摘 要:对4组12个足尺不等管径对接法兰进行了轴心受压及偏心受压试验,研究了不等管径对接法兰在不同强度级差加载时的受力性能。结果表明,每组3个试件的受力机理和破坏特征基本一致,大小管径对接法兰的变形主要集中在小管径一侧。试验中未发生法兰和对接焊缝的破坏,法兰及焊缝的承载力满足设计要求。试件由于靠近刚性法兰加劲肋处钢管鼓曲而破坏,其极限承载力超过承载力设计值的35%~54%。偏心受力会一定程度地降低试件的承载能力,但影响较小,基本在10%以内。对试验试件进行了非线性有限元分析,明确了法兰的破坏机理,了解了法兰的极限承载力。结果表明:受压状态下,对于不等管径法兰连接,带颈锻造法兰由受压为主逐渐转变为受弯为主,导致法兰颈部变坡提前进入屈服,降低了试件的承载力。
关键词:钢管塔; 锻造法兰; 受压性能; 试验研究; 有限元分析
钢管塔主材主要采用法兰连接,目前我国常用有劲法兰(刚性法兰)和无劲法兰(柔性法兰)两种形式[1-2]。有劲法兰在法兰板上焊有加劲肋板,法兰刚度大,螺栓受力简单,但焊接工作量大,且不易保证焊接质量; 无劲法兰则可减少焊接工作量,但没有加劲肋板,法兰变形较大,法兰的强度和刚度相对较小[3]。结合有劲法兰和无劲法兰的特点,研究者们提出了带颈锻造法兰,带颈锻造法兰通过锻造形成一体法兰,综合了传统刚性法兰和柔性法兰的优点,不但具有刚性法兰刚度大、相对变形小的特点,可用于承载力大的塔身主材连接,同时其质量易于控制,便于工厂生产及现场施工。带颈锻造法兰在国外的输电线路中已有了较多应用[4],但在国内的输电线路中应用较少。Willibald[5]、Hoang等[6]分别针对方钢管法兰连接节点和圆钢管法兰连接节点进行了试验研究,分析了螺栓布置方案、螺栓个数、螺栓边距以及法兰盘厚度对节点承载力的影响,初步总结了方钢管法兰连接的破坏模式。Blachowski等对轴拉荷载作用下的圆钢管法兰连接进行了数值模拟分析[7]。王元清等对4种基本形式的法兰连接节点试件进行了四点弯曲加载试验,考察了在节点受弯过程中螺栓和法兰盘的受力特性[8-9]。吴静首次在国内开展了Q420、Q460高强带颈对焊法兰节点轴拉承载力试验研究[10]。冯德奎等[11]和倪阳[12]采用有限元方法分别对新型双圈螺栓大型加劲法兰节点及锻造高颈无加劲法兰节点进行了非线性分析。张庆旭通过有限元方法,结合有关试验,分析了不同参数对法兰节点承载力的影响,提出了方钢管法兰节点的合理螺栓间距及法兰盘与方钢管的合理厚度比[13]。
综上所述,国内外主要针对刚性加劲法兰和柔性未加劲法兰开展研究,而对于带颈锻造法兰的试验研究很少,对于该节点的推广应用缺少较为充分的试验依据。本文针对强度级差柔性带颈锻造法兰,开展不等管径对接法兰轴心受压及偏心受压试验研究,采用有限元软件进行非线性数值模拟,分析其受力性能,提出设计建议,为柔性带颈锻造法兰的工程应用提供参考。
1 对接柔性带颈锻造法兰受压试验
1.1 试件设计与制作
设计了4组共12个足尺试件,如表1所示,带颈锻造法兰与圆钢管焊接,两个带颈锻造法兰之间用高强螺栓连接。其中,第1、2组为轴压试件,第3、4组为偏压试件,法兰强度级差为100%+70%。试件如图1所示,带颈锻造法兰规格如表2所示。
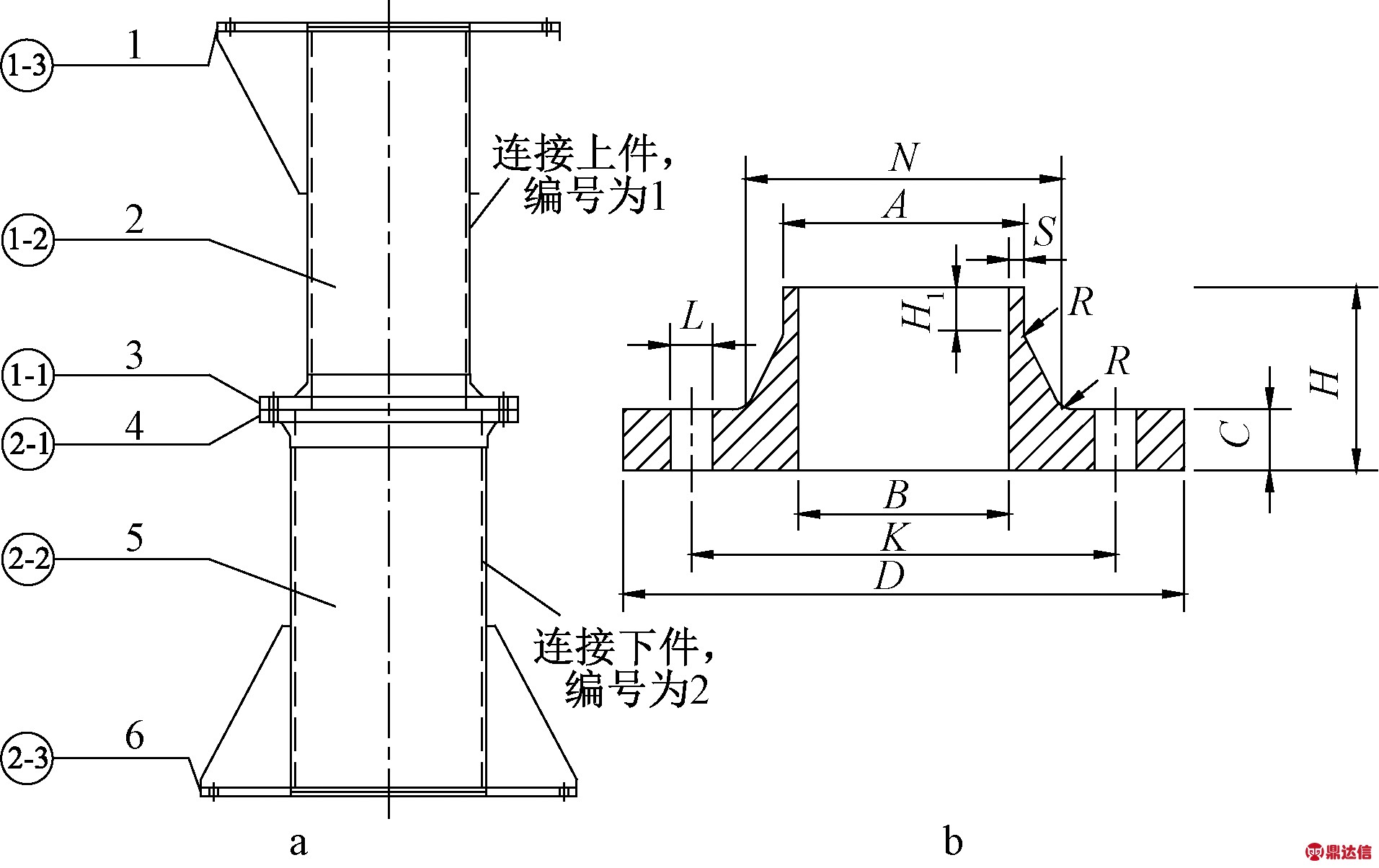
a—不等管径对接法兰;b—法兰设计参数。
1—连接试验装置:有劲法兰1;2—等管径钢管1;3—等管径对接法兰1;4—等管径对接法兰2;5—等管径钢管2;6—连接试验装置:有劲法兰2。
图1 法兰试件示意
1.2 材性参数
带颈锻造法兰和钢管钢材强度,根据GB/T 2975—1998《钢及钢产品力学性能试验取样位置及试样制备》[14]的要求,在钢管和带颈锻造法兰的相应部位取样,并制作材性试验试样,共10组,每组3件。材性试验结果如表3所示。
表1 试件规格
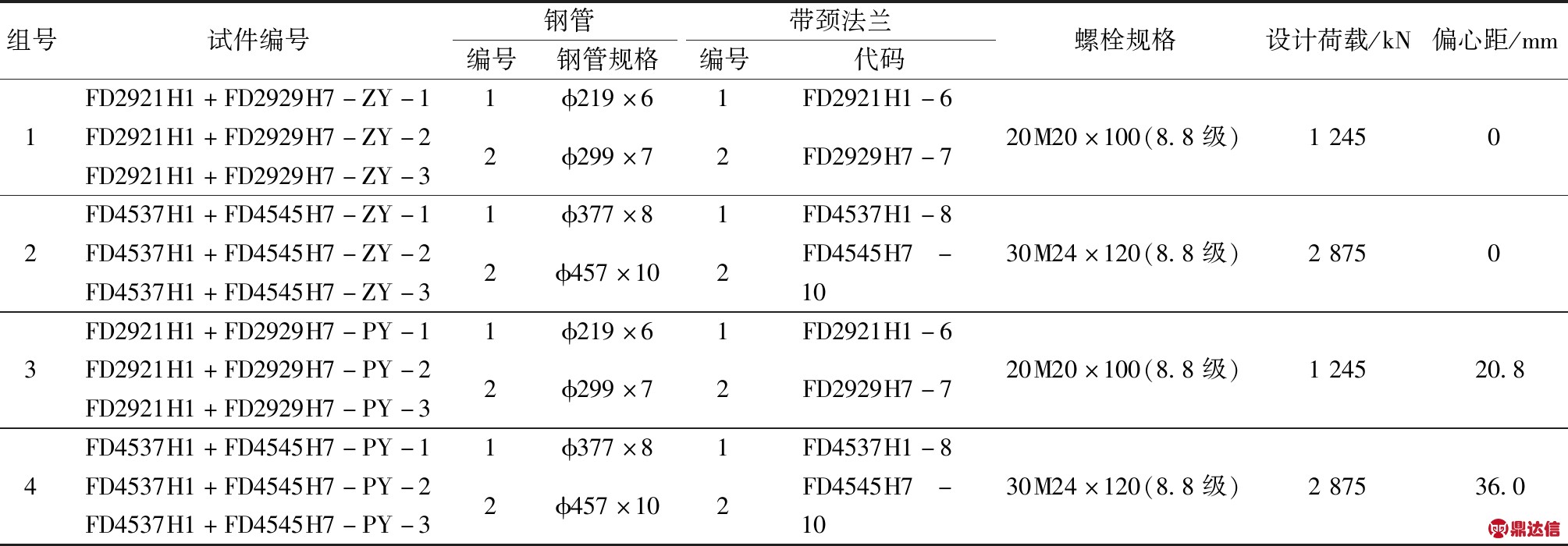
表2 带颈法兰参数

1.3 试验装置和加载方案
试验装置如图2所示。试验为静力加载,加载方案如下:先预加载2次,加载至承载力设计值(P设)的60%,卸载到0%。第3次后逐级加载,加载顺序为:0%P设→20%P设→40%P设→60%P设→70%P设→80%P设→85%P设→90%P设→95%P设→100%P设→105%P设…,每级加载为设计荷载的5%。加载直至满足以下3个条件之一即可停止:超载至150%、试件破坏或加载装置的最大荷载。
表3 钢材材性试验结果
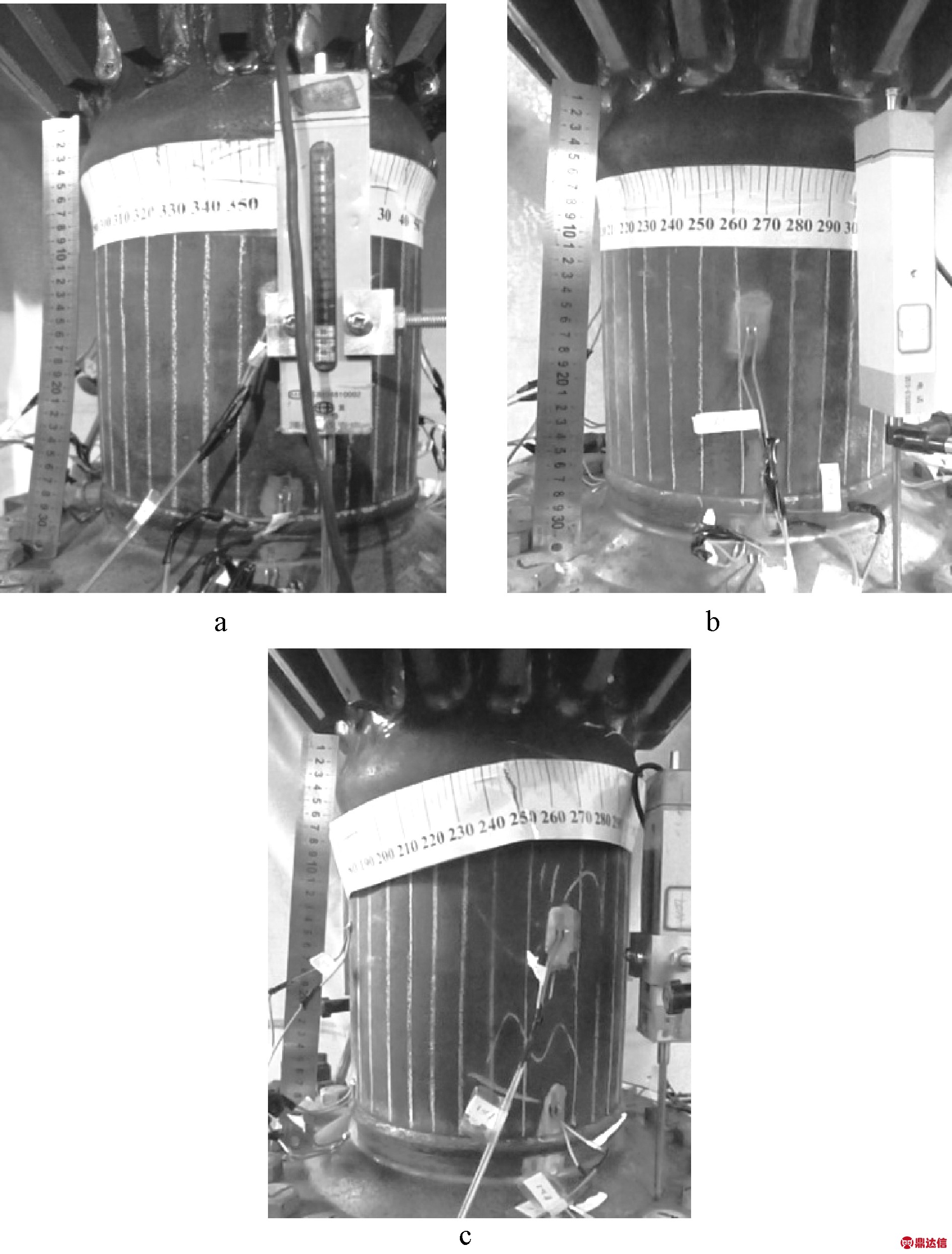
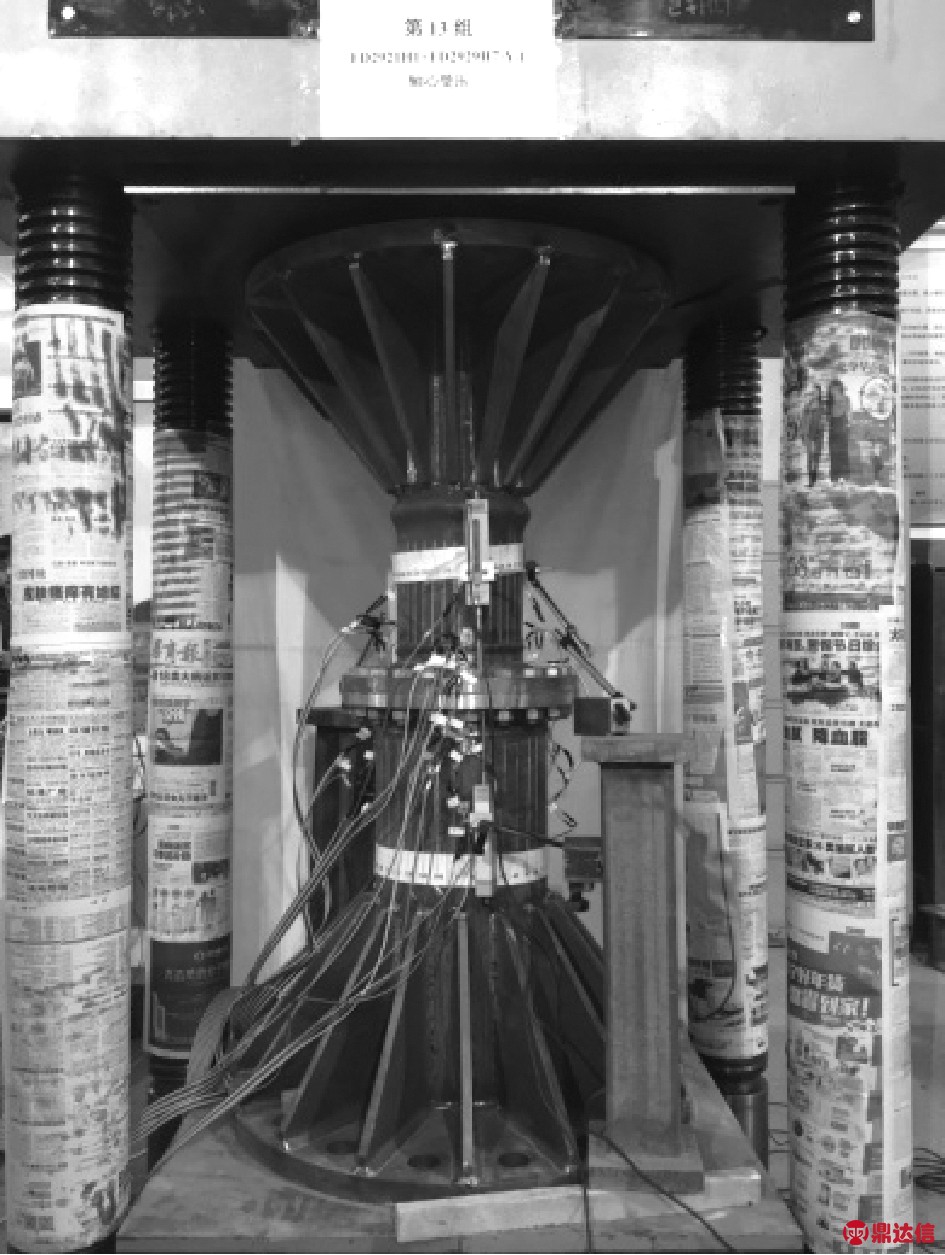
图2 试验装置
1.4 测点布置
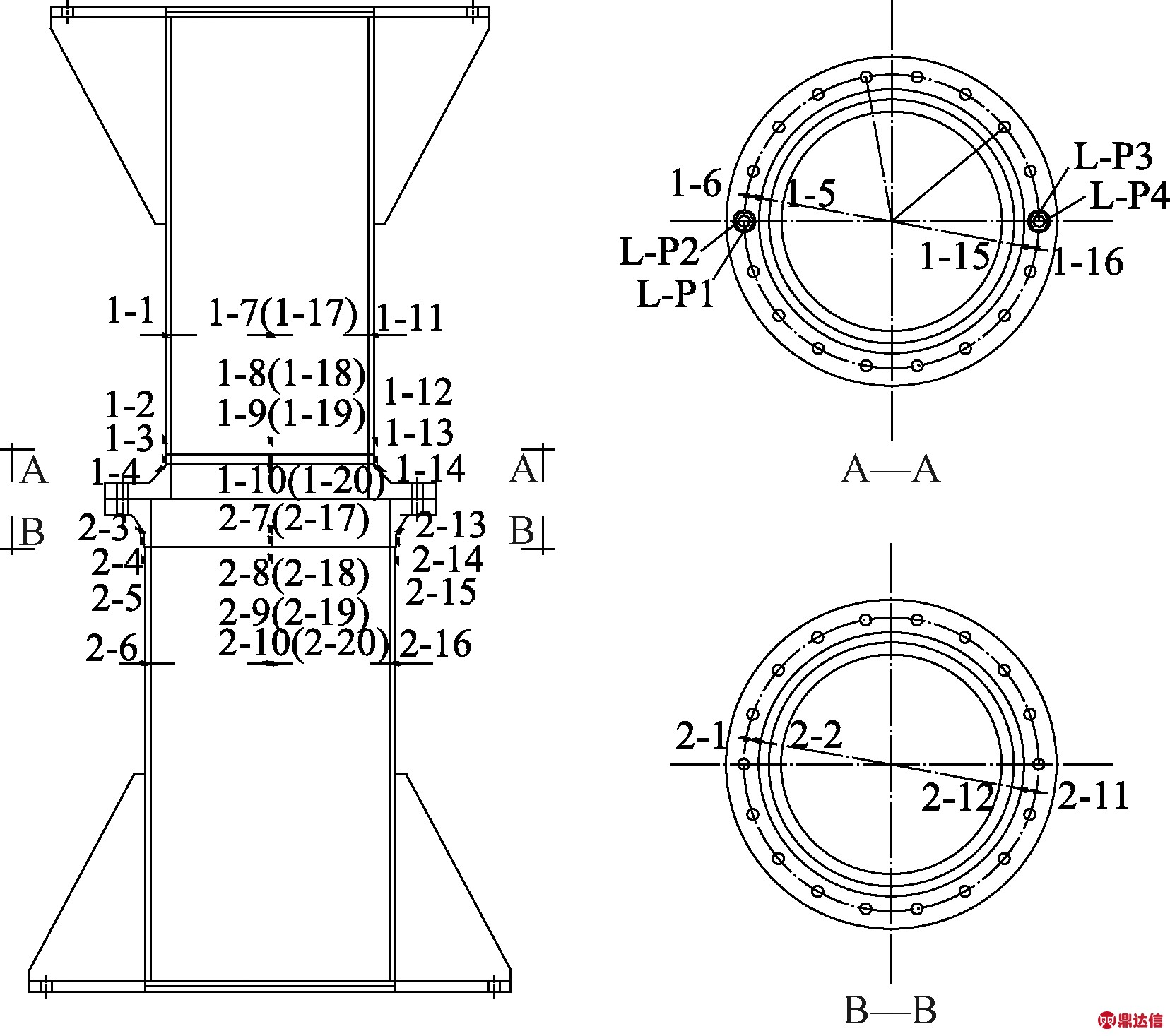
图3 应变测点布置
在法兰盘变坡根部对称设置4个量程为±100 mm 的位移计,测量法兰盘的变形特性。为了准确测量螺栓的应变,对螺栓开槽,在槽内布置应变片。在试件管身中部、近焊缝处钢管端口、近焊缝处法兰颈口、法兰颈部变坡、法兰盘面等部位布置应变片,以监测试件的应力发展情况。应变片测点布置如图3所示,其中,法兰试件连接上件1上粘贴的应变片编号为1-*;连接下件2上粘贴的应变片编号为2-*;螺栓应变片编号为L-P*。
1.5 试验过程和试验现象
1.5.1 试件FD2921H1+FD2929H7
1)轴心受压。
三个试件分别加载至1 560,1 620,1 560 kN时,均无明显现象,分别加载至1 620 kN、1 680 kN(设计值的135%)、1 620 kN(设计值的130%)时,小管径钢管靠近刚性法兰加劲肋处开始鼓曲;分别加载至1 849,1 919,1 842 kN时荷载开始下降,即三个试件的极限承载力分别为1 849,1 919,1 842 kN。荷载分别降至1 290,1 340,1 290 kN(极限承载力的70%)时停止加载,此时三个试件小管径钢管最大鼓曲位置距刚性法兰加劲肋分别约5,4.5,4.5 cm(图4)。
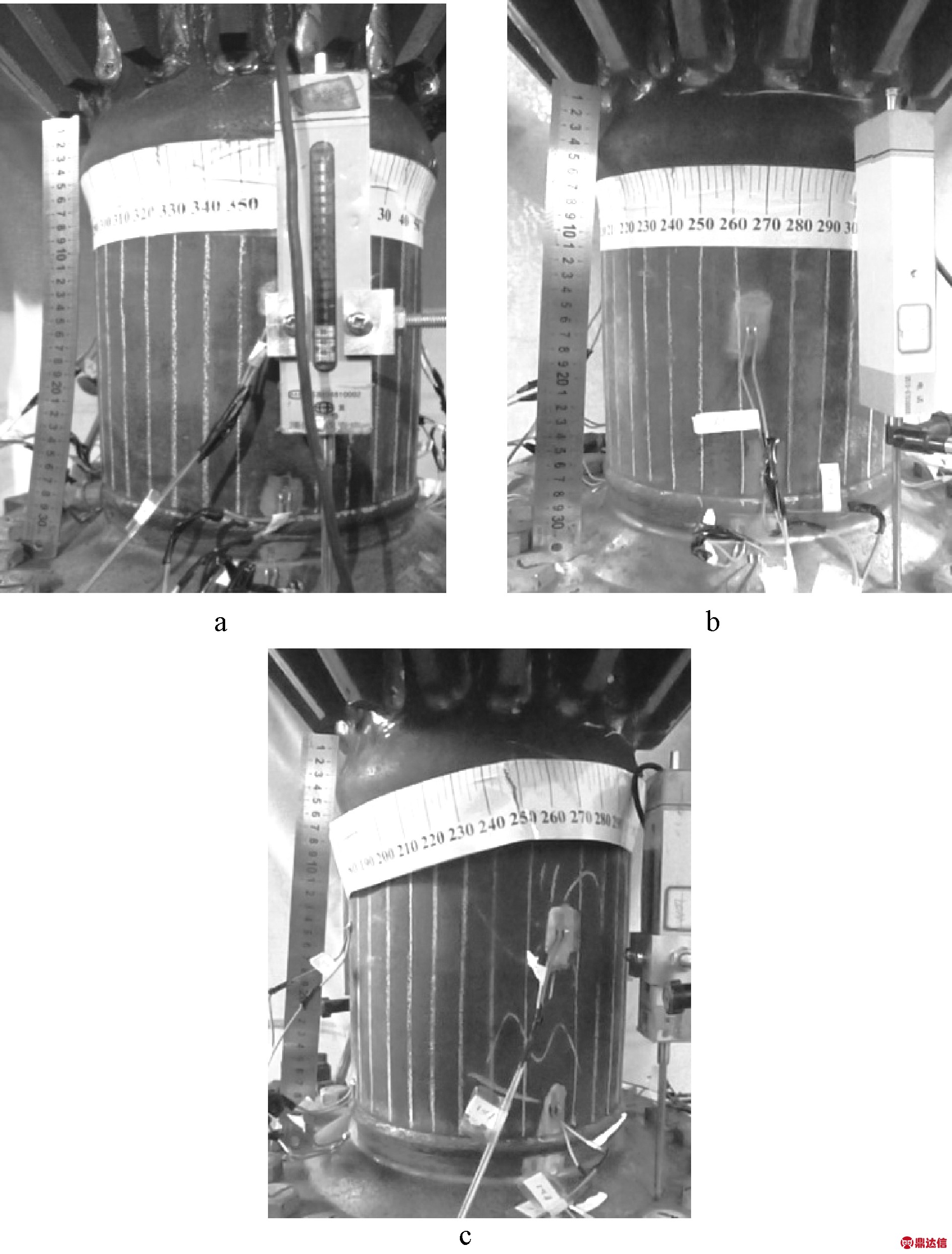
a—FD2921H1+FD2929H7-ZY-1小管径钢管鼓曲;b—FD2921H1+FD2929H7-ZY-2小管径钢管鼓曲;c—FD2921H1+FD2929H7-ZY-3小管径钢管鼓曲。
图4 试件FD2921H1+FD2929H7轴压试验现象
2)偏心受压。
三个试件分别加载至1 430,1 500,1 430 kN时,均无明显现象,分别加载至1 500 kN(设计值的120%)、1 560 kN(设计值的125%)、1 500 kN(设计值的120%)时,小管径钢管靠近刚性法兰加劲肋处偏压侧开始鼓曲;随着荷载的增大,偏压侧鼓曲明显,偏拉侧开始鼓曲;三个试件分别加载至1 920,1 918,1 915 kN时荷载开始下降,即三个试件的极限承载力分别为1 920,1 918,1 915 kN。三个试件荷载均降至1 340 kN(极限承载力的70%)时停止加载,此时小管径钢管最大鼓曲位置距刚性法兰加劲肋均约4 cm(图5),且试件FD2921H1+FD2929H7-PY-1带颈法兰与钢管之间的连接焊缝出现损伤(图6)。
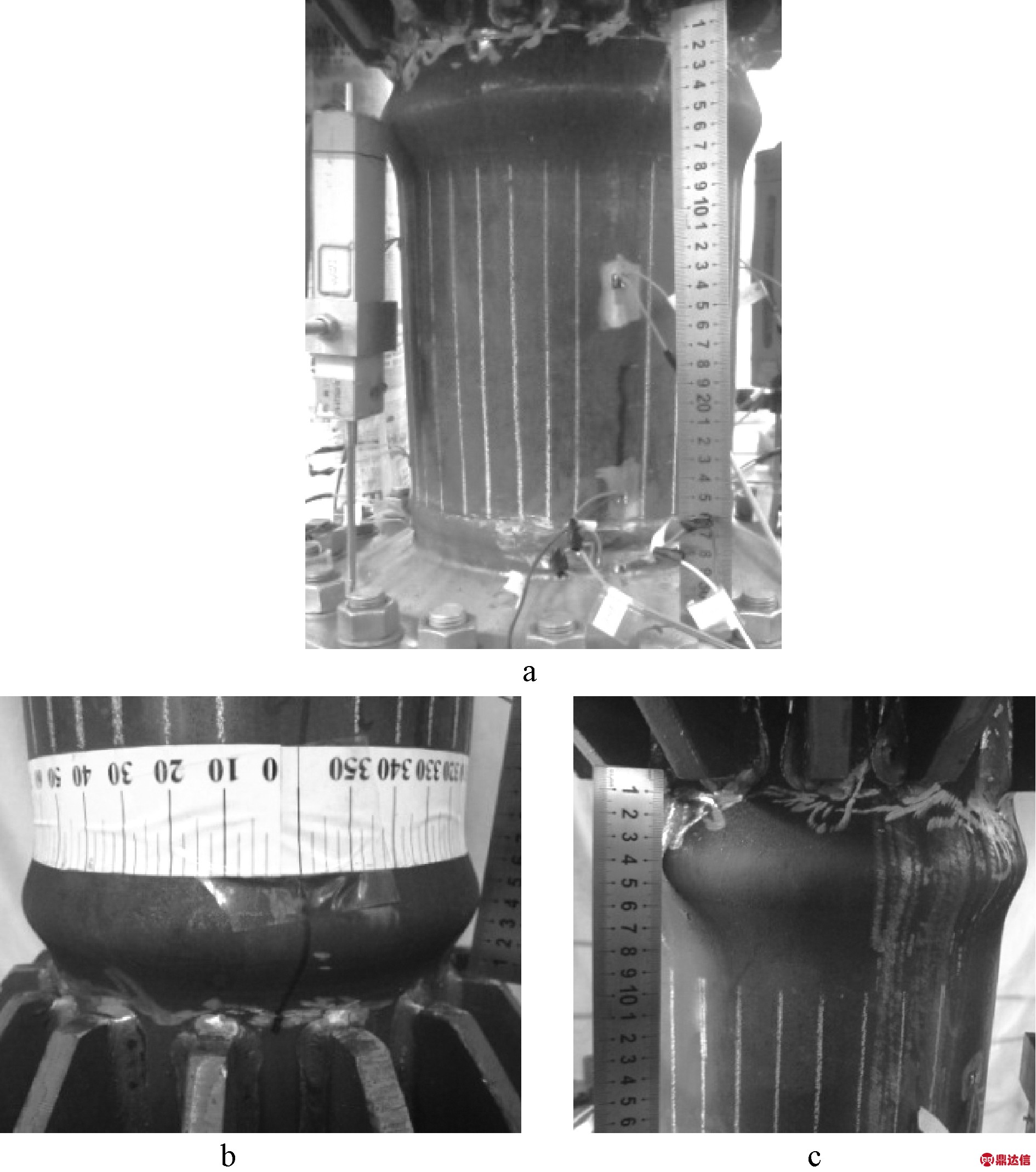
a—FD2921H1+FD2929H7-PY-1小管径钢管鼓曲;b—FD2921H1+FD2929H7-PY-2小管径钢管鼓曲;c—FD2921H1+FD2929H7-PY-3小管径钢管鼓曲。
图5 试件FD2921H1+FD2929H7偏心受压试验现象
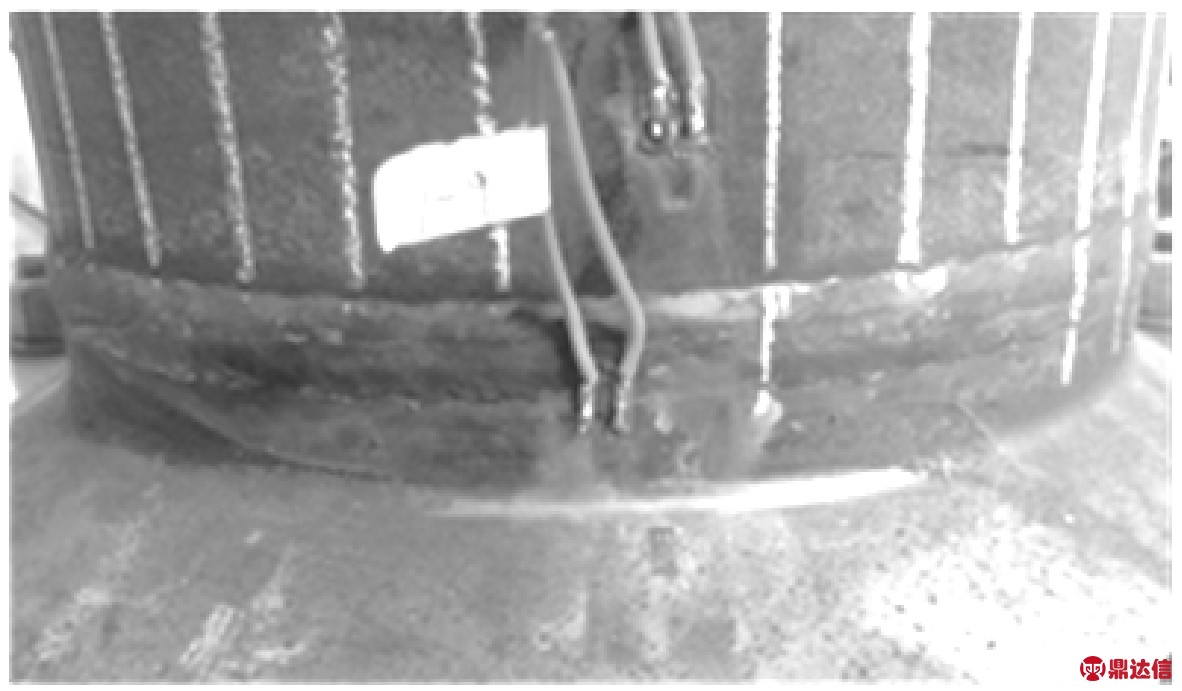
图6 带颈法兰与钢管连接焊缝损伤
1.5.2 试件FD4537H1+FD4545H7
1)轴心受压。
3个试件分别加载至3 450 kN(设计值的120%)、3 310 kN(设计值的115%)、3 310 kN(设计值的115%)时,小管径钢管靠近刚性法兰加劲肋处开始鼓曲;分别加载至4 117,4 081,4 005 kN时荷载开始下降,即三个试件的极限承载力分别为4 117,4 081,4 005 kN。荷载分别降至2 910,2 850,2 800 kN(极限承载力的70%)时停止加载,此时三个试件的小管径钢管最大鼓曲位置距刚性法兰加劲肋分别约6,5.5,6 cm(图7)。
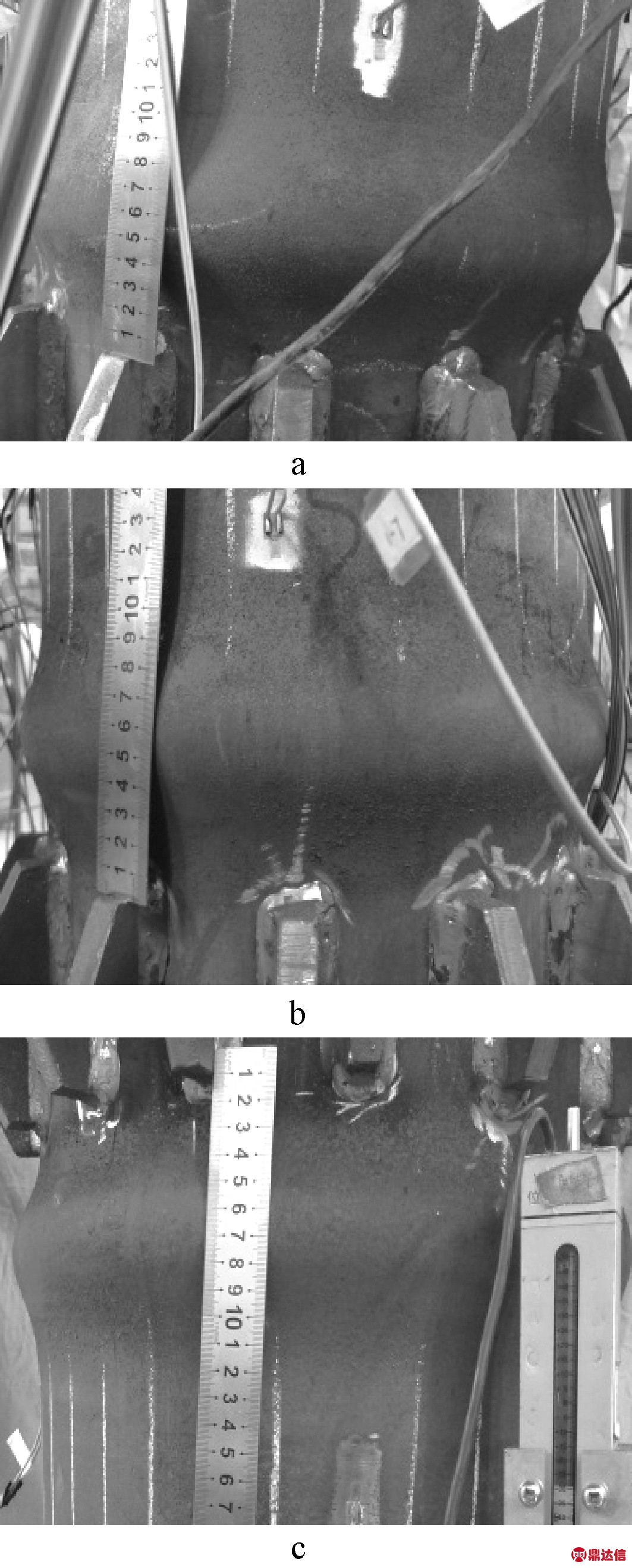
a—FD4537H1+FD4545H7-ZY-1小管径钢管鼓曲;b—FD4537H1+FD4545H7-ZY-2小管径钢管鼓曲;c—FD4537H1+FD4545H7-ZY-3小管径钢管鼓曲。
图7 试件FD4537H1+FD4545H7轴压试验现象
2)偏心受压。
三个试件加载至3 170 kN时,试件无明显现象。加载至3 310 kN(设计值的115%)时,小管径钢管靠近刚性法兰加劲肋处偏压侧开始鼓曲;三个试件分别加载至3 740 kN(设计值的130%)、3 600 kN(设计值的125%)、3 600 kN(设计值的125%)时,偏压侧鼓曲明显,偏拉侧开始鼓曲;分别加载至3 890,3 996,3 894 kN时荷载开始下降,即三个试件的承载力分别为3 890,3 996,3 894 kN。当荷载降至2 720,2 800,2 720 kN(承载力的70%)时停止加载,此时三个试件的小管径钢管最大鼓曲位置距刚性法兰加劲肋均约6 cm(图8)。
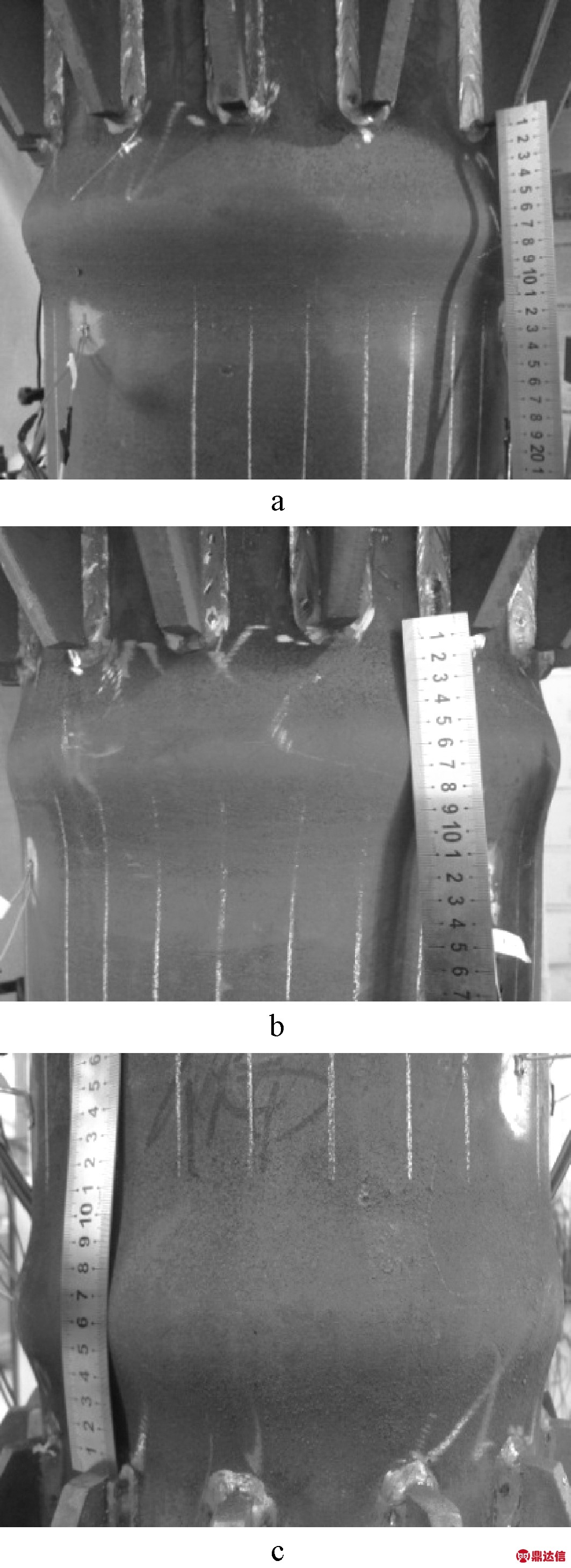
a—FD4537H1+FD4545H7-PY-1小管径钢管鼓曲;b—FD4537H1+FD4545H7-PY-2小管径钢管鼓曲;c—FD4537H1+FD4545H7-PY-3小管径钢管鼓曲。
图8 试件FD4537H1+FD4545H7偏心受压试验现象
2 试验结果分析
2.1 变 形
由试验现象可知,各试件的破坏形态较为一致,均为小管径钢管靠近刚性法兰加劲肋处发生鼓曲,轴压试件鼓曲变形较为均匀,偏压试件的偏压侧鼓曲较偏拉侧明显。
各试件钢管初始鼓曲荷载如表4所示,可知,同组试件初始鼓曲对应的荷载值接近。对于试件组FD2921H1+FD2929H7,轴压试件初始鼓曲的荷载值较偏压试件初始鼓曲的荷载值大,即相同情况下偏压试件较轴压试件更早发生破坏。而试件组FD4537H1+FD4545H7中,轴压试件初始鼓曲的荷载值与偏压试件初始鼓曲的荷载值基本相同,即偏心加载对其破坏机制的影响不明显。
表4 各试件钢管初始鼓曲对应的荷载值比较 kN
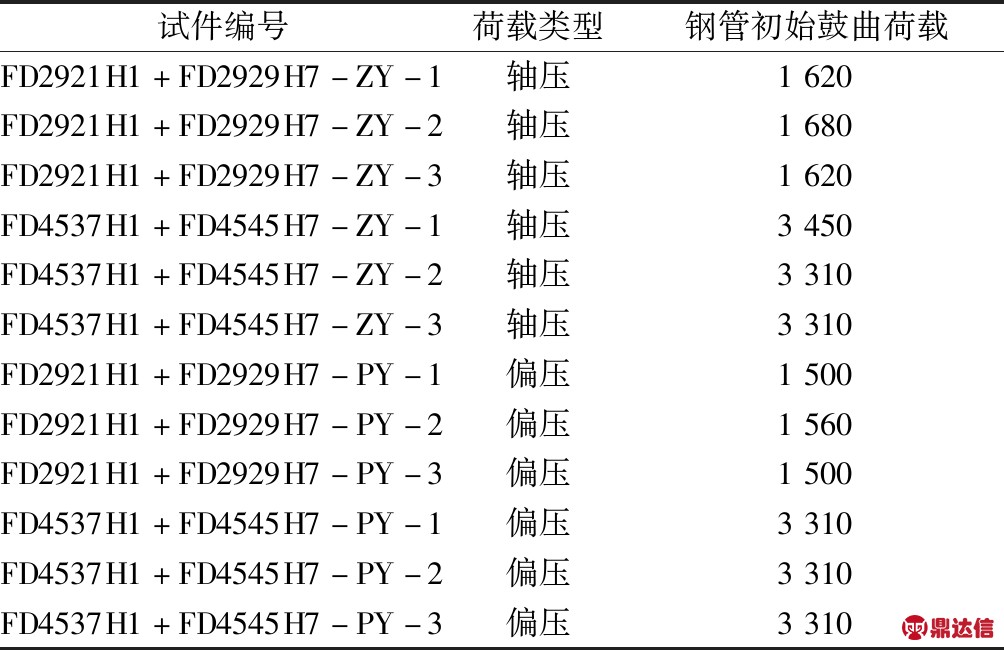
2.2 承载力
试件的荷载-位移曲线如图9所示。可知,各试件均有明确的弹性阶段、弹塑性阶段和极限破坏阶段。加载初期,试件处于弹性,荷载-位移曲线接近直线,每组试件的初始刚度基本相同,屈服荷载后,较小管径钢管靠近刚性法兰加劲肋处出现鼓曲,试件刚度逐渐下降,达到峰值荷载后,试件承载力逐渐降低。对于试件组FD2921H1+FD2929H7,每组试件的荷载-位移曲线基本相同;而对于试件组FD4537H1+FD4545H7,每组试件的荷载-位移曲线基本接近,但个别试件存在一定的差别。
各试件的极限承载力如表5所示。可知,每组试件的承载力接近。对于试件组FD2921H1+FD2929H7,试验值比设计值高48%以上,偏压试件承载力与轴压试件承载力接近,故偏心加载对其承载力的影响很小。对于试件FD4537H1+FD4545H7,试验值比设计值高35%以上,轴压试件承载力高于偏压试件承载力3.6%左右,偏心加载对其影响不明显。
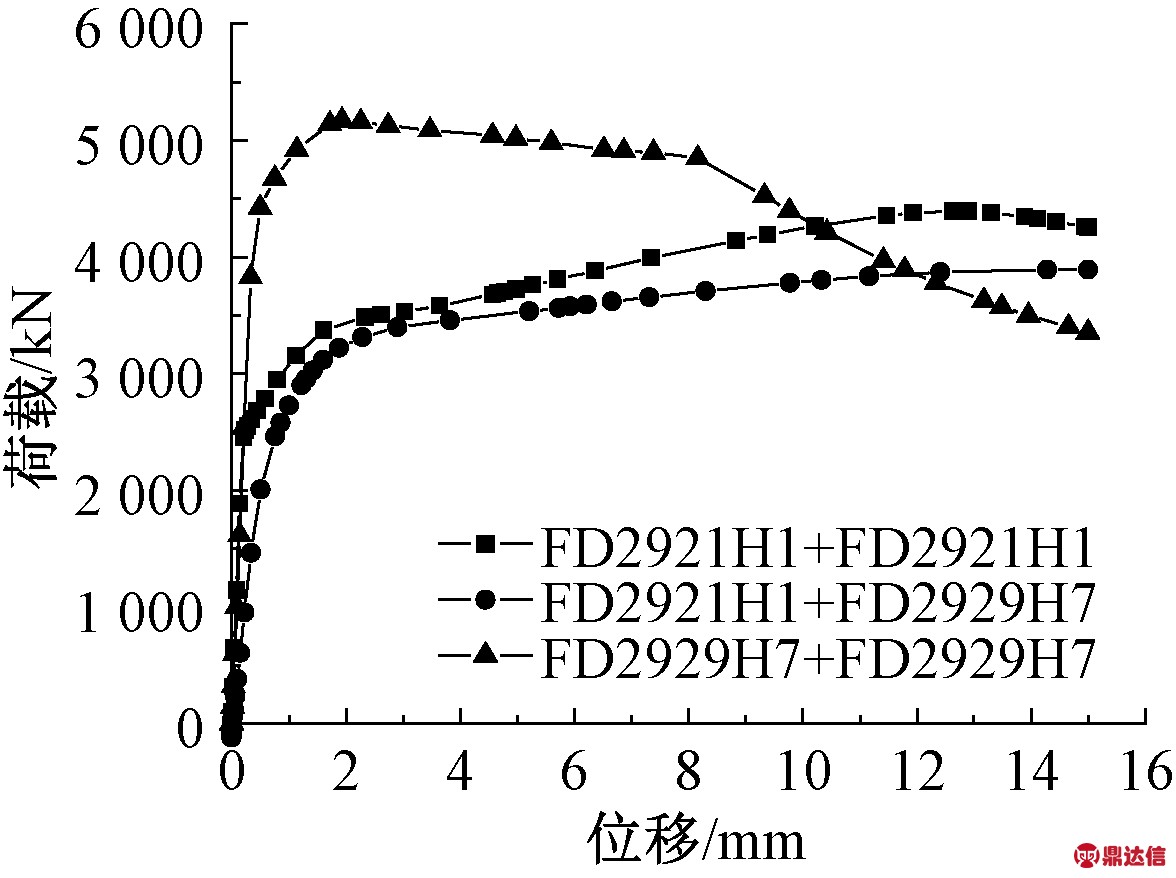
a—试件FD2921H1+FD2929H7-ZY;b—试件FD2921H1+FD2929H7-PY;c—试件FD4537H1+FD4545H7-ZY;d—试件FD4537H1+FD4545H7-PY。
图9 试验荷载-位移曲线
表5 极限承载力
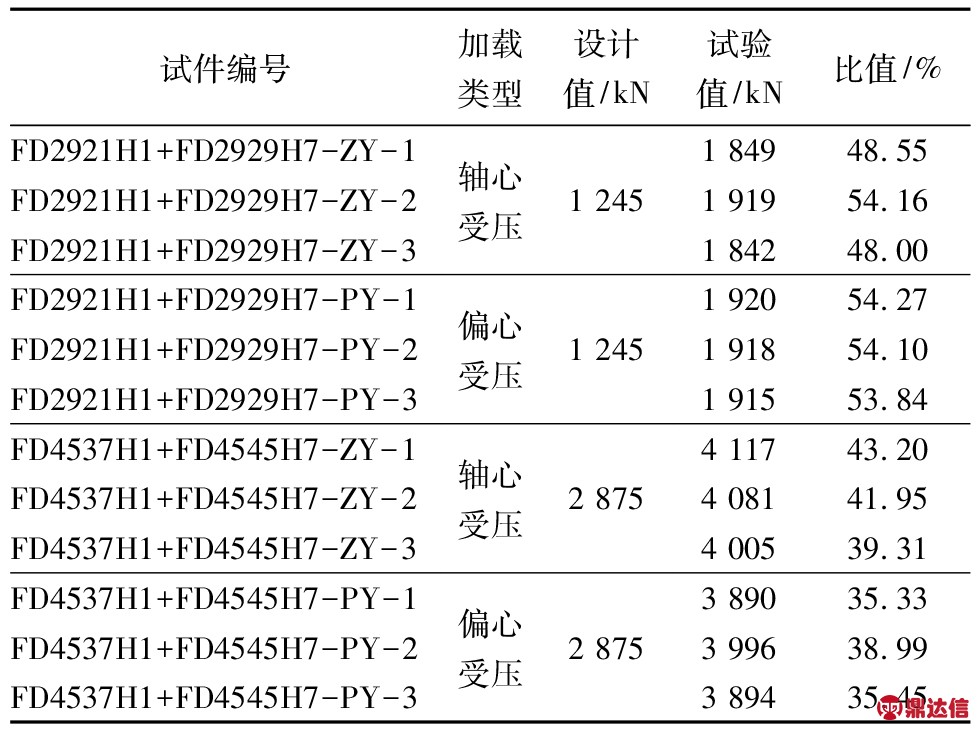
注:比值
2.3 法兰应变分析
以试件FD2921H1+FD2929H7-ZY为例进行分析,法兰应变发展情况如图10所示,图中ε为单轴应变。
2.3.1 近焊缝处法兰颈口
因受力面积较大,大管径带颈锻造法兰近焊缝处法兰颈口应力较小,在加载过程中应变值始终小于屈服应变,保持弹性。对于小管径带颈锻造法兰近焊缝处法兰颈口,加载至承载力设计值时,基本进入塑性阶段;当钢管鼓曲后应变发展加快。对于整个带颈锻造法兰,小管径近焊缝处法兰颈口的应变值最大,且仅法兰颈口进入塑性,是带颈锻造法兰连接的最薄弱处;同时法兰颈口有比钢管更早屈服的趋势,在设计中应适当给予加强。
2.3.2 法兰颈部变坡
初始加载时,应变呈线性增长;加载至承载力设计值,应变增长缓慢;加载至1 620 kN时,应变值有减小的趋势。整个加载过程均处于弹性阶段,且应变值均未超过屈服应变的50%,小管径带颈锻造法兰变坡处应变较大管径带颈锻造法兰变坡处大。因此,法兰颈部变坡处承载力有较大富余。
2.3.3 法兰盘
加载过程中,法兰盘面上的应变较小,且均小于1 000×10-6,始终处于弹性阶段。由于连接不等管径的法兰内径不一致,在受压过程中整个带颈锻造法兰处于弯压状态,导致法兰盘面近变坡根部处于拉伸状态;而法兰盘面近螺栓处由于螺栓预紧力的影响,受力较为敏感,应变发展较为离散。
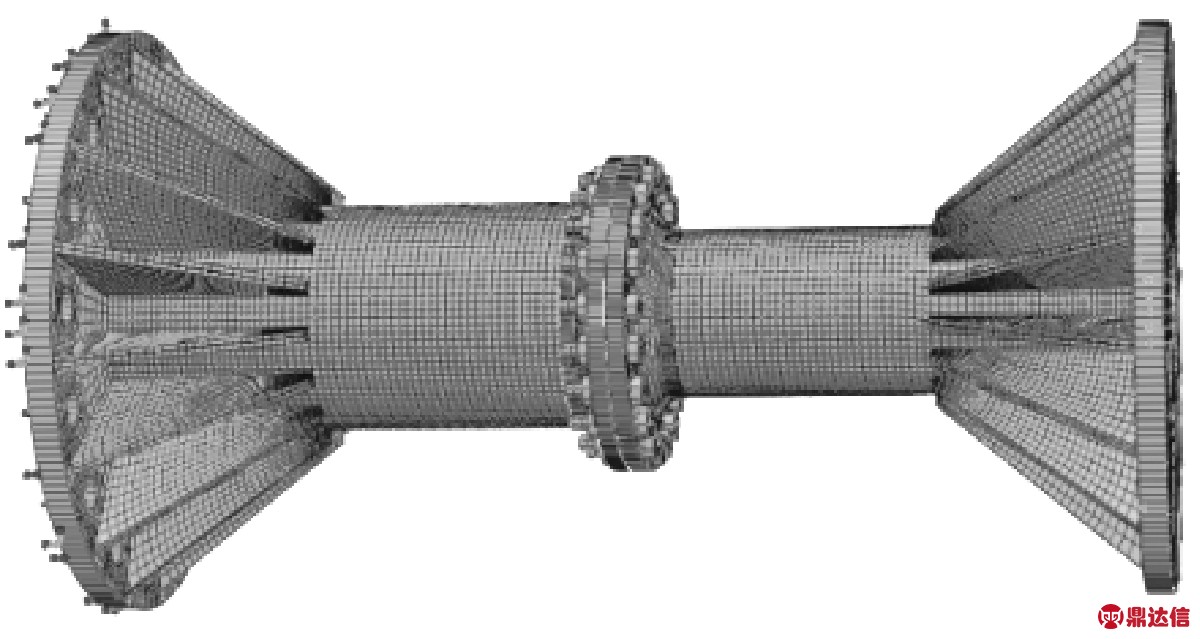
a—近焊缝处法兰颈口;b—法兰颈部变坡;c—法兰盘近螺栓处。
图10 试件FD2921H1+FD2929H7-ZY法兰各应变片的应变发展
3 有限元分析
采用非线性有限元软件ABAQUS 6.13对试验试件进行精细化数值分析,将数值分析结果与试验结果进行对比,剖析其应力发展过程,明确其受力机理和破坏机制。
3.1 模型的建立
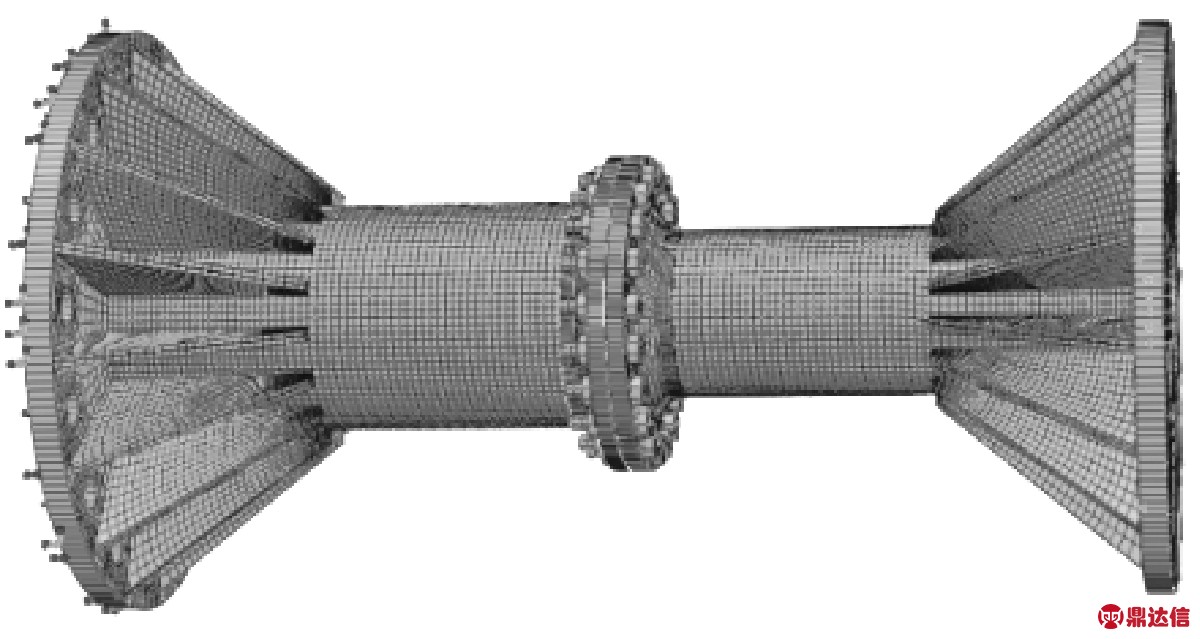
图11 有限元模型
钢材本构模型选用等向弹塑性模型,材性参数按表3所示材性试验结果取值,泊松比取0.3。模型网格划分及边界条件如图11所示,试件各部件均采用八结点减缩积分实体单元(C3D8R)建模,钢管与带颈锻造法兰之间绑定(Tie),构件底部施加固接约束,荷载通过在试件顶部施加位移的方式实现。考虑几何缺陷的影响,初始几何缺陷通过屈曲分析得到。
3.2 有限元结果分析
各试件的破坏形态如图12所示。可知,各试件的破坏形态较为一致,均为小管径钢管靠近刚性法兰加劲肋处发生鼓曲,与试验变形基本一致。有限元模拟能够较好地反映试件的变形形态。
各试件有限元与试验荷载-位移曲线对比如图13所示。可知,有限元荷载-位移曲线与试验荷载-位移曲线相近,两者初始刚度和屈服荷载基本一致;由于有限元分析未能考虑残余应力等影响,因此,有限元计算所得试件承载力略高于试验值。总体上,有限元模拟能够较为真实地反映试件的初始刚度、屈服荷载及承载能力。
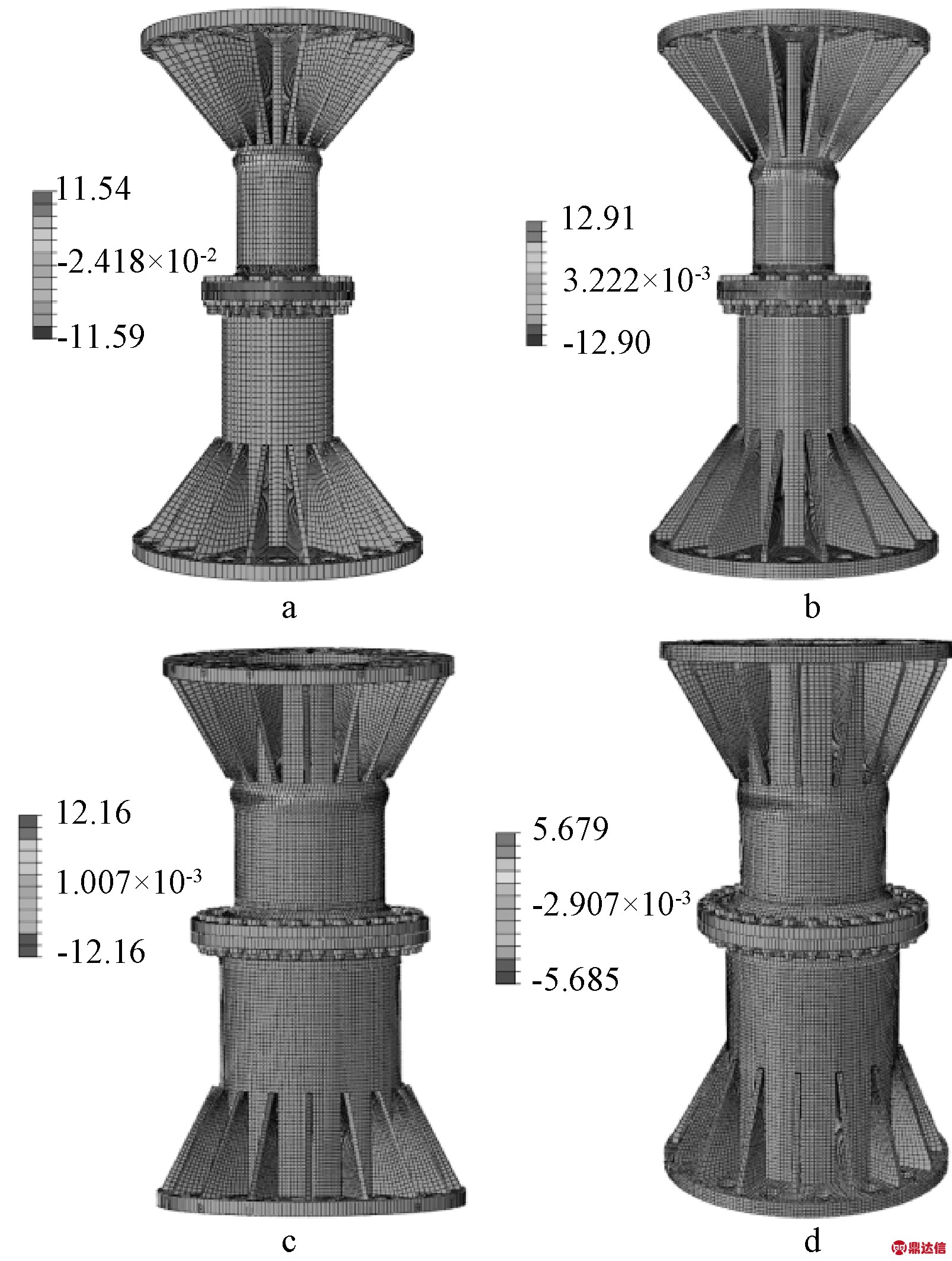
a——FD2921H1+FD2929H7-ZY;b—FD2921H1+FD2929H7-PY;c—FD4537H1+FD4545H7-ZY;d—FD4537H1+FD4545H7-PY。
图12 有限元变形形态 mm
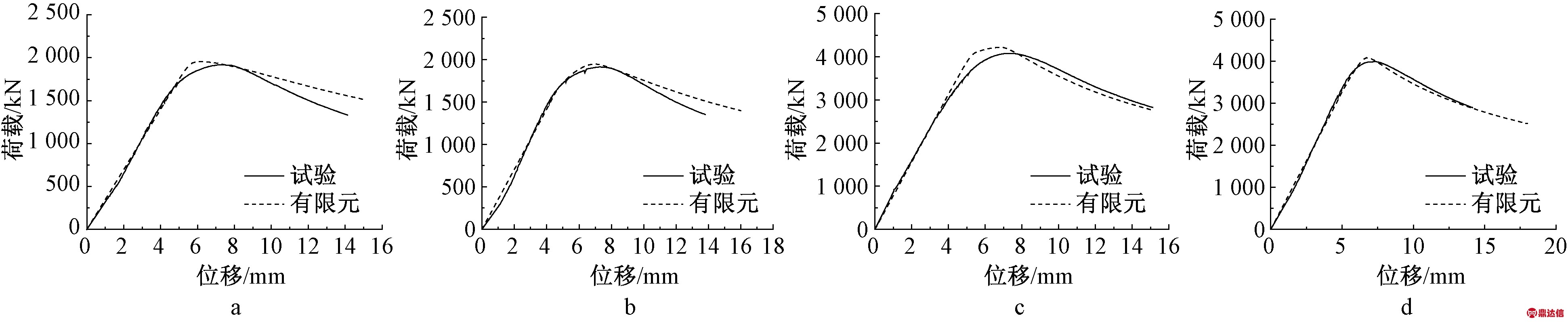
a—FD2921H1+FD2929H7-ZY;b—FD2921H1+FD2929H7-PY;c—FD4537H1+FD4545H7-ZY;d—FD4537H1+FD4545H7-PY。
图13 有限元与试验的荷载-位移曲线对比
3.3 法兰极限承载力研究
由试验可知,试件由于靠近刚性法兰加劲肋处钢管鼓曲而破坏,此时,法兰并未达到极限状态。为了解法兰的极限状态和极限承载力,采用有限元软件ABAQUS对其极限承载力进行分析。模型尺寸与试验试件相同。为了防止钢管、螺栓过早破坏,增大除法兰外其他部件的刚度,弹性模量增大至实际弹性模量的10倍,并约束钢管的面外变形,加载方法与试验相同。
对等管径和不等管径的法兰承载力进行对比研究,针对法兰FD2921H1、FD2929H7建立了3组模型,编号分别为FD2921H1+FD2921H1、FD2921H1+FD2929H7、FD2929H7+FD2929H7;针对法兰FD4537H1、FD4545H7亦建立了3组模型:FD4537H1+FD4537H1、FD4537H1+FD4545H7、FD4545H7+FD4545H7。相应试件模型荷载-位移曲线如图14、图15所示。
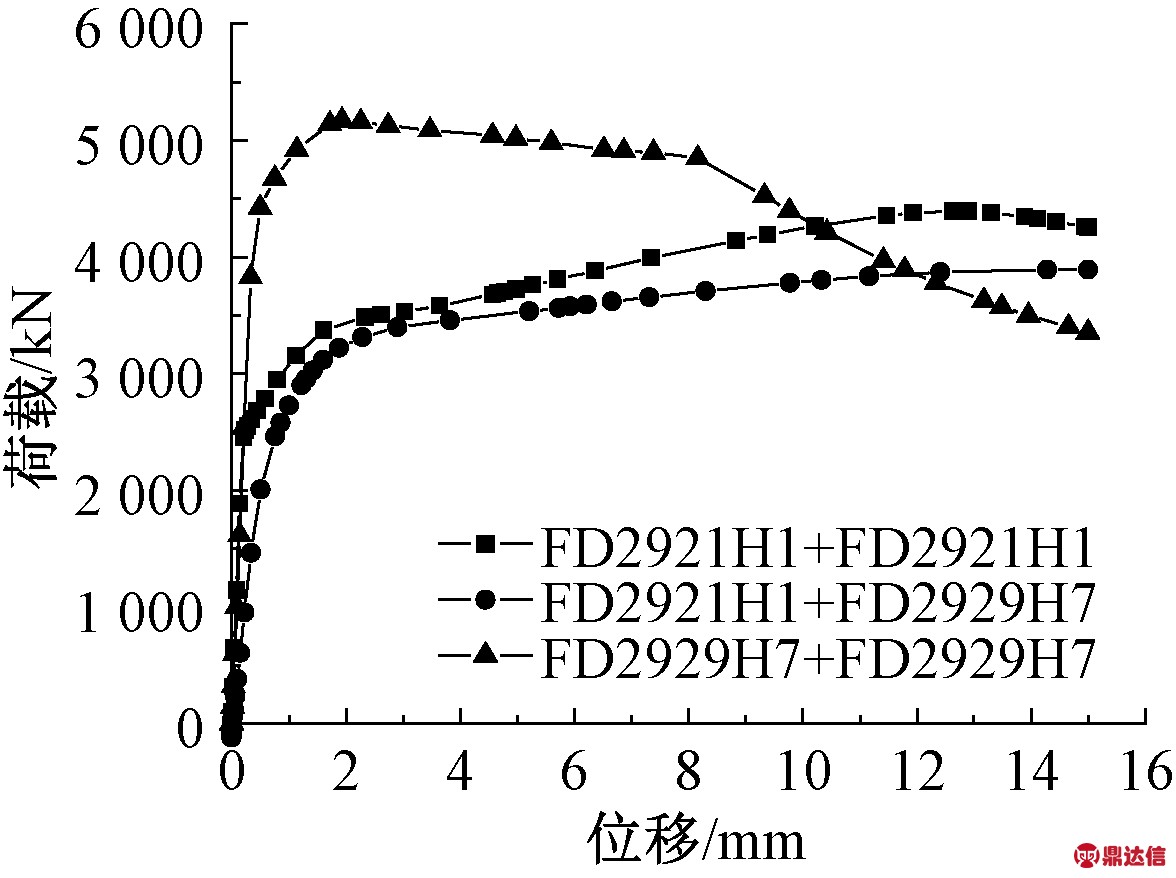
图14 FD2921H1、FD2929H7法兰组的荷载-位移曲线对比
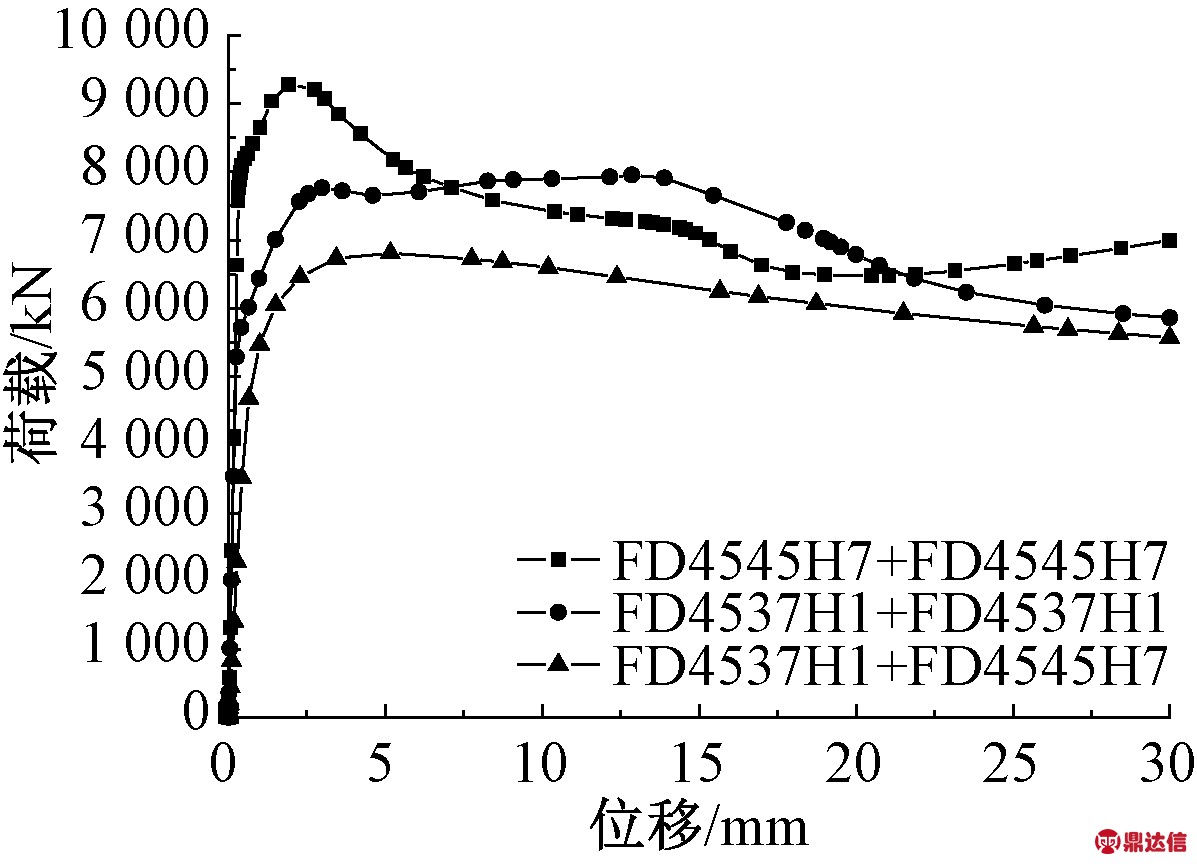
图15 FD4537H1、FD4545H7法兰组的荷载-位移曲线对比
由图14、图15可得各模型对应的屈服荷载和极限荷载如表6所示。由表6可知,FD2929H7+FD2929H7的屈服荷载和极限荷载高于其他两组,FD2921H1+FD2921H1的屈服荷载和极限荷载高于FD2921H1+FD2929H7。FD4545H7+FD4545H7的屈服荷载和极限荷载高于其他两组,FD4537H1+FD4537H1的屈服荷载和极限荷载高于FD4537H1+ FD4545H7。
表6 法兰屈服荷载和极限荷载 kN
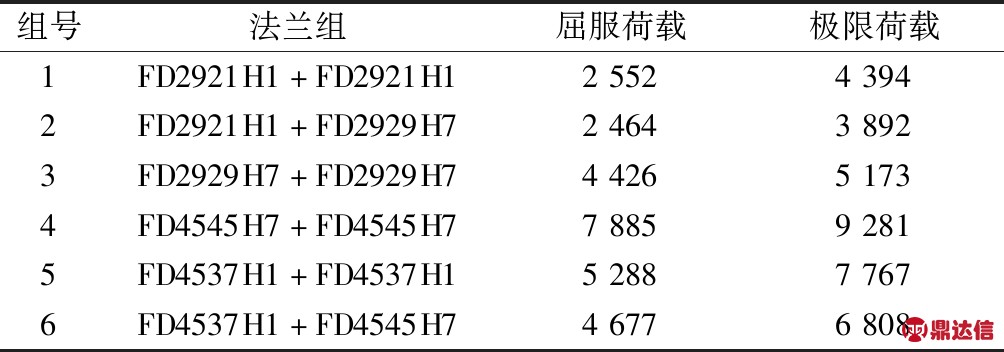
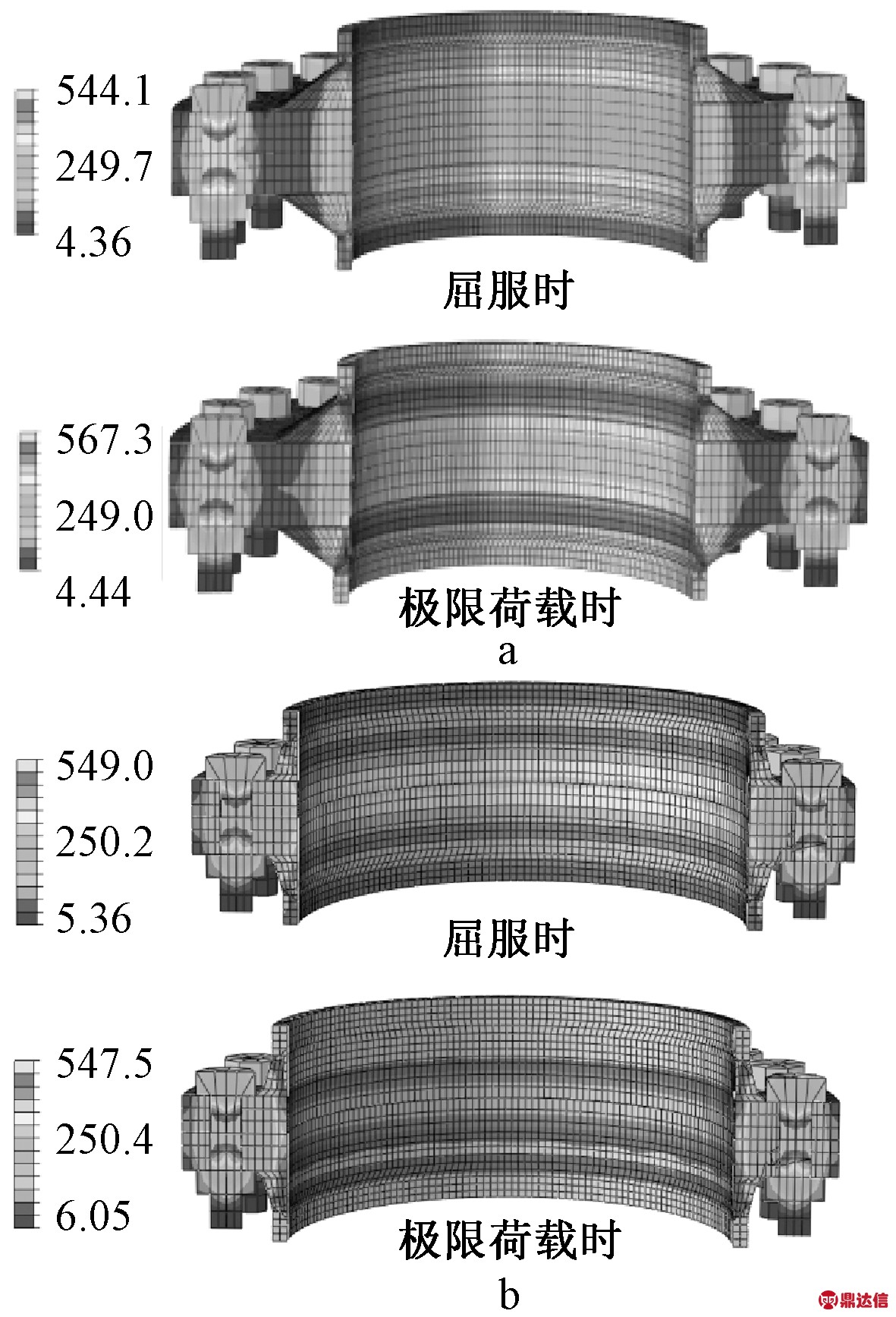
a—FD2921H1+FD2921H1;b—FD2929H7+FD2929H7。
图16 法兰第1组和第3组应力 MPa
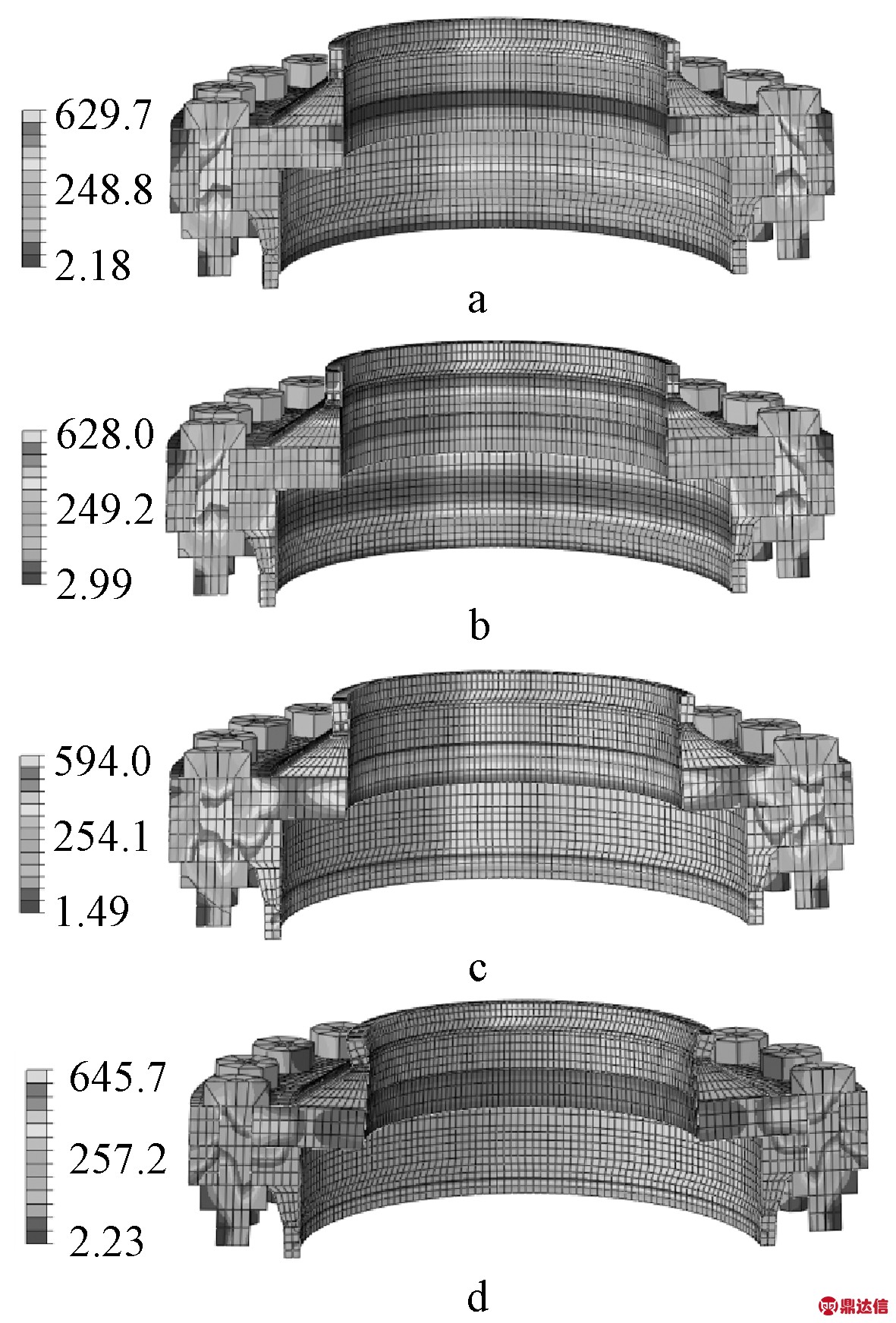
a—小管径近焊缝处法兰颈口局部屈服;b—小管径近焊缝处法兰颈口全截面屈服;c—大管径法兰颈部变坡全截面屈服;d—极限荷载时应力。
图17 FD2921H1+FD2929H7法兰组应力 MPa
FD2921H1、FD2929H7法兰组中各法兰应力发展如图16、图17所示。由图可知,对于等管径法兰连接,近焊缝处法兰颈口首先受压屈服,随后全截面屈服,法兰达到极限状态。对于不等管径法兰连接,首先,小管径近焊缝处法兰颈口受压局部屈服;随后,小管径近焊缝处法兰颈口全截面屈服,同时大管径法兰颈部变坡内侧局部屈服,说明此时大管径法兰盘受弯矩作用影响法兰承载力。随着荷载增大,大管径法兰颈部变坡全截面屈服,大管径法兰由受压为主转变为受弯为主,大管径法兰颈部变坡外侧受拉,内侧受压。极限荷载时,近焊缝处法兰颈口和法兰颈部变坡全截面进入塑性,法兰破坏。
由以上分析可知,不等管径法兰连接受压时,带颈锻造法兰由受压为主逐渐转变为受弯为主,导致法兰颈部变坡提前进入屈服,降低其承载力。FD4537H1、FD4545H7法兰组的变形机制和破坏形态与FD2921H1、FD2929H7法兰组基本一致。
将有限元计算的法兰屈服荷载和设计荷载进行对比,如表7所示。由于设计值只给出同一组中不等管径法兰对接时的设计荷载,在此对同一法兰组取相同的设计荷载。由表7可知,有限元计算法兰屈服荷载远高于设计荷载,有较大的安全裕度,说明在实际中对于受压荷载作用下的钢管法兰连接,其承载力主要由钢管承载力控制。
表7 法兰受压屈服荷载与设计荷载对比
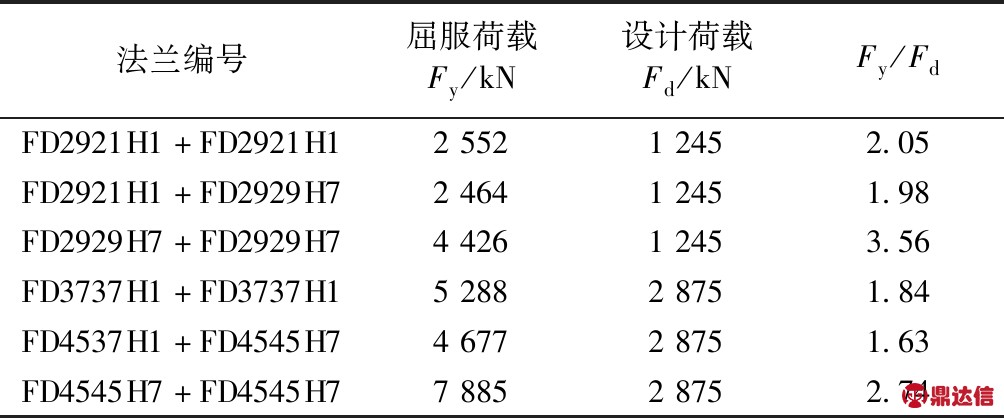
以FD2921H1、FD2929H7法兰组为例,比较FD2921H1+FD2929H7和FD2921H1+FD2921H1,前者的屈服强度较后者并未提高,而法兰FD2929H7+FD2929H7的屈服强度较法兰FD2921H1+FD2921H1明显提高。说明在受压荷载作用下,当采用不等管径法兰连接时,附加弯矩作用的影响不可忽略,受压状态下,带颈锻造法兰由受压为主逐渐转变为受弯为主,导致法兰颈部变坡提前屈服,降低试件的承载力,在设计中应予以重视。
4 结 论
针对特高压钢管塔带颈锻造法兰,开展了不等管径法兰轴心受压和偏心受压试验,并采用有限元软件ABAQUS 6.13对试验试件进行了有限元分析和法兰极限承载力研究。得到以下结论:
1)各组试件的变形形态和破坏机制基本一致,大小管径对接法兰的变形主要集中在小管径一侧。由于连接不等管径的带颈锻造法兰内径不同,在受压过程中整个带颈锻造法兰处于压弯状态,导致法兰盘面处于受拉状态;试件均为小管径钢管靠近刚性法兰加劲肋处鼓曲破坏。
2)受压状态下,试验极限承载力超过承载力设计值35%~54%。试验中未发生法兰和对接焊缝的破坏,表明法兰和焊缝的承载能力能够较好地满足设计要求,且具有较高的安全裕度;偏心受力会一定程度地降低钢管和法兰的承载能力,但影响较小,均在10%以内。
3)在尚未达到承载力设计值时,带颈锻造法兰近焊缝处法兰颈口屈服,且屈服荷载较小,是带颈锻造法兰的最危险点,在设计中应给予加强。
4)受压状态下,对于不等管径法兰连接,带颈锻造法兰由受压为主逐渐转变为受弯为主,导致法兰颈部变坡提前进入屈服,降低试件承载力。