摘要:针对风力发电机组齿轮箱弹性支撑疲劳寿命预测问题,将数值仿真技术应用到了橡胶疲劳分析中。使用橡胶模型参数建立了轴瓦弹性支撑有限元模型,进行了静刚度试验,通过对比发现了仿真结果与试验结果比较符合;选定疲劳损伤模型,进行了橡胶材料的疲劳寿命测试,拟合了模型参数;在风电机组设计载荷下,开展了齿轮箱弹性支撑橡胶的疲劳损伤分析,提出了多轴变载工况下橡胶疲劳分析方法,将疲劳载荷时序加载转换成位移时序加载,计算了时序疲劳载荷损伤和等效疲劳损伤,得到了弹性支撑在不同部位疲劳损伤分布情况。研究结果表明:时序疲劳载荷相对等效疲劳载荷对橡胶的疲劳损伤更大,实际疲劳校核应按时序疲劳载荷进行。
关键词:弹性支撑;橡胶;有限元;疲劳寿命;多轴载荷
0 引 言
风力发电机组运行时,其齿轮箱由于承受来自叶片复杂交变的载荷,将会产生振动和噪声。通过在齿轮箱和机架连接处设置弹性支撑,可以有效解决振动及噪声问题。
对于三点支撑式传动系统,齿轮箱多采用轴瓦式结构弹性支撑,左、右两侧各两组,每组由上、下两片组成,其由橡胶层和钢板硫化而成,在机组运行时主要承受来自齿轮箱扭力臂横向及垂向的载荷,一旦出现损坏将使齿轮箱得不到有效支撑,引起传动链低速轴及高速轴不对中,加剧各连接处轴承磨损,从而对整个传动系统造成破坏,并且在机舱更换弹性支撑耗时长且安全风险大。因此,有必要合理评估机组20年设计寿命期内的弹性支撑受载情况及疲劳损伤。
风电机组载荷一般按照GL准则或IEC61400-1规范等规定的工况进行计算。载荷可分为极限载荷和疲劳载荷,许多风力发电机组部件的设计都取决于疲劳载荷而不是极限载荷[1-2]。机组金属结构件在设计载荷下的强度计算方法已经比较成熟,如轮毂、主轴、机架等强度校核及结构优化方面的研究成果也比较多,而对于一些受载的橡胶件校核则缺少相关的强度校核标准。目前研究主要有针对极限载荷下的强度校核[3],以及单轴简单工况下疲劳计算[4],对于多轴变幅载荷下时序疲劳校核缺少相关的研究。一方面是橡胶材料变形比较复杂,另一方面是橡胶材料试验数据较少。
橡胶构件在波动载荷下会因为裂纹的萌生和扩展而导致失效,目前针对橡胶疲劳寿命预测有裂纹萌生法和裂纹扩展法,裂纹萌生法基于连续介质力学理论尤其适用于分析疲劳寿命空间分布,裂纹萌生法常用损伤参数是最大主应变(或伸长)、应变能密度,应力很少使用,主要是由于橡胶材料疲劳测试中经常是位移控制,应力的数据不是很准确。对于单轴加载产生的裂纹,应变能密度可用于预测裂纹扩展寿命,对于多轴加载情况,裂纹萌生法更适合用于评估疲劳寿命[5]。文献[6]研究了橡胶材料基于某种损伤参量单一工况下的疲劳寿命,但如何可靠、经济地选择疲劳参数并应用于工程实际,仍是待解决的问题。
本文将对齿轮箱弹性支撑橡胶部件在机组20年设计寿命内疲劳损伤进行分析,预测风电机组橡胶件的疲劳寿命。
1 橡胶本构模型
橡胶是一种超弹性材料,其应力应变关系是弹性的,但高度的非线性,通常用应变能函数表示其应力应变关系,并通过拟合橡胶试样简单变形试验的应力应变数据确定应变能函数表达式相关参数。多项式形式的应变能函数是常用的形式,比较简单的形式包括Mooney模型、neo-Hookean模型、简缩多项式模型和Yeoh模型。
本文采用Mooney模型,其应变能函数表达式如下:

(1)
式中:C10,C01,D1—材料参数;I1,I2—第一、二应变张量不变量;J—弹性体积比。
本文进行橡胶试样单向拉伸、单向压缩和平面拉伸3类试验,将试验应力应变数据导入ABAQUS中,ABAQUS应用最小二乘法拟合得到式(1)各材料参数C10、C01、D1。
2 弹性支撑有限元建模分析
2.1 有限元模型
本文在有限元软件ABAQUS中,建立轴瓦弹性支撑的有限元模型如图1所示。
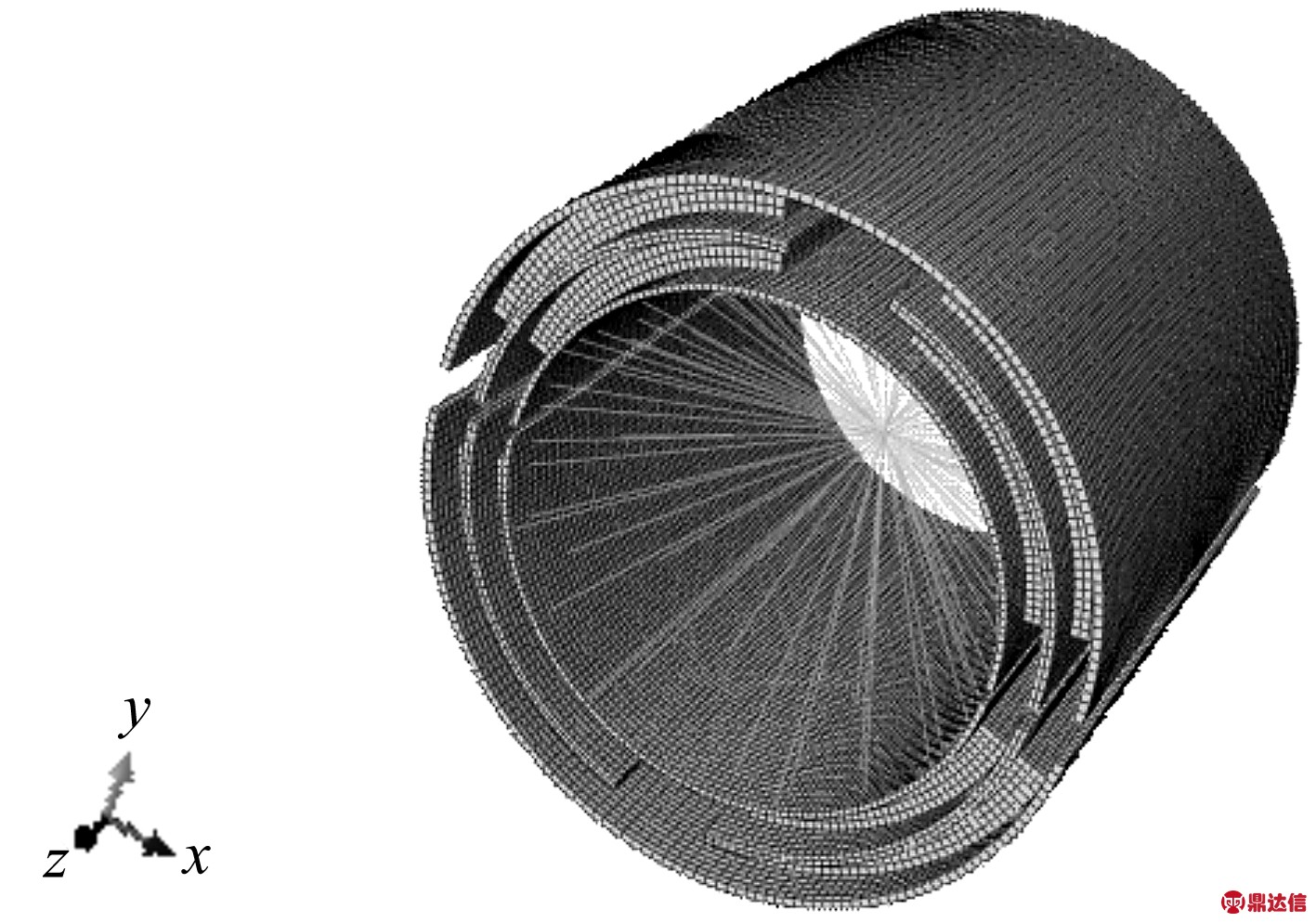
图1 有限元模型
本研究采用C3D8H单元(一阶六面体杂交单元),单元个数65 190。不考虑钢板与橡胶之间的粘结强度,橡胶与钢板结合面设置为绑定,下衬套外表面约束6个方向自由度,来模拟橡胶衬套固定在齿轮箱支撑座上的效果。在弹性支撑中心处建立一个参考点,将橡胶衬套内层钢板外表面与该参考点耦合在一起,第一步在上侧衬套外层钢板表面施加11 mm的z向位移,模拟弹性支撑装配后的预压缩状态;第二步在参考点上分别施加y向及z向载荷,模拟机组运行时受载情况,得到y向和z向的载荷位移曲线。
2.2 有限元分析结果
本研究在y向及z向分别加载500 kN载荷,计算轴瓦弹性支撑应变和参考点的位移,z向加载橡胶应变如图2所示。
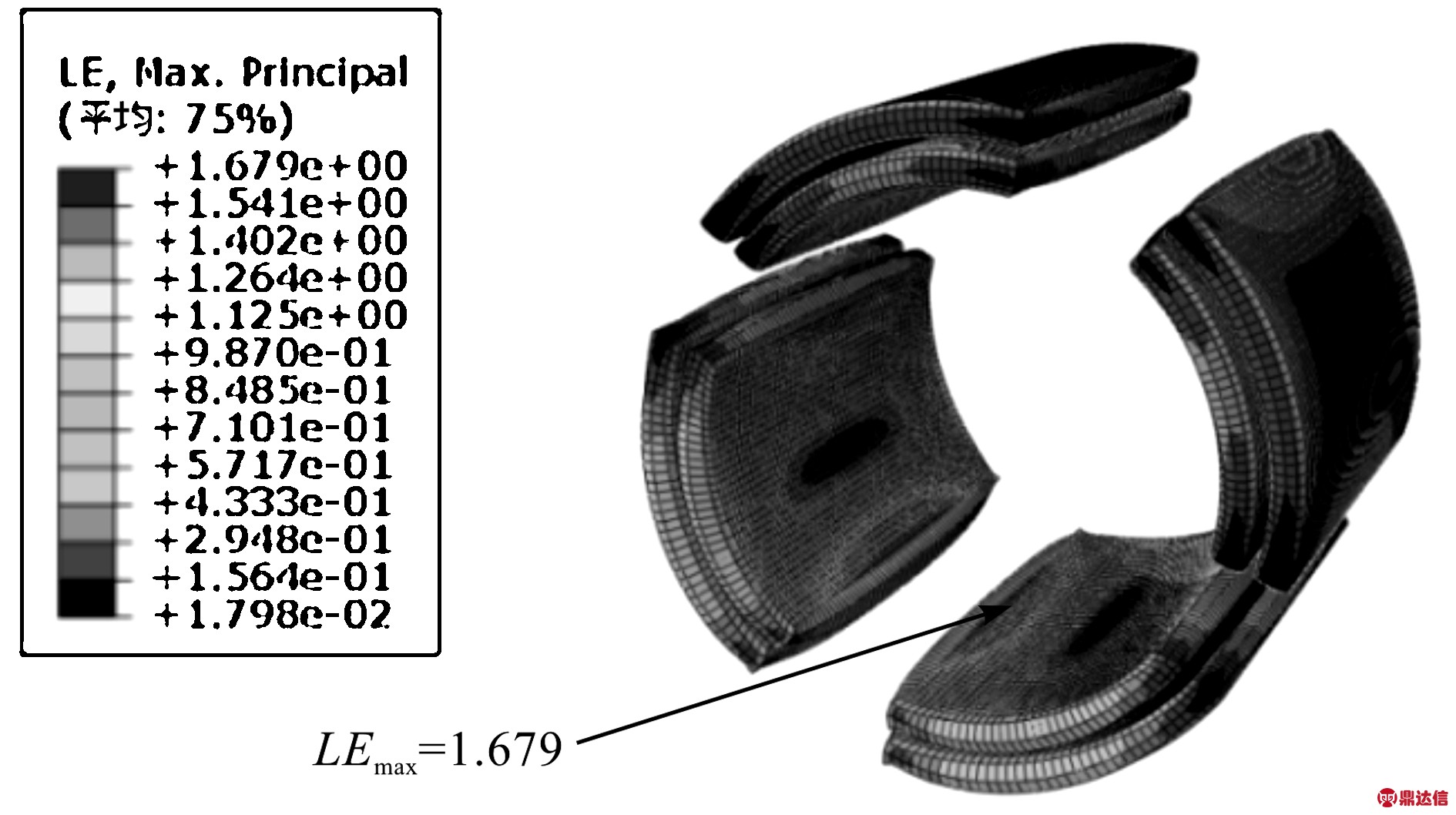
图2 z向加载橡胶应变
从图2中可以看出:最大应变出现在下半轴瓦空腔内里层橡胶与内层钢板相接触区域。
y向加载橡胶应变如图3所示。
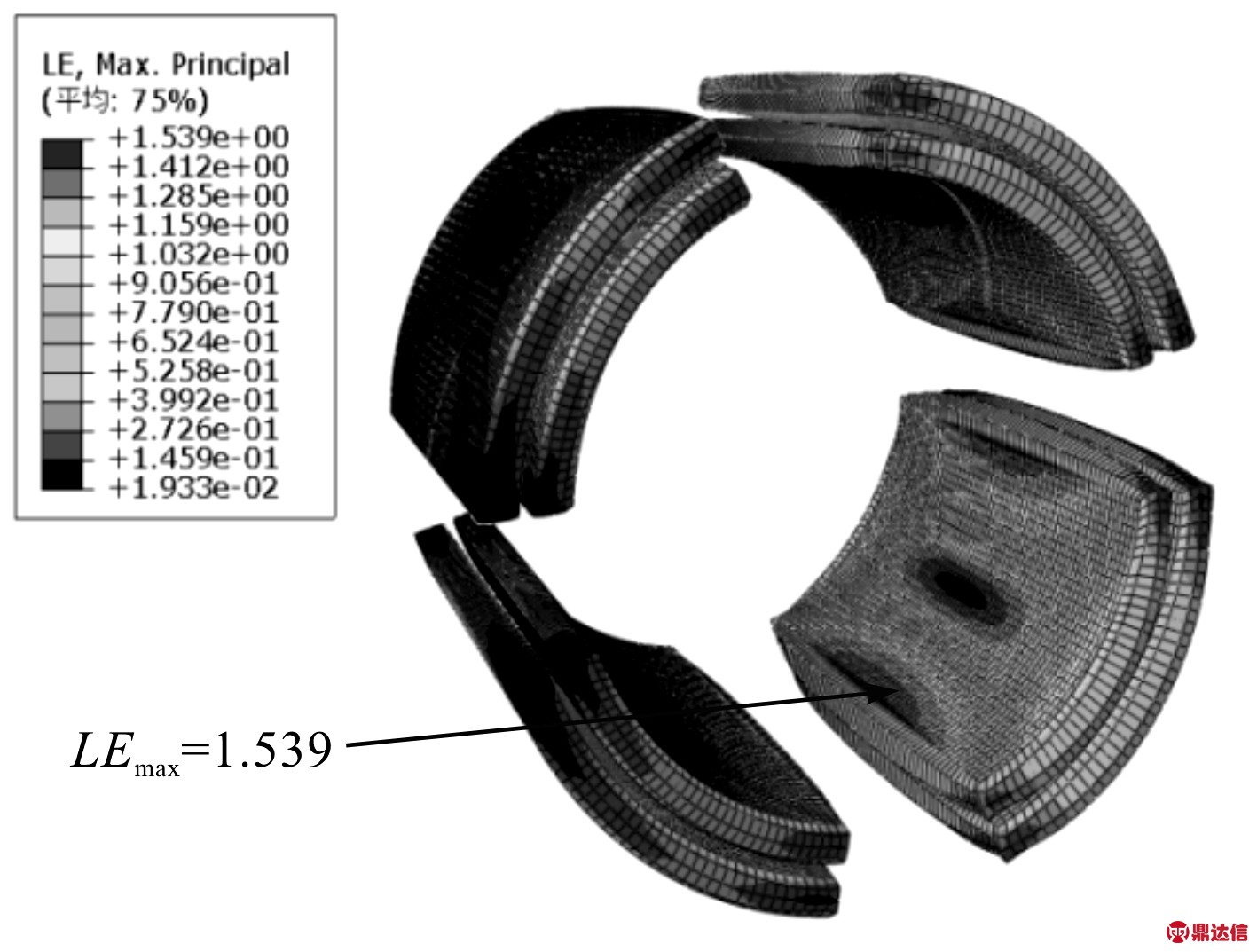
图3 y向加载橡胶应变
从图3中可以看出:最大应变出现在空腔内一侧橡胶与钢板接触区域边缘。同时得到轴瓦弹性支撑y向和z向的位移,并计算模型在y向和z向的刚度。
本研究用工装将弹性支撑固定至万能试验机试验台上,分别施加500 kN的y向及z向载荷,获得500 kN时的刚度,并与仿真结果对比。
计算刚度与试验刚度对照如表1所示。
表1 计算刚度与试验刚度对照

表1结果显示:两者偏差小于5%,可知模型能较准确地模拟轴瓦弹性支撑的变形情况。
3 机组载荷分析
GL规范轮毂中心坐标系如图4所示。
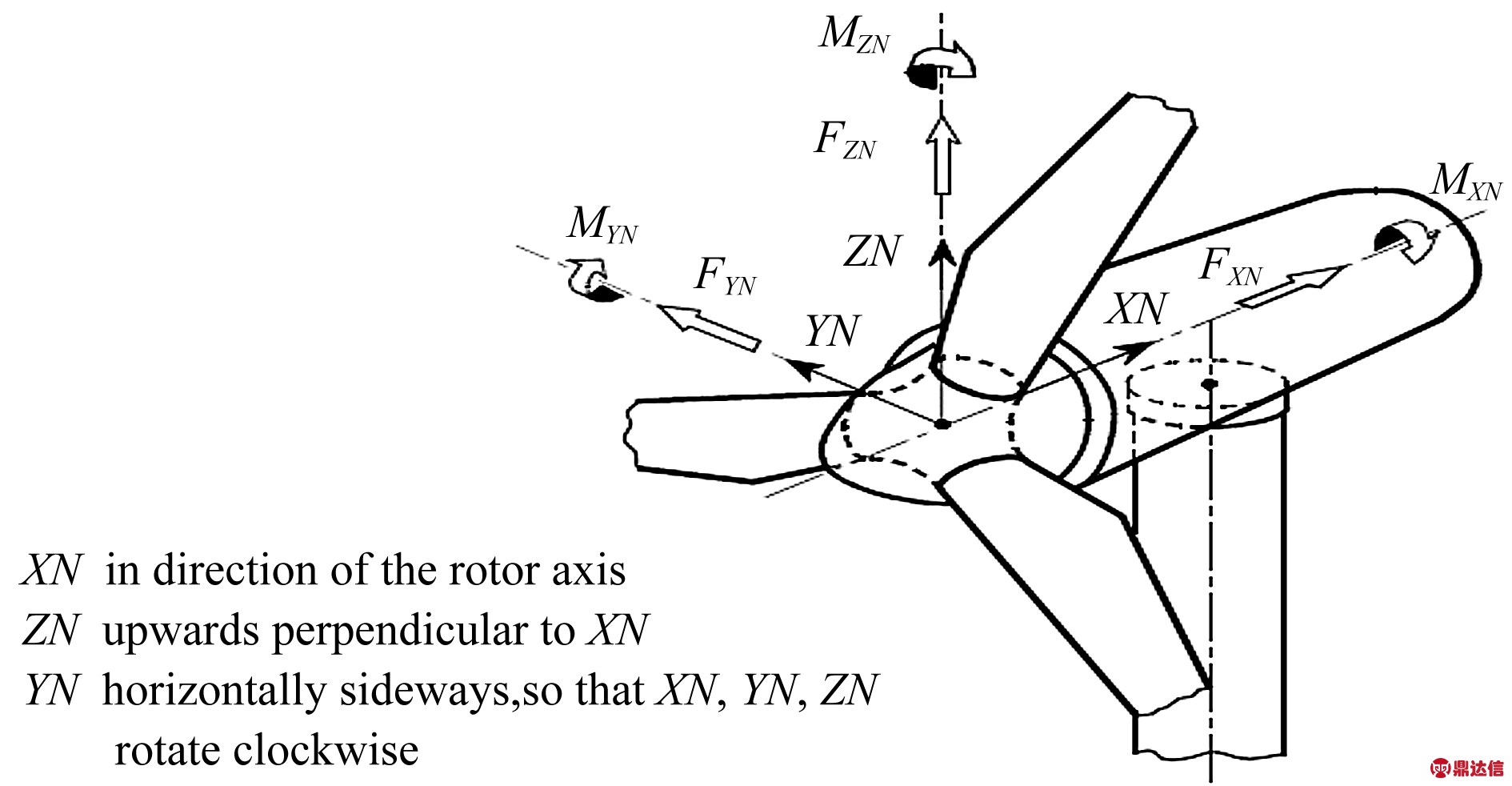
图4 GL规范轮毂中心坐标系
对于传动链三点式支撑方式,传动链简化力学模型如图5所示。
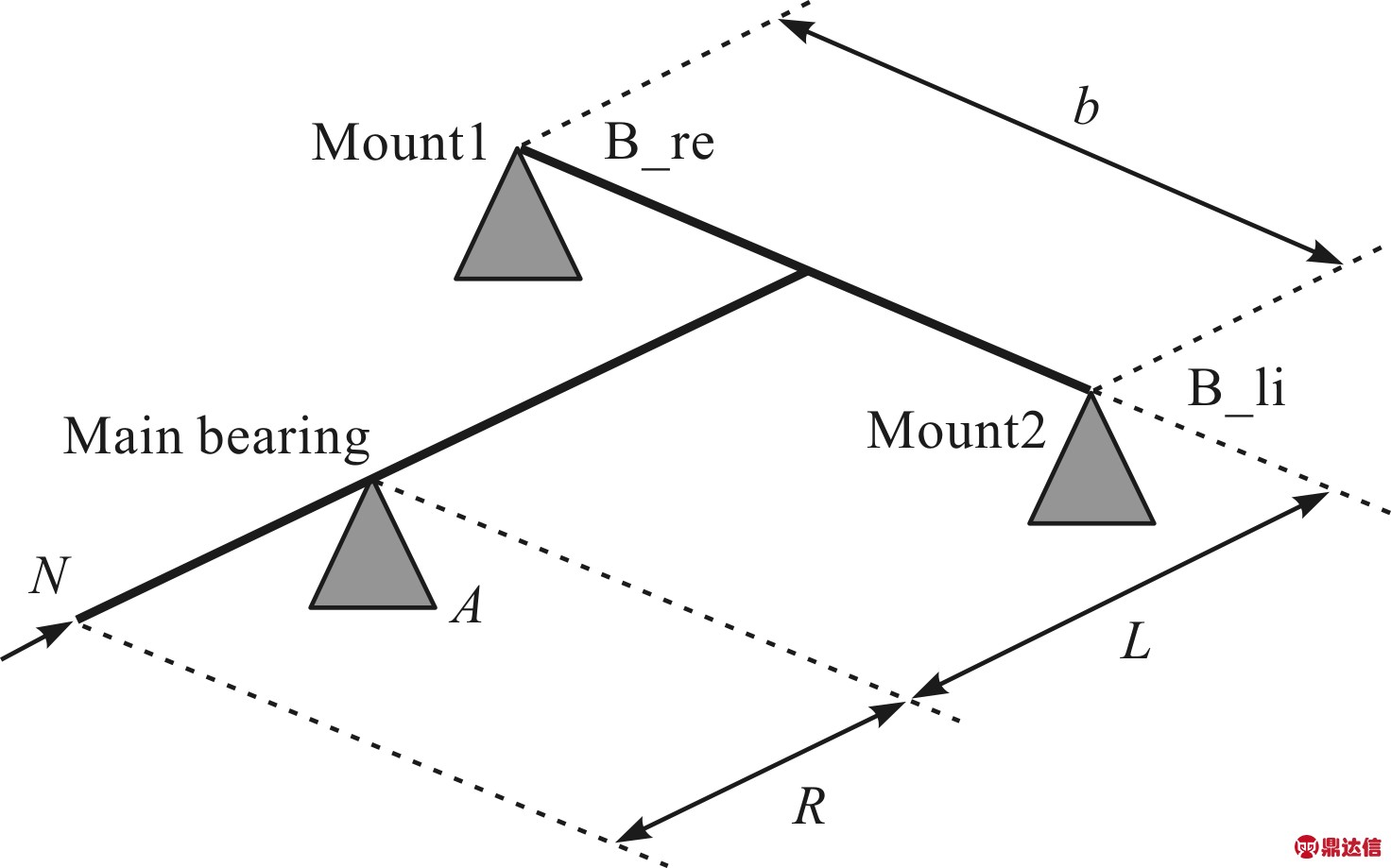
图5 传动链简化力学模型
通过简化模型可以将风轮载荷转换到齿箱单侧扭力臂弹性支撑受到的作用力Fy、Fz,这些力的大小随时间变化,且不具有周期性。橡胶部分在Fy和Fz的作用下产生持续变形。为了防止机组运行时齿轮箱扭力臂与上、下两半轴瓦弹性支撑发生脱离,弹性支撑内外层钢板设计成具有一定的偏心量,装配后产生足够预压缩量。机组运行时橡胶总的变形为预压缩量叠加外载产生的变形,根据已经得到的弹性支撑的刚度,可计算外载引起参考点的位置的变化。本文后续位移计算考虑刚度不变,即变形大小与外载成线性关系。笔者用风力机载荷计算软件Bladed模拟所有疲劳工况,获得各个工况下载荷谱,并结合弹性支撑刚度,转换成弹性支撑参考点的位移,在此基础上叠加预压缩位移,分析在此综合位移下橡胶的疲劳寿命。
作用于风轮的载荷通过主轴,齿轮箱传递到齿轮箱弹性支撑,弹性支撑承受的载荷可以通过传动链的尺寸计算得到:
两侧弹性支撑z向载荷分别为:

(2)

(3)
单组弹性支撑y向载荷为:
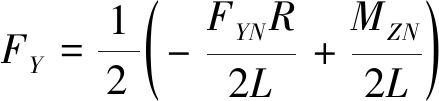
(4)
式中:R—风轮中心至主轴承中心的距离;L—主轴承中心至齿轮箱扭力臂的距离;b—齿轮箱扭力臂跨距。
将上述关系式(2~4)添加到Bladed软件中,对轮毂中心载荷进行后处理,获得齿轮箱两侧弹性支撑的载荷,该载荷可直接用于齿轮箱弹性支撑极限和疲劳强度校核。
4 疲劳寿命计算
4.1 橡胶疲劳寿命模型
如前所述,疲劳损伤参数有最大主应变、应变能密度等,文献[7-8]研究表明,最大主应变可以很好地预测橡胶疲劳寿命,文献[9]结果表明最大主应变对于多轴加载具有较好的精度。
橡胶材料疲劳损伤参量与寿命的关系类似于金属材料,但是由于橡胶材料弹性应变范围很大,塑性变形部分需要除去,其疲劳模型为:
εa=K(2Nf)b
(5)
式中:εa—等效应变幅值;Nf—载荷循环次数;b—疲劳强度指数;K—常数,由疲劳试验拟合得到。
式(5)为单轴疲劳模型,对于多轴疲劳,等效应变法使用多轴工况的等效应变代替式(5)中的单轴应变。本文分别研究使用如下3种应变组合作为等效应变:
(1)绝对值最大的主应变:
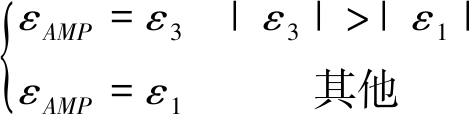
(6)
(2)带符号Von Mises应变:

(7)
式中:νe—材料泊松比;ε1,ε2,ε3—3个主应变。
(3)带符号切应变:
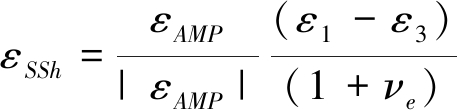
(8)
4.2 橡胶疲劳寿命试验
本文按照GB/T1688-2008标准制作哑铃状试样,并进行伸张疲劳试验[10],获得每种应变及断裂时的循环次数,拟合试验结果得橡胶应变与疲劳循环次数的关系,采用下式进行参数拟合:
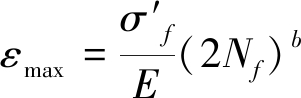
(9)
式中:疲劳强度系数;E—弹性模量;b—疲劳强度指数;εmax—疲劳试验真实应变峰值;Nf—各应变对应循环次数。
为便于疲劳分析软件计算,笔者将试验得到的脉动循环疲劳曲线转化为对称循环疲劳[11],转换公式为:

(10)
式中:R—循环特征;循环特征为0和R时的循环应变幅。
4.3 疲劳损伤累积
对于金属材料,常用的疲劳损伤准则有:线性累积损伤理论、双线性累积损伤理论、非线性累积损伤理论及连续损伤力学累积理论。HARBOUR等[12]研究认为,线性损伤累积准则应用于天然橡胶与试验结果对比误差较小。本研究也采用线性损伤累积准则,利用疲劳分析软件nCode 13.0进行疲劳寿命分析,导入有限元分析获得单位载荷下的真实应变及各工况载荷时间序列,设置橡胶材料性能参数。
5 结果分析与讨论
5.1 时序疲劳强度分析
本文根据位移时序及有限元结果,得到应变张量时间历程数据,然后从应变张量中提取一个合成的应变参数,如绝对值最大主应变,并对主应变时间历程雨流计数,获得每个循环的应变幅值、平均应力及最大应力,最后根据E-N曲线累计损伤。
首先笔者分别计算模型在y向及z向单位位移时的应变,编制MATHEMATICA程序将Bladed软件计算的风轮载荷FYN,FZN的时序文件按照y向及z向刚度转化成位移时序,并叠加预压缩位移,得到总的位移时序文件,并使其符合nCode的输入文件格式要求,在nCode软件中导入有限元计算结果文件、各工况位移时序文件及20年各工况循环次数。
疲劳损伤分布如图6所示。
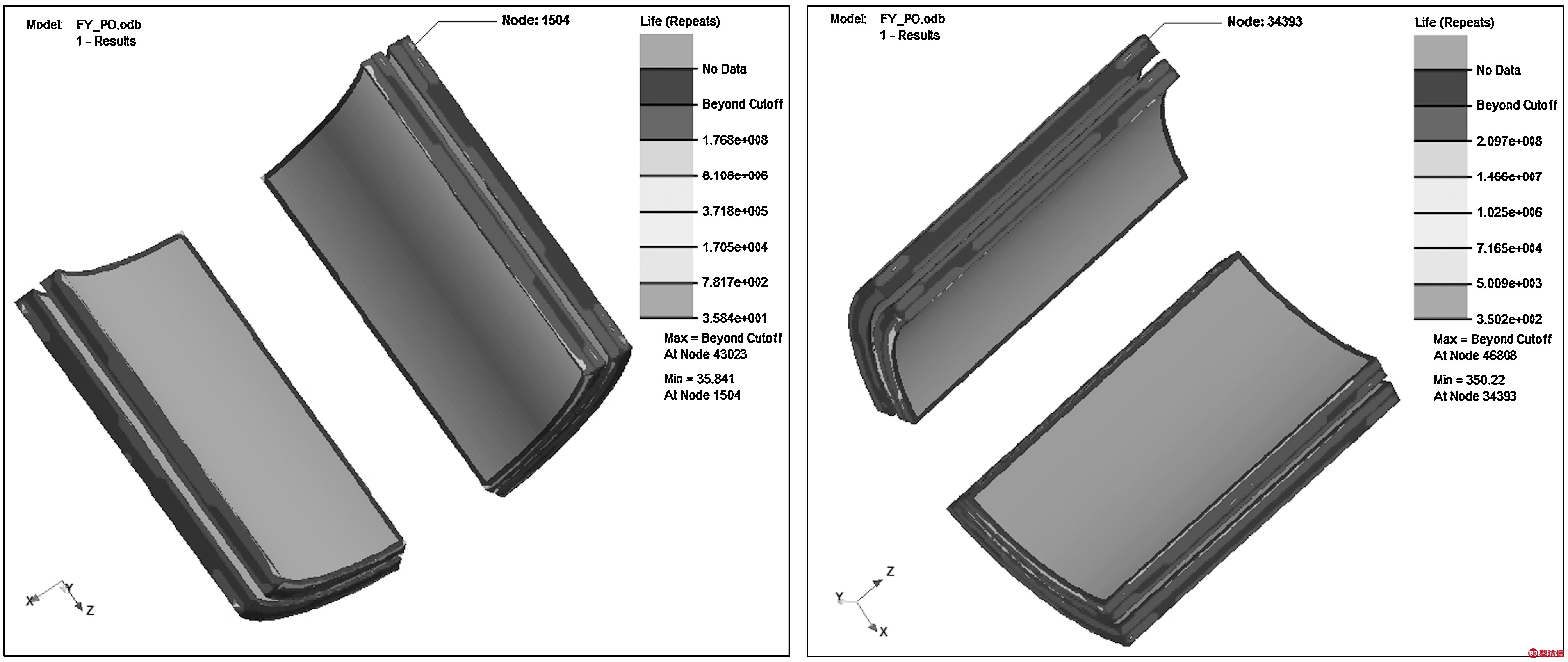

图6 疲劳损伤分布图
从图6中可知:容易出现疲劳损坏的部位发生在橡胶边缘靠近钢板处。其他方法计算的疲劳损伤分布和该图相似。
不同部位橡胶疲劳寿命值如表2所示。
表2 不同部位橡胶疲劳寿命值
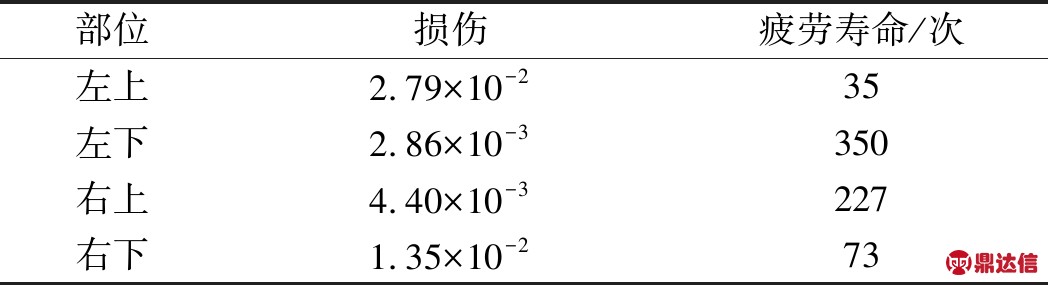
从表2中可以看出:4片支撑轴瓦以左侧上半部分及右侧下半部分(从风轮侧往发电机方向看)橡胶疲劳损伤较大,与风轮顺时针转动时扭力臂受载方向一致,其中,左侧上部分损伤为右下部分的2倍多,说明此处在机组定期维护时更应该受到关注,检查是否有裂纹,有裂纹需及时更换。
5.2 等效疲劳强度分析
目前,齿箱弹性支撑疲劳试验载荷主要采用的是等效疲劳载荷[13],等效疲劳载荷Fe定义为:
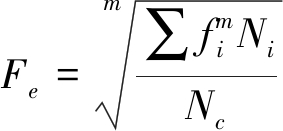
(11)
式中:fi—疲劳载荷谱第i个载荷幅值区间的载荷;Ni—疲劳载荷谱第i个载荷幅值区间的循环次数;m—相关材料S-N曲线的斜率。
由于风电机组零部件设计寿命为20年,即对应载荷总循环次数NC为1×107。
根据式(11),可得到不同m值下的等效疲劳载荷,如表3所示。
表3 不同m值下的等效疲劳载荷
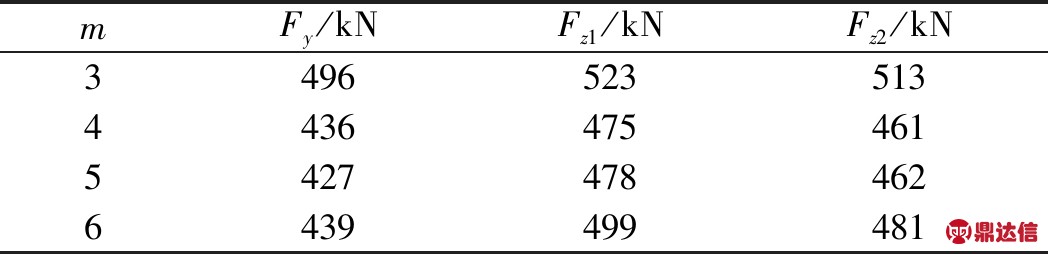
橡胶分析一般取m=5对应的载荷,在nCode13.0中导入标准载荷值对应的有限元计算结果文件,疲劳载荷类型设置为常幅,将表3中m=5对应的Fy及Fz1和Fz2较大的值设置为载荷幅值,计算疲劳寿命。
等效疲劳载荷疲劳损伤分布如图7所示。
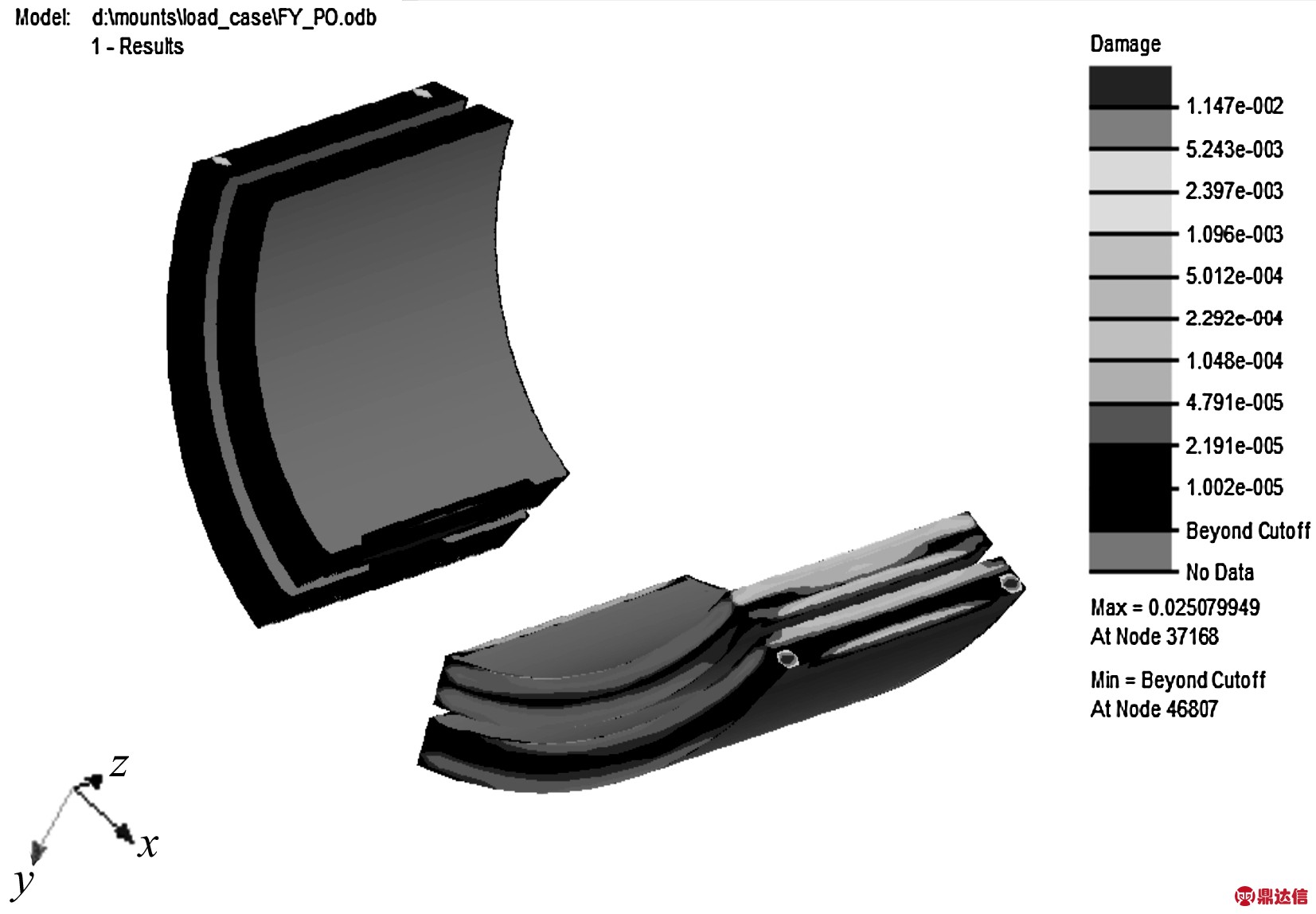
图7 等效疲劳载荷疲劳损伤分布
5.3 实验及结果分析
本文采用大型疲劳试验机进行齿轮箱弹性支撑的疲劳试验,载荷按照上述等效疲劳载荷选取,加载频率为2 Hz,加载1×107次后检查橡胶表面,未出现明显裂纹,表明按该等效疲劳载荷校核有较大安全余量。从以上仿真分析来看,时序疲劳相比等效疲劳载荷造成的损伤更大,考虑到完全按时序载荷进行加载比较困难,实际操作中可以将等效疲劳载荷乘以一个安全系数,作为试验载荷进行疲劳加载。
6 结束语
本文研究了风电机组齿轮箱弹性支撑橡胶疲劳强度分析方法,并针对某2 MW双馈机组齿轮箱弹性支撑,建立了弹性支撑橡胶模型和三维有限元模型,计算了弹性支撑的各向刚度,并结合机组载荷计算所得到的机组载荷,计算了弹性支撑橡胶部件的疲劳损伤,结论如下:
(1)分析了橡胶部件损伤分布情况,并对比了等效疲劳和时序疲劳损伤,结果显示最大疲劳损伤位置比较接近,等效疲劳载荷对应的疲劳损伤值偏保守,实际常幅疲劳试验载荷应适当加大,不应直接以该等效载荷进行试验;
(2)找到了易出现疲劳破坏的位置,最大疲劳损伤点与单向受载应变最大位置接近。根据4片轴瓦上橡胶疲劳寿命分布情况,可通过增加风轮旋转方向对角2片轴瓦刚度,以减小应变幅值,从而可提高弹性支撑的疲劳寿命。