摘要:结合飞行器制造工程专业模具设计课程的教学实际,总结和归纳了零件特点和模具设计流程,提出了一种模具设计流程化方法,并基于CATIA平台开发一套用于冷冲压模具设计的教学系统,方便教师在教学过程中能快速展示多套不同参数的模具设计过程,增强学生的知识面,提升教学效果。
关键词:冷冲压模具;模具设计;CATIA;二次开发
冷冲压是建立在金属塑性变形的基础上,在常温下利用安装在压力机上的模具对材料施加压力,使其产生分离或塑性变形,从而获得一定形状、尺寸和性能零件的加工方法,广泛应用于机械产品、电子产品、轻工产品的零件制造。冷冲压可以加工壁薄、重量轻、形状复杂、表面质量好、刚性好的零件,因此航空产品中包含了数量众多的盒盖类、环套类、法兰类、边框类等冷冲压钣金零件。冷冲压成型工艺依赖高水平的模具设计,对于飞行器制造工程专业的学生,冷冲压模具设计是一门重要的专业必修课。
近年来,工科类高校关注有关模具设计的教学与实践研究,取得了良好的教学效果。武汉理工大学在冲压工艺与模具设计课程教学改革中提出“走出去,请进来”的方式对本课程进行补充性和强化性的教学[1],开阔学生眼界;广东工业大学在合理利用多媒体教学手段提高教学效果方面进行了有益的尝试[2],并提出了基于工作过程向导的模具设计方式[3];南京航空航天大学提出项目教学法[4],增强学生学习场景感与带入感。同时,模具设计领域的学者在商用模具设计CAD系统方面做了很多研究[5-9],其有关经验和成果非常值得模具设计教学借鉴。
在北京航空航天大学飞行器制造工程专业的冷冲压模具设计课程教学中,教师讲授内容主要为工艺分析计算与模具设计两部分。工艺分析计算包括零件毛料展开、排样设计、刃口尺寸计算等知识;模具设计采取展示一套典型模具装配图示例,配合局部细节剖析的方式。在多年教学实践中发现,讲授模具总体设计时所给装配图包含完整的产品结构、形状、位置、装配关系、工艺要求等最终设计结果,局部细节量多且零散,没有有效地组织起来,学生接受难度大,讲解一种类型的模具完整设计过程需要花费大量时间,难以在较短时间内为学生介绍更多模具设计知识。
本文结合我校飞行器制造工程专业模具设计课程设计的教学实际,总结和归纳了零件特点和模具设计流程,提出了一种模具设计流程化方法,并基于CATIA平台开发一套用于冷冲压模具设计的教学系统,方便教师在教学过程中能够在较短时间内讲授多套模具的完整设计过程,增强学生的知识面,提升教学效果。
1 模具设计流程与建模流程
1.1 模具的设计流程
在航空业的冷冲压模具设计中零件形状多为有凸缘或无凸缘的圆筒形、盒形件,如图1所示,该类零件的第一道工序为落料拉深,后续工艺为反拉深、冲裁、翻边和切边等。因此课程教学中涉及模具主要是落料拉深复合模、反拉深模、冲孔模和翻边模等。以圆筒件落料拉深复合模为例,设计流程[10]为:
(1) 零件的工艺性分析。包括解析法计算落料件的毛坯尺寸,计算拉深系数验证能否一次拉深;
(2) 零件拉深工艺计算。包括力和功的计算、落料模及拉深模有关尺寸计算;
(3) 模具结构选择并设计主要零部件。零部件包括落料凹模、凸凹模、拉深凸模、压边圈、卸料板等;
(4) 模具标准件选型设计。包括模座选择、导柱/导套选择、模柄选择、圆柱压缩弹簧选用、压力机选型和导料销/挡料销选用等;
(5) 进行模具零件的装配设计。
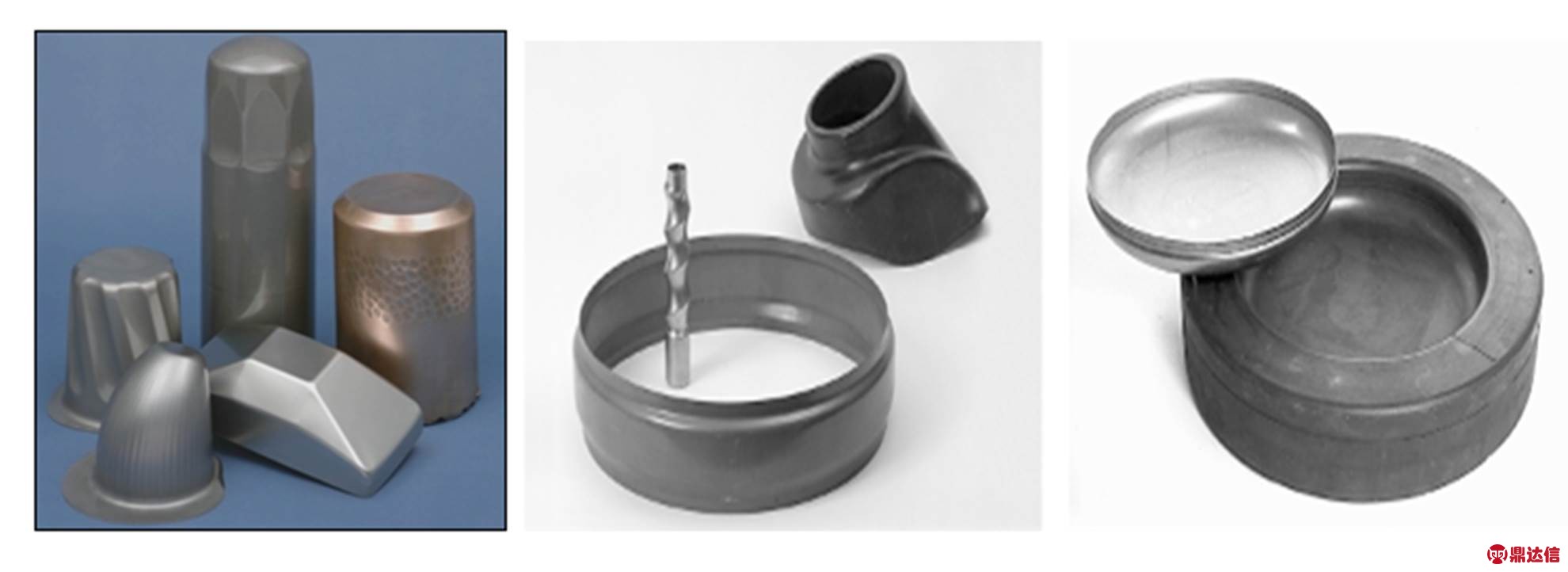
图1 典型的模具成型航空产品
1.2 模具的建模流程
模具零件建模包括:设计参数转化几何参数和参数化建模两个阶段。
在设计参数转化阶段,主要通过公式和图表将零件提供的设计参数转化为模具的部分几何参数,如落料模刃口直径,拉深凸模直径等,按照成型工艺的时间序列依次转化设计参数。
在参数化建模阶段,需分析零件之间外部参数的依赖关系,确定零件建模流程,具体方法为:
(1) 提取每个零件的几何参数;
(2) 对每个零件的几何参数分类,去掉可以通过设计参数确定的部分,考查剩余参数;
(3) 结合模具静态结构及动态模型分析零件的剩余参数与其他外部剩余参数间的函数依赖关系,将2步骤中剩余参数分为需要独立确定的主参数和有外部依赖关系非主参数;
(4) 以零件为节点按照非主参数的函数依赖关系依次连接,如果产生循环则找一个节点拆分成两个节点,形成依赖关系网络图;
(5) 从依赖关系网络图的外侧节点,即指出边的节点(或循环中产生的独立节点)开始设计零件,将完成设计的节点从依赖关系网络图中去掉;
(6) 重复步骤5,直到所有零部件完成设计。
2 模具设计的CATIA设计系统
2.1 系统总体设计
根据模型的设计特点和流程,开发冷冲模辅助设计系统,便于教师在课堂上讲解,提升模具设计教学水平,提高模具设计效率。冷冲模辅助设计系统需满足以下要求:
(1) 能够体现冷冲压模具设计过程;
(2) 能够将设计参数求解转换为建模所需的几何参数并记录;
(3) 能够合理地安排零件建模流程,减少由于独立设计而导致的装配干涉问题,规避反复地修改调整;
(4) 能够提供模具标准件模型快速生成工具,利用派生式建模技术,缩短建模时间。
在本模具设计课程中涉及的模具类型主要有:落料模、拉深模、反拉深模、冲孔模、翻边模和切边模,其中绝大多数零件都需要落料和拉深工序,可以用落料拉深复合模完成。图2为系统层次结构。

图2 系统总体设计方案层次结构图
2.2 软件在教学中的使用
以某法兰盘零件为例,介绍设计系统在教学实践中的应用情况。零件如图3所示。
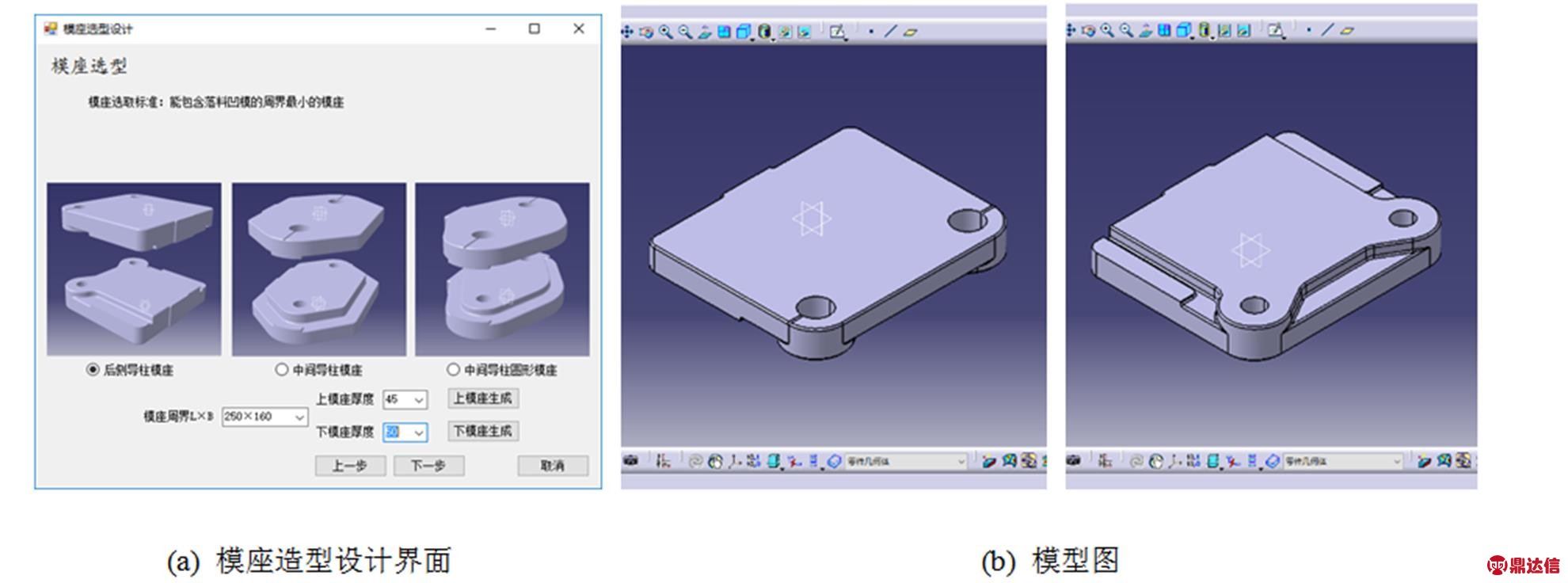
图3 某法兰盘零件图
2.2.1 工艺分析及计算
简单分析可以确定零件第一工序应为落料拉深工艺,在系统中选择落料拉深复合模设计入口进入尺寸输入界面,输入零件尺寸及材料信息即可在CATIA中建立零件模型,如图4所示。
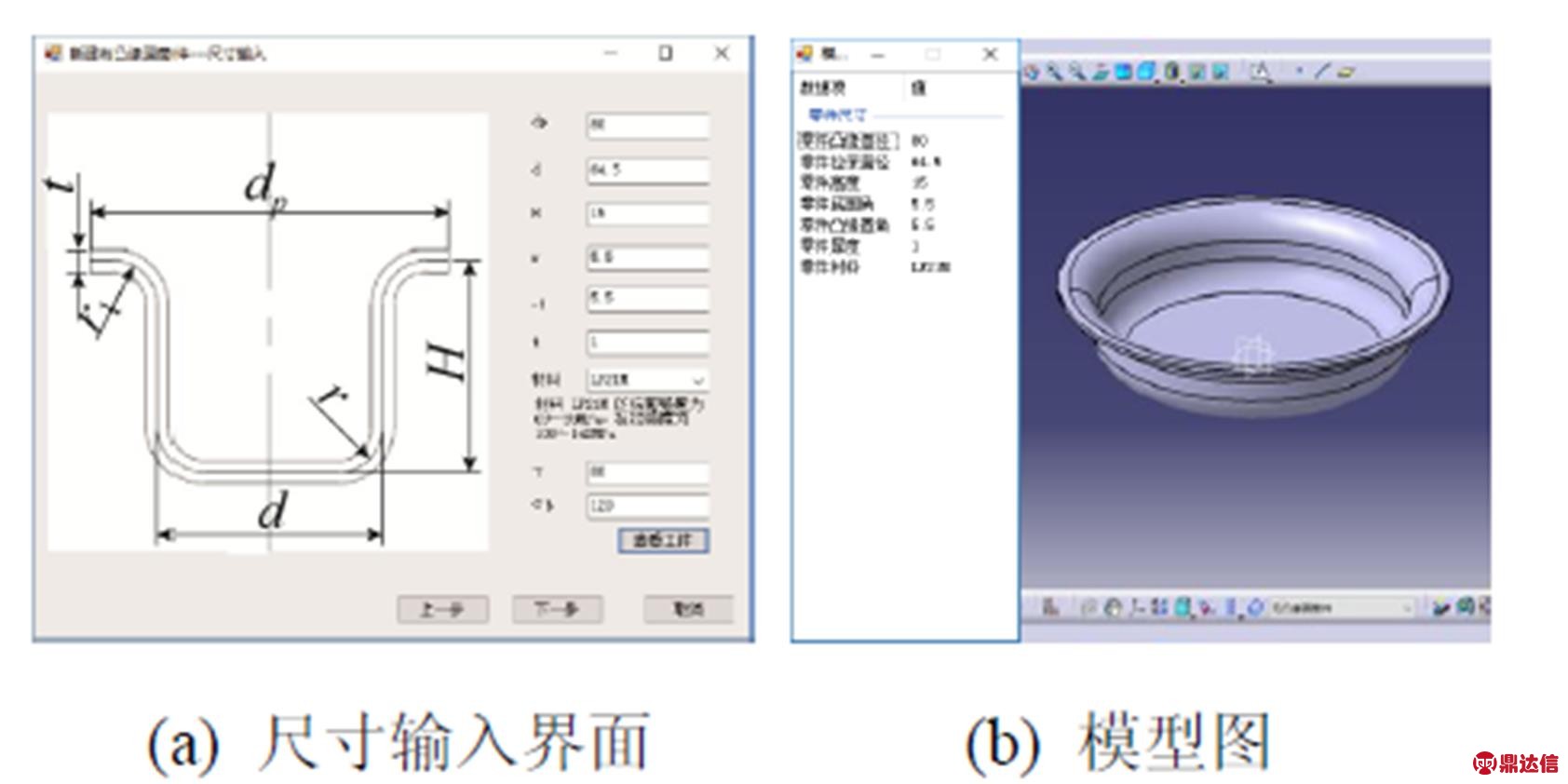
图4 尺寸输入界面及零件建模结果
按照先落料再拉深的工艺过程进行工艺分析与计算,步骤依次为修边余量选取,毛料展开,落料排样计算,冲压力计算,刃口尺寸计算,拉深性验证,拉深模计算,凸/凹模工作部分尺寸计算以及力和功的计算。过程中涉及到的查表、数值计算等全部由软件自动实现,讲解时简单点击即得到结果,大大提升讲解速度,部分分析计算过程的界面如图5~6所示。
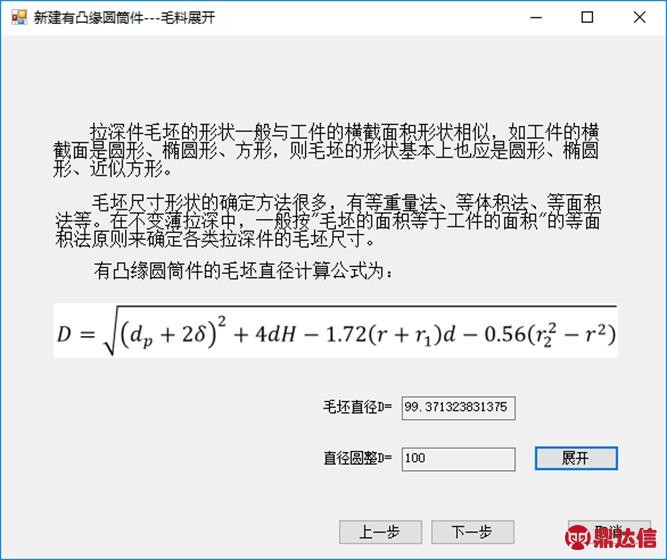
图5 毛料展开界面
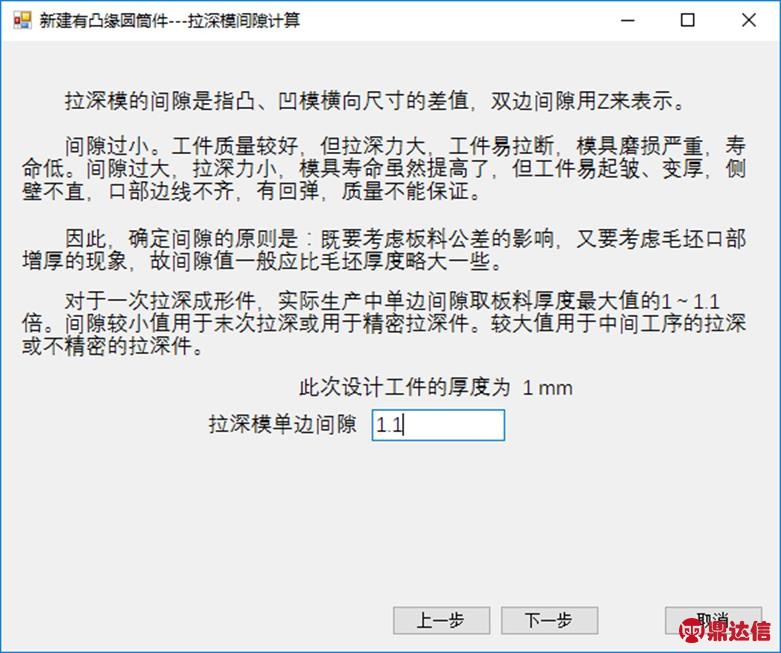
图6 拉深模间隙计算界面
2.2.2 零件建模
根据前述模具设计流程化方法分析,落料拉深复合模建模流程为压边圈→拉深凸模→凸凹模→卸料板→落料凹模,在软件系统编写时,已经分析所有涉及到模具的建模流程并将其固化于系统中,因此工艺分析计算完成后系统自动按照上面的流出开始零件建模,每个零件单独给出建模尺寸设计界面,并将之前计算好的设计参数自动填入,教师只要输入剩余设计参数即可在CATIA软件中得到参数化的零件模型,如图7~8所示,由于流程化方法中已经考虑了零件尺寸间的相互依赖,设计结果基本不需要改动,而且本系统采用参数化建模,特殊情况需要修改也极为快速。
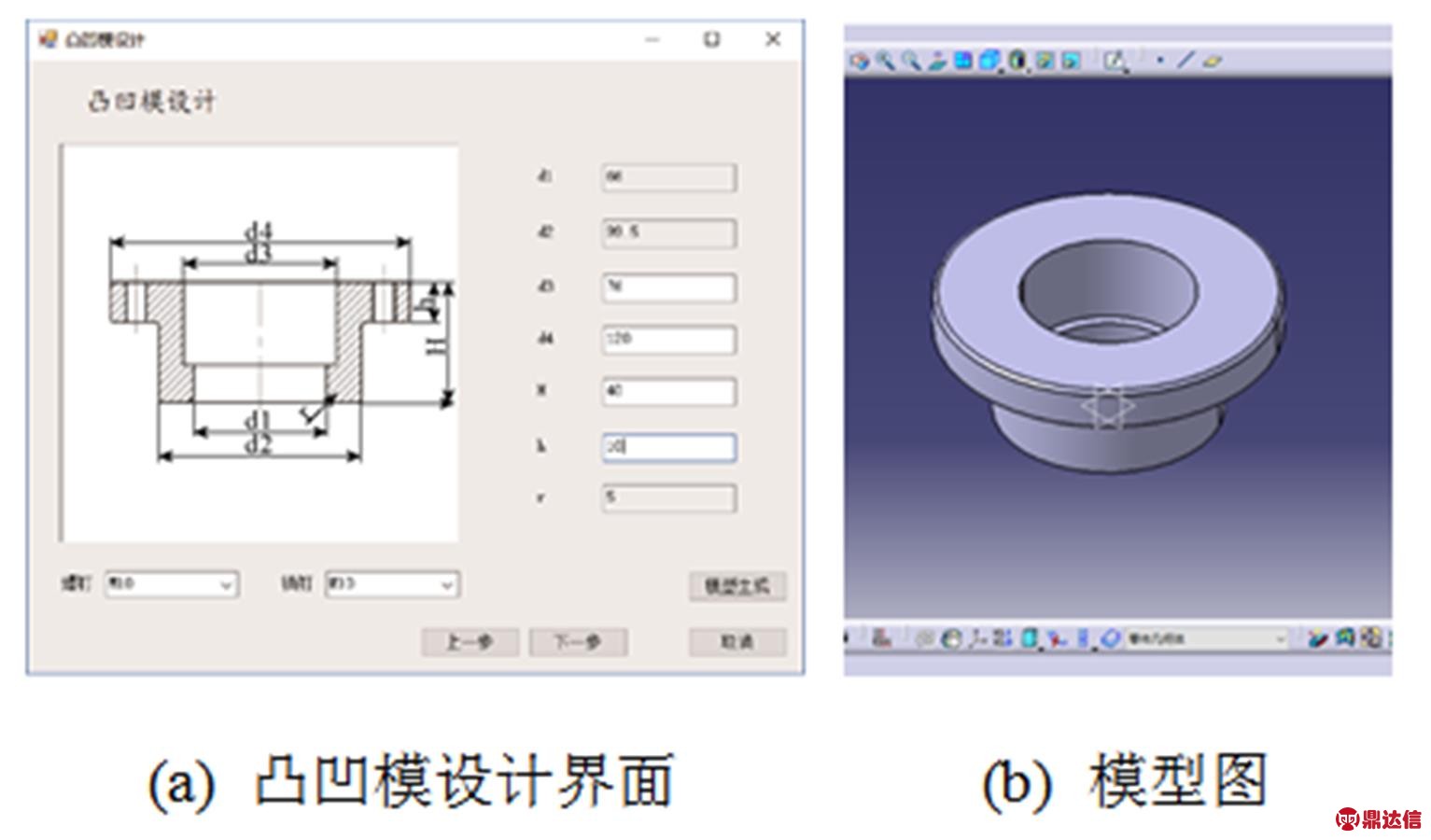
图7 凸凹模设计界面及建模结果
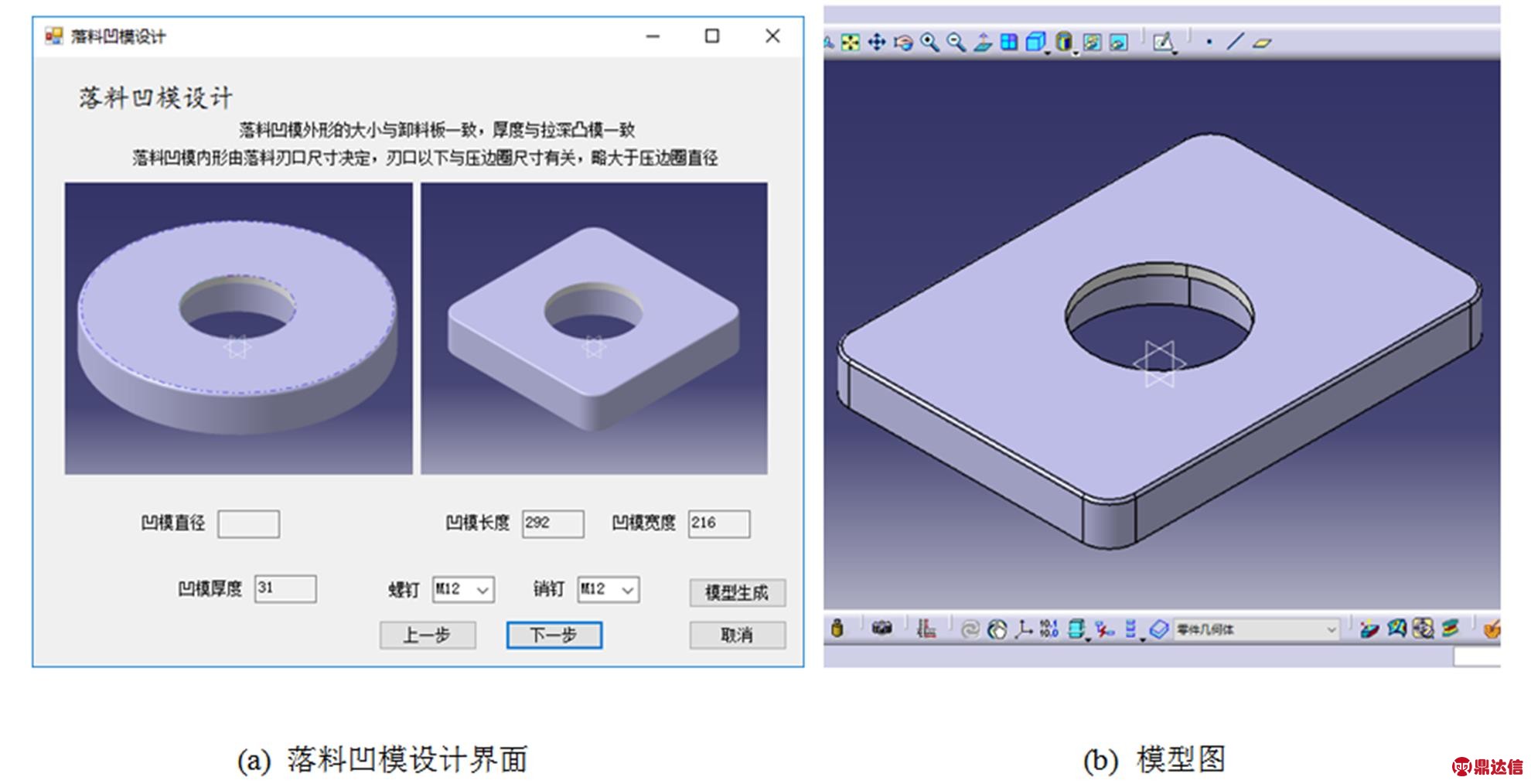
图8 落料凹模设计界面及建模结果
2.2.3 标准件选型设计
根据完成的零件设计,依次选取模座、导柱/导套、压力机型号、模柄以及销钉、螺钉等标准件,软件系统中已经集成了全部模具设计标准件库,教师在软件界面中选择相应的型号即可在CATIA系统中建立标准件实例,如图9所示。其节省了标准件建模时间,避免手工标注件建模错误,大大方便后续装配设计。
2.2.4 模具设计结果
经过分析计算和零件的建模,利用系统中自动化钻孔装配工具,快速完成零件与标准件装配,得到模具设计装配图,如图10所示。该工具还可以为零件设置不同颜色,使装配零件展示效果更好。利用CATIA软件的截面查看功能可多角度、多方位查看模具装配关系,方便教师讲解模具装配的相关知识。
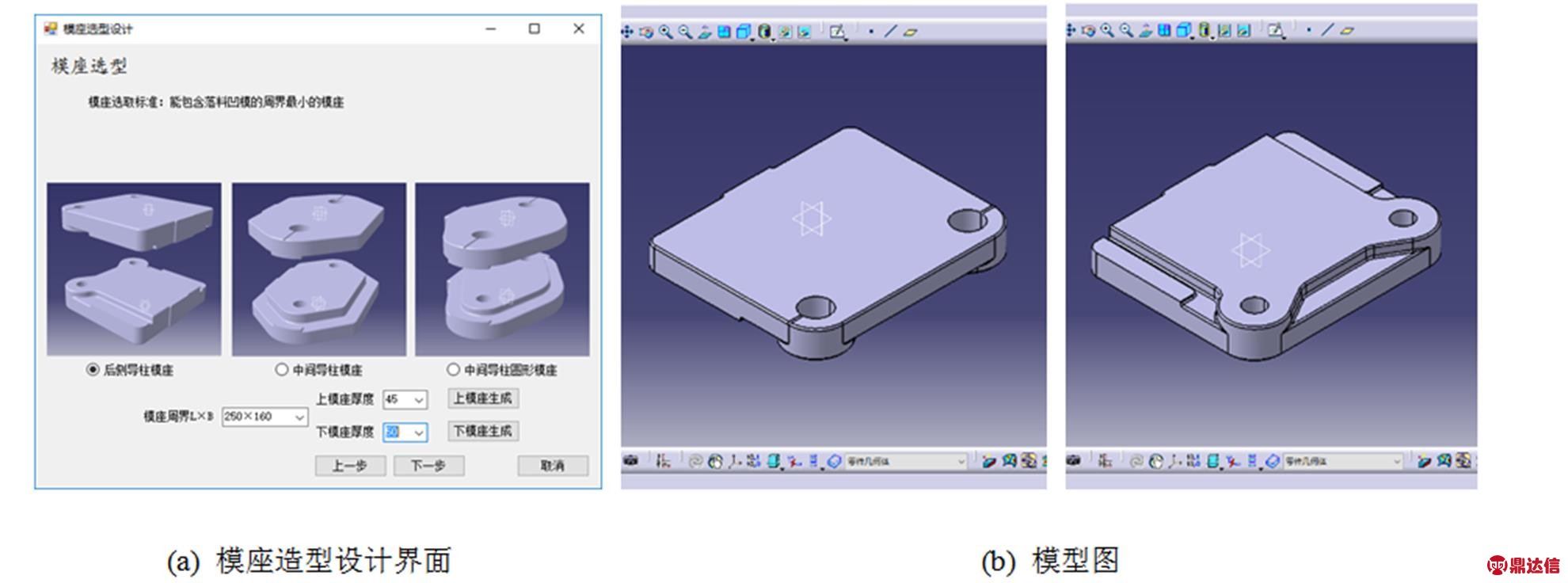
图9 模座选型设计界面及建模结果
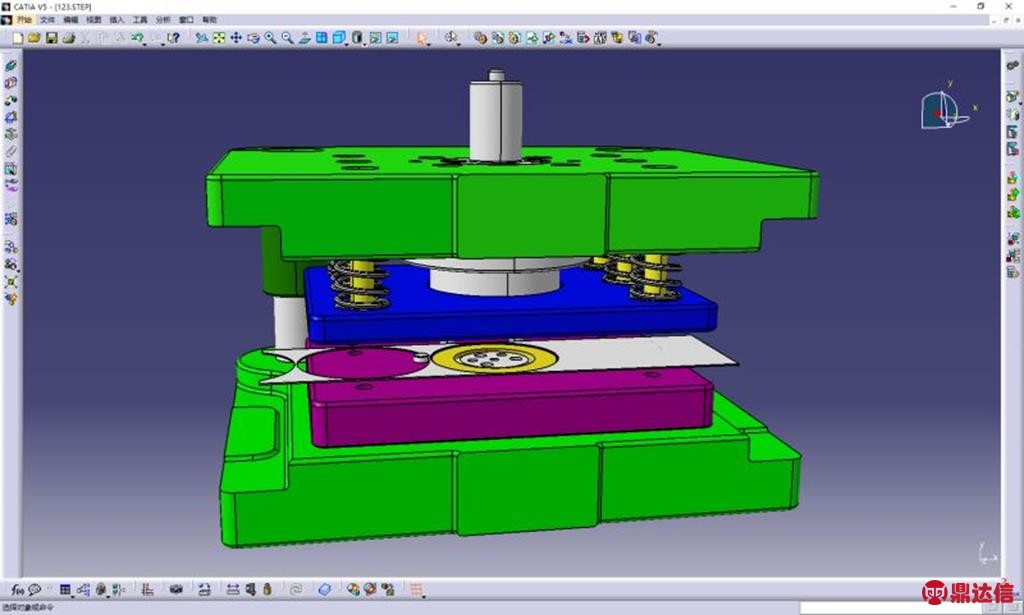
图10 模具设计结果
2.2.5 模具设计检验
在现有的教学实践中,对于设计结果的检验主要依赖于教师检查学生总装配图,需要教师具有扎实的机械制图知识和丰富的模具装配图阅读经验。教师检查每个学生的图纸既费时、费力,又有遗漏或忽略某些问题的可能。现在本系统利用三维软件CATIA建模装配,可以利用其运动分析DMU模块对模型进行运动分析、干涉检查等,丰富了教学内容,而且利用软件检查避免了人为的疏漏,确保错误率低、准确性高,提高了教学质量。
3 结 论
本教学系统已经在本专业的模具设计课程中开始了使用,通过该系统,教师能够选择设计的模具类型以及零件形状,通过软件界面输入零件尺寸,辅助完成工艺分析、工艺计算等计算问题,利用计算结果完成零件结构选型、标准件选型设计和零件装配设计,并在CATIA软件中完成快速建模,方便教师在教学过程中能展示多套不同参数的模具设计过程,增强学生的知识面,提升教学效果。