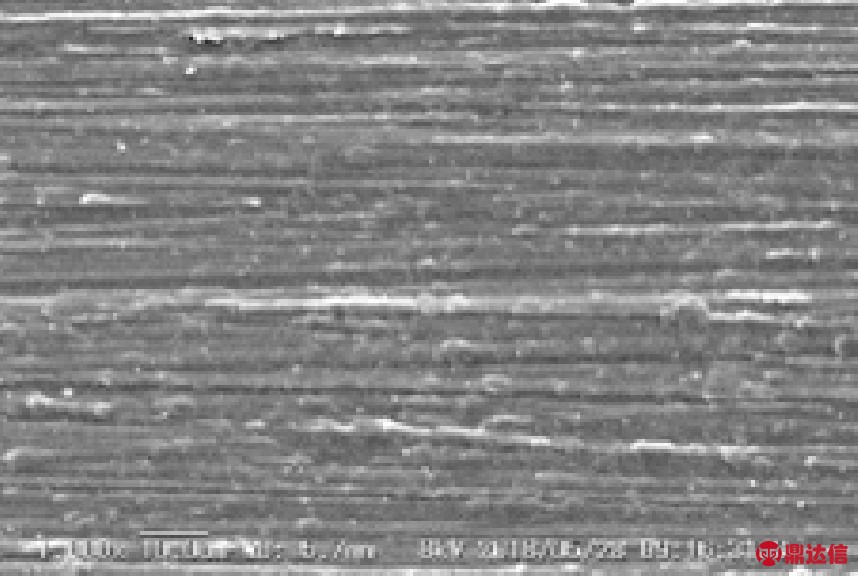
(a)新试样
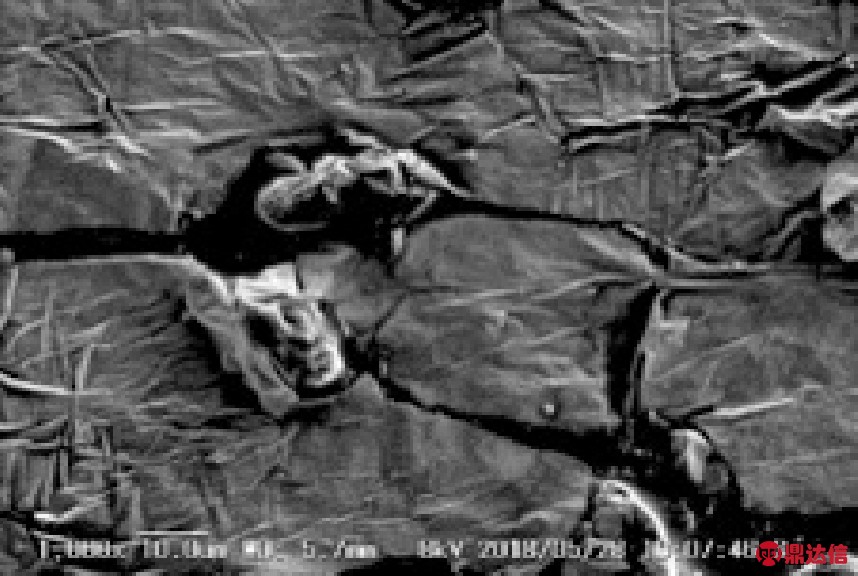
(b)0%-50 h
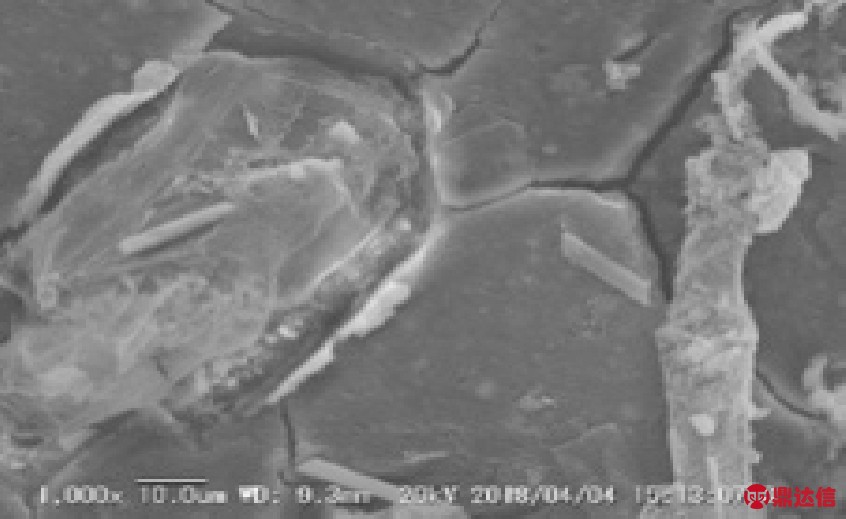
(c)0%-100 h
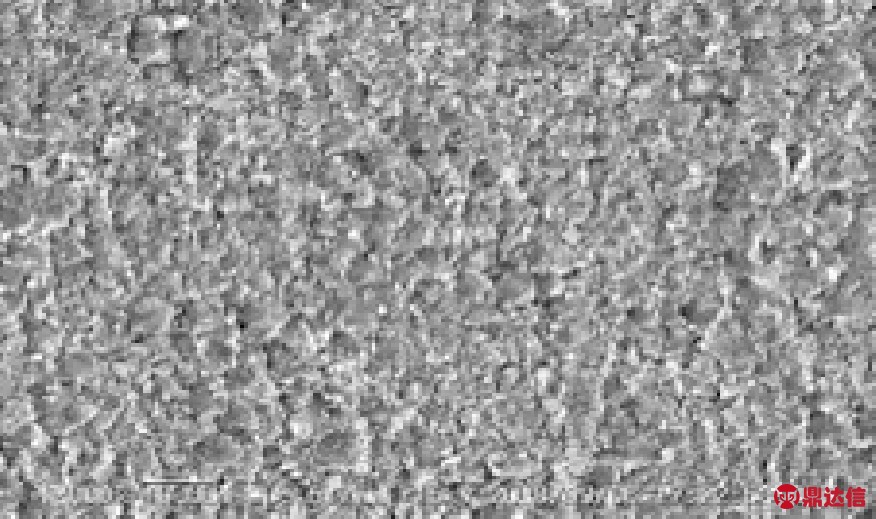
(d)35%-0 h
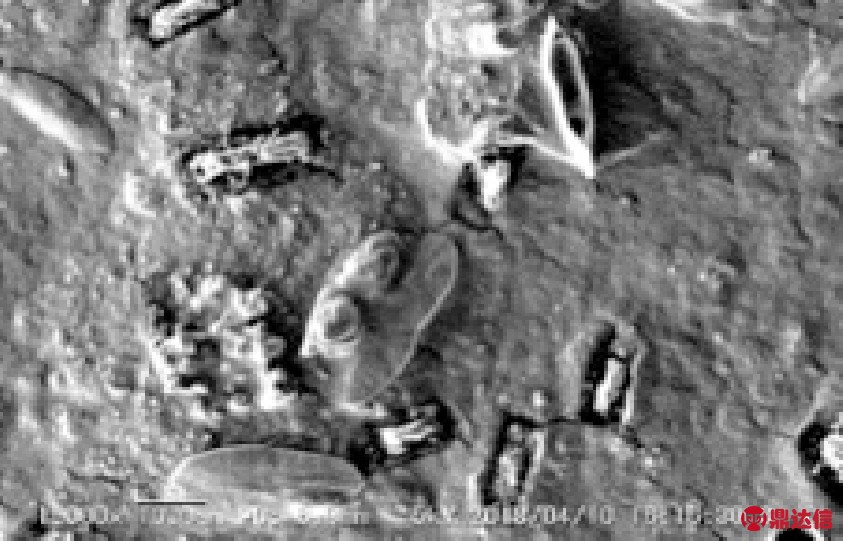
(e)35%-50 h
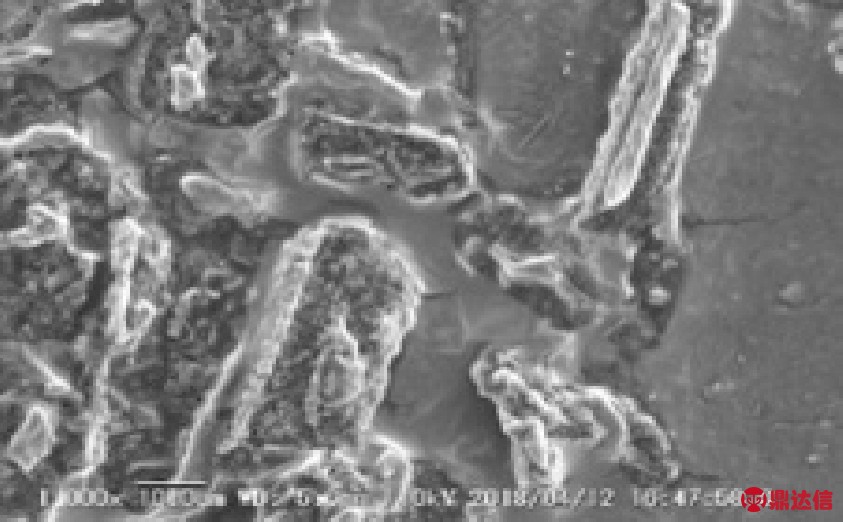
(f)35%-100 h
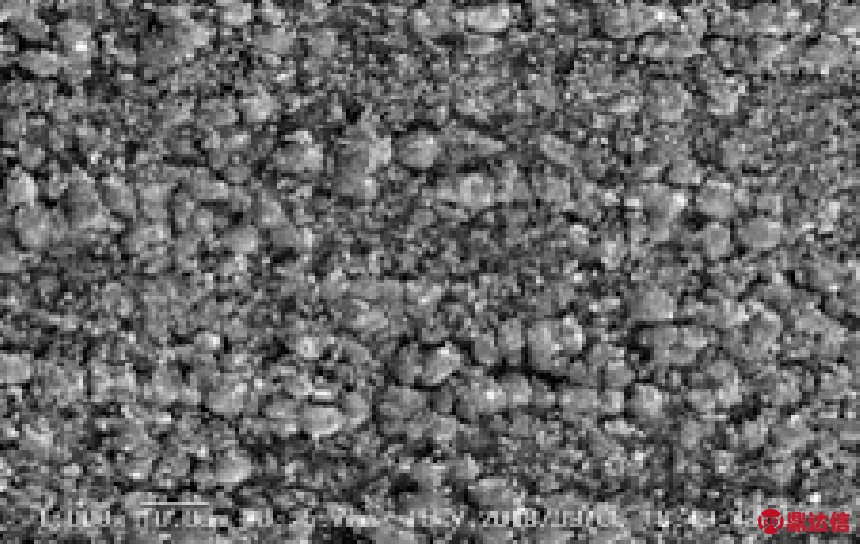
(g)65%-0 h
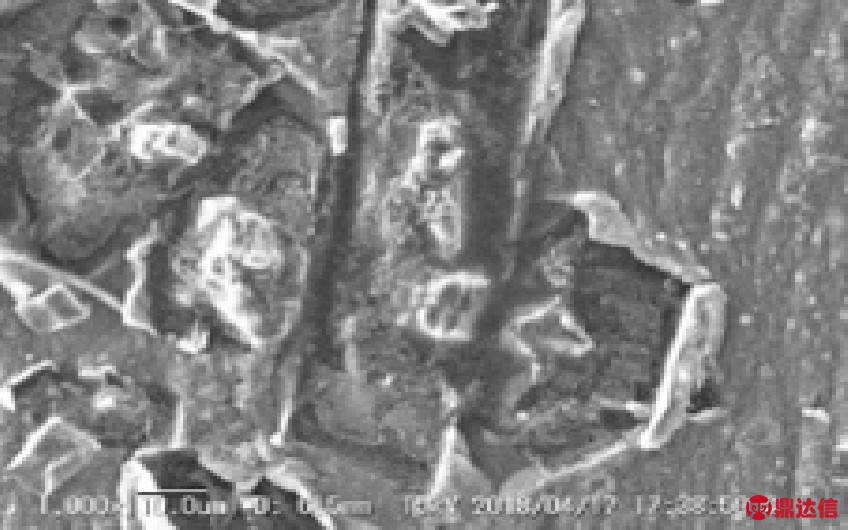
(h)65%-50 h
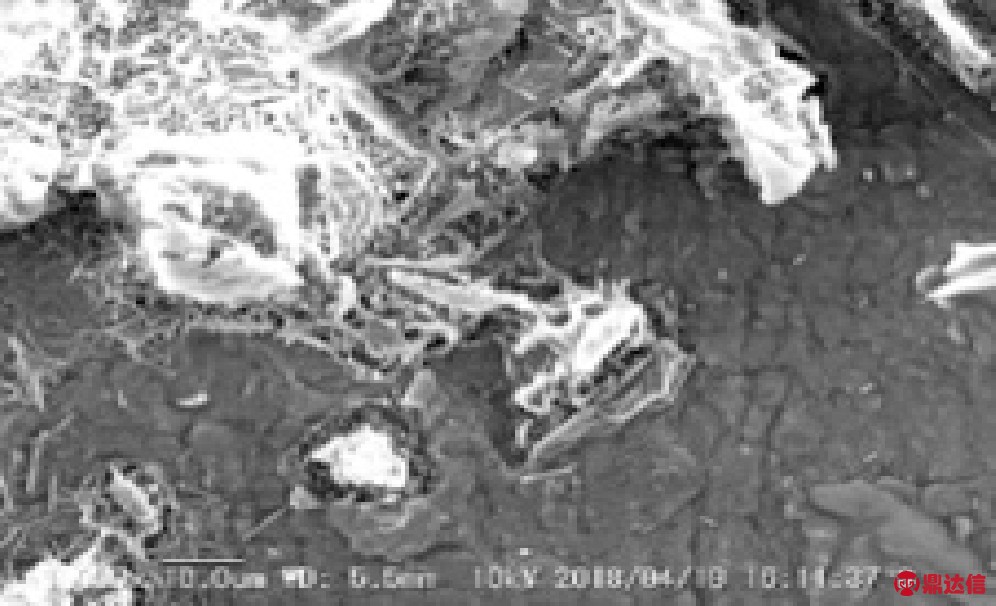
(i)65%-100 h
图3 老化前后乙丙橡胶试样的表面微观形貌(×1 000)
在电-机械应力共同作用下,乙丙橡胶表面变得更加粗糙,出现垂直于拉伸方向的纹路;在相同老化时间下,随着拉伸率增加,试样表面的粉化和聚集现象加重,裂纹增多。
2.2 机械性能分析
在电缆接头安装和使用过程中,为保证一定的界面抱紧力、增强界面绝缘性能,预制橡胶件长期处于“紧绷”状态,这对橡胶材料的机械性能提出了较高的要求。国标GB/T 11017.3—2014中规定:用于110 kV预制式电缆附件的绝缘材料拉伸强度不能低于5.0 MPa,断裂伸长率不能低于300%[17]。本文着眼于这两个参数对老化前后试样的机械性能进行研究,结果如图4所示。
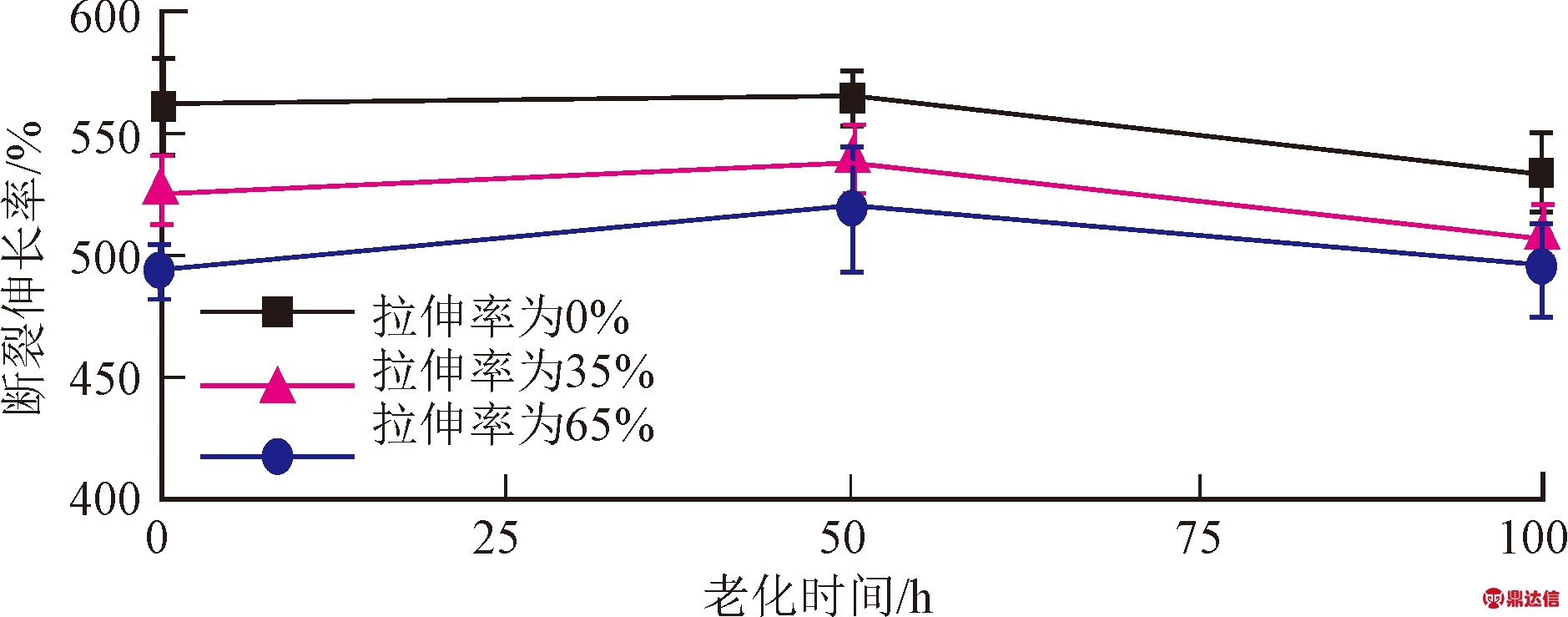
(a)断裂伸长率
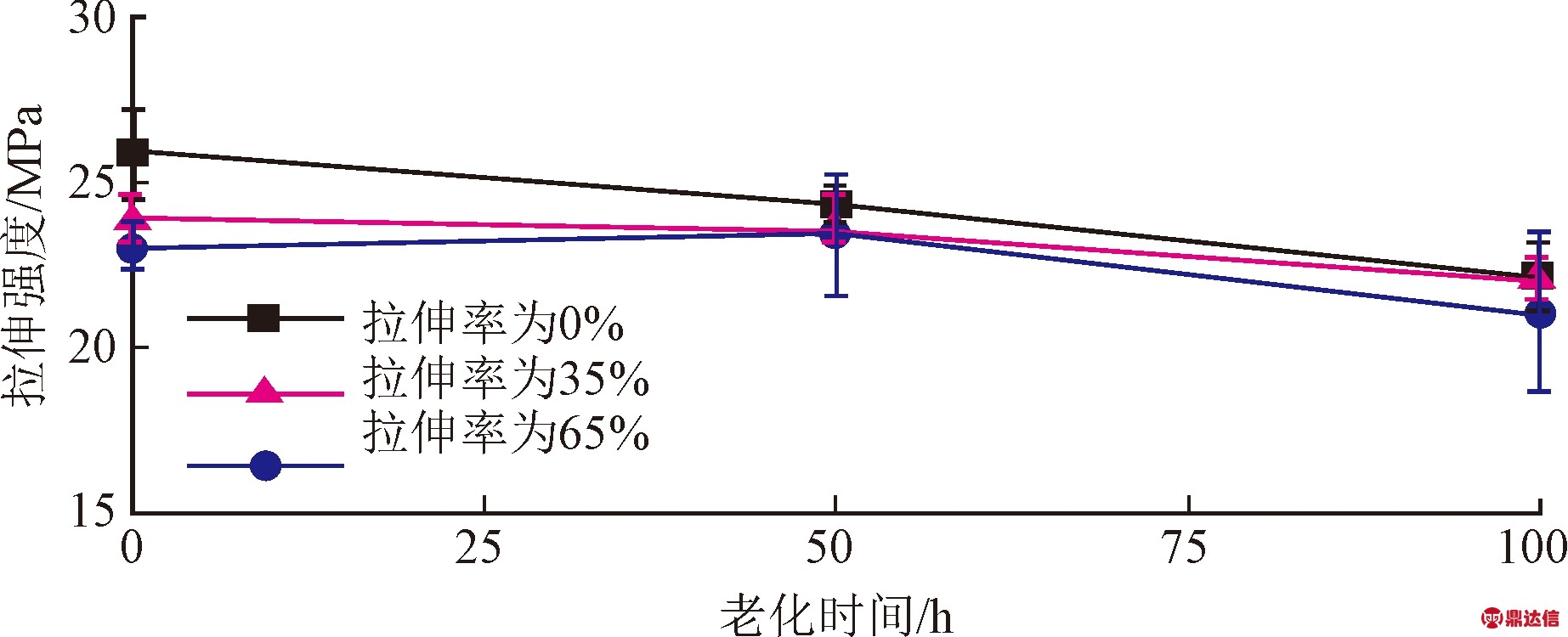
(b)拉伸强度
图4 老化前后乙丙橡胶试样的机械性能参数
由图4可见,在电-机械应力作用下,乙丙橡胶试样的断裂伸长率和拉伸强度都随时间增加呈下降趋势,但变化幅度不大,未超过20%,说明无论老化前后,试样的两个性能参数都满足标准要求。机械拉伸导致的试样机械性能下降可能与外力作用下添加物析出、分子间缠结变弱有关,电应力作用引起的机械性能劣化可能与材料中发生的断链反应和表面的“微裂纹”生成有关。
2.3 体积电阻率测试
试样体积电阻率的测试结果如图5所示。不同条件老化后,乙丙橡胶试样的体积电阻率保持在1016~1017 Ω·cm之间,变化幅度较小,且数值均大于标准要求[17]。其中,体积电阻率基本不随机械拉伸率而变化,仅随电应力作用时间增加而小幅下降,可能与表面断链反应导致的自由基载流子数量增加有关。
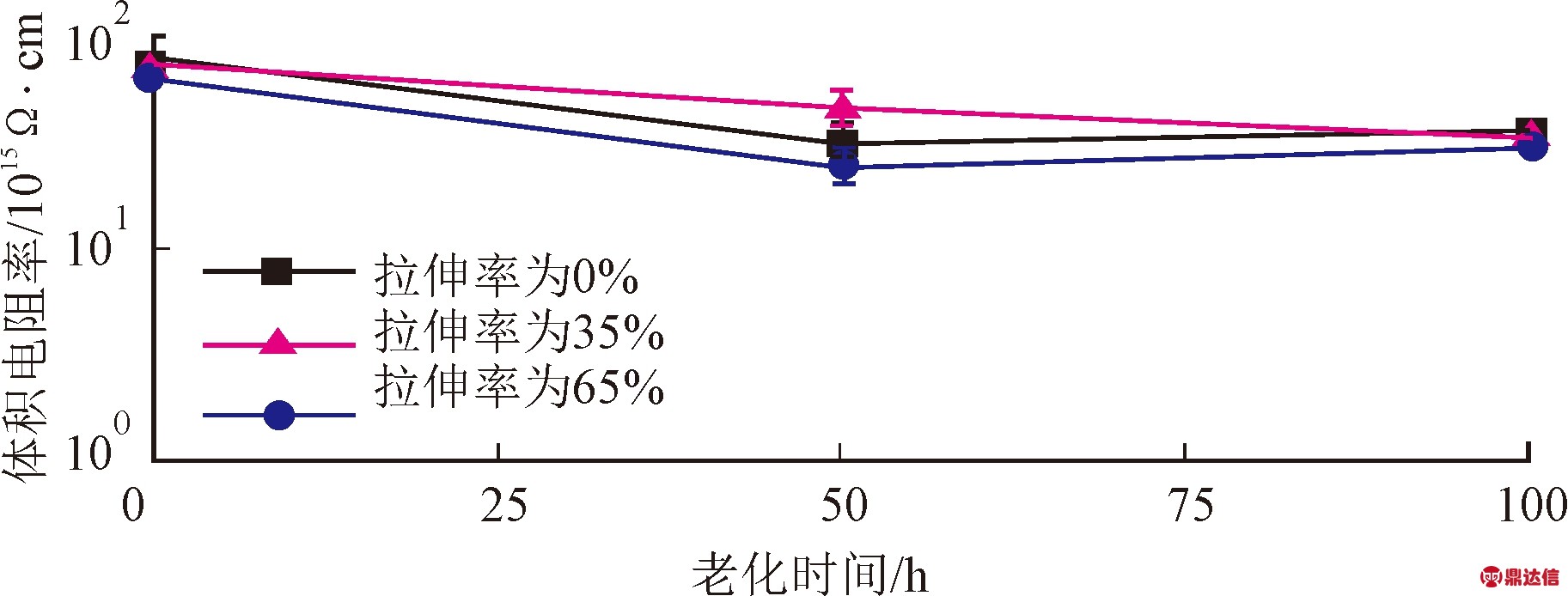
图5 老化前后乙丙橡胶试样的体积电阻率
2.4 交联度测试
对高分子材料而言,交联度可以在一定程度上反映分子的内部结构状态。不同条件老化后乙丙橡胶试样的交联度测量数据如图6所示。

图6 老化前后乙丙橡胶试样的交联度
在萃取过程中,乙丙橡胶试样表面褪色并发生明显的溶胀现象。所有试样的交联度测量值均在84.8%~85.8%之间,变化幅度很小,机械应力单独作用对交联度几乎没有影响,在电应力作用下,交联度随老化时间增加而略微下降。这表明,即使在电-机械应力的耦合作用下,乙丙橡胶也未发生严重的内部断链反应。
2.5 红外光谱分析
红外光谱中谱带的位置、强度和形状的变化可以反映试样内部基团的变化,表征材料老化。测得乙丙橡胶在电应力或电-机械应力作用后典型的红外光谱如图7所示。
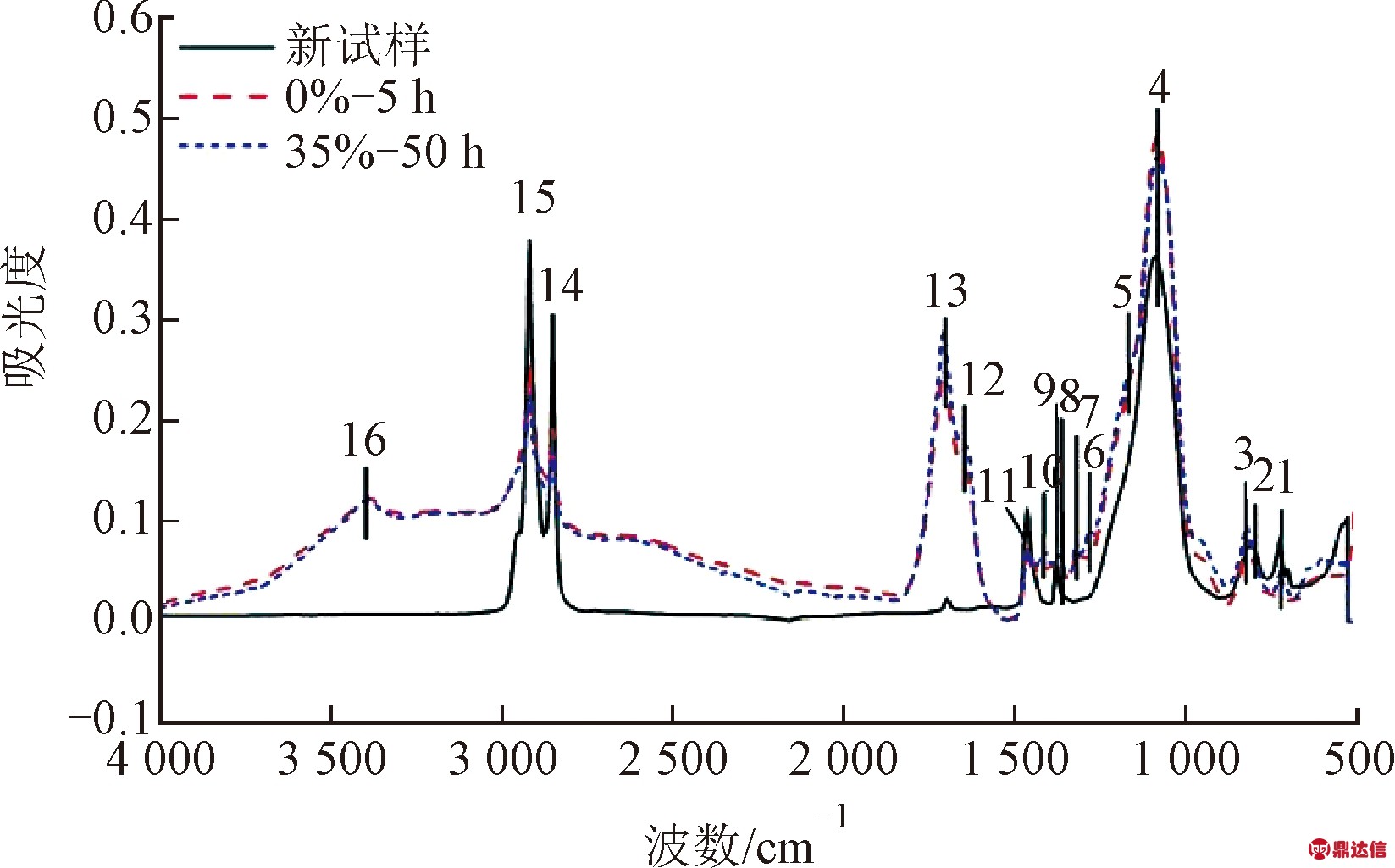
1:(CH2)n骨架振动; 2:—C—CH—; 3:烃基过氧化物; 4:C—O—C或Si—O—Si; 5,8:—SO2—O—反对称和对称伸缩振动; 6,12:—O—NO2—对称和反对称伸缩振动; 7:C—O伸缩振动; 9:—CH2—剪式振动; 10,16:—OH弯曲和伸缩振动; 11:甲基中的C—H弯曲振动; 13,14:CO伸缩振动; 14,15:饱和烃骨架上的—CH2—的对称和反对称伸缩振动
图7 乙丙橡胶老化试样的红外光谱图
图7表明,在电应力或电-机械应力作用下,乙丙橡胶原有基团的吸收峰发生明显变化:位于720 cm-1处的(CH2)n骨架振动峰、1 377 cm-1处的—CH2—振动峰、1 460 cm-1处的甲基C—H振动峰、2 848 cm-1和2 916 cm-1处的—CH2—对称和非对称伸缩振动峰强度明显下降,说明在老化过程中,乙丙橡胶表面主链和侧链发生了严重的断链反应;同时,老化试样的红外光谱在波数为820 cm-1处出现了烃基过氧化物的吸收峰,在1 300~1 250 cm-1和1 650~1 600 cm-1处出现了亚硝基—O—NO2—对称和反对称伸缩振动的吸收峰,在1 725~1 700 cm-1处出现了羰基C=O吸收峰,在1 318 cm-1处出现了C—O吸收峰,在1 410 cm-1和3 600~3 200 cm-1处出现了—OH变形振动和伸缩振动的吸收峰,在1 158 cm-1和1 363 cm-1处出现了—O—SO2—的反对称和对称伸缩振动的吸收峰。所有这些说明,乙丙橡胶在断链的同时发生了氧化反应,生成了亚硝基、羰基和羧基等基团[18-20]。
在上述基团中,—CH2—剪式振动(1 377 cm-1)、对称(2 850 cm-1)和非对称(2 920 cm-1)伸缩振动吸收峰、—CH3中的C—H吸收峰(1 460 cm-1)、—O—NO2—非对称伸缩振动吸收峰(1 650~1 600 cm-1)、C=O伸缩振动吸收峰(1 725~1 700 cm-1)和—OH伸缩振动吸收峰(3 700~3 200 cm-1)的强度变化较为明显,故选择它们来表征不同试验条件下乙丙橡胶的老化程度。
本文以吸收峰的峰高来表征特征基团的强度,测量时,选取吸收峰两端的切线作为基线,经基线校正后的吸光度作为吸收峰的峰高。提取出不同试验条件下老化后试样的红外光谱特征吸收峰强度,结果见表1,不同拉伸率下乙丙橡胶红外光谱随老化时间的变化见图8,不同老化时间下红外光谱随拉伸率的变化见图9。
结合表1和图8可知,在相同拉伸率下,随老化时间增加,乙丙橡胶中—CH2—的相关吸收峰和—CH3吸收峰的强度降低,而C=O、—O—NO2—和—OH等氧化生成物吸收峰的强度增加。这说明,在相同的电-机械应力下,随着老化进程的发展,乙丙橡胶表面的断链、氧化反应更加严重,生成物增多,这与表面微观形貌观察结果相一致。从图9可以看出,在机械应力单独作用下,试样的红外光谱在1 100~1 000 cm-1处出现多处杂峰,—CH2—的相关吸收峰和—CH3吸收峰的强度降低,可能是由拉伸时析出的添加物覆盖在试样表面所致;在电-机械应力共同作用下,随拉伸率增加,乙丙橡胶中—CH2—的相关吸收峰和—CH3吸收峰的强度呈现下降趋势,而C=O、—O—NO2—和—OH等氧化生成物的吸收峰强度略微增加,说明机械应力在一定程度上促进了乙丙橡胶表面的断链、氧化反应。
表1 老化前后试样红外光谱中特征波峰的强度
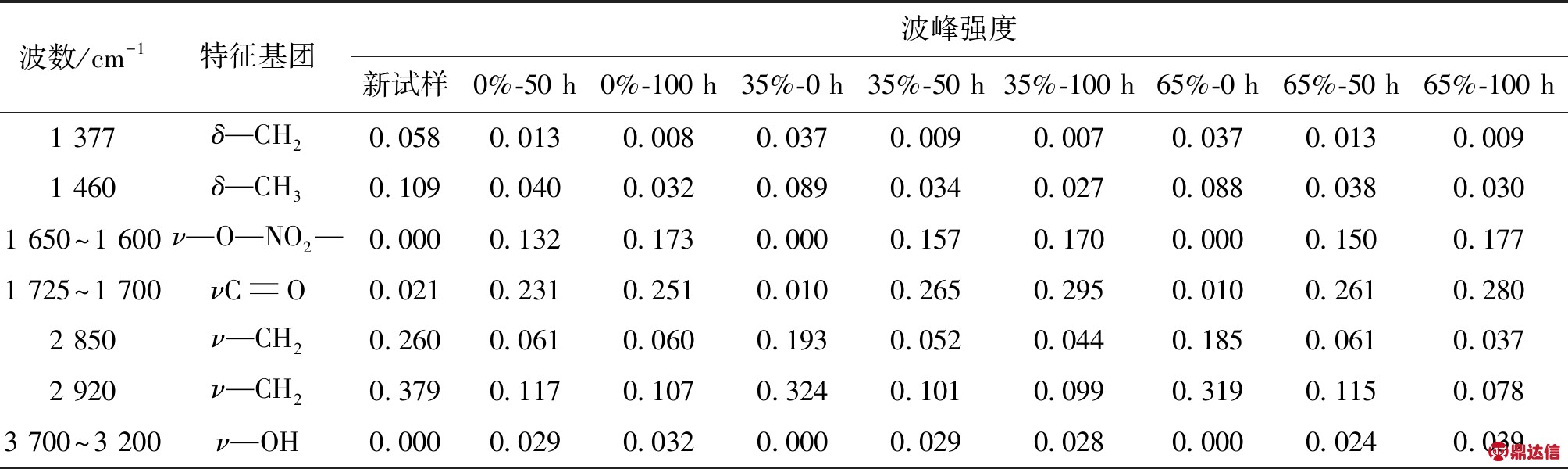
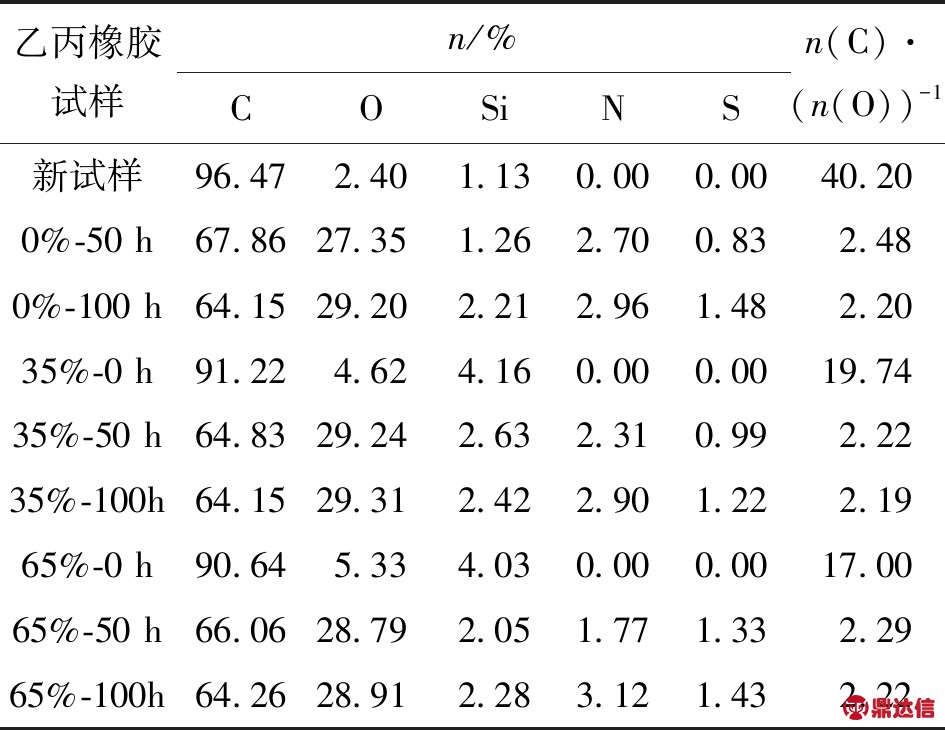
(a)拉伸率为0%
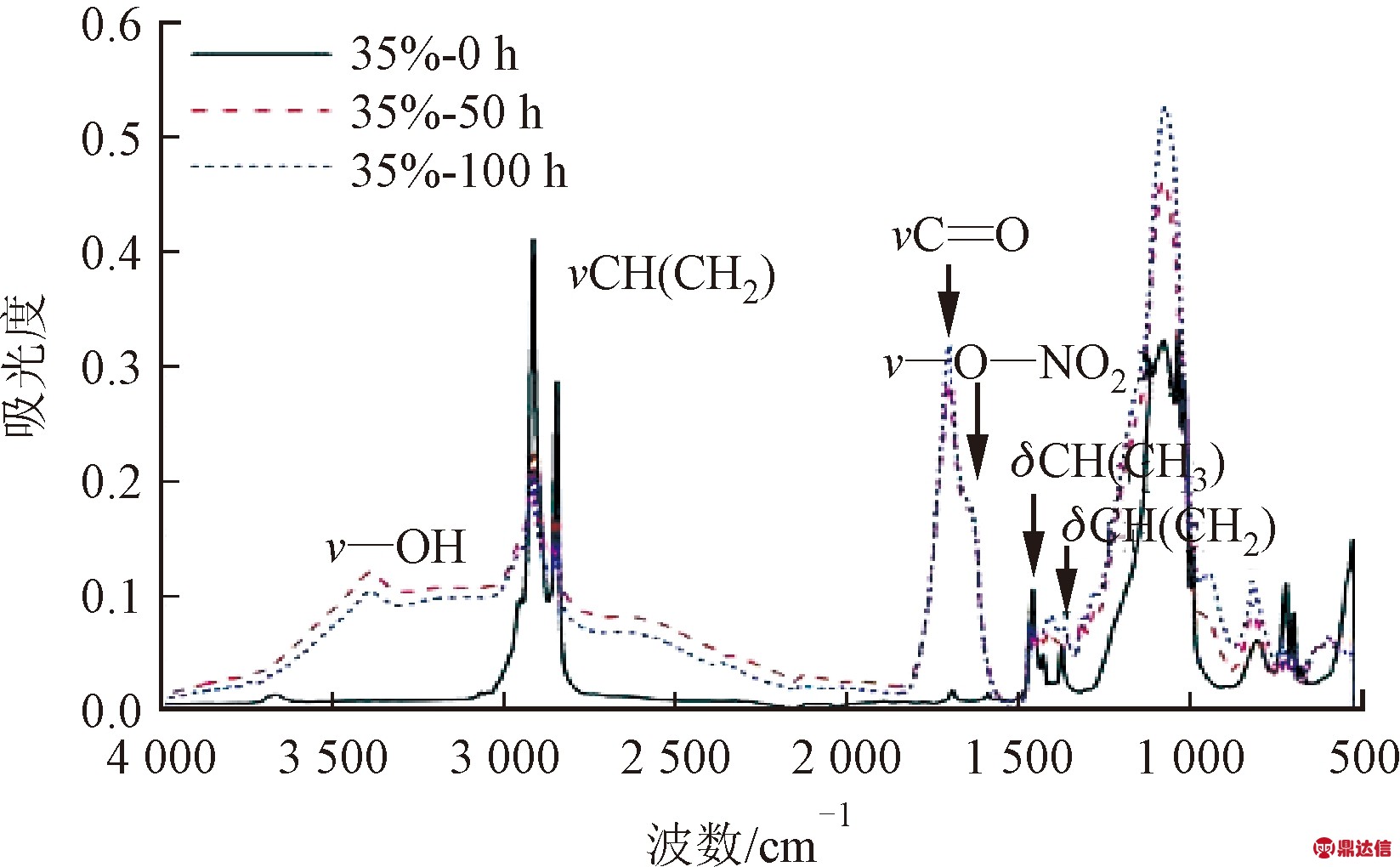
(b)拉伸率为35%
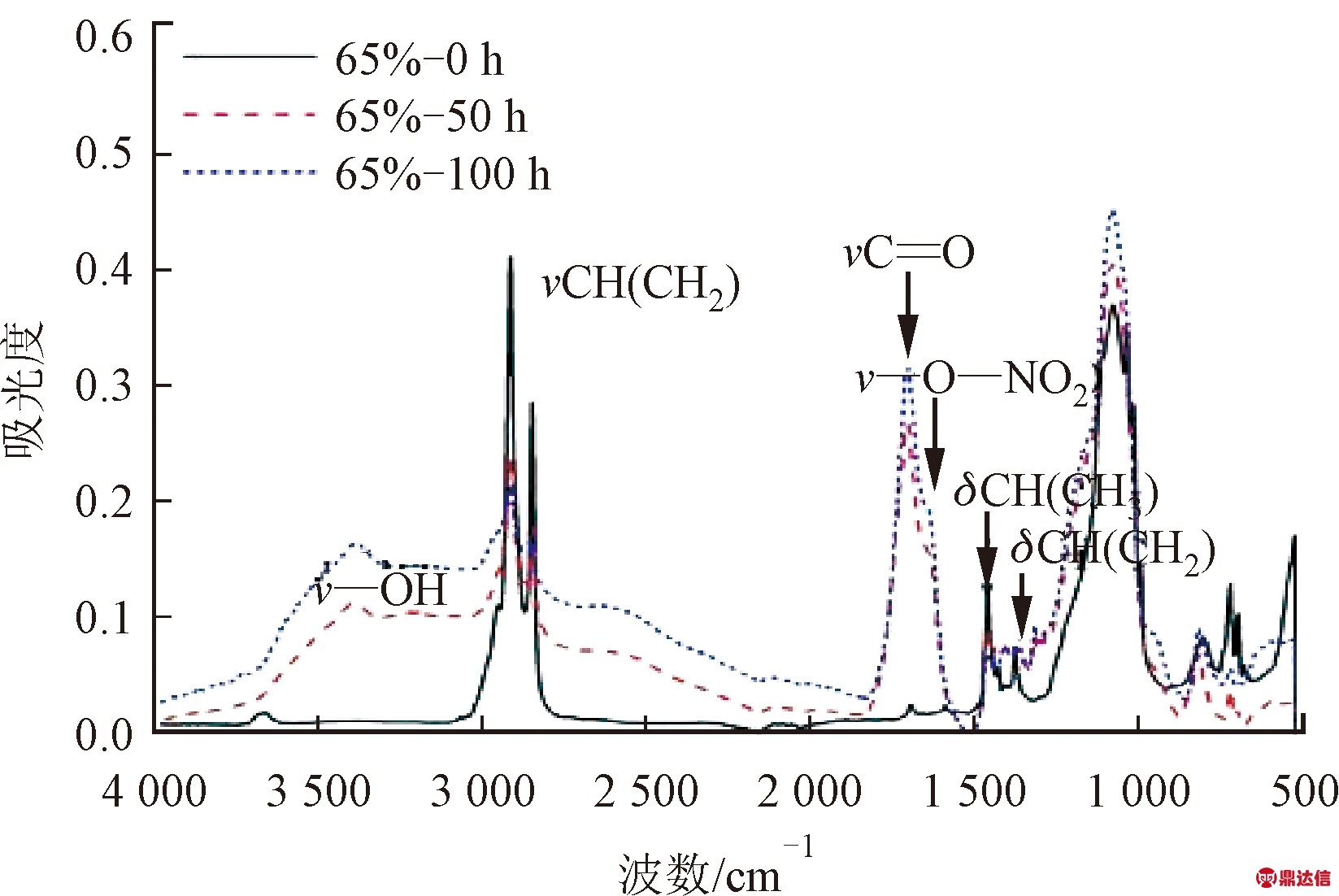
(c)拉伸率为65%
图8 不同拉伸率下乙丙橡胶试样红外光谱随老化时间的变化
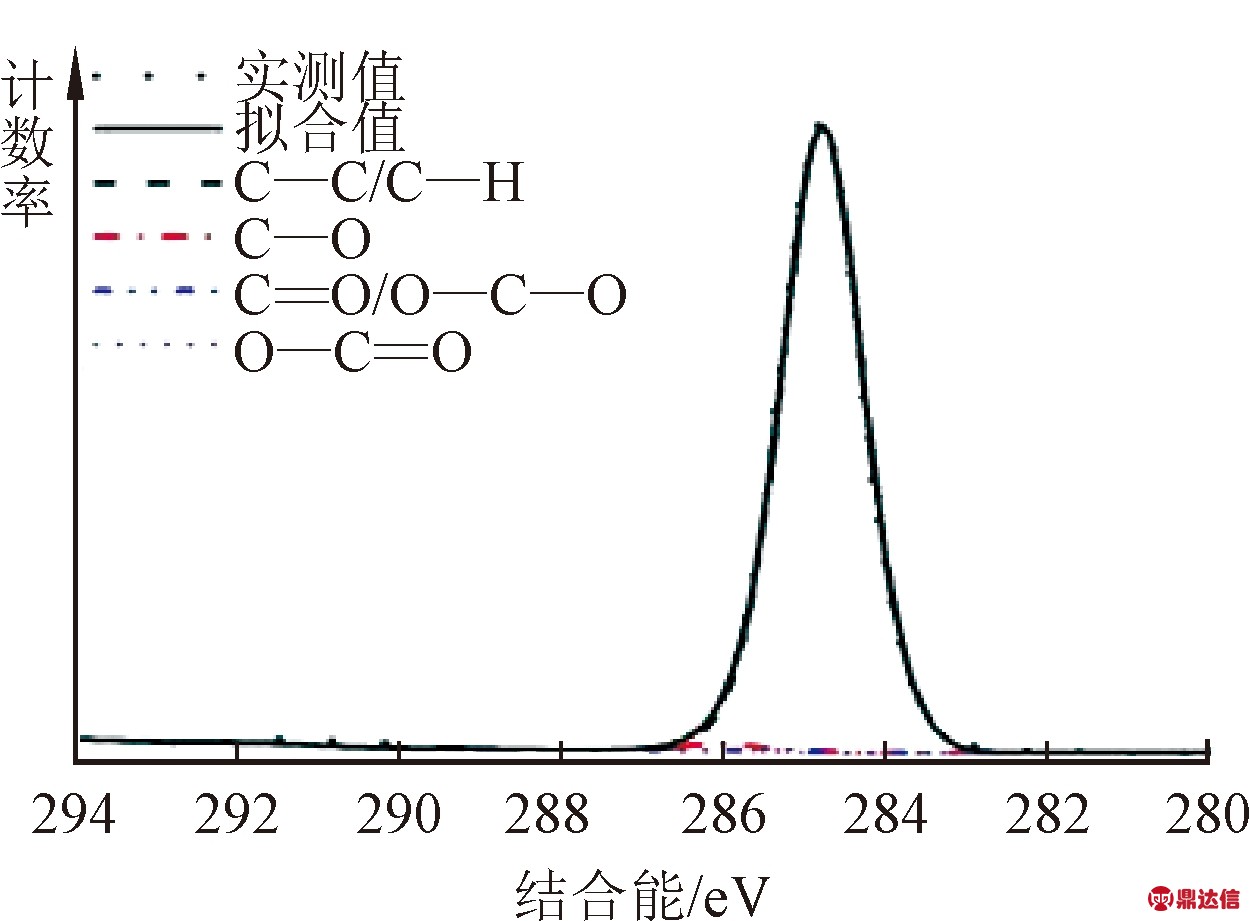
(a)老化时间为0 h
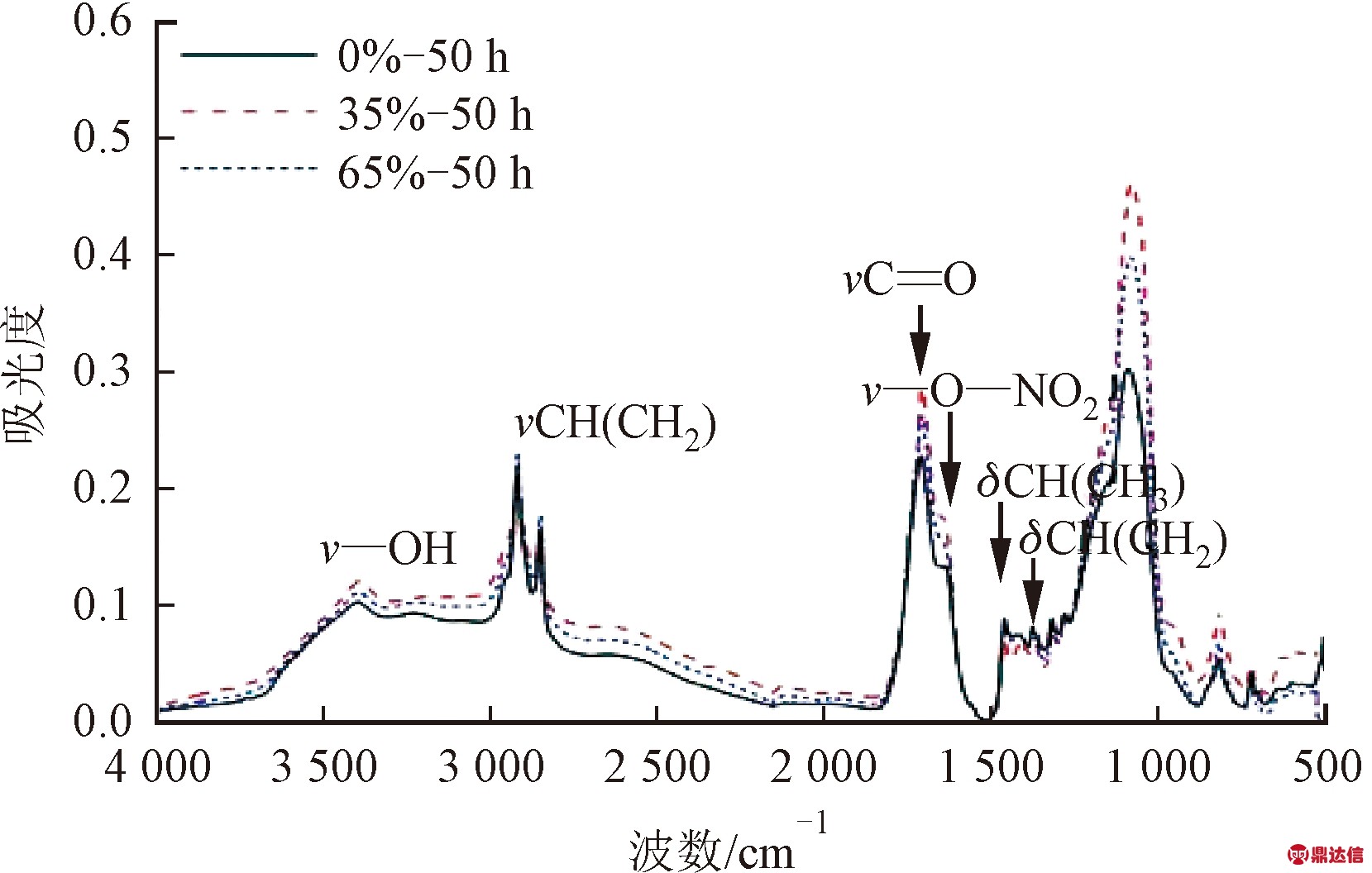
(b)老化时间为50 h
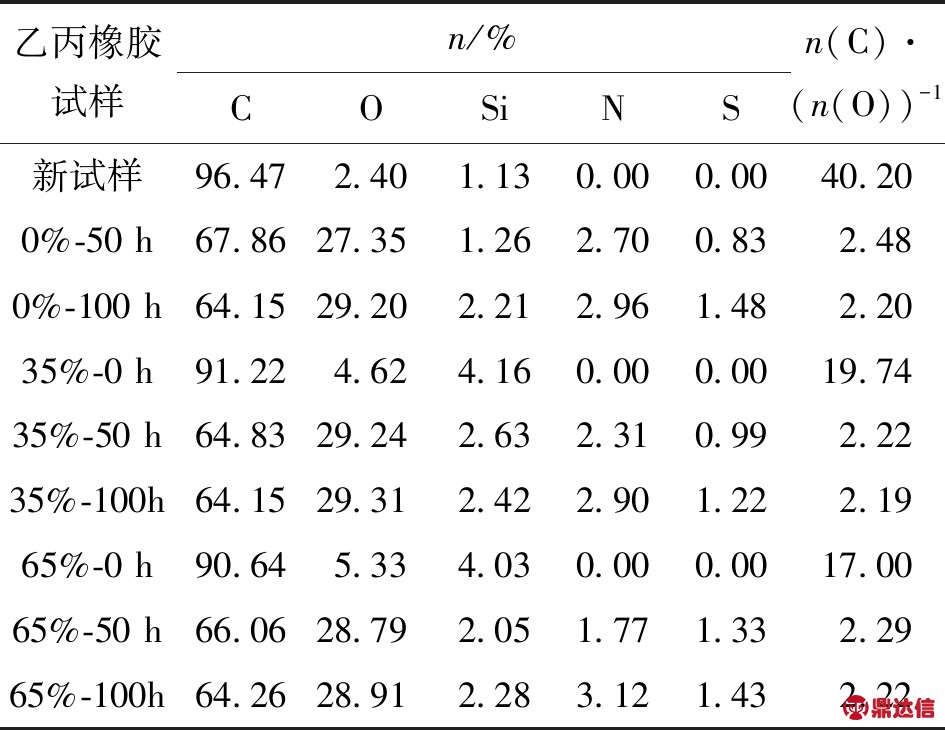
(c)老化时间为100 h
图9 不同老化时间下乙丙橡胶试样红外光谱随拉伸率的变化
2.6 XPS分析
表2给出了XPS测得的不同条件老化前后乙丙橡胶试样表面化学元素的组成和相对含量n,即该元素波峰对应的峰面积与整个能谱总的峰面积的比值。
表2 XPS测得的乙丙橡胶表面元素组成及相对含量
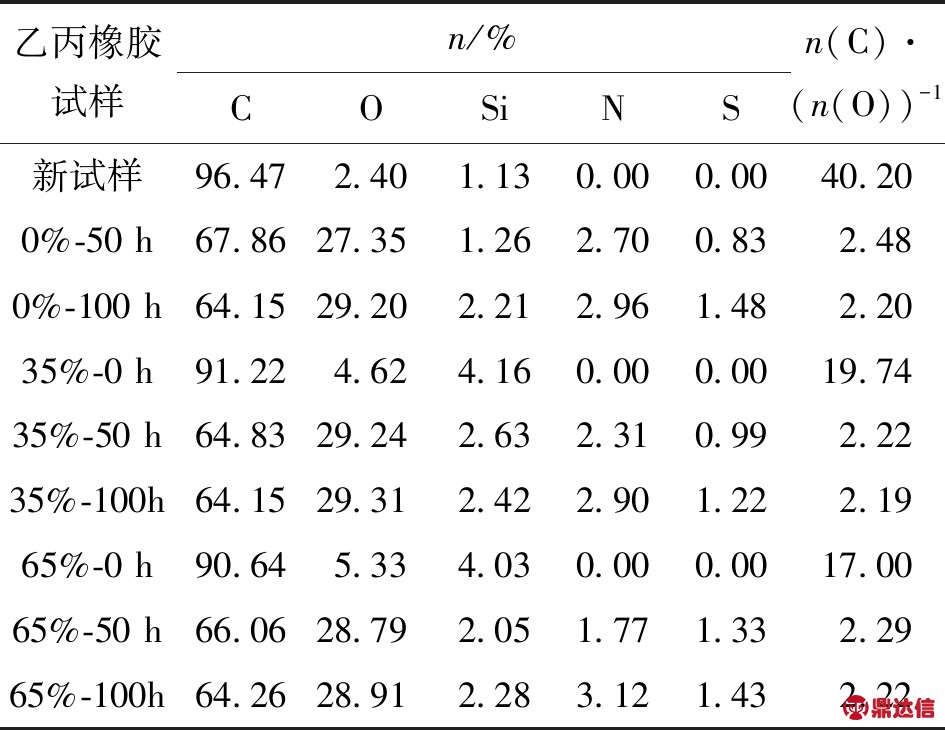
测试结果显示,乙丙橡胶原始试样表面的n(C)、n(O)最高,n(Si)较低,三者总和为100%,其中Si元素主要来源于乙丙橡胶体系中添加的白炭黑,O元素来自制造过程中的添加物、氧化或表面吸附。在机械应力单独作用下,n(C)略微减小,n(O)、n(Si)略微增加,结合扫描电镜的观察结果分析,这是在机械拉伸后乙丙橡胶内部添加物析出至表面引起的。在电应力或电-机械应力共同作用下,乙丙橡胶表面n(C)减小,n(O)增加,n(C)/n(O)明显降低;同时表面检测到N元素和S元素,与红外光谱的测试结果一致,说明放电产生的NO2和SO2在乙丙橡胶表面形成了含氮和含硫极性基团。在同一拉伸率下,乙丙橡胶表面元素相对含量的变化幅度随老化时间增加而增加:原始试样老化至50 h时,元素相对含量的变化最为剧烈,n(C)/n(O)从40.2降低至2.5以下;老化时间进一步延长至100 h时,元素相对含量的变化放缓,n(C)/n(O)变化幅度低于15%,说明老化至50 h时,乙丙橡胶表面的化学破坏已经很严重、趋近饱和。相同老化时间下,若叠加机械拉伸应力,乙丙橡胶表面元素含量的变化幅度略微增加,但并非随拉伸率单调变化。
乙丙橡胶中C元素与O元素的结合增加时,C元素的1s光电子能谱会向高结合能方向移动。根据结合能的大小,高分辨的C1s光电子能谱可以分解为4种成分,分别为C—C/C—H、C—O、O—C—O/C=O和O—C=O,它们对应的结合能分别是(284.6±0.2) eV、(286.2±0.2) eV、(287.7±0.2) eV和(289.0±0.2) eV[21-22]。为进一步说明电-机械应力作用后乙丙橡胶表面化学结构的变化,对高分辨的C1s光电子能谱进行分峰操作,结果如图10所示,表3给出了试样中不同结合态的n(C)的统计结果。
表3 不同乙丙橡胶试样的C1s分峰结果
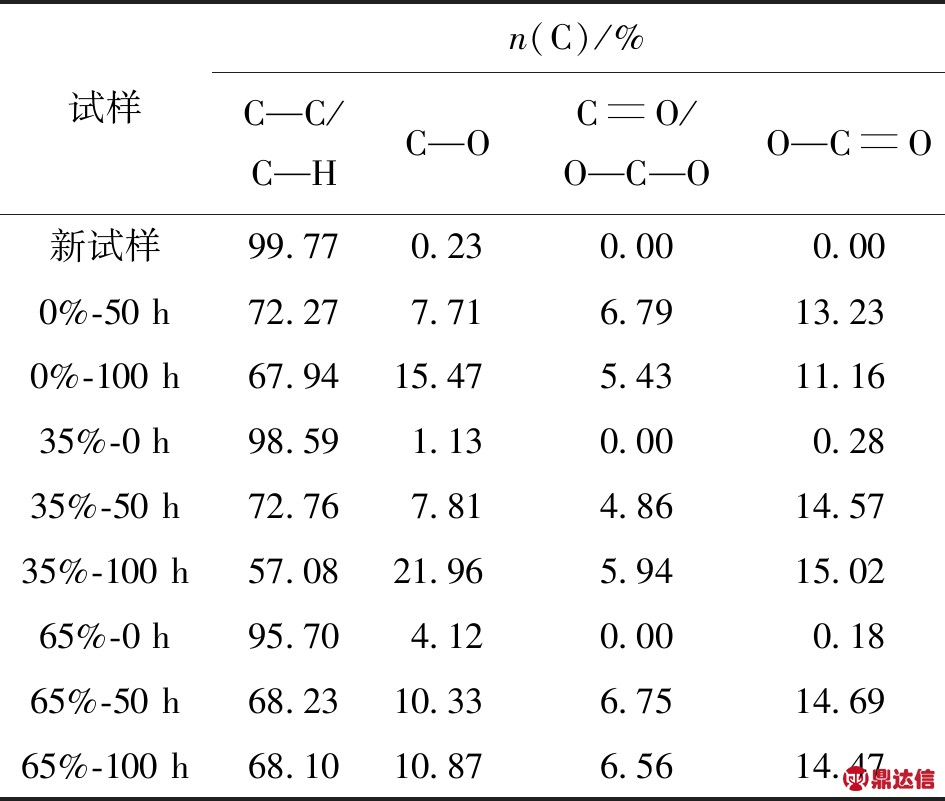
结合图10和表3可知,新试样表面C元素的主要存在形式为C—C/C—H键结合,n达到99.77%,此外还有少量C元素以C—O形式存在,可能是制造过程中的添加、氧化导致的。机械应力单独作用下,乙丙橡胶表面C1s光电子能谱略微变化,C—O峰所占比例稍增加,可能是乙丙橡胶内部添加物在拉伸情况下析出至表面引起的。在电应力或电-机械应力作用下,C1s谱线变宽,并向着高结合能方向移动;分峰处理后,C—C/C—H峰占谱线比例减小,C—O、C=O/O—C—O和O—C=O峰占谱线比例增加,说明老化过程中乙丙橡胶表面发生了断链和氧化反应,生成了醇、酯、酸等物质。
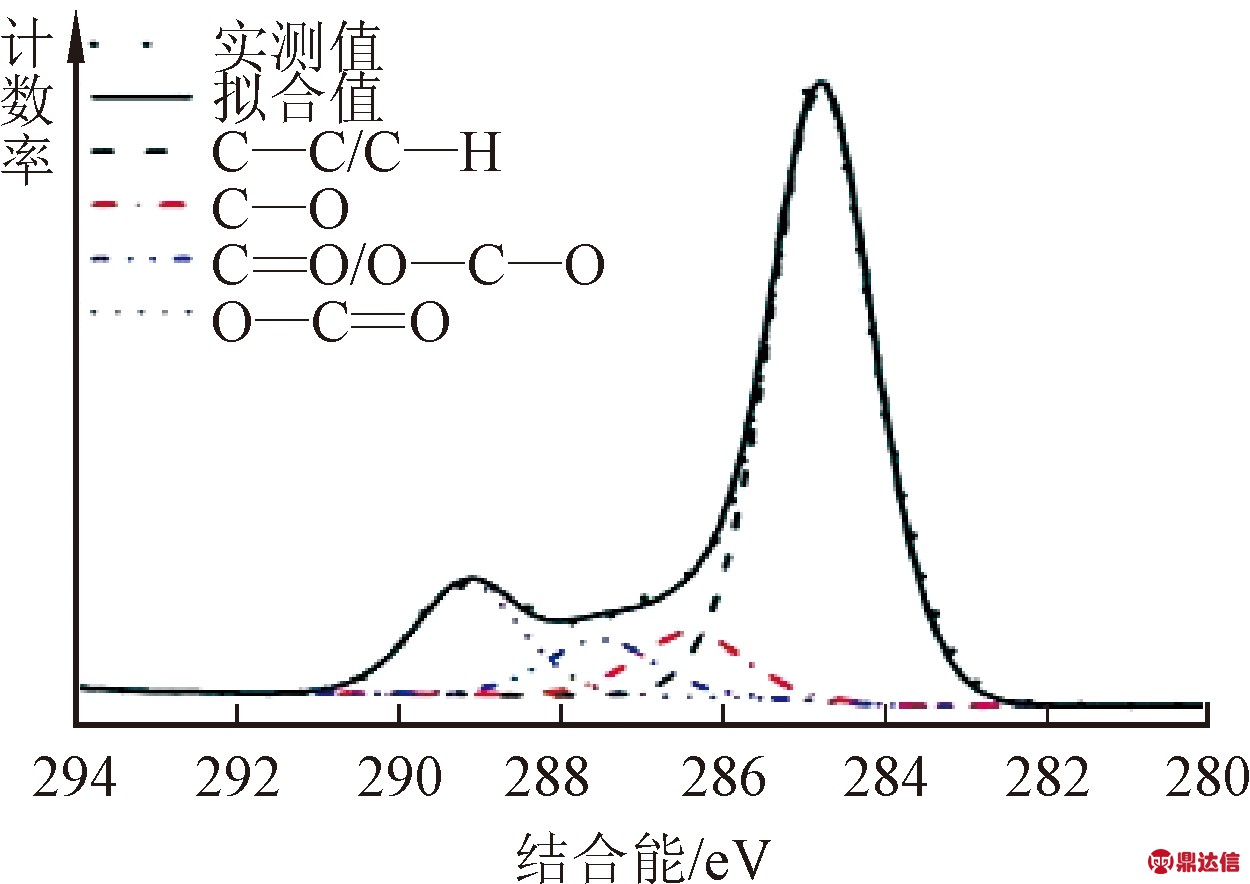
(a)新试样
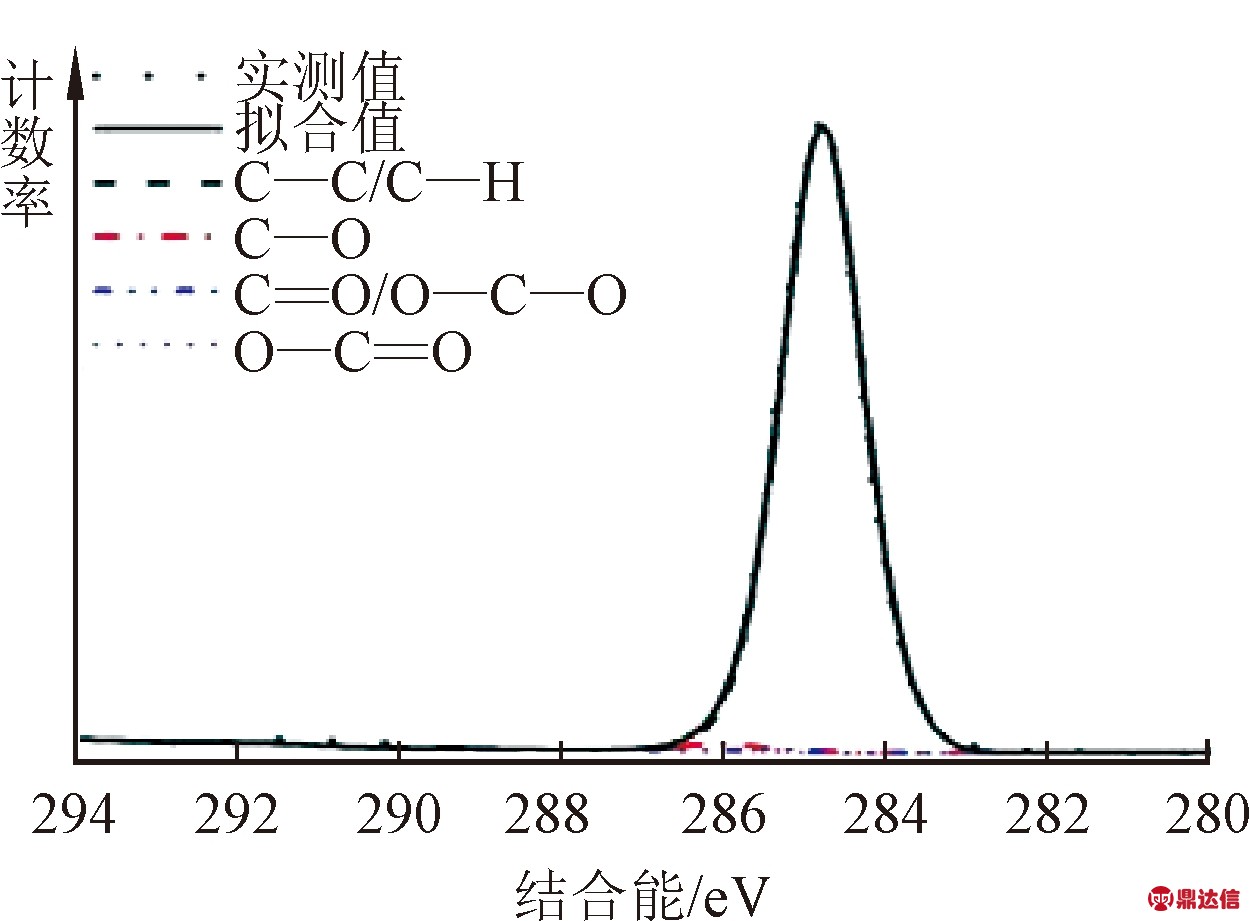
(b)35%-0 h

(c)65%-0 h
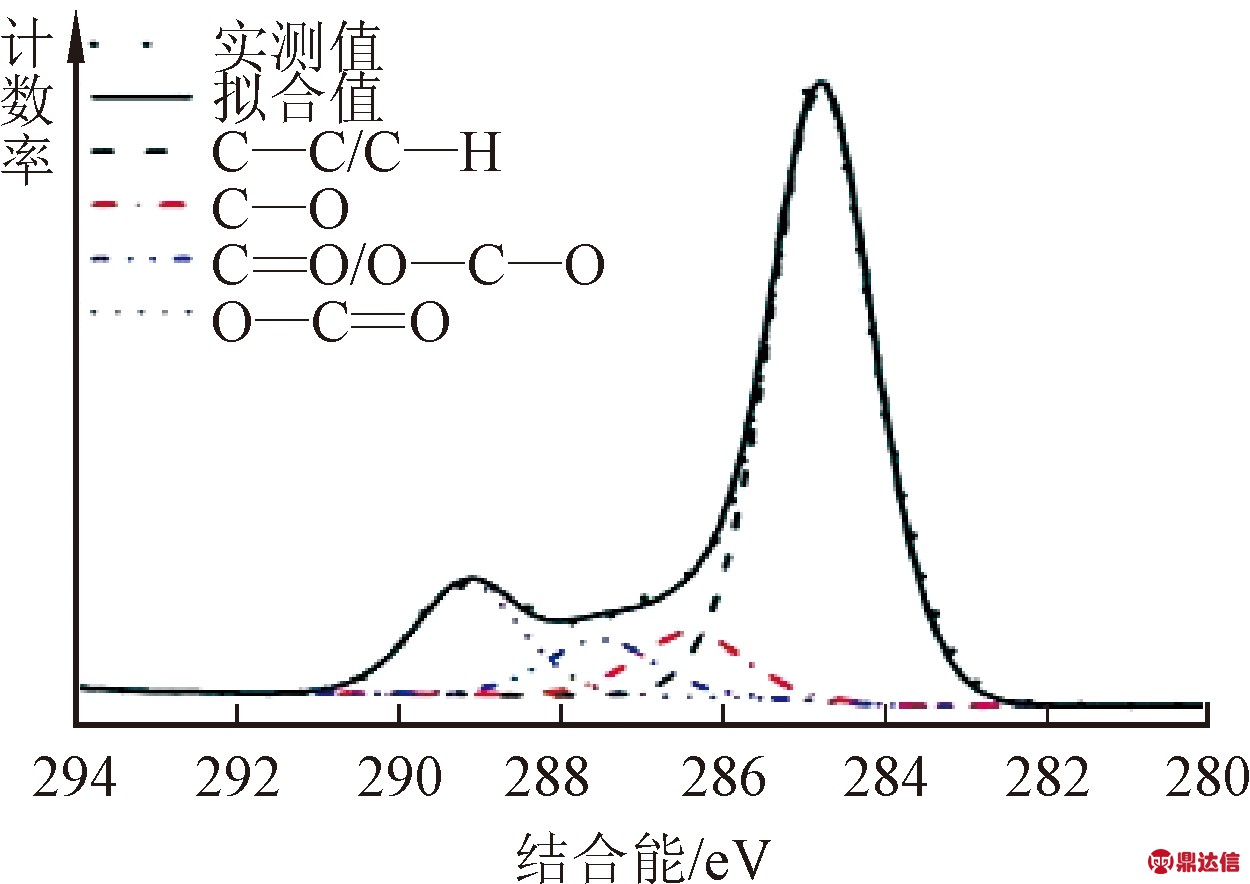
(d)0%-50 h
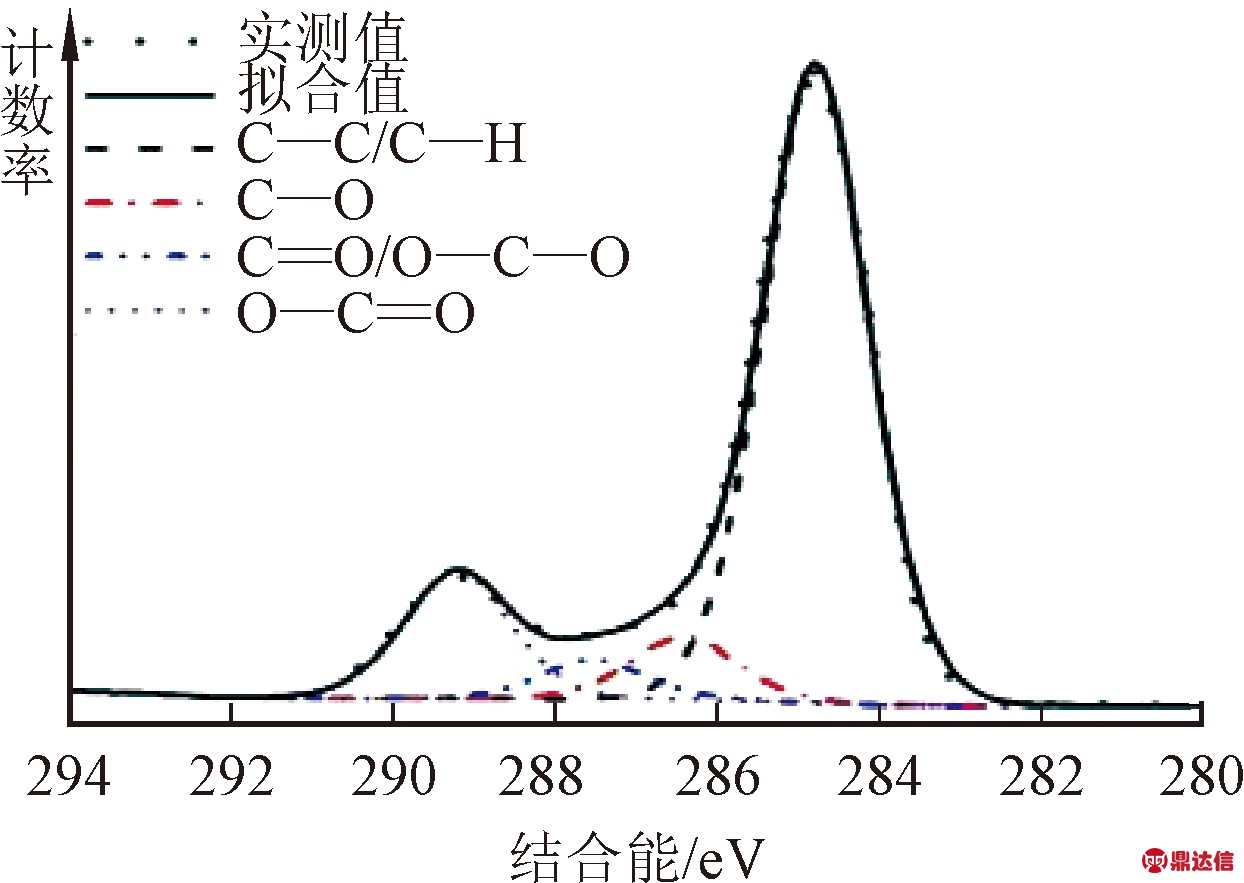
(e)35%-50 h
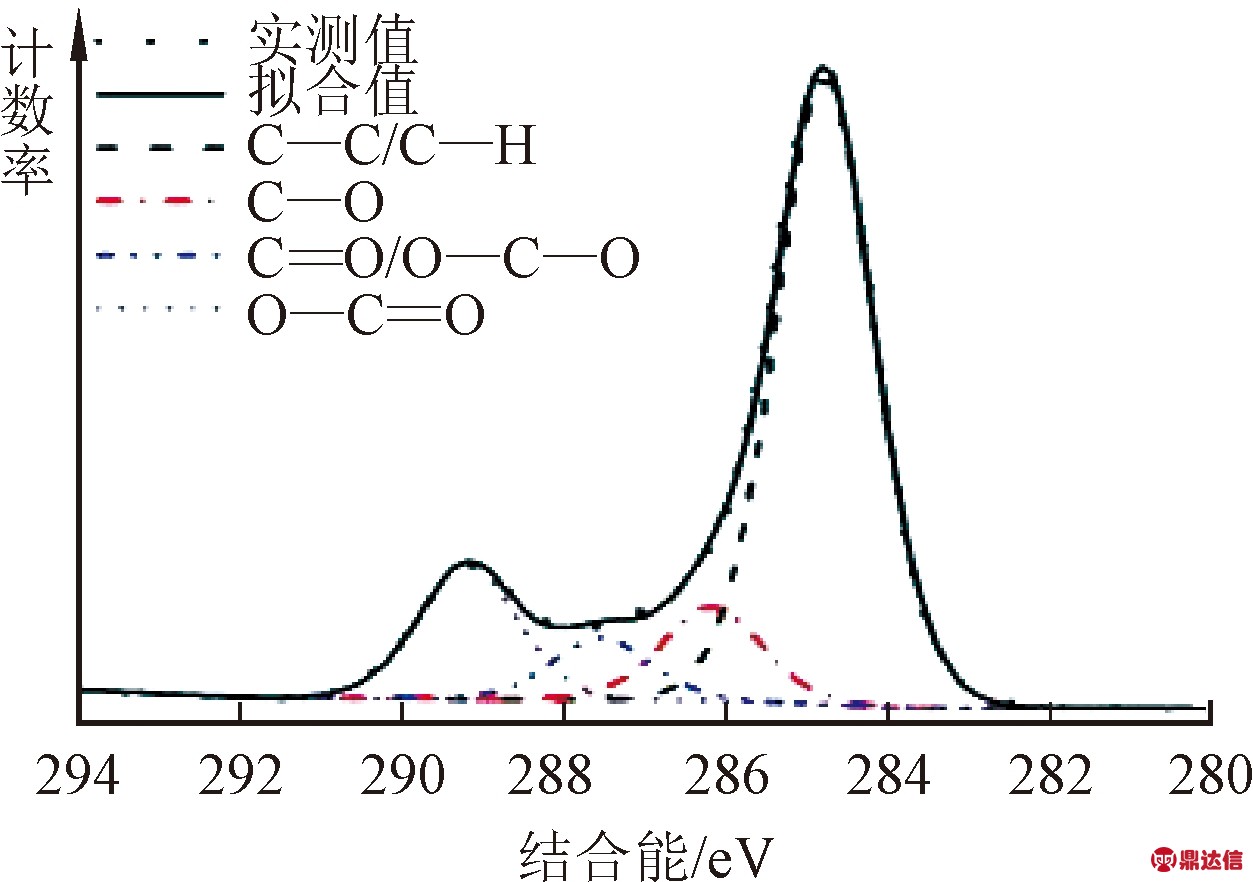
(f)65%-50 h
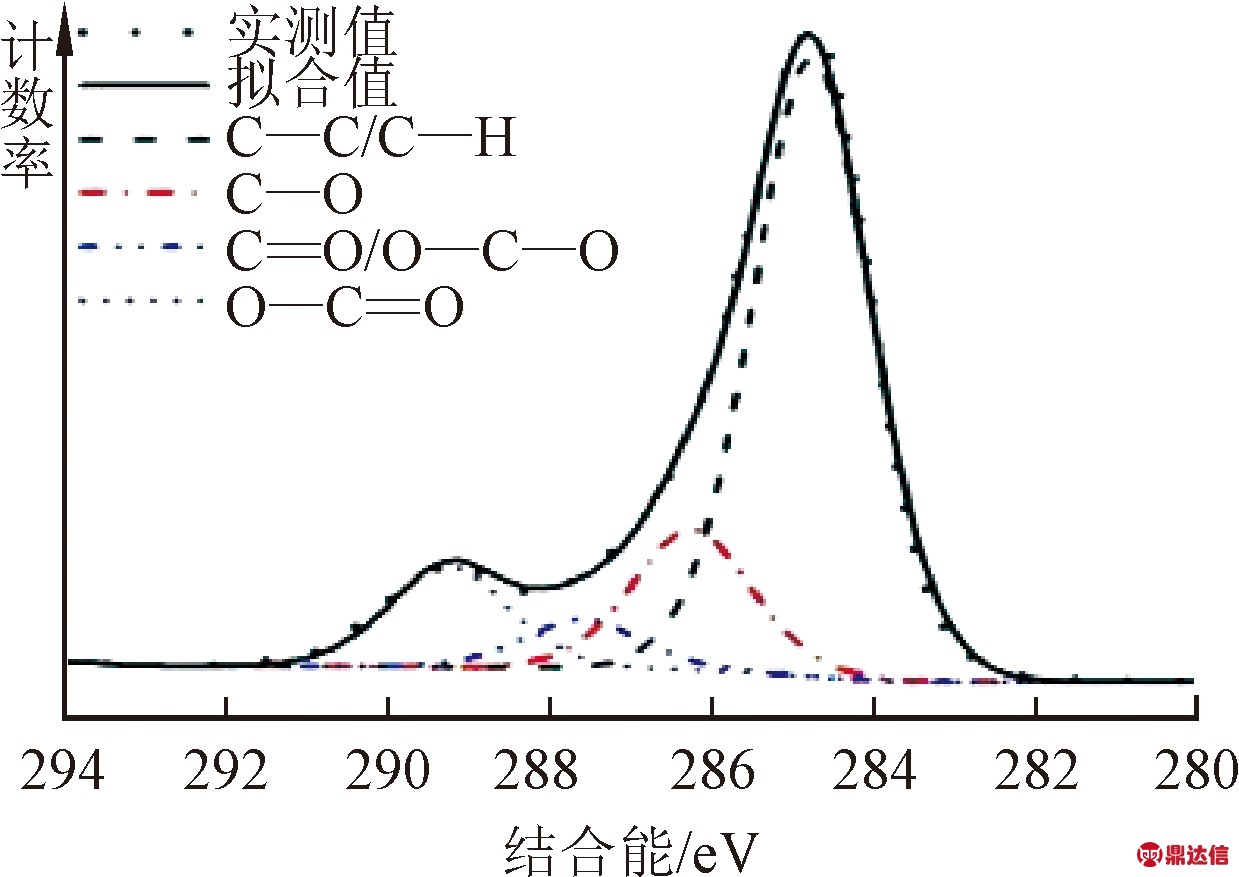
(g)0%-100 h
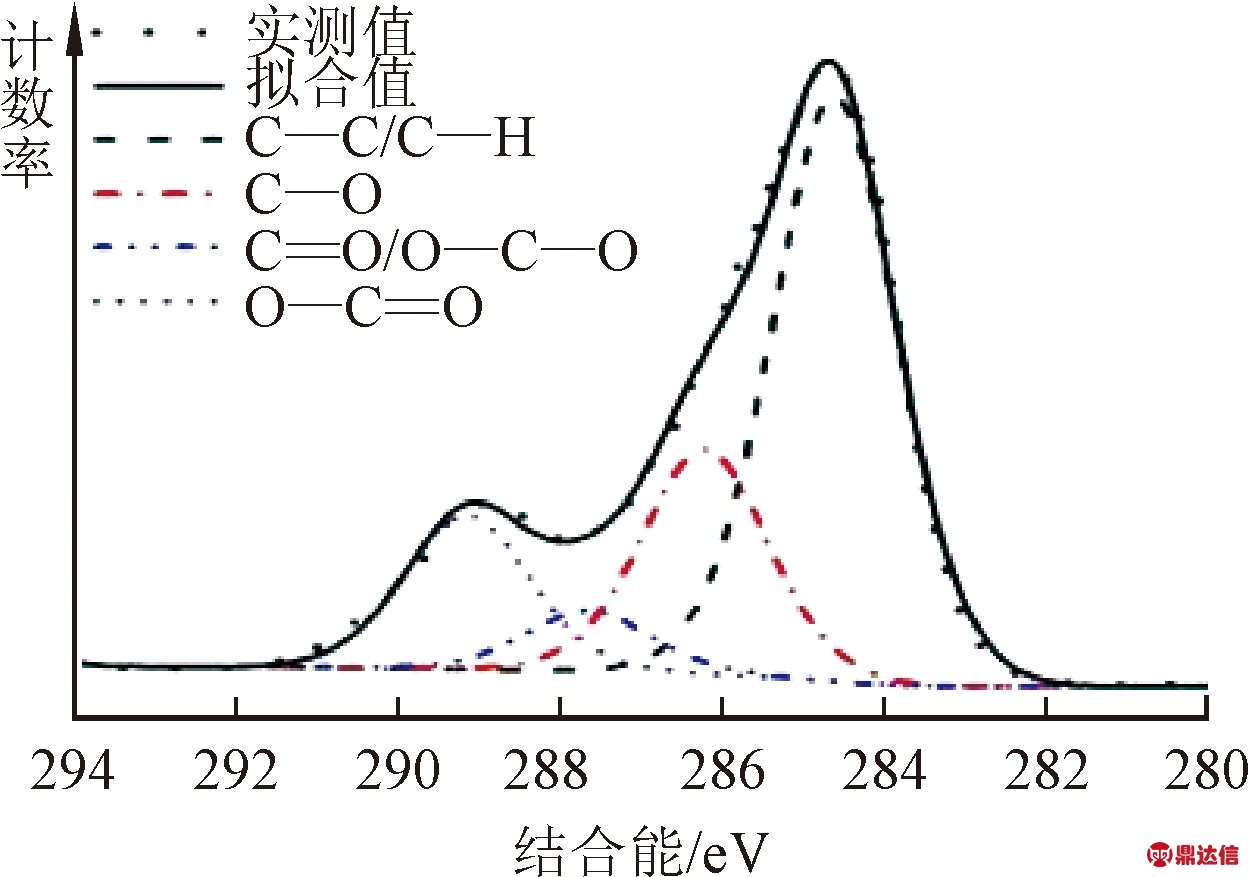
(h)35%-100 h
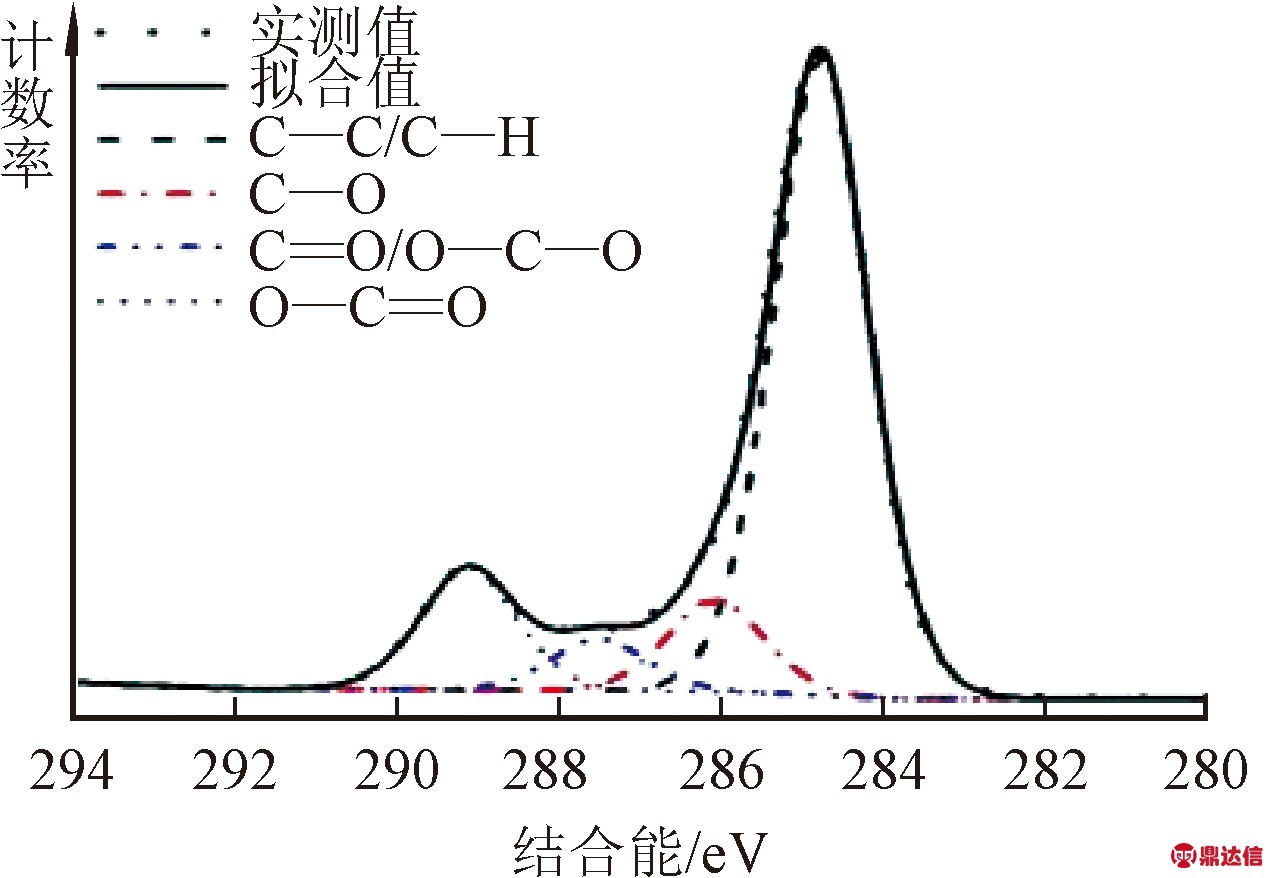
(i)65%-100 h
图10 不同乙丙橡胶试样C1s光电子能谱分峰结果
在相同拉伸率下,随老化时间增加,C—O、C=O/O—C—O和O—C=O中的氧化态C元素含量增加,而C—C/C—H中的n(C)减小;机械应力的叠加使整体C1s光电子能谱的变化更加明显,对应的高氧化态n(C)略微增加。这说明它促进了乙丙橡胶表面C元素的氧化反应,可能是乙丙橡胶分子断链产生的自由基在拉伸状态下与放电生成的氧化物接触更充分所致,但上述促进作用并非与机械拉伸率呈单调对应关系。
3 讨 论
FTIR和XPS分析结果表明,仅对试样进行机械拉伸时,乙丙橡胶表面Si、O元素含量略微增加。在电应力作用下,乙丙橡胶分子中的部分(CH2)n主链、—CH3侧链以及C—H键被切断,生成了—OH、C=O、—O—NO2—和—O—SO2—等氧化基团,表面n(C)降低,n(O)增加,出现了N元素和S元素,C—O、C=O和O—C=O等氧化态的n(C)增加。当机械应力叠加在电应力上,对上述的断链、氧化反应具有一定的促进作用,但并未改变反应类型和生成物的种类。
根据上述分析结果,进一步讨论电-机械应力作用下乙丙橡胶表面化学结构的变化。本文认为,在电应力作用下,气隙放电产生的高能粒子轰击试样表面,导致乙丙橡胶分子中的部分(CH2)n主链、—CH3侧链以及C—H键被切断,生成烃基烷基自由基R·和H·,反应式为

自由基在放电作用下按照过氧化物游离基机理发生氧化反应,生成过氧自由基ROO·,反应式为
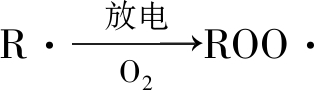
过氧自由基ROO·进一步与乙丙橡胶分子反应,生成氢过氧化物ROOH和R·,反应式为
ROO·+EPDMROOH+R·
R·自由基可进一步发生氧化反应,而氢过氧化物ROOH可分解为烷氧基RO·和羟基·OH,反应式为
ROOHRO·+·OH
羟基·OH可与乙丙橡胶分子反应生成R·和水,反应式为
·OH+EPDMH2O+R·
RO·作为一种重要的中间产物,部分与R·反应生成ROR,部分经过β裂解形成羰基C=O,反应式为
RO·+R·ROR
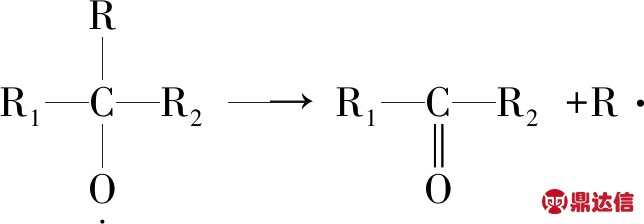
上述过程可解释老化后乙丙橡胶表面出现以C—O、C=O形式存在的C元素。部分羰基C=O以过氧化物游离基机理进一步氧化生成羧基O—C=O,在乙丙橡胶表面生成酸和酯,反应式为

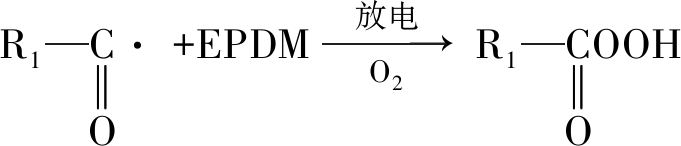

这个过程[22-23]中,机械应力的叠加导致乙丙橡胶分子间的物理交联和缠结变弱,分子活性增加,高分子链间的平均距离增大,更容易暴露在放电粒子轰击和氧化环境中,对上述反应具有一定的促进作用[24]。放电过程还产生了强氧化性的NO2和SO2,乙丙橡胶表面在放电作用下变得粗糙、内部填料析出,并在—OH和粗糙表面吸水的共同作用下变潮湿,NO2和SO2溶解在潮湿的乙丙橡胶表面,最终生成了含氮和含硫极性基[25-26]。
从乙丙橡胶试样的机械性能、体积电阻率和交联度这3个表征材料体积特性的参数(即体积特性参数)测量结果来看,老化后试样的断裂伸长率和拉伸强度小幅下降(降幅不超过20%),体积电阻率几乎不变(1016~1017 Ω·cm),交联度与原始试样相差无几(变化幅度不超过1%)。老化过程中乙丙橡胶试样表面产生了微裂纹,导致局部应力集中,使机械强度下降。由于机械强度更多的是反映体积状态,而微裂纹主要是对表面的破坏,因此老化后试样的断裂伸长率和拉伸强度虽有下降,但幅度未超过20%。总的来说,可以认为乙丙橡胶试样老化后的各项体积特性未发生显著劣化。
这说明,在电-机械应力作用下,虽然试样表面破坏严重,发生了分子链断裂、氧化,生成了羟基、羰基、酯基等,但由于乙丙橡胶材料中添加物和填料较多,在试样表面层被破坏后添加物和填料析出,阻挡了放电产生的高能粒子和活性物质对内部的进一步破坏。因此,试样的表面形态及性能发生了显著变化,但体积特性参数保持稳定。其中,引起试样性能劣化的主要因素是电应力,机械应力对表面化学结构的破坏具有一定的协同促进作用,但未引起试样体积特性的明显变化。
4 结 论
本文以电缆预制接头用三元乙丙橡胶为研究对象,搭建了模拟电缆附件绝缘界面受力状况的电-机械应力耦合试验装置,将乙丙橡胶试样在不同应力条件下老化后,对其表面形貌、力学及电学特性进行了观察及测量,并结合交联度、FTIR、XPS测试分析了老化机理,结论如下。
(1)表面微观及化学分析表明,电-机械应力作用对乙丙橡胶试样表面产生了明显的物理破坏(微裂纹)及化学破坏。在电应力作用下,乙丙橡胶分子中原有基团发生裂解并被氧化;机械拉伸将导致分子缠结变弱,增加内部化学键暴露,促进电应力对橡胶表面化学结构的破坏。
(2)在电-机械应力作用下,乙丙橡胶的各项体积特性较为稳定,除因表面微裂纹导致的机械强度下降外,体积电阻率和交联度都未发生显著变化。
(3)在模拟附件界面的电-机械应力作用条件下,乙丙橡胶的性能变化主要发生在表面,体积特性参数变化不大。这可能与乙丙橡胶材料中大量的添加物和填料有关:当试样表面层乙丙橡胶分子被破坏,添加物和填料暴露在表面,形成了有效保护层,阻挡了放电粒子和活性基团对内部的进一步破坏。