摘 要: 以港口机械配套件精加工车间的设备布局和生产模式为研究对象,针对原生产模式存在的生产周期长、在制品多、搬运距离长、等待时间长等问题,根据生产现场实际运行情况,采取工艺优化、工装升级、快速流动、并行生产、现场管理等多种改进方式,将原先以工序为单位串行加工的车间生产方式,转变成以产品为核心前后工序并行制造的工段制生产方式,大幅提升了生产效率与经济效益。
关键词: 港机配套件加工; 精益生产; 工艺优化; 工段建设
1 引言
港口机械用小型配套件数量多、产品型号多,长期以来,其精加工存在生产效率低、质量问题多、等待浪费较多的状况,迫切需要提升整体加工能力。自2017年以来,通过分析港口机械小型配套件精加工生产现状,根据生产实际引入精益生产理念,采取工艺优化、工装升级、快速流动、并行生产、现场办公等多种改进方式,对现有的生产管理模式进行重组改善,将原先以工序为单位串行加工的车间生产方式,转变成以产品为核心前后工序并行制造的工段制生产方式,生产效率与效益得到有效提升。
2 生产现状调查分析
小型配套件精加工车间主要加工各类减速箱用齿轮、齿轴和小型结构件等产品,产品的加工路线现状见图1。由于车间原布局是按同种类设备集中布局管理的模式,因此在产品加工环节会出现多次跨部门跨车间加工、转运的情况,从而导致了产品生产周期较长、现场在制品过多、转运距离增加等问题。
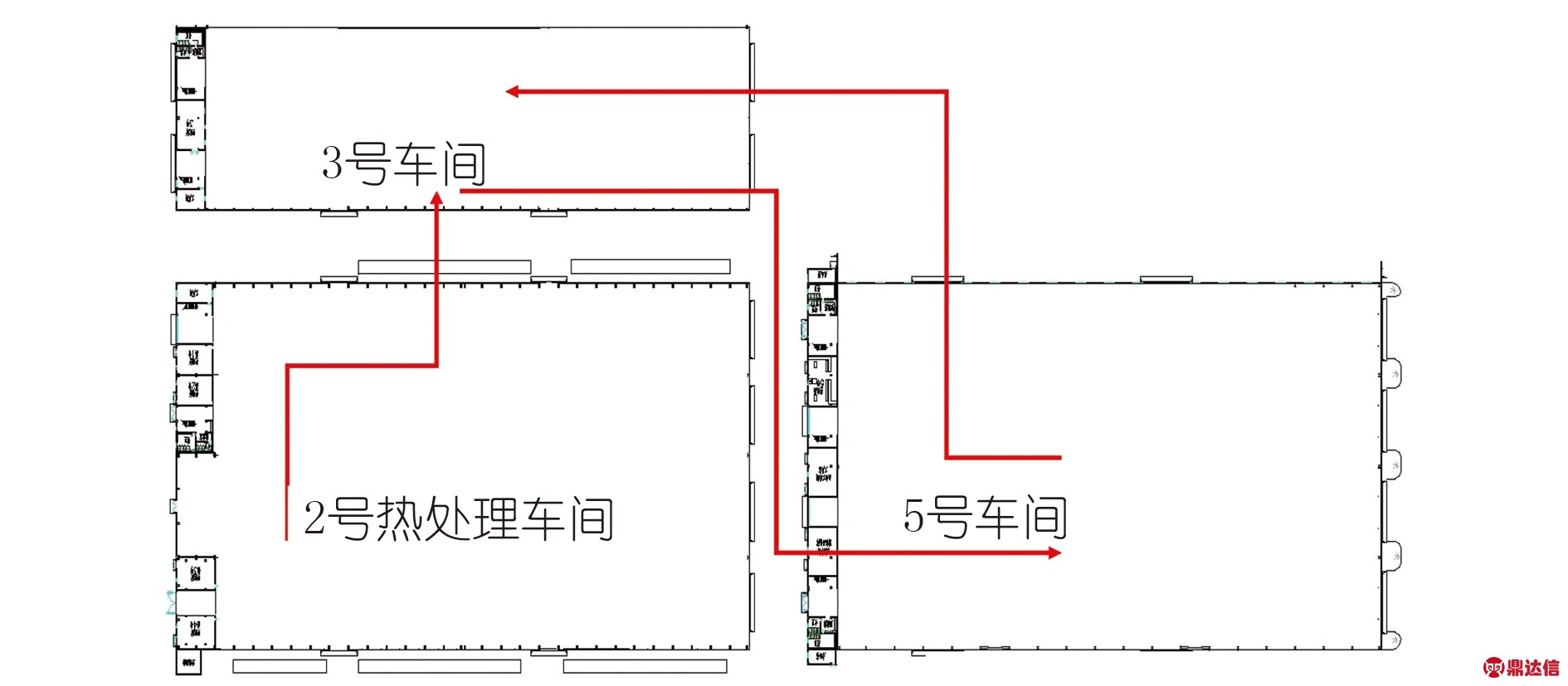
图1 产品加工现状路线图
3 转变生产模式
为了提高效率、缩短产品的生产周期,采取小批量加工和快速流转的方法,对所涉及的主要产品进行工艺路线分解、调整相关设备布局、改变物料转运模式,并对生产计划进行统筹安排。
3.1 优化加工工艺
减速器用齿轴为小件加工车间内主要产品,采用渗碳淬火热处理方式,工件硬度在HRC35~45之间,其热处理后加工工艺为:车3-车4-立铣-钻孔-外磨等5道工序。经研究,采用当前最新硬车加工技术,使用CBN刀具或者陶瓷刀具,在精密车床上对渗碳淬火淬硬钢进行硬车加工,从而达到图纸要求的尺寸精度、形位公差与光洁度要求,同时减少外磨工序。在此理论分析的基础上,分别选择CBN刀具和硬质合金刀具在DMG CTX 310机床上进行实际加工试验,加工效果均较理想,加工表面光洁度可达到Ra0.8,尺寸公差可控制在图纸公差范围内。
经过上述工艺研究与试验验证,对齿轴加工工艺进行优化,采用以车代磨加工方法,钻孔工序在车削中心上直接加工出来。这样优化后减少了2道加工工序,工艺优化为:车3-车4-立铣,生产效率大幅提升。
3.2 调整优化设备布局
对各类产品的加工工艺路径进行统计分析(见表1)。运用ECRS改善四原则进行分析和改善,通过分析、简化工序流程,设备布局优化调整,从而找出更高效的作业方法和作业流程[1]。通过改进,由25台加工设备组成了一段可加工各类减速箱的齿轴、齿轮和小型结构件等产品的小型配套件精加工工段(见图2)。
表1 产品工艺路径统计
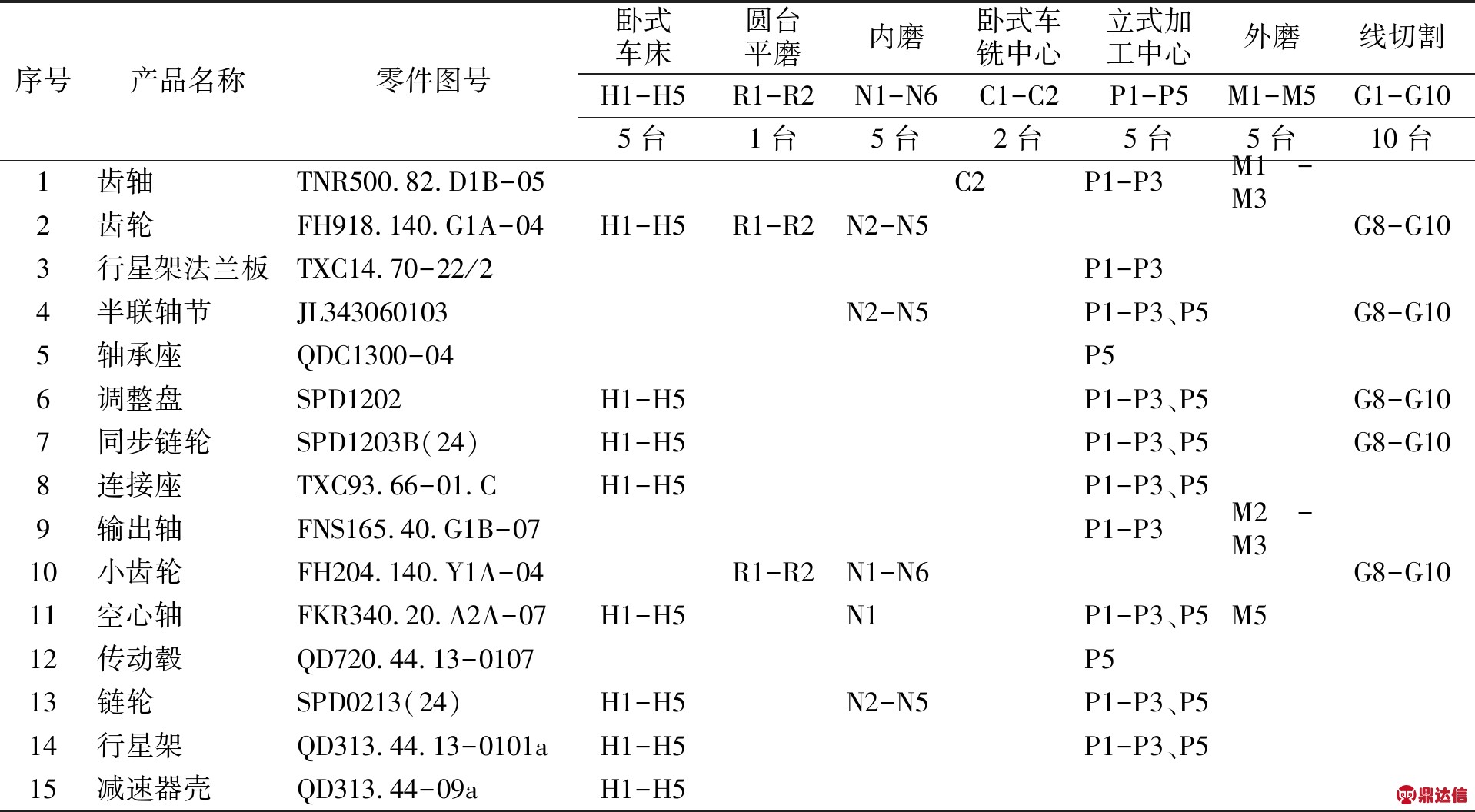
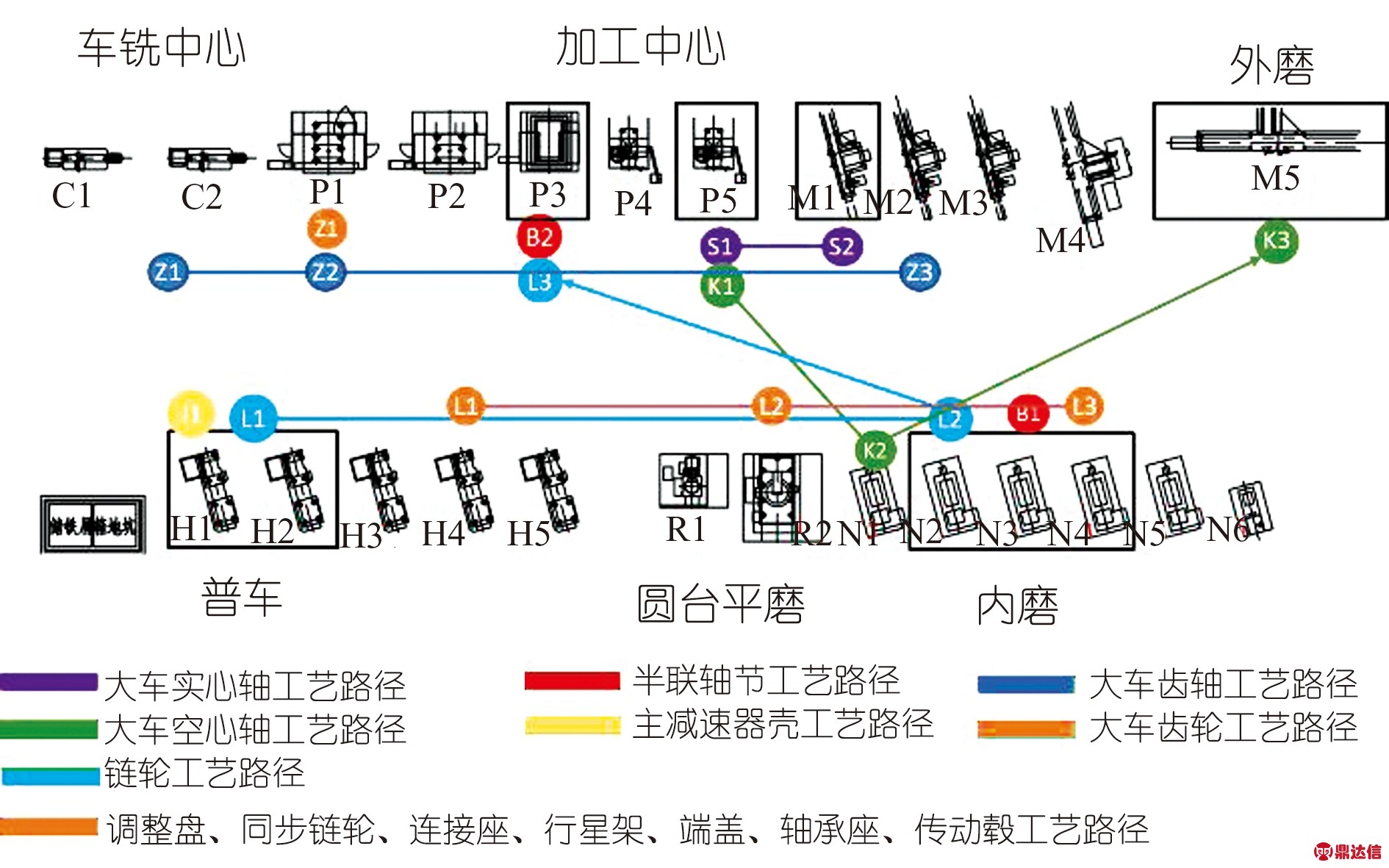
图2 布局调整
3.3 齿轴生产线建设
3.3.1 齿轴加工单元建设
大车齿轴是减速箱的常规组成零件,在热处理后,精加工工段内包含车3-车4-立铣3道工序,如何对3道工序的加工设备进行重新组合,使其能够高效率、高质量的产出,是需要攻克的首要难题。通过对生产零件的工艺路径进行分析,设备布局优化调整后,加工设备以直线型排布,由各个工序完成自己负责的工作后交给下一个工序,形成齿轴精加工小单元。
3.3.2 流动生产
通过收集分析齿轴各工序加工时间,确定生产节拍,在工序间增加自动回转输送线和无动力排辊2种输送工具,使齿轴能够流动生产(见图3)。
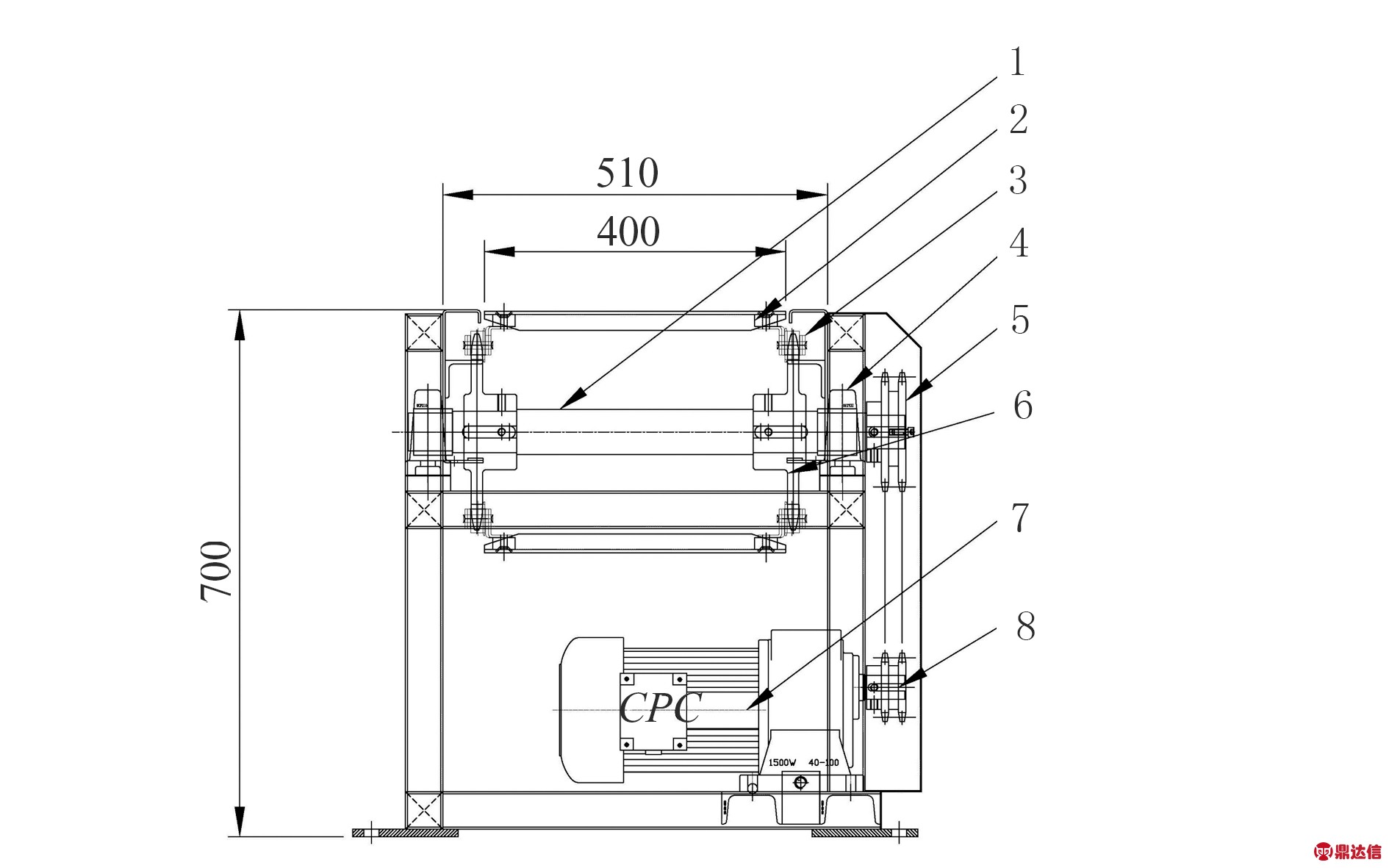
1.驱动轴 2.垫块 3.链板链条 4.哈轴UCP 5.双排链轮 6.链板链轮 7.电机1.5 kW 8.双排链轮
图3 自动回转输送线
3.3.3 产品信息跟踪
为实现工件的信息化跟踪,优化产品质量管理,结合自动回转输送线,在线边增加激光深刻打码机,在轴的端面激光刻录产品信息并形成一个二维码,为产品的数字化跟踪提供基础数据。打码机与输送线之间采用红光感应器信号对接的防错装置,防止在打码过程中输送线突然运动。打码机会在任务结束后给予输送线一个启动信号使其继续运转。在线体末端也设有防错感应器,防止产品还在输送线上的情况下输送线进行回转运动,导致产品掉落线体。
3.3.4 齿轴打码工装
通过之前的产品统计,共有15种尺寸齿轴在此小单元内加工,而打码过程中又需要产品是在相对静止状态下且端面垂直误差小于1 mm,否则会影响打码的效果。经过分析研究进行设计,制作了一套可以快速切换满足单元内各种不同尺寸齿轴放置的工装(见图4)。
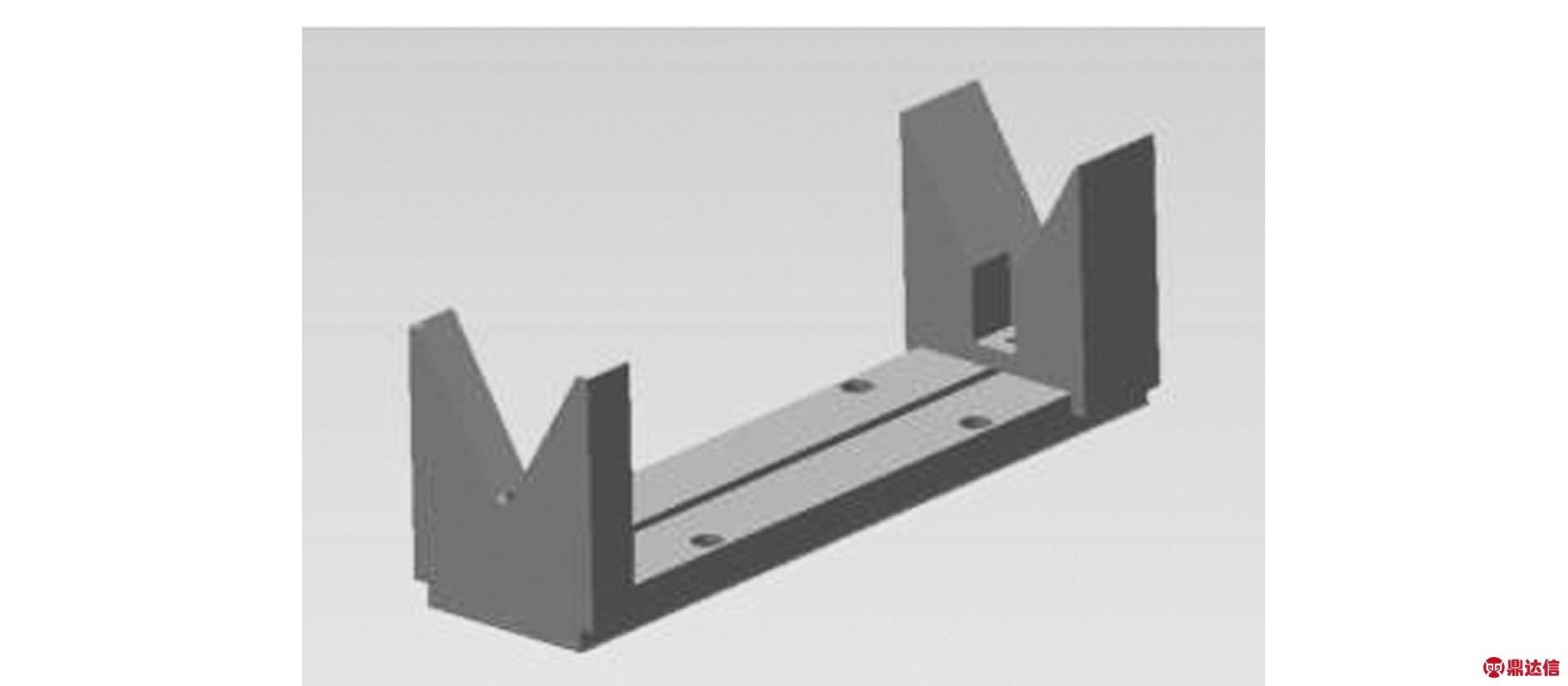
图4 齿轴打码工装
3.4 齿轮生产线建设
3.4.1 齿轮加工单元建设
大车齿轮和齿轴为配套组合件,都是减速箱的常规零件。在热处理后精加工工段内包含车、平磨、内磨3道工序,结合齿轴加工单元建设的经验和小型结构件加工工艺路径,进行布局优化调整后,建设出另一条直线排布的加工小单元(见图2)。
3.4.2 齿轮防划伤工装
齿轮平面经常有划伤现象,经过现场调查分析发现,划伤基本都是在转运及吊装过程中齿轮的面与面直接接触而造成的。对现场的原有转运工装进行现场测量,并制作了配套齿轮防划伤工装(见图5)。
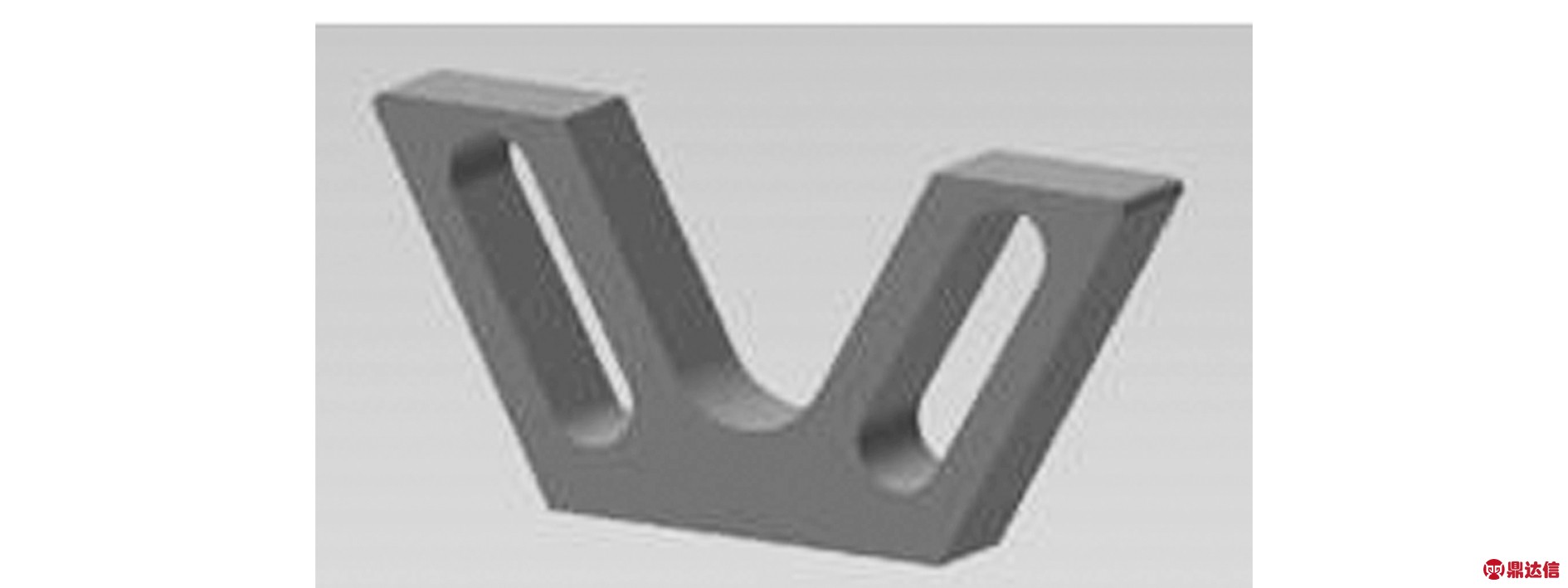
图5 齿轮防划伤工装
3.5 物料转运
3.5.1 AGV物料转运
为实现工段内产品的快速流转,导入AGV自动转运系统,制定相应的AGV系统方案来实现单元间的物料转运(见图6)。AGV通过无线网络与中控系统对接,将各工位的中转命令通过中央控制系统传输给AGV小车执行,从而实现自动化物料快速流转。
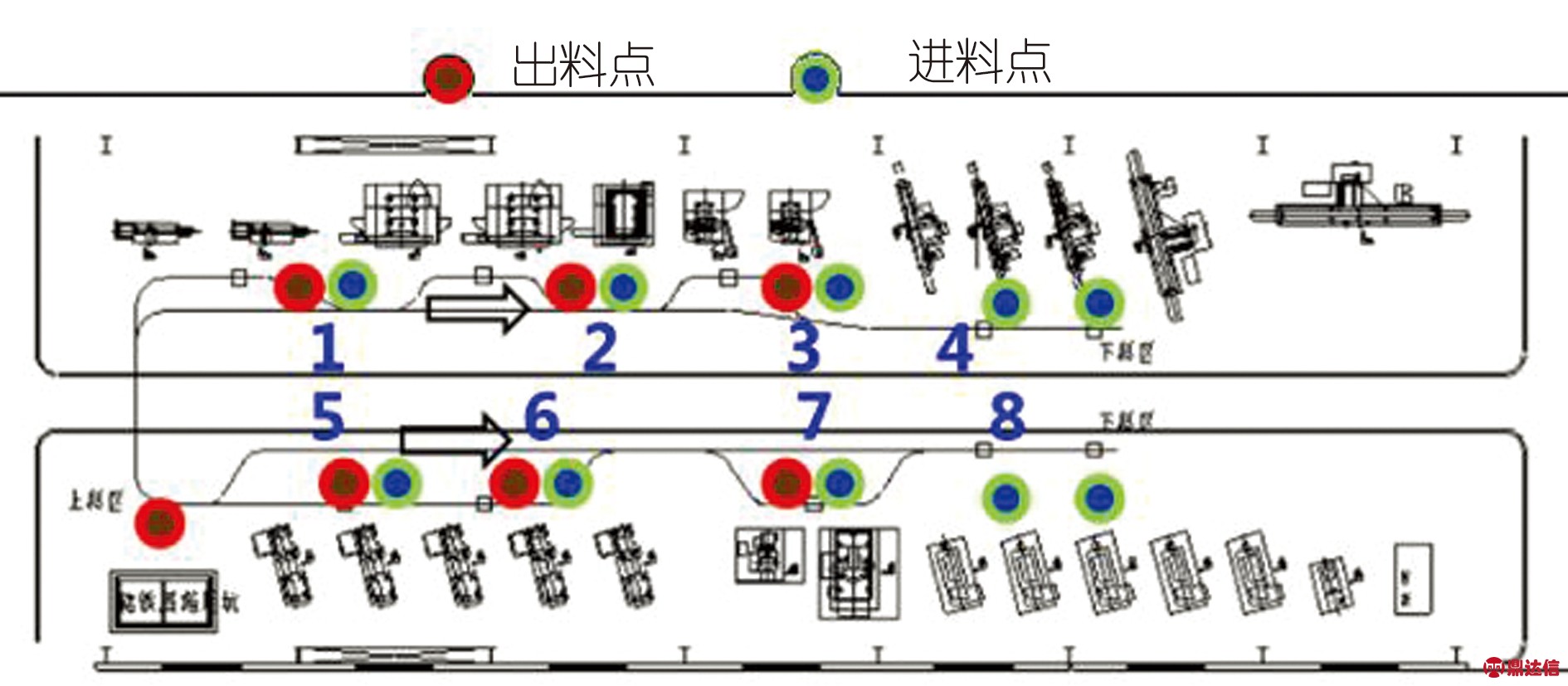
图6 AGV转运方案
3.5.2 AGV转运工装
为了配合AGV的快速流转,制作了相应的转运工装,以满足工段内不同种类的零件摆放转运。以齿轴工装为例,工装采用分体组合式,齿轴放置架采用V型块支撑,可根据齿轴的不同尺寸快速调整到合适位置。工装一次最多可装10件齿轴,实现小批量快速流转,有效避免齿轴在转运过程中造成的磕碰问题(见图7)。
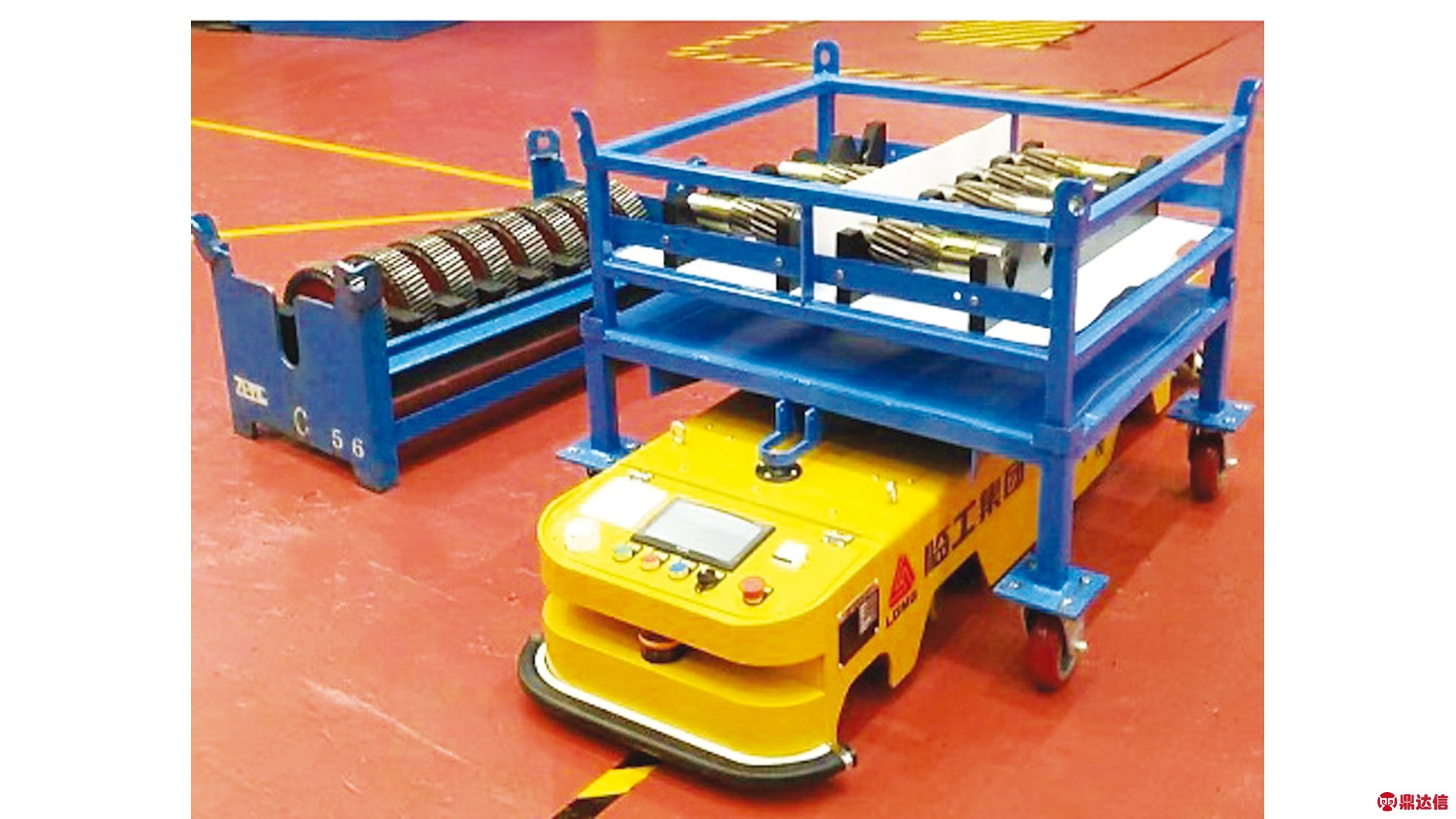
图7 AGV转运工装
4 改革管理模式
4.1 现场办公
车间的高效运转离不开有效的现场管理,车间管理的模式也应该随之改变。为了能够快速响应现场变化,整合区域内项目部管理资源,实行工段管理现场办公,从而第一时间了解现场各种突发状况,提供高效的处理措施,保障现场生产平衡。
4.2 生产计划
结合现场人、机、料等方面合理安排生产,制订生产负荷表,使得生产线能够尽可能地平衡生产。测量收集不同产品的工序加工时间,可预计出设备的每日生产负荷,根据产品生产节点合理调整生产计划,进行平衡生产,从而提升生产线的应变能力,提高生产效率。
4.3 班组建设
加强精益班组建设,在班组建设中设置了质量、安全、效率等模块,并实行一岗双责。每人具体负责一个工序,并对质量、安全、现场、精益、设备等工段内工作进行具体分工。从而做到“大事有人管,小事有落实”。推行“月度之星”评选制度,充分调动员工的主动性和积极性。每月评选出1名工段内明星员工,在各方面表现良好的基础上,根据各层次员工的特色和特长,进行有针对性的表扬和表彰,让所有员工都有积极向上的热情和动力。
5 改变检验模式
该车间原先采用逐道工序检验的方式,即每道工序加工完成后工件均需停止等待检验,检验完成后方可往下流转,导致生产周期长,检验工作量大,漏检情况时有发生。为改变这种状况,在配套件精加工工段内推行“工段制检验”,采用工序首检与工段输出端停止点检验的组合方式。工序首检防止批量质量问题的发生,输出端工件检验把好最终输出关,使得工段内产品质量得到切实保障,同时减少因单工序报验带来的等待浪费,有效地实现了产品的快速流动。
6 结语
经过近1年的改革实践,运用精益生产工具完成了港口机械小型配套件精加工工段建设,将原先以工序为矩阵单位串行加工的车间生产方式,转变成以产品为核心前后工序并行制造的工段制生产方式,生产效率与效益得到了有效提升。小型配套件精加工工段的建设过程,是基于标准化、数字化、精细化、专业化的“四化”管理在港口机械制造领域的应用与探索过程,做到了精益管理与传统制造业的实际无缝贴合,取得了较好的经济效益。