摘要 为了考察线速度对金刚石线锯切割过程的影响,研究了不同线速度条件下金刚石线锯的磨损情况以及硅片表面质量情况, 通过SEM及粗糙度仪对切后线材、硅片等进行微观及量化分析。结果表明:线速度由1 300 m/min提高至1 800 m/min,金刚石线锯磨损量由3.5 μm逐渐降低到2.5 μm,降幅为28.6%;金刚石线锯切割硅材料为塑性及脆性模式混合去除,硅片表面的形貌呈现沟槽状、连续划痕并伴随大量凹坑;随着线速度的增加,硅片表面粗糙度逐渐减小,算数平均粗糙度Ra、最大高度Rz以及最大表面粗糙度Rt数值分别下降了33.7%、37.8%、45.6%,表面凹坑数量随着线速度的增大也逐渐减少。
关键词 金刚石线锯;多线切割;硅片;线速度
从2016年底到2017年上半年,光伏市场逐渐向好,需求量剧增。作为光伏产业链中重要的一环——线切工序,也由传统砂浆切割模式向金刚石线锯切割模式转变。
目前,金刚石线锯线切技术已逐渐成为光伏产业中降本增效的重要手段之一。随着线切设备以及线材的不断优化改进,线切割效率大幅提高、线切成本持续降低。切割时间从砂浆时代的9 h降至2 h左右,单台日切割刀数由2.3刀/天增加至9刀/天,单机产能提升了约3倍。金刚石线锯(基线)线径从最初的120 μm逐渐降低至60 μm,每公斤(13.66 mm/kg)出片数由40片提高至50片,硅料利用率大幅增加。
国内外学者对金刚石线锯硬脆材料的切割及其机理进行了一定的研究。ARKADEEP等[1]研究了金刚石线锯磨损对硅片表面形貌、粗糙度及亚表面损伤层的影响;TAKAAKI等[2]对单晶硅金刚石线锯切割材料去除机理及亚表面损伤进行了研究;MEIβNER等 [3]团队则重点研究了多线切割过程中线网张力的衰减;何健等[4]研究了往复式线切割对单晶硅表面粗糙度的影响;张玉兴等[5]研究了金刚石线切割单晶碳化硅锯切力的机理;高玉飞等[6]对往复式电镀金刚石线锯切割单晶硅片的特性进行了研究。
以上研究均未涉及实际生产环节,基于实际生产过程,采用基线60 μm的金刚石线锯,实验研究了不同线速度下切割线的磨损情况及对切割质量的影响,并进行了一定的理论分析,为硅片用金刚石线锯切片工艺参数的优化提供一定的指导。
1 实验方法
实验采用青岛高测科技股份有限公司自主研制生产的GC-700型号金刚石线锯专用线切机,该型号线切机具有线速度高、张力稳等特点,可满足实验需求。实验所用的金刚石线锯为青岛高测科技股份有限公司生产的60 μm基线电镀金刚石线锯(图1),表1为该型号金刚石线锯的性能表。
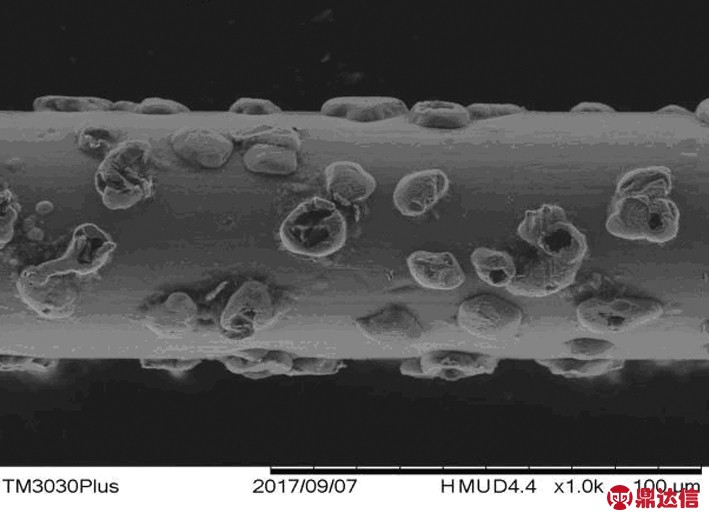
图1 60 μm基线电镀金刚石线锯
表1 金刚石线锯性能表
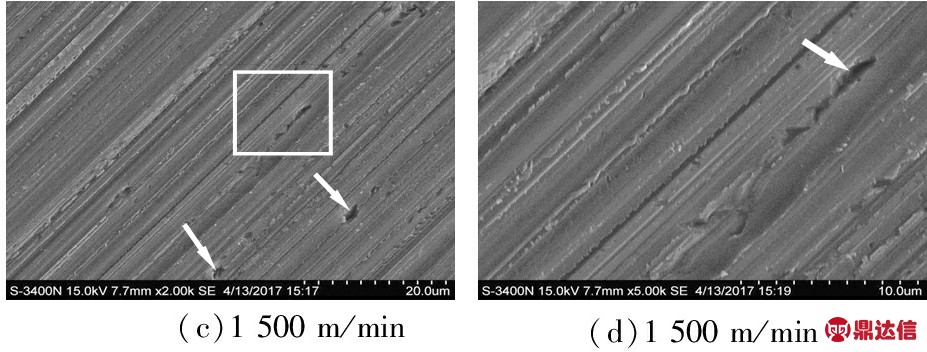
采用往复切割模式,切割原理如下图2所示。硅棒在线网上方,为下压式行进,按工艺设定进行切割。线网进线、回线侧各有一组张力控制单元,用于调整切割张力,主辊上金刚石线锯正反向交替运动对硅棒进行切割,另外线网两侧各有一套喷淋装置用于线材冷却。
实验以目前市场主流M2型单晶硅棒为实验材料,切割棒长650 mm,切割标准片厚为190 μm,使用国产单组分水溶性切割液(每刀用量为1 kg,添加纯水350 L,pH值:6.8~8.0,电导率≤400 μS/cm),切前充分混合搅拌1 h。切割液在线切过程中主要起到润滑、切割过程保证无异常停机,单刀耗时为2 h,使用1 300、1 500、1 800 m/min线速度切割时耗线量相同,切前为全新线网且线网宽度相同。
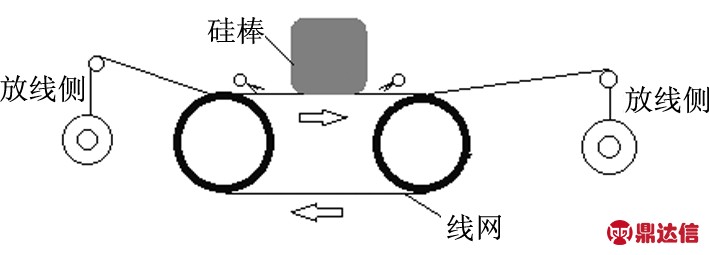
图2 线切原理示意图
冷却、分散等作用。实验工艺如表2所示。
表2 实验工艺表
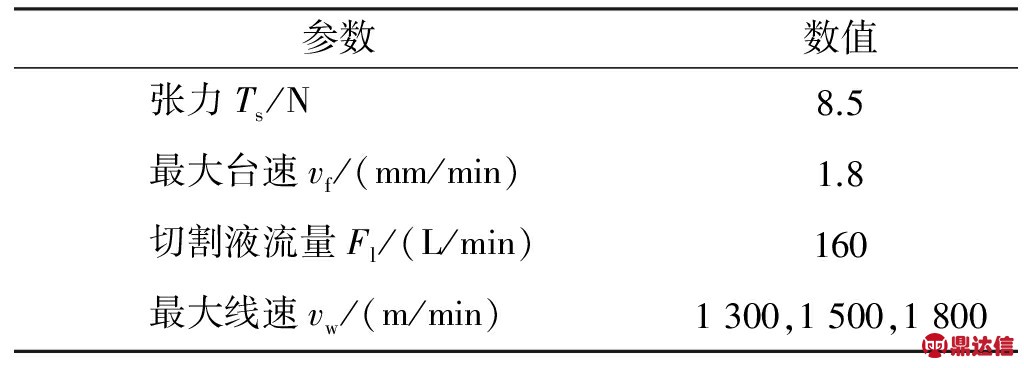
切割结束后,对硅片进行预清洗、脱胶、清洗、甩干处理,确保硅片表面清洁,3刀样片取硅棒相同位置。另外,切后金刚石线锯也取相同切割位置的线样,将线样进行超声清洗、烘干处理后备用。
使用日本三丰SJ-210型表面粗糙度测量仪进行样片表面粗糙度检测;使用日本三丰293-821型数显外径千分尺进行线样线径测量;使用日本日立S-3400N型扫描电镜进行微观形貌分析。
2 实验结果与分析
2.1 切后金刚石线锯形貌分析
图3为不同线速度切后金刚石线锯SEM形貌图。从图3a的1 300 m/min线速度情况中可以看出:大部分金刚石颗粒已裸露出来,且出现明显的磨损现象;图3b线速度为1 500 m/min的情况则较1 300 m/min的磨损稍轻,金刚石颗粒部分裸露;当线速度增至1 800 m/min时(图3c),观察到金刚石颗粒裸露情况较图3b更轻,基本上金刚石颗粒还未出现裸露情况。在实验中,随着线速度的增大,线材上金刚石的磨损情况逐渐减轻,即提高线速度有利于降低金刚石线锯磨损。表3为不同线速度条件下金刚石线锯磨损量对比表。从表3中可以看出:随着线速度的增加,金刚石线锯磨损量逐渐减轻,线速度为1 300 m/min时,切割前后磨损量为3.5 μm,当线速提高至1 800 m/min,磨损量为2.5 μm,进一步验证了SEM照片的结果。
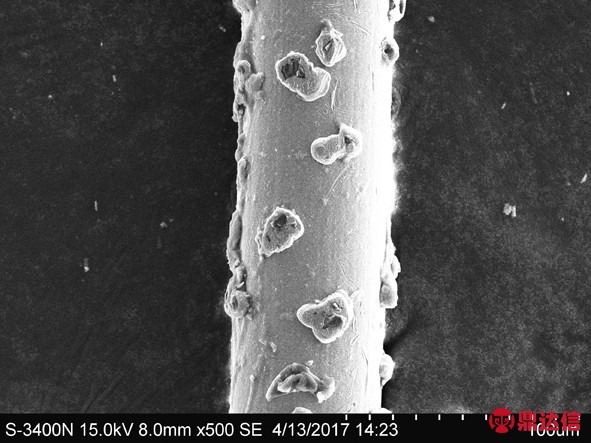
(a)1 300 m/min
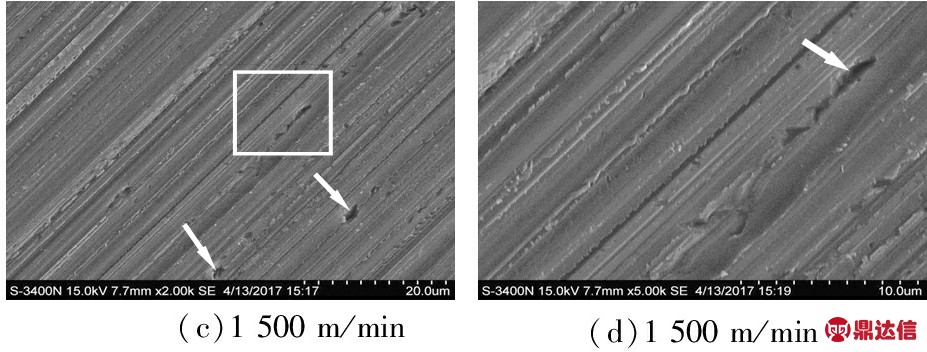
(b)1 500 m/min
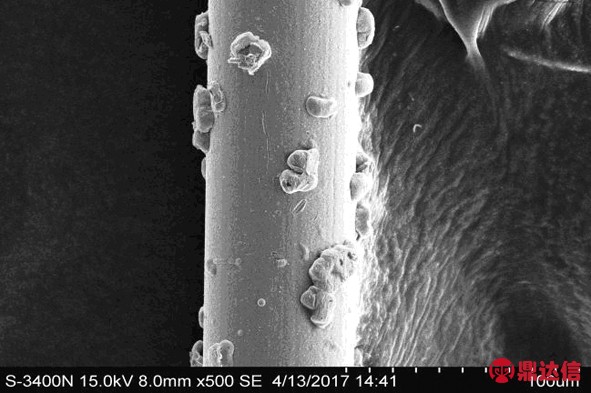
(c)1 800 m/min
图3 不同线速度切后钢线形貌
表3 金刚石线锯磨损量对比表
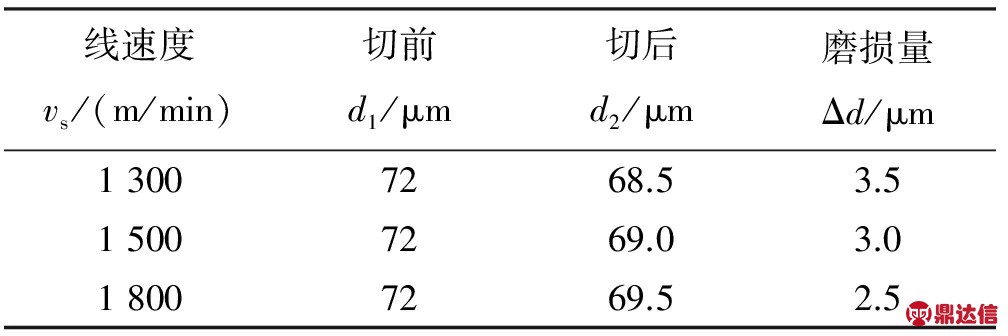
2.2 硅片表面分析
金刚石线锯切割的硅片表面与传统砂浆切割的硅片表面存在明显差异,呈现典型二体磨损特征,图4为金刚石线锯切割后硅片表面形貌。从图4可以看出:硅片表面形貌主要表现为平行划痕,部分划痕边缘还有不规则的脊状隆起,局部还伴随着剥落状微坑,这种微坑即为脆性剥落去除区域。由此可知,金刚石线锯切割以塑性变形为主,脆性剥落为辅。图4中白色箭头所标位置即为脆性剥落区域,该区域典型形貌呈非规则凹坑状,线速度为1 300 m/min时,脆性剥落区域出现了连续链状分布的情况,且凹坑面积大,另外条状塑性区域表现出纹理紊乱、不规则;线速提高至1 500 m/min,(如图4c、4d),硅片表面脆性剥落区域逐渐减少,塑性条纹状区域逐渐增加;当线速提高至1 800 m/min(如图4e、4f),硅片表面脆性剥落区域较1 500 m/min时的更少,塑性条形状区域面积最大,表现出良好的表面状态。由于脆性剥落对硅片的力学性能不利,在实际线切过程中,塑性区域越大则硅片力学性能越优。
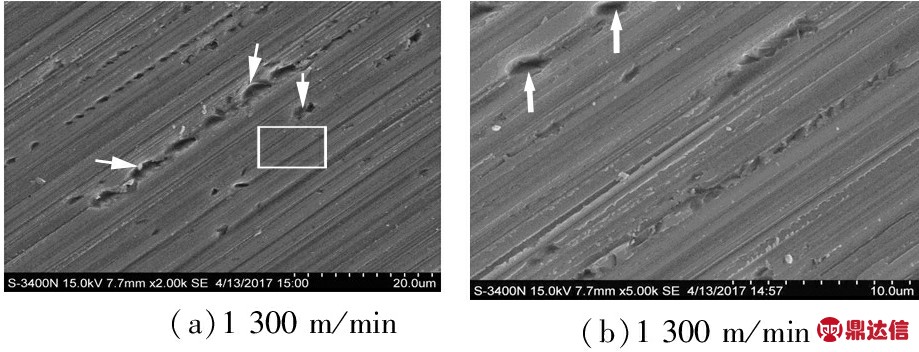
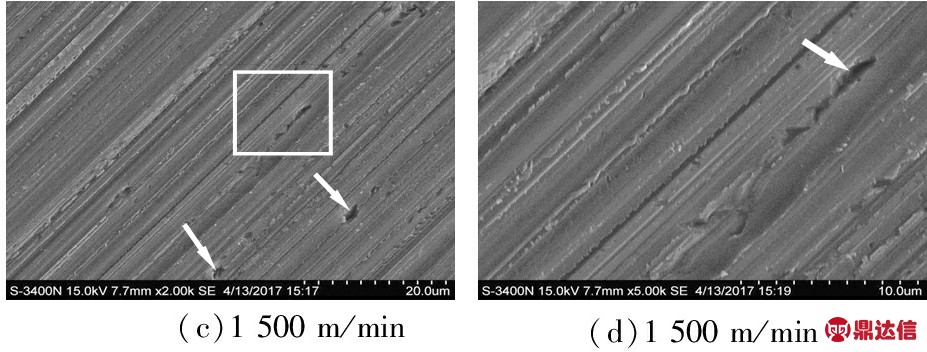
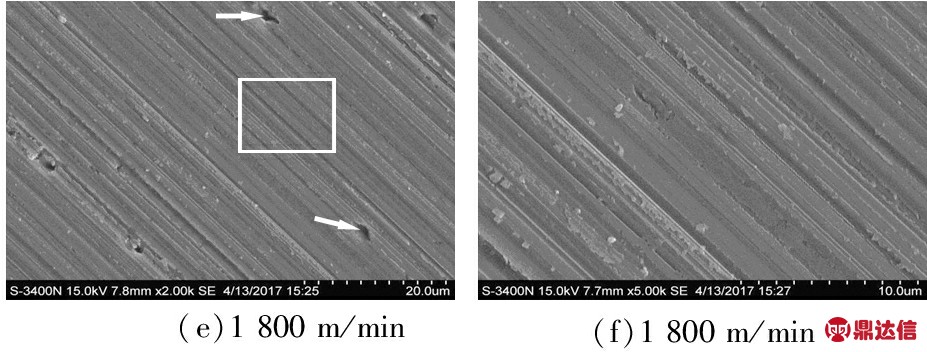
图4 切后硅片表面形貌
图5为不同切割线速度硅片断面形貌SEM照片。将3张图片对比可以看出:随着线速度逐渐增加,断面形貌凹凸感逐渐减轻;当线速度达到1 800 m/min时,断面表面光滑,无明显凹凸感。线速度不同,金刚石线锯在负载时微振动情况会有所差异,造成高线速度时断面表面光滑,低线速度时断面表面粗糙的情况。另外,断面表面差异也与切割过程负载变化等因素有关,线速度提高,在一定程度上增强了金刚石线锯的切割能力,使得相同进给速度条件下,金刚石线锯对垂直硅片表面的压力降低,有利于减小硅片的表面损伤层深度,从而提高断面表面的光滑程度。通过测量样片粗糙度值来表征硅片表面质量,图6为3种线速度条件下硅片表面粗糙度对比图。从图6中可以看出:随着线速度的增加,硅片表面粗糙度值逐渐降低。实验分别验证了算数平均粗糙度Ra、最大高度Rz以及最大表面粗糙度Rt(JIS2001标准)。其中,3种线速度条件下,Ra值下降趋势缓慢,Rz及Rt下降趋势明显;1 800 m/min线速度时,表面粗糙度Rt为1.269 μm,Rz为1.080 μm;而1300 m/min线速度时表面粗糙度Rt为2.349 μm,Rz为1.736 μm;相较1 300 m/min,1 800 m/min条件下Rt、Rz分别降低了46%、38%,表面质量表现良好。通过测量样片表面粗糙度,也进一步验证了SEM照片中不同线速度的差异性。
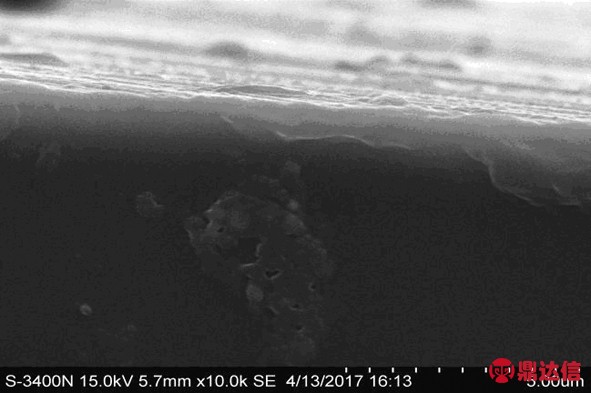
(a)1 300 m/min

(b)1 500 m/min
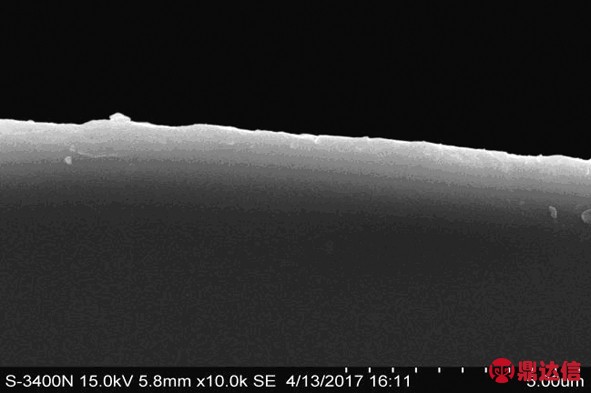
(c)1 800 m/min
图5 不同切割线速度硅片断口形貌图
硅片表面粗糙度主要取决于金刚石线锯线速度及工作台进给速度, LAMBROPOULOS及WANG等对单颗金刚石刻深进行了理论推导。单颗粒刻深的大小与张力、金刚石线锯性能、切割液效果等有关系。
h=0.439(sin θ)1/2(cot ψ)1/3(E/H)1/2(Fn/H)1/2[7];
(1)
Fn=1.032 2(vf)0.935 5(vs)-0.878 5(ρ)0.042 4·D·l[8];
(2)
则
h=kvf0.467 75/vs0.439 25
法藏的汉文敦煌文献从P.2001号编到P.6040号,去掉中间的空号,加上夹杂在藏文中的汉文遗书,总数将近4000号。
(3)
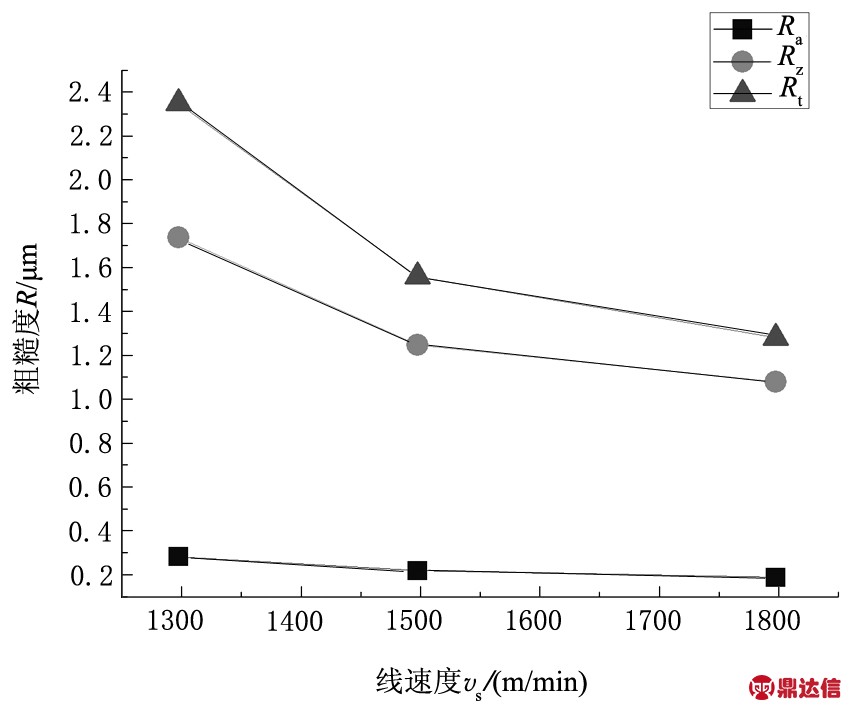
图6 3种线速度条件下硅片表面粗糙度对比图
从公式(3)中可以看出:线速度越高,则刻深越小,反映到粗糙度值则越低,反之亦然。
3 结论
(1)通过对不同线速度下金刚石线锯磨损情况、硅片表面质量的对比,发现随着线速度的提高,金刚石线锯磨损量逐渐减少,由1 300 m/min时的3.5 μm下降至1 800 m/min时的2.5 μm,降幅达到28.6%,利于实际切割过程中降低金刚石线锯使用量,降低硅片加工成本;
(2)硅片表面质量随线速度的提高明显改善,由于脆性模式造成的凹坑数量及面积降低,塑性变形区域逐渐增多,因此提高线速度有利于改善硅片质量,同时对于薄片化也会起到有益的影响。
(3)随着线速度的提高,算术平均粗糙度Ra、最大高度Rz、最大表面粗糙度Rt数值分别下降了33.7%、37.8%、45.6%。