摘 要:机械载荷测试是光伏组件的一个重要测试项目,电池片的机械强度对组件的机械载荷测试有一定程度的影响,所以在做成组件前对不同的电池片做应力分析非常重要,在新产品研发过程中也可作为一项测试项目,以保证后续组件测试的顺利进行。本文根据测试需求而研制出一款四点弯曲检测电池片应力的机台。
关键词:太阳电池应力检测;机械载荷;PLC ;压力传感器
0 引言
光伏组件生产过程中,太阳电池片的机械强度决定了组件的可靠性,而在电池片的生产过程,中原料片的厚度,电池片的烧结、镀膜及印刷等工艺都影响着电池片的机械性能。随着高效电池片和多栅线电池片的发展,市面上专业的电池片弯曲应力测试设备相对较少,然则电池片的应力测试过程会成为电池片生产过程中的一个重要检测指标,同时也可为后续组件的机械载荷测试提供有利的数据支持。
本文设计了一款四点弯曲检测电池片应力的机台,能够实现待检测电池片的弯矩均匀分布,试验结果较为准确,但是压夹的结构设计复杂,工业生产中较少使用。 台在设计上采用新型的铝制镂空拱状球形结构,球的任何一个地方受力,力都可向四周均匀的分散开来,较小的线性接触面,可保证精测精度。
测试过程是将电池片放在有一定距离的两个受力点(也就是四点弯曲夹具的下半部分)上,在受力点的上方有两个点(四点弯曲夹具上半部分)向电池片施加压力,可通过夹具上方的精密压力传感器有效采集电池片在下移过程中的变量值[1]。通过可编辑程控制器(PLC)进行数字运算,组态单元主要是将采集到的数据显示在操作界面上,界面可进行相应的控制操作,并且有压力曲线界面、历史曲线界面和实时的压力参数界面等;从电池片检测后的数据来进行界定和分析,所采集的数据可通过USB端口以报表的形式将数据拷贝出,便于数据分析。
1 太阳电池应力测试系统
所设计的太阳电池应力检测系统主要由供电系统、压力感应系统、压力变送系统、运算控制系统和界面操作系统等组成。结构框图见图1。
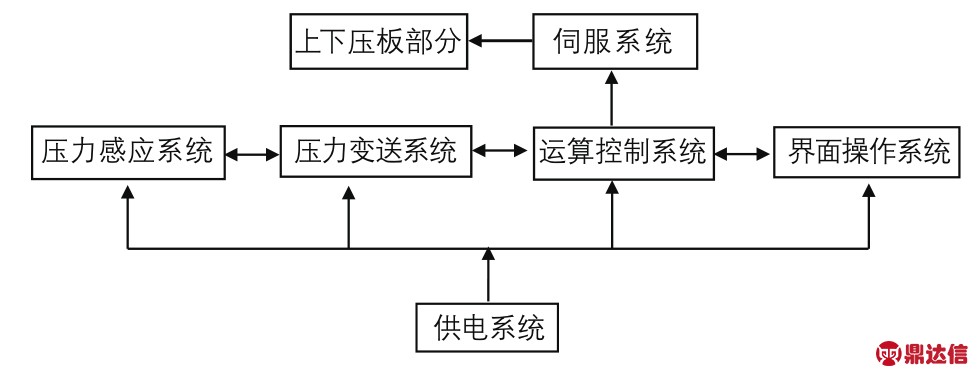
图1 太阳电池应力检测系统框图
供电系统为整个系统提供电源,包括保护装置、变压模块等。控制核心元件主要是压力感应系统,用来检测电池片在受压时的数据。压力变送系统是将压力感应系统的压力信号变成电信号,然后传送到运算控制系统。运算控制系统是整个系统的重要部分,它将压力变送系统发来的电信号通过运算控制系统的A/D模块进行数字转换,再通过界面操作系统进行显示,并且可对设备的运行进行控制。界面操作系统主要包括触摸屏的组态软件,通过和PLC(可编程控制器)进行通讯,相互采集数据,同时也可通过面板按键对控制单元进行控制,操作人员通过操作界面上的按键控制设备的运行,并在界面显示相关报表数据等[2]。
2 压力感应系统结构介绍
压力感应系统是整体设备主要检测元件,主要是感应工作时的压力数据。检测系统包括上压板和上压条、下压板和下压条,以及压力传感器等。压力感应系统结构框图如图2所示。
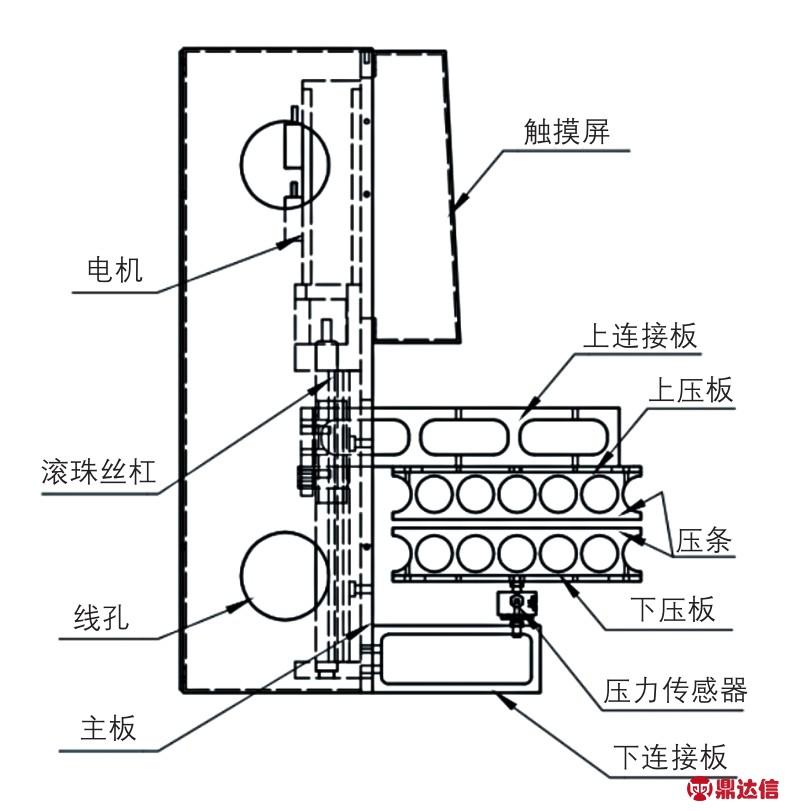
图2 压力感应系统结构框图
上压板部分是通过伺服电机带动上压板和上压条向下位移,下压板部分包括下连接板、压力传感器、下压板和下压条;上压条和下压条之间的间距可根据待检电池片的薄厚进行调节。压力传感器是电池片受到感应压力,传送数据的感应元件。
3 运算控制系统
运算控制系统主要由松下的伺服电机、三菱的PLC单元、镂空拱状承载装置和压力传送装置等组成。如果运算控制系统检测精度不够就会造成检测误差[3,4]。电池片检测步骤如图3所示,其中,图3a是将待测电池片放置到下压条上;图3b是电池片在受到一定压力时的形变过程;图3c是电池片受压达到极限时就会爆裂,在爆裂后检测步骤完成。

图3 电池片检测时的形变过程图
4 控制系统介绍
控制系统是由两种运行模式组成:手动模式和自动模式。手动模式是通过手动控制伺服系统步进式进行位移,可观察不同弯曲时的位移值和压力值;自动模式是采用一键式操作,检测时直至电池片爆裂后数据采集完毕,伺服控制系统自动回原点。电池片应力检测过程如图4所示。
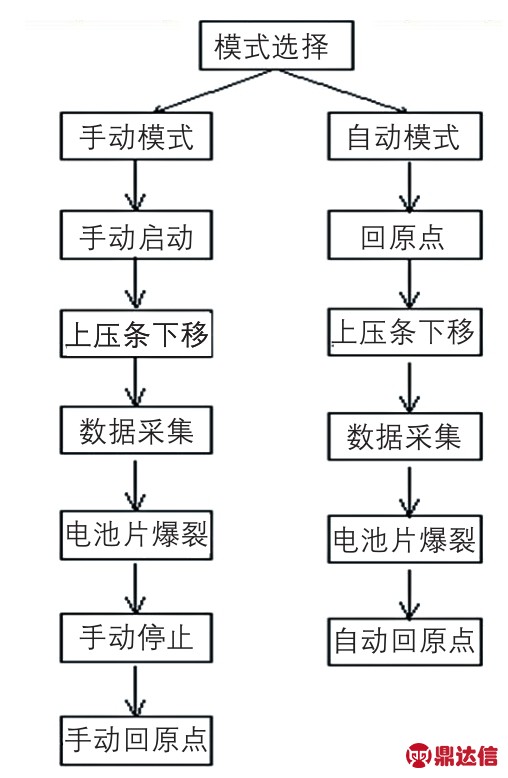
图4 电池片应力检测过程
5 操作系统介绍
在本设计中,使用触摸屏一体机来实现操作和显示,触摸屏界面主要显示工作时的压力数据和曲线,显示太阳电池片的压力值和位移值等;操作按键实现检测系统和传送系统的操作;独立的显示界面将操作界面和曲线界面、报表界面单独显示。
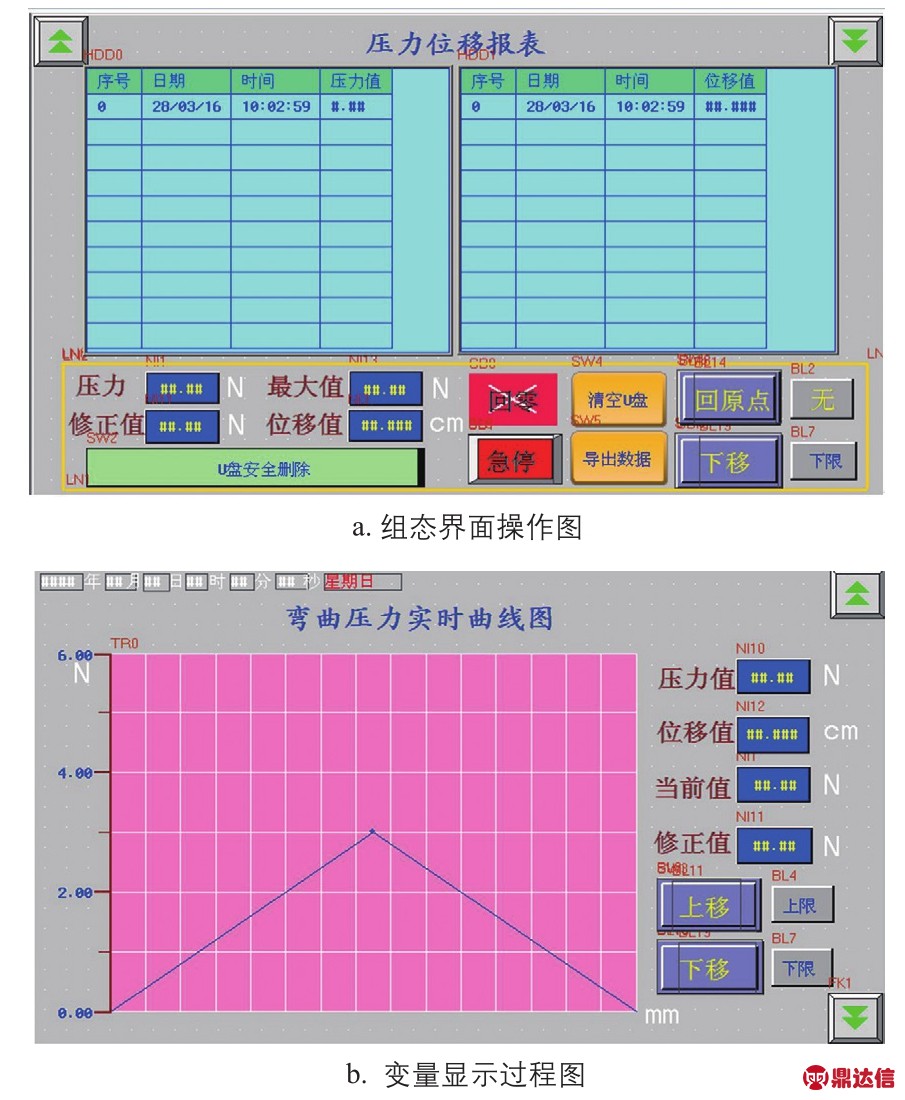
图5 组态界面操作及变量显示过程图
在检测过程中不可或缺的就是触摸屏操作界面,界面上有硬件控制、压力和位移的实时数据信息采集,以及历史数据的保存等功能。在测试过程中,压力传感器会不断的采集数据,所采集的数据通过程序进行运算,运算结果以报表的形式导出,导出的数据可以分析不同压力电池片的应力,实现数据导出[5,6]。实时曲线显示功能可显示在数据采集时的数据曲线,整体设备占用空间小,单人可实现机台操作,主要元件的检测精度小于0.001,设备故障率低;数据采集主要以Excel报表格式输出,方便操作人员采集数据,分析性能。组态界面操作及变量显示过程如图5所示[1,2]。
6 结论
本文是根据电池片的检测需求而设计的一款可检测电池应力的设备,机械结构设计采用新型的铝制镂空拱状球形结构,并采用高精度的压力感应系统、精确的检测单元和传送系统,以及触摸屏显示单元;可检测任何栅线的电池片和较厚的原料电池片,实现整个系统综合设计功能。此设备主要检测电池片在受机械载荷时的形变及在形变过程中所受应力的大小,设计的压条间距可根据检测电池片的薄厚进行调节且对电池的大小和栅线不做限制;通过PLC作为数字运算的关键部分,伺服电机作为传送的控制单元,使太阳电池片的检测数据更加精确。本文所设计的电池片应力测试机台可以满足电池片应力检测需求,为晶硅光伏组件的机械载荷测试提供有力保障。