摘要:研究了用减薄磨削的方式代替碳化硅晶片制片过程中的研磨工序,对线切割后的碳化硅晶片进行磨削试验;对比了减薄和研磨磨削的加工效率,分析了晶片表面粗糙度和晶片厚度变化量。
关键词:碳化硅;研磨;减薄;试验研究
随着半导体行业的飞速发展,半导体材料也在更新换代。第一代半导体材料以硅为主导,技术成熟,广泛应用于集成电路行业;第二代半导体材料以砷化镓和磷化铟为主导,主要应用于信息、光纤通信以及半导体激光器等领域[1];碳化硅材料作为第三代半导体代表性材料,具有高禁带宽度,较高的击穿场强,高热导率等诸多优点,可应用于照明、显示等多个领域。表1对3代半导体材料的物理特性进行了对比。
SiC晶锭经过切割、研磨、抛光和CMP抛光几个工序后加工成碳化硅晶片[1,2]。其中的研磨工序是用高硬度的磨料对线切割后的碳化硅圆片表面进行研磨,从而去除上一道工序在圆片表面留下的切痕和损伤层。为了提高研磨效率,研磨又分成粗研和精研两道工序。粗研使用粒径较大的磨粒进行研磨,主要是用于去除切片工序给碳化硅圆片表面造成的切痕以及损伤层[3]。精研是用粒径较小的磨粒进行研磨,主要去除粗研留下的损伤层,以及保证研磨后晶片的面型精度,为下一步的抛光做准备。
表1 3代半导体材料物理特性对比
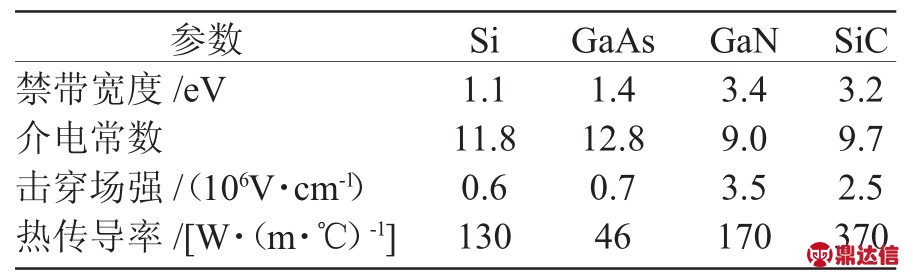
现有粗研效率在3~10 μm/min,表面粗糙度可达0.2 μm左右,精研效率在5~40 μm/h,精研后表面粗糙度在0.1 μm左右,精研后碳化硅晶片TTV在3~6 μm。研究发现碳化硅晶片研磨过程中,研磨热量较大,热量不易散发,容易造成晶片翘曲,平整度变差,同时碳化硅因内部应力大而容易断裂[3,4]。
此外,国内外学者研究尝试了多种磨削方式,例如超声振动辅助磨削,在线电解修整辅助磨削等,用于提高碳化硅晶片的材料去除率以及表面质量[4]。这些磨削方式取得了一定的磨削效果,相对于研磨,这些磨削方式能够降低磨削力,提高表面质量。
采用精密晶圆减薄机,在现有研磨和其他磨削方式的基础上,提出用减薄磨削的方式对切割后的碳化硅晶片进行厚度去除的工艺方案。通过磨削试验,以兼顾碳化硅晶片材料去除率和表面质量为目标,研究碳化硅晶片的减薄效果。
1 试验条件
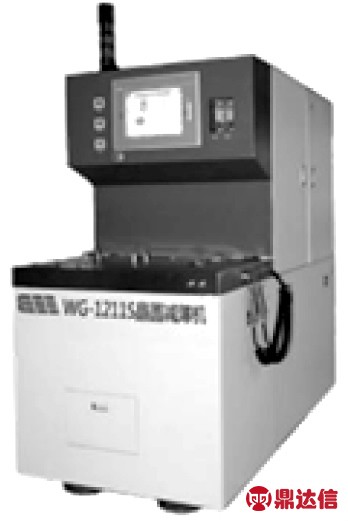
图1 WG-1211S晶圆减薄机
减薄试验采用WG-1211S晶圆减薄机,如图1所示,可加工50~300 mm(2~12英寸)的晶圆,是单主轴单承片台结构,同时承片台单元设有绷架机构,如图2所示,可利用绷架机构减薄不规则尺寸的产品。设备装有在线测量仪,如图3所示,测量分辨率在0.1 μm,该测量机构是全闭环控制,对减薄过程中的晶圆进行实时厚度检测,以消除减薄过程中的热膨胀和磨轮损耗的影响,从而保证晶圆厚度的一致性和准确性。
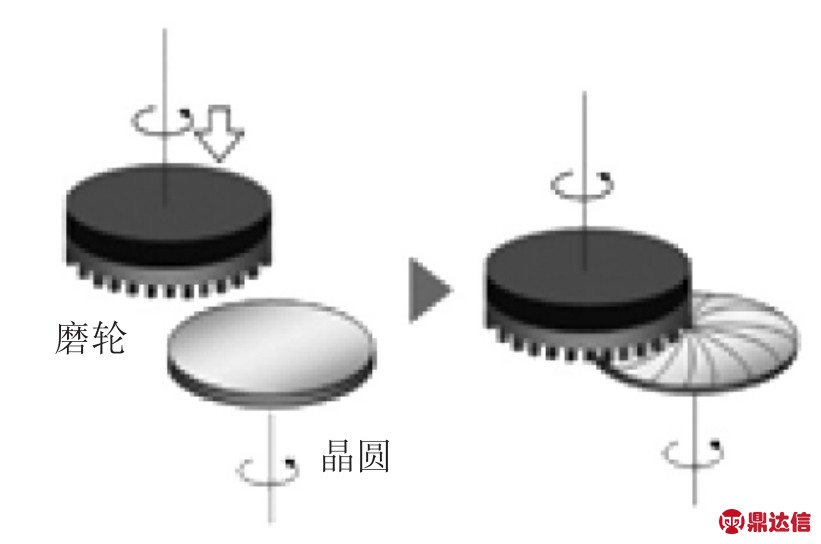
图2 带绷架机构吸附方式
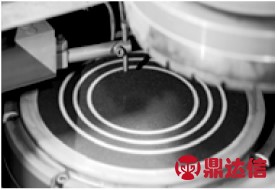
图3 在线测量仪位置示意图
减薄机根据in-feed磨削原理进行设计,晶圆自旋转的同时,主轴机构带动砂轮旋转,同时砂轮向下进给,进而实现减薄过程,减薄原理如图4所示[5,6]。减薄机的关键技术参数指标见表2。
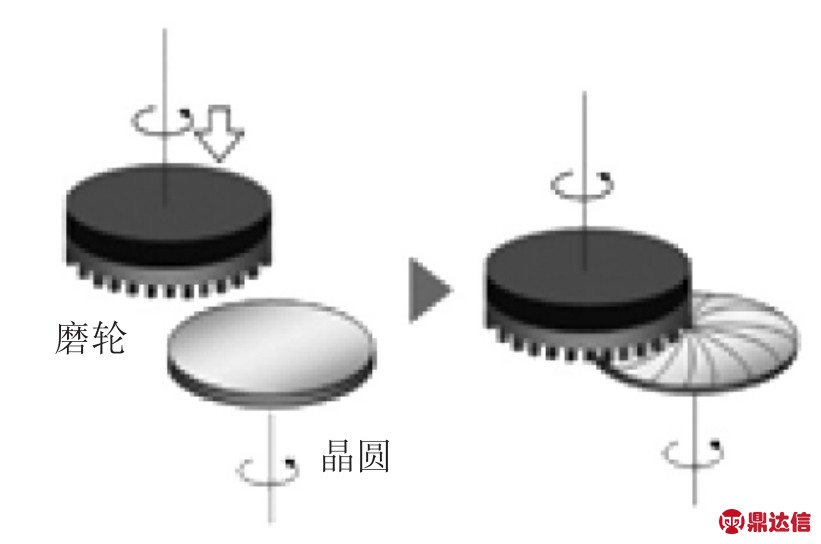
图4 in-feed磨削原理示意图
试验过程中,磨削液和冷却液均为20℃±1℃的去离子水,砂轮选用直径300 mm的目数#1200,#2000,#4800陶瓷结合剂砂轮。碳化硅样片选择的是线切割后的100mm(4英寸)碳化硅晶片,初始厚度450μm,进过三次减薄试验后,减薄至200μm。
表2 WG-1211S晶圆减薄机主要技术指标
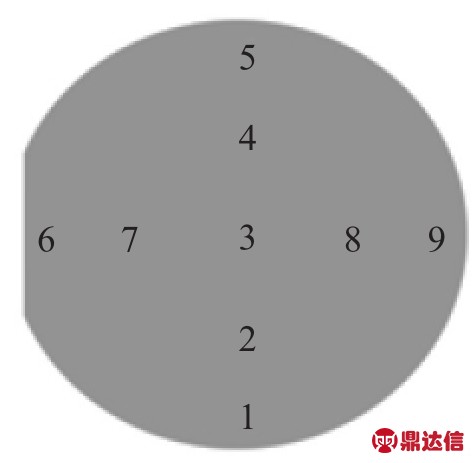
2 检测方法
减薄后采用Sigmatech UltraMapS-200BFP晶圆厚度翘曲测量系统对碳化硅晶片进行测量。该测量系统可以测量50~200 mm的晶片,厚度测量范围在50~3 000 μm,扩展的翘曲变形范围达5 mm,可用于测量晶片的TTV、TIR、WARP,以及BOW值。
采用美国Veeco公司的WYKO NT1100型表面轮廓仪对碳化硅晶片的表面形貌和表面粗糙度值Ra进行测量。该仪器利用光学干涉法对晶片表面进行非接触测量,测量范围从亚纳米级到毫米级。
3 试验过程
将碳化硅晶片用UV膜(160 μm)固定在绷架上,将绷架真空吸附在多孔陶瓷承片台上,如图5所示。
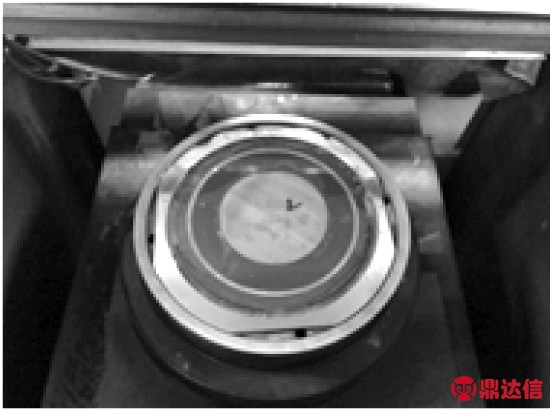
图5 碳化硅晶片磨削前
首先采用目数1200#的砂轮对碳化硅晶片进行减薄,将上一道工序中碳化硅晶片表面的切痕进行去除,同时保证去除效率,减薄厚度在150 μm左右;再次采用目数2000#的砂轮进行减薄试验,将上一步1200#砂轮减薄给晶片带来的损伤进行去除,并减小了内应力,减薄厚度在70 μm左右;最后采用目数4800#的砂轮对晶片表面进行减薄,将上一步2000#砂轮减薄带来的损伤进行去除,再次减小内应力,同时保证面型精度和晶片翘曲度等,减薄厚度在30 μm左右。试验工艺参数见表3。
表3 试验工艺参数
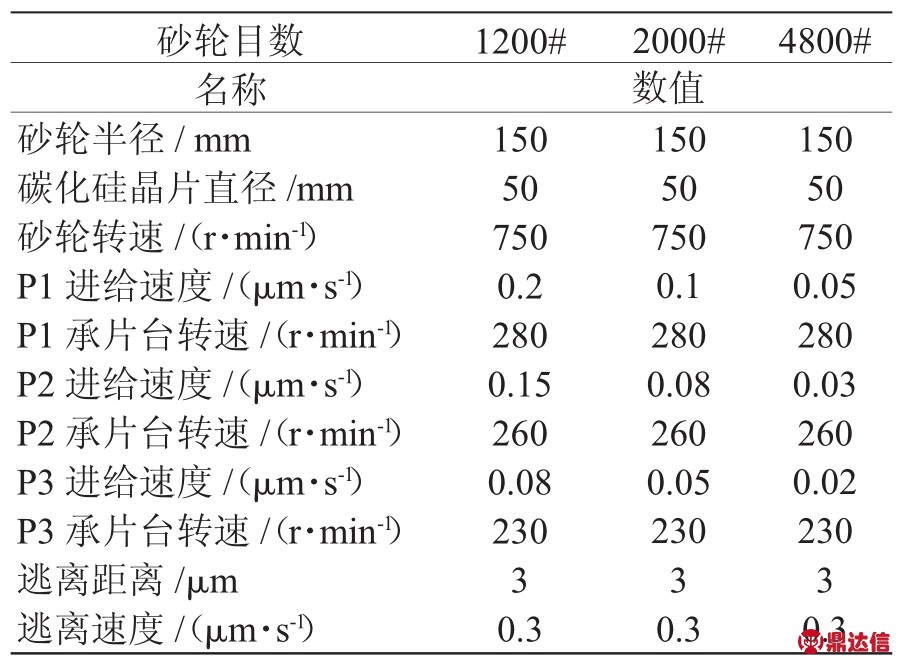
4 试验结果与分析
用WYKO NT1100型表面轮廓仪观查减薄后的碳化硅晶片表面形貌并测量表面粗糙度Ra值。图8(a)、(b)、(c)是1200#、2000#、4800#金刚石砂轮减薄后碳化硅晶片的表面形貌,从图中可以看出,三种目数的砂轮减薄后,晶片表面纹理均匀细致,2000#砂轮减薄后晶片的表面纹理比1200#砂轮减薄后晶片的表面纹理浅,但是2000#和4800#号磨削碳化硅晶片表面有破碎和斑点(见图6(b)、(c)中圆内)。
从图7中可以看出,轮廓仪测量了0~10 μm范围内晶片表面的高度变化。在4~5 μm之间,晶片表面高度由0.02 μm左右变化至0.11 μm左右,也就是图7左图中亮斑(圆内)所在位置,该现象表明,亮斑是高于晶片表面的凸起。导致亮斑产生的原因分析可能砂轮目数越高,自锐性越差,在磨削碳化硅这种高硬度材料时,砂轮上的金刚石磨粒极易磨损和钝化,加上磨削区域温度较高,导致砂轮齿中结合剂的部分被高温烧伤,如图8中砂轮齿上的黑色区域所示(图8圆内区域),结合剂不能及时带着钝化的磨粒一起脱落,进一步导致钝化的磨粒继续参与磨削碳化硅晶片,由于磨削能力不足,钝化的磨粒对碳化硅晶片表面的挤压,造成了图7中亮斑的形成。

图6 金刚石砂轮减薄后碳化硅晶片表面形貌
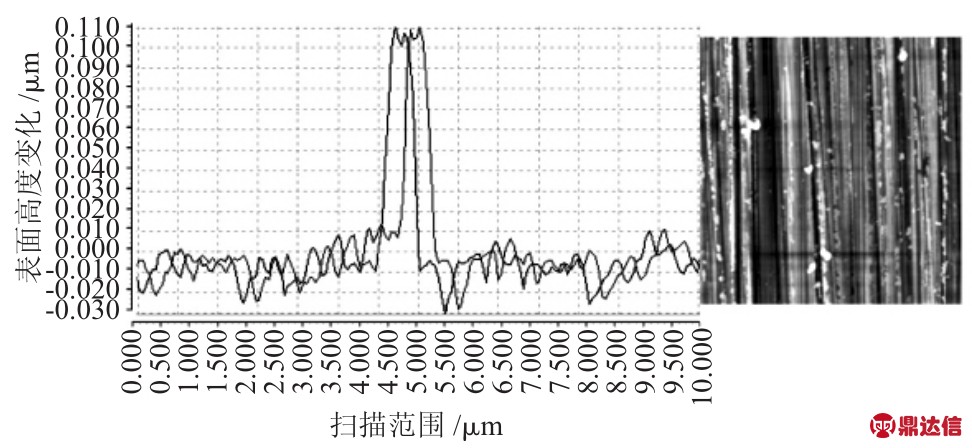
图7 4800#砂轮减薄后碳化硅晶片表面形貌
按图9的测量方式测量晶片表面9点的粗糙度值,1200#、2000#、4800#金刚石砂轮减薄后碳化硅晶片的表面粗糙度值Ra范围分别是:45~55 nm、25~35 nm和6~15 nm。从测量数据可以看出,随着金刚石砂轮目数的增加,减薄后晶片表面质量逐渐变好,但是亮斑的存在会使晶片表面质量变差。
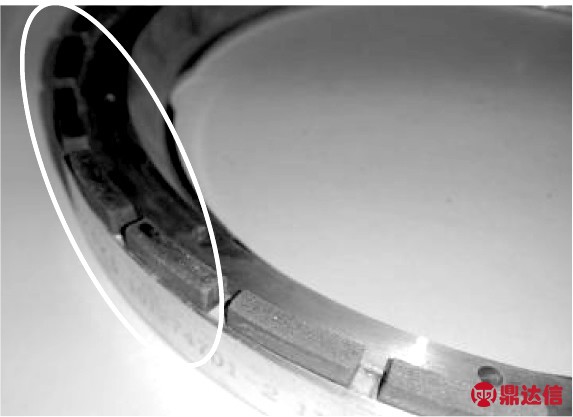
图8 被烧伤的金刚石砂轮表面
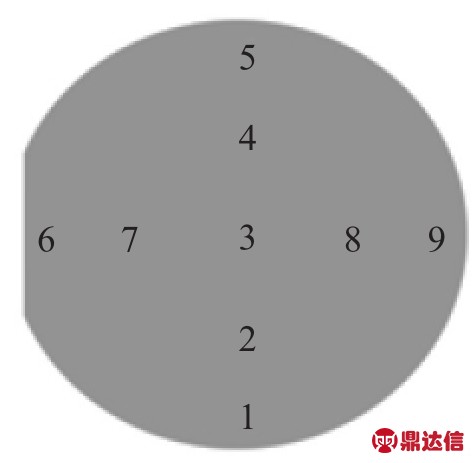
图9 减薄后碳化硅晶片表面粗糙度测量点
用Sigmatech UltraMapS-200BFP晶圆厚度翘曲测量系统对最终减薄后的碳化硅晶片进行测量,测量值见表4。从表4中可以看出,最终减薄后,晶片平均厚度在210 μm左右,距离目标厚度200 μm差10 μm,TTV为2.05 μm,比碳化硅晶片研磨后的TTV值要小,晶片的翘曲度值为34.75 μm,弯曲度值在20 μm以内。
表4 减薄后碳化硅晶片厚度翘曲等测量值

5 结束语
在碳化硅晶片制作过程中,通常采用研磨对碳化硅晶片进行厚度去除,我们采用减薄的方式代替研磨工序对晶片进行厚度去除,并进行试验比较分析。用WG-1211S晶圆减薄机对线切割后的100 mm碳化硅晶片进行厚度去除,利用三种不同目数的砂轮将晶片从450 μm减薄至200 μm。最终晶片减薄至210 μm,TTV为2.05 μm,4800#金刚石砂轮减薄后晶片的表面粗糙度值Ra在6~15 nm,根据表3中的工艺参数得出1200#砂轮减薄效率在6~7.3 μm/min,2000#砂轮的减薄效率在2.5~3.6 μm/min,4800#砂轮的减薄碳化硅晶片效率在1~1.5 μm/min,跟研磨碳化硅晶片的效率以及晶片表面质量和TTV等相比,减薄的方式能实现切割后碳化硅晶片的厚度去除。