摘 要:针对铝合金法兰盘镶铸件中出现的较大缩孔、疏松现象,用ProCAST软件对其进行了数值分析,重新设计了镶铸工艺中的浇铸系统,并再次用ProCAST进行模拟,此时缩孔及疏松明显变少。采用正交试验法,优化了镶铸工艺参数,得出在浇铸温度为660 ℃、浇口速度为35 m/s及模具预热温度为180 ℃时,法兰盘内部的缩孔、疏松现象最少,工件质量最佳。实际生产表明,在新的浇注系统和工艺参数条件下,产品质量明显提高,且与模拟结果较为吻合。
关 键 词:镶铸;电机法兰盘;ProCAST软件;数值模拟;正交试验法
镶铸工艺是先将已加工好的金属材料的零件放在铸型里,再进行浇铸,使铸造合金在凝固时与该金属零件形成整体,以提高或改善铸件的局部性能[1]。镶铸法在有色金属铸件中使用较为广泛,其主要的优点是:避免或减少铸造过程中出现的气孔、疏松等缺陷;克服难铸造的特征或简化铸造工艺;提高零件的局部耐磨性[2]。但在运用镶嵌法的实际生产中,仍会出现不少问题。
1 产品缺陷分析
本文所研究的电机法兰用于电梯的电机上,其中心部位要求有较好的耐磨性和刚性;生产中选用45号钢作为镶嵌件;同时为了防止嵌件松动,在圆筒型嵌件外表面加工出3个环状矩形槽。在实际生产中,该产品壳体底部的异种金属边界上经常出现间隙,部分间隙甚至超过0.5 mm,在压铸成型部位易出现大量的疏松和缩孔等缺陷,详见图1。
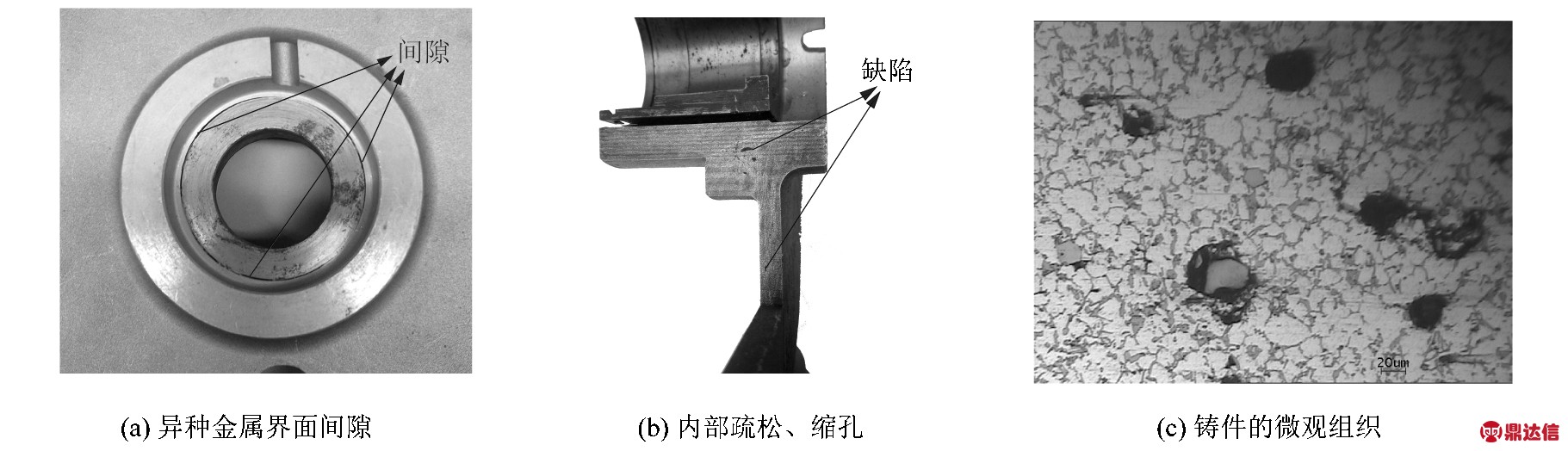
图1 实际生产中的缺陷
Figure 1 Defects in actual production
1.1 模型的建立
首先采用三维建模软件UG画出浇铸体和镶嵌件的三维造型,再利用HyperMESH软件对三维图形进行有限元面网格划分,最后再在ProCAST软件中进行体网格划分,法兰盘的铸件及镶嵌件模型如图2所示。
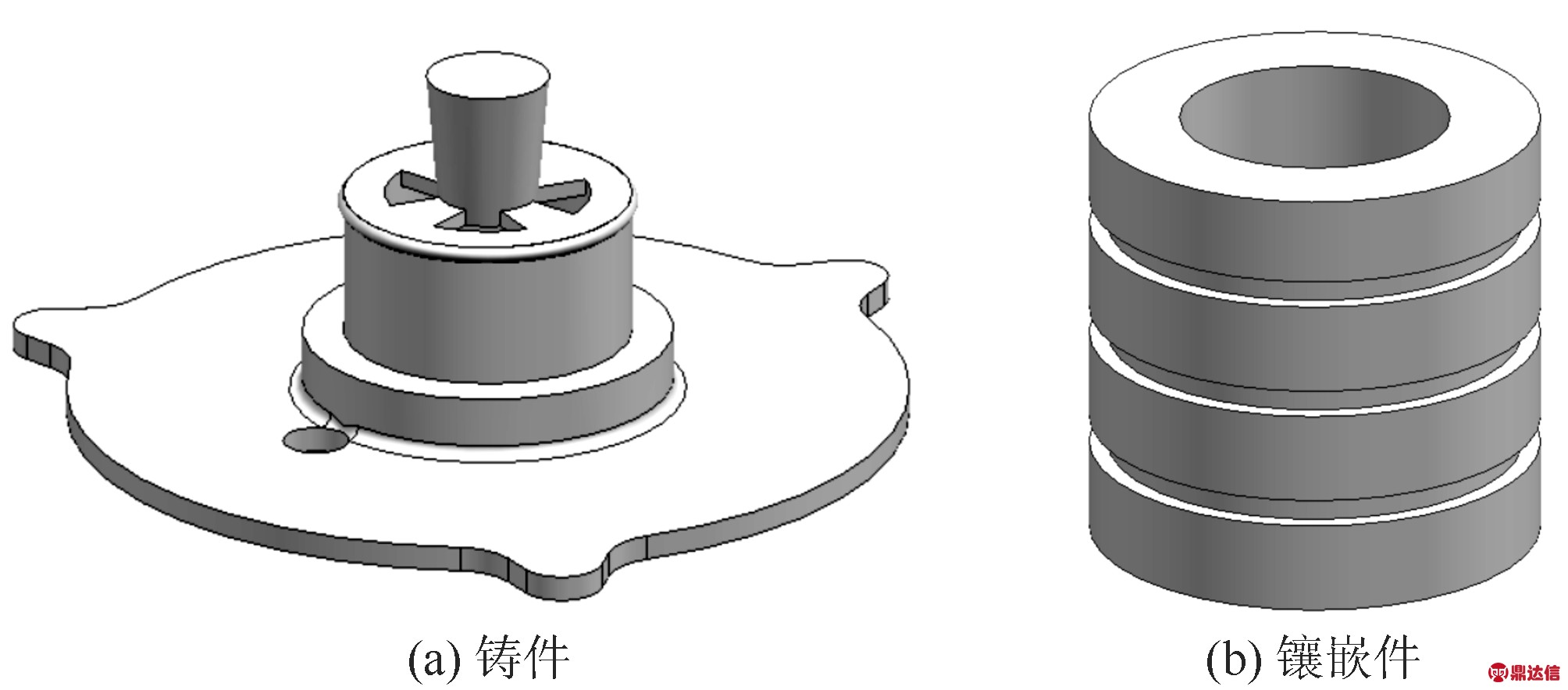
图2 法兰盘的铸件及镶嵌件模型
Figure 2 Model of casting and insert for flange
1.2 工艺参数
影响压铸件质量主要因素有浇铸系统、浇铸温度、填充速度、模具的预热温度等。浇铸系统的设计跟浇铸件的结构复杂程度、尺寸大小有关,本次模拟的浇铸系统设计在离法兰盘面较远的一端,且采用中心浇道。浇铸温度比浇铸合金的液相线温度高50~100 ℃,模拟浇铸温度设为700 ℃。填充速度跟浇铸的合金材料和浇铸件的壁厚、尺寸有关;对于铝合金来说,其充填速度一般为20~30 m/s,由于本铸件的壁较厚,最厚处已达22 mm,故设置浇口处的速度为30 m/s。模具的预热温度对压铸模的使用寿命、压铸件的顺利充型、冷却后的铸件质量等具有重要意义,对于铝合金的压铸,壁厚大于3 mm的简单结构,预热温度一般为150~180 ℃,此次模拟不仅需要对模具预热,还要对中间的镶嵌件进行预热,镶铸件的预热温度一般为200~250 ℃;故模具和镶铸件的预热温度分别选为150 ℃和200 ℃。压铸件材料为铝合金,美国牌号为A356,模具材料为H13,镶铸件材料选择CK45。模具与压铸件、压铸件与镶嵌件之间的界面传热系数分别为1 500 W/(m2·K)和1 800 W/(m2·K)[3]。表面冷却方式设置为空冷。模拟总步数设为3 000步,且终止温度为30 ℃。
1.3 模拟结果分析
初次模拟的结果如图3所示,铸件填充完成的时间为0.033 1 s,凝固时间为18.463 1 s,其缺陷所出现的位置基本与实际生产相吻合。大量的缩孔、疏松主要出现在壳体壁最厚的区域, 且离浇铸系统较远,少量的缺陷分布在法兰盘面上。出现这种现象的主要原因是:法兰盘上的台阶厚度较厚,成圆环形,且浇铸系统的位置离壳体的厚端较远,浇铸液体在最后冷却收缩凝固时,因镶嵌件和铸件的热收缩率不同,厚壁处内部易出现缩孔、疏松现象;且因铸件未完全包裹住镶嵌件或填充不足等原因造成了异种金属接触间的缝隙问题[4~5]。
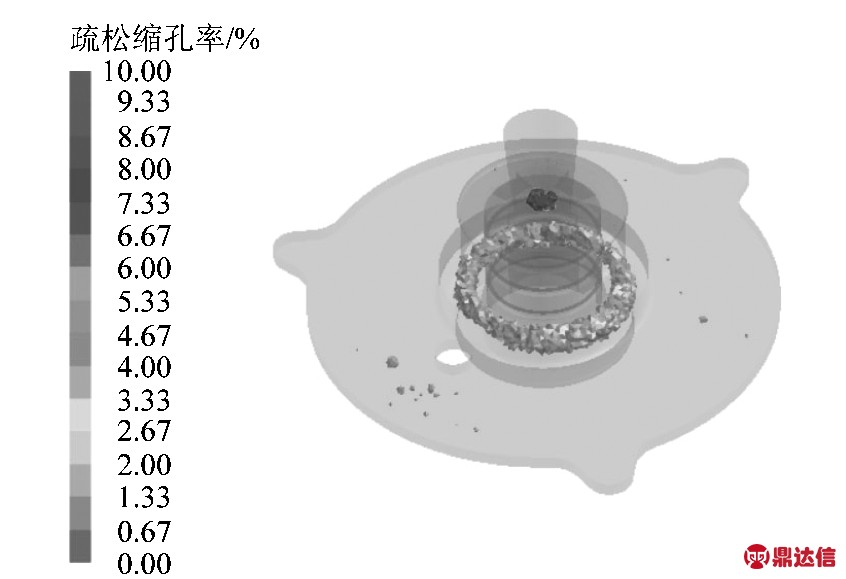
图3 初次模拟结果
Figure 3 Results of initial simulation
2 浇铸系统改进
根据初次模拟结果的分析,新的浇铸系统设置在离法兰盘面较近的一端,且选择中心浇道类型,并在上下2端面处添加2个薄圆环,使铸件完全包住镶嵌件。
2.1 直浇道设计
直浇道的结构和形式与所选用的压铸机类型有关,分为热压室、卧式冷压室和立式冷压室压铸机用3种直浇道[6]。本铸件采用的是卧式冷压室压铸机进行加工,主要由浇口套、浇道镶块、浇道推杆和余料组成。直浇道的尺寸由浇口套的尺寸所决定,直径为30 mm,为避免金属液在压射冲头未工作时流入型腔,一般直浇道要偏于浇口套的内孔上方。
2.2 横浇道设计
横浇道是将金属液从直浇道引入内浇口的一段通道。其结构形式和尺寸大小不仅与压铸件的形状、尺寸有关,还与内浇口的形式和位置等有关[7]。本浇注系统设计为扇形式(扩张式),其截面积尺寸可按下面的经验公式进行计算:
Ar=nAg。
式中:Ar为横浇道的截面积,mm2;n为系数,冷压室压铸机取3~4;Ag为内浇口的截面积,mm2。计算得到Ar为152 mm。横浇道的长度可按照下面的经验公式计算:
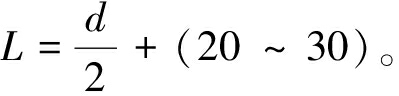
式中,L为横浇道长度,mm;d为直浇道直径,mm。计算得到L为35 mm。
2.3 内浇口的设计
内浇口的主要作用是将金属液体引入型腔,设计主要是确定其位置、导流方向、形状和尺寸。本浇注系统的内浇口选择在浇铸件的顶部。内浇口的横截面积的确定有理论估算和经验数据2种,本设计选择适用于所有压铸合金的经验公式:
Ag=0.026 8×V0.745。
式中:Ag为内浇口的面积,cm2;V为压铸件与溢流槽的体积之和,cm3。计算得出Ag约为38 mm2。
2.4 新浇铸系统下的模拟
使用新设计的浇注系统模型进行模拟,加工参数的设置与初次模拟相同。模型和模拟结果见图4。
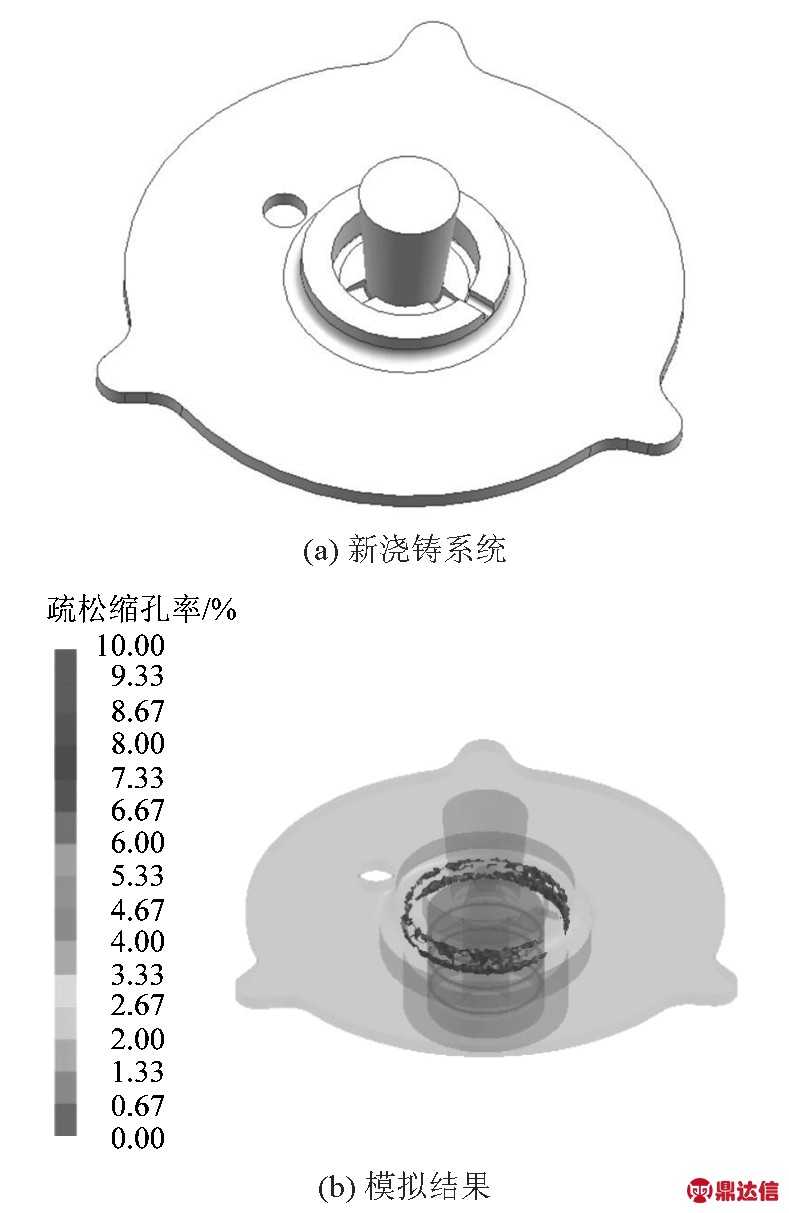
图4 模型及模拟结果
Figure 4 Model and simulation results
此次结果中的缩孔、疏松位置仍主要分布在厚壁凸台的内部区域,但相比初次模拟结果,其范围较小,且铸件与钢芯的端头相嵌处的缝隙现象基本消失。
3 工艺参数优化
为了进一步减少缩孔、疏松的范围,得到质量更好的铸件,在使用新设计的浇注系统模型下,利用正交试验法对加工工艺参数进行优化[8]。试验因素及水平见表1。
此3因素3水平正交试验的评判标准为缩孔、疏松的满意度,选用正交表L9(33),进行9组试验,正交试验方案见表2。
表1 正交试验因素水平表
Table 1 Factor form of Orthogonal test
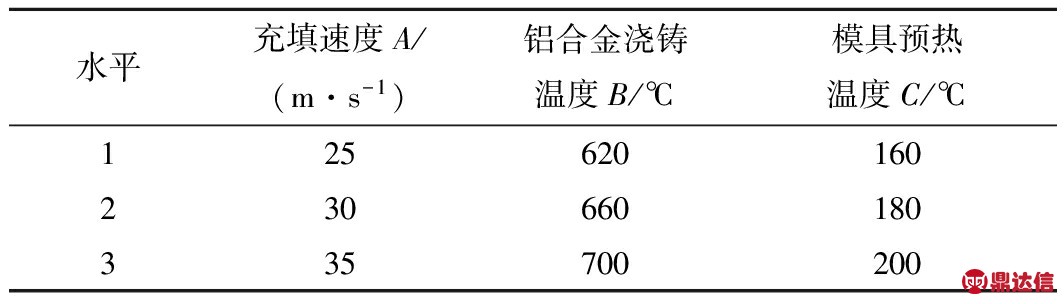
表2 正交试验方案
Table 2 Orthogonal test scheme

针对缩孔、疏松的满意程度是根据其分布的位置是否影响后续的机加工和分布的范围大小来决定。充填速度的高低对铸件的外轮廓和内部质量具有重要意义,充填速度过低,会使铸件的外轮廓不清晰;速度过高,则会使铸件内部的气孔增多,力学性能降低。合金浇铸温度过高,合金收缩大,铸件易产生裂纹;浇注温度过低,易产生冷隔、浇铸不足等缺陷。模具的预热可延长模具的使用寿命,避免金属液因激冷而失去流动,减少裂纹和缩孔等缺陷[9~10]。采用综合评分法,得出试验影响因素的主次为B,A,C,且最佳组合为B2A3C2。所以,得到的最优加工参数为:浇铸温度为660 ℃,充填速度为35 m/s,模具预热温度为180 ℃。
优化加工参数后的模拟结果如图5所示,虽在厚壁内部还存在少量缺陷,但已满足压铸件的质量要求。
4 生产验证
在新的浇注系统和数值分析最优加工参数条件下进行实际生产,抽检新产品,发现该产品克服了在异金属界面处出现间隙的现象,并且产品内部的缩松现象显著减少,缩孔现象基本消除(如图6所示),产品质量明显提高,满足使用要求。
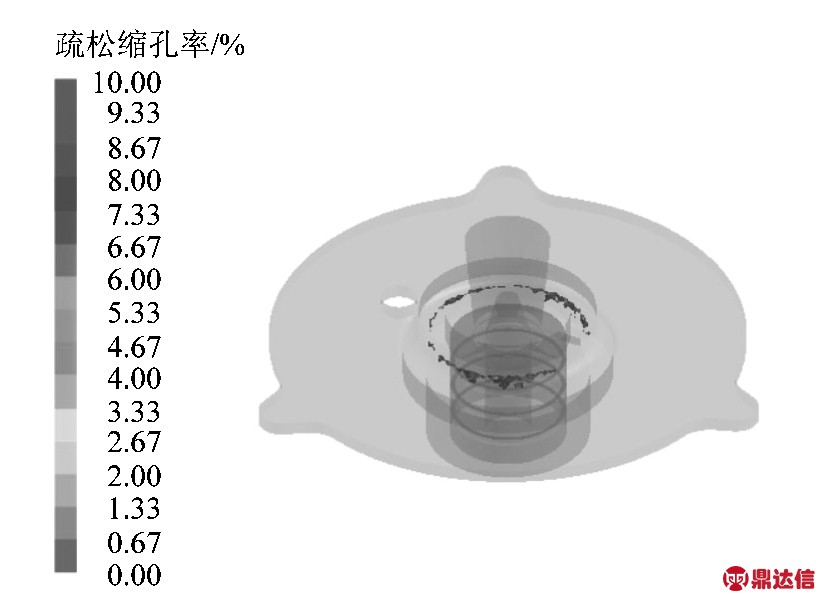
图5 模拟结果
Figure 5 Results of simulation

图6 新工艺参数下的产品
Figure 6 Products under new process parameters
5 结论
1) 课题组改进了铝合金壳体镶铸工艺中的浇铸系统。浇注系统应设计在离法兰盘面较近的一端,且采用中心浇道类型,此时工件异种金属界面间隙消失,缩孔、疏松缺陷显著减少。
2) 课题组用正交试验法优化了主要的加工参数。最优的加工参数为:浇铸温度为660 ℃,充填速度为35 m/s,模具预热温度为180 ℃。