摘 要:线痕的存在影响电池片的生产质量。本文通过分析线痕产生的原因,阐述了线痕对电池的影响,并简单解析了线痕分选的标准。
关键词:硅片;线痕;电池;印刷
目前,光伏行业面临产能过剩的状况,客户对于组件的要求越来越严格,电池片的质量又影响到组件质量,而硅片质量的好坏直接关系到电池的制备。线痕是影响硅片表面质量的一个重要因素。电池片生产过程中制绒需要利用腐蚀的各向异性,而线痕可能对腐蚀造成影响,在印刷浆料过程中会影响到印刷效果,从而增加电池制备的困难并且影响转化效率。
一、线痕产生的原因
线痕是硅片在切割过程中产生的痕迹,属于硅片的外在缺陷,也是硅片经常出现的问题。产生线痕的原因有很多,大致分为以下3类:
(一)跳线、断线的因素
跳线造成的线痕一般会集中在晶棒的某一段,有时整个晶棒也出现线痕;断线后的晶棒即使能够挽救回来,或多或少也会产生线痕片。跳线造成的线痕一般都是单一线痕;断线造成的线痕也会是单一线痕,有时会形成亮线片。
(二)砂浆因素
在硅片切割过程中,由于砂浆的切割能力不足,导致钢线直接摩擦硅片表面而形成的线痕大多是均匀的小细纹线痕,严重的还会带有亮线。
(三)硅块内部杂质因素
若硅块内部存在杂质,由于杂质与硅的硬度不同,当高速运转的钢线带动碳化硅切割到该处时便会产生线痕。一般会是凹、凸的线痕,表面可以看到黑点(杂质)。这类线痕直接导致硅片表面不合格。
二、线痕对电池的影响
多晶硅电池片制备工艺需要硅片经过制绒、扩散、刻蚀、P E镀膜、印刷烧结、测试包装最终产出电池片。印刷烧结是生产多晶硅太阳能电池最关键的步骤之一,即在硅片的正面和背面制造非常精细的电路,将光生电子导出电池。这个金属镀膜工艺通常由丝网印刷技术来完成——将含有金属的导电浆料透过丝网网孔压印在硅片上形成电路或电极。在正面印刷过程中,使用最多的是密栅丝网,其目的是为了更多吸收电池片表面的电荷来提高电池的转换效率。线痕的存在除了影响到电池生产中的碎片率,还会影响到电池的外观质量乃至电池性能。
存有线痕的硅片经过制绒腐蚀,在印刷过程中,如果印刷前硅片线痕的方向与电池正面栅线的方向平行一致,会导致某一根栅线印粗,影响最大的是电池片的外观质量,从而会影响组件的外观。
如果印刷前硅片线痕的方向与电池片正面栅线的方向垂直,会导致在线痕线上多根栅线印虚,直接影响电池片的效率和外观。在电池分选过程中,存在栅线粗和栅线印虚严重的电池,直接会判为斑点片(即不合格片)。若硅片表面存在亮线,在制绒腐蚀时,不容易将亮线处腐蚀掉,从而导致在P E镀膜或印刷后仍能够看到亮线。明显的亮线直接影响到电池的外观质量,甚至是组件的外观质量。
三、线痕硅片的分选
为了提高电池片的转换效率,使用最多的是密栅工艺。电池片正面栅线越密集,栅线印刷在线痕上的几率越大,线痕硅片对电池的影响也越明显。一般情况,会将线痕分为亮线和锯痕两类进行分选。
(一)亮线类
肉眼观察亮度在硅片表面存在高于正常硅片颜色的情况可以划分到亮线类,亮线在不同灯光下所呈现的亮度也不同,它是没有深度的。亮线要按照其亮度和覆盖面积进行分选。在基于人工分选硅片的生产中,按照亮度分选很难将标准量化。因此最常用的方法就是按照亮线的覆盖面积进行分选。图1为亮线片。
(二)锯痕类
锯痕与亮线最大的区别是锯痕是有深度的,如图2。
通过对锯痕深度在5um-10um、10um-15um、15um-20um三种锯痕片进行试验,发现锯痕深度越小,且锯痕较平缓的硅片做的电池片表面外观不合格率越小。因此,锯痕一般是按照深度的大小进行分选。在实际生产过程中,锯痕分布会有所不同。对于硅片存有单根锯痕或几根锯痕,从侧面观察形如此类锯痕可以依据测厚仪进行检测(锯痕取值为锯痕高点值与硅片平面的距离)。针对锯痕分布区域覆盖整个表面,用测厚仪是无法测量此类型线痕片,在满足硅片厚度均匀的条件下,可以使用硅片线痕测试仪或粗糙度仪对其进行测量。实验数据中,针对锯痕存在覆盖整个表面的硅片,使用粗糙度仪测量锯痕深度=15um的硅片,对电池已经有明显影响。基于成本计算,锯痕深度>15um的硅片一般不会予以使用。
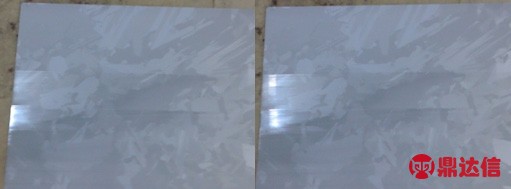
图1 亮线片
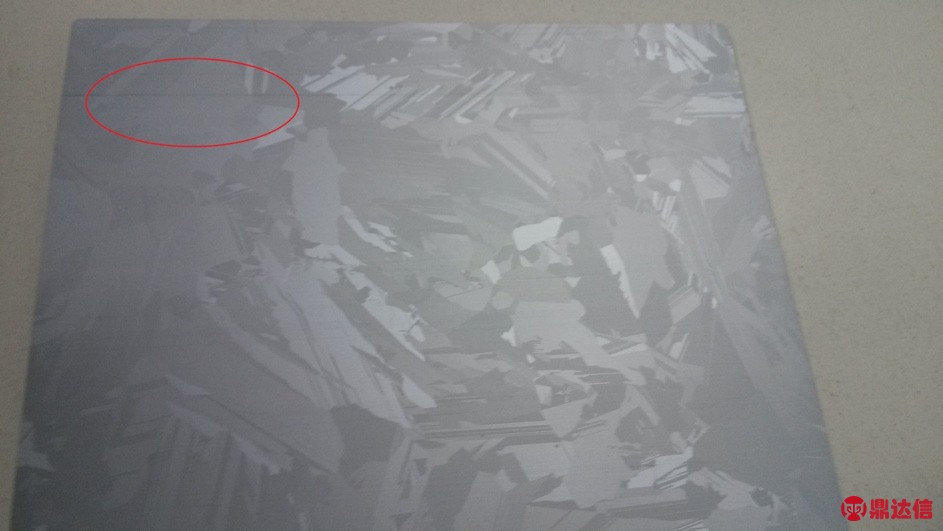
图2 锯痕片
四、结论
在多晶电池的生产过程中,要降低电池表面不合格,除了优化电池工艺,还需要控制硅片尤其是线痕片的质量。要控制线痕片的质量,需要针对各种线痕片产生的原因进行改进。若线痕片已经产生,需要对其按照一定标准进行分选,使得成本最优。