摘要:传统的粗磨工艺在加工蓝宝石薄片过程中遇到很大挑战,易于产生崩边、隐裂和碎片等问题。双面金刚石研磨、单面金刚石磨削、双面金刚石研磨垫等新工艺可以解决上述这些问题。在蓝宝石精磨工艺中,细粒碳化硼和金刚石颗粒镶嵌的陶瓷研磨盘配合的双面研磨工艺,可以有效地降低粗磨过程中造成的表面损伤;使用细粒金刚石研磨液的单面铜盘工艺亦是一种有效的精磨工艺。本文对二者的优缺点进行了比较。蓝宝石的抛光速率较慢,一般不超过5~10 μm/h。蓝宝石抛光的主流仍是使用二氧化硅抛光液。在二氧化硅抛光液中添加其它细粒磨料或采用氧化铝抛光液等其它方法,仍处于试验阶段。轻压抛光对提高蓝宝石的表面质量非常关键。兆声清洗工艺可以减少蓝宝石表面的微小缺陷,兆声单片清洗工艺尤为有效。
关键词:蓝宝石薄片;金刚石研磨盘;蓝宝石精磨;兆声清洗
1 引 言
蓝宝石(Sapphire)俗称“刚玉”,又称白宝石。它是氧化铝的单晶形态,分子式为Al2O3,晶体结构为六方,晶格常数为a=b=0.4758 nm,c=1.2991 nm。蓝宝石具有良好的光学、热学、介电性能和优良的力学性能,同时具有优良的化学稳定性和热稳定性能以及抗辐射性能,是一种综合性能优良的多功能晶体材料,广泛应用于半导体外延衬底材料包括氮化镓衬底、SOI衬底(SOS),光学窗口以及激光基质材料等[1]。
蓝宝石晶体具有独特的机械加工特性。采用IC晶片加工的精密磨削和抛光技术,能够获得超精密纳米尺寸精度的表面。单面抛光工艺完成的单面抛光蓝宝石晶片(SPS),主要是作为氮化镓外延生长的衬底材料及SOS(硅+蓝宝石)。双面工艺完成的透明蓝宝石晶片(DPS),主要是作为光学的镜头、医学领域、手表(或I-Watch)表面、航天航空领域的视窗、手机方面的应用(包括显示屏、摄像头、摄像头盖、Home键)等。
正因为蓝宝石具有特别稳定的化学性质和很高的硬度,这就增加了蓝宝石材料的加工难度。随着技术的不断进步,对蓝宝石产品的要求越来越高,包括蓝宝石的厚度更薄,表面缺陷的尺寸更小,表面缺陷的数量更少。所以,蓝宝石晶片加工过程面临许多技术挑战,其中包括粗磨、精磨、抛光和清洗等工艺过程。本文将对所有这些问题进行详细的技术分析和讨论,寻求解决之对策。
2 粗磨工艺
2.1 传统的双面研磨工艺
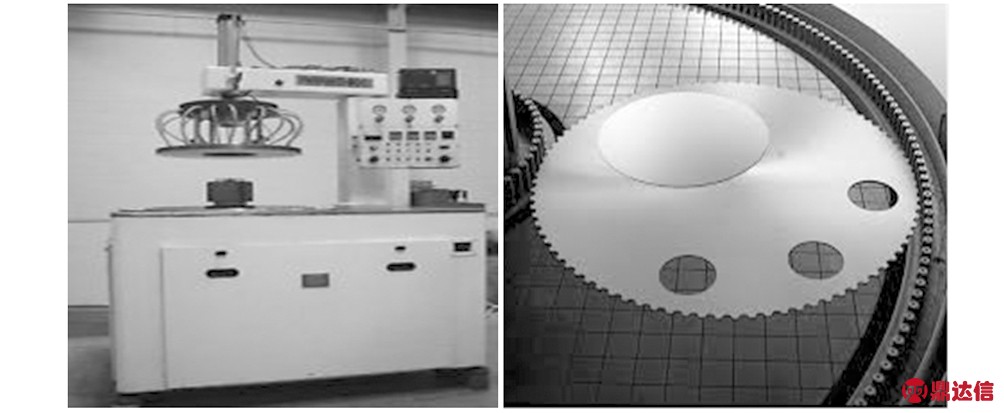
图1 传统双面研磨工艺示意图
Fig.1 Schematic diagram of traditional double side lapping process
因为蓝宝石的硬度大,一般的磨料对蓝宝石没有切削力。碳化硅和碳化硼流动磨料均可用来研磨蓝宝石,但是碳化硅的磨削能力衰减得很快,使用时间太短,故此在工业上碳化硼磨料的应用更为广泛[2]。传统的双面研磨设备如图1所示。
因为蓝宝石衬底片背面粗糙度一般要求在0.8~1.2 μm之间,所以碳化硼颗粒的平均粒度(D50)在60~65 μm之间,其成份及粒度分布如下表1所示。尽管对平均粒径有一定要求,但是颗粒的粒度分布显得更为重要。如果粒度的分布很不均匀,在研磨过程中容易产生晶片崩边、隐裂和碎片等问题。
对于最终产品是双抛片的研磨工艺,可以适当减小碳化硼颗粒的平均粒度。这样,研磨片表面的粗糙度相应变小,损伤层厚度变薄,从而降低精磨和抛光时间。值得注意的是,碳化硼研磨浆料的使用寿命会相应降低。
表1 碳化硼颗粒(240目)的成份和粒度分布特性
Table 1 Composition and size distribution characteristics of 240 mesh B4C grains
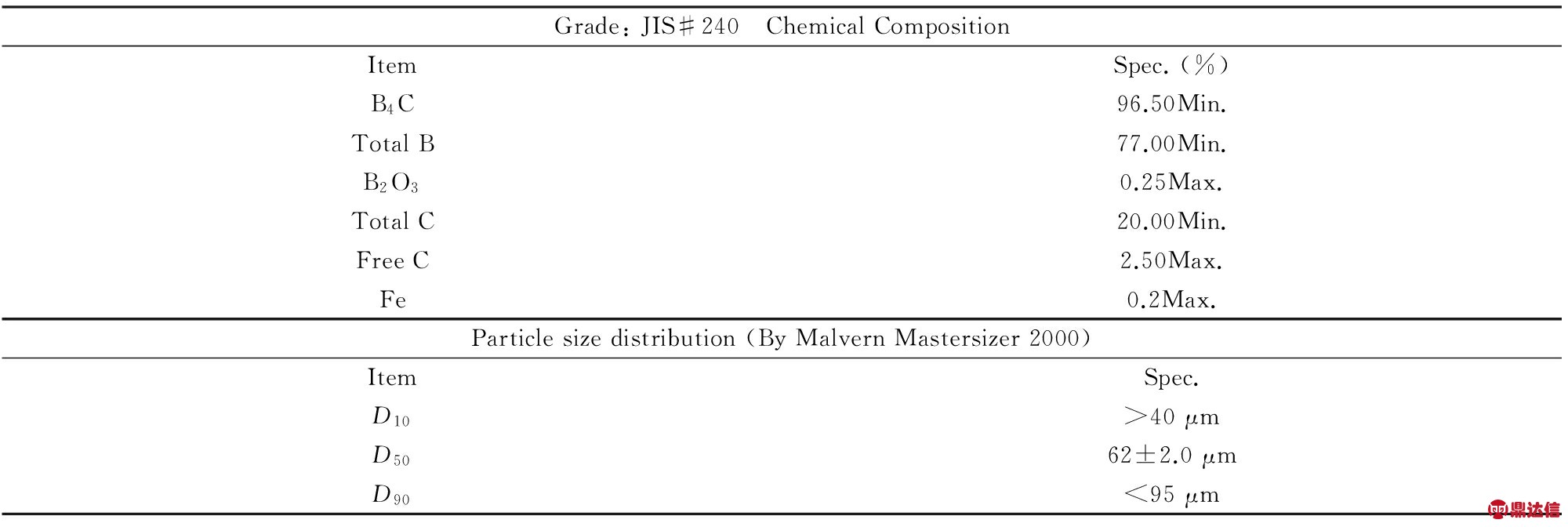
最近几年,蓝宝石在各个领域的应用越来越广泛,人们对超薄片的需求越来越大。例如,对于50 mm的蓝宝石晶片,研磨后的厚度要求在300~350 μm之间。这样的要求导致粗磨碎片率增加,产品的成品率显著下降,研磨工艺面临很大的挑战。采用的一般对策是切割片研磨前退火、采用保护性倒角等方法。
针对双面粗磨过程出现的上述各种问题,下面介绍几种新型的双面粗磨工艺。
2.2 双面金刚石盘研磨新工艺
近年来,双面金刚石盘研磨工艺开始出现。该工艺的特点是:固定研磨颗粒金刚石镶嵌在研磨盘里,整个盘面是由小块金刚石模块拼凑而成,如图2所示[3]。研磨过程只需通冷却水,不需要研磨浆料。该工艺的最大特点是:磨削去除量大,对研磨薄片特别有利;可减少在浆料研磨过程中因粗颗粒引起的晶片隐裂、崩边及碎片等问题;工艺过程环保,易于操作。但对设备的要求相对较高,需要具有一定的转速和压力。
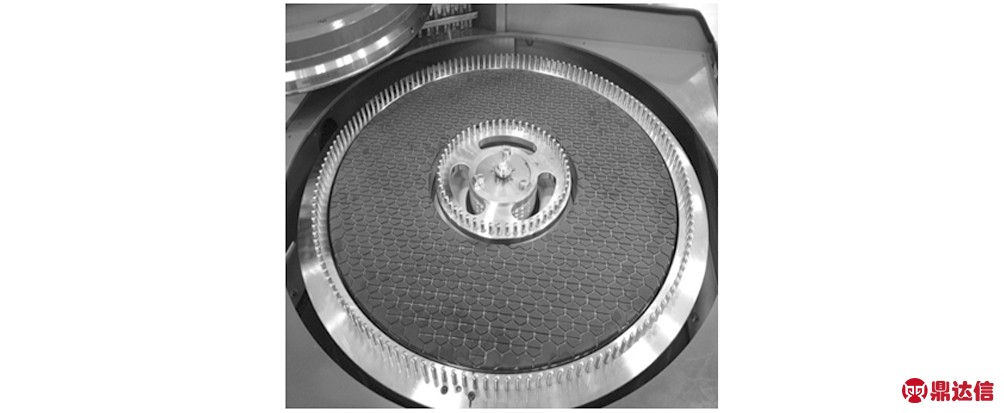
图2 双面金刚石研磨盘示意图
Fig 2 Schematic diagram of double side diamond lapping platen
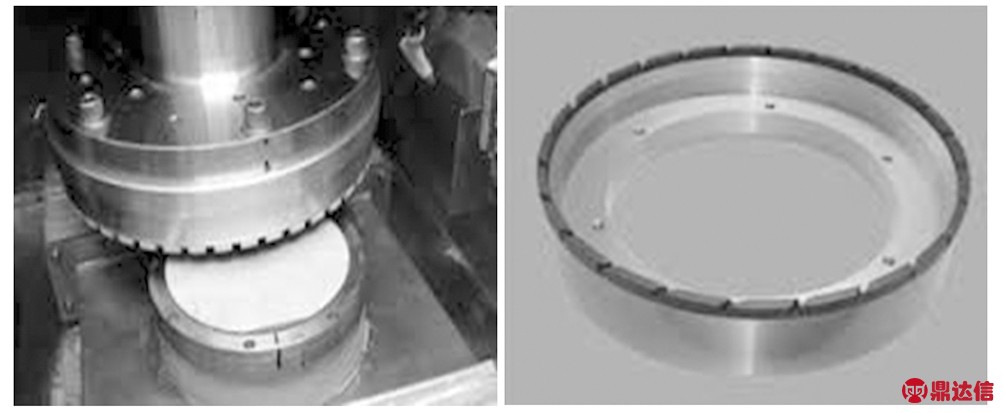
图3 单面金刚石研磨砂轮(grinder)示意图
Fig 3 Schematic diagram of single side diamond grinder wheel
2.3 单面金刚石砂轮磨削工艺
单面金刚石砂轮减薄工艺,目前主要用于大规模集成电路硅材料的减薄及LED蓝宝石芯片的减薄。该工艺和非固定磨料的研磨工艺相比较的结果列于表2。对于研磨厚度在300 μm以下的蓝宝石片子,其机械强度低,易于破碎,因此该工艺具有独特优势。主要原因是:蓝宝石晶片通过液体蜡或固体蜡固定在陶瓷载片盘上,使用单面金刚石研磨砂轮磨削(图3),片子的侧向基本不受力,大大减少了蓝宝石的碎片率。
表2 固定磨料和非固定磨料工艺比较
Fig.2 Lapping process comparison using fixed and loose abrasive
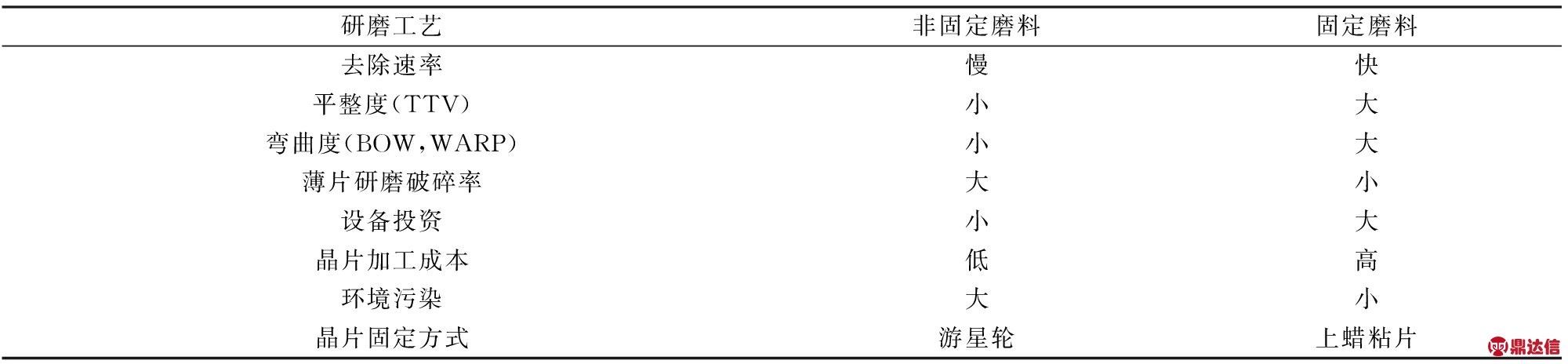
一种改进型的金刚石砂轮磨削工艺,文献亦有报道[4]。金刚石砂轮独立自转,蓝宝石片工件不但能够自转,还可以来回摆动。因此,蓝宝石的表面质量和加工效率有着显著的提高。
2.4 双面金刚石研磨垫新工艺
美国的3M公司研制的TDT金刚石研磨垫(2 mm×2 mm的小方格),可用于蓝宝石的研磨。该工艺和传统的研磨工艺相比,金刚石研磨颗粒已经固定在研磨垫以内,不需要外加研磨颗粒。针对6英寸的蓝宝石晶片,使用80 μm的TDT金刚石研磨垫和60 μm的碳化硅研磨进行对比研究,结果表明:经过TDT研磨过的蓝宝石研磨片的表面应力低,且粗糙度(Ra)在0.6~0.65 μm;经过碳化硅磨料研磨后的蓝宝石Ra在0.8~0.9 μm[5]。
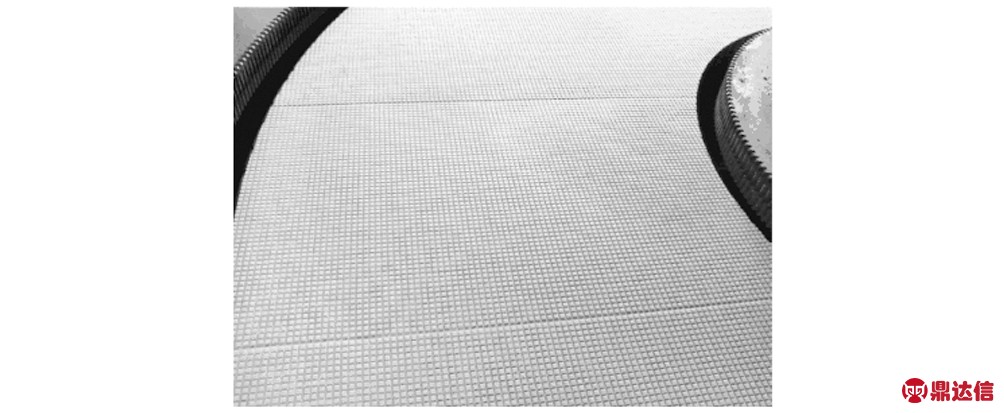
图4 TDT研磨垫在SpeedFam 16B抛光机上示意图
Fig 4 Schematic diagram of lapping pad on SpeedFam 16B polisher
韩国汉阳大学的Hyuk-Min Kim 和Jin-Goo Park等[6],使用美国3 M的Trizact 677 XA金刚石研磨垫对直径为101.6 mm的C向蓝宝石晶片进行了研究,结论如下:
(1)如果只用纯水来研磨蓝宝石,速率很低;
(2)三甲基胺作为分散剂来分散氧化铝颗粒,用氧化铝浆料在IC1010的抛光垫上研磨蓝宝石,速率亦很低;
(3)三种不同的金刚石研磨垫分别使用3 μm、6 μm、9 μm的金刚石颗粒,蓝宝石晶片的研磨速率随金刚石颗粒粒径的增大而增加;
(4)蓝宝石研磨速率随压力、转速、Al2O3浓度与分散剂的浓度比的增大而增加;
(5)氧化铝颗粒用来调整和暴露研磨垫中的金刚石颗粒,对控制研磨速率起着关键作用,蓝宝石的研磨速率可达1 μm/min。
南京航天大学的朱永伟教授等[7,8]对金刚石研磨垫在蓝宝石加工中的应用进行了深入的研究,结论如下:
(1)粗研蓝宝石晶片时,采用固结磨料(W50)加工后的工件表面粗糙度(Ra<0.2 μm)明显优于相同粒径游离磨料(Ra 约为0.2 μm);与经W 14 加工后的蓝宝石粗糙度接近。
(2)差动腐蚀法的数据表明: W 50 和W 14 游离磨料研磨后蓝宝石工件的亚表面损伤层深度分别为49 μm 和7 μm,而含相同粒径的固结磨料研磨后的工件亚表面损伤层深度则分别为6 μm和3 μm。
(3)使用W 14镀镍金刚石固结磨料研磨蓝宝石晶片,研磨液仅为去离子水时,材料去除率(MRR)为150 nm / min,表面粗糙度(Ra)为76 nm;研磨液中加入2%的乙二醇后,相应的MRR为224 nm / min,Ra为51 nm。
3 精磨工艺
3.1 细粒碳化硼的双面研磨工艺
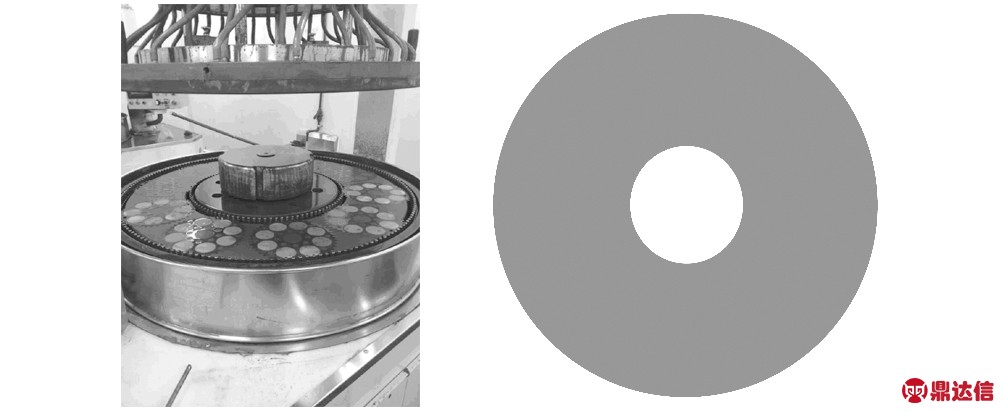
图5 双面精磨设备及金刚石研磨盘
Fig 5 Double side fine lapping tool with diamond embedded lapping platen
研磨工艺通常采用铸铁盘,如图1所示。但是,当采用细的碳化硼研磨颗粒,如W 10,W 7,W 5,W 3.5等,铸铁盘材料容易造成蓝宝石表面的划伤,尤其是铸铁盘开槽处、内圈、外圈。最近几年发展起来的一种新型金刚石研磨盘,参见图5。该盘是通过将金刚石颗粒分散在氧化铝陶瓷颗粒中,配合细粒碳化硼颗粒W7(粒度分布,参见表3),进行烧结,制作而成的盘。该工艺非常有效地去除粗磨工艺造成的较深坑点,降低蓝宝石表面粗糙度。蓝宝石表面稍有透明,并伴有很浅的划伤。研磨去除率可达0.2~0.5 μm/min。
表3 碳化硼颗粒(W7)的成份和粒度分布特性
Table 3 Composition and size distribution characteristics of W7 B4C grains
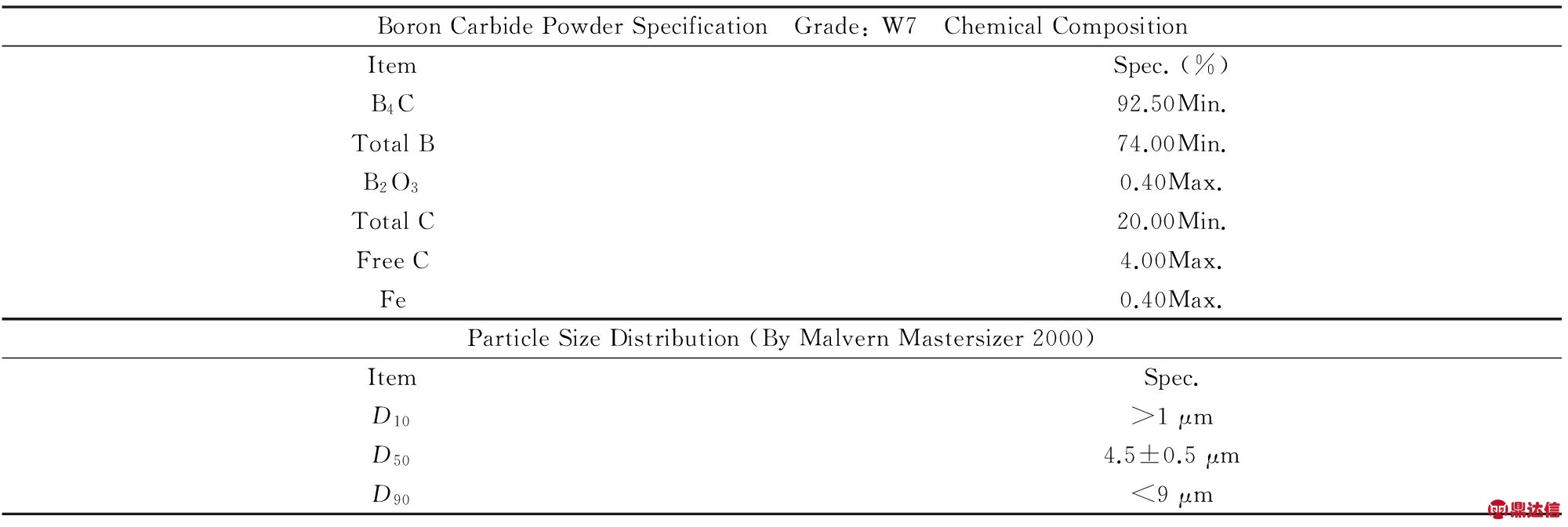
3.2 细粒金刚石颗粒的单面铜盘工艺
树脂铜盘是由铜粉、树脂、固化剂等在高温条件下压铸而成的,对盘面要求是:硬度合适、无气孔、耐磨性好、性能稳定。
蓝宝石晶片用蜡粘附在陶瓷盘上,进行单面研磨。研磨速率一般控制在1.0 μm/min左右。
用于蓝宝石研磨的金刚石是多晶颗粒,又称聚晶金刚石,或多晶钻石。与单晶金刚石相比,聚晶金刚石有更多的晶棱和磨削面,每条晶棱都具有切削能力,因此对蓝宝石的研磨有很高的去除率。聚晶金刚石具有自锐性和韧性,在研磨过程中,粗颗粒会破碎成更小的颗粒,可避免对工件表面造成划伤,而新的裂面具有更多锋利的切削棱,既保证了工件表面质量,又提高了研磨切削效率,在蓝宝石材料加工过程中显示出它独特的优越性。铜抛精磨原理及树脂铜盘,如图6所示。在工业应用中,一般选用3 μm或6 μm的金刚石研磨液,参见图7。
铜盘精磨工艺比较有效地去除粗磨工艺带来的较深的亚微米损伤,在蓝宝石LED衬底片加工工艺中起着不可替代的作用。在透明的蓝宝石光学产品应用中,可以采用铜盘金刚石研磨工艺,但是和双面精磨工艺相比,没有很强的优势。这两种工艺的详细比较结果参见表4。值得注意的是,铜盘金刚石研磨工艺对加工超薄的蓝宝石晶片,如260 μm厚度及以下的光学片,有其独特的优势。
表4 铜抛金刚石研磨和碳化硼双面精磨工艺对比
Table 4 Process comparison between diamond single side lapping and BC4double side lapping

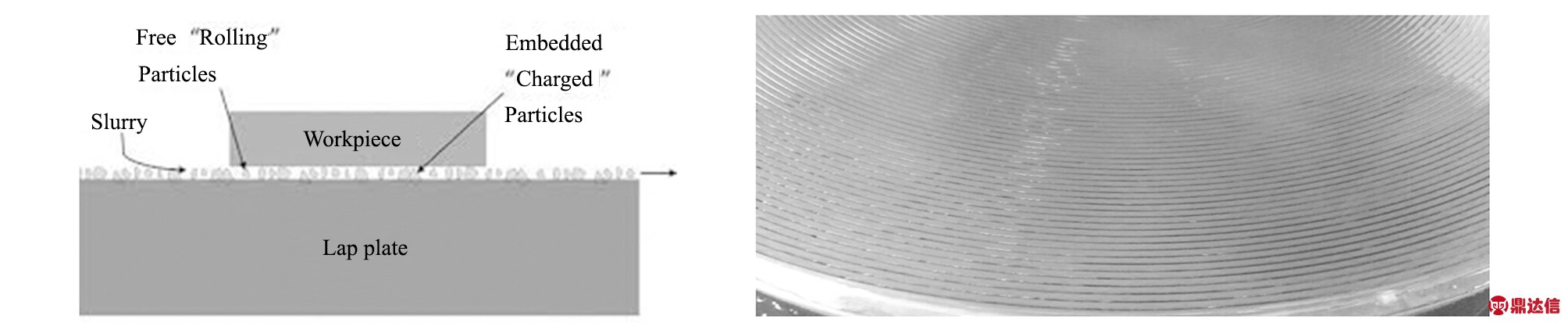
图6 铜盘精磨和树脂铜盘示意图
Fig 6 Schematic diagram of fine lapping with resin-bronze platen

图7 金刚石研磨液的粒径分布图
Fig.7 Size distribution of diamond lapping slurry
3.3 电解在线修整(ELID)金刚石磨削工艺
电解在线修整金刚石磨削工艺是利用电化学反应原理,持续不断地将新鲜的金刚石颗粒表面暴露出来。采用金刚石颗粒较细的砂轮,可以得到表面光滑的蓝宝石:#2000号金刚石砂轮,粗糙度Ra为3.6 nm;#8000号金刚石砂轮,粗糙度Ra为1.6 nm。砂轮的速率为1000 r/min,工件的速率为300 r/min。去除速率根据实际情况调整[9-12]。
3.4 化学机械磨削(CMG)单面加工工艺
大连理工大学康仁科教授领导的团队在蓝宝石化学机械磨削单面加工工艺方面取得了令人瞩目的成就[13]。磨削盘的材料分别由600#的二氧化硅、三氧化二铁、氧化镁通过树脂粘结而成;碳酸氢钠和氧化钙作为添加剂,可以起到调整盘的孔隙率、改善蓝宝石表面活性等作用。
化学机械磨削蓝宝石的特点如下:
(1)磨料的硬度一般比蓝宝石低;
(2)在研磨过程中,磨料与蓝宝石之间有化学反应;
(3)添加剂直接或间接与蓝宝石发生化学反应。
蓝宝石经过磨削后的最佳表面粗糙度在2 nm左右。氧化镁磨削蓝宝石的粗糙度最佳;氧化铁磨削蓝宝石的去除率最佳。
4 抛光工艺
目前,蓝宝石抛光行业主流采用的仍是纳米二氧化硅作为抛光液,最后得到抛光表面的粗糙度(Ra,原子力显微镜测试)均在0.3 nm以下。在抛光过程中,二氧化硅抛光液与蓝宝石表面的反应如下式所示,产物是硅酸铝的二水化合物[14,15]。
Al2O3+2SiO2+2H2O=Al2Si2O7·2H2O
尽管三氧化二铝磨料可以作为蓝宝石抛光液[16-19],但由于现在生产的三氧化二铝磨料一般是通过煅烧、研磨、筛选而得,要想得到均匀一致性好、粒径达到纳米级的三氧化二铝很困难。最致命的是三氧化二铝硬度大,抛光表面划伤严重;粘度大,抛光表面不易清洗干净,很难保证抛光材料的表面平整度[1]。尽管有报道说,三氧化二铝作为抛光液,但目前只是在试验阶段,主要问题在于:(a)对设备的转速要求较高;(b)蓝宝石表面粗糙度相对较大;(c)表面缺陷稍多;(d)成本较高。
美国的Abhaya K. Bakshi等使用粒径为100~400 nm的α或β型碳化硅抛光蓝宝石。他们利用二氧化硅涂层对碳化硅表面进行软化处理,以期减少蓝宝石的表面划伤。原因在于二氧化硅涂层可以钝化或减少碳化硅颗粒的尖角。颗粒的内核仍然是硬度较大的碳化硅,磨料保持着较优的抛光去除速率[20]。他们还使用碳化硅和二氧化硅的复合抛光液(30% SiC,70% SiO2)加工R向的蓝宝石,与不添加碳化硅的二氧化硅抛光液相比,抛光速率可提高30%~50%[21]。
在二氧化硅抛光液中加入催化剂(Fe-Nx/C)可以提高蓝宝石的抛光速率,提高幅度约为15%;该催化剂含有三氧化二铁、四氧化三铁、吡啶型氮、吡咯型氮[22]。
利用超声波的振动能显著提高SiO2硅溶胶抛光蓝宝石过程中的去除速率(约3.8倍),并且粗糙度有所降低。超声波是加在单面抛光机的抛头上的[23,24]。可能解释的原因是[25,26]:
(1)二氧化硅颗粒在蓝宝石表面的运动路径加长了;
(2)二氧化硅颗粒与蓝宝石的接触压力提高了;
(3)超声波的振动和气蚀作用,加强了二氧化硅颗粒与蓝宝石表面的作用。
目前,蓝宝石材料的晶向一般是C向,因蓝宝石材料硬度较大,化学活泼性差,与抛光其它材料相比,其抛光速率相对比较慢。目前,国际上蓝宝石的一般抛光速率不超过5~10 μm / h。河北工业大学宗思邈、刘玉岭在实验室利用自主研发的抛光液在高pH值,约为12.5、高磨料浓度(50%)以及快速将抛光温度升至45℃,蓝宝石抛光速率可达11.3 μm/h[1]。大连理工大学的李树荣、金洙吉研究了不同的pH调整剂对抛光速率的影响,比较了氢氧化钠、氢氧化钾、氢氧化钙和氨水四种无机碱,发现氢氧化钾能明显提高蓝宝石的抛光速率[27]。河北工业大学于江勇、刘玉岭在研究中将纳米级的氧化铝颗粒(浓度为2%)加入到SiO2抛光液中,可以将蓝宝石的抛光速率从9 μm/h提高到11.3 μm/h,且二氧化硅抛光液的稀释率从1∶1提高到1∶2[28]。除了抛光设备之外,影响抛光速率的主要因素是抛光液。此外,和C向蓝宝石相比,A向、M向、R向的抛光速率更慢。可能的原因是C向蓝宝石晶体方向是(0001),且原子键合是O-Al-Al-O-Al-Al-O;M向和A向蓝宝石晶体方向分别是(10-10)和(11-20),他们的化学键合是Al-O-Al-O。因为Al-Al比Al-O键能小且键合要弱[29],C向蓝宝石的抛光主要是将Al-Al键打开,故抛光速率相对较快。研发多系列的高效蓝宝石抛光液显得尤为迫切。
抛光工艺分为单面抛光工艺和双面抛光工艺。关于蓝宝石的平整度(TTV)和弯曲度(WARP)指标,一般而言,双面抛光设备加工出来的蓝宝石晶片要比单面设备加工的蓝宝石片好,主要由双面抛光的原理所决定的。在直接双面抛光过程中,晶片可以实现自转及大范围的公转。这样,抛光出来的片子的平整度要好。另外,在直接双面抛光过程中,实现了正面和反面受力均等、同步抛光,因此,蓝宝石片子的弯曲度要好。6寸蓝宝石双抛片平整度和弯曲度的测试结果,如表5所示。
表5 蓝宝石双抛片平整度和弯曲度测试结果
Table 5 Flatness and curvature of sapphire double side polished wafer
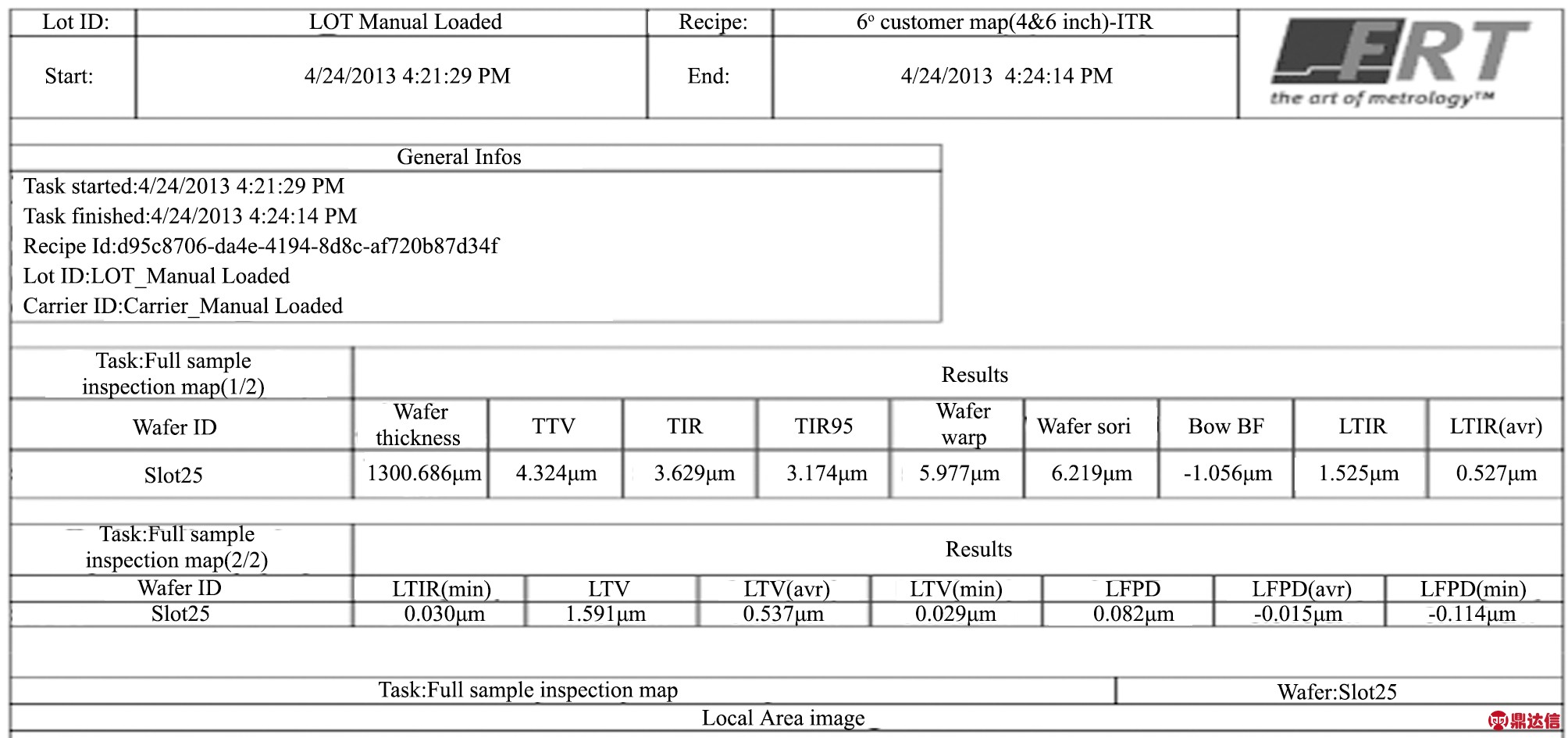
随着对最终蓝宝石产品的质量要求越来越高,表面质量的要求也随之提高。蓝宝石表面质量的好坏,除了取决于最终的湿法化学清洗,抛光结束前的最后一步的轻压抛光(buffing polish)亦非常重要,往往被忽视。轻压抛光的特点是轻压、转速快、时间短。轻压抛光完成得好,可以降低表面粗糙度、减少表面缺陷。
5 清洗工艺
光学级的蓝宝石抛光后清洗工艺相对比较简单,表面质量只要满足于光学要求即可,但半导体行业使用的蓝宝石对表面要求很高。在抛光完成后,需要进行多步清洗、甩干,然后在惰性气体气氛(N2) 中进行包装,达到开盒即用(epi-ready)。
二氧化硅抛光液抛光蓝宝石表面生成的产物是Al2SiO5,蓝宝石表面含硅的厚度约20.5 nm[30]。蓝宝石抛光后清洗工艺比较复杂,但业界一般采用的是湿法清洗(Wet bench),选用的化学试剂也种类繁多。标准的清洗工艺大多采用SC1(氨水,双氧水,水)、SC2(盐酸,双氧水,水)和硫酸+磷酸[31]。SC1、SC2中几种组份比例大小,可以根据实际情况进行调整。硫酸和磷酸的比例通常是3∶1。清洗后的效果由两方面来表征:第一,用Candela来测定蓝宝石的表面缺陷,测试结果如图8所示;第二,蓝宝石表面金属离子含量,可用TXRF来测量,结果如表6所示。目前的清洗方式是多片清洗(Cassette Cleaning),一般是25片。SC1清洗槽一般配备的是超声清洗,超声波的频率一般是40 kHz、80 kHz、120 kHz和200 kHz。随着半导体技术的不断发展,对表面缺陷的要求越来越高,因此,清洗工艺水平必须得到进一步提升。目前,对蓝宝石表面点缺陷(LPD)的要求是在0.3 μm以上。将来的要求可能是0.2 μm或0.1 μm,甚至在0.1 μm以下。因此,清洗槽必须配备兆声单元,进一步加强表面清洗效果,去除微小缺陷。此外,带有兆声喷头的刷片技术(scrubbing)对清洗微小缺陷亦是非常有效的。近年来发展起来的一种新的单片兆声清洗技术- MegPie清洗技术,对清洗微小缺陷行之有效。其兆声发生器离开晶片表面的距离短,因此其振动能量更强。兆声发生器是扇形形状,声波能量分布更均匀[32]。因此,晶片表面的损伤小、交叉污染减少、清洗过的表面更均匀。单片兆声清洗的示意图,参见图9。
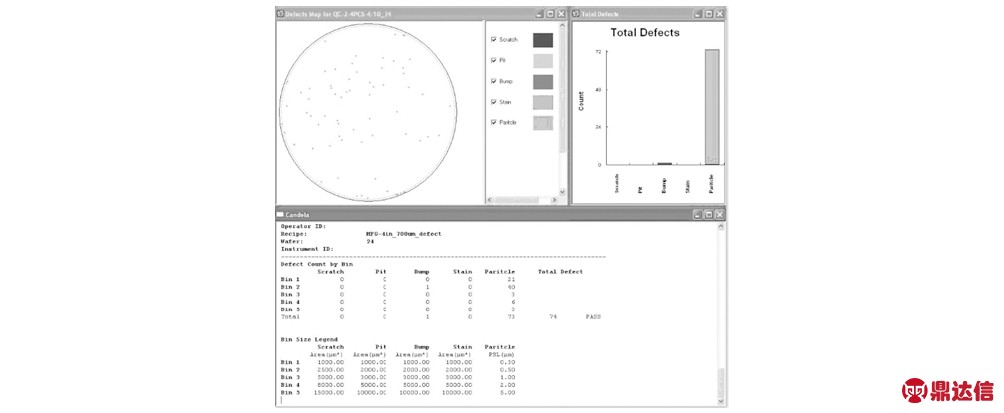
图8 蓝宝石晶片表面缺陷测试结果
Fig.8 Surface defect test result of sapphire wafers
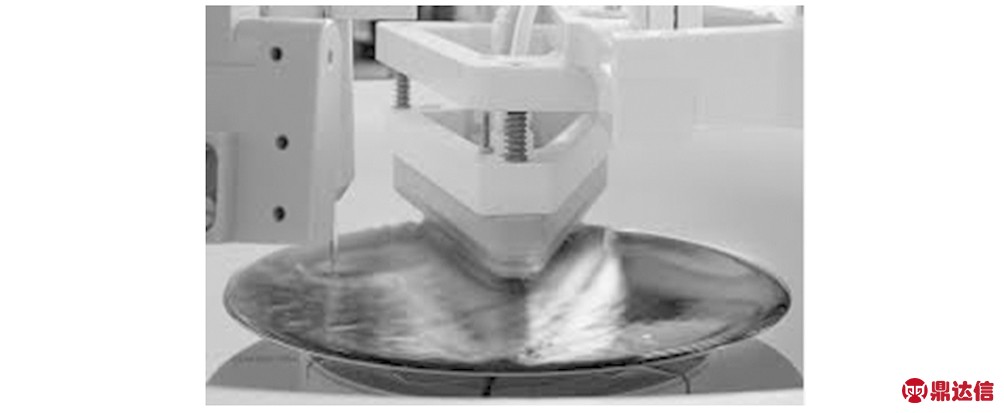
图9 单片 MegPie清洗工艺示意图[32]
Fig.9 Schematic diagram of single wafer MegPie cleaning
表6 蓝宝石表面金属离子含量的TXRF测量结果
Table 6 metal ion contents on sapphire wafer surface by TXRF

6 结 论
(1)针对传统粗磨工艺遇到的各种挑战,双面金刚石盘研磨、单面金刚石盘磨削(grinder)、双面金刚石研磨垫新工艺有望解决磨削速度慢、加工薄片的破碎率高及环境污染等问题。
(2)细粒碳化硼的双面研磨工艺和细粒金刚石颗粒的铜盘精磨工艺各有优缺点:前者在平整度和弯曲度方面有优势;后者的去除速率快且对薄片加工更为有利。
(3)二氧化硅抛光液仍然是蓝宝石抛光的主流,针对C向的蓝宝石抛光液,需要在抛光速率方面进一步提高。对A向、R向、M向蓝宝石的抛光速率特别低,在技术方面亟待突破。
(4)在蓝宝石清洗(Post CMP Cleaning)方面,兆声清洗与传统的超声清洗相比,能够有效降低表面缺陷。兆声单片清洗技术是一个行之有效的方法。