摘要:本文针对某机型薄壁钛合金法兰盘高精度内花键跳动合格率极低的现象,根据零件结构、钛合金特性和插齿原理,从插齿刀、插齿夹具、切削参数等方面研究和探索加工高精度内花键的方法和控制手段,为类似零件的内花键插齿提供了理论依据和加工方法。
关键词:薄壁;钛合金;插齿夹具;切削参数
某机型钛合金法兰盘属于薄壁易变形零件,内花键精度高,给插齿加工带来了一系列问题:
(1)钛合金切变系数小于或接近于1,切削时,刀具易磨损;钛合金切削时温度高,比45钢高出一倍,散热性差,刀具易烧损;单位面积上的切削力大,容易崩刃;切削时,钛屑及被切表层易与刀具材料咬合,产生严重的粘刀现象,引起剧烈的黏结磨损,以上情况严重影响插齿加工精度。
(2)内花键加工后需对花键进行喷丸,进一步影响花键跳动。
1 研究内容
(1)解决零件材料切削困难,刀具易磨损以及粘刀问题。
(2)解决零件因壁薄,加工过程中产生变形的问题。
(3)保证插齿工序加工的零件,内花键跳动在0.025以内,喷丸后,花键跳动在0.03以内。
2 技术方案
(1)选用切削性能及散热性能良好的合金钢作为插齿刀具材料,并增加涂层要求保证切削及耐磨性,严格要求其齿形、齿向、累积、跳动误差。
(2)分析零件受力,根据零件受力情况,改善夹具,增加加工刚性。
(3)摸索插齿参数,调整零件进给速度、径向进给。
3 实施过程
3.1 刀具优化
钛合金材料韧性大,导致切削时切削力大,且加工时散热情况不好,大部分热量留在刀具上,对刀具磨损大。所以,本方案必备条件是一把适合钛合金零件插齿的刀具,刀具设计为带涂层的硬质合金刀具,齿形误差不大于0.004,跳动误差不大于0.008,周节累积误差不大于0.015。
3.2 夹具优化
根据技术方案的分析,夹具的设计需存在相反方向的力F1'、F2'来限制零件的加工变形(图1)。
在A处增加内端面的辅助支撑,在B处增加定位支撑(见图2),通过夹具间接加厚零件,增大零件刚性,通过施加一个反向的力F2’,减小F2对薄壁零件产生的变形影响,从而达到提高内花键精度的目的。通过工艺试验,发现夹具压板与零件外圆配合间隙需保持在0.015~0.025较为合适,且夹具材料需采用硬铝,一方面减轻压板重量,另一方面可以保护零件外观,防止压伤零件表面。
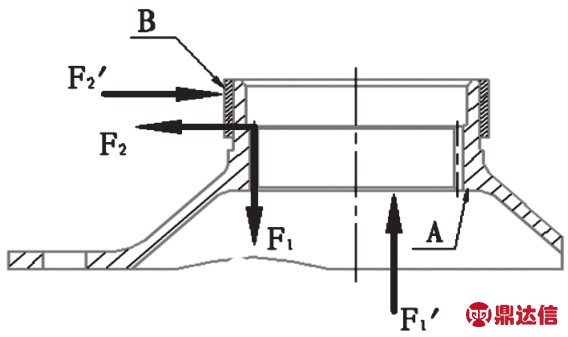
图1 夹具改进原理分析
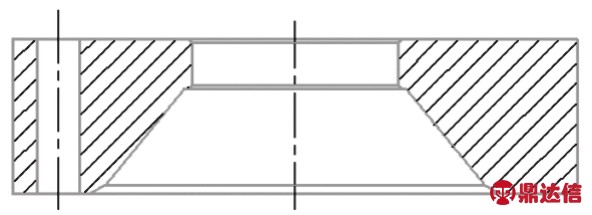
图2 夹具压板
3.3 切削参数优化
(1)插齿余量分配优化。普通零件加工,切削余量大约在2mm左右,插齿加工分为三个阶段,余量分配见表1所示:
该法兰盘插齿余量为1.4m,由于该零件结构、材料的特殊性,余量分配不能按照普通钢制件零件进行,第三刀精刀无论余量剩多少,齿圈跳动都难以保证要求。因此,零件加工时需增加第四刀,在第四刀加工时,通过第四刀的切削加工修复齿圈跳动,通过工艺试验可以确定第4刀余量为0.02mm时,改善效果最明显。
(2)切削速度优化。常规插齿速度设置是越来越快,切削速度从50m/min增加到110m/min,通过加快切削速度,来改善切削效果,减小刀具与零件的挤压时间来提升齿圈跳动。但该方法存在缺陷,加快速度导致机床稳定性变差,刀具与零件在精加工时产生的磨削热增加,零件所受冲力增大,变形情况超出加工控制要求。因此,在各个阶段采用匀速加工比较适宜,切削速度通畅可选用70m/min。
(3)圆周进给量优化。粗加工时,为保证切削效率,进给量较大,精加工时为保证齿圈跳动,进给量不宜过快。因此,加工时采用以下两种方案进行对比试验,一个为圆周进给量不变,一个为圆周进给量逐渐减小。
表1 普通插齿余量分配
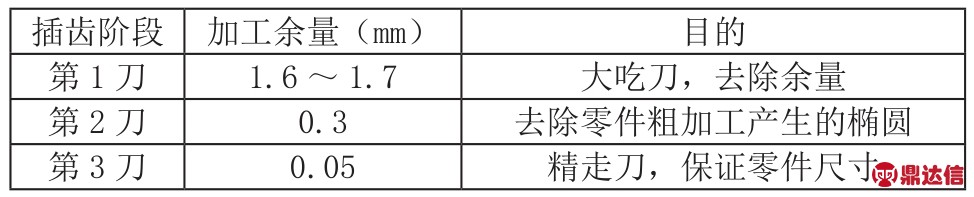
根据对比试验结果可以看出,方案1加工情况优于方案2,验证了零件精加工时,进给量不能过大,均匀地降低进给量有助于修复零件的椭圆,保证齿圈跳动的原理。
表2 圆周进给量试验方案
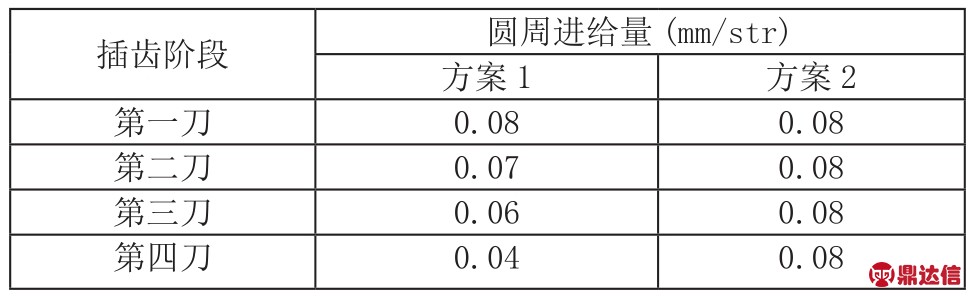
4 结语
运用前述技术方案和方法,通过连续批次加工,内花键尺寸、技术要求都达到了设计要求,达到了预期目的。本文通过探索、研究,确立了薄壁钛合金内花键插齿的工艺方法、控制手段,具有极佳的应用推广价值。该项研究属于国内首创,填补了高精度钛合金内花键插齿技术的空白,处于国内领先水平。