摘 要 为了将常规气井常用的电潜泵排水采气工艺应用于高含硫气井,同时满足高含硫气井保护套管的要求,基于高含硫气井的完井方式及电潜泵排水采气工艺自身的技术特点,针对套管保护、气体干扰及深井电潜泵机组振动等问题,在完井管柱设计、工具配套等方面开展了攻关研究,并在L2井进行了排水采气工艺设计。结果表明:①所研发的一套以罐装电潜泵系统为主体、结合锚定式插管封隔器形成的高含硫气井完井管柱系统能够实现电潜泵的正常运行,并且满足保护套管的要求;②采用多相流泵及放气管线可以应对气体干扰的问题,使用自动换向阀可以降低电潜泵复杂流道对气井自喷的影响,配套带锚定机构的插管封隔器能够降低管柱振动;③所设计的罐装电潜泵系统可应用于Ø244.5 mm和Ø177.8 mm套管,其中Ø244.5 mm套管对应的电潜泵最大排量为900 m3/d、最高扬程为4 500 m;Ø177.8 mm套管对应的电潜泵最大排量为300 m3/d、最高扬程为3 000 m。结论认为,该项研究成果为高含硫气井实施电潜泵排水采气工艺提供了技术支撑。
关键词 高含硫气井 电潜泵 排水采气 罐装系统 完井方式 保护套管 插管封隔器 多相流泵
0 引言
高含硫气井在完井时,一般采用井下安全阀+耐蚀合金油管+永久式封隔器的完井管柱,并在封隔器以上的油管—套管环空中注入保护液[1-6],避免生产套管与酸性流体介质直接接触,保证气井安全生产。在此完井方式条件下,气井生产时,油管成为唯一的生产通道,油管和套管不连通。随着地层压力降低,气井携液能力逐渐下降;如开展排水采气工艺,受限于上述完井方式,无现成排水采气工艺实施通道[7],从而加剧井底积液,积液严重时会引起气井水淹关井。特别是部分大产水量的气井,水淹后复产较为困难。
电潜泵排水采气工艺作为一种高扬程、大排量的排水工艺,用于大产水量气井的水淹复产,效果有目共睹[8]。但实施电潜泵排水采气工艺的常规气井,其完井管柱中没有封隔器。生产时,套管和油管处于连通状态,井内流体与套管直接接触,这种完井方式难以满足高含硫气井保护套管的要求,使电潜泵在高含硫气井排水采气的应用受到很大限制。因此,围绕电潜泵排水采气工艺在高含硫气井的应用所面临的技术难点,结合高含硫气井完井方式和电潜泵排水采气工艺技术特点,在完井管柱设计、工具配套等方面开展研究,提出一项适合于高含硫气井的电潜泵排水采气工艺技术,为高含硫气井开展电潜泵排水采气工艺探索出一条可行的道路。
1 技术挑战
1.1 套管的保护
高含硫气井完井方式强调对套管的保护,生产时,油管成为唯一通道,油、套环空与油管中的流体处于隔绝状态。而目前应用了电潜泵排水采气工艺的常规气井,其完井管柱中没有封隔器(图1),气井产出的气体主要从油、套环空产出,因此会破坏这种隔绝状态,导致具有腐蚀性的介质直接与套管接触,使套管失去保护。需要针对高含硫气井特殊的井筒完整性和保护套管的要求,重新设计适用于开展电潜泵排水采气工艺的完井方式,以解决两者之间的矛盾。
1.2 气体干扰的影响
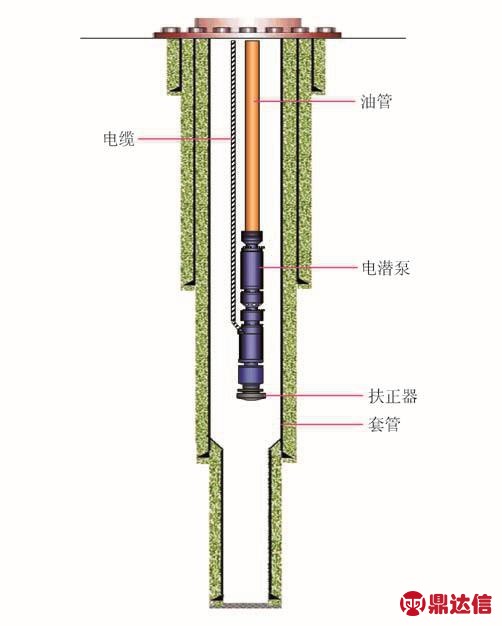
图1 采用电潜泵排水采气工艺的常规气井完井管柱示意图
气体干扰是电潜泵用于气井排水采气工艺必然面临的问题,将对电潜泵的平稳运行造成影响,严重时会导致电潜泵气锁停机,从而降低电潜泵运行时效,难以达到连续排液、让气井恢复正常生产的目的。因此,如何降低气体干扰对电潜泵运行的影响是设计气井完井方式和电潜泵系统选型时必须考虑的问题。
2 关键技术对策
针对高含硫气井完井特点,结合电潜泵用于高含硫气井排水采气工艺面临的技术难题,从完井管柱设计、应对气体干扰、降低电潜泵机组震动等方面进行技术攻关,并提出了针对性的技术方案。
2.1 以罐装电潜泵系统为主体的完井管柱系统
为实现高含硫气井的顺利排水采气,并完成对套管的保护,气井的完井管柱系统采取罐装电潜泵系统与插管封隔器相结合的方式,如图2所示。
罐装电潜泵系统主要包括罐装系统和电潜泵两部分,其中罐装系统为顶部带有电缆穿越系统、下部为带有油管密封总成的圆筒结构,两头均有相应的密封机构。将整套电潜泵机组置于罐装系统内,电潜泵机组上部与油管连接至罐装系统的顶部,罐装系统的顶部与上部完井油管连接,罐装系统下部的油管密封总成插入下部插管封隔器中。电潜泵机组位于罐装系统内的电缆通过罐装系统上部的电缆穿越系统与位于罐装系统外的电缆相连,从而保证电力的供应。
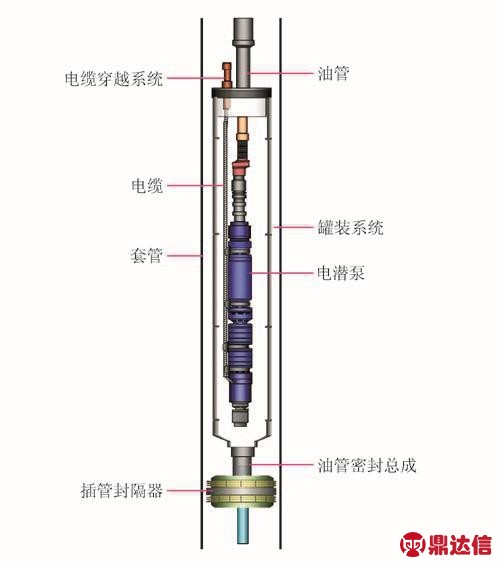
图2 考虑套管保护的电潜泵完井管柱示意图
电潜泵运行时,所有流体均从插管封隔器内部通道进入罐装内,再被泵送至油管内直到地面,油管是唯一的流通通道,井内气水介质不会进入油套环空内。
2.2 应对气体干扰的措施
2.2.1 多相流泵
电潜泵机组的核心部件为离心泵,其对气体的抗干扰能力是决定电潜泵排水采气时能否正常运行的关键。为降低离心泵吸入口游离气的含量,常规电潜泵机组一般配有分离器。在生产时,套管主要产气,油管主要产水。而采用罐装电潜泵系统后,气井产出的气和水都通过电潜泵进入油管中,油管是唯一的生产通道。如果再配备分离器,则分离出的气体容易集聚在罐装系统的上部,压低罐装内的液面,最终引起离心泵气锁停机,因此罐装电潜泵系统不能配备分离器。但为保证整套电潜泵机组在高气液比情况下的正常运行,需采用对气体抗干扰能力更高的离心泵。多相流泵是近年来离心泵在克服气体干扰方面取得的一大进展,该型泵通过大角度的叶轮设计允许更多的气体通过叶轮流道(图3),同时将流道中的大气泡打碎为细小的气泡,减少气泡聚集。其对气体的抗干扰能力比一般离心泵高15%~20%(图4),能够在井下游离气含量达到75%的情况下正常工作而不被气锁,满足了离心泵在罐装系统中正常工作的需要。

图3 多相流泵流道结构示意图
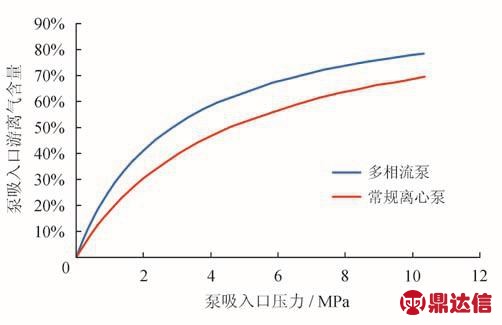
图4 多相流泵与常规离心泵性能对比图
2.2.2 放气管线
由于气水自然分离,在罐装系统内部,游离气容易聚集在罐装系统的上部,压低罐装系统内的液面。当液面被压低至泵吸入口附近时,会引起电潜泵运行波动,甚至导致气锁停机。为进一步提高电潜泵机组对气体的抗干扰能力,在罐装系统上部安装放气管线,从罐装系统上部直接接至井口。通过地面控压放掉罐装系统内的气体,保证电潜泵在罐装系统中的沉没度以减少气体对电潜泵运行的影响。
2.3 气井自喷时流道切换
部分气井通过一段时间连续排液后,可实现自喷生产,这时就不再需要电潜泵进行辅助排液,电潜泵可停止工作。但在罐装电潜泵系统中,由于流体直接从泵吸入口进入电潜泵内,要通过电潜泵内部复杂的流道才能进入上部油管中。而流体流经电潜泵流道时会产生较大的压降,从而减弱气井带液自喷的效果。
自动换向阀因其灵活的流体转向控制优势已在电潜泵排水采气井中得到了较好的应用[9],在此,可考虑在电潜泵罐装系统的电潜泵出口加装自动换向阀,以实现电潜泵工作\关闭状态下流道的切换,增强气井带液自喷的效果。该工具主要通过其内部挡块和旁阀实现流体的转向控制(图5)。当电潜泵正常工作时,流体推动内部挡块向上移动,自动换向阀的旁阀关闭。流体经电潜泵从自动换向阀内部进入油管,直到地面;当气井能够自喷时,电潜泵停止工作,内部挡块下移,旁阀打开,流体直接从旁阀进入油管,则不需经过电潜泵,从而避免了不必要的压降损失。
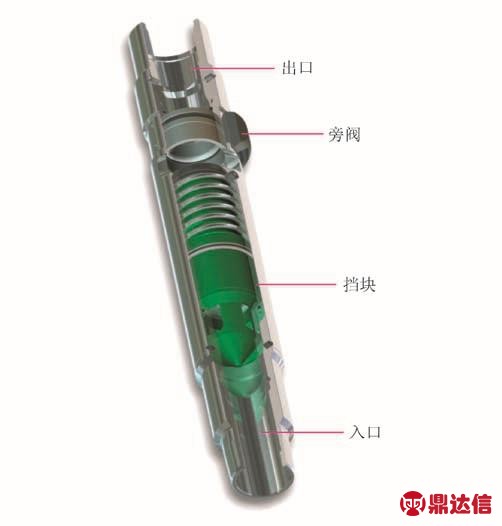
图5 自动换向阀结构示意图
2.4 降低管柱震动的对策
川渝气田的高含硫气井井深大多超过3 000 m,如龙岗礁滩气藏井深普遍超过5 000 m。电潜泵在超过3 000 m的井中运行,产生的管柱震动较大。以TD90井为例,泵挂深度达到4 050 m,电潜泵管柱仅采用扶正器进行扶正;在电潜泵运行时,使管柱的径向震动加速度常常超过4个重力加速度。如果震动得不到有效控制,将对电潜泵机组的运行带来极大隐患,同时也可能导致插管封隔器失效,使气水介质进入油、套环空。因此在选择封隔器时,应选用带有锚定机构的插管封隔器(图6)。通过带锚定机构的封隔器,来降低管柱震动,保证电潜泵机组的稳定运行和封隔器密封效果。
2.5 防腐材质选择
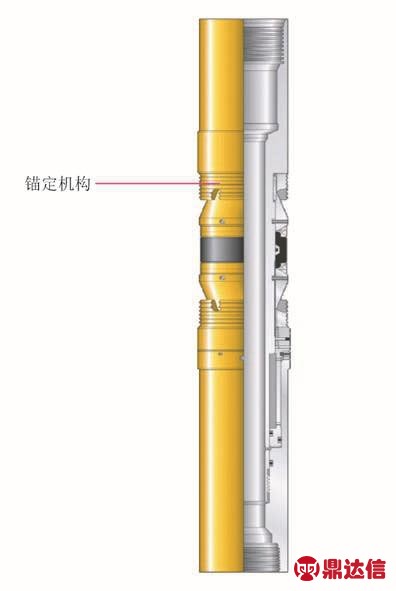
图6 带锚定机构的插管封隔器示意图
罐装电潜泵系统的材质(电潜泵机组材质和罐装材质)按照气井相应的气水介质条件,选用高等级的防腐材质并结合防腐喷涂即可,通行做法如下[10-15]:①各接头采用不锈钢材料,壳体采用镀层、涂层防腐;②电潜泵机组壳体外表面及接头外表面为高镍合金层,再采用防腐蚀涂料进行防腐处理;③保护器轴、泵轴、分离器轴采用高强度、耐腐蚀的蒙乃尔合金材料;④泵出口接头、先镀高镍合金层,再在外表喷涂耐油耐腐蚀涂料或采用不锈钢材料制造;⑤连接花键套采用高强度、耐腐蚀的蒙乃尔合金材料;⑥大扁、小扁电缆采用铅护套,铠皮采用蒙乃尔材料;⑦小扁电缆头外壳采用高镍铸铁材料,并外加防腐涂层,如有必要可采用黄金小扁头;⑧电缆保护器采用不锈钢材料。
3 实施步骤与技术参数
3.1 实施步骤
具体实施时,分为以下几步:①完成通井刮管作业;②下入带锚定机构的插管封隔器,油、套环空替入保护液并坐封;③在井口完成罐装电潜泵系统的连接;④下入罐装系统,油管密封总成插入已经坐封的带锚定机构的插管封隔器内;⑤完成井口装置安装与生产流程恢复;⑥启动电潜泵运转。
电潜泵运转时,气液从插管封隔器和锚定式油管密封总成内部通道进入到罐装系统内,再经离心泵一起泵入进油管直至地面。整个过程不会有气或水进入环空中,从而实现在排水采气的同时保护套管的目的。同时,整个电潜泵机组位于罐装系统内,依靠带有锚定机构的插管封隔器,相比于常规的电潜泵工艺完井,管柱震动能得到有效降低,以保证插管封隔器的密封效果。
3.2 选型流程及技术参数
罐装电潜泵系统中电潜泵机组的选型与常规电潜泵机组的选型相比,除不进行分离器选型外,其余流程基本一致。通过气井流入动态与泵特性曲线的综合分析,对气井进行不同生产压差下的工况计算,使优选出的离心泵、电机等机组运行参数能满足气井各生产阶段的需求,如图7所示。
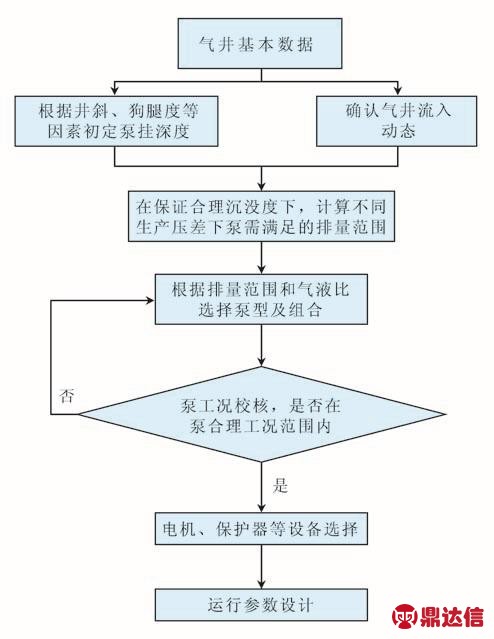
图7 电潜泵排水采气工艺机组选型流程图
同时,罐装电潜泵系统的关键技术参数包括电潜泵工作的最大排量与最大扬程,其主要受限于罐装规格,而罐装规格需要与套管规格相匹配。因此根据套管规格,选择对应罐装尺寸,并结合电潜泵机组的选型结果,形成罐装电潜泵关键技术参数,如表1所示。
4 实例设计
以L2井为例,其产层深度为4 700 m,地层压力为38 MPa,温度为140 ℃;原井内管柱封隔器下入深度为4 500 m,封隔器以上为Ø177.8 mm套管,该井硫化氢含量为15 g/m3。生产初期自喷期间最高产水量为150 m3/d,气藏工程设计推荐该井的排水规模为200 m3/d。
4.1 完井管柱设计
在完井管柱方面,根据该井原井下封隔器位置及封隔器以上套管尺寸,设计罐装电潜泵系统泵挂位置4 100 m,新下入带锚定机构的插管封隔器位置4150 m。整个完井管柱从下到上分别为带锚定机构的插管封隔器、电潜泵罐装系统和油管。其中,电潜泵罐装系统配套自动换向阀以实现电潜泵工作\关闭状态下流道的切换、放气管线以降低气体干扰的影响,带锚定机构的插管封隔器以降低管柱震动,具体完井方式如图8所示。
4.2 机组选型设计
根据该井基本井况与生产情况,按照电潜泵排水采气工艺设计选型流程,并结合目前电潜泵常见规格,对电潜泵机组进行选型设计。
根据气藏工程设计推荐排水规模为200 m3/d的要求和气井流入动态的分析,选用工作排量范围在250~400 m3/d的多相流泵,最大扬程3 000 m,以满足气藏工程对排水规模的需求。同时,L2井封隔器以上为Ø177.8 mm套管,因此选用Ø139.7 mm罐装(壁厚6.2 mm),电潜泵机组最大外径114.3 mm。详细选型设计如表2所示。
4.3 材质选择
根据该井气水介质情况,电潜泵机组和罐装系统使用耐腐蚀材质,具体材质选择如表3所示。
表1 技术参数表

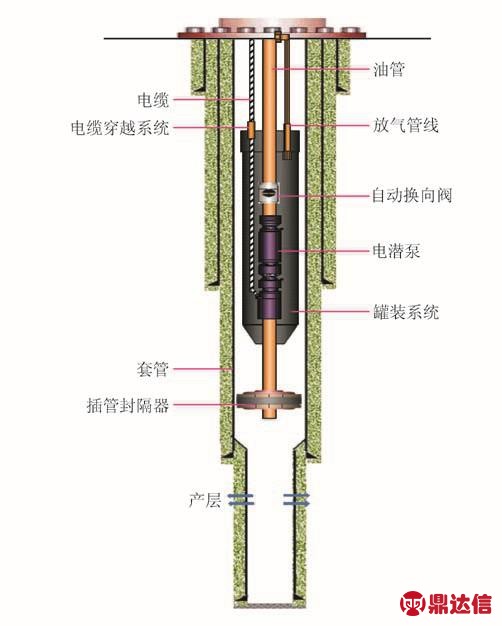
图8 L2井罐装电潜泵系统完井管柱示意图
表2 电潜泵机组和罐装系统选型参数表
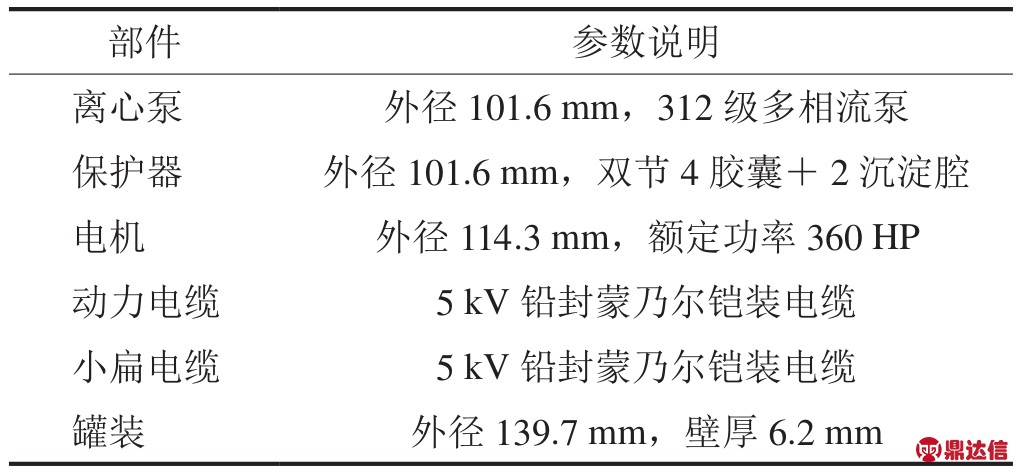
表3 电潜泵罐装系统材质选择表
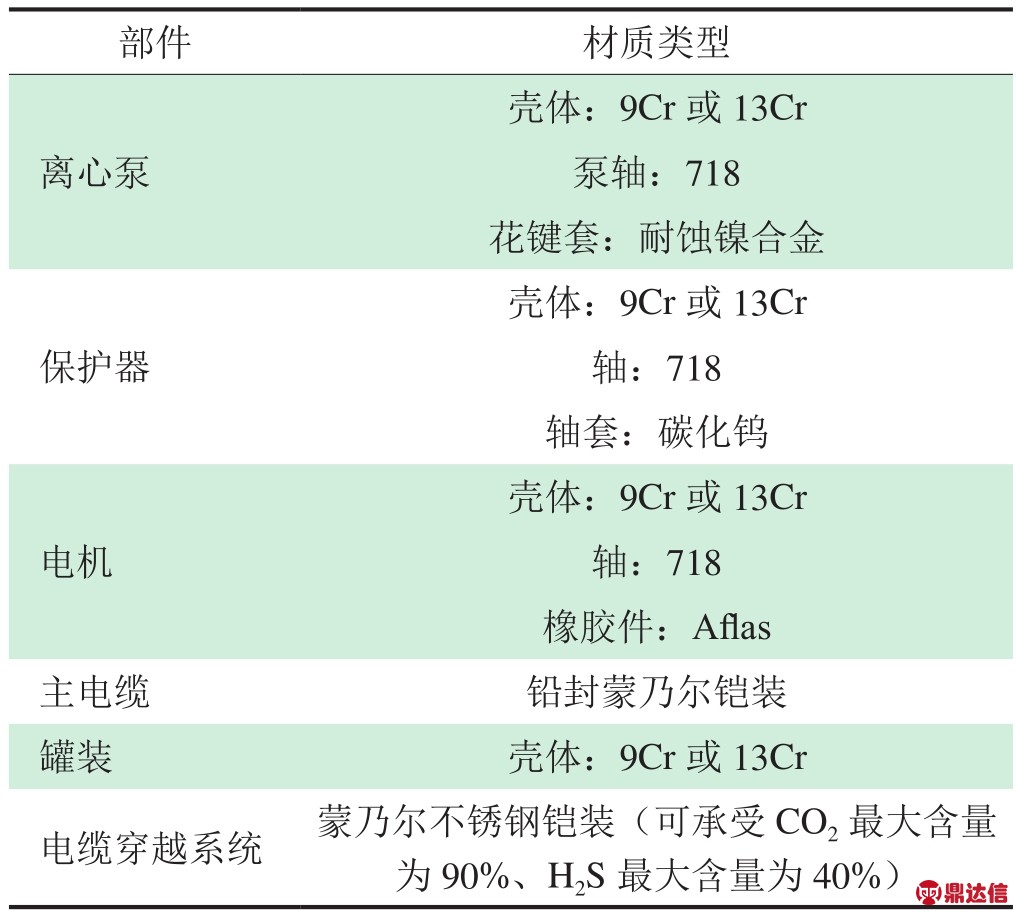
5 结论
1)罐装电潜泵系统结合锚定式插管封隔器形成的高含硫气井完井管柱系统能够实现电潜泵的正常运行,同时满足保护套管的需要。
2)罐装电潜泵系统采用多相流泵和放气管线以应对气体干扰的影响,在电潜泵罐装系统的电潜泵出口加装自动换向阀以实现电潜泵工作\关闭状态下流道的切换,增强气井带液自喷的效果,同时选用带有锚定机构的插管封隔器,降低管柱震动,保证电潜泵稳定运行,实现气井正常生产。
3)新设计的高含硫气井电潜泵完井系统可应用于Ø244.5 mm和Ø177.8 mm套管中:在Ø244.5 mm套管中,电潜泵的最大排量为900 m3/d,最高扬程为4500 m;在Ø177.8 mm套管中,电潜泵的最大排量为300 m3/d,最高扬程为3 000 m。