摘 要:目前对带子系统的动力包双层隔振系统的隔振设计尚未形成一套行之有效的设计方法,针对这一研究现状展开了对其隔振设计的研究。提出了一种先优化设计主隔振系统确定一、二级隔振器刚度,然后将子系统充当主系统吸振器按照H∞准则设计出子系统隔振器刚度的两级优化设计方法。以某型内燃动车动力包为研究对象,采用提出的两级优化设计方法对动力包进行优化设计,并基于优化后的参数对动力包进行了隔振性能测试。结果表明,经过优化后,在常规工况和停机工况,动力包双层隔振系统皆具备优良的隔振性能,验证了方法的有效性。
关键词:子系统; 动力包双层隔振系统; 两级优化; 吸振器; 隔振性能
动力包作为一个特殊的双层隔振系统,较之典型双层隔振系统,除了兼具优良的隔振性能外,还具有可靠性、安全性高和经济性好的特点,此外还具备结构紧凑和节约安装空间的优势。国外动力包发展地已较为成熟,并且广泛应用于铁道车辆、船舶等诸多领域。但该项技术还没有得到广泛的传播,很少见到有关动力包双层隔振的研究和报道。目前,国内对动力包的隔振设计的研究还处于一个初步探索阶段并没有形成一套非常行之有效的设计方法。因此,有必要对其进行深入系统的研究。与典型的双层隔振系统不同,动力包除了一、二级主系统外在中间构架上还安装有一个本身不带激励源的子系统[1],这也是其设计难度较典型双层隔振系统大的缘故。对于典型的单层或双层隔振系统许多学者进行了大量的研究,得出了许多有参考价值的成果。袁惠群等[2]对具有分布质量的双层隔振系统的振动特性进行了分析。CHEN等[3]采用最大熵方法对双层隔振系统进行了优化设计。UNGAR等[4]采用阻抗导纳法分析了高频时隔振系统的隔振效果,得到了单层和双层隔振系统的插入损失。HU等[5]分别从理论和实验的角度对一艘游轮上的双层隔振系统进行了研究。孙玲玲等[6-8]从隔振参数设计的角度出发研究了隔振系统中功率流的传递特性。近年来随着国内内燃动车的兴起,动力包实现了首次国产化,孙玉华等[9-12]对该内燃动车动力包的双层隔振设计,从解耦优化和模态匹配的角度进行了较为系统的研究,取得了良好的效果。但其研究在进行参数设计时,主系统和子系统是分开设计的,没有考虑互相之间的耦合,这样会使得最终设计参数与最优参数存在较大误差。
为了解决上述问题,本文提出一种两级优化的思想。首先将动力包双层隔振主系统抽象为12自由度系统,以支座动反力为目标,在保证系统解耦度和机组振动烈度尽量小的前提下对隔振器刚度进行多目标优化,确定一、二级隔振器刚度。然后,将整个系统抽象为18自由度动力学模型,创新性的将动力包散热器子系统充当主系统吸振器,按照H∞准则设计出其隔振器刚度。最后结合仿真和实验结果验证该方法可行性和有效性。
1 动力包双层隔振系统模型抽象
1.1 系统介绍
动力包双层隔振系统实物图如图1所示,其中柴油机和发电机通过连接套刚性连接构成双层隔振系统的一级主系统,通过五个一级隔振器安装于构架上。构架和刚性安装于其上的水箱、空滤、消音器等构成双层隔振系统的二级主系统,通过四个二级隔振器安装于基础上。散热器通过四个隔振器安装于构架上构成双层隔振系统的子系统。
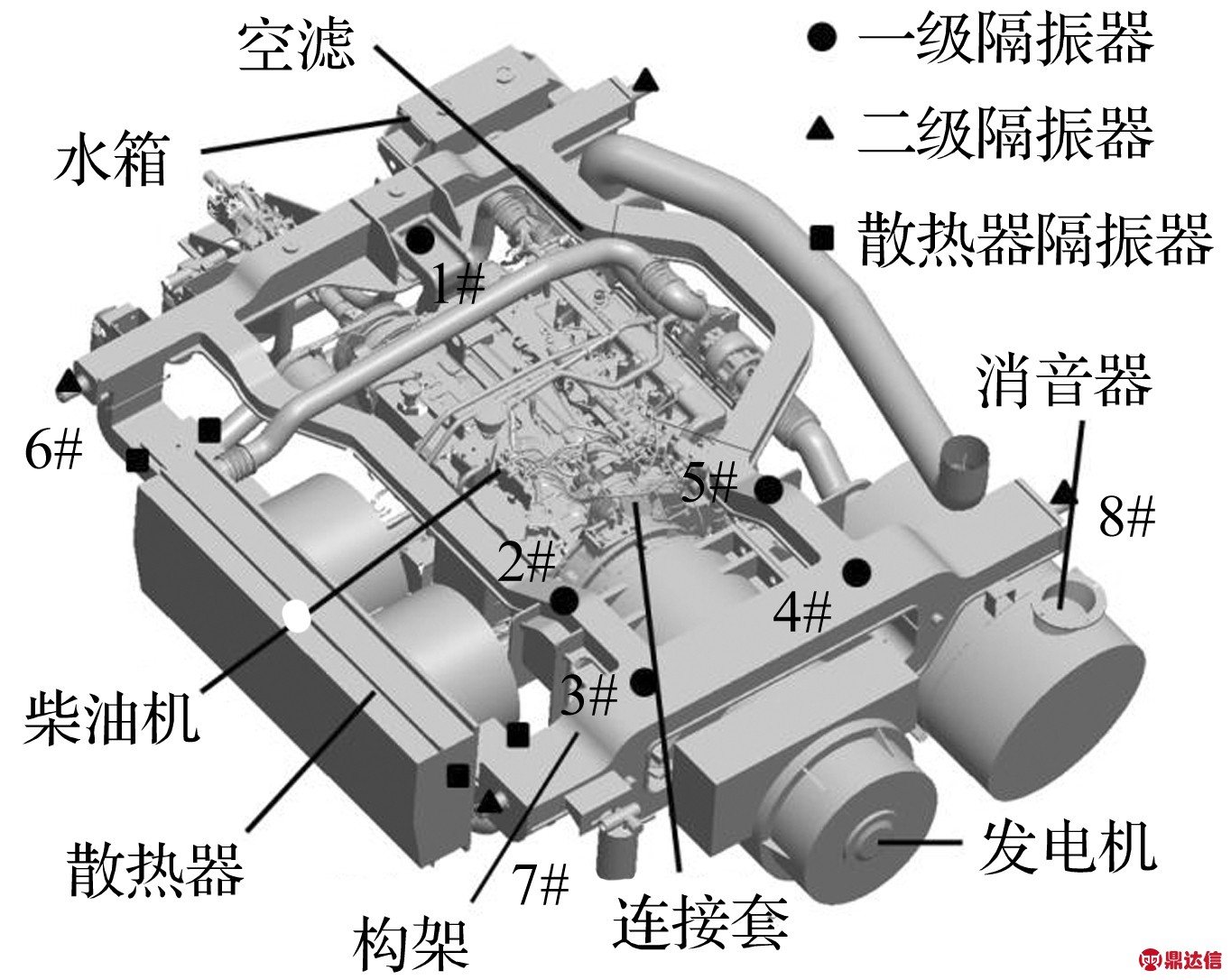
图1 动力包双层隔振系统实物图
Fig.1 Physical diagram of powerpack double-layer isolation system
1.2 动力学模型
以柴油发电机组的质心为原点建立含子系统的双层隔振系统的18自由度的动力学模型,如图2所示。
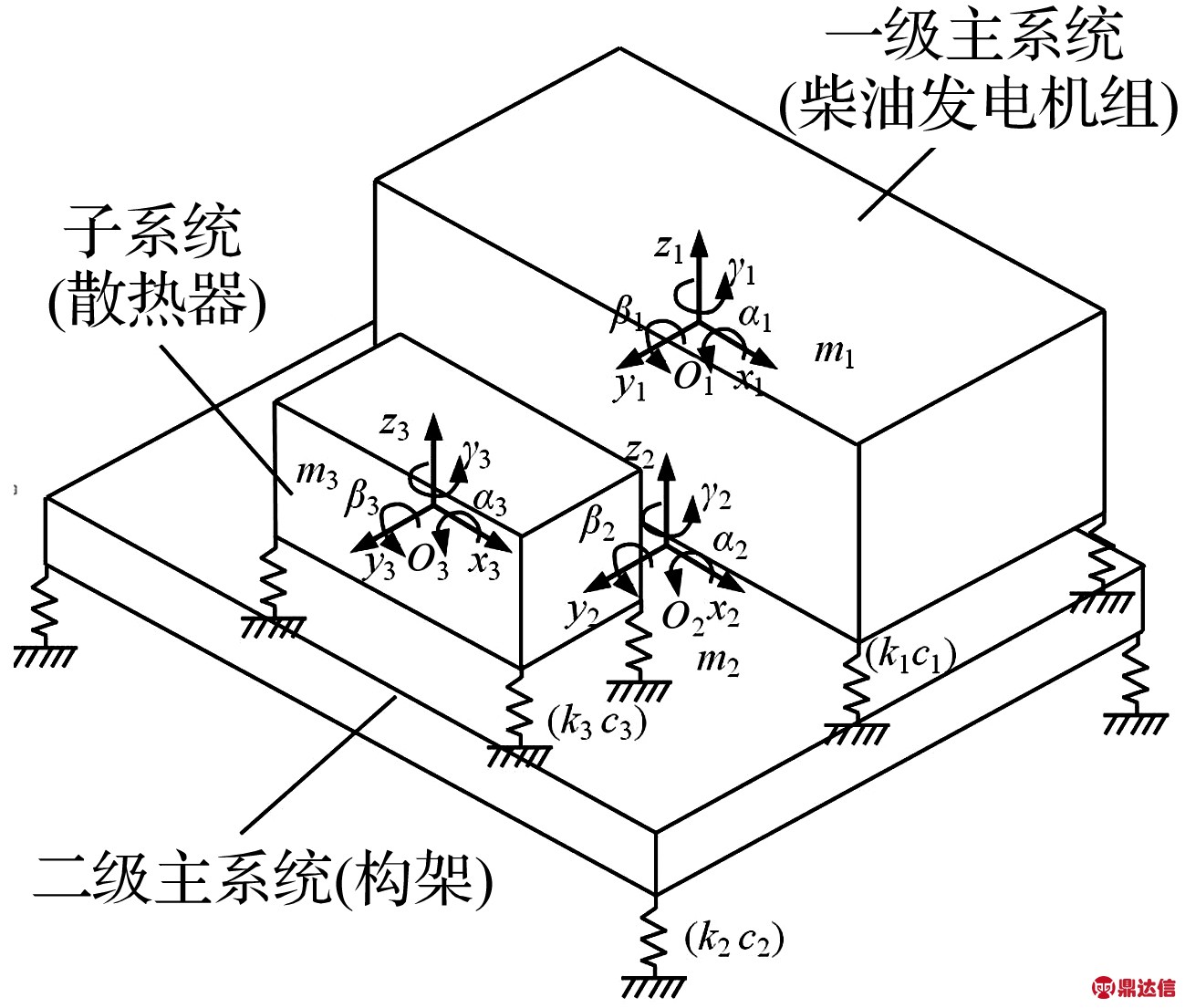
图2 内燃动车动力包双层隔振系统动力学模型
Fig.2 Dynamic model of diesel railcar powerpack double-layer isolation system
图2中O,O1,O2,O3分别为参考坐标原点和机组、中间构架、散热器的质心。O-XYZ和(α,β,γ)为参考坐标系及其惯性主轴。O1-X1Y1Z1,O2-X2Y2Z2,O3-X3Y3Z3和(α1,β1,γ1),(α2,β2,γ2),(α3,β3,γ3)分别为机组、中间构架和散热器的动坐标系和惯性主轴。
本文所研究的动力包双层隔振系统,其激振源为六缸柴油机,其主要激振力为柴油机3、6主简谐倾倒力矩,柴油机曲轴连杆系统的动平衡精度高,离心惯性力和往复惯性力相对于柴油机倾倒力矩非常小可忽略不计。系统的动力学方程可写为如下形式[14-15]:
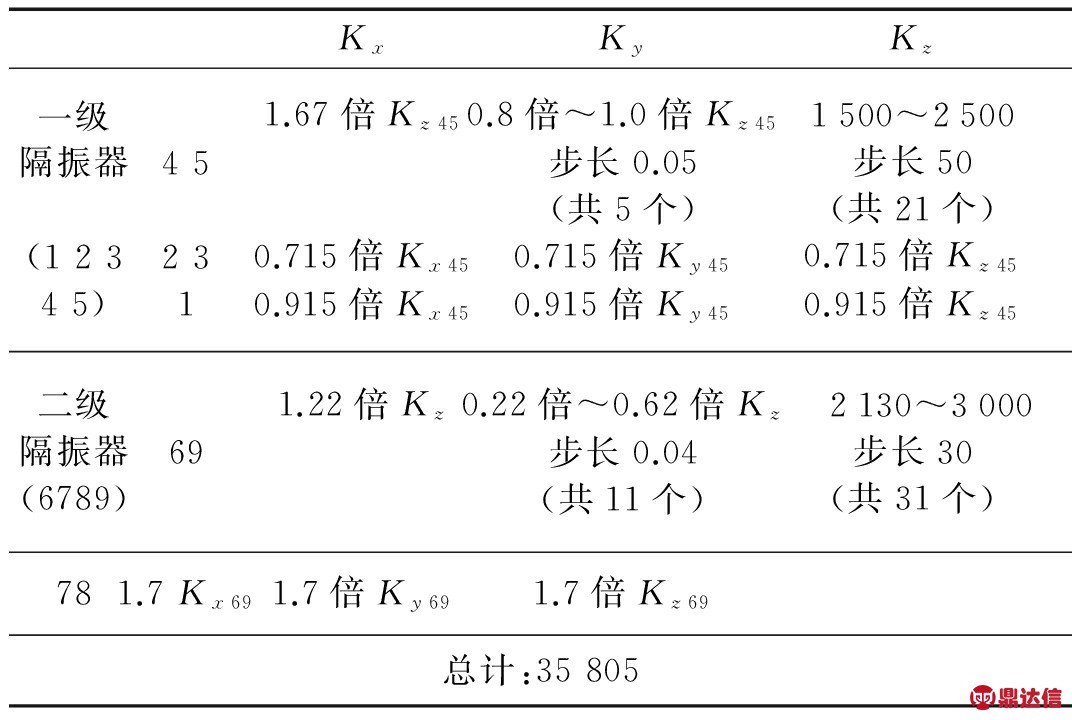
(1)式中:质量、阻尼和刚度矩阵均为18阶方阵,与之对应的加速度、速度、位移量也是18维的,具有下列形式:
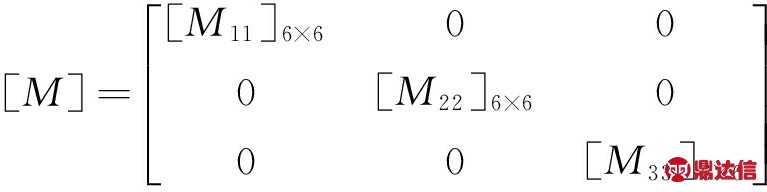
[C]=

[K]=

{U}=[x1,y1,z1,α1,β1,γ1,x2,y2,z2,
α2,β2,γ2,x3,y3,z3,α3,β3,γ3]T
{F}=[0,0,0,M0sinωt,0,0,0,0,0,0,0,0,0,0,0,0,0,0]T
只考虑系统的强迫振动的稳态响应,系统的解可设为{U}={A}cosωt+{B}sinωt,将其代入式(1),则{A}、{B}可由下式求出
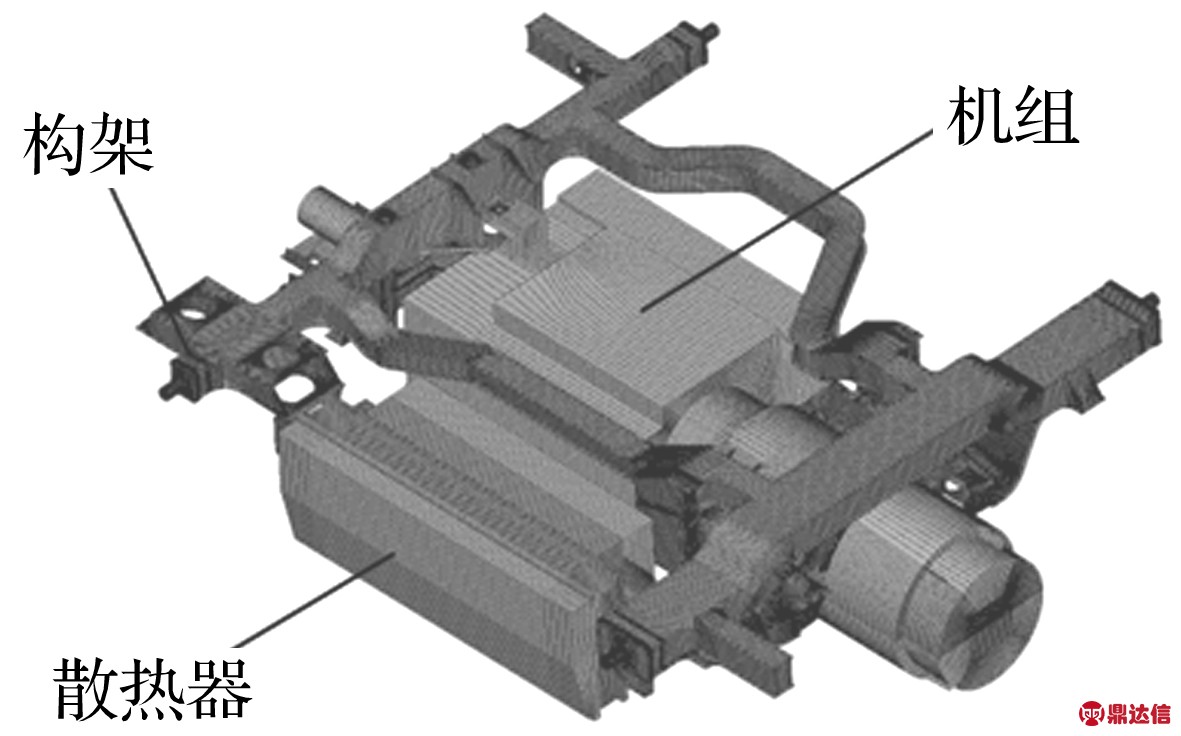
(2)
2 双层隔振系统刚度参数优化
本文所研究的动力包双层隔振系统,因为受安装位置和空间布置的影响,系统各部件的质心位置和隔振器安装位置及角度都不可调。故只能通过优化隔振器刚度来改善系统的隔振性能。
对于动力包双层隔振系统而言,除了要隔离柴油发电机组在稳定工况下的激振力,还要最大限度地隔离发动机在启动或停机时的激振力。因为发动机在启动或停机的过程将不可避免地引起隔振系统或车体的共振,从而严重影响动车的乘坐舒适性,有时甚至会造成结构的冲击破坏。因此,必须将系统传递给车体的动反力减到最小,体现在系统的力传递率上即为使其最大峰值最小。如果直接用18自由度动力学模型对系统进行隔振优化,因为系统的自由度数以及刚度变量较多,计算量将会非常庞大,且不好实现两个隔振目标的统一。本文所研究的动力包散热器子系统本身不带激励源,不能直接激励起双层隔振系统的振动,但由于子系统与主系统之间同时存在较为强烈弹性耦合和惯性耦合,子系统参数对主系统固有特性有较大的影响,能对主系统中力的传递起到间接地调节作用。同时,柴油机怠速工况(900 r/min)下主简谐倾倒力矩频率(45 Hz)高于动力包的模态共振频率,因此子系统在稳定工况时刚度对隔振器动反力的影响是单调递增的。考虑到动力包双层隔振系统的以上特性,可将系统分目标进行两级优化:一级优化,在不考虑子系统的情况下,将动力包抽象为12自由度动力学模型,以机组在怠速工况下传递给系统的动反力最小为目标,在保证系统解耦度和机组振动烈度尽量小的前提下进行多目标优化,确定一、二级主系统隔振器刚度;二级优化,建立动力包双层隔振系统的18自由度动力学模型,保持主系统隔振器刚度不变,将子系统充当一个6自由度吸振器进行刚度设计,按照H∞准则设计出空冷子系统的隔振器刚度。
2.1 主系统刚度参数设计(一级优化)
2.1.1 刚度组合的确定
1) 一、二级隔振系统各隔振器垂向刚度比的确定
对于本文所研究的双层隔振系统,各一级隔振器安装位置相对3个惯性主轴都不对称。如果各隔振器选用相同刚度,其静压缩量将会不同,机组会发生倾斜。此外,机组6个自由度的振动模态将严重耦合,各主方向振动相互影响,系统隔振性能将会严重恶化。因此,可通过隔振器刚度的合理匹配,减小6个自由度的模态耦合和相互影响,优化系统隔振性能。
一级隔振系统的刚度矩阵可由下式给出[13]。
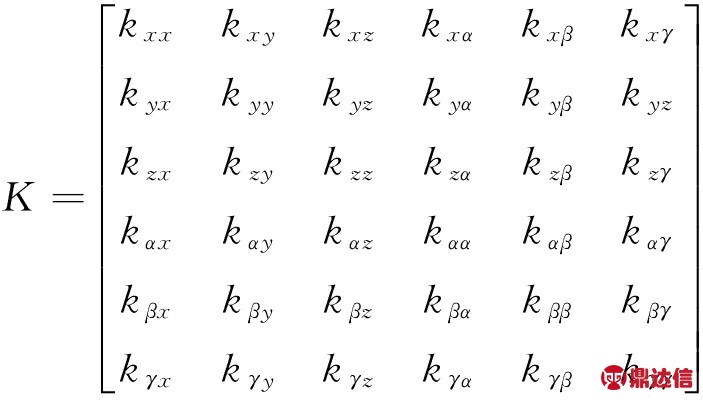
(3)
根据文献[13]的分析,将一级隔振器分为三组,取隔振器1#和隔振器2#、3#的垂向刚度分别为隔振器4#、5#的0.915和0.715倍,可使隔振器弹性力尽量对称,减小8个刚度系数kxγ、kγx、kyγ、kγy、kαz、kzα、kβz、kzβ,有利于一级系统解耦度的提高,同时也有利于机组的调平。同样,当二级主系统的隔振器7#、8#的刚度为隔振器6#、9#的1.7倍时,可尽量减小二级主系统刚度矩阵非对角线上的8个刚度系数,提高二级主系统的解耦度。
2) 一、二级隔振器刚度横垂比和纵垂比的确定
本文所研究的双层隔振系统隔振器安装高度与系统质心在垂向存在较大的距离,不可避免地会带来α方向和y方向的模态耦合,为降低主要激励(3、6谐次倾倒力矩)方向(α1方向)的模态频率和提高其解耦度,在隔振器z向刚度一定的情况下,应在y向选较小的刚度。根据一、二级隔振器(分别为锥形隔振器和Ⅴ型隔振器)的结构特性,其刚度横垂比的最小值分别为0.8和0.2。由此定出一、二级隔振器刚度横垂比的变化区间分别为0.8~1.0和0.22~0.62。为了保证隔振系统在动车行驶方向的稳定性(x向)分别取一、二级隔振器刚度纵垂比为1.67和1.22。
3) 一、二级隔振器垂向刚度的确定
按照隔振器压缩特性和车载设备的稳定性要求,动力包的垂向频率应大于8 Hz,再由双层隔振系统一、二级主系统的质量可定出一、二隔振器的垂向总刚度的变化区间分别为4 400~7 400和11 500~16 200。
根据一、二级隔振器垂向总刚度的变化区间和各隔振器的垂向刚度比,计算出一级隔振器4#、5#以及二级隔振器6#、9#的变化区间,分别为1 500~2 500、2 130~3 000。
4) 刚度组合的生成
取一级隔振器4#、5#垂向刚度变化的步长为50,隔振器刚度横垂比的步长为0.05;二级隔振器6#、9#的步长为30,隔振器刚度横垂比的步长为0.04。采用排列组合的方法生成包含35 805种隔振器刚度方案所构成的组合,如表1所示。
表1 刚度组合
Tab.1 Stiffness combined
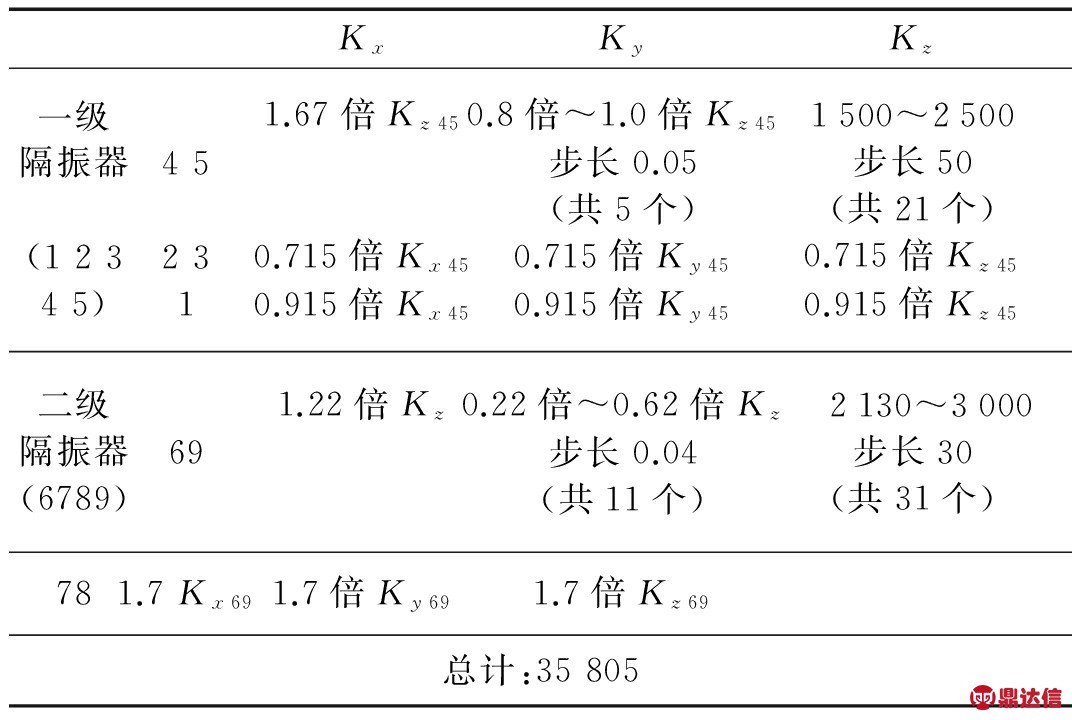
2.1.2 优化目标及优化策略的确定
动力包作为一个激励系统,对动车最直接的影响为在四个二级隔振器位置给车体作用了四个动反力。如果系统传递给车体的动反力过大将引起车体强烈的振动,不但会影响车辆的正常运行和车体的疲劳寿命而且车辆的声振舒适性也会大幅度变差,因此隔离系统传递来给车体的力是隔振设计最主要的目标。此外,对动力包本身又要求有足够的稳定性和良好的工作环境,即要求动力包双层隔振系统有足够的动、静刚度和较小的振动烈度。由于发动机的激振力频率成份非常复杂,并且在发动机启动或停机时其主简谐激振力的频率会经过系统所有的模态频率,因此要尽量提高隔振系统各模态间的解耦度,尤其是在激振力方向的解耦度,避免系统出现强烈度耦合共振。
根据以上分析本文确立如图3所示的优化策略:首先单独以二级隔振器动反力最小、机组振动烈度最小、α向解耦度最大、综合解耦度最大四个目标函数[16]采用枚举法对表1所示刚度组合进行优化计算确定各优化目标下的最优刚度方案;然后计算出分别采用四个最优刚度方案时各隔振性能指标的值;最后通过比较优选出使二级隔振器动反力相对最优,其他隔振性能指标较优的一组隔振器刚度方案作为最终刚度方案。
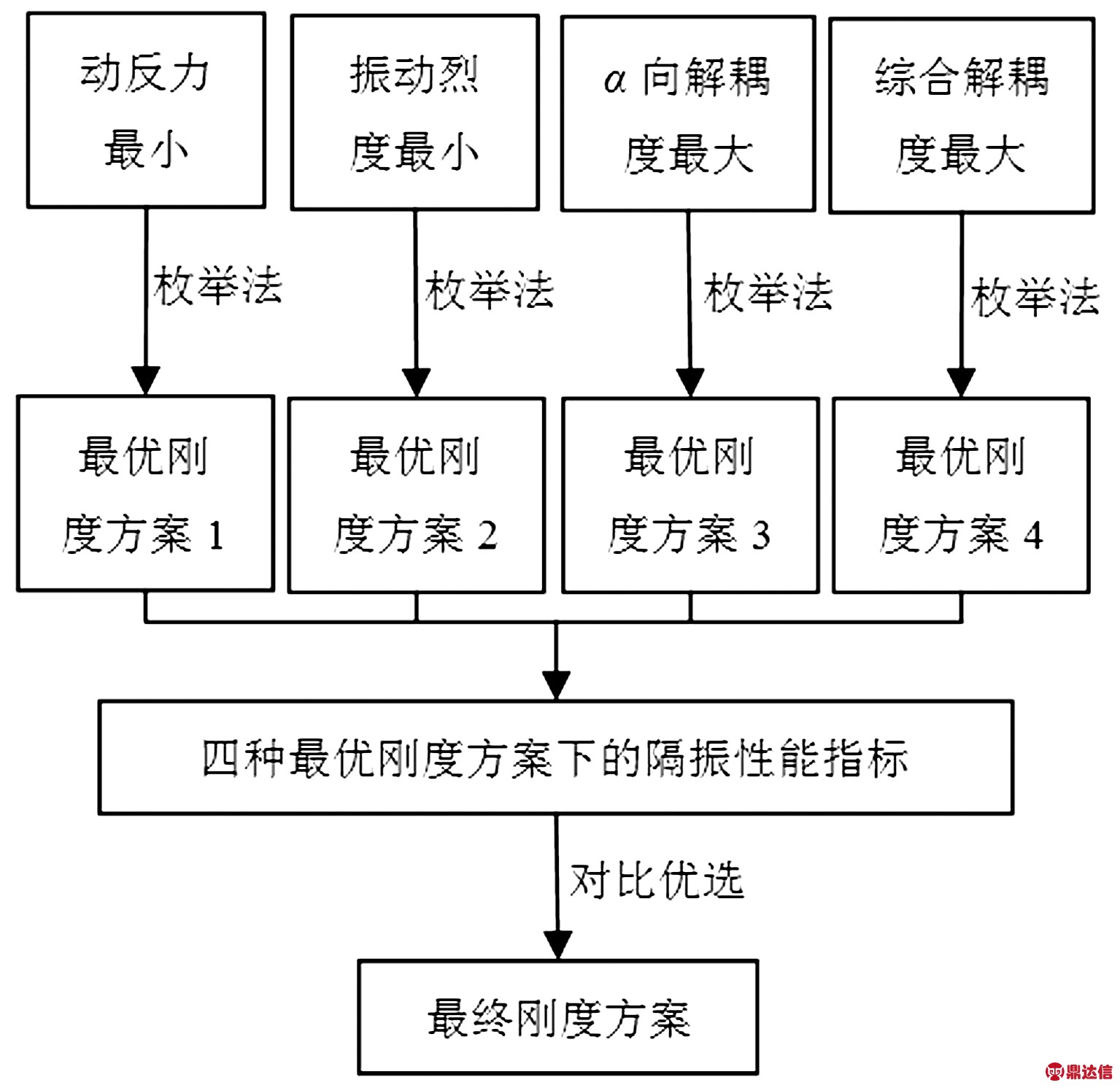
图3 优化策略流程图
Fig.3 Flowchart of optimization strategy
2.1.3 最优刚度的确定
根据上文确立的优化目标和优化策略,采用表1所示的刚度组合,对双层隔振主系统进行优化计算,结果如表2所示。
从表中可以看出,当采用动反力最优的刚度方案时,振动烈度最优,同时α向解耦度和综合解耦度也较优。当采用α向解耦度最优的刚度方案时,其余三个优化指标都较差。当采用综合解耦度最优的刚度方案时,动反力过大。而隔振系统的主要目标为隔离系统传递给车体的力,以达到减弱车体振动,提高乘坐舒适性的效果。因此,可将动反力最优的隔振器刚度方案,作为主系统的最终刚度方案。
表2 各最优刚度方案下系统隔振性能指标
Tab.2 Isolation vibration indexes under different optimal stiffness schemes
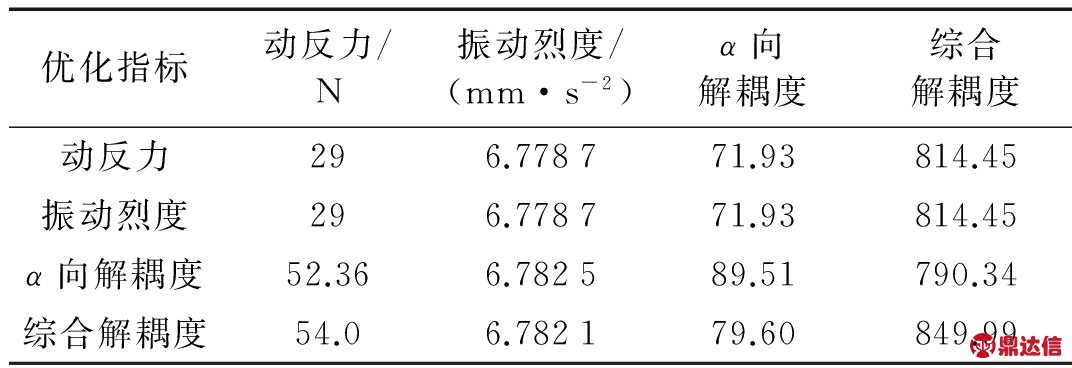
2.2 子系统刚度设计(二级优化)
散热器子系统,在转速较低时离心惯性力很小,可看做一个无激励源子系统。当转速超过1 800 r/min时,离心惯性力的频率接近构架模态频率会引起构架的结构振动,因此有必要对其进行隔振。并且,如果将散热器与构架刚性连接,会带来一系列疲劳和强度问题。因此,子系统刚度参数的设计原则为:在低频时使子系统充当一个多自由度吸振器对主系统进行减振,在高频时又要能隔离本身的高频激振力向构架传递,且要保证本身在柴油发电机组常规工况时具有较好的振动烈度水平。
当空冷风扇转速为1 800 r/min时,子系统的激振力频率为30 Hz,根据隔振原则子系统的垂向和横向固有频率应小于激振频率倍,即小于21.2 Hz。同理为了避免在外界激励下子系统与主系统发生耦合共振,子系统的垂向固有频率应大于动力包垂向频率的
倍,即大于11.3 Hz。根据子系统的上、下限频率,可确定子系统垂向刚度的变化区间。
图4为子系统隔振器的示意图,隔振器左、右两安装点之间的间距很小,因此要适当增大垂向刚度,以保证子系统在滚动方向的稳定性。子系统隔振器结构特性,决定其x和y向水平刚度相等。设定子系统垂向固有频率为18 Hz,取隔振垂向刚度和水平刚度的比为1.5∶1,初步设计出子系统的刚度方案,采用上文建立的18自由度模型,计算出动力包双层隔振系统的力传递率,如图5所示。
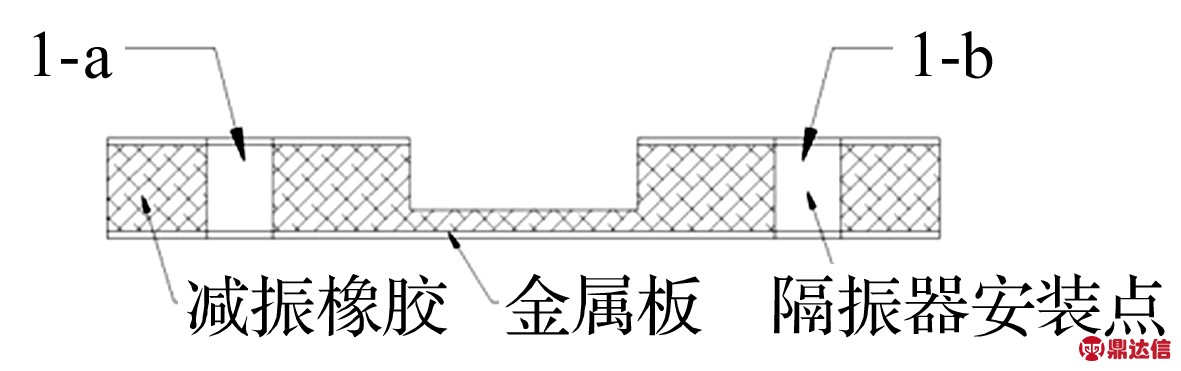
图4 子系统隔振器示意图
Fig.4 Schematic diagram of subsystem isolator
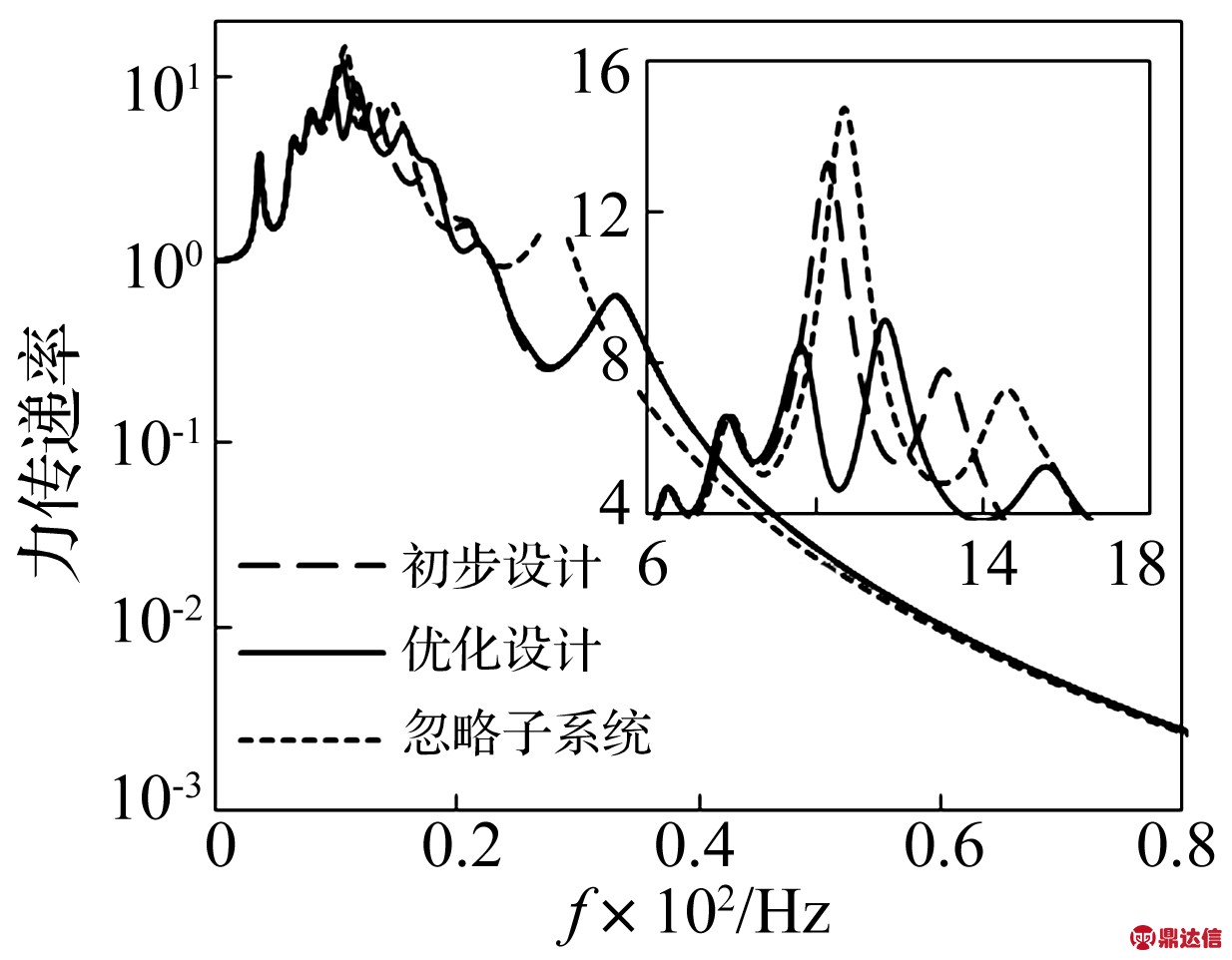
图5 双层隔振系统传递率曲线
Fig.5 Transmissibility curves ofdouble-layer isolation system
从图5可以看出,增加一个子隔振系统,二级主系统的当量刚度变大,对应于α2向模态的共振峰后移,系统高频隔振性能稍有变差。但在激振频率45 Hz(怠速3.0谐次激振力频率)时,两者的传递率近似相等,故不会恶化系统在稳定工况的隔振性能。
同时子系统的增加,使双层隔振系统对应于激振力方向(α1向)主模态的力传递率曲线共振峰分化为两个峰值减小的共振峰,此时子系统相当于一个多自由度的吸振器,能有起到抑制双层隔振主系统的振动提高双层隔振系统的低频隔振性能的作用。在初步刚度方案下,双层隔振系统最大共振峰出现在10 Hz附近,对照其能量分布表(表3)可知,该共振峰对于系统的α1(激振力方向)向模态,该模态为α1-y2-y3的耦合模态,此时系统的能量输入和输出都很大,发动机的激振力经过系统被放大13.9倍作用于车体上,将会引起车体剧烈振动,严重影响动车的乘坐舒适性。观察到,α1-y3耦合也较为严重,为了减小双层隔振系统的力传递率,可用子系统y3向模态来控制双层隔振主系统的α1向模态,即将子系统的横向振动看成一个单自由度的当量系统来充当双层隔振主系统的吸振器。根据吸振器设计原则[14],子系统y3向模态与主系统α1向模态的固有频率比为:
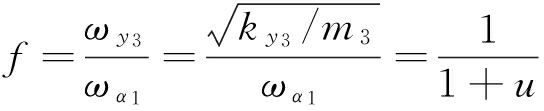
(4)
式中:u为子系统与α1向模态的当量质量之比,u≪1,因此子系统的横向刚度可近似由式(5)求出:

(5)
保持子系统垂向刚度不变,以隔振器横向刚度为优化变量,取子系统横向刚度的近似值为初始值,取橡胶隔振器结构阻尼比为0.1,在初始刚度正负100%的区间内对系统的力传递率进行梯度优化,求出使动力包双层隔振系统力传递率最大峰值最小(H∞准则)的子系统隔振器刚度作为子系统的最终刚度。
优化设计后双层隔振系统的力传递率如图5所示,从图中可以看出,优化后系统力传递率曲线在高频段几乎不变,其最大峰值由13.9降为了8.6。此时系统既具备普通双层隔振系统优良的高频隔振性能,又能克服传统双层隔振系统低频隔振系统不足的缺点。在α1(激振力方向)向模态下子系统y3向振动的能量百分比由优化前的12.1%增加到了优化后的33.68%,而二级主系统的y2向振动的能量百分比由优化前的22.6降为了优化后的1.88%。由以上分析可知,子系统的作用为:既减小了主系统的能量输入,又将二级主系统大部分振动能量转移到了子系统本身,以达到减弱二级主系统振动和二级隔振器动反力的效果。
表3 优化前双层隔振系统能量分布[1]
Tab.3 Energy distribution of double-layer isolation system before optimization

3 隔振性能评估及试验分析
为了验证该两级优化方法的有效性,下文将建立包含柔性构架的动力包双层隔振系统刚柔耦合模型,并且结合试验,分析优化后双层隔振系统各项动力学性能。
动力包双层隔振系统刚柔耦合模型如图6所示,其中机组和散热器采用Mass21质量单元模拟其质量属性,采用Shell181壳单元划分网格,将壳单元密度设置很小,弹性模量设置很大,以将其模拟为刚体;柔性构架采用Shell181壳单元建立,其他附属装置采用Mass21质量单元模拟刚性固定于构架上。
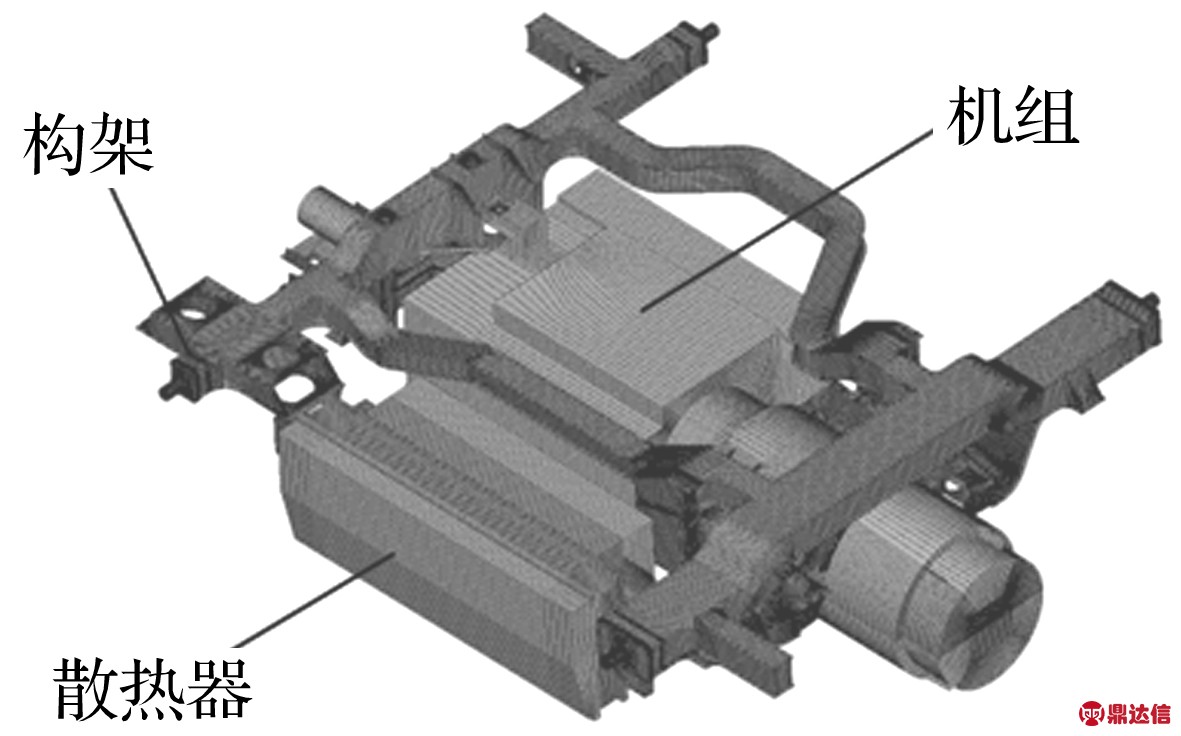
图6 动力包双层隔振系统刚柔耦合模型
Fig.6 Rigid-flexible coupling model of powerpack double-layer isolation system
试验测试系统由朗斯三向加速度传感器,LMS SCADAS测试系统,微机测试平台组成。试验中机组和散热器的振动烈度测点根据铁标TB/T 3164—2007进行选取。为了分析系统的传递特性和隔振器的动反力,在一、二级隔振器上下布置了相应的测点。其中各点的速度和位移通过LMS软件积分得到,各隔振器动反力为隔振器上、下位移差和隔振器刚度乘积与隔振器上、下速度差与隔振器阻尼乘积的平方和开根号。图7给出了动力包二级隔振器上、下,一级隔振上、下和散热器隔振器测点的照片。
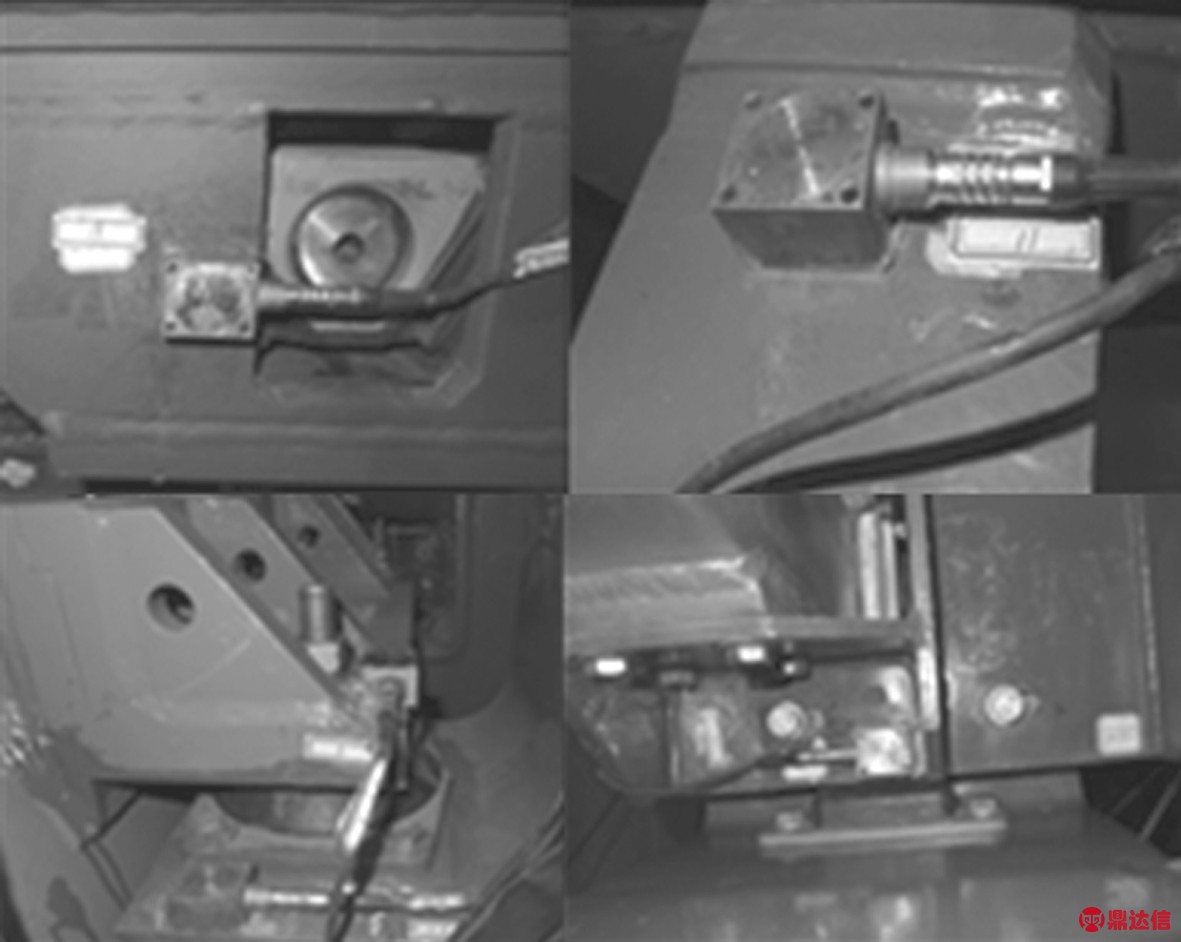
图7 动力包部分测点照片
Fig.7 Photos of several test points of powerpack
3.1 传递特性分析
分别采用刚体模型和刚柔耦合计算的系统力传递率曲线如图8所示。从图中可知系统刚柔耦合模型的力传递率曲线最大值为8.8,较之忽略子系统情况下的最大传递率减小40%,系统低频隔振性能大为提高。怠速工况3.0和6.0主简谐激振力的传递率分别为0.07和0.03,系统隔振效率高达93%,而在其它稳定工况双层隔振系统的隔振效率更高,系统隔振性能良好。
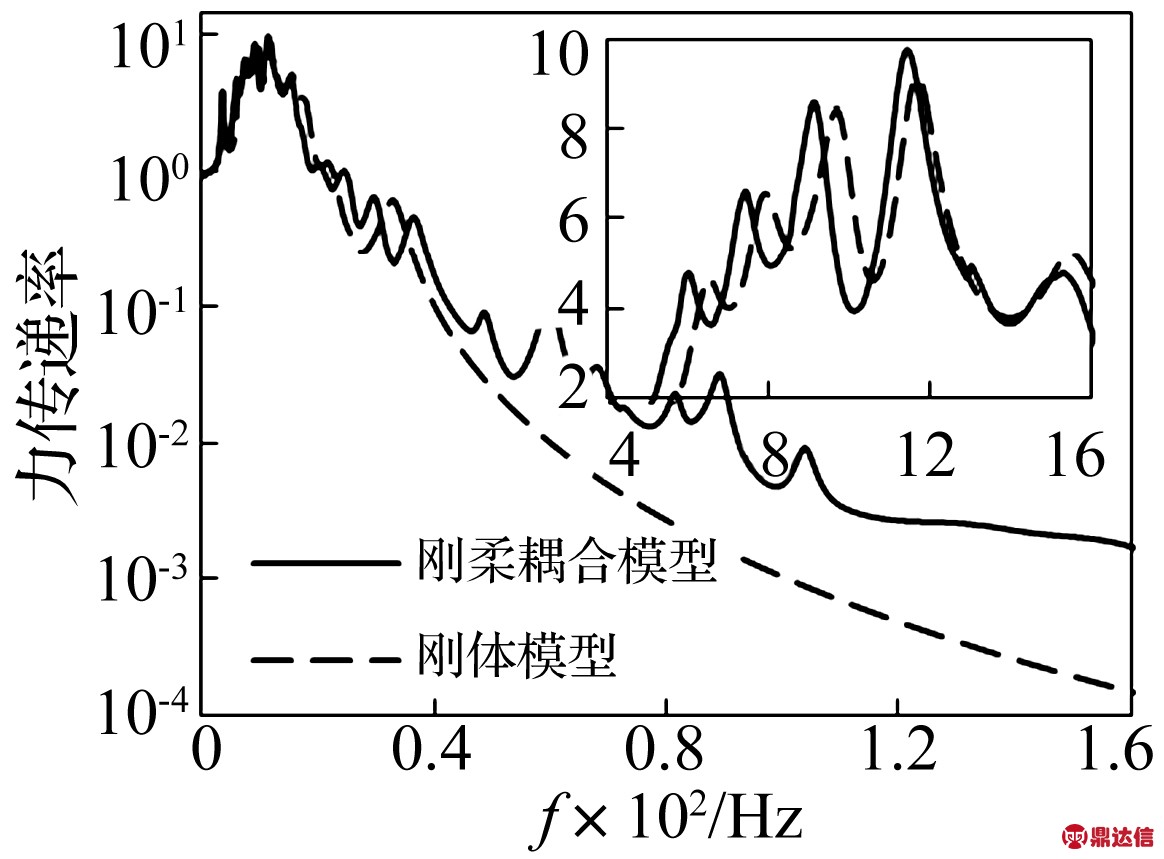
图8 两个不同动力学模型的传递率曲线
Fig.8 Transmissibility curves of two different dynamic models
对经过优化设计后的动力包样机进行振动测试(下同),发动机停机工况(从怠速停车)动力包各部件3.0谐次位移振幅曲线(最大主简谐激振力对应的位移振幅)如图9所示。从图中可以看出,机组和构架在10 Hz左右(200 r/min)附近各有一峰值大小相近且振幅较小的共振峰,这与力传递率在10 Hz附近的特性是相吻合的。此时,散热器在机组第二个共振峰峰值频率处存在一个较大的峰值。这说明,由机组输入的很大一部分振动能量转移到了子系统,从而减弱了构架(二级主系统)的振动,同时也间接的抑制了机组的振动(一级主系统),子系统充当双层隔振主系统的动力吸振器。
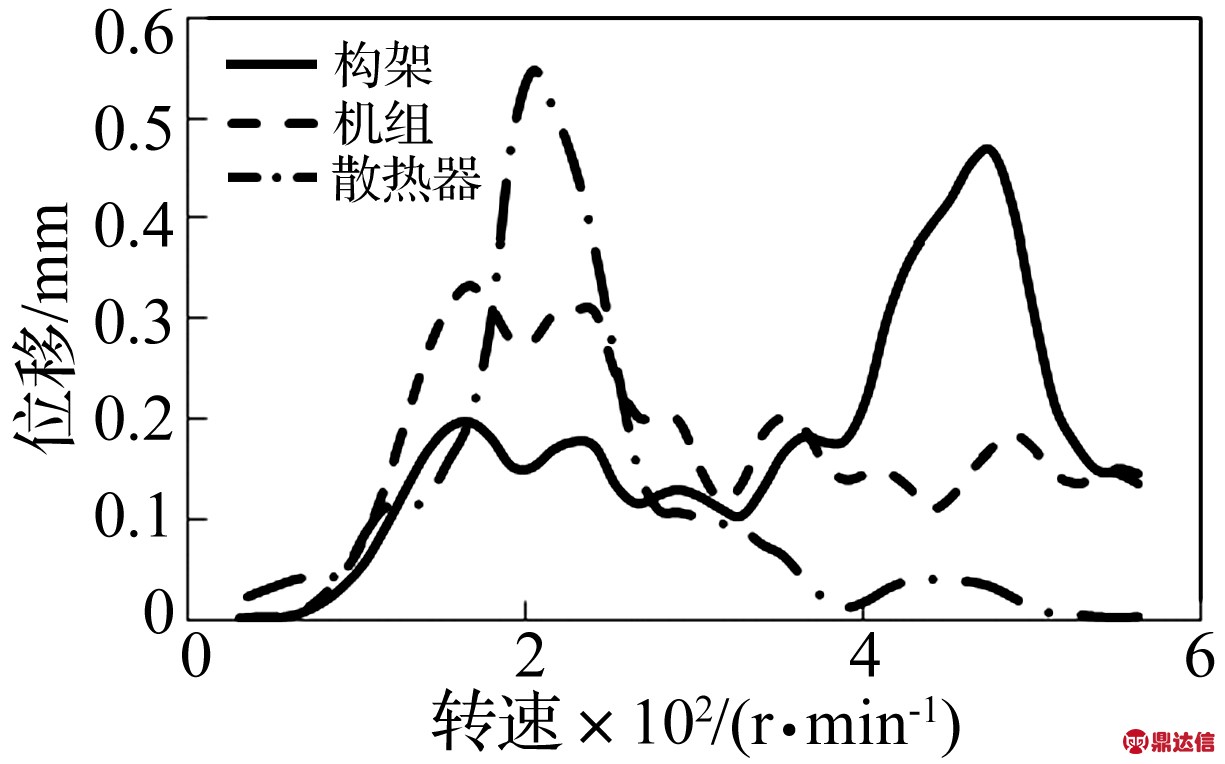
图9 发动机停机工况动力包各部件位移振幅曲线
Fig.9 Displacement amplitude of various components of powerpack after shutdown
3.2 动反力分析
仿真预测和实测所得的二级隔振器动反力随发动机转速的变化曲线如图10所示。从图中可以看出,二级隔振器的实测动反力最大值为296 N,小于用文献[12]中优化设计后的374 N,隔振系统传递给基础的力较小,满足设计要求。
系统刚柔耦合模型仿真计算所得动反力远小于实测动反力。通过分析实测信号的频率成分可知,实测信号包含很大一部分非主简谐的谐次成分,而仿真计算只能考虑柴油机的1、2、3、6(柴油机为六缸机)的激振力。抽取实测信号的1、2、3、6谐次的成分计算所得动反力,比原信号计算所得动反力明显减小,且两者随转速变化规律基本一致。刚柔耦合仿真计算所得动反力,小于阶次提取后的激振力,这是因为柴油机因为做功不均匀和转速波动产生的1、2谐次激振力较预测要大的原故。两者随转速变化的规律在低转速(小于1 400 r/min)时基本一致,当转速大于1 400 r/min时因为柴油机高频主简谐激起了柴油发电机组的结构模态,系统产生强烈的共振,而刚柔耦合模型并没有考虑机组的柔性,两者变化不再一致,由此可说明刚柔耦合模型与动力包实际模型相符。系统刚体模型计算所得动反力,与刚柔耦合模型规律基本一致,由于没考虑构架柔性的原故,频率相对前移。
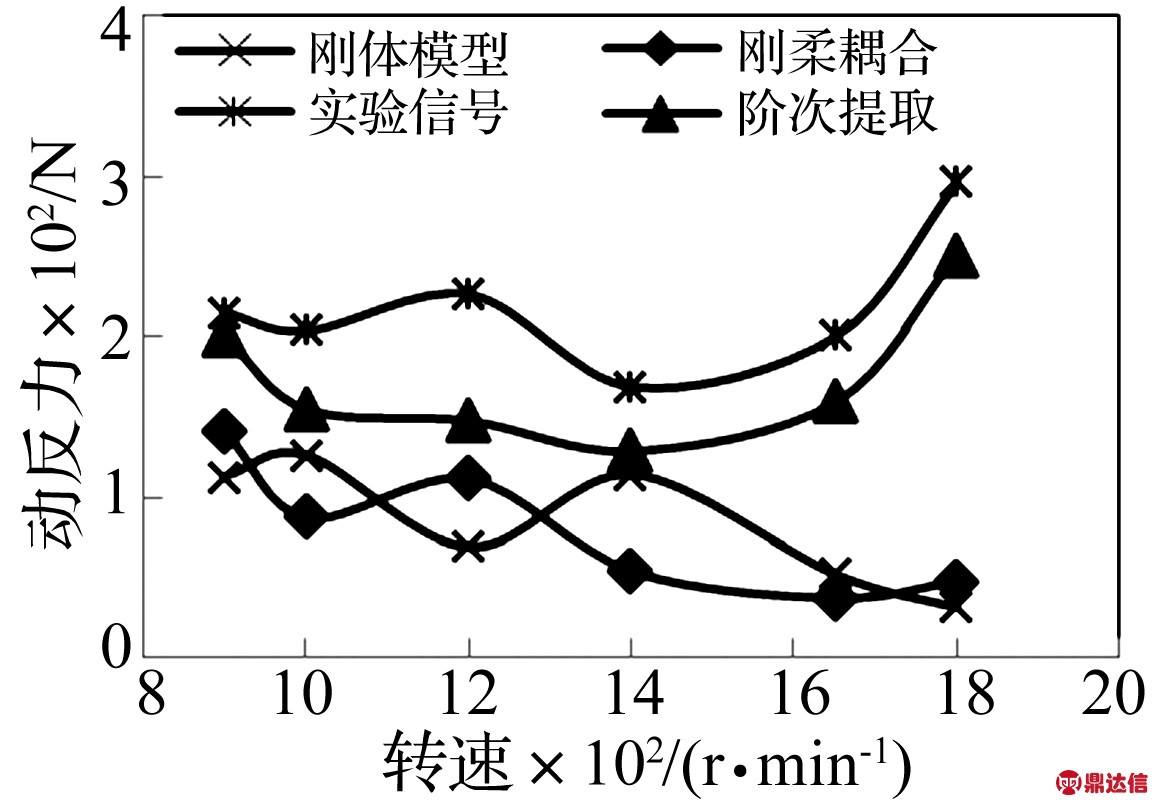
(注:“刚体模型”和“刚柔耦合模型”分别为采用两种动力学模型计算的结果,“实测信号”是由实测信号计算所得结果,“阶次提取”为对实测信号进行阶次提取后计算所得结果,下同。)
图10 二级隔振器支反力随发动机转速变化曲线
Fig.10 Curves of the second stage isolator reaction force changing with engine rotational speed
3.3 振动烈度分析
柴油机常规转速工况下机组振动烈度如图11所示。从图中可以看出,机组实测振动烈度最大值为15.45 mm/s,根据柴油机车车内设备机械振动烈度评定方法(GB 5913—1986)评定为等级B,其中900 r/min和1 000 r/min的振动烈度水平为等级A,柴油发电机组振动烈度水平良好,满足设计要求。
与动反力相类似,进行阶次提取后机组的振动烈度水平相对实测振动烈度明显变小,且两者规律基本一致。而通过刚柔耦合模型和刚体模型仿真计算所得的机组在柴油机各转速工况下的振动烈度几乎完全相等,这与动反力的规律是不一致的。图12为采用刚柔耦合动力学模型仿真计算所得的机组y1向(离心惯性力横向分力及往复惯性力),z1向(离心惯性力的垂向分力),α1向(发动机倾倒力矩)在激振力的整个频域内直线振动速度响应曲线,其中激振力的幅值大小为柴油机900 r/min工况下的激振力幅值。由图可知,当激振力频率大于15 Hz时,机组振动烈度主要由倾倒力矩决定,其他激振力对机组振动烈度的贡献量很小且随着频率的增大,机组振动速度程单调均匀递减趋势。由此可见机组振动速度基本不受构架结构振动影响且随转速的增大呈递减趋势,这与仿真计算所得振动烈度随转速的变化趋势是一致的。返观实测振动烈度只在低转速阶段(转速小于1 000 r/min)随转速的增大而减小,在高转速阶段反而随转速的增高而增大,这与仿真的结果正好相反。究其原因是因为在高转速时柴油机主简谐高频激振力激起了机组的强烈的结构振动。
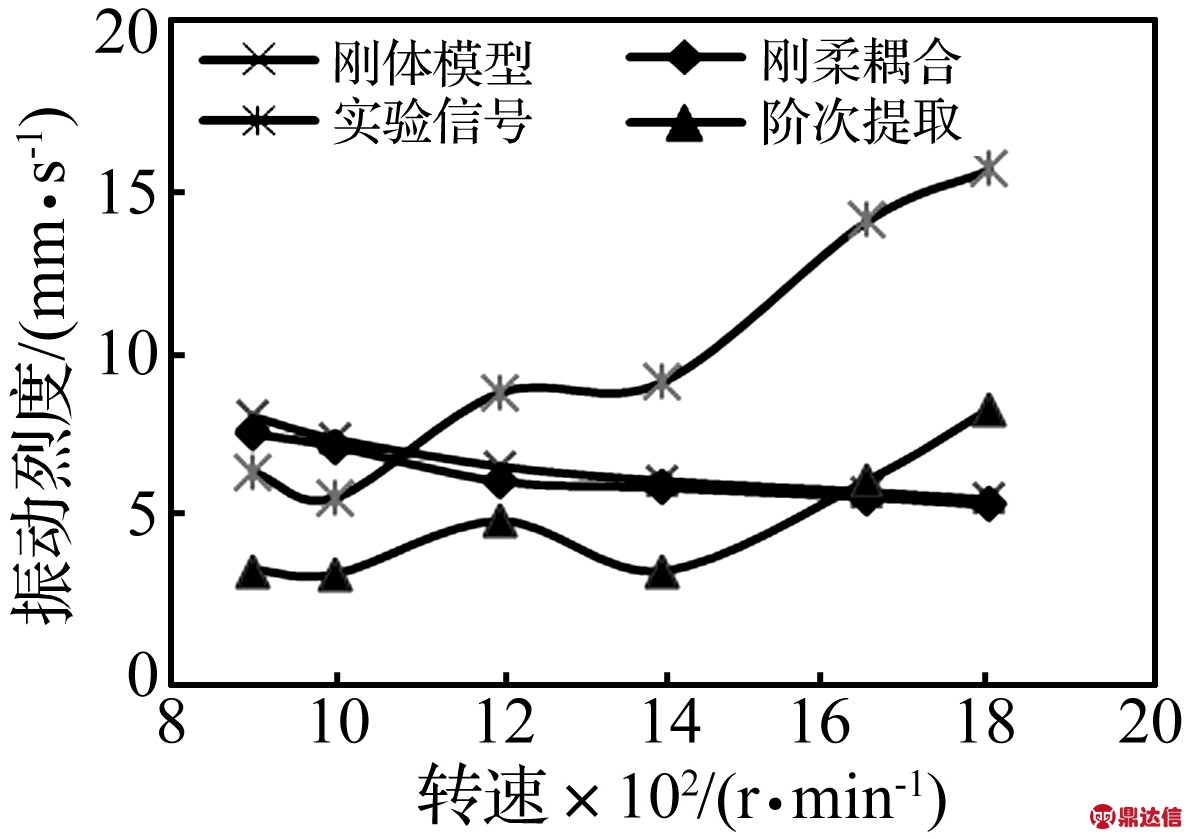
图11 机组振动烈度对比
Fig.11 Comparison of diesel generator set vibration intensity
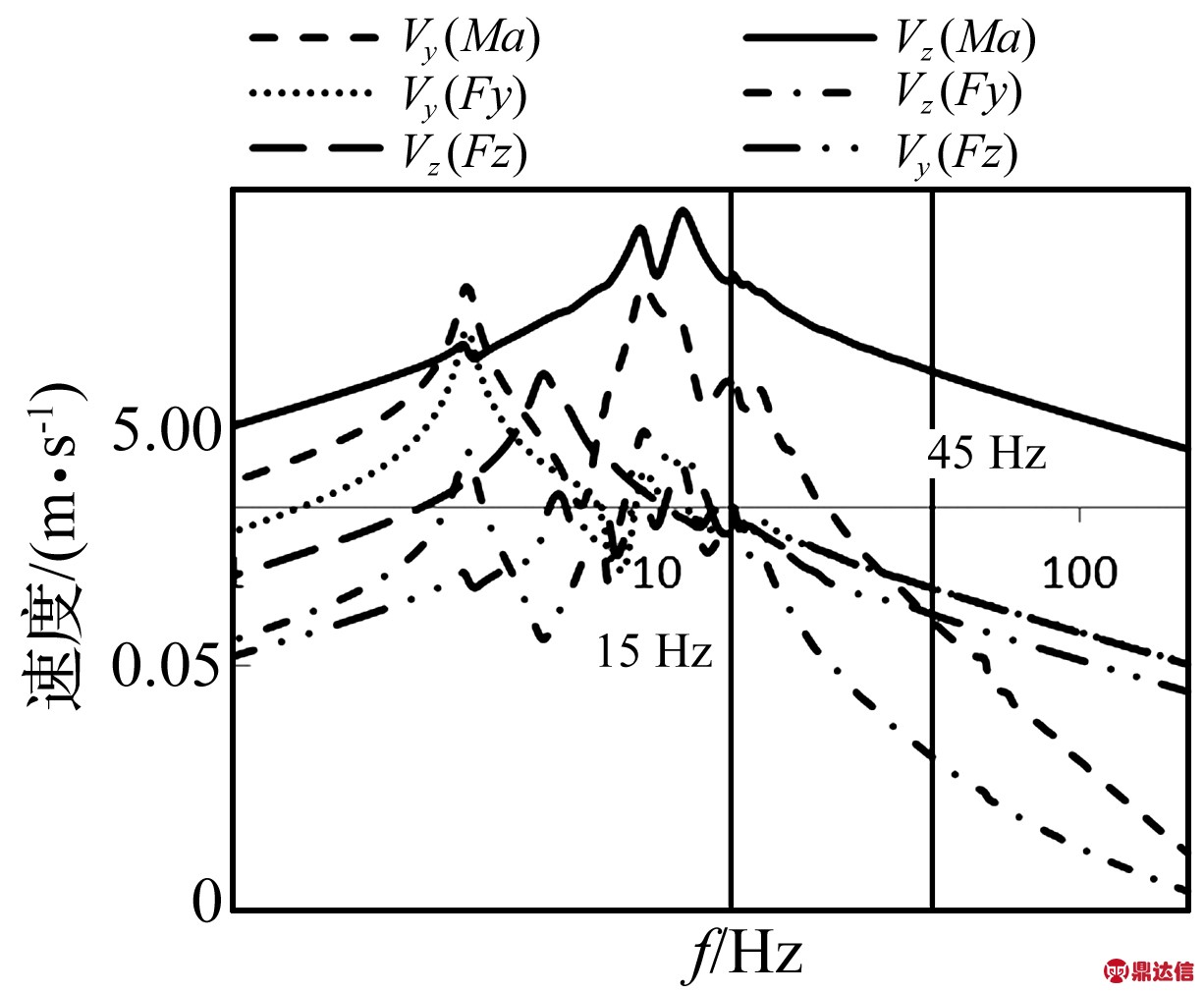
图12 三种不同激励下机组的速度响应
Fig.12 Velocity response of diesel generator set under three different excitations
图13为散热器在发动机常规转速工况下的振动烈度。从图中可以看出,散热器的最大实测振动烈度为4.97 mm/s,烈度水平为B级,除900 r/min和1 800 r/min两个转速工况,其余转速工况下散热器的振动烈度水平均为A级,散热器振动烈度水平良好,满足设计要求。
从图14采用刚柔耦合动力学模型仿真计算所得的散热器的速度响应曲线可知,与机组振动烈度不同,散热器的振动烈度受柔性构架的结构振动的影响很大。这也解释了分别用刚体模型和刚柔耦合模型仿真计算的散热器振动烈度结果不一致的原因。与机组振动烈度类似,由于受到构架和机组结构振动的共同影响,散热器仿真计算和实测的振动烈度随柴油机转速的变化,只在低转速时一致,在高转速时变化趋势相反。从上文的分析可知,因为柴油发电机组是一个大刚度的复杂弹性体,致使仿真计算的振动烈度与实际的振动烈度随激振力频率(柴油机转速)的变化并不一致。但柴油发电机组固有频率远高于双层隔振系统的刚体模态的固有频率,系统隔振器刚度对柴油发电机组的固有模态几乎无影响。因此,在对隔振系统进行优化设计时将柴油发电机组等效成刚体是合理的。
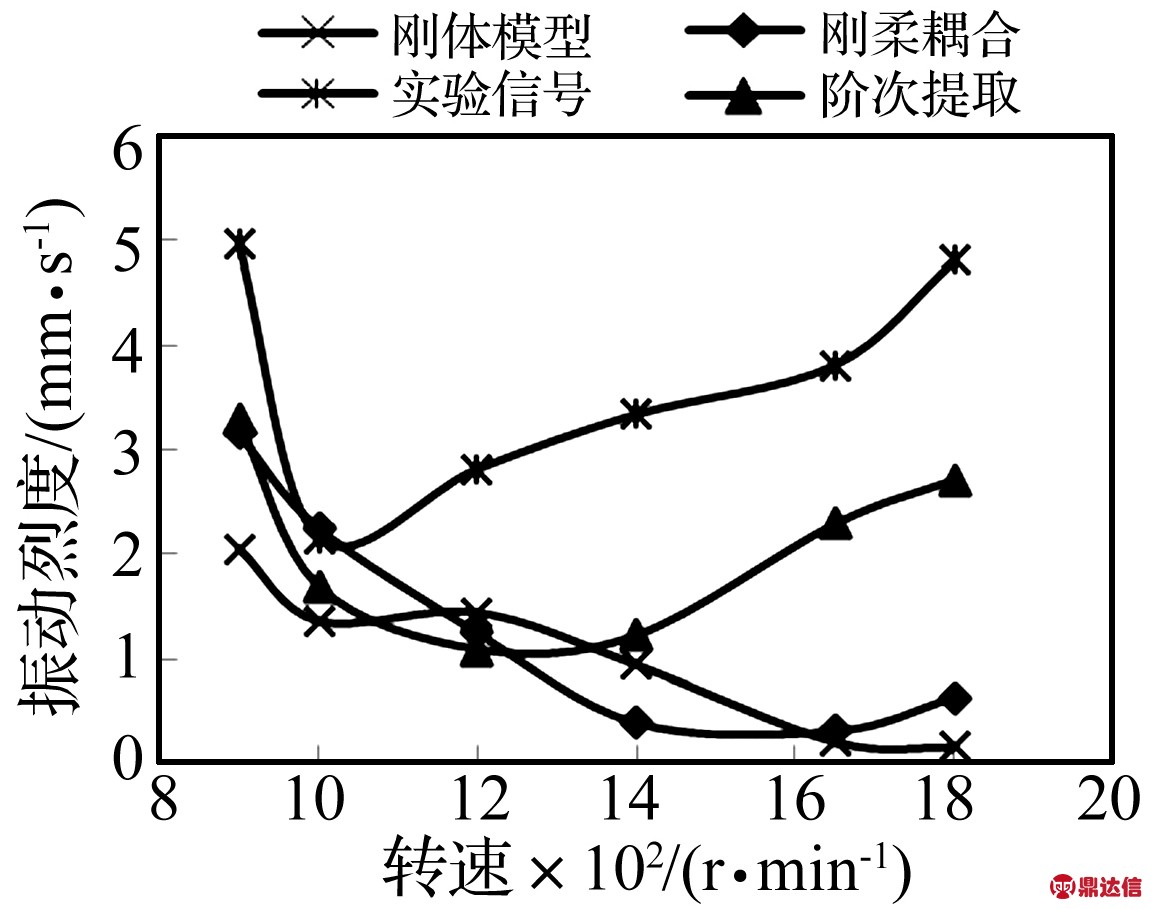
图13 散热器振动烈度对比
Fig.13 Comparison of radiator vibration intensity
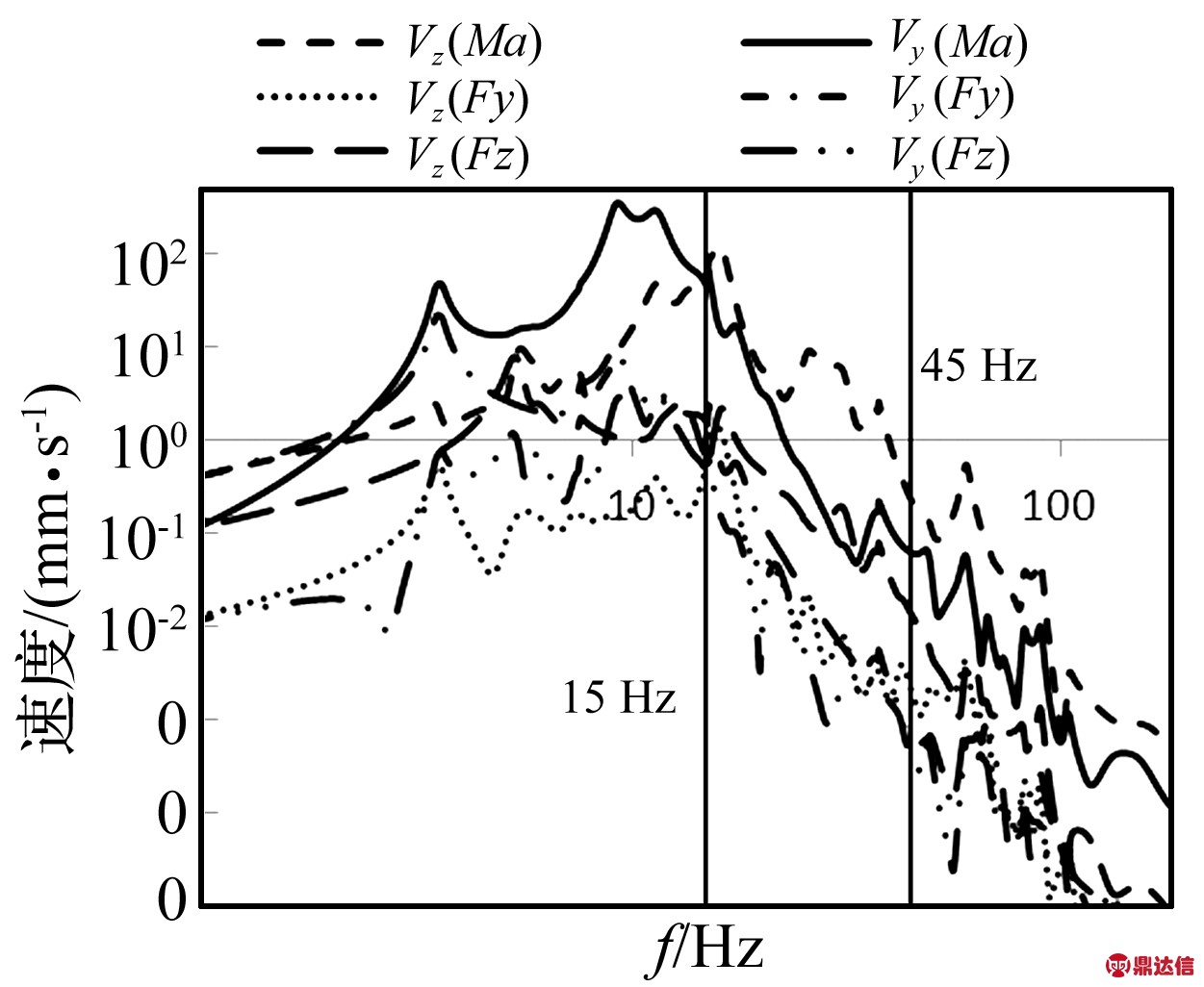
图14 三种不同激励下散热器的速度响应
Fig.14 Velocity response of radiator under three different excitations
4 结 论
(1) 提出了一种两级优化的思想:首先在不考虑子系统的情况下,将动力包抽象为12自由度动力学模型,对双层隔振系统进行优化设计,确定一、二级主系统隔振器刚度;然后建立动力包双层隔振系统的18自由度动力学模型,保持主系统隔振器刚度不变,将子系统充当一个6自由度吸振器进行刚度设计,按照H∞原则设计出空冷子系统的隔振器刚度。经过优化设计后,双层隔振系统既具备普通双层隔振系统优良的高频隔振性能,又能克服传统双层隔振系统低频隔振性能不足的缺点。
(2) 用子系统与激振力方向耦合的模态(y3向模态)控制主系统在激振力方向(α1向)的模态,可使子系统发挥较好的吸振作用。此时子系统的作用为:既减小了主系统的能量输入,又将二级主系统大部分振动能量转移到子系统本身,以达到减弱二级主系统振动和二级隔振器动反力的效果。
(3) 经过参数优化设计后,在柴油机机常规工况和停机工况,动力包动反力较小,机组和散热器振动烈度水平较优,动力包双层隔振系统隔振性能良好,满足工程设计要求。