摘 要:研究了碲锌镉(CZT)晶片表面的机械研磨和机械抛光工艺。采用不同粒度的Al2O3磨料对CZT晶体表面进行机械研磨和机械抛光,并研究了工艺参数变化对CZT晶体表面质量、粗糙度、研磨速度和抛光速度的影响。结果表明,机械研磨采用粒度2.5 μm的Al2O3磨料,最佳的研磨压力和研磨盘转速分别为120g/cm2 和75r/min,研磨速度为1μm/min;机械抛光采用粒度0.5μm的Al2O3抛光液,最佳的抛光液浓度为6.5%(质量分数),抛光速度为0.28μm/min。AFM测试得到机械研磨后晶片表面粗糙度Ra值为13.83nm,机械抛光4h后,Ra降低到4.22nm。
关键词:碲锌镉;机械研磨;机械抛光;研抛速度;粗糙度
1 引 言
碲锌镉(CZT)晶体是一种新型三元化合物半导体材料。由于电阻率高、原子序数大、禁带宽度随锌含量的不同在1.4~2.26eV范围内连续变化,CZT可用于制作X射线、γ射线等高能射线探测器[1]、碲镉汞红外探测器的外延衬底[2]、激光窗口和薄膜太阳能电池[3]等。
CZT晶片的表面状态对其作为器件和外延衬底应用有着重要影响。CZT晶锭切割后的晶片表面存在损伤层,表面损伤层内晶格周期性被严重破坏,形成空间电荷区,造成表面漏电流,从而影响了CZT电极接触和器件性能[4,5]。外延衬底需要具有完整的超光滑表面,衬底表面的损伤层、杂质以及微缺陷将导致外延生长薄膜的高位错密度、晶格畸变等[6]。随着实际应用对晶片表面质量要求的不断提高,需要建立专用的晶片磨抛设备以及相应的磨抛技术。
目前,CZT晶片的磨抛方法主要包括机械研磨、机械抛光、化学机械抛光和化学抛光。机械研磨和机械抛光是在专用磨抛装置中,依靠磨抛料的机械磨削作用实现对CZT晶片的研磨和抛光,去除晶片表面损伤层,提高表面平整度,降低表面粗糙度。化学机械抛光和化学抛光是在机械抛光过程的基础上,加入化学腐蚀液腐蚀晶片表面,有利于降低晶片表面粗糙度,但化学机械抛光过程的机械抛光和化学腐蚀之间的平衡通常较难控制,且化学腐蚀会改变晶体表面的化学计量比,使表面富碲。因此,机械研磨和机械抛光是CZT晶片表面处理的基础,对其进行深入研究十分必要。CZT晶体的莫氏硬度约为2.3,是典型的软脆材料,机械研磨和机械抛光通常采用莫氏硬度为8的Al2O3 磨抛料,有利于提高磨抛速度。张振宇等[7,8]采用Al2O3磨抛液对CZT晶片进行机械研磨和机械抛光,研究了不同研抛压力对晶片表面粗糙度的影响,最后采用SiO2纳米球抛光液进行化学机械抛光得到粗糙度值为2.196nm CZT晶片表面。张梅等[9]依次采用粒度为9、3和1μm的Al2O3抛光液加工CZT晶片后得到粗糙度为6.54nm的晶片表面。
本文采用不同粒度的Al2O3磨料对CZT晶体表面进行机械研磨和机械抛光,系统研究了研磨压力、研磨盘转数、抛光液浓度、抛光时间对晶片表面质量、粗糙度、研磨和抛光速度的影响,获得CZT晶体机械研磨和机械抛光最佳的工艺参数。
2 实 验
2.1 实验设备
本实验采用的机械研磨抛光设备为沈阳科晶公司生产的UNIPOL-802精密磨抛机,其转速范围是0~125r/min。表面宏观形貌测量采用金相显微镜,其放大倍数为100~1000倍。表面粗糙度测量采用Nanonavi SPA-400SPM原子力显微镜,分辨率在X、Y方向为0.2nm,Z方向为0.01nm。晶片厚度采用千分尺测量,测量精度为1μm。
2.2 机械研磨
选取体积10mm×10mm×3mm的CZT晶片样品9片。采用分析纯、粒度为 W2.5(μm)的Al2O3粉与去离子水配成研磨液,充分搅拌后放入超声清洗机中超声30min,使得Al2O3粉均匀分布。在相同研磨时间(30min)内,研究不同的研磨压力、研磨盘转速对CZT晶片表面质量和研磨速度的影响。晶片编号和研磨参数见表1所示。
2.3 机械抛光
对机械研磨后的CZT样品进行机械抛光,采用分析纯、粒度为W0.5Al2O3磨料,在无纺布抛光垫上进行机械抛光。机械抛光采用研磨实验中得到的最佳的研磨压力和转速参数,研究不同的抛光液浓度和抛光时间对CZT晶片的表面粗糙度和抛光速度的影响。
表1 研磨参数选择
Table 1 Parameters of the lapping process
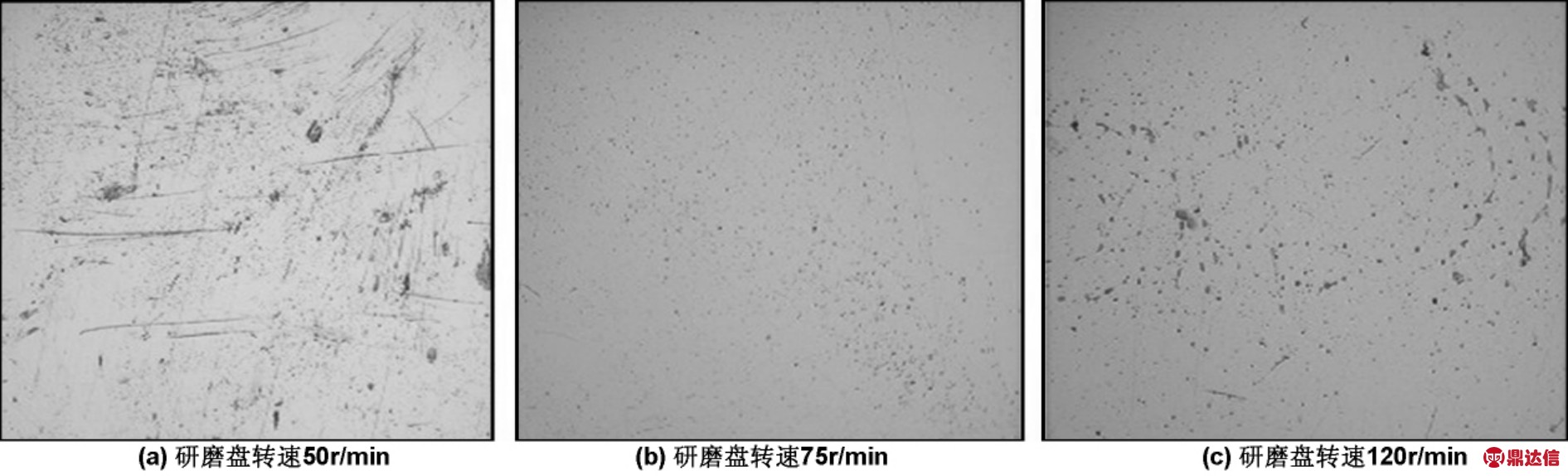
3 结果与讨论
3.1 机械研磨
机械研磨的主要目的是去除CZT晶锭切割后晶片的表面损伤层,并使晶片表面平整、光洁、划痕少,厚度达到预定的要求。因此,研磨实验把晶片表面研磨速度和表面质量作为衡量指标。Al2O3粉的粒度越大其研磨速度越大,但是相应地对晶片表面造成的损伤也越大,且在晶片表面边缘容易出现崩边的现象。综合考虑CZT表面质量和研磨速度的要求,实验采用粒度为W2.5的Al2O3粉在UNIPOL-802精密磨抛机上进行机械研磨,实验参数见表1。图1为CZT晶锭切割后得到晶片的表面形貌,图2~4为使用不同研磨压力和研磨盘转数研磨后晶片的表面形貌图,图5反映了晶片的研磨速度变化规律。
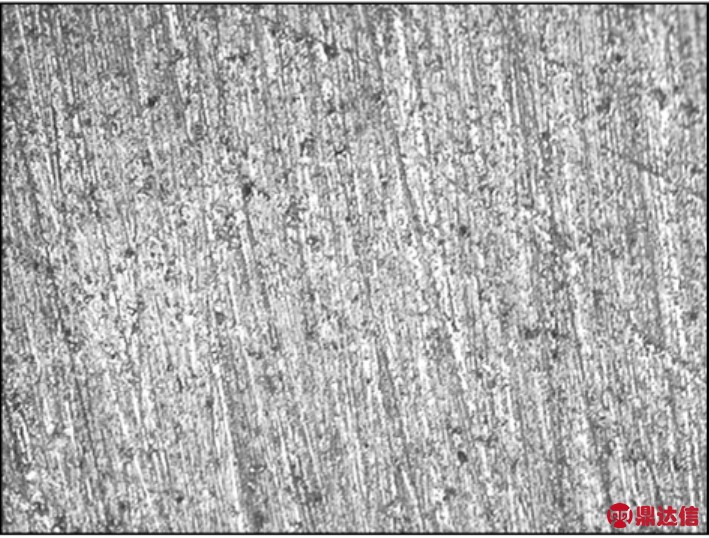
图1 CZT晶锭线切割后晶片的表面形貌(×200)
Fig 1 The surface of CZT after wire saw(×200)
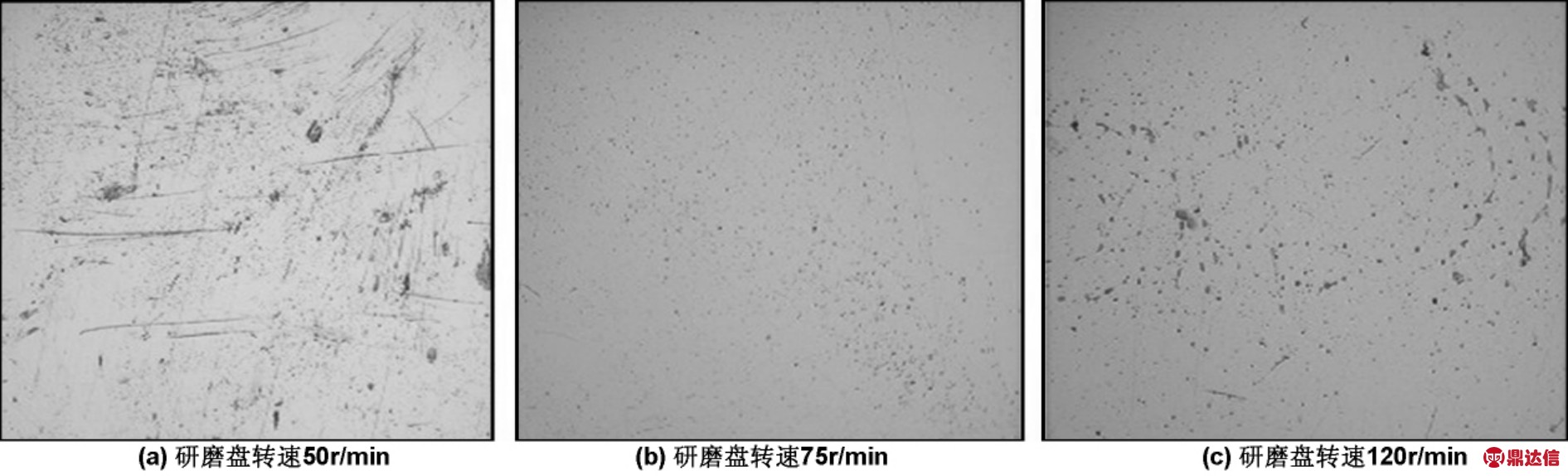
图2 研磨压力为65g/cm2,不同研磨盘转速下研磨30min后CZT晶片的表面形貌(×500)
Fig 2 The surface morphology of CZT wafer after 30min lapping by different plate speeds with the lapping pressure of 65g/cm2(×500)
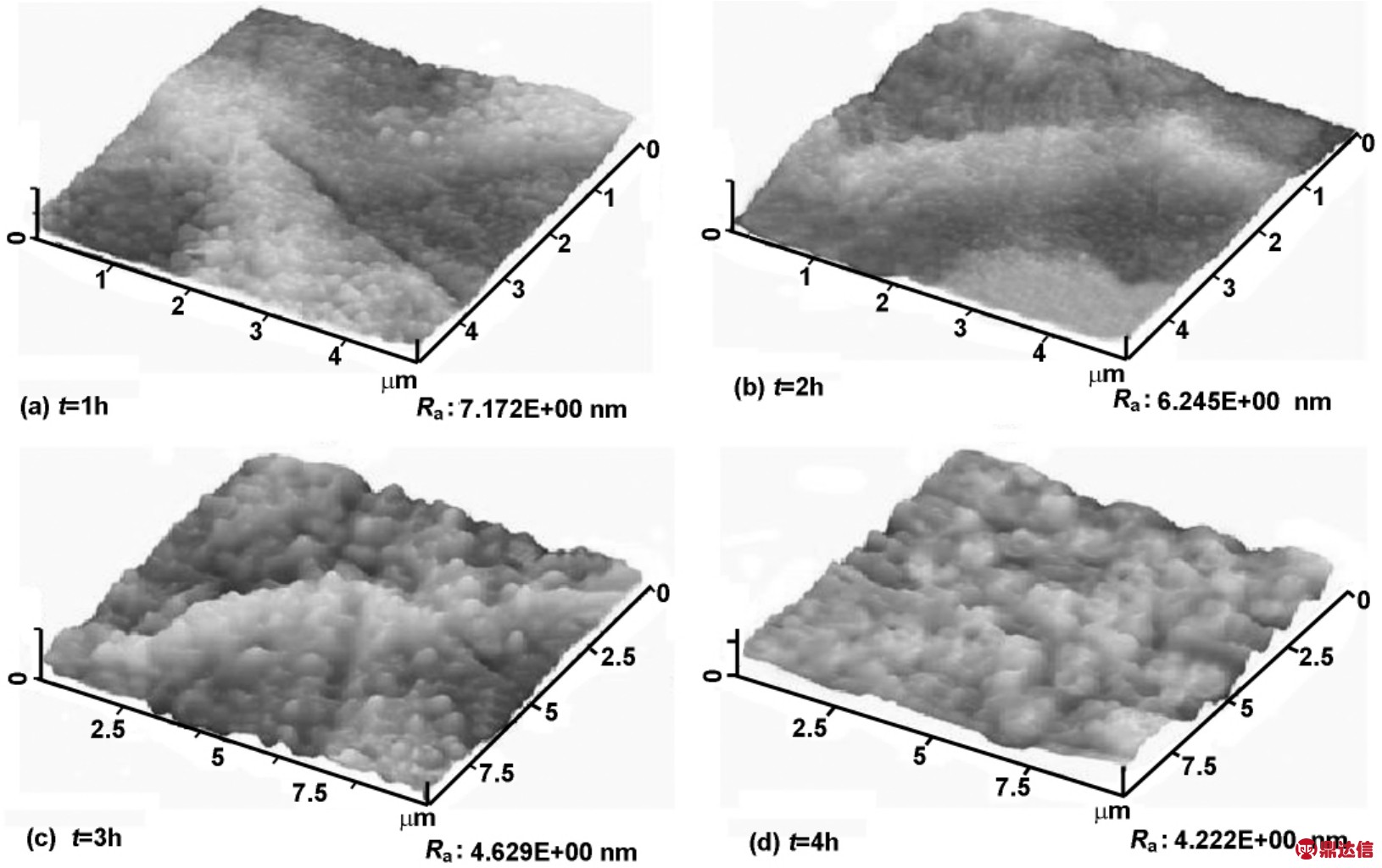
图3 研磨压力为120g/cm2,不同研磨盘转速下研磨30min后CZT晶片初始表面形貌(×500)
Fig 3 The surface morphology of CZT wafer after 30min lapping by different plate speeds with the lapping pressure of 120g/cm2(×500)
从试验结果看出,切割后的CZT晶片表面有大量的无规则深划痕和杂质存在,且平整度较差。采用粒度为W2.5的Al2O3粉进行机械研磨,在相同研磨压力下,30min研磨时间内:当研磨盘转速为50r/min时,晶片的表面划痕密度较大;转速增大到75r/min,晶片的表面划痕密度迅速减小;转速增大至100r/min,表面划痕密度又开始增大,表面质量也变得较差。晶片表面的研磨速度也表现出类似的规律,首先随着研磨盘转数的增加而增加,转速增大到75r/min,研磨速度最大,转速增大至100r/min,晶体的研磨速度反而开始下降。当研磨盘转速较低时,研磨液中的Al2O3磨粒和CZT晶片表面凸起碰撞的速度较低,作用力较小,因而研磨速度低,在30min内不足以使晶片表面平整,且表面划痕密度大。随着研磨盘转速的增加,Al2O3磨粒对CZT表面的冲击越来越频繁,作用力也增加,从而使晶片研磨速度增加,有效去除晶片的表面损伤层,晶片表面平整,划痕密度大幅降低。研磨盘转速进一步增大后,虽然Al2O3磨粒和CZT晶片表面凸起的碰撞进一步加剧,但此时研磨盘中的磨粒液在较大离心力的作用下容易被甩出,所以,晶体去除率反而降低,同时磨粒的不均匀分布导致晶片平整度降低,划痕密度增大。

图4 研磨压力为185g/cm2,不同研磨盘转速下研磨30min后CZT晶片初始表面形貌(×500)
Fig 4 The surface morphology of CZT wafer after 30min lapping by different plate speeds with the lapping pressure of 185g/cm2(×500)
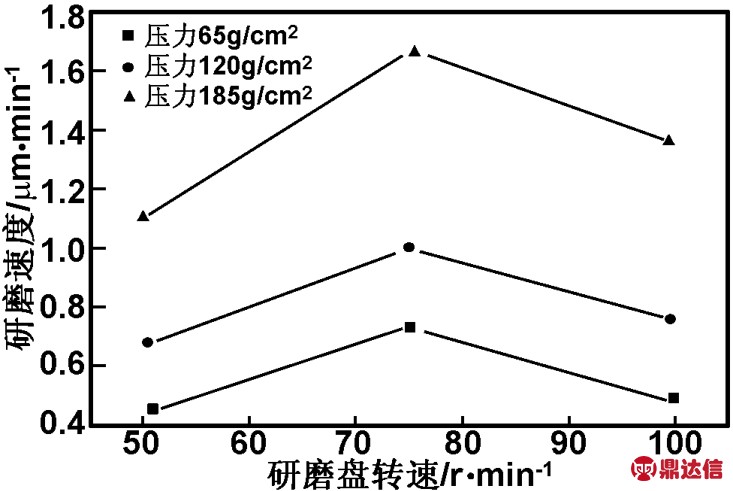
图5 CZT晶片机械研磨速度随压力和转速的变化规律
Fig 5 The variation of the lapping rate of CZT wafers related to the lapping pressure and the plate rotating speed
图5显示在相同研磨盘转速下,随着研磨压力的增加,晶体去除率增大。当研磨压力较小时,CZT晶片表面与Al2O3磨粒之间的摩擦力面积较小,从而晶体去除率较低,同时,压力小的配重块在研磨盘上的旋转不平稳,会造成晶体在研磨时与研磨盘发生冲击,产生崩边现象。随着研磨压力的增加,CZT晶片表面和Al2O3磨粒之间的摩擦力面积增大,从而CZT晶片的去除率增大,有利于晶片表面平整和划痕密度降低。但是,研磨压力过大则容易在晶片表面引入深划痕,如图3(c)、图4(c)所示,降低晶体表面质量。
综合分析研磨压力与主轴转速对晶体研磨速度和表面质量的影响,得出最佳的研磨压力为120g/cm2、主轴转速为75r/min左右。此时,研磨速度约为1μm/min。
3.2 机械抛光
机械研磨后的CZT晶片需要进行机械抛光加工,以进一步去除晶体表面损伤层,降低表面的粗糙度。本实验采用W0.5粒度的Al2O3抛光液,在无纺布抛光垫上进行机械抛光。首先比较了不同浓度的抛光液对CZT抛光速度的影响,结果如图6所示。可以看出,随着抛光液浓度的增加,抛光速度增大,浓度达到6.5%(质量分数)后抛光速度增大趋于平缓。机械抛光过程中,抛光液浓度过大,不利于磨粒的均匀分散,易形成较大的磨粒团,不利于去除表面损伤层和降低表面粗糙度;而抛光液浓度过小则影响抛光效率,并会造成晶体与研磨盘表面直接接触,出现崩边现象。因此,在保证材料抛光速度的前提下,W0.5粒度的Al2O3抛光液浓度应选为6.5%(质量分数),有利于保持磨粒的均匀性和分散性,且不会造成抛光液的浪费。

图6 不同浓度Al2O3抛光液的CZT晶片抛光速度
Fig 6 The mechanical polishing rate of CZT wafer vs.the concentration of Al2O3polishing suspension
机械研磨后的CZT晶片表面的AFM图(图7)显示表面粗糙度Ra值为13.83nm,可以看到晶片表面有明显的划痕存在。CZT晶片采用6.5%(质量分数)浓度的Al2O3抛光液,机械抛光不同时间后,晶片表面的AFM图谱如图8所示。
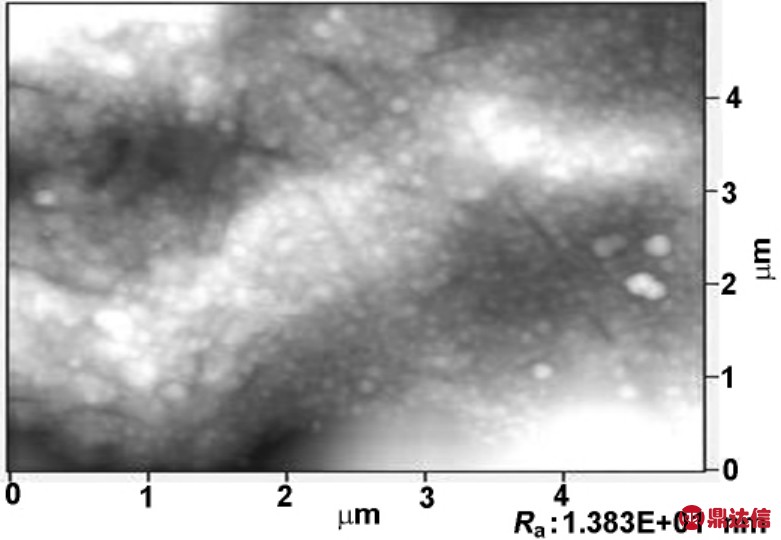
图7 CZT晶片机械研磨后AFM表面形貌
Fig 7 The AFM surface morphology of CZT wafer after mechanical polishing
经过1h的机械抛光后,晶片表面Ra值迅速降低到7.17nm。这是由于晶片初始表面粗糙度高,磨粒和晶片表面凸起的接触面积较大,凸起迅速被磨平,Ra值显著下降。3h后,表面Ra值下降到4.63nm。此后,随着时间的增加,晶片表面逐渐变平坦,磨粒与平滑表面之间摩擦力减小,Ra值降低趋于稳定,4h后Ra达到最小值4.22nm。同时,从图8(d)(机械抛光4h)中可以看到,晶片表面没有任何微裂纹、划痕和嵌入硬质颗粒等存在。实验结果表明,通过对CZT晶片表面机械研磨、机械抛光工艺参数的改进和有效控制,可有效地去除CZT晶片表面损伤层,降低晶片表面粗糙度,获得较理想的CZT晶片表面状态,为精确测量CZT晶体的电学性能和CZT器件制作打下了良好的基础。
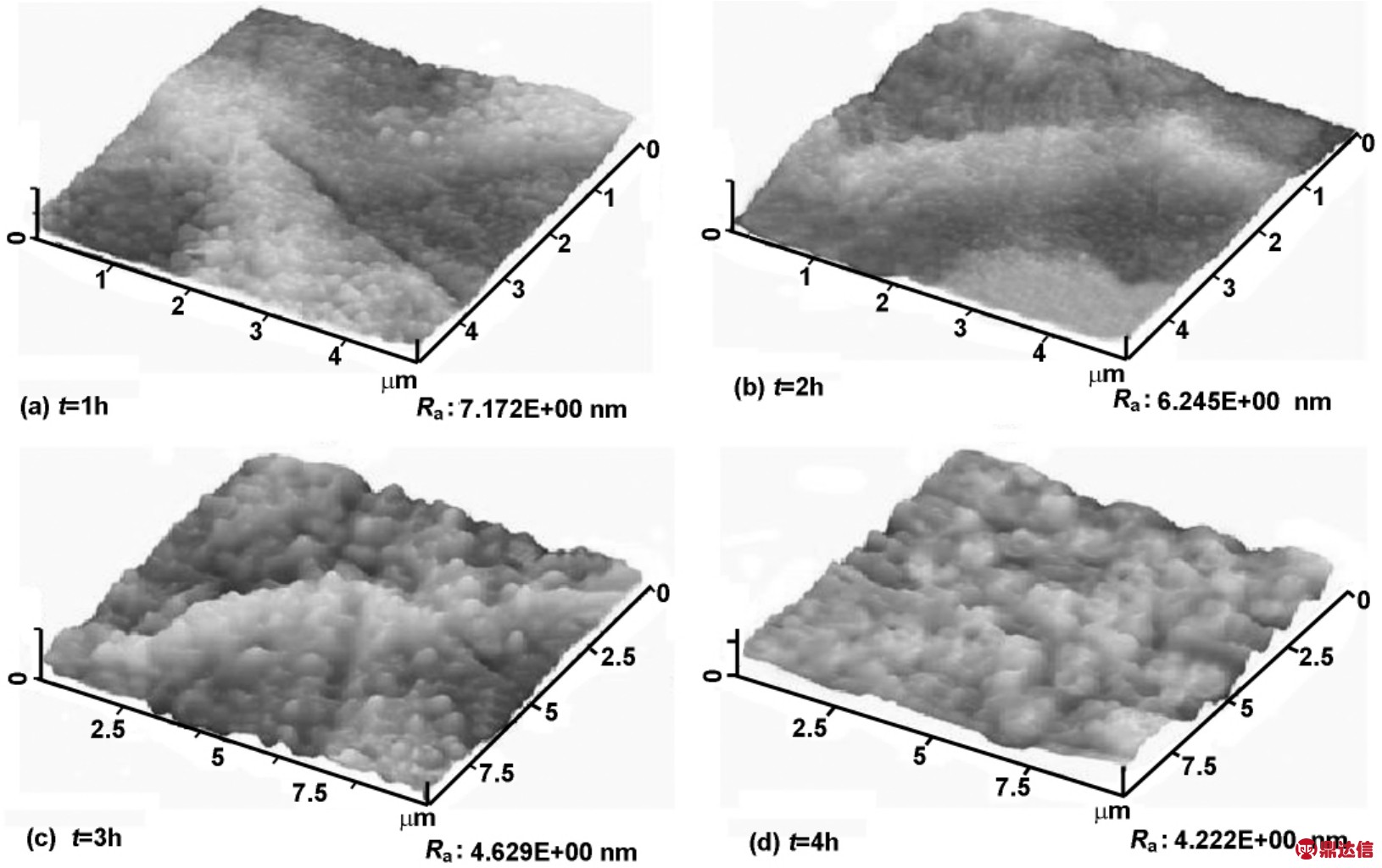
图8 CZT晶片不同机械抛光时间后晶片表面的AFM形貌图
Fig 8 The AFM surface morphology of CZT wafer with different mechanical polishing times
4 结 论
采用不同粒度的Al2O3游离磨料在UNIPOL-802精密磨抛机上对CZT晶体表面进行机械研磨和机械抛光工艺研究。采用金相显微镜、原子力显微镜、晶片厚度测试等手段研究了不同机械研磨、抛光工艺参数对CZT晶体表面质量、粗糙度、研磨速度和抛光速度的影响。通过多组实验数据比较,获得了CZT晶片机械研磨和机械抛光的优化工艺参数,主要结论如下:
(1) 机械研磨采用粒度W2.5的Al2O3磨料,最佳的研磨压力为120g/cm2,研磨盘转速为75r/min,研磨速度为1μm/min。晶片表面平整,划痕密度最低,且无深划痕出现。
(2) 机械抛光采用粒度W0.5的Al2O3抛光液,最佳的抛光液浓度为6.5%(质量分数),抛光速度为0.28μm/min。AFM测试表明机械研磨后晶片表面粗糙度Ra值为13.83nm,机械抛光4h后,Ra值降低到4.22nm。