摘要 随着硅片厚度的增大和芯片厚度的减小,硅片在加工中的材料去除量增大,如何提高其加工效率就成了研究的热点之一。由于化学机械抛光过程复杂,抛光后硅片的质量受到多种因素的影响,主要包括抛光设备的技术参数、耗材(抛光垫和抛光液)的性质和硅片自身在抛光时的接触应力状态等。本文介绍了硅片化学机械抛光技术的研究进展,讨论了影响硅片抛光后表面质量和表面材料去除率的因素,如抛光液、抛光垫、抛光压力等,并对目前用于硅片化学机械抛光的先进设备进行了综述。
关键词 硅片; 化学机械抛光; 抛光液; 抛光垫; 抛光设备
随着半导体工业的迅猛发展,集成电路的集成度越来越高,电子元器件的尺寸越来越小。同时为了降低生产成本、提高生产效率,硅片的直径越来越大,硅片表面的平整度要求越来越高,已达到纳米级水平。传统的平坦化技术,如选择淀积、旋转玻璃法等,仅仅能实现局部平坦化,但对于微小尺寸特征的电子器件,必须进行全局平坦化才能满足硅片的使用要求。化学机械抛光(chemical mechanical polishing,CMP)的概念于1965年由美国的WALSH等[1]提出,是目前为止唯一能够实现硅片局部和全局平坦化的工艺技术,被广泛应用在半导体制造领域。虽然半导体材料已经发展到第三代,但作为第一代的硅材料仍然是最重要的衬底材料。据统计,全球95%以上的半导体芯片和器件仍采用硅片作为基底功能材料。
IC制造过程如图1所示,主要包括硅片制造、IC制造(前端工艺、后端工艺)、测试与封装几个阶段。在IC制造过程中,无论是氧化扩散、化学气相沉积还是溅镀和保护层沉积,均需要多次使用CMP技术。

图1 集成电路制造过程简图
Fig. 1 Process schematic of integrated circuit manufacturing
硅片逐渐大尺寸化,使得对硅片的表面质量要求更为严格;硅片厚度的增加也使得减薄过程中需要去除的材料量增加。因此,如何提高其加工效率成为了研究热点之一。由于化学机械抛光技术是一个复杂的化学和机械协同作用的技术,因此影响抛光过程和效果的因素很多。抛光参数的改变将会直接对硅片平坦化的质量产生影响。目前,影响硅片抛光质量的因素主要有3个方面,分别如图2所示[2]:首先是抛光设备的技术参数,包括抛光盘和抛光头的转速、抛光压力和抛光时的环境温度等;其次是CMP中使用的耗材参数,主要为抛光液和抛光垫的技术参数;最后是硅片自身的影响,主要指硅片特性及其与抛光垫接触时的弹塑性性能等。
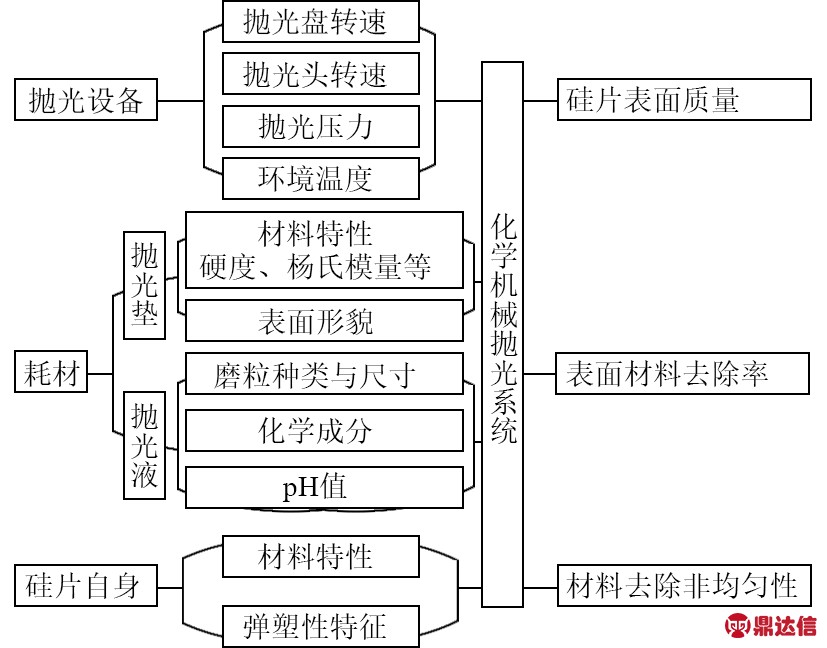
图2 硅片CMP过程中的影响因素
Fig. 2 Influencing factors in silicon wafer CMP process
首先,介绍化学机械抛光技术的基本原理及其技术优势;然后,概述抛光液、抛光垫和抛光压力等因素对硅片抛光后的表面质量和表面材料去除率影响的研究现状;最后,对目前国内外用于硅片CMP加工的不同类型的设备进行介绍。
1 CMP技术基本原理与优势
1.1 CMP技术的基本原理
CMP工作原理如图3所示。整个系统主要由3部分组成,分别是夹持硅片进行抛光的抛光头、安装抛光垫的工作台和抛光液的供给设备。在抛光过程中,硅片被吸附或粘在抛光头上,并施加一定压力,使得待加工表面与抛光盘接触。抛光头和工作台在电机的驱动下可按照一定转速旋转,通常情况下,抛光头和工作台的转速基本一致[3]。由纳米或者微纳米磨粒和化学溶液组成的抛光液通过抛光液供给装备添加到抛光盘表面,然后通过工作台转动时的离心力使其均匀分布在抛光盘表面。抛光过程中抛光液与硅片间发生化学反应,使得硅片表面生成比较容易去除的物质,然后由磨粒与硅片表面的机械摩擦作用将生成的物质去除,通过化学和机械的交替作用实现对工件表面的超精密抛光。
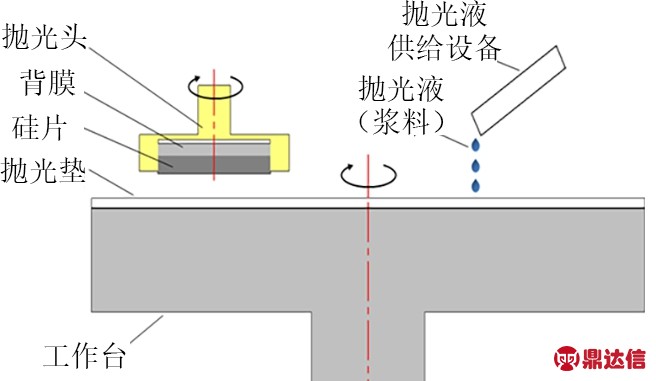
图3 传统化学机械抛光原理示意图[3]
Fig. 3 Schematic diagram of traditional CMP process[3]
CMP的化学反应机理比较复杂,影响因素很多。根据抛光对象的不同,具体的抛光机理也有差别。通过对硅片表面各种材料在CMP过程中化学机理的研究与总结,得到CMP的化学反应通式为[4]:

(1)
其中:M表示未与抛光液发生反应前的材料;R表示抛光液中的氧化剂、络合剂等反应物;L表示反应后生成的易于去除的反应物薄膜;D表示反应生成的副产物,如气体和溶于抛光液中的化学反应物等;α、β、n、m为系数;k1为速度参数,其值由氧化剂的性质决定。
硅片在CMP过程中,一般使用碱性抛光液,如二氧化硅碱性溶液、氧化镁水剂、二氧化钛碱性溶液等。目前最常用的是二氧化硅碱性抛光溶液。其反应方程式如下[5]:

(2)
1.2 CMP技术的优点
化学机械抛光技术综合了化学抛光和机械抛光的优势。它克服了纯化学抛光过程中的表面平整度和平行度差的问题,也克服了纯机械抛光过程中表面光洁度差、损伤层厚度大的缺点。化学机械抛光在获得较高表面质量的同时,还能兼顾一定的抛光效率,是目前能够实现基片全局平整化的唯一方式。化学机械抛光技术具有很多优点[6],具体如下:
(1)可以对不同材料和表面进行全局平坦化,能对多层金属互连介质中的绝缘体、导体等不同材料进行全局平坦化;
(2)可以在一次化学机械抛光中同时实现对多种材料的平坦化加工;
(3)可以消除材料表面的缺陷,减少表面起伏,改善表面形貌,增加集成电路产品的可靠性;
(4)CMP过程中不会产生有害气体,对健康影响小。
2 CMP抛光工艺的影响因素
2.1 抛光液
抛光液是影响CMP中材料抛光质量的关键因素之一。一般由磨粒、去离子水、氧化剂、络合剂、表面活性剂以及pH调节剂等组成。抛光液需要具备流动性好、无毒和抛光速度快等特点。在化学机械抛光过程中,抛光液中的添加剂与晶圆表面反应产生化学作用,磨粒在晶圆表面通过摩擦提供机械作用。因此,抛光液对CMP性能的影响重大。众多学者对此开展了研究,将影响因素归纳为磨粒和化学添加剂2类。
2.1.1 磨粒对CMP抛光性能的影响
在硅片的化学机械抛光过程中,磨粒主要通过微切削、划擦等方式作用于被加工表面,借助机械力实现硅片表面材料的去除。磨粒直径一般为几十纳米,常用的磨粒有二氧化硅(SiO2)、氧化铝(Al2O3)、氧化铈(CeO2)和金刚石等。磨料的硬度、粒径、形状及其在抛光液中的质量浓度等综合因素决定了磨粒的去除行为和能力。
FU等[7]针对磨粒的形状对硅片表面材料去除率的影响进行了研究。假设在抛光过程中硅片和磨料均发生完全的塑性变形,研究了锥形磨粒和球形磨粒与硅片之间的相互作用规律。2种形状磨粒接触的示意图如图4所示。
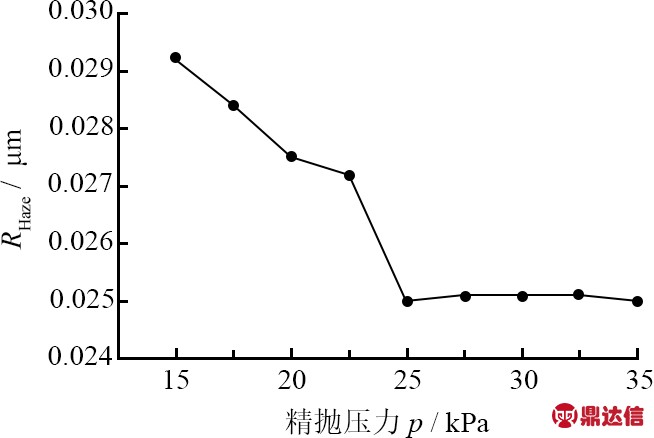
ZHOU等[8]研究了SiO2磨粒的粒径对100 mm单晶硅片表面材料去除率的影响。在磨粒粒径分别为10、20、50、80、110和140 nm的抛光条件下进行试验,验证了表面材料去除率随磨粒粒径呈非线性变化。当SiO2磨粒粒径为80 nm时,得到最大的表面材料去除率,并且能够获得Ra为0.6 nm的良好表面。ZARUDI等[9]研究了使用15 μm和50 nm的Al2O3磨料对硅片进行化学机械抛光后的表面形貌。试验表明,在抛光压力为79 kPa,工作台平均转速为30~50 r/min的情况下,采用15 μm的Al2O3磨料抛光后的硅片表面粗糙度Ra为0.5~0.7 μm;当使用50 nm的磨料进行抛光时,硅片平均表面粗糙度Ra可以达到0.1~0.3 nm,但是硅片表面的材料去除率要比15 μm磨粒条件下的低1个数量级。
同时,国内外的学者也对抛光液中的复合磨粒进行了一系列的研究。杨玉芝等[10]提出了一种在硅片化学机械抛光中使用复合磨粒的方法,以此提高表面材料的去除率。研究发现,复合磨粒中小粒径的磨粒可以大量吸附在大粒径的聚合物粒子上,使得参与抛光的有效磨粒数目增大,机械作用增强,从而加快材料的去除。另外,聚合物粒子还能使抛光垫和硅片之间产生一定间隙,增强抛光液的润滑作用,有利于化学反应的进行。通过试验验证了在抛光盘和抛光头的转速均为50 r/min,抛光压力为22 kPa的情况下,使用由质量分数为5%的SiO2磨料和3%的BGF微球配制而成的复合磨粒抛光液对硅片进行抛光时,抛光速率最大,能够达到353 nm/min。
黄亦申等[11]研究了一种脉冲磁场辅助型磁性复合磨粒的化学机械抛光技术。他们采用磁性聚合物微球与SiO2磨粒组成的复合磨粒抛光液,发现在抛光过程中,磁性微球受到磁力作用时将有利于复合磨粒进入抛光区,以二体磨损的方式去除硅片表面材料。并通过工艺试验发现,在施加不同频率和占空比的脉冲磁场前后,硅片的表面材料去除率从137 nm/min提高到288 nm/min。当频率为5 Hz,占空比为50%时,材料去除率获得最大值,此时硅片的表面粗糙度Ra值由405 nm减小到0.641 nm。具体的抛光结果如图5所示。
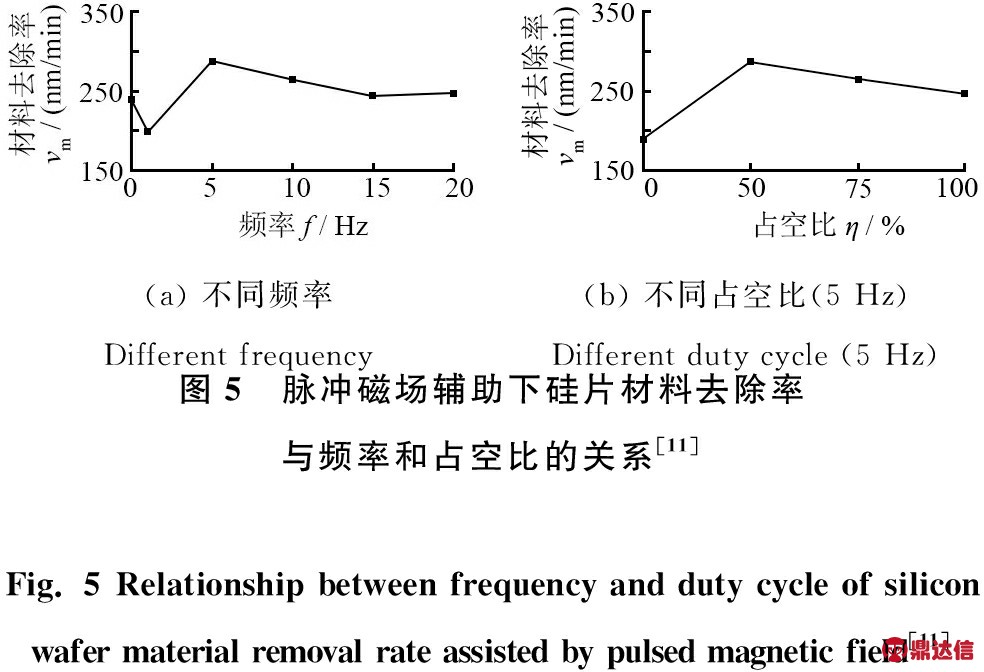
2.1.2 化学添加剂对CMP抛光性能的影响
抛光液pH值的大小会对硅片表面的生成物、材料的去除以及抛光液的黏性等产生影响,而pH值调节剂的添加能够为CMP抛光过程提供一个稳定的抛光环境;表面活性剂能够使磨粒之间产生排斥力,防止磨粒团聚,保证磨粒的分散性,减少硅片表面产生划伤缺陷等;络合剂能够将去除的材料溶解在抛光液中,减小杂质颗粒对抛光过程的污染。因此,很多研究人员研究了化学机械抛光时,抛光液中加入不同种类和浓度的化学添加剂对硅片表面质量的影响。
LIU等[12]采用有机碱氢氧化物多胺作为pH调节剂,使用小尺寸(15~20 nm)的硅溶胶抛光液,并加入FA/O表面活性剂后,有效降低了硅片损伤层的厚度,并获得了200 nm/min的抛光速率。WANG等 [13]使用Al2O3和CeO2磨粒与氧化剂H2O2在碱性抛光液中对硅片进行化学机械抛光,分析了氧化剂浓度、pH值和抛光液流速对表面材料去除率的影响。试验表明:在pH值小于9时,使用Al2O3磨粒时,材料去除率随着抛光液pH值的增大而降低;在pH值为9~10时,CeO2磨粒可以提高材料去除率。试验结果如图6所示。结果表明:2种磨料下,较高的抛光液流速或者较高的氧化剂浓度都能够获得更高的材料去除率。一种较好的抛光环境为pH为10,氧化剂体积分数为0.4%,流速为70 mL/min。
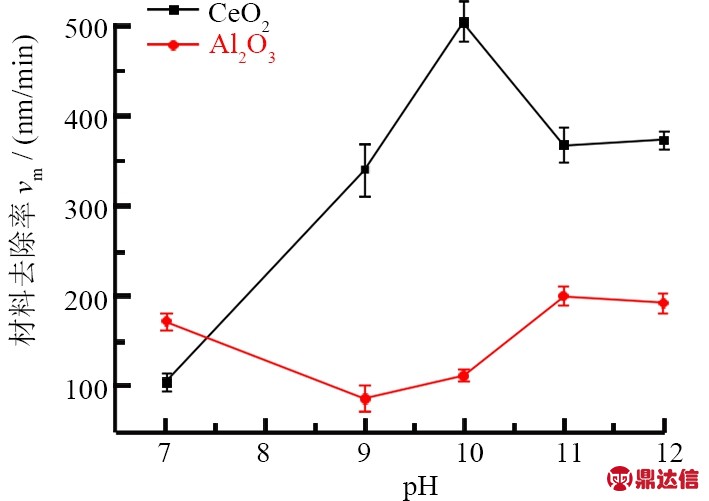
图6 不同pH值条件下磨粒对材料去除率的影响[13]
Fig. 6 Effect of abrasive particles on material removal rate under different pH values[13]
钟旻等[14]设计的试验是采用磨粒粒径为80 nm、浓度为10%的硅溶胶抛光液,控制抛光液pH值为10.5~11.0,添加浓度为0.5%~1.0%的速率促进剂后,抛光速率能够达到697 nm/min,比相同工艺条件下的进口抛光液的抛光速率500 nm/min提高了近40%。王亮亮等[15]研究了抛光液中不同质量分数的碱含量与硅片抛光时产生橘皮现象的关系。他们向硅溶胶抛光液中分别加入质量分数为0.2%、0.3%、0.4%、0.5%和0.6%的某种碱性溶液,在抛光盘转速为60 r/min,抛光压力为0.16 MPa的情况下抛光30 min,发现当碱的质量分数高于0.4%时将会发生橘皮现象。因此,应在保证抛光速率的基础上合理控制碱的添加量。杨金波等[16]研究了化学机械抛光过程中,有机和无机pH调节剂的添加对硅片表面材料去除率的影响。通过试验发现:pH调节剂会影响硅片表面钝化膜的形成和去除,进而影响硅片的材料去除率。当采用有机调节剂时,在pH值为10.85时将获得最大的抛光速率,采用无机KOH调节剂将抛光液pH值控制在10.0~11.5范围内时,抛光速率随着pH值的增大而增大。具体的试验结果如图7所示。因此,在抛光液维持在相同的pH值时,加入有机碱pH调节剂的抛光速率比使用无机KOH调节剂时大。
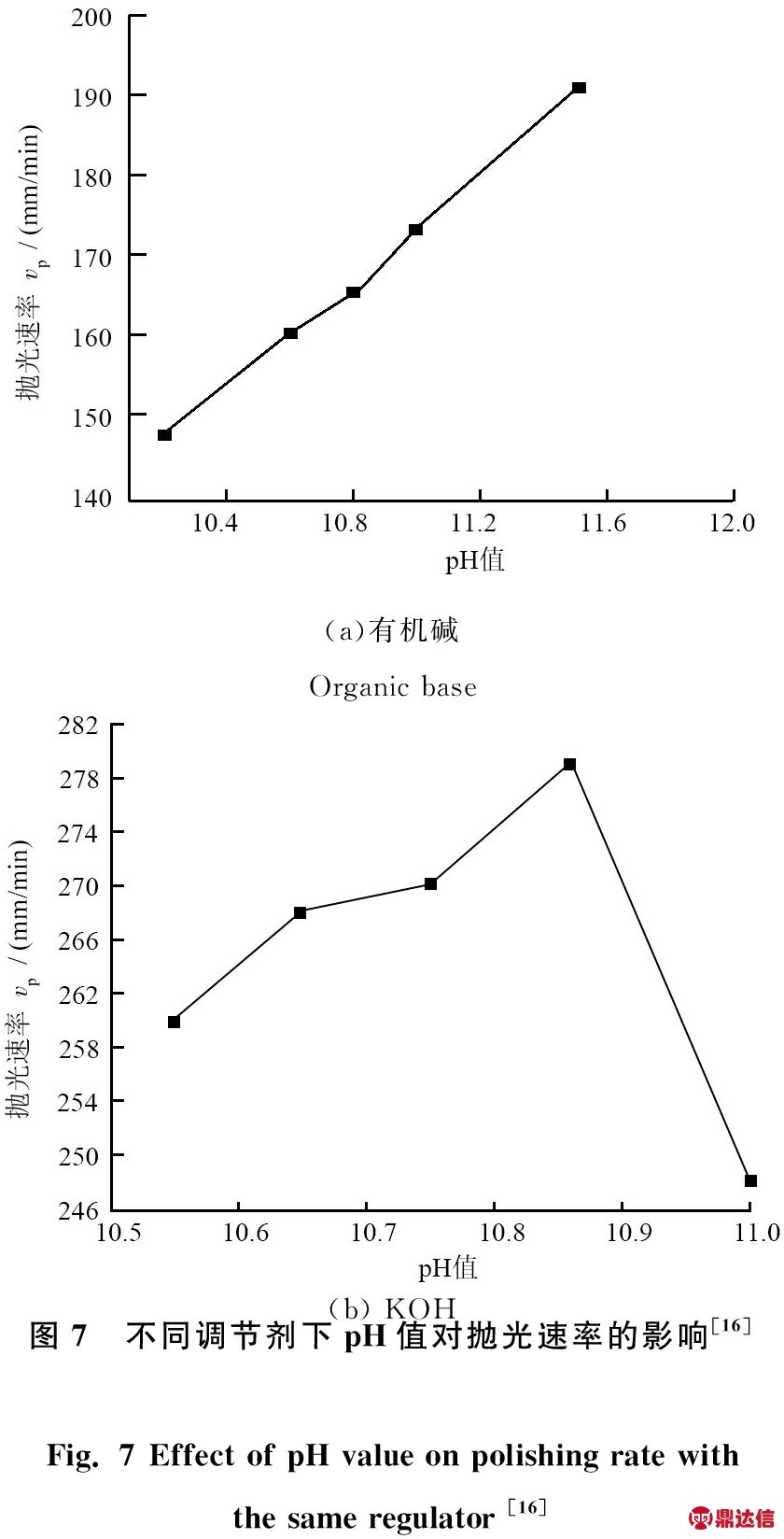
张文倩等[17]针对直径为300 mm的硅片,研究了不同稀释比例的FA/O型抛光液对硅片表面材料去除量的影响,其结果如表1所示。试验使用的是包含SiO2磨料、多羟多胺螯合剂以及其他辅助试剂的FA/O型碱性硅抛光液,抛光液的pH值为12.20,磨粒粒径为80~100 nm。试验表明:在稀释体积比为1∶30时硅片正面的去除量为10.08 μm,但是背面的去除量仅为3.34 μm,略低于生产要求的3.50 μm。他们针对试验结果,对抛光液进行了优化,在原有的抛光液中增加少量KOH,使pH值变为12.45。优化后进行试验发现,5.5 min内背面去除量增加到3.67 μm,15 min内正面去除量增加到12.29 μm,均能够满足工艺要求。
表1 不同稀释体积比的情况下硅片的去除量[17]
Tab. 1 Silicon wafer removals at different dilution volume ratios[17]
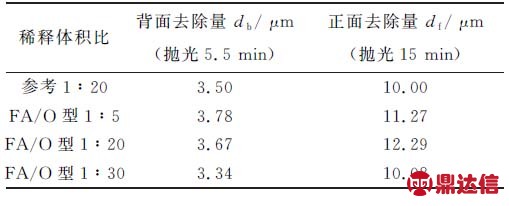
HONG等[18]研究了硅片化学机械抛光时,碱性抛光液中添加FA/O表面活性剂后对硅片表面微粗糙度的影响。他们采用的抛光液由FA/O表面活性剂、FA/O螯合剂和硅胶组成,其中胶体二氧化硅磨粒的平均粒径约为60 nm。试验结果表明:FA/O表面活性剂分子吸附在硅胶颗粒的表面,可以防止硅胶颗粒吸附在晶圆表面,抛光后晶圆表面几乎没有颗粒污染,有效降低了硅片表面微粗糙度,提高了硅片的表面质量。
2.2 抛光垫
抛光垫是影响化学机械抛光的重要因素之一。抛光垫有输送和储存抛光液,去除抛光过程中产生的碎屑等杂质,传递和提供材料去除所必需的机械载荷,为磨粒摩擦作用创造条件等作用[19]。抛光垫的粗糙度、微孔形状、孔隙率和力学性能等因素将直接影响CMP过程,进而影响工件的表面质量。因此,研究抛光垫在硅片CMP过程中产生的影响,选择和设计使用合理的抛光垫是获得较好晶圆表面质量的重要途径之一。
闵新力等[20]对单晶硅片抛光时的接触压力场进行了理论分析和计算,研究了抛光垫弹性模量和抛光垫厚度等参数对抛光后硅片平面度和表面质量的影响。研究结果表明,抛光垫厚度小,泊松比大时,会出现硅片中心压强高的现象。因此,适当减小抛光垫的厚度、弹性模量和泊松比能够使硅片在抛光过程中的接触压强分布较均匀。张春翔等[21]研究了抛光垫的使用寿命对硅片抛光效果的影响。他们使用SUBA系列聚氨酯抛光布和POLITEX系列精抛光布,在抛光压力为24 kPa,抛光液流量为1.8 L/min的条件下,应用日本不二越的SPM-19抛光机,对直径为100 mm的硅片进行了试验。分别记录了使用抛光垫1、5、15、30、50 h和更换抛光垫前6个时间点的硅片抛光速率和硅片的几个技术参数(TTV、TIR、STIR)。分析数据后得出以下结论:抛光速率随着抛光垫的使用时间延长而下降。当抛光垫的使用时间在5~30 h时,硅片抛光的各参数值保持稳定。
YIM等[22]研究了抛光垫孔径对硅片抛光后的表面质量的影响。他们通过使用1种较大孔径(100 μm)和3种较小孔径(小于50 μm)的抛光垫对直径为300 mm的硅片进行抛光试验。研究发现,使用孔径为100 μm的抛光垫抛光的硅片RMS值为0.18 nm,而使用小孔径的抛光垫抛光后的硅片RMS值为0.12 nm。因此,使用孔径小的抛光垫,更有助于实现硅片表面的平坦化。但是,小孔径抛光垫容易使硅片表面缺陷水平增高。SATAKE等[23]研究了抛光垫厚度以外的抛光因素,用来防止接触应力集中在工件边缘附近。他们首先在抛光垫表面引入了具有较大宽高比的凹槽,来制造具有各向异性高杨氏模量的抛光垫。并通过试验发现,具有凹槽的抛光垫抛光后硅片的边缘塌边量(roll-off amount,ROA)较小。基于这个结论,他们设计了一个宽2.2 mm,深1.0 mm的格子槽式抛光垫,以获得较高的杨氏模量。抛光垫表面凹槽如图8所示。除此之外,他们认为大泊松比的抛光垫也利于减小硅片边缘的塌边量,并将具有足够硬度和弹性的乙烯-醋酸乙烯酯泡沫与橡胶混合获得大泊松比的抛光垫。通过与商用抛光垫的抛光效果对比,验证了设计的抛光垫能有效减小硅片塌边量。
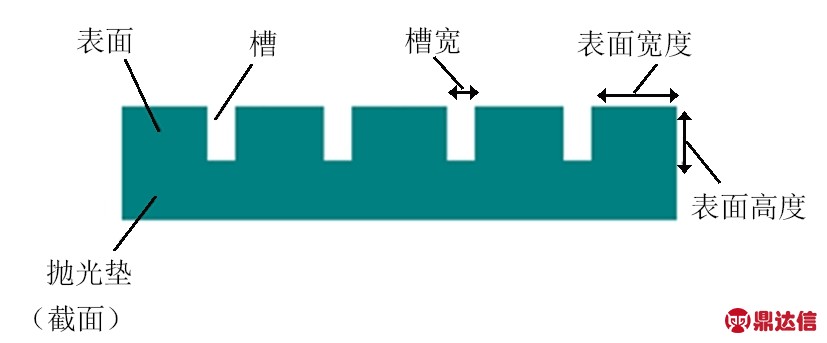
图8 抛光垫表面凹槽示意图[23]
Fig. 8 Schematic diagram of surface groove of polishing pad[23]
WANG等[24]在考虑化学机械协同作用的前提下,研究了抛光垫与硅片之间接触点的大小和分布,在抛光垫粗糙度尺度下建立了材料去除率(MRR)模型。并使用A型和B型2种类型的抛光垫,分别模拟接触点分散分布和接触点集中分布2种实际接触条件。A型和B型抛光垫表面形貌如图9所示。试验结果表明:使用A型抛光垫进行抛光的硅片表面材料去除率高于B型抛光垫的。即抛光垫与硅片接触点分散分布时,可以获得更高的材料去除率。
最近,SATAKE等[25]又研究了抛光垫的黏弹性行为及其对硅片边缘附近材料去除分布均匀性的影响。采用硅溶胶抛光液,直径为35 nm的磨粒,13.8 kPa的抛光压力对直径为125 mm的硅片进行了双面抛光试验。设计了2种试验环境:一种是硅片载体中心与抛光盘中心角度不变的情况;一种是硅片载体中心与抛光盘中心角度分别为0°、-20°、-40°、-60°、-80°的情况。试验结果表明:在2种条件下抛光后的硅片平均的材料边缘滚落值(edge roll-off,ERO)分别为450 nm和370 nm,因此,提出的抛光条件能够有效减小硅片的ERO值。
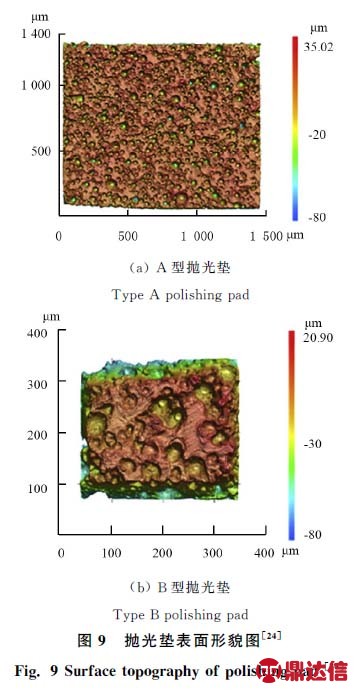
2.3 抛光压力
在硅片的CMP过程中,抛光压力的大小、在抛光面上的分布均匀性和接触压强的分布状态会对硅片质量产生直接影响,是一个关键的工艺参数。一般情况下,随抛光压力的增大,CMP的机械作用增强,有利于提高抛光速率;但当抛光压力过高时,会造成抛光速率不均匀、抛光垫磨损严重,并增大了划痕出现的概率,降低硅片的抛光质量。因此,施加稳定可靠的抛光压力对抛光速率和硅片表面质量具有非常重要的意义。
LUO等[26]基于接触力学理论和统计学理论,建立了硅片-磨粒-抛光垫之间的接触模型。他们认为硅片与磨粒、抛光垫与磨粒之间产生的接触变形均为塑性变形。具体的接触模型示意图如图10所示。这个接触模型考虑到了有效磨粒数、抛光垫特性和抛光工艺参数等因素,但是未能将材料去除率进行定量化。
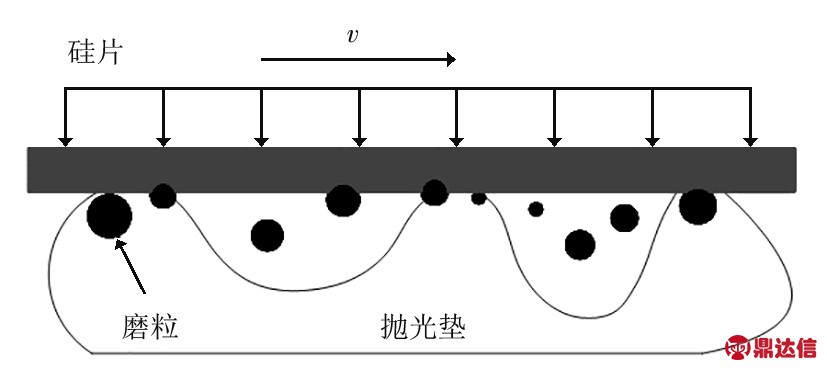
图10 硅片-磨粒-抛光垫之间的接触模型示意图[26]
Fig. 10 Schematic diagram of contact model between silicon wafer and abrasive polishing pad[26]
LIN等[27]研究了抛光头对硅片表面接触应力分布的非均匀性影响。在0~0.035 MPa的压力范围进行仿真分析,发现硅片中心区域和最大应力将随抛光头背压的增大而增大,但应力分布的非均匀性将会减小。因此,在抛光过程中,可以通过适当提高抛光头的背压,获得更平整的加工表面。
吕玉山等[28]利用有限元分析方法,建立了硅片有背垫抛光时的接触力学模型和边界条件,对接触压强的分布进行了分析计算,并通过试验验证,获得了硅片与抛光垫接触表面压强的分布形态和背垫的物理参数对压强分布产生的影响。杜家熙等[29]研究了硅片表面的接触压力随外加载荷的变化。他们将硅片与抛光垫之间的接触模型简化为刚性平头压入弹性半空间的模型。作用在抛光垫上的压力分布通过以下公式进行计算:
(3)
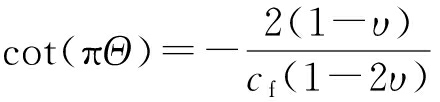
(4)
其中:cf为摩擦系数,P0为硅片上的平均工作压力,r为半径。
在 P0=20.685、41.370、62.055 kPa,r=50 mm,υ=0.28,Δx=0.05 mm(步长)的条件下进行了试验,结果如图11所示。从图11可以看出:硅片表面接触压力随外加载荷的增加而增大,但接触压力分布曲线基本以平行态变化。
ZHOU等[30]在研究CMP过程中的接触压力分布时,在混合弹流润滑模型的基础上,引入了层状弹性理论,该理论可以更加准确高效地预测接触压力的分布和硅片表面的材料去除率,并通过试验验证了该理论的合理性。除此之外,杨玉梅等[31]通过试验,研究了不同的抛光压力对硅片微粗糙度的影响。试验中抛光压力分别设置为15.0、17.5、20.0、22.5、25.0、27.5、30.0、32.5、35.0 kPa。每种压力下均抛光5片硅片,抛光清洗后对硅片的微粗糙度值进行测量,测量结果如图12所示。
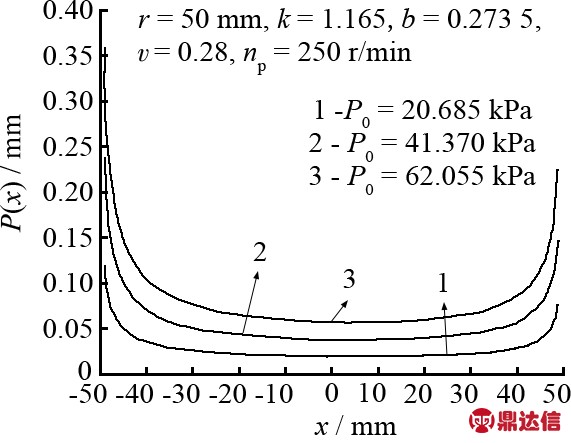
图11 压力对硅片表面接触压力分布的影响[29]
Fig. 11 Effect of pressure on contact pressure distribution on silicon wafer surface[29]
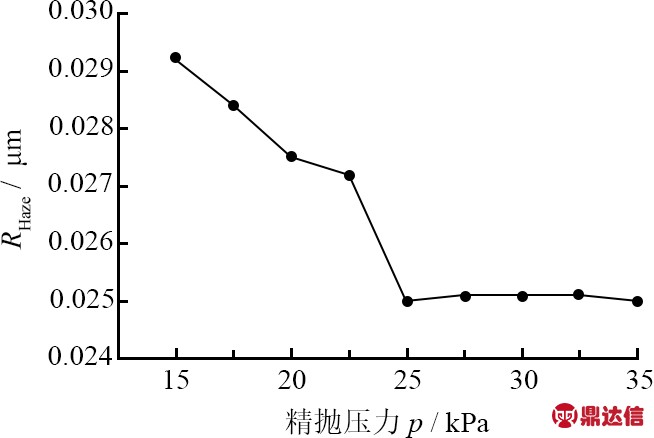
图12 硅片在不同抛光压力下微粗糙度值[31]
Fig. 12 Micro roughness of silicon wafers under different polishing pressures[31]
图12表明:当抛光压力为15.0~25.0 kPa时,硅片表面微粗糙度值随压力增大而减小,视为表面质量改善阶段;当抛光压力为25.0~35.0 kPa时,微粗糙度值趋于稳定,不会随着压力的增大而改变。基于普莱斯顿方程进行分析,这种试验结果与化学机械抛光过程中占主导地位的是化学作用还是机械作用有关。
2.4 抛光设备
在半导体行业中,CMP技术最早被应用于硅片衬底的抛光和硅片的回收利用。20世纪80年代中期,美国的IBM公司成功将CMP技术应用到内存芯片的生产制造过程中。随后,CMP技术逐渐被广泛应用于各种逻辑电路和存储器芯片的制造过程中。同时,美国和日本的CMP设备厂家陆续推出了不同种类的CMP设备来满足日益增长的技术需求。随着晶圆尺寸的不断增大和特征尺寸的减小,对CMP平坦化效果的要求越来越高,这就给抛光设备提出了更高的要求,国内外的技术人员也越来越注重CMP抛光设备的研究与改进。
目前CMP设备主要有3种类型:(1)旋转式CMP设备,以美国应用材料和日本荏原制造所为代表;(2)轨道式CMP设备,以Novellus为代表;(3)以美国的Lam Reasearch公司为代表的皮带平移式CMP设备[32]。随着CMP技术的发展,对设备也提出了很多新要求,如设备的集成化、高精度的温度控制系统与自动传输系统、干进干出系统等[33]。国内进行CMP设备研发的单位主要有天津华海清科机电科技有限公司和中国电子科技集团公司第四十五研究所。但是据统计,中国大陆地区的高端CMP设备仍依赖于进口[34]。下面主要介绍几种比较典型的CMP设备现状。
2.4.1 德国的Peter Wolters公司
德国的Peter Wolters为欧洲知名的半导体设备制造商,一直专注于CMP设备的研发,其设备在金属工业、半导体工业和陶瓷工业等被广泛使用。Peter Wolters公司设计生产的CMP设备的型号主要有:PM200-Apollo、HFP200、HFP300、AC microLine 1500-P3,AC microLine 2000-P3,AC microLine 2000-P4等。其中,HFP为Peter Wolters设计开发的用于300 mm硅片加工的最新设备。该设备具有4个抛光头,2个抛光台,可以实现硅片的自动传输功能,其抛光头转速为0~120 r/min,抛光工作台转速为0~125 r/min。此外,Peter Wolters的AC microLine系列高效双面抛光机,在主要部件的模块化系统基础上增加了最新的精密控制、驱动和测量技术,提高了工艺的可靠性,操作更加简便。所有的机器均可以配备自动化装备,可进行半自动和自动化版本的选择,不仅能够提高生产率,还保证了最佳的单位成本,更加经济。该型号的CMP抛光双面抛光设备,可以用于加工直径为200~450 mm的硅片。该系列的设备具有独特的上压板自适应控制(upper platen adaptive control,UPAC)系统,能够保证在抛光过程中上下工作轮之间的平行和间隙的稳定,补偿了由于热膨胀等因素引起的工作轮偏转等问题。
2.4.2 日本荏原(Ebara)制造所
日本荏原(Ebara)制造所设计生产的旋转式CMP抛光设备近几年的销售量遥遥领先。其主要的设备型号有F-REX200型和F-REX300型。其中F-REX300是针对300 mm的IC制造设备,具有2个抛光头和2个抛光台,抛光头转速范围为10~120 r/min,抛光台转速为10~150 r/min。F-REX300设备的特点是增加了清洁装置的数量,使其在更换消耗品和在系统运行时进行其他维护方面更先进。截至2019年9月,日本荏原(Ebara)制造所已经出售了800多台200 mm圆片的CMP设备,100多台300 mm圆片的CMP设备。
2.4.3 天津华海清科机电科技有限公司
2017年2月24日,天津华海清科机电科技有限公司研制的300 mm Universal-300 Plus型CMP设备正式进入中芯国际并投入工艺生产。这是首台国产CMP工艺设备进入集成电路大生产线。该设备用于大生产线wafer reclain(硅片再制造)生产,加工后的硅片表面粗糙度小于1 nm。截至2019年4月,该机已累计加工6万余片硅片。此后,天津华海清科机电科技有限公司相继推出了Universal-200 Plus和Universal-200型的化学机械抛光机,用于200 mm晶圆的精密加工。其中,Universal-200型CMP设备的材料去除均匀性优于进口设备30%以上,同时还能兼顾150 mm晶圆的化学机械抛光,被广泛应用于集成电路制造、MEMS制造、硅片抛光等多个领域。
2.4.4 中国电子科技集团公司第四十五研究所
2017年11月21日,中国电子科技集团公司第四十五研究所成功研制200 mm化学机械抛光机并完成了离线测试。这是国内首台拥有完全自主知识产权的200 mm化学机械抛光商用机。该抛光机设备具有光学在线终点检测模块,可以使晶圆的片间非均匀性≤ 3%,并且攻克了高精度低压力控制技术,设计研发了适用于CMP生产线的压力控制模组,其控制精度可以达到±0.137 9 kPa,调节时间小于1 s。
3 结论
本文介绍了硅片化学机械抛光技术的研究现状,主要包括影响硅片表面质量和表面材料去除率的因素,如抛光液、抛光垫、抛光压力等,并对目前用于硅片化学机械抛光的先进设备也进行了总结。虽然近年来CMP技术发展很快,但是仍面临着很多尚未解决的问题。例如,CMP过程中的工艺参数变化对表面材料去除率、材料去除非均匀性和表面质量的影响等实际问题仍然没有完全解释清楚,CMP的去除机理仍有待进一步的研究和分析。同时,国内外各设备厂商仍然需要研制更为先进的CMP设备,以满足先进集成电路技术的发展。