〔摘 要〕某国外矿山大型钢井架总高65 m,结构型式为圆钢管双斜柱钢井架,采用模块化设计技术。本文介绍了钢井架的结构设计和模块化技术全过程,并重点对钢井架的结构选型、模块划分及组装进行了较为详细的阐述。工程应用结果表明,该新型钢井架节约用材,施工简便,具有明显的综合经济效益。
〔关键词〕钢井架;圆钢管斜柱;主体结构设计;模块化分割;模块化安装
井架作为矿山竖井提升的主要构筑物,主要用于支承提升天轮、固定提升套架和承受矿井提升荷重。目前矿山竖井井架一般采用大型箱型体钢结构。传统的井架安装方法:将钢井架划分为主、副斜架吊装单元,采用地面分片组对,使用吊装设备将主、副斜架竖立就位并完成对接,拼接部位高空焊接固定完毕后,再将设备吊运到位进行安装。由于大型箱型钢结构井架构造复杂、用钢量多、焊接工作量大,且加工制作周期长,施工过程中存在对吊装设备要求高、现场焊接质量难以保证、施工措施费用高、安装难度大且精度差等缺点。本文结合具体工程,对传统的双斜撑式钢井架进行截面选型优化,并将模块化技术理念引入到钢井架的设计与施工中,提出一种节约用材、施工简便的新型圆钢管斜柱钢井架。
1 工程概况
某铜矿项目位于土耳其北部卡斯塔莫努区,该矿区属高原区,山峰起伏,钢井架建于海拔1 100 m的高山顶峰,设计年提升量1 500 kt。钢井架总高度为65.0 m,井架底部平面尺寸24 m×36 m,井架沿竖向设7层平台,标高18.0 m为卸载平台;3层罐道平台标高分别为:标高28.50 m、36.0 m,45.0 m;2层天轮平台分别为:下天轮平台标高为51.1 m、上天轮平台标高57.6 m;顶层为天轮安装检修平台,其标高为65.0 m。井架主结构为塔形钢架结构,主斜柱采用圆钢管格构柱,副斜柱采用单圆管钢柱,斜柱基础采用独立基础,钢井架采用欧洲标准规范和中国规范双控方式进行设计。项目的效果图见图1,整体结构三维模型见图2。
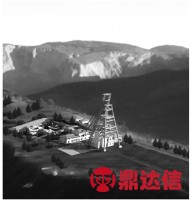
图1 钢井架效果
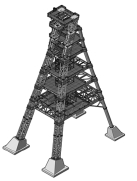
图2 钢井架三维模型
2 主体结构体系
2.1 结构的选型
采用传统的设计思路,将钢井架划分为主、副斜架大型箱型钢结构吊装单元,采用地面分片组对,使用吊装设备将主、副斜架竖立就位并完成对接,拼接部位高空焊接固定完毕后,再将设备吊运到位,进行安装。由于建设场地地处高原,道路狭窄而且坡度大,大型钢构件的现场运输、吊装非常困难,几乎难以实现。
根据现场实际情况,通过理论分析,借鉴冶金矿山模块化建造技术的研究成果,决定采用模块化新型圆钢管斜柱钢井架,结合井架平台的使用功能进行安装模块划分,减少了钢结构件的运输重量和尺寸,预安装部分主要设备,模块间采用螺栓连接,提高了安装精度,大大节约了现场安装工时,降低工程造价。
2.2 结构的型式
钢井架一般分为单斜撑式和双斜撑式两种结构型式。本工程的井架设计具有高度较高、钢丝绳破断力大、抗震设防烈度高等特点。这给井架结构的稳定性、可靠性及顶点位移控制提出了更高的要求,因此主体结构采用较为可靠的双斜撑式钢井架。钢井架工艺平台立面见图3。
2.3 截面选型和材质
由于主斜架承担大部分提升荷载,是井架主要受力构件,所以用钢量所占比重比较大。主斜架为压弯构件,斜架计算长度大,因此通常为稳定控制。这要求斜架柱截面的回转半径比较大,才能满足柱的稳定性。通过与组合箱型截面方案对比,相同力学特性大截面柱,主斜架采用圆钢管格构柱截面可以节省钢材。圆钢管可以工厂加工成型,加工简便,大大减少焊接工作量。圆管单肢构件重量轻,单肢柱圆管现场法兰连接,便于现场安装。主斜柱截面示意见图4。
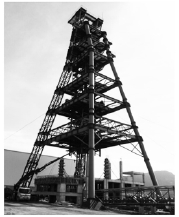
图3 钢井架工艺平台立面
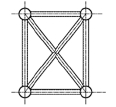
图4 主斜柱截面示意
钢材的采购遵循在满足使用的物理力学性能的前提下就近采购的原则。本工程地处土耳其,现场材料供应为欧标钢材,因此钢井架采用欧洲标准的钢材,主要构件采用S355J2低合金高强度结构钢-20℃冲击韧性的合格保证),支撑、系杆等次要构件采用S355JR。
3 荷载工况及荷载组合
3.1 荷载工况
本工程钢井架计算的荷载取值及荷载组合均严格按照欧洲荷载规范[1]EN1991要求。荷载工况如下:1)永久荷载。天轮设备2台共360 kN,平台楼面恒载取1.0 kN/m2,井架结构自重由程序自动计算。2)可变荷载。平台操作活荷载取5 kN/m2,楼梯活荷载取4 kN/m2,走道活荷载取2.5 kN/m2;提升钢丝绳工作荷载:竖向力1 049 kN,水平力312 kN;卸载装置工作荷载230 kN,主提升、紧急提升罐道绳液压拉紧装置荷载分别为2 240 kN和560 kN,天轮检修起重机起吊重量20 t;风荷载:设计风速为26 m/s。3)偶然荷载。偶然荷载包括断绳荷载和地震荷载。提升钢丝绳断绳荷载:竖向力6 657 kN,水平力1 876 kN。地震荷载:地震基本加速度0.3 g。
3.2 荷载组合
按承载能力极限状态和正常使用极限状态分别进行荷载效应组合,并取各自的最不利的效应组合进行设计。计算主要采用了以下6种荷载组合:1)1.2恒+1.4平台活载+1.3提升工作荷载+1.2钢丝绳罐道荷载+1.4吊车荷载;2)1.2恒+1.4平台活载+0.85×1.3提升工作荷载+0.85×1.2钢丝绳罐道荷载+0.6×1.4吊车荷载+1.4(风);3)1.2恒+0.6×1.2平台活载+1.0断绳荷载+0.85×1.2钢丝绳罐道荷载+0.6×1.4吊车荷载+0.2×1.4(风);4)1.2恒+1.3提升工作荷载+1.0钢丝绳罐道荷载+1.3(地震);5)1.0恒+0.8(1.0平台活载+1.0提升工作荷载+1.0钢丝绳罐道荷载+1.0吊车荷载);6)1.0恒+0.6平台活载+ 1.0提升工作荷载+1.0钢丝绳罐道荷载+0.6吊车荷载+0.2(风)。
4 结构计算及设计
本工程钢井架设计安全等级为二级,应按两种极限状态对结构及构件进行承载力与稳定计算,必要时应进行结构的倾覆及滑移验算,需要控制变形的结构构件还应进行变形验算。井架结构的荷载效应按弹性理论进行分析[2]。钢井架是由平面桁架组成的空间钢结构,对于体形复杂的井架结构应采用空间分析方法进行荷载效应计算[3]。
本工程采用SAP2000通用有限元分析软件建立三维模型对钢井架进行空间分析计算,并按照欧洲钢结构设计规范EN1993[4]对钢构件进行截面设计,并用中国规范进行验算,以两者中较严格的标准进行安全度控制,确保新型结构的安全可靠性能。
5 钢井架的模块化设计
为了适应高原山区的运输条件,提高建造安装效率,节省工程造价,本工程设计进行了进一步研究,分析结果得出采用目前先进的模块化工厂建造技术,可以大大提高效率,合理地进行模块划分,有助于设备安装和吊装。
5.1 模块化分割
模块化工厂建设首先要进行模块化设计,遵循工艺合理性优先原则,根据单元模块功能、重量、几何尺寸进行模块划分,且各模块应具有相对独立功能属性,并符合国际海事组织(IMO)专业的标准和规则,使其能够同时满足设备制造、工艺流程的布置、陆路和海洋运输、模块组装和现场安装的要求[5]。根据钢井架工艺提升方案并考虑运输的要求,主要分割为卸载平台模块、紧急罐笼罐道绳固定平台及紧急罐笼天轮平台模块、主提升罐道绳固定平台模块、下天轮平台模块,上天轮平台模块、天轮安装检修平台模块,共6大模块。由于卸载平台模块空间尺寸较大,超出公路运输尺寸要求,因此需将该模块继续分割成若干个子模块。模块化的井架强调设备与钢平台高度集成,各模块由钢平台结构与钢平台上的工艺设备组成并具有相对独立功能。例如:天轮平台模块是由天轮和支承天轮设备的钢平台组合,卸载平台模块是由卸料设备和支承卸料设备的钢平台组合而成;其它辅助钢平台由工厂加工并以散件形式运输至现场进行地面组装。钢井架模块划分示意见图5。钢井架完工实景见图6。
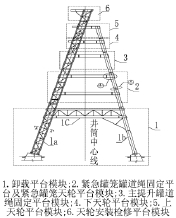
图5 钢井架模块划分
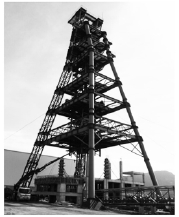
图6 钢井架完工实景
5.2 模块化梁、柱典型节点设计
各模块的主副斜柱、主梁的拼接均采用等强度设计原则。主副斜柱拼接点不仅要求强度连续性,而且要求抗弯刚度的连续性。法兰连接具有便于连接、刚度大、承载力高、柱截面尺寸适用范围广等优点。本工程柱拼接采用加劲肋法兰连接,由于设置了加劲肋,刚度大、承载力高、变形小,可以减小法兰板厚度。梁柱刚接采用带悬臂段的短牛腿,牛腿与主梁的翼缘、腹板两侧加连接板完全采用高强螺栓连接,可减少工厂焊接工作量,加快各模块工厂预组装的进度,悬臂段端部的外加强环较大的提高梁柱节点抗弯承载力。圆管柱拼接大样详见图7,主梁拼接大样详见图8。
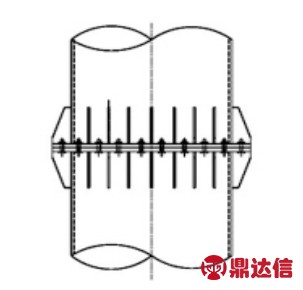
图7 钢斜柱法兰拼接
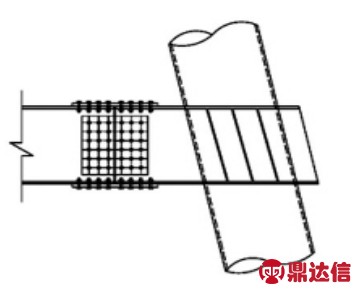
图8 主梁拼接
6 模块的制作、安装
6大模块及其子模块分别由制造厂完成制作,并将相应的设备根据设计安装在对应的模块上,然后整体运输至现场;其它辅助钢平台构件由工厂加工,并以散件形式运输至现场;现场地面进行卸载平台各子模块和辅助平台组装;钢井架的模块化安装采用搭积木式安装模式,由下至上将模块依次吊装就位,通过钢斜柱法兰拼接安装固定。
7 结语
通过钢井架进行截面选型优化,采用圆钢管格构主斜柱和型钢组合的桁架大跨度梁替换传统钢井架设计的箱型截面,即以圆钢管空间单元结构体系代替传统的大型箱型钢结构平面单元拼装结构体系,可以节省钢材,加工简便,大大减少焊接工作量;采用模块化设计与施工技术,使钢井架实现集成化、模块化,很好地解决了大型钢构件运输、吊装难题,可进行设备预安装,减少了钢井架结构及提升设备安装所需的大量现场人工时,缩短了现场安装工期,提高了安装精度,降低了安装成本。该项技术创新已经成功地申请了国家专利,具有良好的应用前景。