【摘要】为改善分体式SCR系统安装空间要求高、尿素易结晶、维修成本高等缺点,设计了一种把喷嘴和SCR系统集成的结构;运用CFD方法对4种不同进口结构进行仿真对比,确认最优结构后制作样件,将新样件安装在发动机台架上进行结晶试验和排放试验。结果表明,SCR系统中无结晶并且能达到国IV排放要求,表明该集成式结构可行并且优于分体式结构。
1 前言
柴油机排气中PM、NOx是两种主要的排放污染物,且两者之间有着矛盾的生成关系。目前,机内净化已经无法满足需求,而机外净化已经成为趋势,其中SCR技术已经成为主要手段之一。SCR技术通过优化喷油和燃烧过程,尽量在机内控制微粒PM的产生,而后在机外处理富氧条件下形成的NOx,即使用车用尿素水溶液(体积分数为32.5%)对NOx进行选择性催化还原,还能降低部分HC,从而达到既节能又减排的目的,并且尿素溶液容易储存,常温下很稳定,没有刺激性气味。该项技术是欧洲主流技术路线,欧洲长途载货汽车和大型客车几乎全部采用这一技术,在国内正在成为最具有应用前景的柴油机后处理技术。本文将对传统SCR系统的结构进行优化设计,从而达到提高系统各方面性能的目的。
2 分体式SCR系统现状
传统的分体式SCR系统设计中,为使尿素和尾气达到很好的混合效果,一般将喷嘴安装在SCR系统进口前300 mm以上,如图1所示。
从图1可以看出,尿素从喷嘴喷出后,容易被直接喷射到排气管管壁上,虽然尿素液滴会随尾气蒸发掉大部分,但是依然会有一部分沉积在管壁上,久而久之形成液膜,进而形成结晶,其不但会对管壁造成腐蚀,还会堵塞管道,因此该结构不但在安装空间要求上有很大的局限性,而且因排气管腐蚀、堵塞后需要更换而造成运行成本和维护成本的上升。
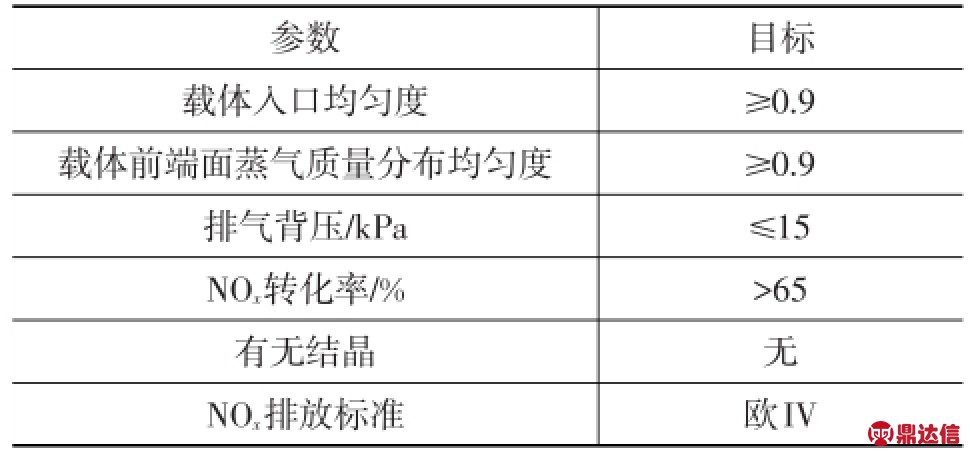
图1 传统SCR系统结构示意
分体式SCR系统尿素喷射状态如图2所示。
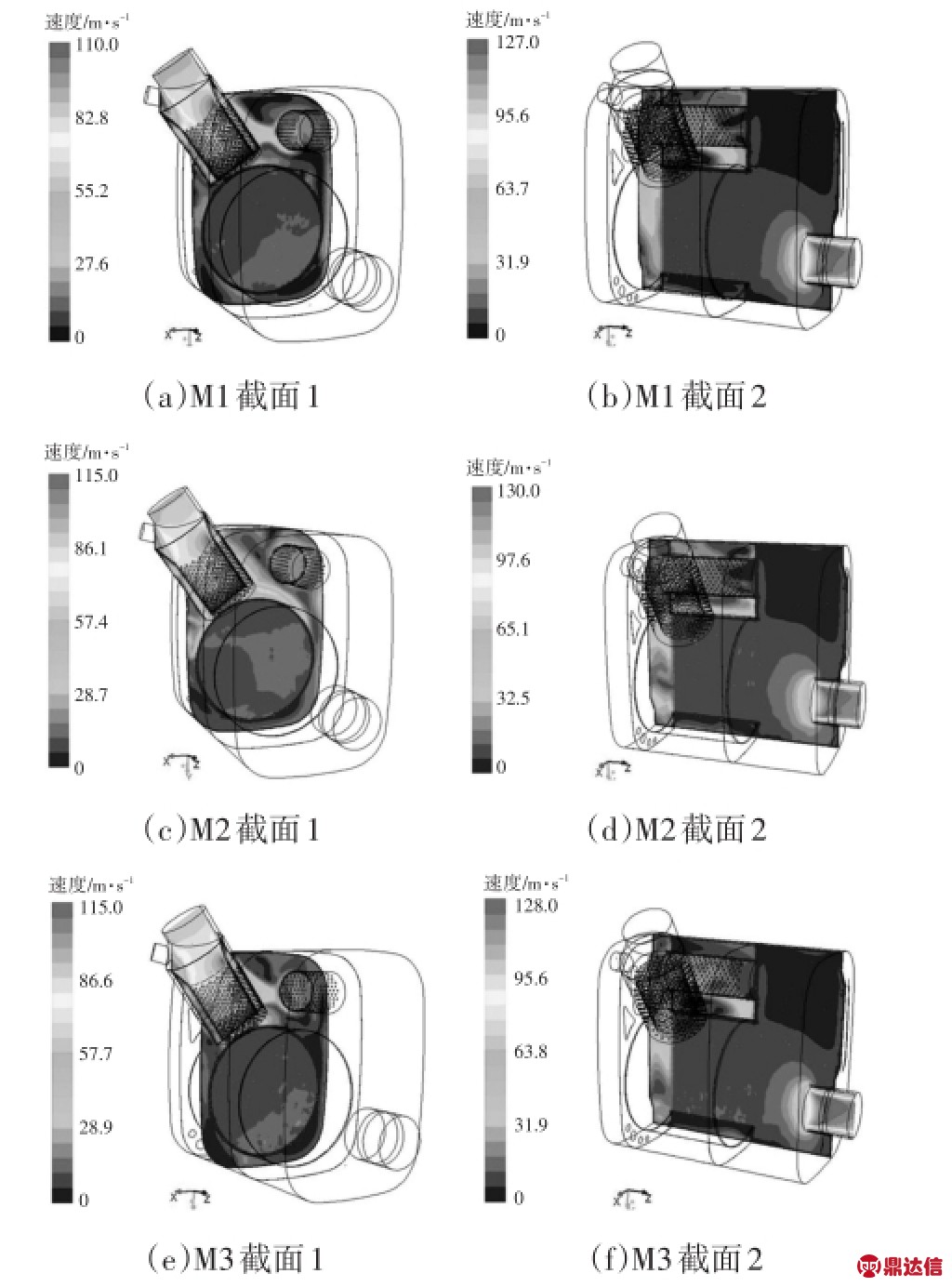
图2 分体式SCR系统尿素喷射状态
由图2可以看出,液体从喷嘴喷出后直接撞击在排气管壁上,此处的结晶风险非常高。
3 集成式SCR系统设计
将喷嘴集成到SCR系统进气口上是一个创新型的设计,不但可以节省安装空间、降低运行和维护成本,同时还能降低结晶风险和提高SCR系统的转化效率。因此,针对该新型的创新理念,并根据车厂提出的安装要求,设计开发集成式SCR系统,通过CFD仿真计算得出结构内部的流场、喷射、蒸发情况并以此来确定结构,同时通过试验验证这种结构是否可以满足各项技术要求。设计目标如表1所列。
表1 设计目标
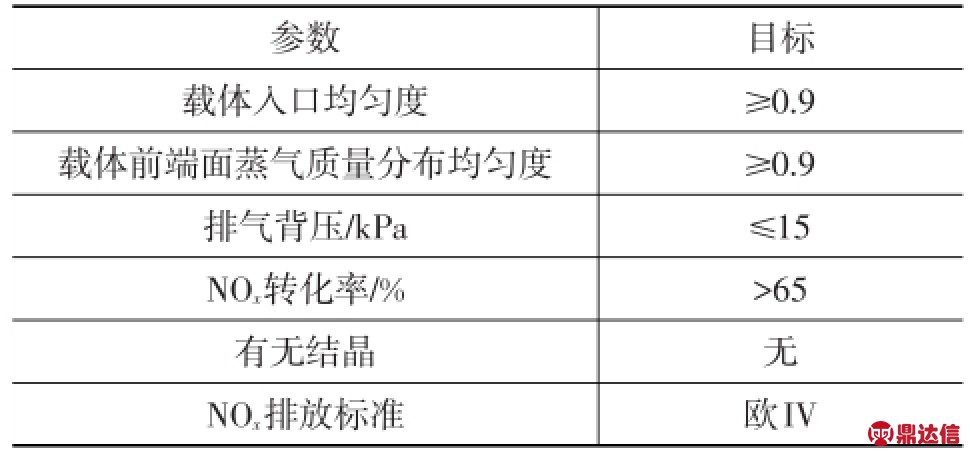
3.1 数学模型
采用FLUENT中的欧拉-拉格朗日离散模型,将空气处理为连续相,液滴处理为离散型,采用标准的湍流模型建立连续相和两相流中的DPM模型耦合的控制方程组进行计算。
3.1.1 连续相数学模型[2]
模型中包括连续性方程、动量方程、标准的k-ε湍流模型和能量方程。流体运动通用的控制方程为:

式中,ρ是连续相的密度;Φ是通用变量,可分别代表速度、动量、湍动能k、湍动能耗散率ε和温度;u是速度矢量;SΦ、ΓΦ分别是广义源项和广义扩散系数。
3.1.2 离散相颗粒的控制方程
FLUENT中通过积分拉式坐标系下的颗粒作用力微分方程来求解离散相颗粒的轨道。对每个单颗粒求解运动控制方程:
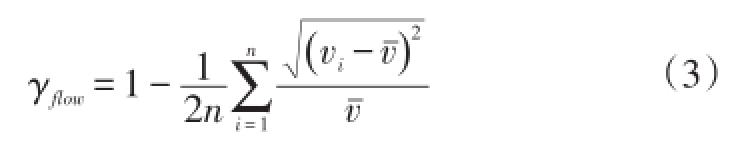
式中,vk为颗粒的运动速度;mk为该颗粒的质量;(∑F)k表示该颗粒所受的合力。
3.2 结构设计及CFD仿真计算
3.2.1 模型
图3为车厂提供的SCR系统进气口位置。可知,无法安装很长的进气管。
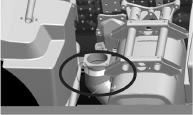
图3 整车总装图示意
为满足车厂要求,根据尾气进气方向,在进气口段设计一个斜台,将喷嘴的位置调成合适的角度安装在斜台上,并且把进口段设计成双层套管的形式,进口段结构决定着尿素与气体混合蒸发的程度,最终影响结晶的状态。针对该问题,设计4种不同进口结构的SCR喷射系统M1~M4,其中M1为套管底部全部封死;M2为中间封死,旁边敞开;M3为底部封死但是开孔;M4为中间封死但有鼓包,旁边敞开。结构如图4和图5所示。
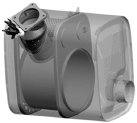
图4 集成式箱式SCR系统示意
3.2.2 网格生成
载体部分为规则实体,故采用六面体网格,其余部分的结构较复杂,故采用四面体网格,整体网格数量为170万。网格模型如图6所示。
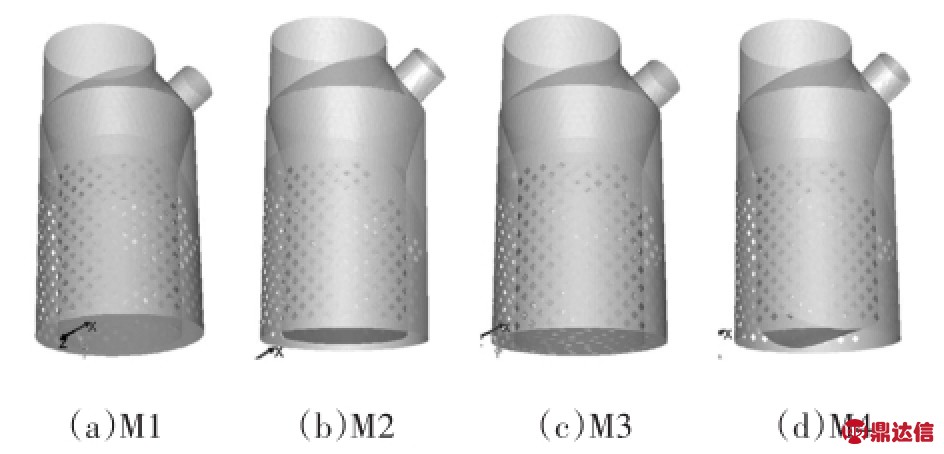
图5 4种不同进口结构的SCR喷射系统
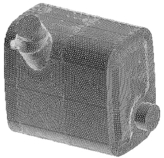
图6 网格模型
3.2.3 边界条件设置
a.流体相:气体为连续相。
b.颗粒相:采用压力旋流雾化模型,以水代替尿素水溶液[3],选择离散相和连续相耦合计算,动态曳力模型考虑颗粒的破碎与合并,破碎模型选择泰勒比模型,液滴为球形[4]。
c.进口边界条件如表2所列。
表2 进口边界条件

d.出口边界条件:SCR出口定义为压力出口。
e.壁面边界条件:连续相采用无滑移固体壁面边界条件,计算时为标准壁面函数法;颗粒相在壁面处不满足无滑移条件,与壁面的碰撞类型为escape类型。
3.2.4 仿真结果及分析
模型的2种截面如图7所示。
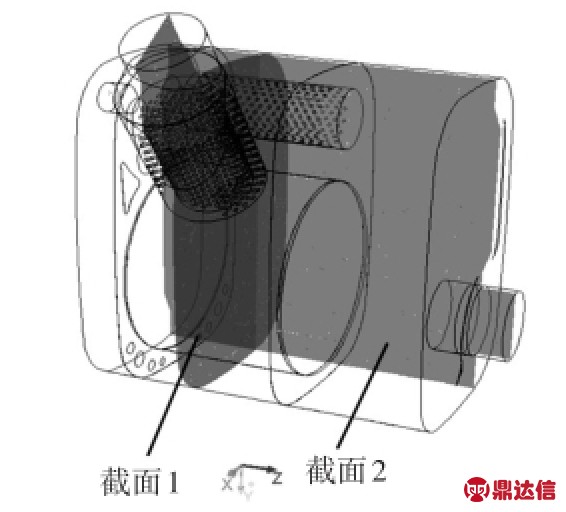
图7 模型截面
a.压力分布
截面的压力分布如图8所示。
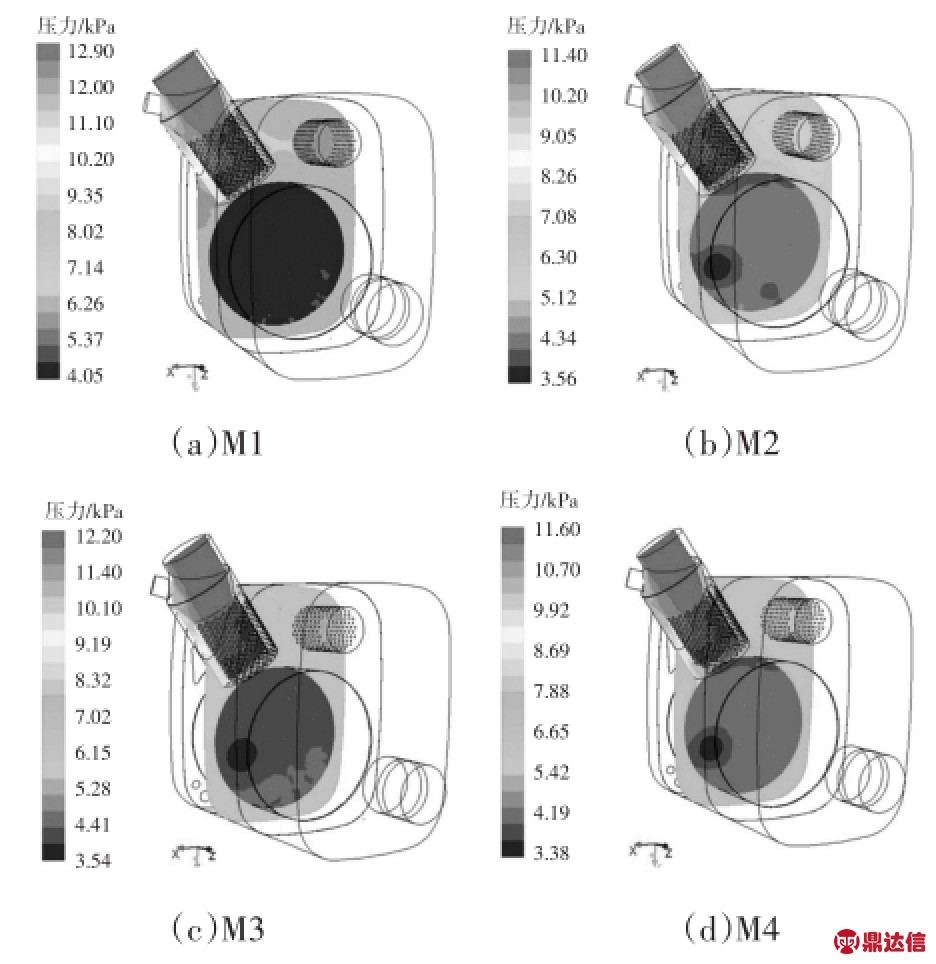
图8 截面的压力分布
由图8可以看出,4种模型的压力分布趋势基本一致,进口双层套管的压降很大,占总系统压降的一半,这是由于其是双层多孔管的结构形式,气流反复经过面积扩张和缩放造成的,在车厂提供的最大排气流量的工况下,系统总压降仍能满足≤15 kPa的设计要求。
b.速度分布
截面的速度分布如图9所示。
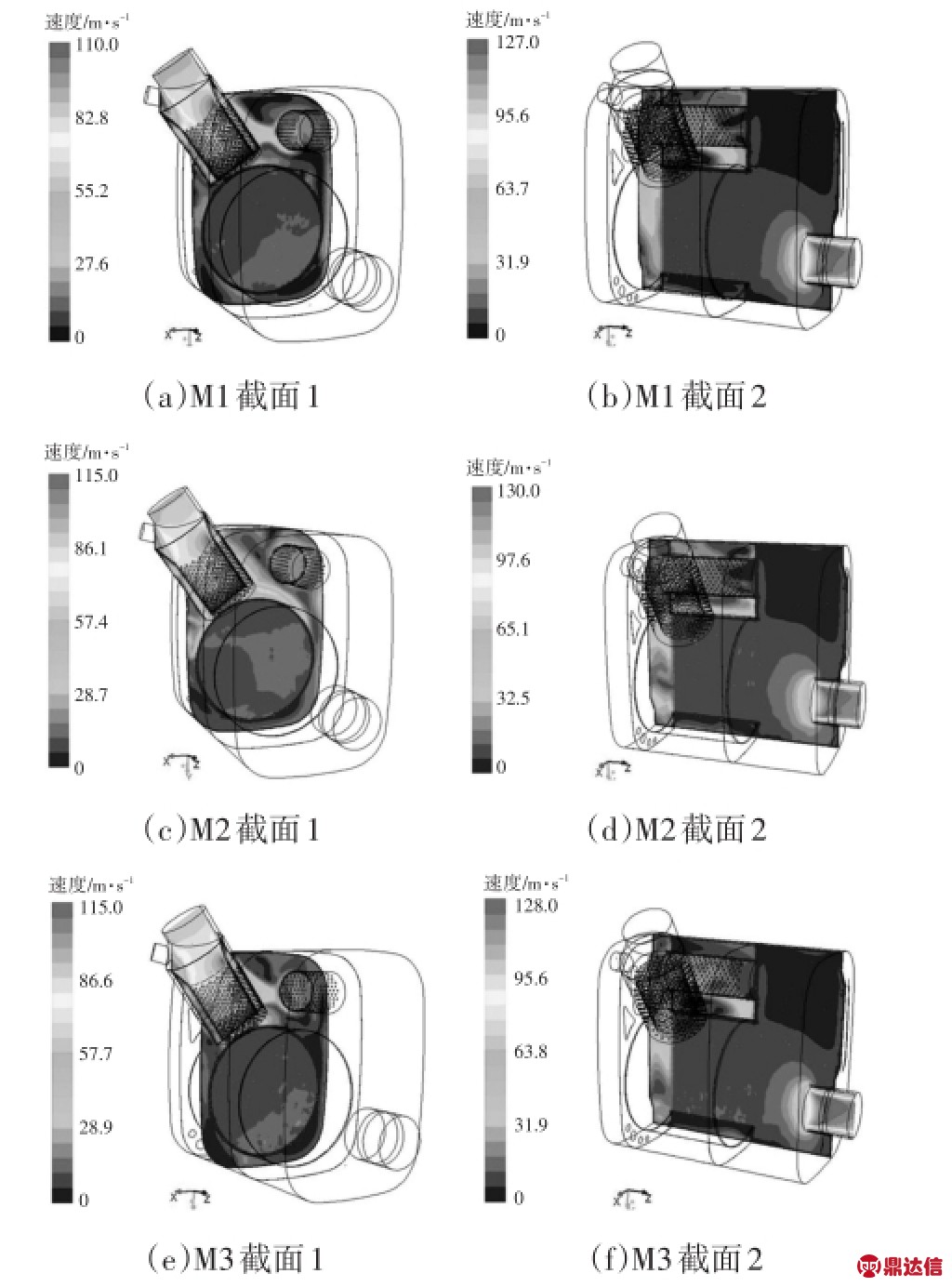
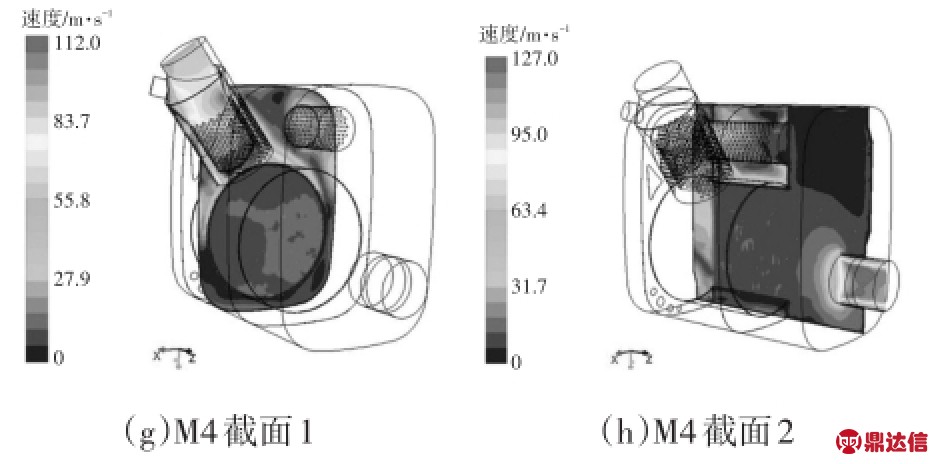
图9 截面的速度分布
从图9可以看出,4种模型的速度分布趋势基本一致,气流在经过双层套管时速度值有很大的梯度,腔体内的速度梯度不大,因此腔内的流场相对均匀。由于液滴粒子要随尾气进行扩散,因此腔内的流场最好是均匀的。
c.均匀度分布
对于SCR系统,要保证气流速度和反应物浓度的绝对均匀是不可能的,一般将不均匀度控制在可以接受的范围内。要研究各种因素对于均匀性的影响,必须对均匀性给出合理的评判准则。均匀度越大,表示分布越均匀,均匀度等于1表示分布完全均匀。
载体中间截面上速度分布及流动均匀指数γflow的关系为:
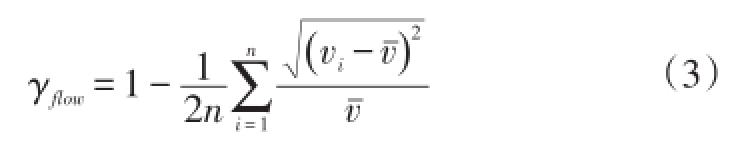
式中,vi为某个截面各单元网格上的气体速度值;vˉ为某个截面上气体速度的平均值;n为截面上的网格总数。
载体中间截面速度分布均匀度如图10所示。

图10 载体中间截面速度分布均匀度
从图10可以看出,M1的分布较好,M3与M4差别不大,M2较差。
载体入口截面上蒸气质量分数分布及蒸气均匀分布指数γvapor的关系为:

式中,mi为某个截面上各单元网格上的蒸气质量;mˉ为某个截面上蒸气质量的平均值。
载体入口蒸气分布均匀度如图11所示。
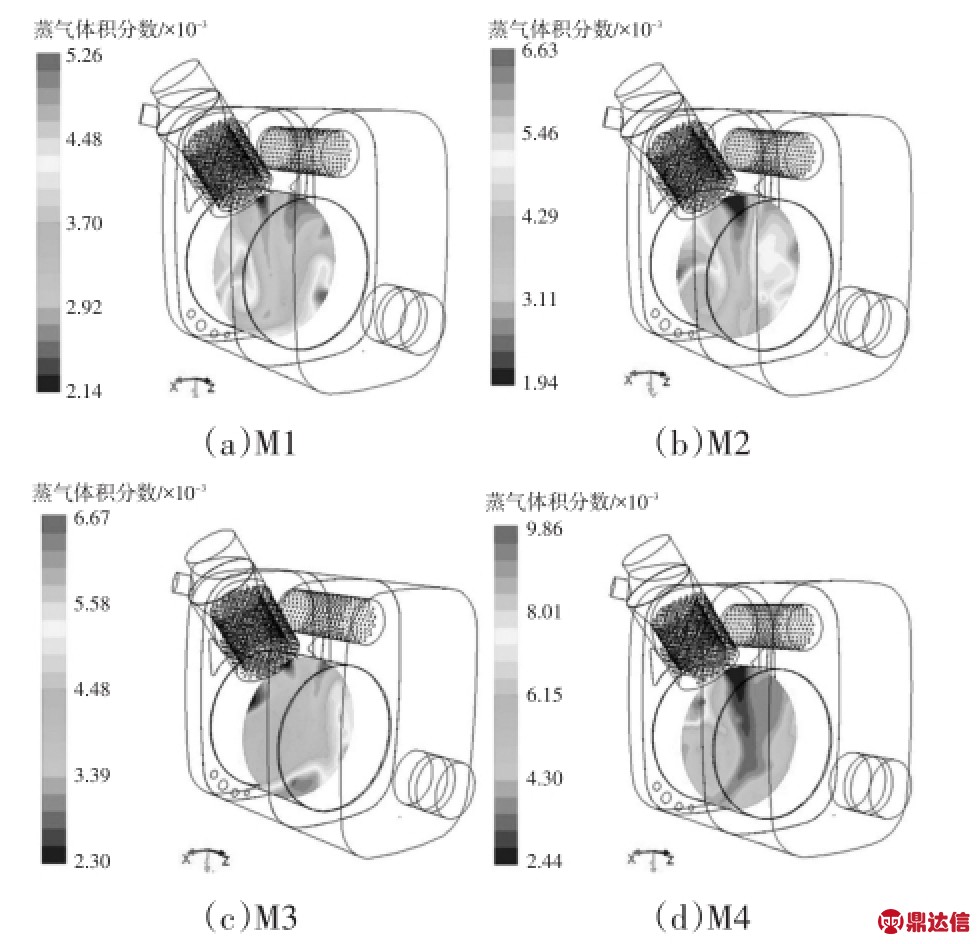
图11 载体入口蒸气分布均匀度
从图11可以看出,M1与M3分布较好,M2与M4分布较差。
速度分布和蒸气质量分布均匀度直接共同决定着SCR系统的NOx转化效率。综合来看,M2和M4的转化率会较差。
d.粒子喷射轨迹
通过观察粒子的运动轨迹,可以判断液滴蒸发、结晶的情况[5]。液滴粒子轨迹如图12所示。
从图12可以看出,双层套管的结构有助于增加液滴粒子的运动路径,从而能增强液滴粒子蒸发效果,且由于喷嘴合适的安装位置和角度,使得液体喷出时撞击不到套管的管壁上,从而减少结晶的风险,并且液滴粒子在达到载体前端时基本上蒸发完毕。CFD结果如表3所列。
从以上各项仿真结果来看,在双层套管的底部开孔有助于蒸气分布均匀度,背压也有所降低,但是把底部全部打开,就会使得液滴粒子的运动轨迹缩短,不利于分布均匀性,而且会直接打在包住载体的内筒体上,因此在能满足设计目标的基础上,选择M1进行样件制作。