摘要:为了满足带轴锥齿轮超声研磨加工的谐振频率要求,利用波动理论对不同结构的3种带轴锥齿轮的超声变幅系统进行谐振设计,建立了统一的谐振频率方程,并对位移放大系数和最大应力进行了比较。运用有限元方法,对由复合变幅杆和换能器组成的超声激励-变幅振动系统进行了模态分析和谐响应分析。最后对超声振动系统进行了阻抗分析和频率测试。试验结果表明:实际超声振动系统的谐振频率为23.269 kHz,与设计频率误差约1.17%,试验结果与有限元分析和理论分析结果基本吻合,验证了理论设计的准确性。
关键词:锥齿轮;谐振频率;复合变幅杆;研齿;阻抗分析
0 引言
研齿作为大批量生产的汽车后桥准双曲面齿轮的精加工工艺,在实际生产中得到了广泛应用。传统的研齿方法材料去除率低,对齿面的修整作用效果不明显。为解决以上问题,进一步提高齿轮的精加工水平,在齿轮制造领域引入特种加工方法和复合加工技术势在必行[1-2]。秦慧斌等[3]、吕明等[4]将超声振动加工与传统珩齿工艺组合起来,对齿轮和变幅杆组成的振动系统进行了设计,提高了加工效率和轮齿精度。
魏冰阳等[5-7]对小模数弧齿锥齿轮的超声研磨进行了实验研究,结果表明:超声研齿与普通研齿相比,在齿面表面质量和材料去除率上都有明显的提高。但是齿轮的超声研磨加工需要专门的超声振动系统,一方面,由于较大模数的锥齿轮尺寸和质量较大,使超声研齿系统的谐振设计较为困难,需要将变幅杆和齿轮放在一起考虑[8];另一方面,齿轮的研磨等需要适合的振幅才能达到较好的效果[9]。其中,变幅杆动态特性直接影响着超声研齿振动系统的性能,从而决定被加工零件的精度和加工效率。本文对中等模数螺旋锥齿轮的复合变幅杆进行设计,并比较了它们的放大倍数和最大应力情况。同时对换能器也进行了简单的设计,并将设计的复合变幅杆和换能器组合成超声振动系统,在有限元软件中进行动力学分析,然后制作出所设计的超声研齿系统,并进行了频率测试,以验证超声研齿系统理论设计的正确性。
1 复合变幅杆的数学模型
超声研齿振动系统由超声换能器、变幅杆以及被研的带轴的锥齿轮组成,其结构示意图见图1。
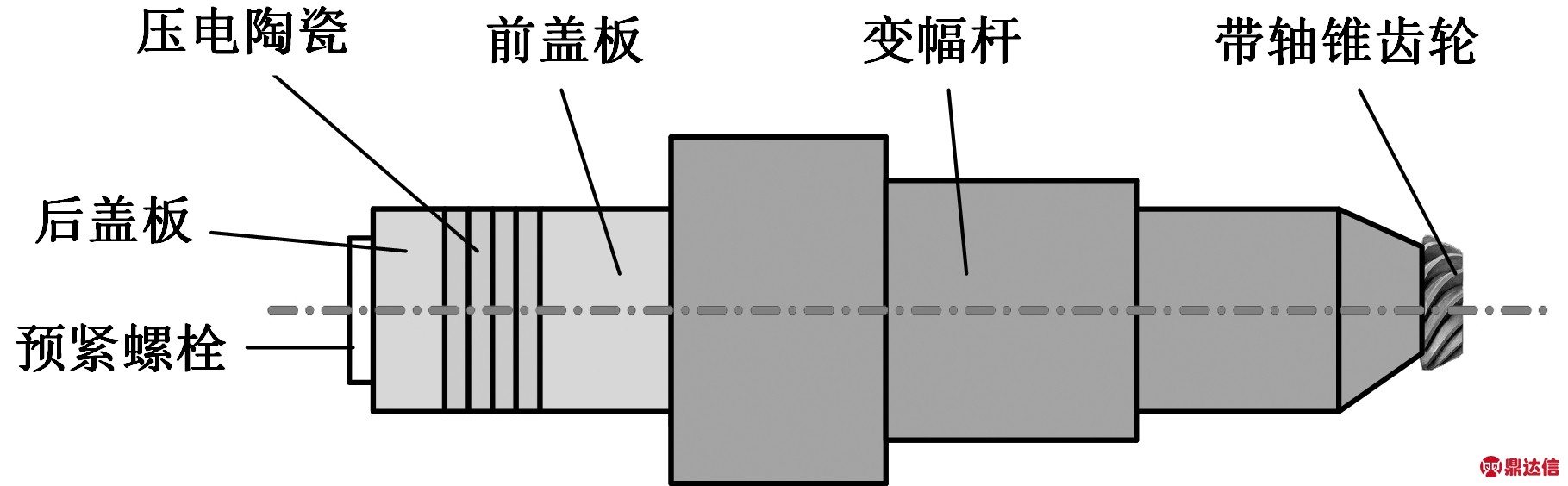
图1 超声研齿振动系统示意简图
Fig.1 The sketch of ultrasonic gear-lapping system
换能器将超声波发生器产生的超声信号转化为机械振动,通过变幅杆的振幅放大作用,产生研齿加工所需要的能量。对于不同结构和材质的变幅杆,其放大倍数、形状因数等特性均不相同,这些特性对变幅杆的性能影响很大。由于阶梯型变幅杆具有放大倍数和形状因数较大且易于加工等特点,因而被广泛应用。鉴于工件齿轮的质量较大,对整个系统有明显的影响,所以在设计变幅杆时,需要综合考虑变幅杆与齿轮。本文考虑了3种不同结构的变幅杆与被简化的带轴的锥齿轮组成的复合变幅杆并进行谐振设计和分析。3种复合变幅杆的结构简图见图2。
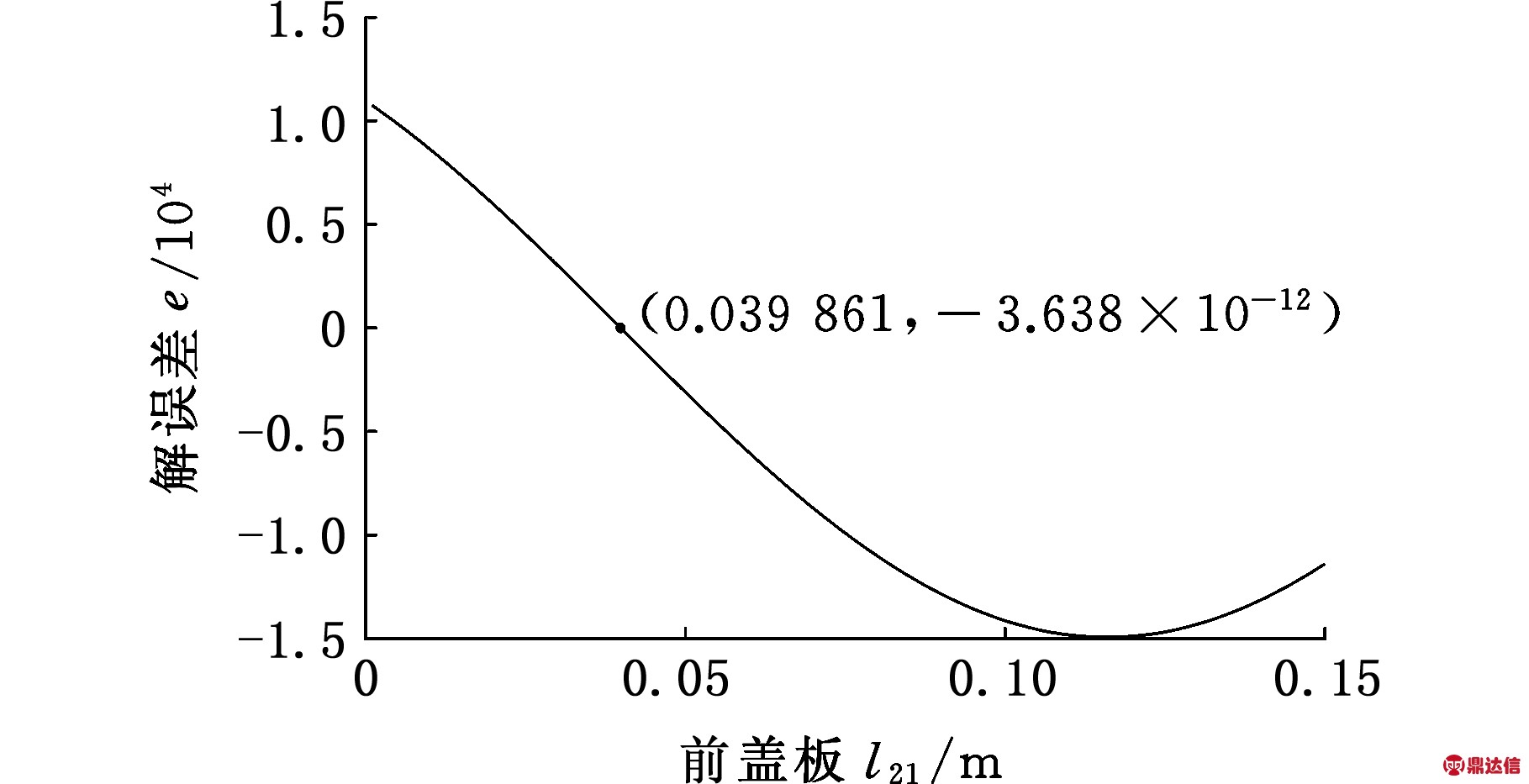
(a) (b)
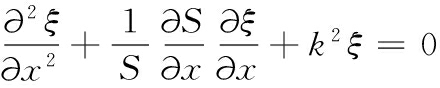
(c)
图2 复合变幅杆的示意简图
Fig.2 The sketch of compound horn
根据这3种变幅杆的结构特点,建立统一的数学模型坐标系,如图3所示:以复合变幅杆的轴向为x向、径向为y向建立坐标系,原点设置在变幅杆节面与变幅杆中心线的交点处。
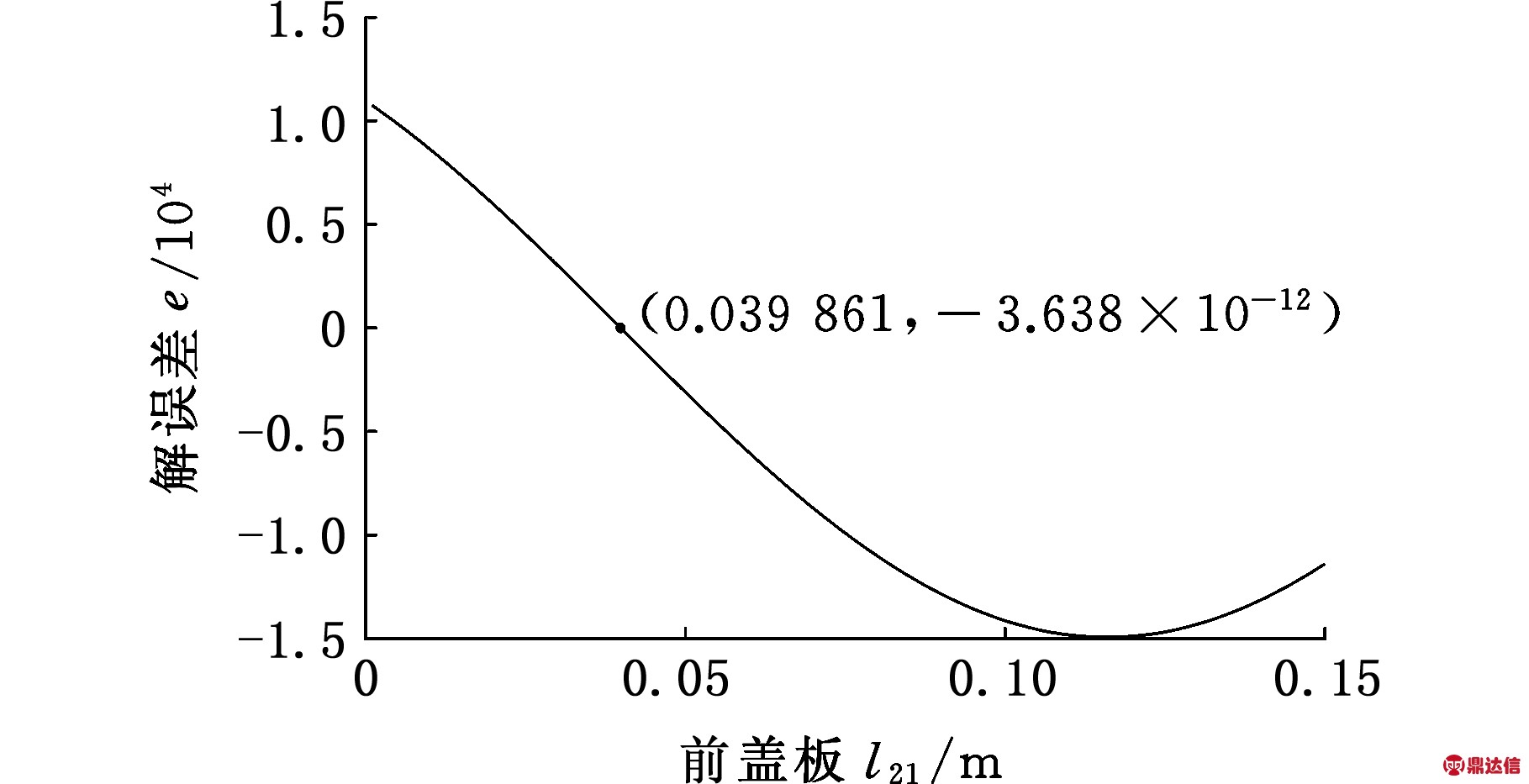
图3 复合变幅杆的理论数学模型
Fig.3 The mathematical model of compound horn
考虑到轴齿轮与变幅杆材质不同,将复合变幅杆分成5段,l1、l2、l3、l4、l5为各段的长度,ξ0、ξf分别为复合变幅杆的输入端位移和输出端位移。S1、S2、S3、S40、S41、S50、S51分别为复合变幅杆各段的横截面积,根据不同的S2、S3、S40、S41,即可得到图2中a、b、c三种不同形式的复合变幅杆。
2 超声振动系统的谐振方程
假设变幅杆由均匀、各向同性材料所构成,不考虑机械损耗,当其横截面尺寸远小于波长时,其横向位移与纵向位移相比甚小,可略去不计,此时在变幅杆的横截面上,质点位移分布是均匀一致的[10]。在简谐振动情况下,杆的纵向振动的波动方程为[11]
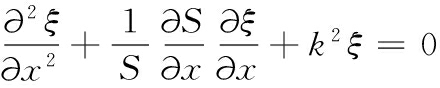
(1)

式中,k为圆波数;ω为圆频率;c为纵波在系统中的传播速度;E为弹性模量;ρ为密度。
由式(1)可得复合变幅杆各段的位移表达式:
ξn(x)=

(2)

式中,An1、An2为待定系数;n为对应变幅杆的段数。
对应的应变函数的表达式为
εn(x)=
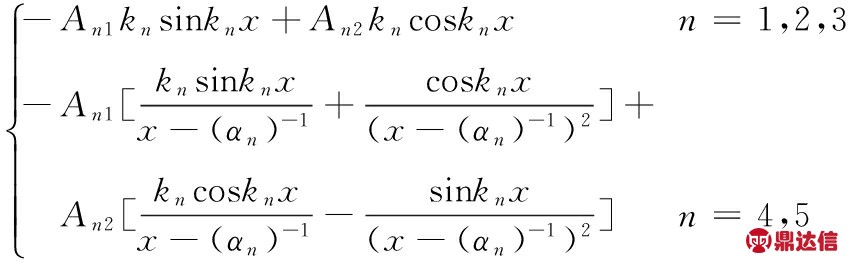
(3)
复合变幅杆纵向自由振动时,应满足力和位移的连续条件及边界条件,对于复合变幅杆的左端面:
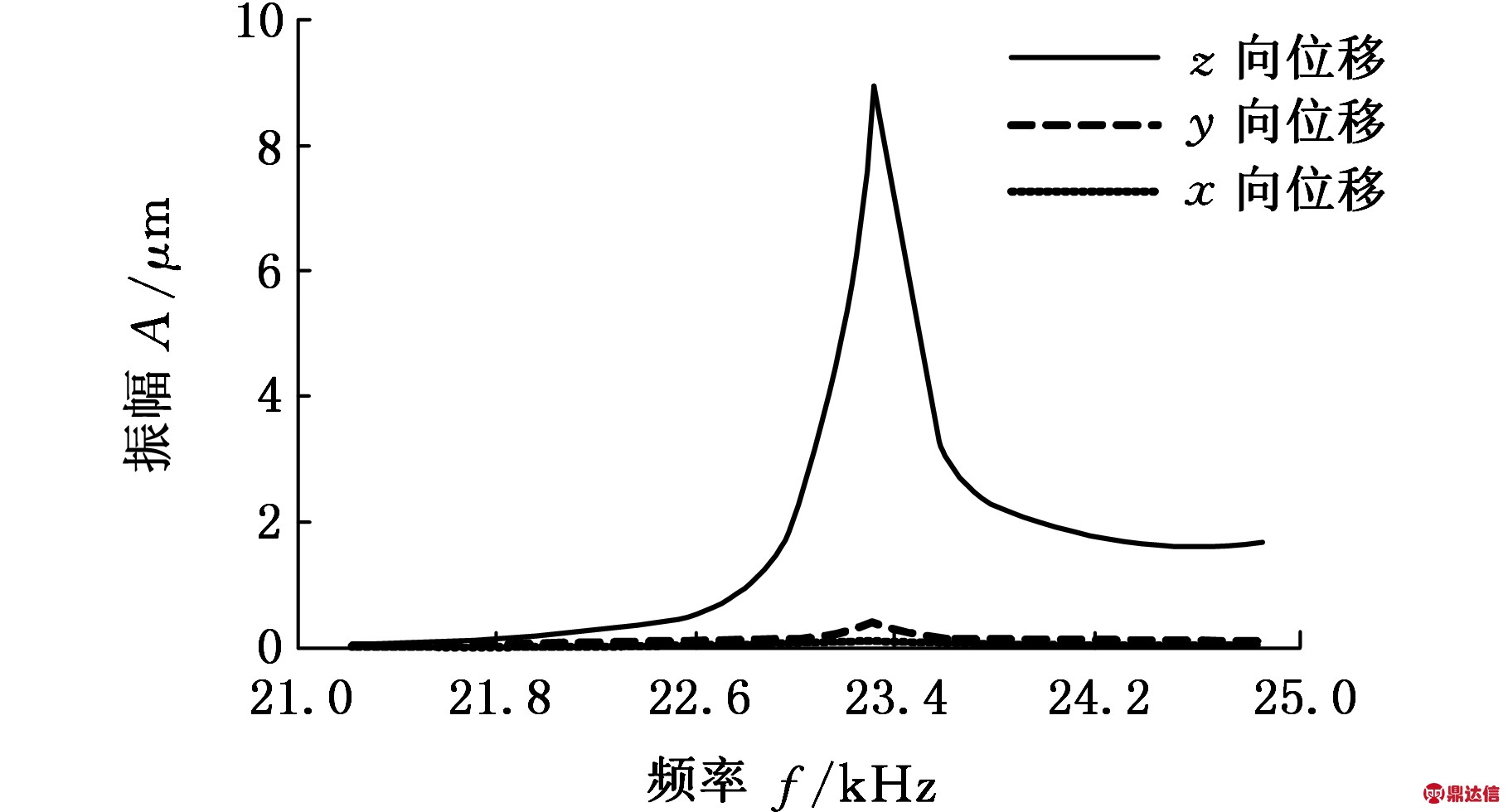
(4)
中间各段连接处应满足:

(5)
n=1,2,3,4
复合变幅杆的右端面应满足:

(6)
将式(2)、式(3)分别代入式(4)~式(6),经过化简后可得到一组线性方程:
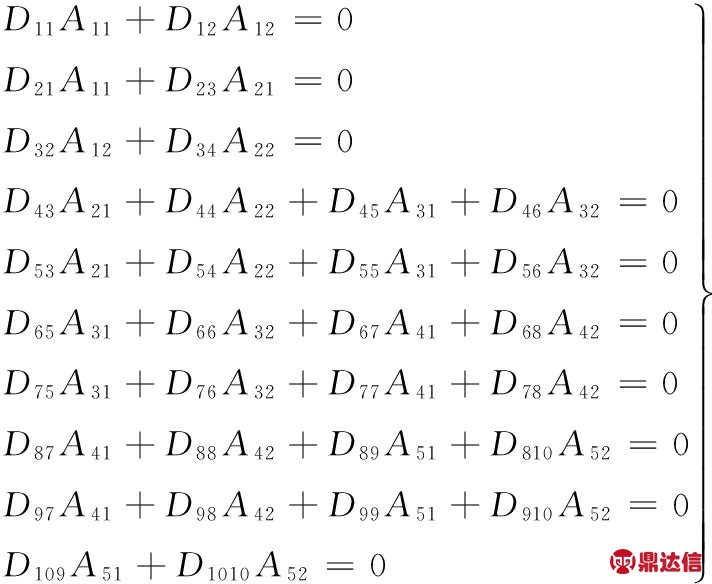
(7)
Δ=
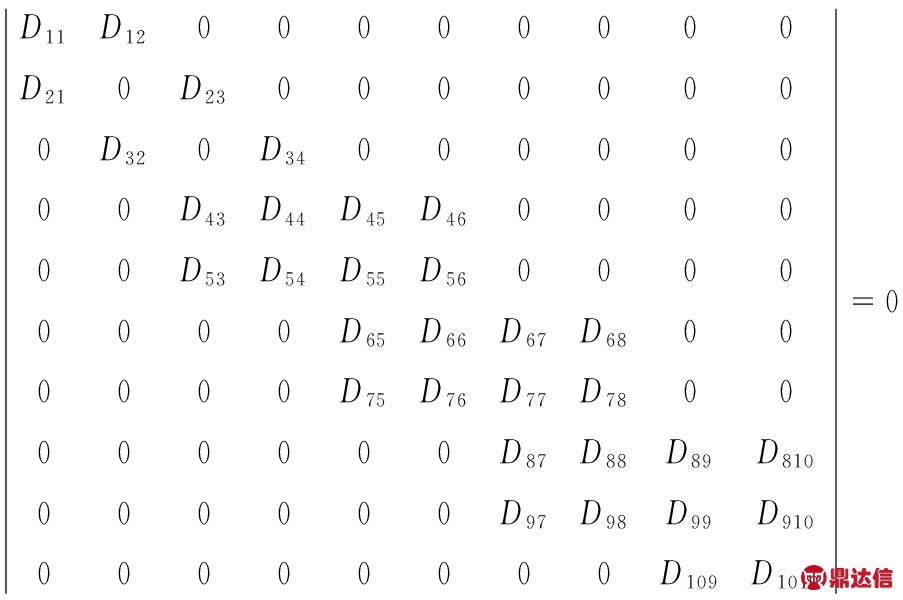
(8)
其中,Dij分别为式(2)、式(3)中An1、An2的系数。
式(7)中An1、An2的系数组成的行列式即复合变幅杆的谐振频率方程(8)。依据此方程可对复合变幅杆进行参数设计。
同时,还可得到复合变幅杆的振幅放大倍数M:
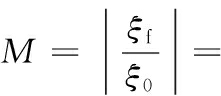

(9)
3 复合变幅杆的设计
复合变幅杆的设计谐振频率f=23 kHz,材料为钛合金,齿轮的材料为20 CrMnTi,复合变幅杆各段的材料属性见表1。
由于第Ⅲ、Ⅳ段中同时含有齿轮轴和变幅杆两种材料,故密度和声速的等效公式如下:
表1 材料特性参数
Tab.1 The characteristic parameters of material
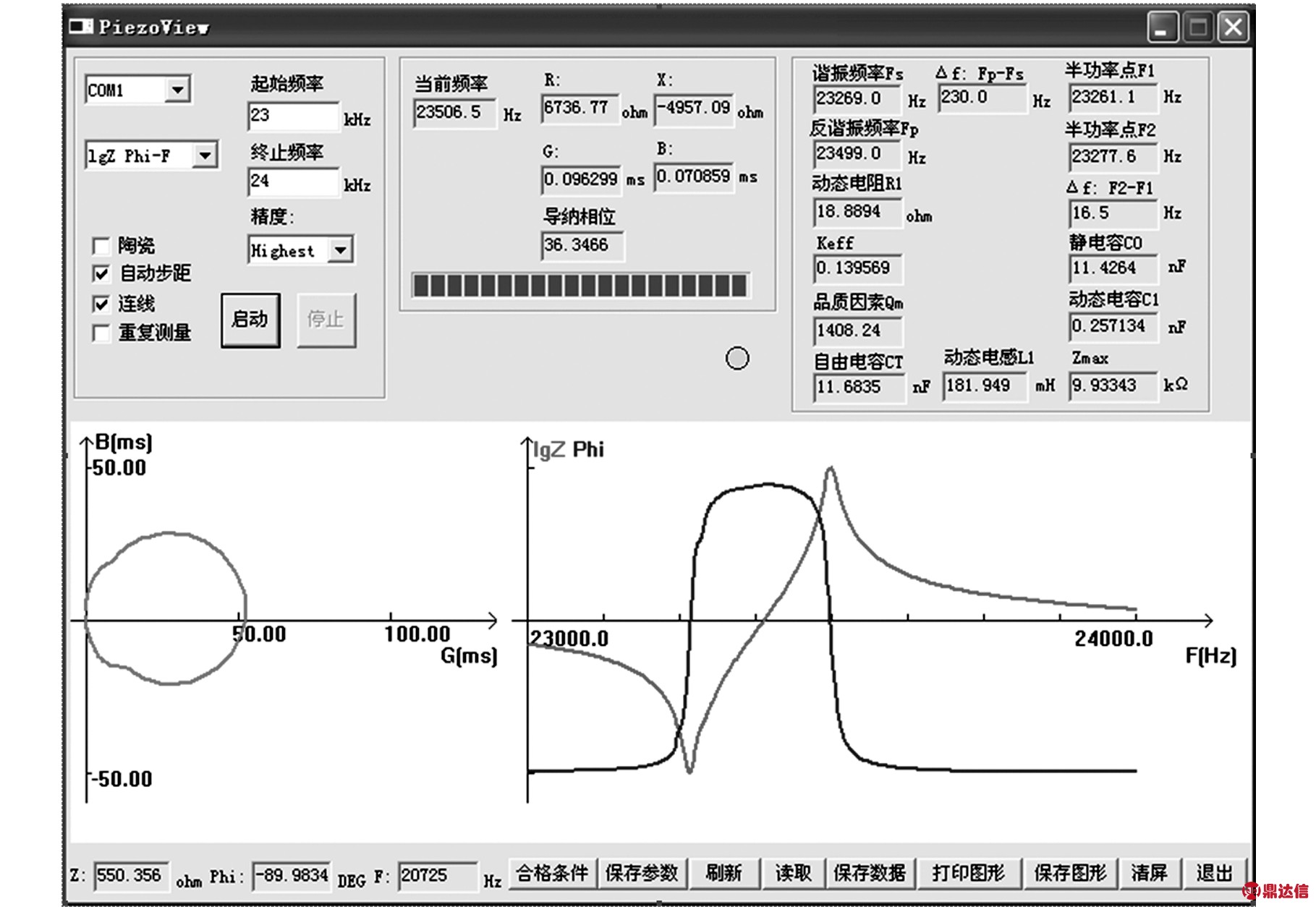
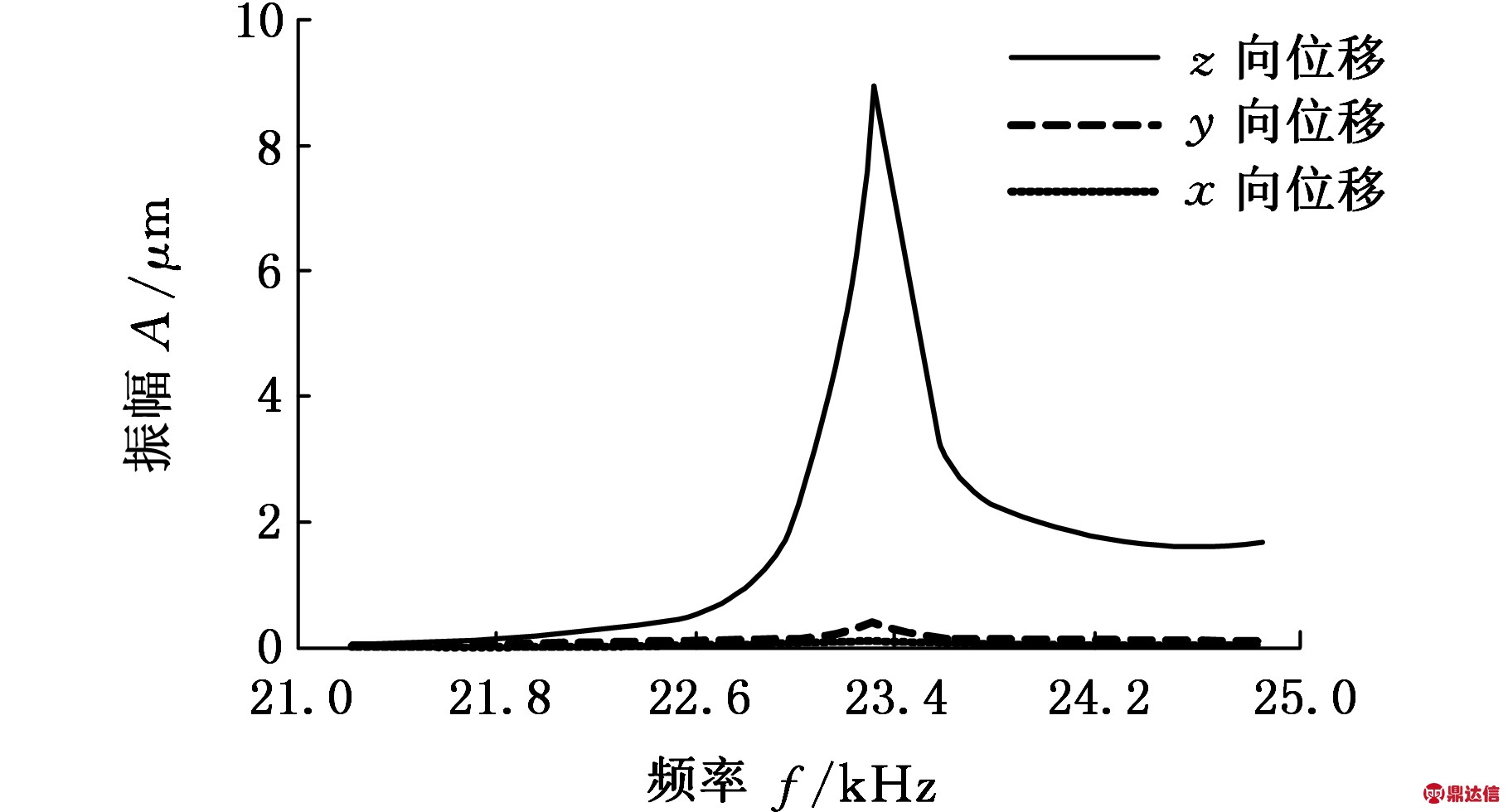
(10)
式中,ρp、ρb分别为钛合金和锥齿轮的材料密度;cp、cb分别为钛合金和锥齿轮的材料声速。
根据带轴锥齿轮的结构特点,复合变幅杆的初始设计尺寸参数见表2。
表2 复合变幅杆的初始尺寸参数
Tab.2 The initial parameters of compound horn
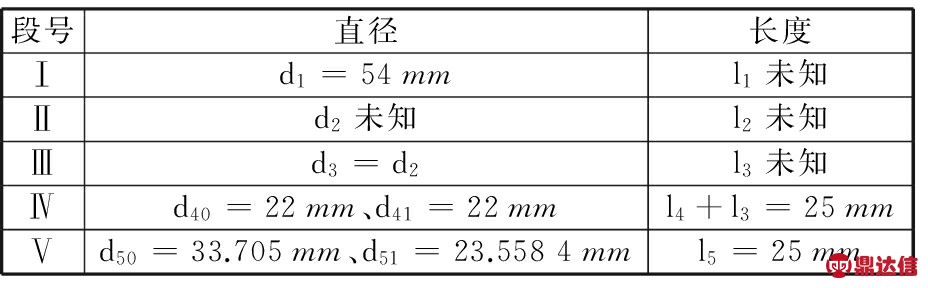
由于复合变幅杆的节面位置位于第Ⅰ段与第Ⅱ段的连接面处,故l1决定着预设节面处的位移大小。根据机械波在介质中传播的位移函数可以得到预设节面处的位移,从而可得l1与预设节面处位移的关系,如图4所示。由图4可知,当节面处的位移为0时,l1为56.81 mm。
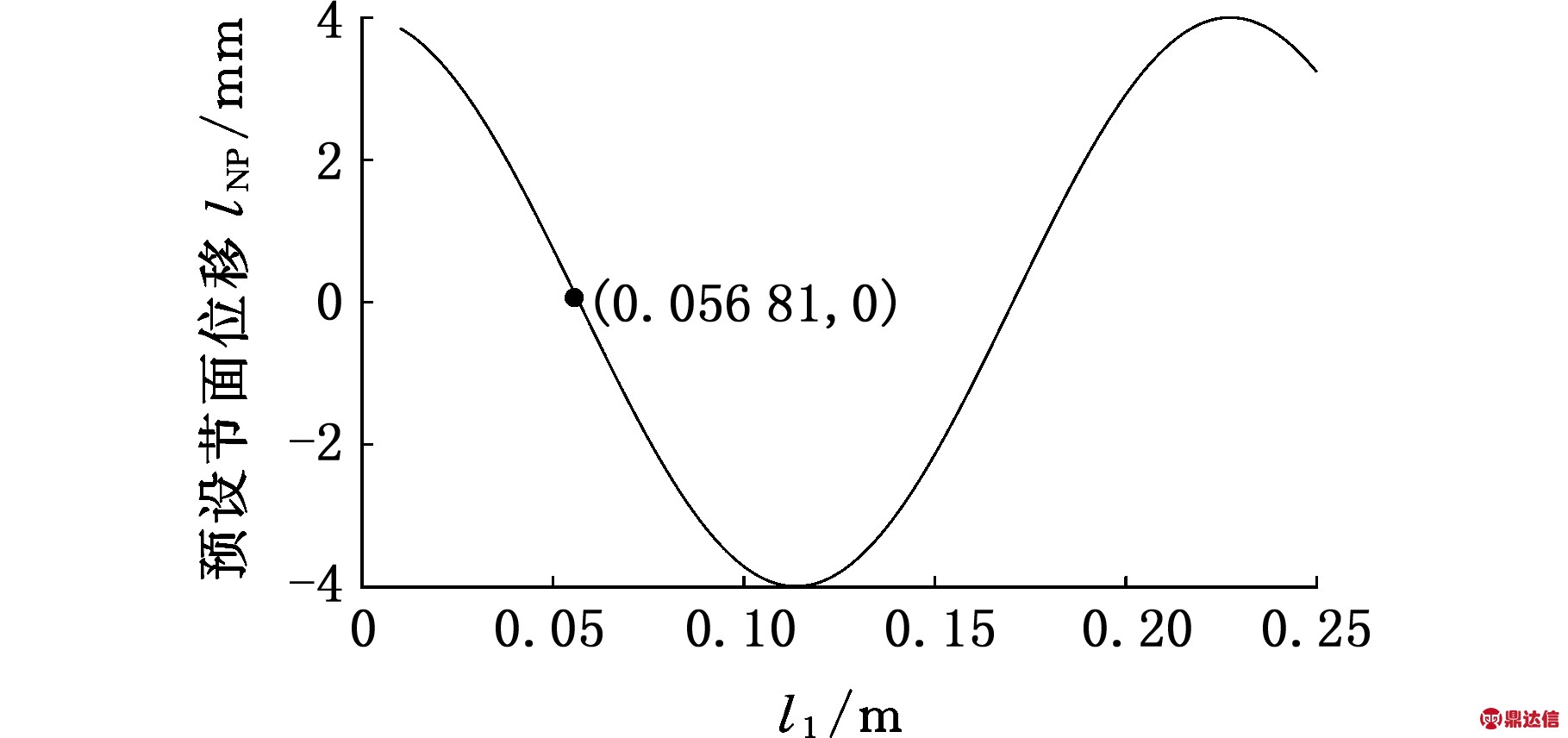
图4 l1与预设节面位移的关系
Fig.4 The relation between l1 and the position of nodal plane
将l1的值代入谐振频率方程,可以得到关于未知参数l2、l3和d2的关系。同时这些参数的大小又由锥齿轮和换能器的参数所限制,故它们必须在一定范围内变动,l2、l3和d2的关系曲面如图5所示。
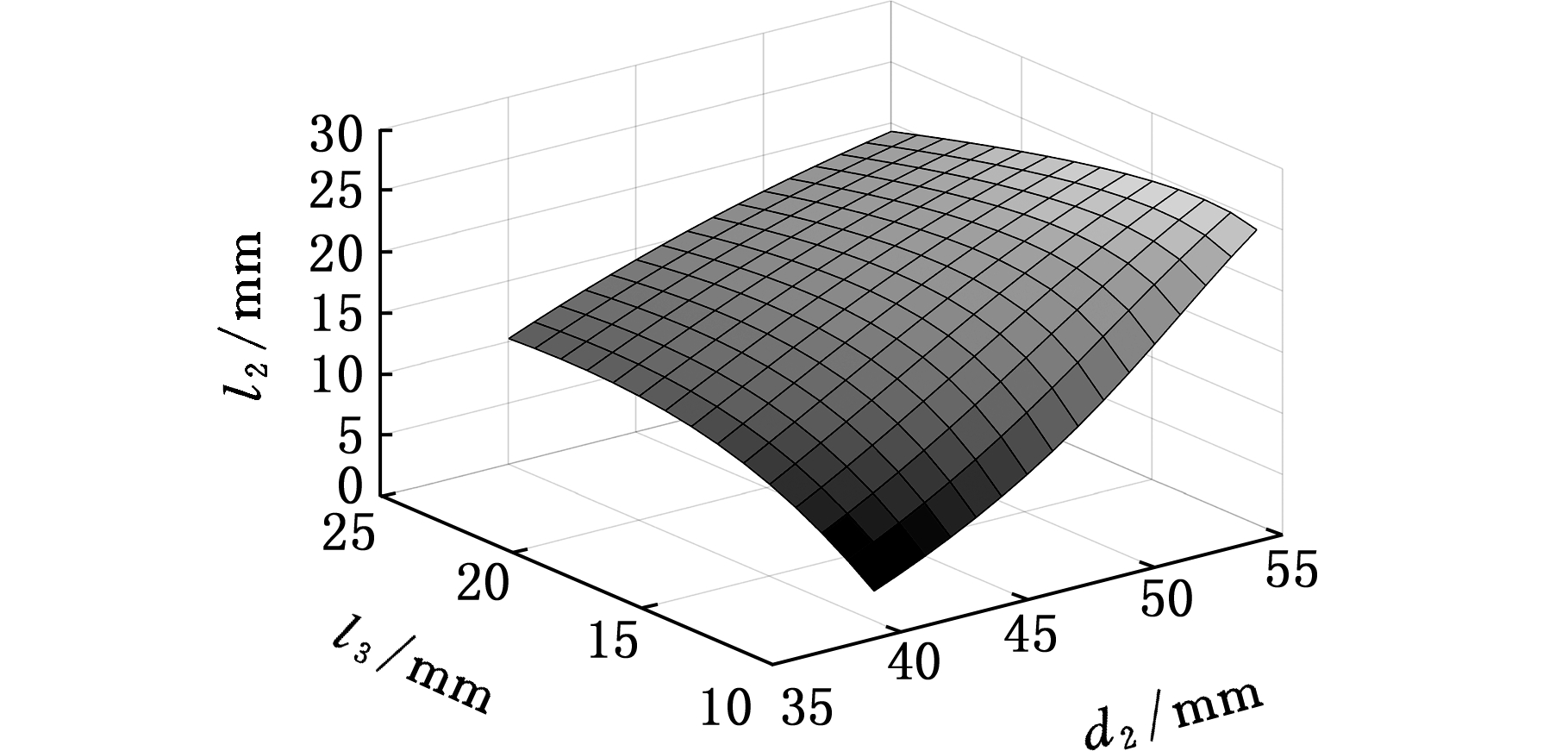
图5 l2、l3和d2的关系曲面
Fig.5 The relationsurface of l2,l3and d2
由上述l2、l3和d2的关系曲面以及l2和d2的关系曲线,同时考虑到换能器和锥齿轮的实际情况,可以确定其他未知参数。为保证所得参数满足谐振要求,设置l2值附近的一个范围,将所有设计参数和l2的一个范围重新代入谐振频率方程(8)得到计算频率,定义频率方程解误差e为计算频率与设计频率的差与设计频率的比值,可得出不同l2与e之间的关系,如图6所示。由图6可知,当l2=10.9 mm时,频率方程解误差值e约为0,使复合变幅杆在设计频率处达到谐振,满足设计要求。
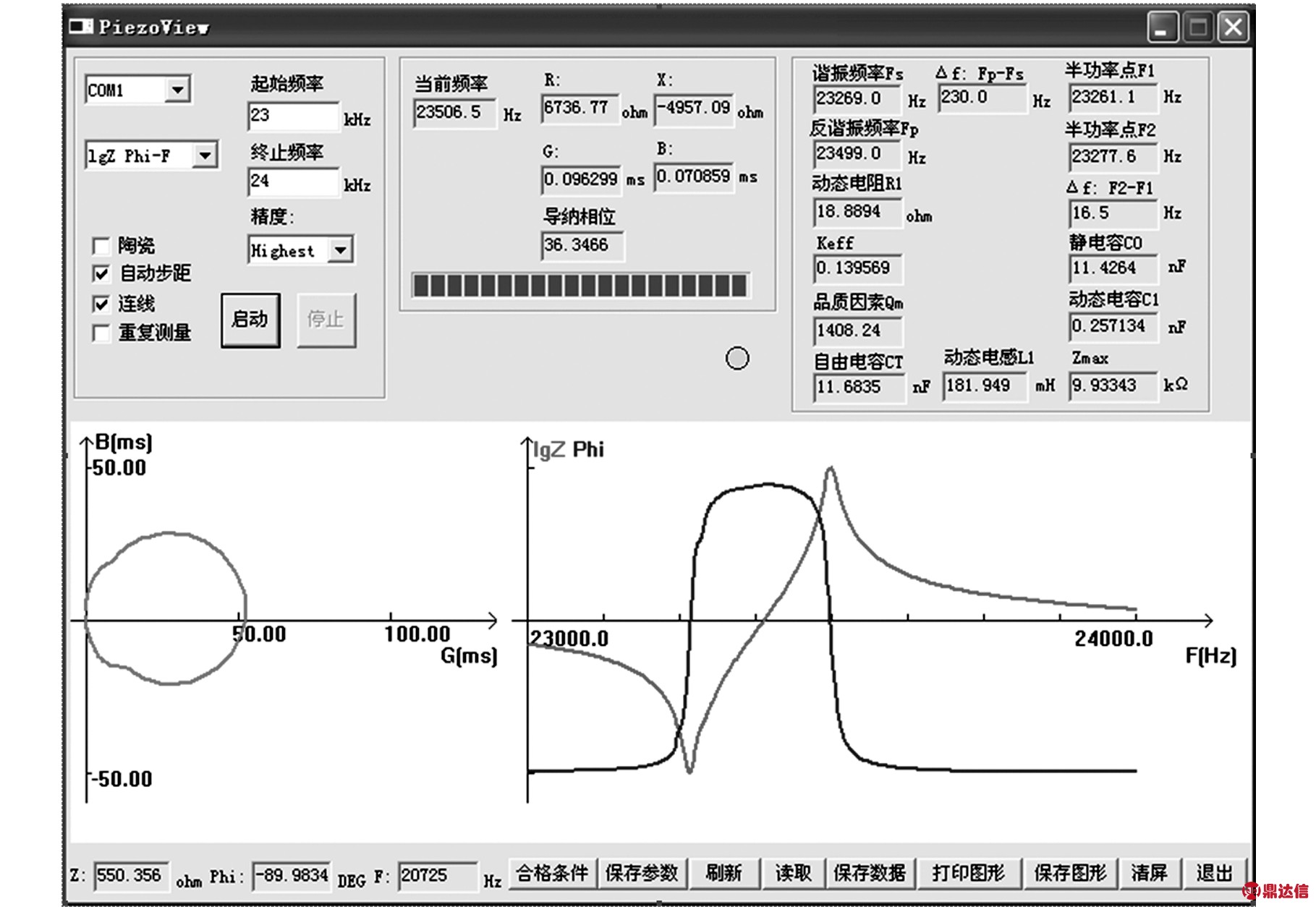
图6 l2与频率方程解误差e的关系
Fig.6 The relation between l2 and the error e of frequency equation
假定复合变幅杆输入端的振幅ξ0为4 μm,将上述设计的复合变幅杆的参数代入到根据力和位移的连续条件和边界条件所列的方程组中,求解可得到系数A11、A12,A21、A22,…,A51、A52的值,然后将其代入复合变幅杆各段的位移函数中,可得复合变幅杆的位移分布曲线,如图7所示。由图7可以看出,复合变幅杆的位移在齿轮小端面处达到最大值,符合设计的要求。
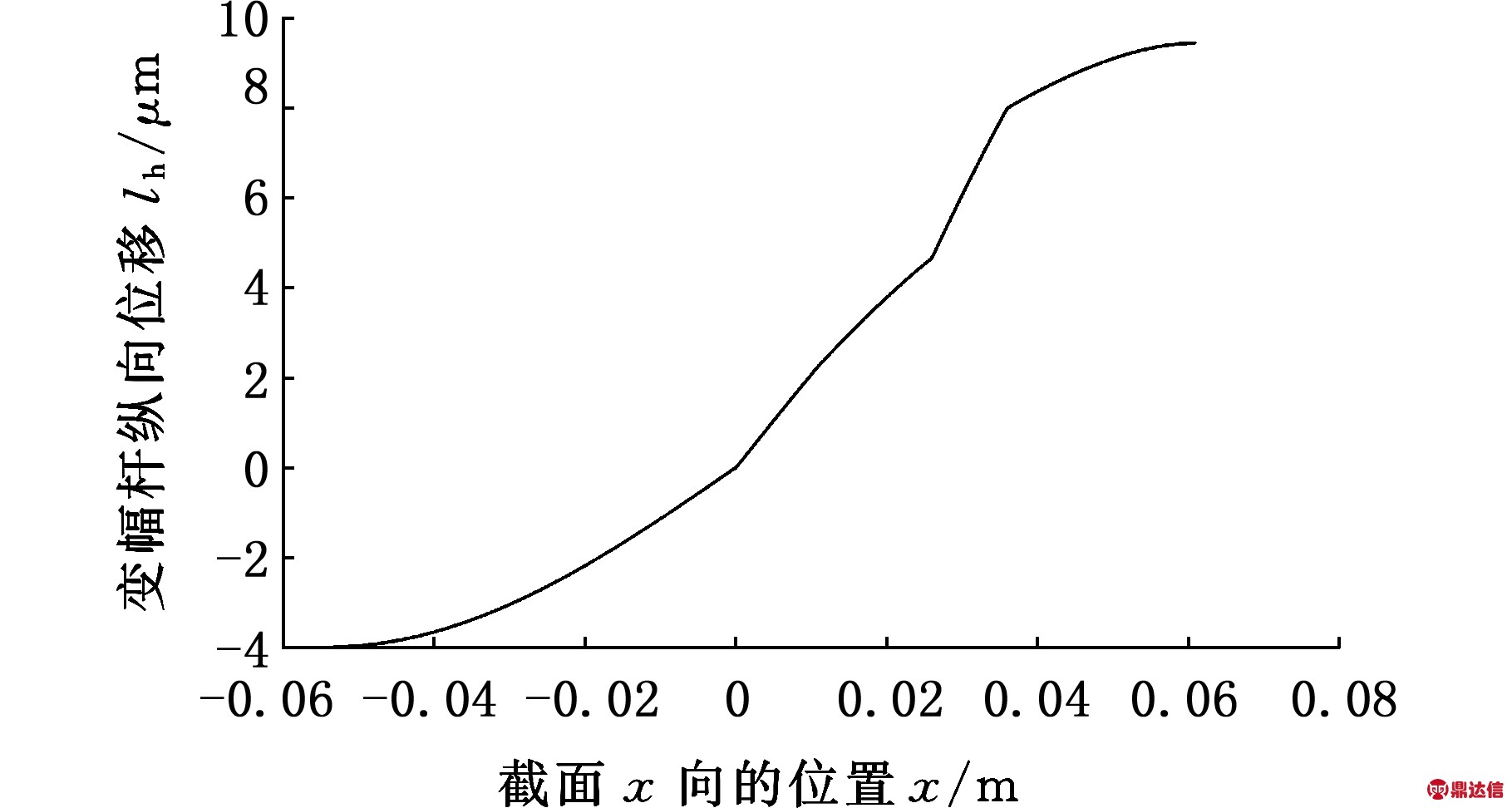
图7 变幅杆位移分布曲线
Fig.7 The displacement curve of compound horn
根据上述设计参数可得变幅杆的振幅放大倍数M=2.36,代入式(3)后可得截面突变处最大应力
σmax=Enεmax=343(MPa)
(11)
根据上述方法,对于其他两种复合变幅杆,可得对应的振幅放大倍数和最大应力,见表3。
表3 三种复合变幅杆的特性参数
Tab.3 The characteristic parameters of three kinds of horn
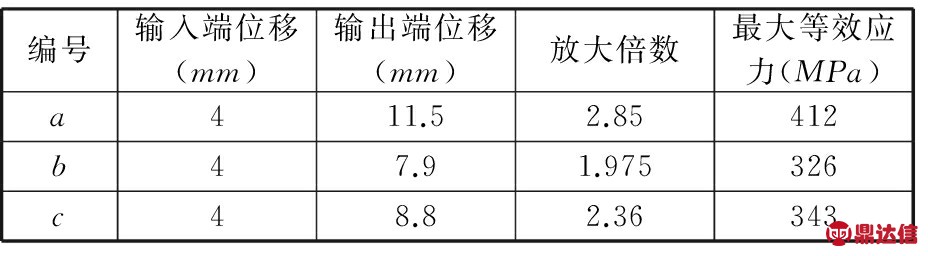
由表3可知:这3种复合变幅杆中,杆a的放大倍数最大,但截面突变处的最大应力也是最大的;杆b最大应力在三种复合变幅杆中最小,但其放大系数也是最小的;杆c放大倍数和最大应力均处于中等,最大应力小于材料的许用应力。基于安全可靠因素和实际的需求,选取第3种复合变幅杆做进一步的分析。
4 换能器的设计分析
换能器包括前后盖板、压电陶瓷、预紧螺栓,其结构示意图见图8。换能器的初始尺寸参数见表4。
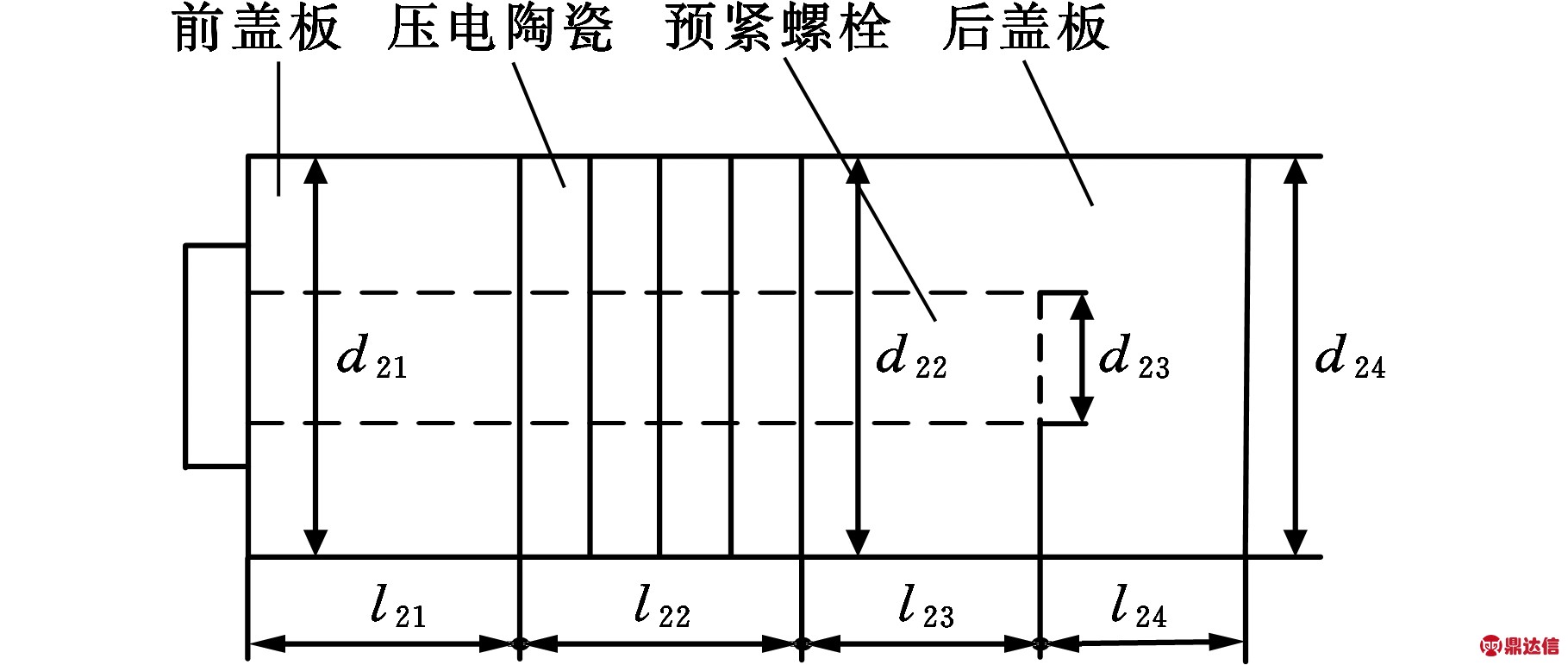
图8 换能器的结构示意图
Fig.8 The sketch of transducer
表4 换能器的初始尺寸参数
Tab.4 The initial parameters of transducer

前后盖板的材料选用不锈钢,压电陶瓷采用PZT-4。设计频率f=23 kHz。将上述参数代入谐振频率方程,可得到频率方程解误差与后盖板纵向长度的关系曲线,如图9所示。
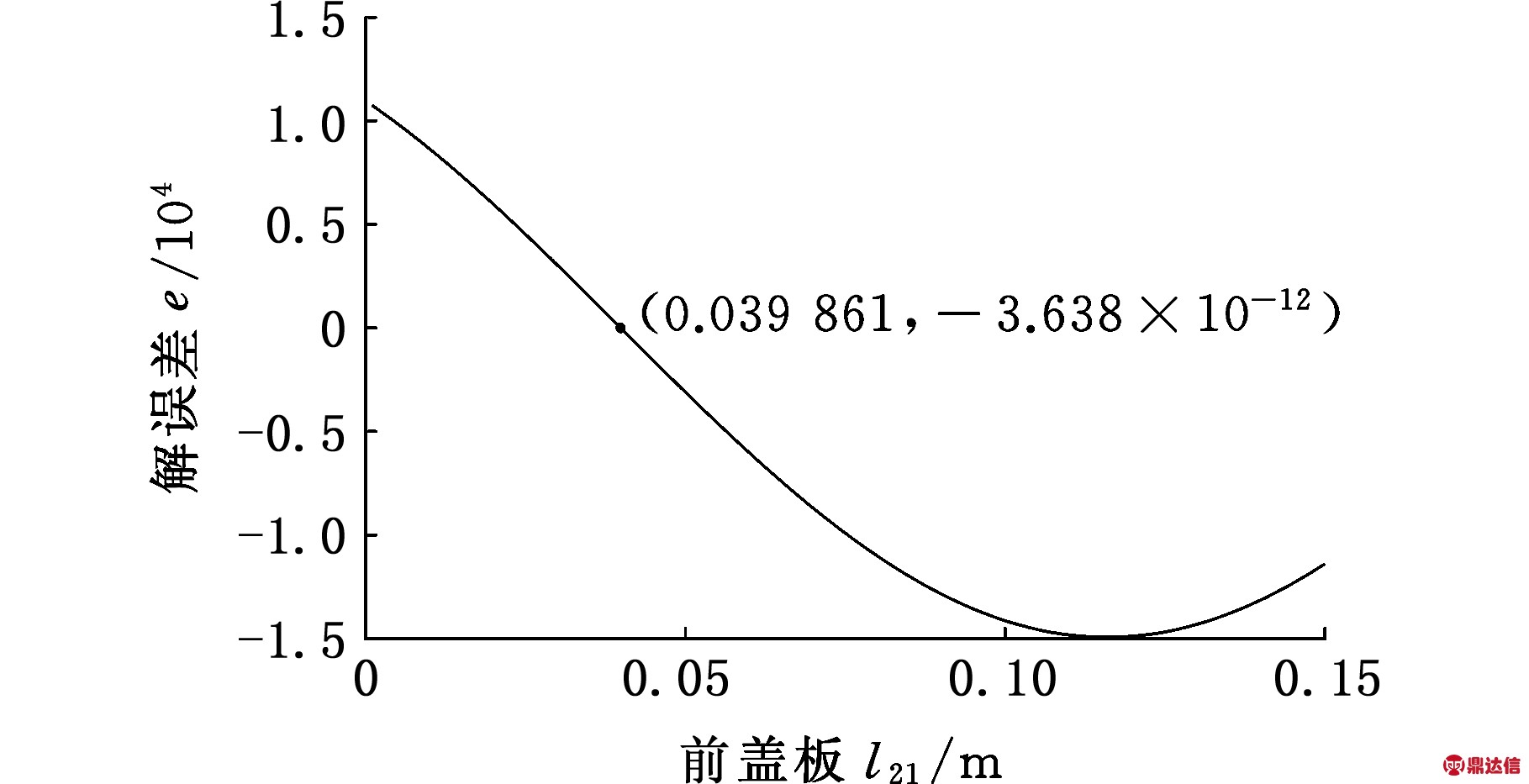
图9 l21与频率方程解误差e的关系
Fig.9 The relation between l21 and error e of frequency equation
由图9可以看出,当前盖板的长度l21为39.861 mm时,频率方程的解误差约为0,即满足换能器的谐振频率方程。假设换能器的输出端位移为4 μm,并将换能器的设计参数代入位移函数,可得其位移曲线,如图10所示。换能器的总长度为半个波长,在输出端时达到极大值。
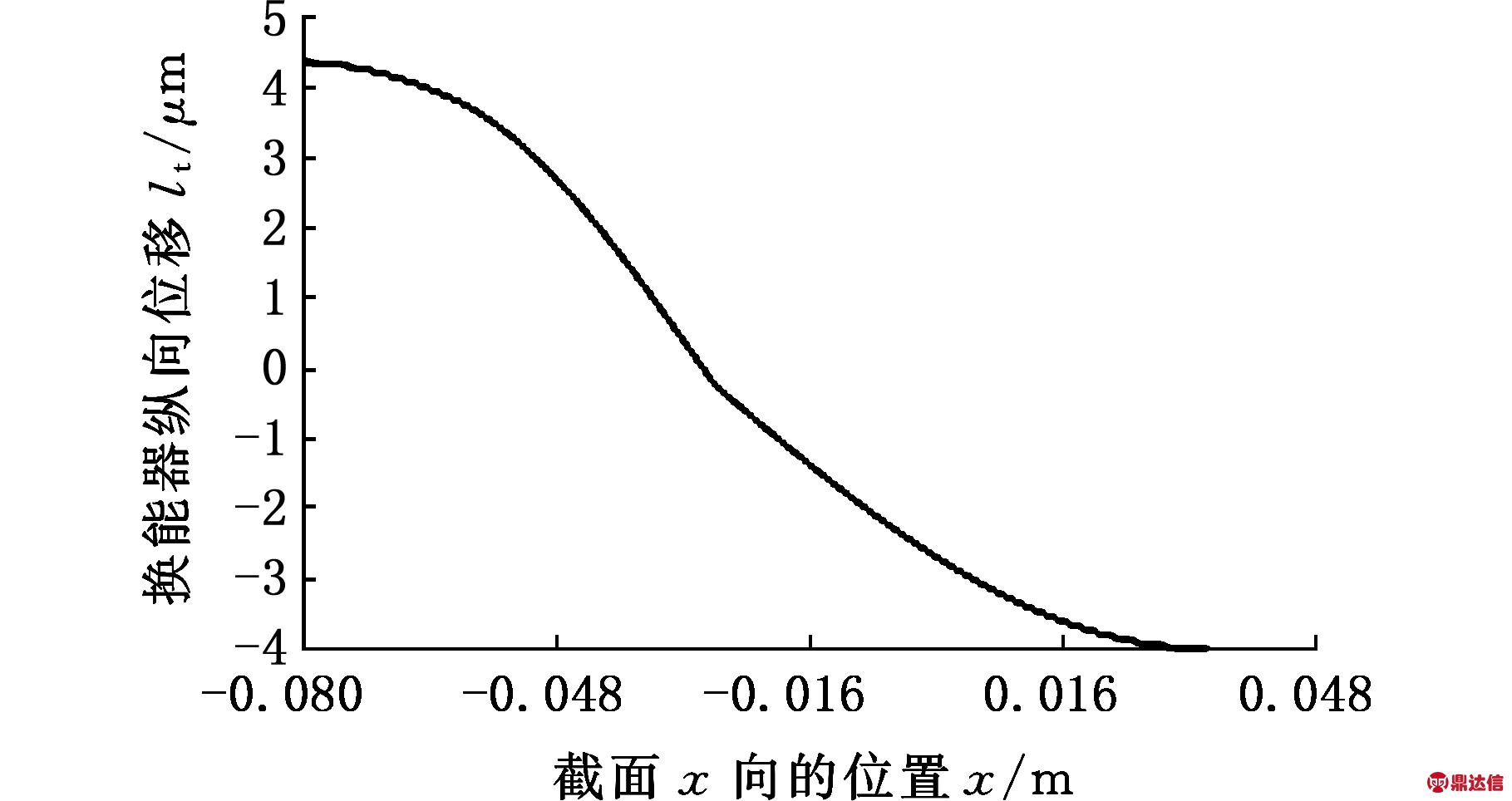
图10 换能器的位移分布曲线
Fig.10 The displacement curve of transducer
5 超声研齿系统的动力学仿真
根据上述设计分析,利用第3种复合变幅杆和换能器的理论设计参数,在ANSYS中建立1/8有限元模型,进行动力学分析。换能器前后盖板和复合变幅杆的单元类型均为Solid45,压电陶瓷片的单元类型为Solid5。对于复合变幅杆,在法兰盘处施加零位移约束,前端面上施加预紧力约束来模拟超声振动系统在机床上的实际安装情况。得到超声振动系统的位移云图见图11。
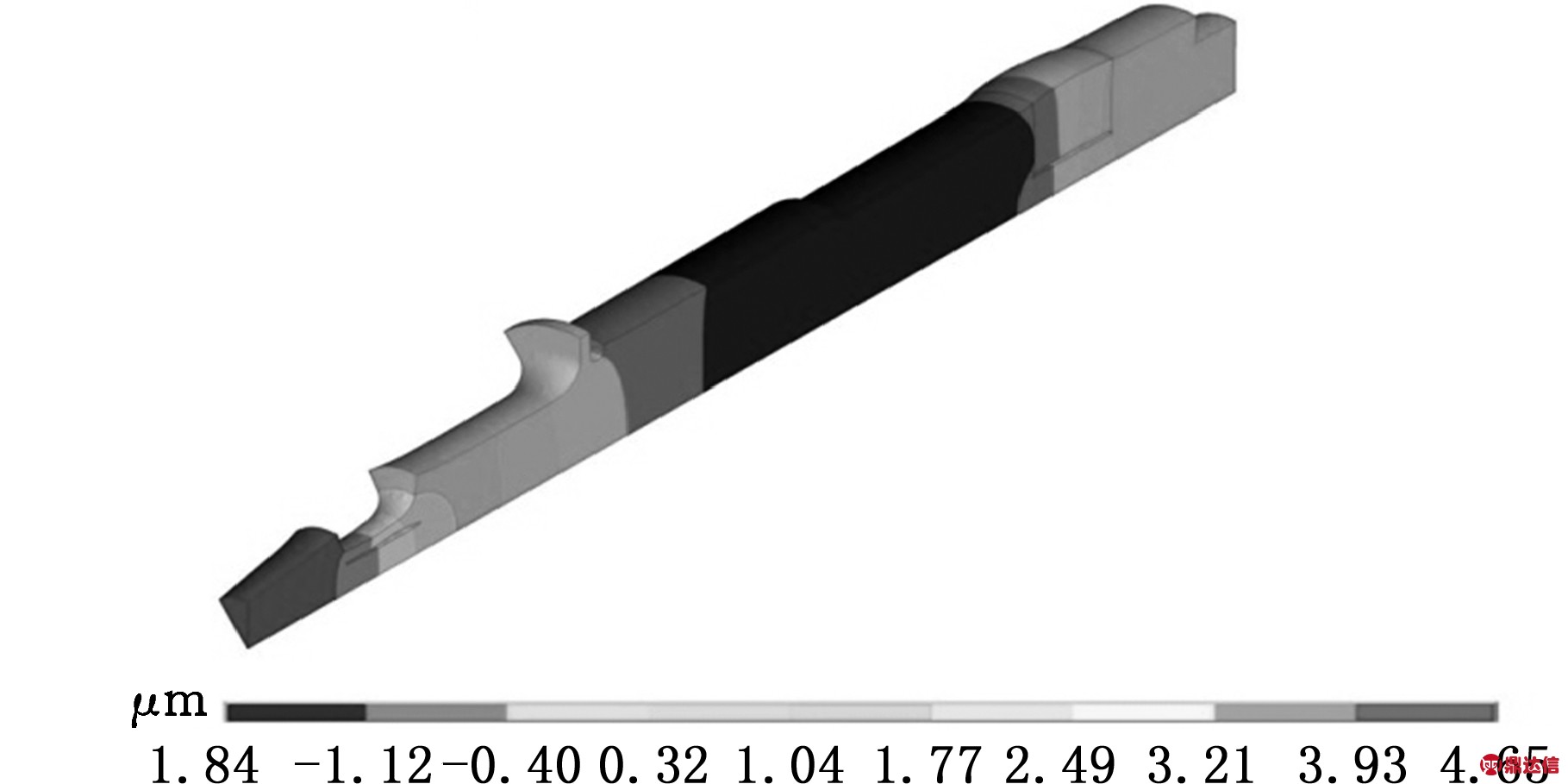
图11 超声振动系统的位移云图
Fig.11 The displacement cloud chart of ultrasonic vibration system
由图11可以看出,超声振动系统的谐振频率为23.294 kHz,与理论设计频率相比,误差为1.26%。利用ANSYS的路径读取功能,得到其轴向位移分布曲线,如图12所示。由图12可以看出,从换能器端面输出的位移,经过变幅杆的放大作用,到齿轮端面达到最大值,放大系数约为2.46。同时也可以看出,换能器和复合变幅杆均为半波长,与理论设计一致。
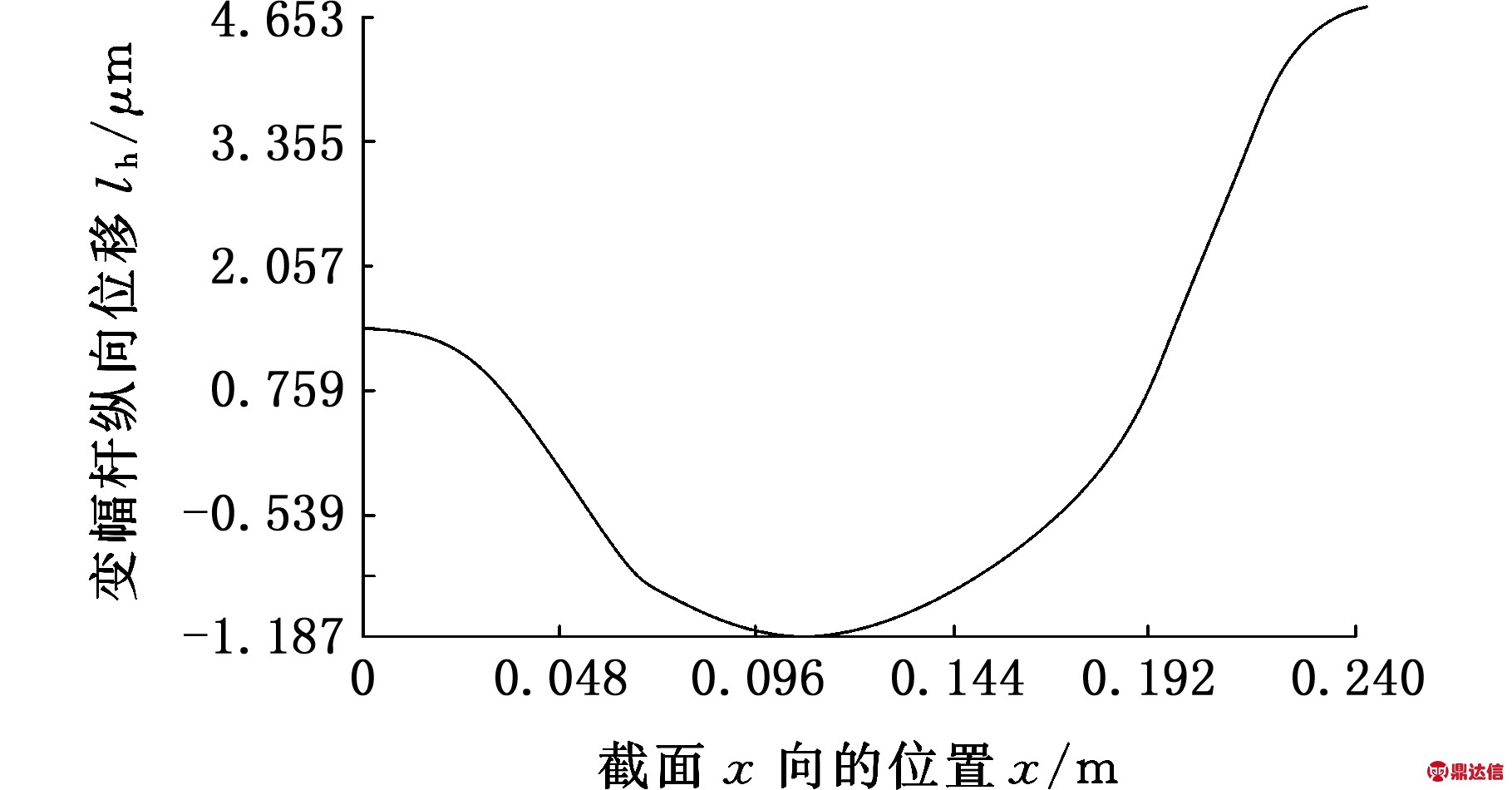
图12 超声振动系统的位移分布曲线
Fig.12 The displacement curve of ultrasonic vibration system
对复合变幅杆进行谐响应分析,分析后取齿轮中部外径上一个节点,可以得到节点沿轴向位移随频率的变化曲线,如图13所示。由图13可以看出:在谐振频率23.294 kHz时,该点振幅沿x轴方向达到最大值9 μm,说明该频率为超声振动系统的谐振频率。
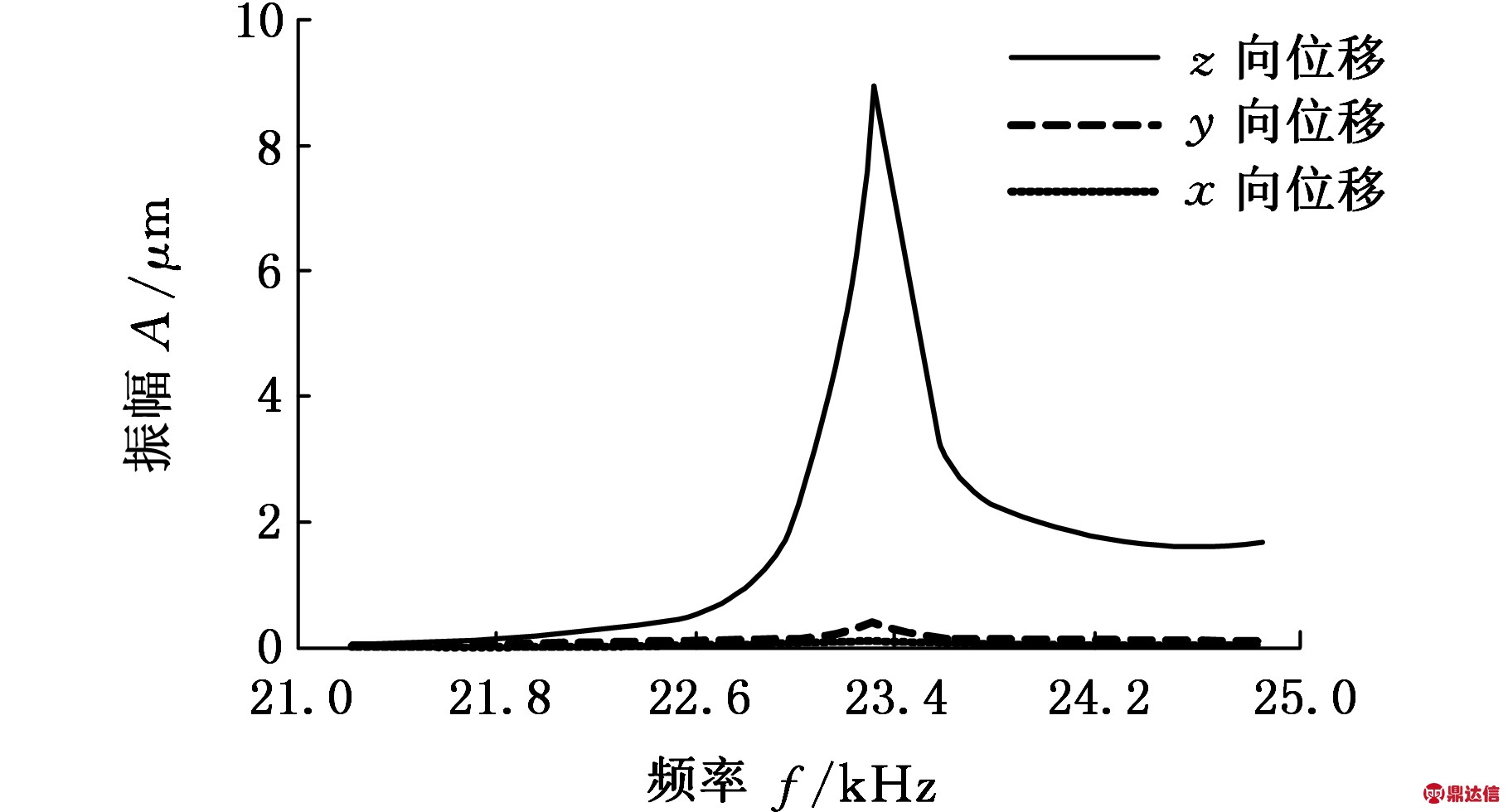
图13 锥齿轮的幅频曲线
Fig.13 The amplitude-frequency curve of bevel gear
仿真模型与理论设计的频率和放大系数存在一定的误差,原因主要有:①理论设计时对模型进行了简化,而有限元仿真时考虑了节面位置安装时使用的法兰,并施加了预紧力约束,两者的模型有一定差距。②理论分析时换能器的预紧螺栓和齿轮轴的部分,由于材料的不同采用了等效的措施,与实际模型存在一定误差。
6 谐振频率测试
按照上述设计的超声振动系统尺寸,对各部分进行加工,并将其连接在一起,由于变幅杆节面小法兰处的振幅为零,可将该小法兰与大法兰连接,以便将其固定于机床。加工的超声振动系统实物如图14所示。
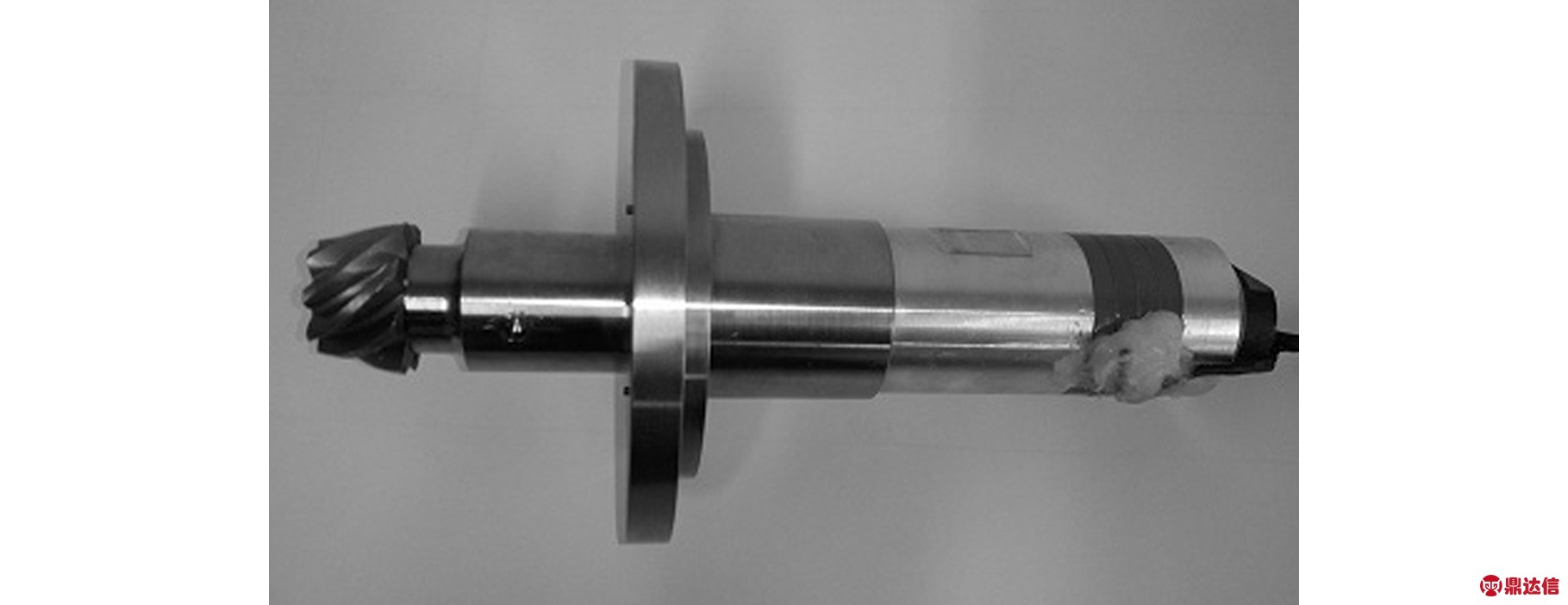
图14 超声振动系统实物
Fig.14 The real ultrasonic vibration system
将加工的超声振动系统进行频率测试,测试装置由超声振动系统、阻抗分析仪和计算机三部分组成。阻抗分析仪型号为PV70A,使用配套的PiezView软件系统,选择“串口”为COM3。通过换能器输入的正负极接口将超声振动系统接入阻抗分析仪,在软件界面上设置“精度等级”为normal,“坐标系”为lgZ Phi-F。设置完成后,输入“起始频率”为23 kHz,“终止频率”为24 kHz,进行谐振频率搜索,其结果见图15。
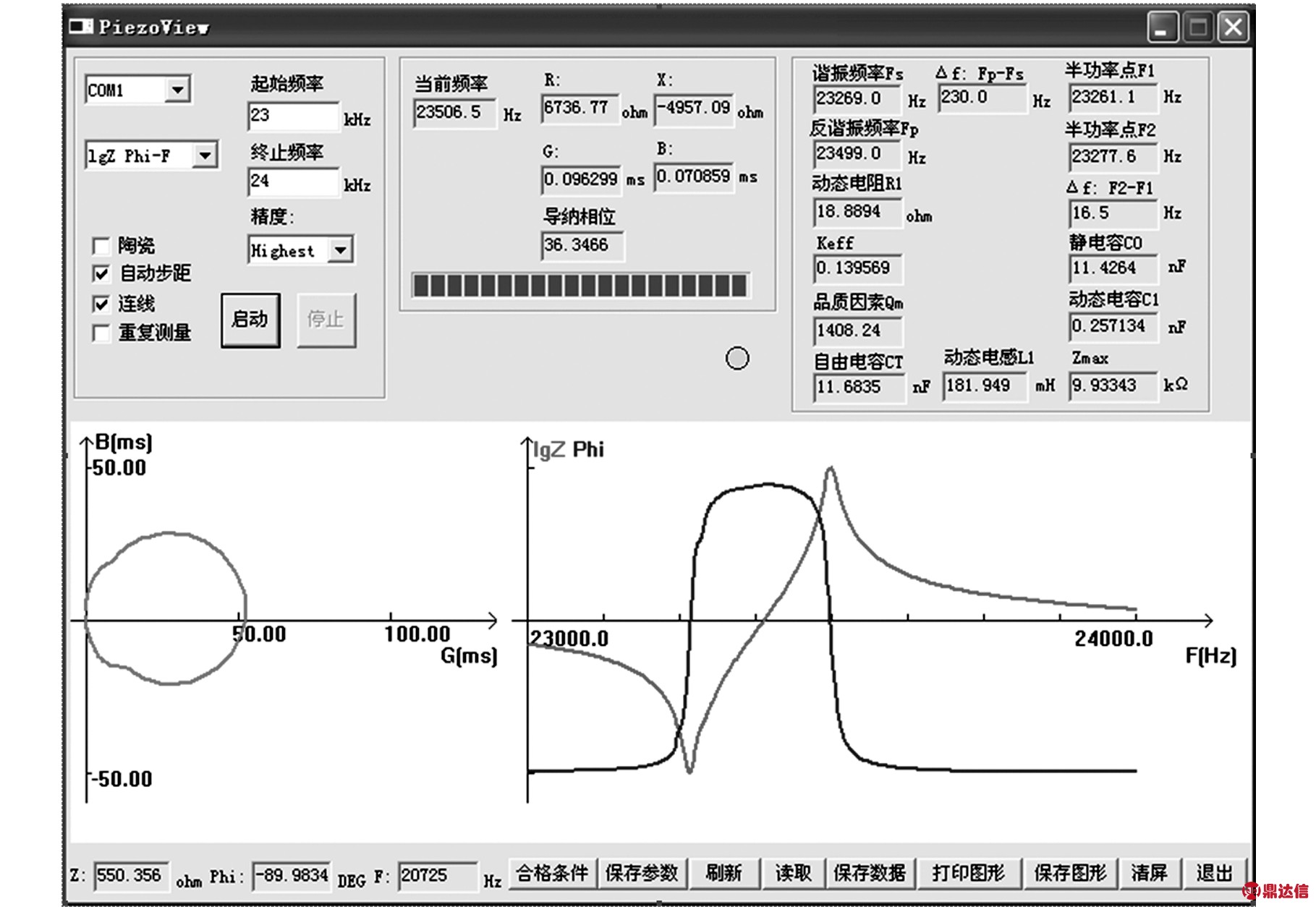
图15 阻抗分析结果
Fig.15 The result of impedance analysis
由图15可以看出,导纳圆完整且形状很好,阻抗模数的导纳曲线正常,对数坐标只有一对极大值和极小值,阻抗相位曲线是一条平滑的矩形曲线,该超声振动系统的实测谐振频率为23.269 kHz,与设计频率误差约为1.17%,在超声波发生器的谐振频率搜索范围,满足实际加工要求。
7 结论
本文对带轴锥齿轮和阶梯型变幅杆组成的复合变幅杆进行了设计计算、有限元仿真和试验验证,试验结果表明所设计的超声振动系统阻抗相位曲线光滑,谐振频率为23.269 kHz,与设计频率误差约为1.17%,满足了实际需要,为带轴的锥齿轮超声研磨系统的设计提供了参考依据。