摘要:随着电力电子行业的飞速发展,新型电磁材料的投入使用,对电子元器件的高频磁性能提出了新的要求。磁芯作为电子元器件的核心部件,其发展程度直接决定电子元器件的性能,这就要求具有优异高频软磁性能的材料发展。本文综述了四种软磁材料的发展历程,对每种软磁材料的优缺点进行了归纳总结,同时指出了未来的发展方向,并重点对近年来研究热门的软磁复合材料进行了梳理。粒径大小可控、包覆层对核层的包覆均匀程度以及从实验室走向产业化的大批量制备方法是未来高频软磁复合材料的发展趋势。
关键词:电力电子;软磁材料;高频低损;低矫顽力
电力电子行业的飞速发展,大至高压输电,以变压器为核心的输变电系统;小至电子元器件,以电感、电子变压器为核心的电力电子变频设备,即微电子领域,都面临着高频率、高功率转换、高能流密度的挑战,而这都离不开其关键因素—软磁材料的发展[1-3]。高频软磁材料是制造大功率变压器、电感、电子变压器等器件的主要成分,因此高频软磁材料的发展水平直接决定电力电子领域的发展进程。
软磁材料由于具有低矫顽力、低剩磁、高饱和磁化强度等优点,被广泛用于电力电子行业中[4]。电感、电子变压器等器件作为电力电子变频设备中的核心部件,高磁导率、高频低磁损是未来的发展趋势,因此长期以来国内外的专家学者一直在为提高电磁元器件的能流密度、减小部件尺寸和质量、提高材料的饱和磁化强度、降低高频下的涡流损耗而努力[5,6],包括器件结构上的创新和材料成分上的创新。例如变压器,采用层状硅钢材料,而不是一整块铁芯,就是从结构上提高高频使用性能的代表;后期科研工作者又从材料本身创新,从最早的金属基材料,到铁氧体、非晶纳米晶,再到现在的软磁复合材料,性能由低到高,成分由简单到复杂,已经发展成为多种类的软磁材料体系,为现代工程技术的发展提供了强有力的支撑[7,8]。
几种软磁材料的应用背景不尽相同,在各自的领域各司其职,如硅钢主要应用于变压器和驱动电机的核心部件;铁氧体主要应用于开关电源以及电源适配器中的电感、滤波器等元件;非晶纳米晶和软磁复合材料虽然发展较晚,但是有望取代甚至已经部分取代传统软磁材料。不过作为软磁材料体系,都是朝着高频低损耗、高磁导率、高能流密度的方向发展[9,10],因此提高软磁材料的高频性能、降低高频应用背景下的损耗成为近年来软磁材料的研究热点。
例如器件高频应用情况下的涡流损耗(We),正常工作情况下,磁损可分为磁滞损耗(Wh)和涡流损耗(We),其中Wh=f∮HdB[11],也可以表达为Wh=kAf[12],A代表磁滞回线的面积,二者表达意义相同,We=CB2f2d2/ρ[11],因此材料在正常工作频率下,磁损可表述为:
W=Wh+We=f∮HdB+CB2f2d2/ρ
(1)
从式(1)中可以看出,磁滞损耗与f成正比,涡流损耗与f的平方呈正比,因此在中高频下,材料的涡流损耗将逐渐主导能量传输损耗的大小。试举一例:当电子器件工作频率从1kHz提高到100kHz时,理论上,Wh将提高100倍,而We则提高到了10000倍,因此对于高频应用的磁芯来说,降低磁芯材料的涡流损耗至关重要。由公式(1)得出,涡流损耗与材料的电阻率成反比,因此通常采用提高电阻率的方法来降低材料的涡流损耗,软磁复合材料的诞生主要源于此方面的原因,国内外的科研工作者也通过各种途径在尽可能少地影响磁导率的情况下,把提高软磁复合材料的电阻率作为研究重点,具体实施方式为制备核壳结构的软磁复合材料,该结构是以磁粉作为核,有机和无机的绝缘添加物作为壳,构成复合材料体系,近年来此方面的研究引起了国内外学者的广泛兴趣[4,13]。
1 软磁材料的研究进展
尽管四种软磁材料的出现顺序不同,近年来的受重视程度也有区别,但每种材料的存在各有千秋,表1列出了四种常见软磁材料目前主要存在的优缺点。
表1 四种软磁材料的主要优缺点
Table 1 Advantages and disadvantages of four types of soft magnetic materials
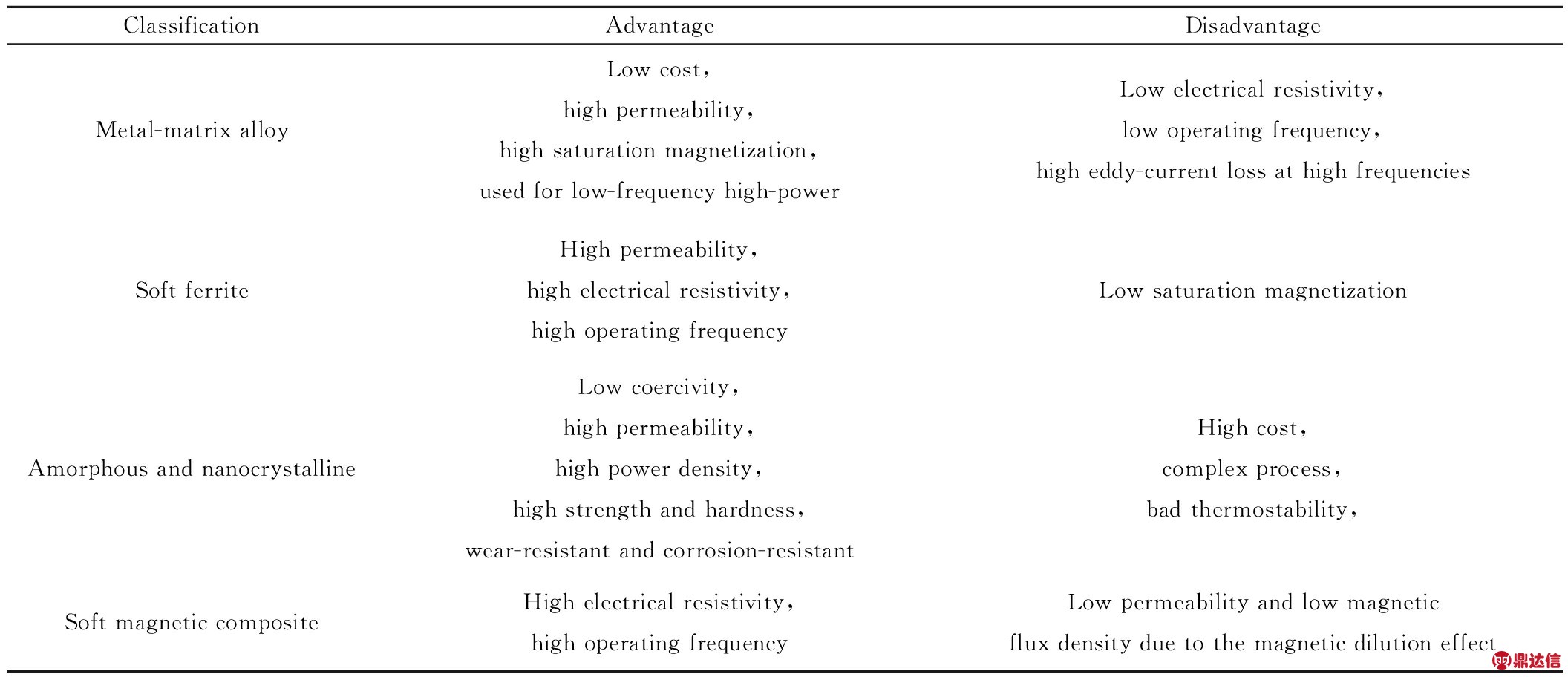
1.1 金属基材料
软磁材料的发展就是从纯铁开始的,1823年斯特金制造的第一块简易电磁铁,标志着软磁材料的诞生。起初,人们使用铁含量在99.5%以上的优质钢作为磁体,此种材料具有较高的饱和磁感应强度,但是纯铁电阻率低,矫顽力也较大,限制了它的使用范围,一般只在直流状态下使用。随着科技的发展以及对材料性能要求的提高,人们逐渐在铁中加入其他元素,从最早的Fe-Si系、Fe-Co系、Fe-Ni系二元合金发展为后来的Fe-Ni-Co系、Fe-Si-B系等多元合金[14-16]。1902年Barrett等[16]通过在体系中添加Si,并在气氛保护下,经长时间高温退火,改善了热轧钢的磁性能,并于1903年美国投入生产。后来随着冷轧技术的发展,人们通过冷轧工艺研究出来有特定取向的硅钢,这种双取向硅钢大大提高了硅钢片的磁性能[14]。后期科研工作者又研究出FeCo合金,相较于纯Fe、Fe-Si系合金,FeCo合金具有更高的居里温度(Tc>940℃),更高的饱和磁感应强度(Bs>2.0 T),但是由于FeCo合金涡流损耗较高,只适合在直流和低频下使用[15]。因此后来又出现了Fe-Al系、Fe-Ni系等二元合金,直到后来的Fe-Ni-Co系、Fe-Si-B三元合金,甚至后来的多元合金[17]。这些合金通过不断改善加工工艺,提高了材料的综合软磁性能。直到现在关于金属基软磁材料的研究仍在继续,例如:新能源汽车在石油能源日益枯竭以及环境的日益恶化的大背景下成为未来汽车的发展趋势,其电机驱动系统是新能源汽车的三大核心部件之一,汽车的电机驱动系统要求体积小、高能流密度以及高的可靠性等,因此无取向硅钢成为电机系统的核心部件,这一关键材料我国尚不能工业化生产[18]。日本在这一方面处于垄断地位,其中新日铁、住友金属在这方面投入了大量研究,近年来也申请了很多专利,在保证高饱和磁感应强度的同时,主要通过固溶强化[19,20]、析晶强化[21,22]等提高电工钢的强度以满足汽车驱动电机的需求。孙乃坤等[23]研究了B掺杂对SmFe10Mo2合金的相结构和磁性能的影响,结果表明,掺杂B后,合金相的结构保持不变,居里温度由270℃提高到334℃,显著提高了合金的使用温度。随着电力电子领域对软磁材料器件小型化、轻量化、高频化要求的提高,科研人员在金属基软磁材料的成分组成、晶粒尺寸大小等方面开展了大量的研究,从而导致组成成分较为多元的、性能优良的细晶金属基软磁材料飞速发展。由于金属材料的低居里温度、低电阻率等特征,提高金属基软磁材料的使用温度,降低高频下的涡流损耗是金属基软磁材料未来的发展方向。
1.2 软磁铁氧体
软磁铁氧体最早是由荷兰实验室的Snoek于1935年研制成功[24],其相比金属基材料具有更大的电阻率,更低的高频涡流损耗,因此在高频情况下得以广泛应用。软磁铁氧体按晶体结构可分为立方晶系的尖晶石型(适于低频、中频和高频)和六角晶系的磁铅石型(适于特高频,可达2GHz)[25]。常见的软磁铁氧体材料有Mg-Zn,Cu-Zn,Ni-Zn,Mn-Zn等系列,其中,Mn-Zn铁氧体的产量和用量最大[26,27]。20世纪50~80年代是软磁铁氧体发展的黄金时代,占据了除电力工业之外的各个领域。我国在20世纪50年代才开始软磁铁氧体材料的研发与应用,由于当时技术与发达国家差距较大,整个60年代材料的性能以及制备工艺都是很缓慢的。到了70年代,实验室已经能够研制出磁导率为10000的高磁导率铁氧体材料,80年代,由于彩色电视机的迅猛发展,对电源滤波器的要求较高,不少企业开始投入大量的研究,已经开发出初始磁导率5000的铁氧体材料[28]。尽管软磁铁氧体的电阻率高,在高频下的涡流损耗较小,但是Bs仅为金属基软磁材料的1/4左右,因此,各国科研工作者和企业都投入了大量的物力和人力,通过调节烧结气氛,控制烧结工艺以及稀土等微量元素的掺杂等来提高软磁铁氧体的性能[29,30]。陆国权小组[31]研究了Bi2O3掺杂NiCuZn铁氧体,并控制其烧结温度对磁性能的影响,结果表明:烧结温度低时,不利于提高器件的密度,因此导致较低的磁导率,当烧结温度为1000℃时,材料磁导率升高,能量损耗密度也达到最低。张兴凯等[30]用溶胶-凝胶自燃烧法研究了镧掺杂对钡铁氧体纳米粉体的影响,得出镧掺杂对后续热处理过程中的晶粒长大有抑制作用,对于合成的产物颗粒大小有一定的细化作用,且在较高的热处理温度下更为明显,进而影响粉体的磁性能;随镧掺杂量的提高,获得纯相铁氧体粉体的温度也随之升高。马玉启等[32]研究了Sn4+取代对NiZn功率铁氧体磁性能的影响,结果表明:随Sn4+取代量的增加,晶格常数逐渐增大,但是晶粒尺寸变化不大,饱和磁通密度Bs逐渐下降,起始磁导率μi先上升后下降,功率损耗Pcv的变化则与μi相反。当Sn4+取代量为0.04时,NiZn功率铁氧体具有较高的起始磁导率和较低的功率损耗,且功率损耗随温度的上升而降低,因此适于使用温度较高的电源变压器功率磁芯使用。近年来,随着电子产品向超薄微型化发展,对软磁铁氧体提出了更小体积、更高功效的要求,其核心问题就是控制材料的显微结构,采用纳米级尺度的添加物粉体代替原微米尺寸的粉体,有利于更好地控制晶粒尺寸,进而可以制备出密度高、晶粒细小均匀的纳米材料,因此纳米级软磁铁氧体材料的制备成为国际研究的热点。
1.3 非晶/纳米晶
1.3.1 非晶
非晶态磁性材料由于具有短程有序、长程无序的特点,不具有磁晶各向异性,因此相比于铁氧体材料具有高磁导率和低矫顽力等优良的综合软磁性能。1967年美国加州理工学院的Duwez学者从液相中快速淬火,得到Fe75-P15-C10非晶合金[33],从此开启了人们对非晶合金的研究。随着非晶制备技术的发展以及对非晶软磁性能的认识,Fe-Co基非晶合金逐渐得到了人们的关注,起初研究者在Fe-Co二元晶态合金中添加20%(摩尔分数)不同配比的Si,B,C,P等类金属非磁性元素,来提高非晶合金的形成能力,从而研制出了Fe-Co基非晶软磁材料,Fe-Co基非晶合金具有Fe基非晶合金高的Bs和Co基非晶合金接近于0的磁致伸缩系数,磁导率和居里温度也较Fe基非晶高等优点[34,35]。此外非晶合金还具有非常高的机械强度,早在2004年,日本的Inoue课题组就通过调节各组分的含量,FeCoBSiNb体系的断裂强度就超过了4000 MPa[36]。2001年,赵玉华等[37]研究了退火温度对CoFeNbSiB体系的磁性能的影响,结果表明:当退火温度(Ta)低于470℃时,合金具有很好的软磁性能;当Ta提高到540~560℃时,矫顽力明显增加,在弱场下的磁化强度变得很低,软磁性能明显下降;当继续提高退火温度,Ta高于580℃时,开始向晶态转变,有Co-B,Fe-B及其化合物析出,磁性反而有所改善。但由于非晶合金中需要添加非磁性的类金属元素以提高非晶形成能力,因此一般非晶合金的Bs比晶态的低。另外由于非晶合金处于非平衡态,在较高的温度下有向晶态转变的趋势,因此提高非晶合金的高温稳定性是非晶合金的发展趋势。日本著名科学家Inoue在非晶软磁材料领域具有很高的造诣,直到现在还在开展相关方面的研究[35,38,39]。
1.3.2 纳米晶
1988年日本学者Yamauchi通过在Fe-Si-B合金体系中添加Cu和Nb两种元素,在超过体系晶化温度以上,通过热处理,得到了10nm左右的FeSiBCuNb(FINEMET)纳米晶材料[15],FINEMET比Fe基非晶合金具有低的磁致伸缩系数,低于Fe基非晶合金和Mn-Zn铁氧体材料的能量损耗,因此受到了科研工作者极大的关注。但由于Fe基纳米晶低的居里温度(Tc<300℃),2001年,Laughlin小组[40]用Co代替FeZrBCu非晶合金(NANOPERM)中的部分Fe,得到了非晶和纳米晶共存的FeCoZrBCu合金(HITPERM),HITPERM典型的组成成分为Fe44Co44-Zr7B4Cu,Bs可达到2T,居里温度约为960℃,提高了材料的高温稳定性。2014年,浙江大学的熊亚东等[41]采用熔体快淬法先制备出Fe73.5CuNb3Si13.5B9非晶条带,然后通过高能球磨打碎成磁粉,在磷酸溶液中进行钝化,最后在1.64~1.96GPa压力下压制成磁环,并经过500℃退火处理以消除应力,制备出了晶粒大小为14.3nm的非晶和纳米晶两相共存的合金。测试结果表明:合金呈现出了优良的磁性能,在100 kHz,0.1T测试条件下,能量损耗密度为583 mW/cm3。
20世纪90年代后期,非晶和纳米晶软磁材料逐渐成为软磁铁氧体的竞争对手,其在性能上远优于铁氧体,可以说非晶纳米晶材料的出现为软磁材料增添了高性能的新材料。但是在制备成本上相比于铁氧体还处于劣势,因此在中低端市场上竞争力不如软磁铁氧体,但是在高技术领域已经开始崭露头角。如今解决非晶合金的高温稳定性,抑制纳米晶的晶粒长大,降低生产成本,提高非晶纳米晶材料的产量是当前制备非晶纳米晶材料面临的问题。
1.4 软磁复合材料
为了进一步提高使用频率,综合改善软磁材料的性能,软磁复合材料应运而生。软磁复合材料(Soft Magnetic Composites, SMCs)是一种在磁性粉末表面包裹一层绝缘介质的磁性材料。包裹这层绝缘介质的目的是增加材料的电阻,在高频应用背景下,降低材料的涡流损耗;另外对于一些纳米级甚至亚微米级的易氧化的材料,还能起到防氧化的作用,同时也能提高材料的常温甚至高温稳定性。软磁复合材料多以核壳结构居多,结构示意图如图1所示,其中核的成分主要是金属合金,壳的成分既可以是无机的也可以是有机的,既可以是磁性的也可以是非磁性的。无机的主要包括等氧化物和磷酸盐类,此外还有研究工作者在磁性合金表面包覆一层磁性的铁氧体[50],以弥补非磁性壳引起的饱和磁感应强度的损失;有机包覆主要以热固性材料为主,包括环氧树脂,丙烯酸树脂和聚氨酯类等[4]。早期的SMCs就是铁-树脂材料,但由于树脂耐高温性差,玻璃化转变温度较低,易发生软化,不适于高温热处理。后期人们又研究用氧化物、磷酸盐等耐高温的无机材料包覆[29]。
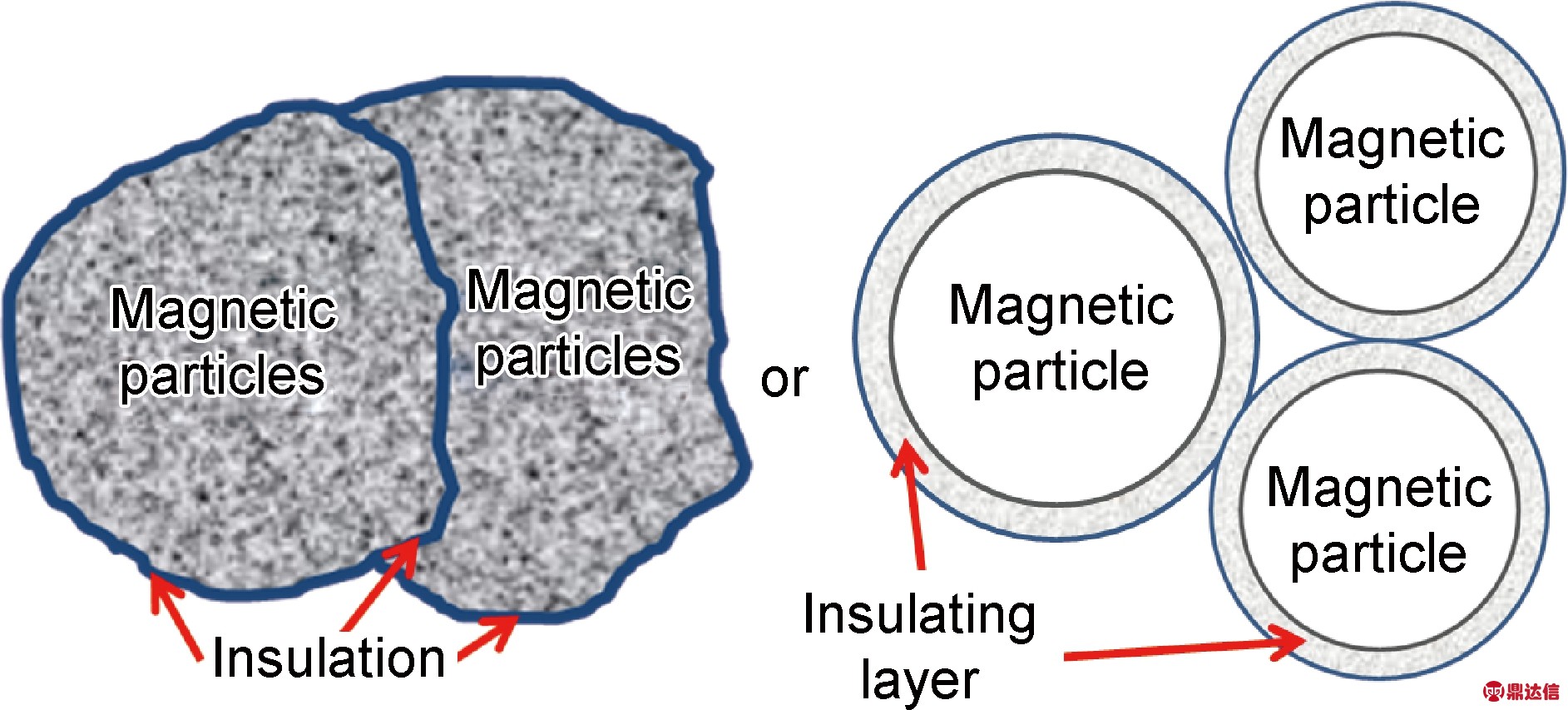
图1 软磁复合材料结构示意图
Fig.1 A schematic diagram of the component elements of a powder core
有机包覆方面,陆国权小组[51]将苯并环丁烯(BCB)溶解在甲苯和丙酮组成的溶剂中,对坡莫合金进行包覆,经过脱溶、烘干步骤,得到核壳结构的复合材料粉末,将粉末成型固化得到磁环,最后对得到的磁环进行复数磁导率和能量损耗密度等磁性能测试。结果表明,相对于纯坡莫合金粉末,合金粉占84%(体积分数)的复合材料,应用频率至少在10MHz时仍然保持较好的磁性能,而纯粉末在1MHz时,磁性能就已经开始下降,应用频率至少提高了10倍。能量损耗密度测试结果表明,在5MHz,9mT测试情况下,能量损耗密度为300mW/cm3,而纯坡莫合金在5MHz,1mT的情况下,能量损耗密度值就已经达到了300mW/cm3,结果如图2所示。此种方法制备的优点是操作简单,相比于化学制备方法而言,一次可以制备的量较大。此外BCB的玻璃化转变温度高达350℃,因此可以满足绝大多数日常使用的电源适配器、功率转换器等。
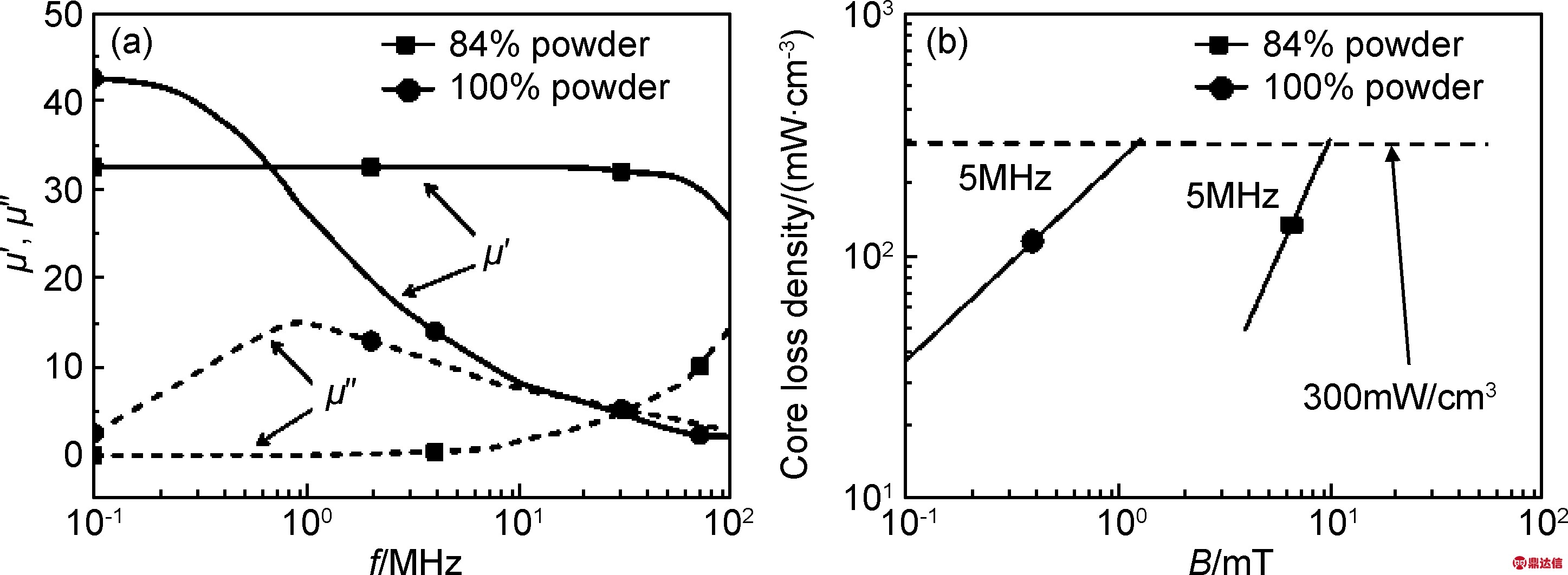
图2 纯坡莫合金与84%复合材料的复数磁导率(a)和功率损耗密度对比(b)[51]
Fig.2 Complex permeabilities (a) and core loss densities (b) for pure permalloy core, 84% permalloy + BCB composite[51]
无机包覆方面,南京大学的钟伟等[43]研究用溶胶凝胶联合高温氢气还原的方法制备Fe-SiO2复合材料,制备的Fe核粒径大小为5~10nm,SiO2壳的厚度为0.5nm。复数磁导率测试结果表明,在1GHz时,材料的磁导率实部(μ′)仍然保持稳定,虚部(μ″)仍然保持在一个很低的数值,有效地降低了材料的涡流损耗,提高了使用频率。
Liu等[46]也是采用溶胶凝胶的方法制备FeNi3-Al2O3复合材料,通过调节Al3+的浓度来控制Al2O3层的厚度,结果表明,当Al3+摩尔分数为20%,在1GHz时,磁导率实部(μ′)仍高达12,虚部(μ″)仍保持在很低的数值,显著提高了材料的使用频率。
长春工业大学的昝朝等[28]则是研究了Fe基微胞结构的软磁复合材料,制备过程主要分为两个阶段,包覆过程和放电等离子烧结过程(SPS),选择高饱和磁感应强度的Fe-6.5Si微米粉为核,高电阻率的Ni0.5-Zn0.5Fe2O4为壳,通过SPS烧结,在烧结温度480℃和烧结压力600MPa条件下制备的金属-陶瓷微胞结构的块状软磁材料Fe-6.5Si/Ni0.5Zn0.5Fe2O4,电阻率达到了1.679×104μΩ·mm,饱和磁感应强度达到1.505T,总损耗为23.39W/kg,为后续开发其他微胞结构的材料提供了参考依据。
软磁复合材料相比非晶纳米晶具有较高的电阻,相比于铁氧体又有更高的饱和磁化强度,因此制作的器件体积可以更小,在一些应用范围内可以取代铁氧体,其市场需求量也日益增长[52]。但当前包覆层的添加量以及包覆厚度、均匀程度是软磁复合材料面临的主要问题,因为包覆层的添加量过多势必会引起整体饱和磁感应强度的降低,太少又不能有效地起到降低涡流损耗的作用;此外目前软磁复合材料的制备主要集中在溶胶凝胶法、水热法等化学研究阶段,还不能大量生产,因此大批量高效的制备方法、粒径大小可控、包覆层厚度均匀等是未来软磁复合材料需要解决的问题。
2 应用及发展
近年来,电力电子用高频电感器、功率转换器、大功率变压器等器件设备得到了广泛应用,然而在飞速发展的同时,也遇到了很多问题,尤其是高频应用面临的涡流损耗问题,亟须高电阻率、高能流密度、低磁损、低矫顽力的软磁材料发展。目前以硅钢为代表的金属基软磁材料主要应用于高功率变压器,新能源的电机系统等,变压器中面临的主要是硅钢的高频涡流损耗问题;驱动电机系统则需要硅钢的高强度来保证高的转矩以应对复杂工况,同时还要保证高的μi提高能量转化率和效率,因此增加电阻率以降低变压器的能量损失;提高机械强度的同时也提高磁导率以增加电机驱动系统的高转换效率是未来的发展趋势,主要通过热处理(包括激光退火)、制备多元合金、固溶,析晶强化以及细化晶粒等手段对金属基软磁材料进行磁性能和力学性能的改性。软磁铁氧体根据种类不同,主要应用于以通讯设备和宽、低频变压器为代表的电子产品和以高频开关电源为代表的电子元器件,前者要求具有高的磁导率(μi>10000),高频开关电源的发展趋势则是体积小、质量轻以及高频段,因此进一步提高磁导率、提高和加宽工作频率、降低损耗、满足宽温区间和微型化是未来的发展目标,主要通过元素掺杂和Ca,Si,Ta,Nb等氧化物的添加,提高晶界电阻的同时细化晶粒,以及采用纳米级的添加物粉体对晶界显微结构的控制等手段对铁氧体性能进行改进。非晶纳米晶材料由于高电阻率、高磁导率、低矫顽力等特征,是高频变压器、互感器的理想材料,成为软磁材料的又一发展方向和热点,也是坡莫合金和铁氧体的换代产品。用非晶纳米晶制成的器件具有质量轻、体积小、磁性能好等优点,在诸多领域有着广泛的应有前景,尤其体现在高技术领域,但由于制备技术限制导致成本较高,热稳定性欠佳,因此提高高温稳定性、降低制备成本是亟待解决的问题,目前主要采用掺杂非磁类元素提高非晶的成形能力以及采用不同的热处理工艺提高非晶纳米晶的磁性能。软磁复合材料由于具有比非晶纳米晶更高的电阻,比铁氧体更高的饱和磁感应强度,在最近十几年取得了相当大的进展。其结构大多以核壳结构居多,欧洲、美国、澳大利亚等一些发达国家已经用软磁复合材料来研究电机系统,发展前景极好。当前软磁复合材料主要面临两大问题:一是包覆层的添加量以及厚度和均匀程度,因为添加量和包覆均匀程度都会对材料的磁性能构成影响,并进一步影响成品的性能;二是大批量的高效制备方法。因此开发更多高效大批量的制备方法、核壳层的尺寸等显微结构和控制包覆层的厚度和均匀程度是软磁复合材料研究的主要目标。
3 结束语
由于衡量磁性材料性能的参数比较多,抛开力学性能仅就磁性能而言,就包括磁导率、饱和磁化强度、矫顽力、高频情况下的复数磁导率以及功率损耗等,因此在实际使用中需要全面权衡软磁材料的成本、综合磁性能等因素而选择合适的材料,所以尽管金属基软磁材料发现最早,但仍然占据自己的一席之地,其余三种软磁材料在各自的领域也各司其职。
金属基、非晶纳米晶以及铁氧体三种软磁材料发展时期较长,研究也更为成熟,因此若想在这方面有大的创新就变得比较困难,与几十年前相比,成分和工艺的创新已经变得缓慢很多。而发展最晚的软磁复合材料由于其优秀的高频性能,近年来吸引了各国科研工作者大量的研究。因为软磁复合材料至少包括核和壳两种不同的成分,研究方法也包括种类繁多的化学法和物理法,因此在这方面呈现了广阔的研究前景。尤其是近年来飞速发展的电力电子业对高频化的特殊要求,正迎来了软磁复合材料发展的新契机,但也正是因为其复杂的结构,想实现包覆层对核层的均匀包覆以及从实验室走向产业化的大批量制备方法还需共同努力。