摘 要:本文研究了三种不同种类的磨料对SiC单晶片去除率的影响。最终选用金刚石磨料作为SiC单晶片的化学机械抛光磨料。结果表明:固结磨料CMP的材料去除率是游离磨料的3倍以上,固结磨料抛光垫,可大幅度提高材料去除效率。
关键词:固结磨料;SiC晶体;化学机械抛光;材料去除率
0 引言
目前市场上的6H-SiC单晶片主要用于LED照明,其在LED领域的强大市场牵引力将促使其取代Si成为第三代半导体衬底材料。由于SiC单晶体本身具有较高的硬度和较强的化学稳定性,化学机械抛光技术(chenmical mechanical polishing,CMP)是目前唯一能够实现SiC单晶体全局平坦化(global planarization)的超精密加工方法。由于SiC单晶体的研抛难度极大,所以高精度、高效率、低成本的晶体基片加工技术是SiC单晶衬底材料制备技术的关键和以后的发展方向。
传统的游离磨料化学机械抛光存在着明显的缺点:磨料在抛光液中不能重复利用导致损耗大、加工成本高、对环境污染大;磨料的运动轨迹不确定性导致其加工切削量的不均匀,很难保证较高表面平整度;磨料的在抛光垫和工件之间随机运动导致过抛光的现象;游离磨料化学机械抛光的成品率偏低,较大的去除量才可能达到较高的表面质量。固结磨料化学机械抛光液中只含有化学物质不含磨粒,没有抛光浆料和悬浮微粒处理问题,没有修整抛光垫以及清理抛光料浆所带来的停工问题,对环境的造成污染较小 。
本文针对SiC单晶材料的特性和加工表面质量要求,通过SiC单晶片游离磨料化学抛光加工试验,以材料去除率(MRR)和表面粗糙度(Ra)为目标,选出适合抛光SiC单晶片的磨料。并比较了固结磨料和游离磨料抛光工件的去除速率以及抛光后工件的表面粗糙度。
1 试验
试验对象采用直径2英寸的单晶6H-SiC基片,该在研磨抛光机上抛光,进行游离磨料抛光时,将选定的氧化剂、有机碱分别用去离子水稀释后混合,分别加入相同含量不同种类的磨料,在进行固结磨料化学机械抛光时,抛光液中添加相同的化学试剂,不添加磨料。
抛光后,称量晶片抛光前后基片的质量,以计算抛光去除率;轮廓仪测量抛光前后的表面粗糙度。由于SiC单晶体本身特殊的原子堆叠结构导致其分为C面和Si面,本文只分析了C面的试验结果。
2 结果与讨论
2.1 磨料种类的对抛光结果的影响
如果材料去除率过低将直接影响到抛光效率,不能及时去除上一步工序留下的损伤;另外,化学机械抛光中影响到抛光结果的因素非常多,过低的去除率将很难判断实验因素对结果的直接影响。
磨料的对比试验是通过游离磨料化学机械抛光完成的,试验中磨料粒径为W1-2,每500ml抛光液中添加6g磨料微分,抛光液通过使用分散剂和搅拌器抛光液保证抛光液的悬浮均匀性。
实验结果表明,比较相同粒径情况不同种类的四种磨料对
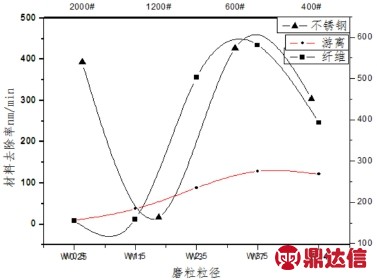
图1 粒径对材料去除率的影响
SiC单晶体去除能力的不同,四种磨料中,碳化硼、白刚玉、硅溶胶等三种磨料对SiC的可加工性较差,只有金刚石对SiC单晶体的材料去除率明显。因此,本文在固结磨料抛光垫订制时都选取金刚石磨料制作的固结磨料抛光垫。
2.2 固结磨料CMP和游离磨料CMP的试验对比
试验中采用纤维衬底固结磨料抛光垫、不锈钢衬底固结磨料抛光垫进行固结磨料化学机械抛光,抛光垫的磨料采用金刚石。另外采用基于金刚石磨料的游离磨料化学机械抛光进行时结果对比。各组试验中采用的化学试剂成分相同。
实验结果得出不同粒径型号的固结磨料抛光垫SiC晶体的C面的抛光结果。在抛光液加工时,不锈钢基底的固结磨料抛光垫上的工件很容易在其表面打滑,影响正常加工,同时大粒径的抛光垫,对SiC表面损伤及其严重,边缘磨损严重,容易掉块。抛光垫表面及颗粒的不均匀导致加工后的SiC表面粗糙度较高,有明显的大颗粒划伤。通过磨料粒径的变化来做单因素试验,游离磨料化学机械抛光液根据实验室配方配制成,最后添加相同含量的磨料微粉。
图1游离磨料CMP、纤维衬底固结磨料抛光垫抛光、不锈钢衬底固结磨料抛光垫抛光后的数据结果,总体来说抛光后表面粗糙度较高些,材料去除率值较大,较游离磨料提高幅度很大。由于抛光技术不成熟,制作的抛光垫参数不稳定,导致去除率不呈线性关系,没有明显规律性。
3 结论
试验结果表明,固结磨料化学机械抛光材料去除率高于游离磨粒化学机械抛光,可重复使用磨料,对环境污染小,是非常有前景的平坦化技术,抛光液中化学试剂的加入有效提高了材料去除率和表面质量。
1)固结磨料CMP的材料去除率是传统CMP的3倍以上。
2)固结磨料抛光垫,可大幅度提高材料去除效率。
3)从试验过程和结果来看,固结磨料CMP后表面划痕更多,用于抛光垫技术问题,表面损伤相对游离磨料化学机械抛光更严重。
4)固结磨料化学机械抛光不需要像游离磨料化学机械抛光垫一样进行频繁修整,抛光液中无磨料,抛光后设备更易清洗。