摘 要:多晶硅片或单晶硅片是光伏产业链中太阳能电池片生产的基板材料,近年光伏产业的迅猛发展极大促进了硅片制造技术和装备的飞速发展,文章介绍了当前晶体硅太阳能电池用硅片制备的主要工艺,并对其中的关键技术及发展状况进行了论述。
关键词:硅片;制备;工艺;关键技术
1 前言
太阳能电池是通过光电效应直接将太阳辐射能转换为电能的半导体器件,按基板材料可分为多晶硅、单晶硅、非晶硅、碲化镉CdTe、铜铟硒CIS、铜铟镓硒CIGS、砷化镓GaAs、磷化铟InP及聚合物电池等多种类型。前三种属硅基太阳能电池,目前占全球太阳能电池总量的98%,其中又以多晶硅电池、单晶硅电池等晶体硅太阳能电池占据总量的80%以上,为当前全球太阳能光伏的应用主流,我国所生产的太阳能电池90%以上为晶体硅太阳能电池。
太阳能光伏产业链由多晶硅材料制造-硅锭(棒)/多晶硅片 (单晶硅片)生产 -多晶 (单晶)太阳能电池片制造-组件封装以及光伏发电系统 (组件加上逆变器、控制器、蓄电池等辅助设备)建设构成实用的户用系统或联网系统等多个产业环节组成。多晶硅材料制造处于产业链的上游,是铸造多晶硅锭或直拉单晶硅棒进行切割加工生产多晶硅片或单晶硅片的主要材料,制成的多晶硅片或单晶硅片提供给产业链中游的电池生产作基板材料制造多晶硅电池片或单晶硅电池片进行组件封装。太阳能光伏产业链组成见图1。
近年来,随着能源短缺、环境污染等问题的严重,太阳能电池因其清洁环保、可再生的特点赢得了巨大的市场空间,2010年全球太阳能电池产量已达15 GW(1 GW=1 000MW),其中多晶硅电池占54%,单晶硅电池占37%。随着全球光伏产业的蓬勃发展,我国太阳能光伏制造业也迅速成长,2007年我国开始成为世界太阳能电池的最大生产国,迄今已连续四年产量位居世界首位,2010年产能已达20 GW,实际产量超过8 000 MW,占全球总产量的50%以上[1]。我国太阳能电池产业的爆发式发展极大推动了我国在多晶硅材料制造、铸锭多晶硅与直拉单晶硅切割加工硅片生产领域的迅猛发展。
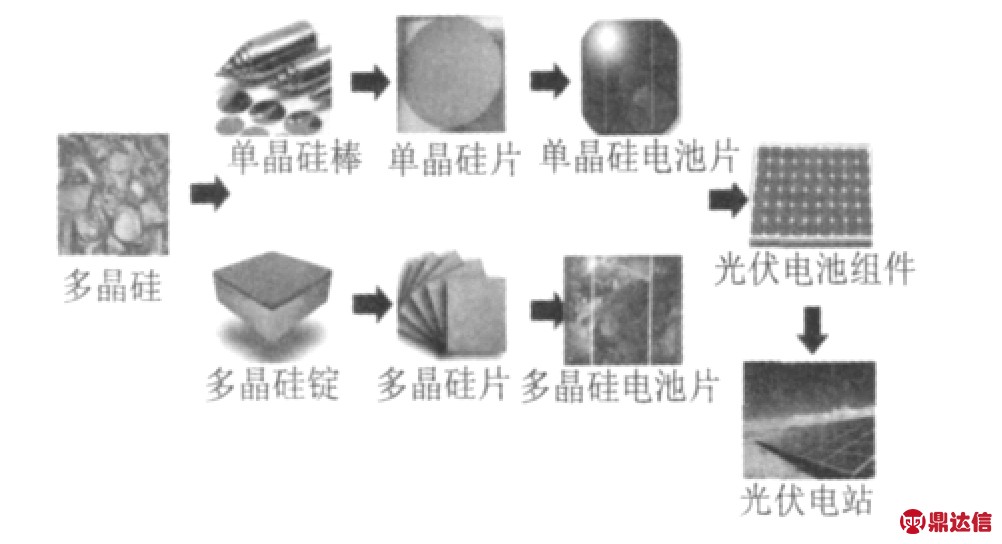
图1 太阳能光伏产业链组成
Fig.1 The composition of solar power photovoltaic industry chain
2 硅片制备工艺与关键技术
当前,用于制造晶体硅太阳能电池片的基板材料多晶硅片主要是通过多晶硅材料定向凝固(DSS)生长多晶硅锭后切割加工制成,单晶硅片则是通过多晶硅材料直拉 (CZ)单晶硅棒后切割加工制成。与直拉单晶硅相比,铸锭多晶硅虽存在晶界形状复杂、高密度位错、缺陷和杂质浓度相对高、少子寿命低、最终电池片光电转换效率比直拉单晶硅低1%~2%的缺点,但也具有单台设备产量大、生产效率和材料利用率高、原材料纯度要求宽 (可使用单晶硅头尾料、埚底料与返回料)、能耗小及生产成本低等多方面的对比优势。因此,铸锭多晶硅近年来不断挤占直拉单晶硅的市场份额,成为了目前最主要的太阳能硅电池材料。
多晶硅片制备的主要工艺包括:多晶硅材料准备→铸锭多晶生长→破锭切方→平磨和倒角表面处理→多线切割→清洗→检验分选等环节。单晶硅片制备的主要工艺包括:多晶硅材料准备→直拉单晶生长→晶棒截断→切方→滚磨表面处理→多线切割→清洗→检验分选等环节。主要工艺流程见图2。
多晶硅片和单晶硅片制备工艺的主要区别在于前端的晶体生长技术和装备不同,后端的切割加工处理工艺基本相同,其关键技术主要包括铸锭多晶硅生长技术、直拉单晶生长技术、多线切割技术等。
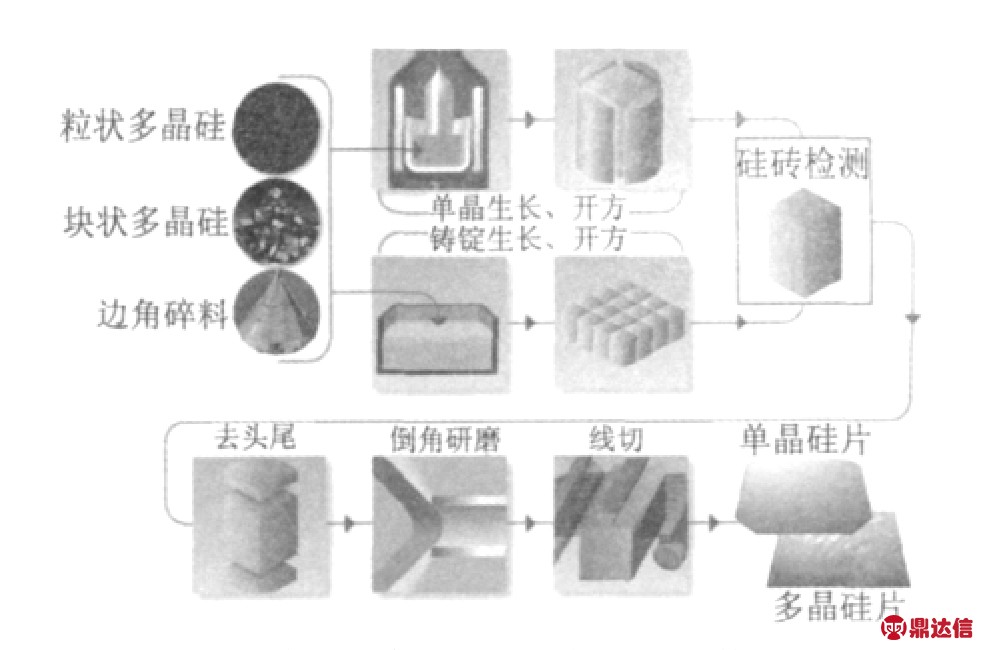
图2 单晶、多晶硅片制备主要工艺流程
Fig.2 Main process flows for preparation of monocrystalline and polycrystalline silicon wafer
2.1 铸锭多晶硅生长技术
铸锭多晶硅生长技术主要分为浇铸法和直接熔融定向凝固法[2]。
1975年,德国Wacker公司首创了将熔化后硅液从坩埚中导入另一经过预热的模具中,通过控制冷却速率和采用定向凝固技术形成晶锭的浇铸法多晶硅材料制造技术,由于受热场等方面的影响,所得晶锭质量不高。其后,研究发展了直接熔融定向凝固法技术,简称直熔法,又称布里奇曼法。此法是将多晶硅料装于方形石英坩锅置于专用的多晶硅铸锭炉内,直接将多晶硅原料在坩埚中熔融,然后将坩埚从热场逐渐下降或从坩埚底部通冷源,严格控制垂直方向上的温度梯度,使固液界面从坩埚底部向上尽量平直移动生长,由于晶体生长结束后一直保持高温,对多晶硅晶体起着“原位热处理”,晶体内热应力降低使晶体内位错密度降低,从而长出取向较好的柱状结构晶粒和电学性能较为均匀的晶锭,与浇铸法相比显著提升了晶体质量,并且具有生长方法简单、易生长出大尺寸的硅锭、易实现自动化的生长控制、易切割成方形硅片,且具有材料利用率较高和成本较低等优点,成为了目前产业界广泛采用的重要技术。
直熔定向凝固法制备多晶硅晶锭的工艺过程主要包括:硅料清洗→坩埚准备→装料→加热→化料→硅晶体生长→退火→冷却等。
为了保证铸锭多晶硅的质量,在铸造多晶硅的生长过程中,关键应控制和解决使其保持有均匀的固液交界面温度、使得铸锭多晶硅存在尽量小的热应力以及能生长出尽量大的晶粒和减少来自于坩埚的污染等技术。
当前,国际上先进成熟的专用铸锭多晶硅生长设备主要由美国和德国的公司生产,铸锭多晶硅单锭质量在400~450 kg之间,单锭生产周期50余小时。发展的趋势是单锭质量和尺寸不断增大,追求生产效率和成晶率的不断提升和能耗与成本的降低,现单锭质量大于600 kg的铸锭设备已投放市场,800 kg甚至1 000 kg的铸锭设备正在研发。我国近年来在铸锭设备的研究和生产方面取得了长足发展,技术水平已逐步接近国际先进水平,市场占有率正快速提升。
2.2 直拉单晶硅棒生长技术
单晶硅棒的生长是采用高纯多晶硅为原料,在直拉单晶炉内将多晶硅熔化,熔融的单质硅在凝固时硅原子以金刚石晶格排列成许多晶核,晶核长成晶面取向相同的晶粒,晶粒平行结合起来便结晶成单晶硅。
单晶硅棒生长技术按晶体生长方法的不同分为直拉 (CZ)和区熔 (FZ)两种,获得的单晶硅分别称为直拉单晶硅和区熔单晶硅。直拉法单晶硅是将多晶硅料装于圆形高纯石英坩锅置于专用的直拉单晶炉内熔化后,经籽晶引导生长而成。此法适用于生产中低阻无位错的单晶硅,主要用于制作晶体管、二极管、集成电路等产品。悬浮区熔法对位错等指标要求较高,是一种无坩埚技术,高温熔体不会被坩埚材料污染,主要用于制作高电阻率的半导体分立器件与探测器等产品。由于CZ法比FZ法更容易生产出大尺寸的单晶硅棒以及成本和性能的原因,目前直拉单晶硅材料的应用占85%以上,太阳能电池用单晶硅一般采用直拉法制备。
为了生长出高质量的 (电阻率、氧含量及氧浓度分布、碳含量、金属杂质含量、缺陷等达标)硅单晶棒,在采用直拉法单晶生长时,关键应控制和解决的技术主要有:①根据不同直径硅单晶的生长技术要求选择合适的单晶生长系统。②生长系统内的热场设计,确保晶体生长有合理、稳定的温度梯度。③生长系统内保温材料的选用;改善热对流的热屏技术设计。④生长系统内的氩气系统与夹持技术设计;为提高生产效率采取连续加料的系统设计。⑤晶体生长过程的工艺控制:包括晶体的提升速度及转速、坩埚的转速、氩气压力及流量等各项工艺参数的优化设置,以实现对单晶硅中氧及氧浓度分布、碳含量、缺陷及电阻率均匀分布的有效控制[3]。
直拉法生长单晶硅棒的工艺过程主要包括:加料→熔化→缩颈生长→放肩生长→等径生长→尾部生长→冷却等。
2.3 硅砖 (棒)多线切割技术
铸锭多晶硅和直拉单晶棒经破锭开方与表面处理后对硅砖 (棒)进行多线切割和后处理即产出硅片。
多线切割是目前国际上先进的加工技术,对硅砖 (棒)切割具有切割表面质量和切割效率高、可切割大尺寸材料、方便后续加工等优点,目前已逐渐取代传统的内圆切割技术。它是通过切割钢线的高速运动,将磨料 (碳化硅微粉)和切割液(聚乙二醇)混合成的砂浆带入切割区对硅砖(棒)进行研磨切割,可一次性将总计1 m长的硅砖 (棒)切割为数千片薄片的新型切割加工技术。
近年来,随着光伏产业在电池片生产方面的技术发展,对硅片的切割加工质量也提出了更高要求:如硅片不能有表面损伤 (细微裂纹、线锯印记),对形貌缺陷 (弯曲、凹凸、厚薄不均)也有严格的控制指标要求。一方面硅片趋向大尺寸发展;二方面硅片必须有极高的平面精度和极小的表面粗糙度;三方面由于硅片的机械脆性,切割工艺如果不能实现对工艺线性、切割线速度和压力、切割冷却液的精密控制,所产生的细微裂纹和弯曲都会对产品优良率直接产生负面影响;四方面为了不断降低硅料的切割损失以降低成本,要求切割钢线的直径要不断减小。然而,为使生产效率达到最大化,更高的切割速度和更大的切割荷载将会加大切割钢线的拉力,增加切割线的断裂风险。由于同一硅块上所有硅片是同时被切割的,一旦发生切割线断裂事故,所有正在切割的硅片都将成为废品。但使用更粗更牢固的切割钢线也不可取,这会增加硅料的损失减少每次切割所生产的硅片数量。
对硅砖 (棒)的多线切割是硅片生产的关键工序,技术要求是:①切割精度和表面平行度高,翘曲度和厚度公差小。②断面完整性好,消除拉丝、刀痕和微裂纹。③保证成品率前提下切出超薄形硅片以及缩小钢丝切缝,降低硅料损耗。④提高切割速度,实现自动化切割。⑤切割过程对碳化硅微粉的粒型及粒度,砂浆粘度与流量,钢线速度、张力与硅棒进给速度等的优化控制[4]。
为此,多线切割机的关键技术包括①高精度排线导轮 (导丝辊)多辊同步驱动技术;②钢线保持相对恒定的张紧力,保证切割表面质量的恒张力控制技术;③配合钢线张力自动控制进给系统,保证在不断线的条件下实现切割高效性的高精度切割进给伺服控制系统;④高精度排线导轮系统的制造及耐用度技术等。
由于多线切割机制造技术难度大,核心技术长期被瑞士、日本等国家的极少数公司所垄断,目前国内使用的多线切割机几乎全部依赖进口,随着我国光伏产业的不断发展,我国相关企业正在积极开发具有自主知识产权的多线切割技术及装备。
3 结语
晶体硅太阳能电池用硅片的制备是光伏产业链中最重要的关键环节之一,太阳能电池的发展方向是不断提高电池的光电转换效率和减薄化,最大限度降低每瓦生产成本,以有利于发电成本的降低,并最终促进光伏应用市场的飞速发展为目标。因此,硅片作为电池生产的基板材料,硅片尺寸大小决定了电池片尺寸,其内在与表面质量,以及每瓦硅片生产的硅料消耗等对电池生产成本的降低具有重要影响。随着太阳能电池片制造技术逐步向大尺寸和减薄化方向发展,硅片尺寸也从最初的103 mm×103 mm、125 mm×125 mm发展到目前主流的156 mm×156 mm方形硅片,更大的210 mm×210 mm硅片已出现 。而硅片厚度从最初的300 μm以上降至目前主流的180~200 μm,更薄的150 μm已可生产,每瓦硅片的硅料消耗从最初的12 g以上降至目前的7 g左右。光伏产业链各个制造环节持续降低成本的需求和压力极大推动了硅片制备工艺在多晶铸锭、单晶硅拉制、多线切割等关键技术和设备的全面进步,并且大量的先进制造技术如类单晶技术、带状硅片制造技术正在积极研发,将对光伏产业制造技术的进一步发展不断提供有力支撑,进而有力促进光伏应用市场的快速发展。