摘要:采用甲基苯基聚硅氧烷(PMPS)与聚硅氮烷PNS-3为复合基体,气相法白炭黑和炭纤维为填充材料,制备了有机硅耐烧蚀复合材料,并采用氧乙炔焰烧蚀实验的方法研究了材料的烧蚀性能。在对烧蚀后的材料形貌SEM分析和采用XRD、FT-IR、EDS等方法进行了成分分析的基础上,发现加入聚硅氮烷后,苯基硅橡胶的烧蚀行为发生了变化,提出了氧化层、成炭层、陶瓷层、裂解层和基体五区域的新烧蚀模型,并对烧蚀机理进行了初步探讨。研究表明,绝热层在烧蚀过程中,氧化层主要组分是SiO2,起到隔绝氧化性气氛渗入的作用;氧化层下是新生成的耐高温、耐氧化的SiC陶瓷;成炭层坚硬致密起到了热防护的作用。
关键词:甲基苯基聚硅氧烷;耐烧蚀材料;氧化层; 陶瓷层;成炭层
0 引言
近几十年来,随着火箭和宇航技术的发展和进步,构造简单、质量轻、推重比大的冲压发动机得到大力的发展和应用。固冲发动机一般采用固体火箭助推器与冲压发动机共用一个燃烧室的方案,发动机工作时,当助推器中的固体推进剂不完全燃烧后,补燃室内表面完全暴露在主发动机所产生的高温高速燃气之中,且由于空气的进入,补燃室内处于一种富氧的状态下,燃气组分、空气中的氧、绝热层材料之间会发生比较剧烈的化学反应。这样,固冲补燃室绝热层比普通燃烧室绝热层所面临的工作环境要恶劣得多,烧蚀也更为严重[1-2]。因此,富氧条件下的热防护是固体冲压发动机研制的关键技术之一。
传统的绝热层主要是三元乙丙橡胶和丁腈橡胶等,C/C复合材料具有密度低、高温力学性能优异、热膨胀系数低、耐热冲击等优点,一度被认为是最理想的在超高温条件下应用的隔热材料之一。然而,在富氧、高温、高冲刷环境下,碳层和C/C复合材料都会发生显著氧化和烧蚀,剥蚀程度大,难以形成牢固而致密的碳层,失去隔热功能,不能满足新一代高性能航空航天器发展的需求。以—Si—O—链为主链的硅橡胶具有耐高低温、耐紫外线、耐辐照、耐候、抗烧蚀及电绝缘、防潮等优点,广泛用于航空航天、电子电气、纺织、建筑等领域。另外,硅橡胶氧化后的产物是二氧化硅,从而成为富氧条件下绝热层的首选材料[3-4]。1963年,Whipple就已对硅橡胶耐烧蚀材料在不同的热流下性能进行了实验评价,验证了有机硅橡胶在451~2 926 kJ/(m2s)热流下具有良好的耐烧蚀性能[5]。1971年,美国DOW Coring公司成功研发出了具有优异耐烧蚀性能的复合材料DC93-104[6]。1991年,该公司制得的以聚二甲基硅氧烷与聚甲基苯基硅氧烷为基体的复合材料,用于保护航天器发动机,效果良好[7]。台湾“天弓I型”导弹也采用的是以液体苯基硅橡胶为主体的有机硅绝热层,显示出优异的热防护性能。苯基硅橡胶复合材料作为冲压发动机绝热层,为有氧烧蚀绝热提供了新的思路。
利用陶瓷先驱体浸渍裂解技术( PIP)制备耐高温复合材料,也是实现富氧条件下的热防护功能的一条途径,该材料具有抗高温氧化、聚合物分子可设计合成工艺简单等优点。含硅聚合物瓷先驱体,如硅化碳陶瓷前驱体聚碳硅烷、SiOC陶瓷前驱体聚硅氧烷、Si3N4—SiC复合陶瓷前驱体聚硅氮烷以及聚硼硅氮烷等含杂原子聚合物成为制备新型耐烧蚀材料的发展方向。Xu Tian-heng等[8]利用PIP方法,以硅树脂为前驱体制备了三维炭纤维增强的SiOC陶瓷基复合材料。Xu Cai-hong等[9]制备利用硅氮陶瓷先驱体全氢聚硅氮烷(PHPS)用于聚酰亚胺基体上,通过裂解氧化得到的SiO2,可有效保护基体面上原子氧的腐蚀;张宗波采用聚合物前驱体热解方法,制备了良好抗氧化性的SiBCN陶瓷。利用PCS制备的C/SiC复合材料在氧乙炔火焰下表现出优异的耐烧蚀性能[10-12]。 然而,上述陶瓷虽然具有良好的耐烧蚀性能和机械强度;但其前驱体不能直接使用,必须在严格的条件下裂解成陶后,才能转化为耐烧蚀陶瓷层,制备得到的陶瓷绝热层脆性大,几乎没有延伸率,易在振动条件下开裂,这极大地限制了这类材料的应用范围。
鉴于苯基硅橡胶的优异性能和陶瓷前驱体成陶后的耐烧蚀功能,本文以苯基硅橡胶/SiOC陶瓷先驱体为基体,以白炭黑,炭纤维等作为填充材料的一种新型耐烧蚀绝热层,并研究了其在氧乙炔火焰下的烧蚀行为,对烧蚀机理进行了初步探讨,提出了一个5层烧蚀模型。
1 实验
1.1 原料
甲基苯基硅氧烷(PMPS,平均相对分子质量为80万,苯基的摩尔含量为30%):自制;气相法白炭黑,美国卡博特公司TS-530;炭纤维:T800型炭纤维,日本东丽公司生产;将连续的炭纤维短切成长度为3 mm的短纤维,丝径为8 μm,并以无水乙醇为介质进行超声波分散,聚硅氮烷(PNS-3),中国科学研究院化学所提供;硫化剂,2,5-二甲基-2,5-双(叔丁基过氧基)己烷。
1.2 试样制备
按照表1配方制备硅橡胶复合材料,制备分为橡胶混炼和硫化。
表1 硅橡胶复合材料配方
Table1 Formula of the silicone rubber ablative composite

注:1)每100 g橡胶中的含量(份数)。
将生胶放入开炼机中进行混炼,破胶后,将辊距调至2 mm,生胶包辊后,加入白炭黑;然后,把辊距调大到5 mm,加入炭纤维,混匀后停放12 h。将混炼胶放入开炼机上,加入PNS-3;混匀后,加入硫化剂双二五,混炼均匀,出片。采用平板硫化机硫化,硫化温度为170 ℃,硫化时间由硫化仪测定的正硫化时间确定;之后,在烘箱中二次硫化,条件为200 ℃×4 h。
1.3 性能测试
1.3.1 氧乙炔焰烧蚀
根据GJB—323A96标准,对样品进行氧乙炔焰烧蚀,热流密度为4152.9 kW/m2,火焰喷嘴内径为2 mm,喷嘴垂直于样品表面,且距离样品表面为10 mm,烧蚀20 s。
1.3.2 烧蚀成分表征
采用扫描电子显微镜观察烧蚀层各区域的微观形貌。采用德国BROOK公司TENSOR37型号傅里叶变换红外光谱仪检测烧蚀样品各区域的分子结构的变化中,红外透射光谱波数范围为400~4 000 cm-1,衰减全反射(ATR)光谱扫描范围为600~4 000 cm-1;采用X射线衍射仪对烧蚀后各层晶相的检测,扫描角度范围为20°~90°。
2 结果与讨论
2.1 复合材料形貌的表征
按照国军标GJB—323A96测得材料的线烧蚀率为0.079 mm/s,质量烧蚀率为0.09 g/s,表现出较好的耐烧蚀性能,样品烧蚀后的形貌及剖面如图1所示。根据样品烧蚀后的剖面图1(b),将烧蚀样品平行于烧蚀面打磨,分别观察距离烧蚀火焰不同层次的烧蚀形貌。图2是耐烧蚀材料氧乙炔烧蚀后的烧蚀层不同层面的SEM图片。
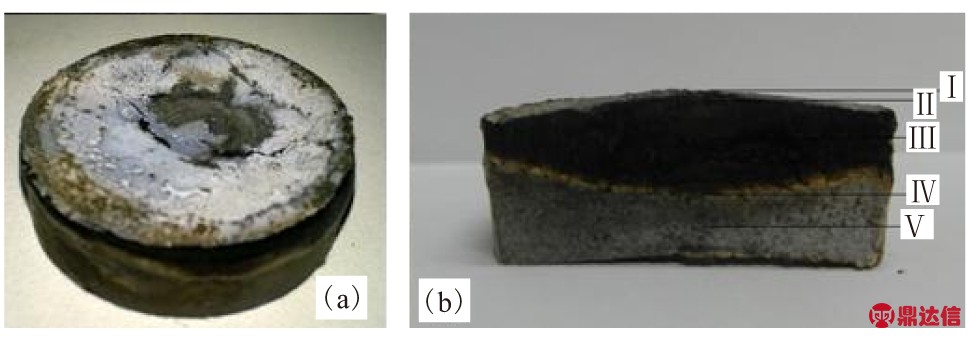
(a)耐烧蚀材料 (b)横截面
图1 氧乙炔火焰烧蚀后的耐烧蚀材料及其横截面
Fig.1 The photo of the ablative composite and the cross section after ablation
图2(a)是烧蚀层表面I的SEM图片,可看到该层非常致密光滑,并且在表面上铺满白色球状颗粒,该颗粒大小均匀,为0.5 μm左右。电子能谱分析表明,该白色颗粒的主要成分是SiO2。
表面层I下方的II层是形状为不同于其它层的粉末颗粒,颗粒松散,粒径大小分布不一,从几十纳米到几微米,且看不到CF存在,见图2(b)。电子能谱分析表明,该颗粒主要是SiC。
Ⅱ下方的Ⅲ的SEM见图2(c)~(f),其化学组成与微观结构不同于传统的耐烧蚀材料。图2(c)是表面俯视图,看到该层分裂成彼此被炭纤维相连的块状结构,块与块结构之间的缝隙大约为50 μm。从图2(d)中看到,不同于I、II两层,该层可观察到纤维状物质,经分析是加入的CFs,其中部分CFs表面光滑,部分覆盖有光滑颗粒状物质,该物质被证实为SiOC陶瓷。图2(e)是主视图,从中看到呈柱状结构分布,形成簇,簇中分布着炭纤维,炭纤维的直径约为8 μm,贯穿于各簇内部和各簇之间,对该层起到连接增强作用。另外,电镜照片可清晰地看到烧蚀后,炭纤维表面包裹着一层陶瓷状物质,见图2(g)~(h)。在图2(g)上,可更直观地观察到炭纤维表面上包覆着陶瓷。在本层出现碳纤维的原因是由于在靠近表层(I、II)的CFs被高温氧化冲刷,成为CO2而消失,而沿着表面层至内部,一方面温度逐渐降低,与高温氧化气流接触少,同时基体树脂在高温条件下形成了SiOC陶瓷层,从而保护CFs。图2(h)为III层以及炭纤维表面新生成的SiOC陶瓷微观形貌。
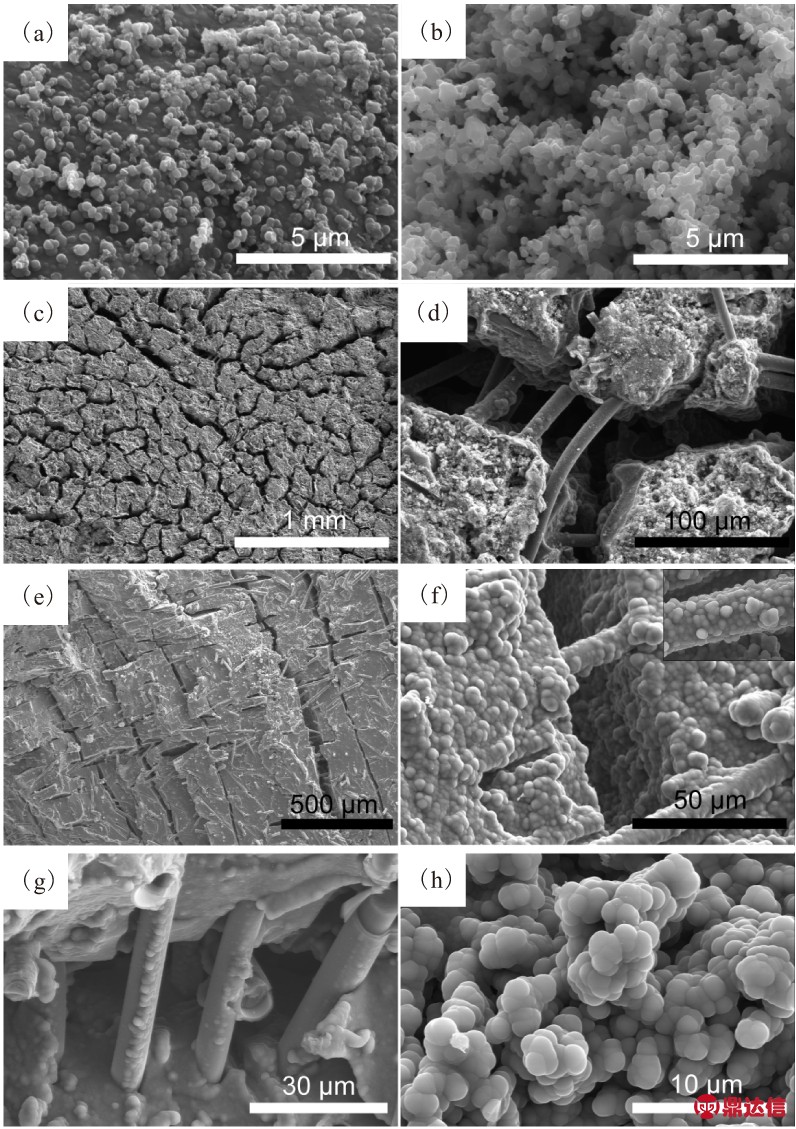
图2 氧乙炔焰烧蚀后的表面Ⅰ(a)、Ⅱ(b)Ⅲ(c~f)和 炭纤维表面(g~h)
Fig.2 SEM photos of silica layer(a), ceramic layer(b), carbon layer(c~f)and carbon fiber(g~h)
Ⅲ层与基体层之间的第Ⅳ个剖面结构见图3(a),从图中看到,该区域的孔隙很大,缝隙宽度大概100 μm,也没有Ⅲ 那么规整,是整个材料最脆弱的部分,在烧蚀过程中最易脱离基体,极大地影响着烧蚀材料的整体性能。该部分是基体部分刚刚开始发生裂解,生成大量的裂解气体,但是温度又不高,不能碳化或成陶,体积膨胀最严重,从而容易断裂。
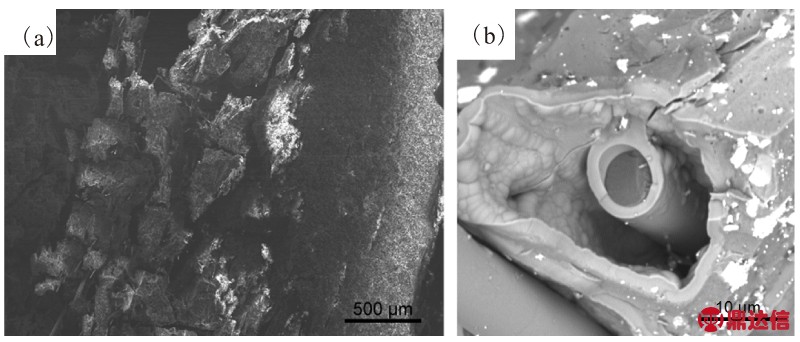
(a)裂解层 (b)炭纤维
图3 氧乙炔焰烧蚀后的裂解层与炭纤维
Fig.3 SEM photos of pyrolysis layer and CFs
2.2 烧蚀层组成研究
为了进一步研究在烧蚀的不同部位形成不同形貌的原因,采用EDS对各层的元素分布进行了研究,结果见图4。从中能够看到Si、O、C、N 4种元素在每层分布变化的情况,在表2中也标出了各个烧蚀层的可能的化学组成。表面层(I)的元素组成为SiO2.1C2.8,由此可推测出表面多为SiO2颗粒和生成的碳;II的元素组成为SiO0.07C2.3,氧元素几乎未被检测到,可看成是SiC和多余的碳组成。Ⅲ的元素组成为SiO1.8C6.2,Si、O 元素在此层分布很少,组分大部分由裂解生成的碳组成;Ⅳ的元素组成为SiO1.7C1.85N0.5,N元素的存在可说明聚硅氮烷在此层所在位置的温度条件下,还未完全裂解。
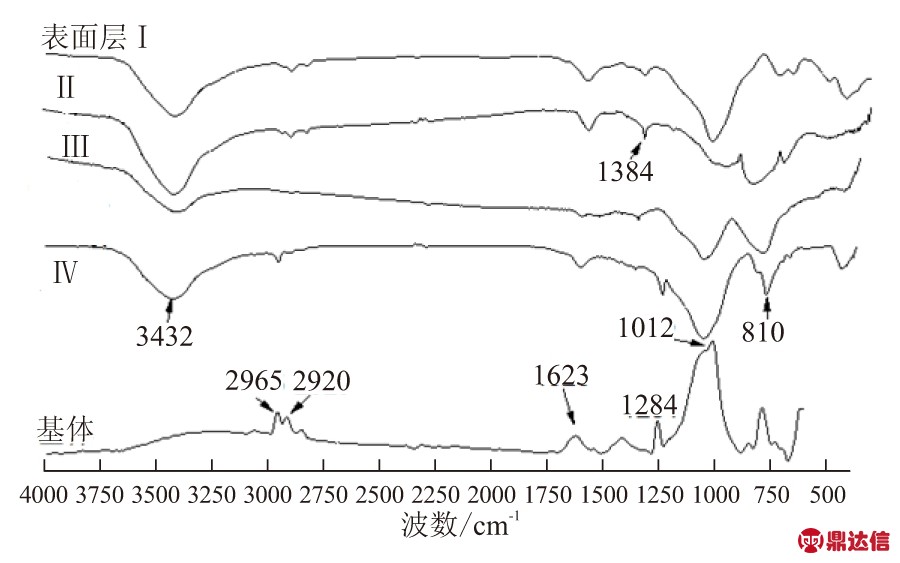
图4 各烧蚀层区域的元素分布结果
Fig.4 The EDS patterns of all sections
表2 各烧蚀区域的元素组成与可能的化学组分
Table 2 The EDS patterns of all sections and possible ingredients
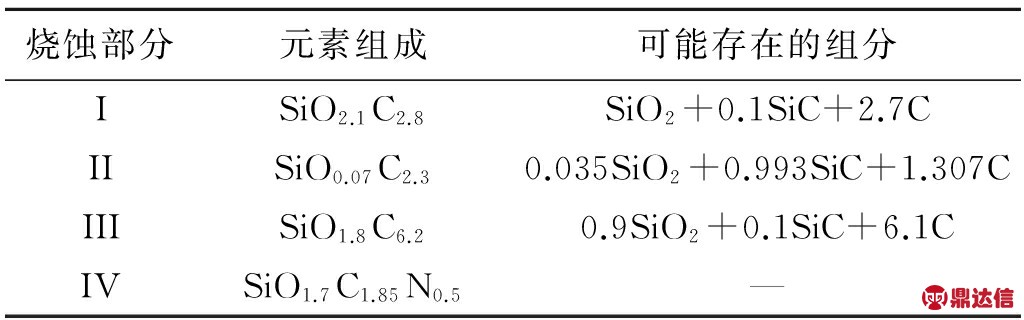
图5中的红外图谱是烧蚀后材料从表层到基体的红外光谱。2 965 cm-1和2 920 cm-1处为C—H伸缩振动吸收峰,1 284 cm-1处表示Si—CH3的面内摆动吸收峰,Si—O—Si伸缩振动吸收峰在1 000~1 100 cm-1范围内出现,—OH伸缩振动吸收峰在3 432 cm-1。Si—C伸缩振动吸收峰在690~890 cm-1。有机基团(—CH3/—CH2—)从基体到表面逐渐变弱直至基本消失;而在表面层红外图谱中主要是Si—O—Si(1 012 cm-1附近)和SiO2表面的—OH(3 432 cm-1)吸收峰,表明表面层的主要成分为SiO2,这与能谱分析的结果相一致;Ⅱ的红外图中主要是Si—C(810 cm-1附近)和羟基(—OH)的吸收峰;在Ⅲ中,Si—O—Si、Si—C的特征峰都存在。在Ⅳ的红外图谱中2 920 ~2 965 cm-1区间,1 284、1 623、1 012 cm-1都有红外吸收峰出现,与基体红外很相近,此区域开始发生裂解,并没有完全由有机转化为无机状态。从红外图谱可看出,各层的红外吸收与能谱分析结果基本一致。
X-RD是研究陶瓷结构及成分的一个有效手段,图6(a)、(b)分别是Ⅱ和Ⅲ的XRD图谱,图6(a)图谱中2θ为35.5°、60.5°和72.5°对应衍射峰分别为β-SiC晶体中(111)、(220)和(311)晶面的衍射峰。采用谢乐方程[13]可计算出SiC晶粒尺寸。
Size=Kλ/(FWcosθ)
式中 Size为晶块尺寸(nm);K为常数,一般取K=1;λ是X射线的波长(nm);FW(S)为试样宽化(Rad);θ则是衍射角(Rad),根据XRD中2θ为35.5°的衍射峰,可求出SiC晶粒的尺寸为30 nm。
2θ为26.3°处为石墨化的碳的衍射峰,表明Ⅱ的组分中有新生成的SiC和石墨化的碳。另外,XRD中2θ为10°和35°有光环晕,这通常为无定形的Si—O—C,表明Ⅲ中及CFs表面为SiOC陶瓷[14-15]。
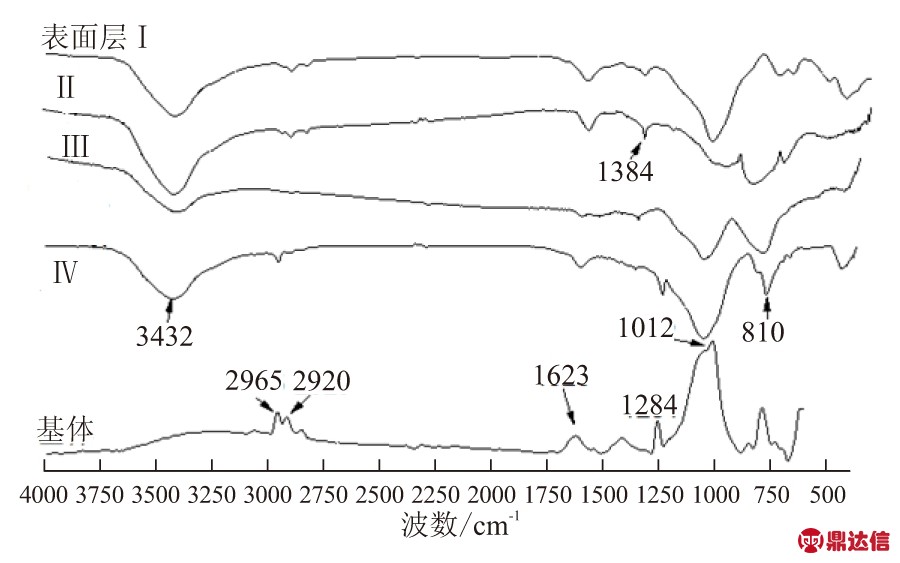
图5 各烧蚀层的红外光谱图
Fig.5 FTIR spectrum of all sections
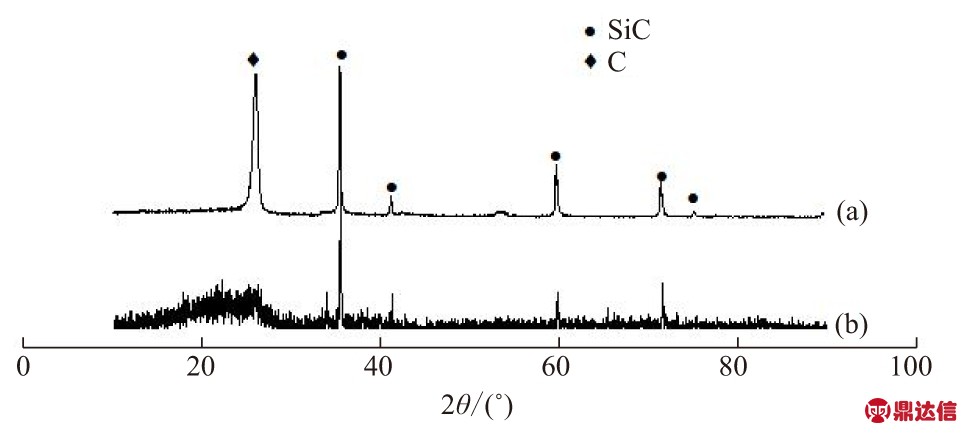
图6 Ⅱ(a)和Ⅲ(b)的XRD图谱
Fig.6 XRD patterns of (b)carbon layer and (a)ceramic layer
2.3 烧蚀模型的建立
绝热层材料烧蚀模型的建立已得到较多的研究。目前,文献报道的烧蚀模型有:二层模型、三层模型、四层模型等[16-17],如Dong Yong等[18]提出,材料在烧蚀后可分为原始层、裂解层、陶瓷层和硅氧层。该模型很合理地解释了材料的烧蚀机理,但忽略了烧蚀过程中C元素的变化及成碳层对烧蚀试样的关键作用。
本文通过分层剥离方式,在仔细研究距离烧蚀面不同距离烧蚀样品的形貌和成分的基础上,发现聚硅氮烷和苯基硅橡胶复合材料的烧蚀行为与其他材料有所不同,烧蚀后材料可其分成5层(图7),从接触火焰表面到未被烧蚀区域分别为第I层是高温氧化层,氧乙炔火焰直接喷吹该区域,耐烧蚀材料发生高温氧化作用,产生一层薄的白色氧化层,远离火焰中心的区域氧化层较为坚硬,主要是熔融SiO2—SiC;第II层是陶瓷转变层,在氧化层下方区域出现松软的、颗粒状绿色区域,主要是高温下形成的SiC陶瓷;第III层是成炭层,由较为致密坚硬的黑色柱状碳层,烧蚀层的主要部分,厚度大概为4 mm(整体厚为10 mm),柱层之间由于气体流走留下缝隙而相互分离,由CF相连;第IV层是裂解过渡层,在该层有机基体开始高温裂解,有机相向无机相转变过渡态;第V层是原始基体,没有发生明显的烧蚀物理变化和烧蚀化学变化。在烧蚀过程中,随着烧蚀时间的延长各层逐步向下推移,一旦形成稳定的抗烧蚀陶瓷层,烧蚀作用将明显减弱。
2.4 烧蚀机理探讨
从烧蚀模型可看出,绝热层在氧乙炔焰烧蚀过程中,形成了界面和成分清晰的5层结构。这是由于在烧蚀过程中,从烧蚀面开始沿着垂直于解热层方向形成了温度梯度,绝热层不同部位的温度不同,发生了不同的复杂的化学反应,形成了不同的结构。
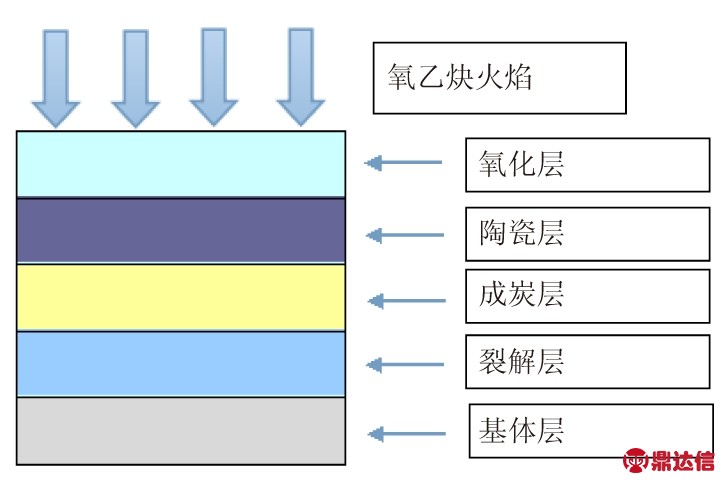
图7 氧乙炔火焰烧蚀模型
Fig.7 The schematic plot of the ablative composite after ablation
烧蚀时,热量和温度的传递需要一定的时间,远离烧蚀面的材料,温度低,不会发生明显的物理化学变化,还保持良好的弹性,这就是基体层;向着烧蚀面方向,材料的区域温度不断升高,当达到有苯基硅橡胶热裂分解温度时,将产生大量气体,该层是裂解层。在该层主要发生2类反应:一类是苯基硅橡胶主链解扣式降解[19],产生环硅氧烷等小分子,这类分子蒸汽压低,该反应一般发生在500 ℃以下,解聚的温度越高,耐热性越好,对保持绝热层性能越好,该阶段发生的反应如式I所示。
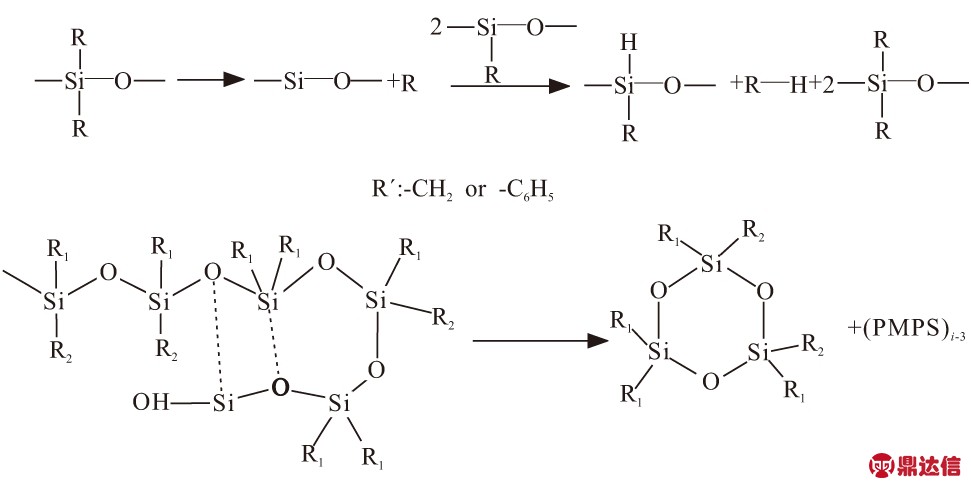
反应式I甲基苯基聚硅氧烷的裂解
随着温度的继续升高,另一类反应开始发生,主要是绝热层有机基团的断裂、碳化,生成大量的小分子气体而溢出,如H2、H2O、CO2、CO和CH4等烷烃及氮的氧化物(见反应式II),这是在裂解层形成大量空隙的主要原因。

R:—CH2 or—C6H5
反应式II 硅橡胶分子侧链的断裂及氧化
在此阶段,苯基硅橡胶及聚硅氮烷开始向无机转变,形成SiO2、无定型碳等,该反应的温度一般在500~800 ℃。与二甲基硅橡胶相比,苯基硅橡胶中苯基的存在,不仅提高了基体的热稳定性,更重要的是提高的残碳量,对形成簇状碳层至关重要。另外,在此阶段聚硅氮烷虽然开始分解,但陶瓷转化还未开始,但对苯基硅橡胶表现出良好的稳定作用,图8(b)是苯基硅橡胶与聚硅氮烷复合材料与纯苯基硅橡胶的热重分析对比图。由图8可知,复合材料的起始裂解温度为500 ℃,800 ℃时的残重为82 %,比纯苯基硅橡胶(图8(a))的起始裂解温度提高了75℃,较苯基硅橡胶32%的残重也大大提高。
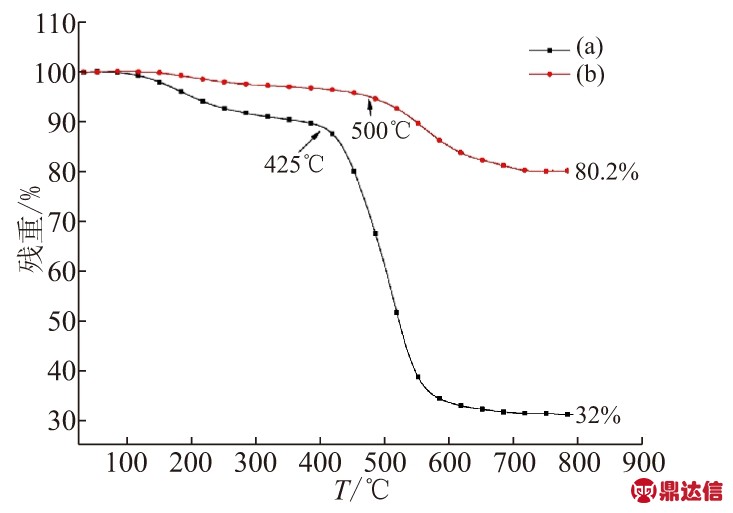
图8 聚硅氧烷(a)和复合材料(b)N2气氛下热失重曲线
Fig.8 TG curves of (a)PMPS and (b)the ablative composite
如前所述,在此层中,有机组分的裂解产生了大量的气体,导致材料内部致密度降低,并在层间形成大量孔隙,强度也有所下降,但由于在热解初期[20],材料整体的孔隙率和渗透率都较低,热解气体的溢出率小于产生速率,容易在层间产生较大的压力,导致材料膨胀,甚至是层间脱落,这是绝热层最薄弱环节。为了验证此层结构,考察了氧乙炔火焰下烧蚀5 s后烧蚀样品的结构(图9)。从图9可看出,此时材料内部有很多孔洞,但由于烧蚀层较薄,气体可冲破表层溢出,并在表面形成孔洞,导致表层疏松。这进一步证实了裂解层形成的原因。
随着温度进一步升高,裂解层小分子逐步消失,在高温无氧的条件下逐步碳化,生成炭层,该层并非传统意义上的焦炭层。从元素分析结果得知,炭层主要由Si—O—C 3种元素构成,其中碳主要来自于高苯基含量基体的分解、碳化。与裂解层相比,成炭层结构更加致密,这主要是由于经过裂解,残余物主要是基体分解产生的C、SiO2以及聚硅氮烷初步转化形成的类陶瓷,并有部分覆盖在炭纤维表面,高温条件下碳层进一步致密、收缩,材料的强度、密度都有所提高,但裂解产生的缝隙,进一步变大,见图2(f)。由于炭化层的孔隙率较大,燃气中的氧化性组分可能会渗入炭层,在炭化层与碳发生反应,消耗一定的碳,并随着烧蚀时间的增加,炭化层将会向裂解层推移。

图9 烧蚀初期的材料
Fig.9 The ablative composite after early ablation
从数据可看出一个异常的现象:在陶瓷层II中的主要成分是SiC陶瓷,Si和O的含量很少。结合氧化层的SEM、EDS结果和红外图谱,推测主要是在高温条件下填充材料二氧化硅一部分会随着气流迁移到烧蚀材料表面,沉积或被吹扫离开表面,另一部分则在炭层上部与碳发生碳热还原反应[21],生成碳化硅,形成碳化硅陶瓷层,见反应式III。

反应式III碳热还原反应
与火焰和氧气充分接触的材料表面,氧化生成的或者随气流上升到表面的氧化硅已经由固态变为液态,在中心区不断的生成,不断的被吹扫走,在离烧蚀中心区较远的部位,则冷却形成致密氧化层。值得一提的是炭纤维在不同烧蚀层中的含量和形貌是不同的,在氧化层和陶瓷层中未发现CFs的存在,但在其他3层中都分布有炭纤维,只是在成碳层和裂解层中,炭纤维表面覆盖有陶瓷状物质,如图3(b)烧蚀后裂解层中炭纤维的SEM所示,EDS显示该物质是非晶结构的Si—O—C,而未加入聚硅氮烷陶瓷前驱体的体系中未发现该现象。一般来说,单纯的CFs在有氧条件下400 ℃左右,就会氧化而消失,而在本体系中, CFs表面被Si—O—C陶瓷覆盖,一方面减小了成碳层、裂解层中炭纤维的氧化损失,提高了炭纤维的补强效果;另一方面,Si—O—C陶瓷在表面高温氧化气流冲刷下,能生成SiO、CO等气体,带走大量的热,对CFs起到了保护作用,延长了炭纤维在烧蚀过程中的补强作用,减少烧蚀。
3 结束语
(1)与传统的耐烧蚀材料的烧蚀行为显著不同,炭纤维增强甲基苯基聚硅氧烷(PMPS)与聚硅氮烷PNS-3的耐烧蚀复合材料在氧乙炔火焰烧蚀下,形成了由氧化层、陶瓷层、成炭层、裂解层和基体5层结构组成。各层结构与成分明晰,其中氧化层的主要成分是SiO2,陶瓷层的主要成分是纳米SiC。
(2)高温条件下,聚硅氮烷PNS-3作为陶瓷前驱体与聚甲基苯基硅氧烷(PMPS)相互作用,促进了基体树脂的陶瓷转化,形成SiC陶瓷层和在炭纤维表面形成Si—O—C陶瓷层,陶瓷层的形成一方面与氧化层产生协同作用,在提高耐温、耐冲刷的同时,还阻止氧气的渗入保护炭层免受氧化,提高了复合材料的热氧化稳定性与隔热作用;炭纤维表面形成的陶瓷层提高了炭纤维的耐氧化性能,充分发挥了纤维的增强作用。
(3)炭纤维增强甲基苯基聚硅氧烷(PMPS)与聚硅氮烷PNS-3耐烧蚀复合材料和新型烧蚀结构的研究,为新型绝热层的设计提供了新思路。