摘 要:磨削工艺直接影响着磨削后晶片的表面质量参数,在这些参数中,总厚度变化(TTV)是鉴别晶片几何参数好坏的重要指标之一。分析了磨削工艺中承片台转速、主轴进给速度、主轴转速对TTV的影响。
关键词:晶圆减薄;磨削;总厚度变化
从硅单晶锭到能够用于集成电路等器件制造的硅片需要一系列的机械和化学加工过程。硅片加工是IC制造系统中重要的基础环节,硅片的加工精度、表面粗糙度和表面完整性直接影响IC的线宽和IC芯片的性能。IC制造过程包括硅片制备、前道、检测和后道四个阶段,整个过程中要应用到微细加工和超精密加工等先进制造工艺和设备,而其中硅片的超精密加工(包括超精密磨削、研磨和抛光)工艺和设备在IC制造过程中具有重要作用,是IC制造的关键技术。受成品芯片制造成本因素的驱动,硅片尺寸不断增大,已由半世纪前的φ12.5 mm增加到目前的φ450 mm[1],晶圆厚度向超薄化发展。随着硅片尺寸的增大,对超薄晶圆面型精度的要求也不断提高。例如,JB-802型全自动晶圆减薄机可以将φ200 mm晶圆磨削到70 μm(见图1),总厚度变化(TTV)小于1.5 μm;BGP300全自动晶圆减薄抛光一体机可以将φ300 mm晶圆磨削抛光到50 μm,总厚度变化(TTV)小于2.5 μm。晶片总厚度变化量(TTV)是晶圆减薄机的一项重要指标,直接影响后续的各项封装工艺和芯片的最终质量。因此,通过不断完善磨削工艺参数,如承片台转速、主轴进给速度、主轴转速等,最终达到降低磨削后晶圆的TTV值。
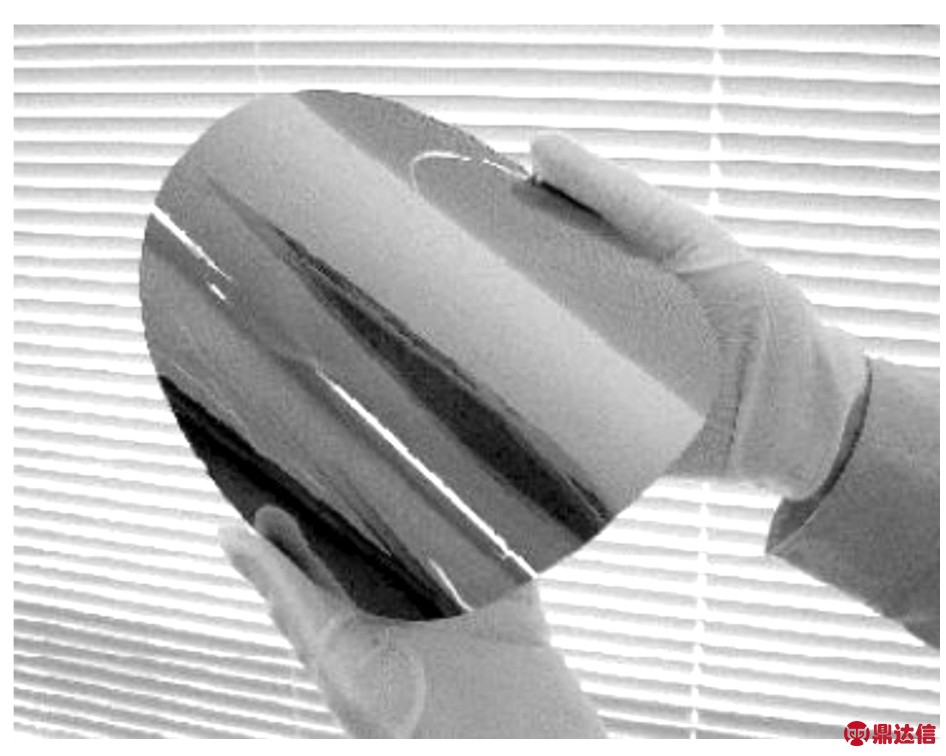
图1 超薄片弯曲示意图
1 晶圆减薄机工艺过程和原理
1.1 晶圆减薄机工艺过程
硅片背面磨削一般分为两步:粗磨和精磨。在粗磨阶段,采用粒度46#~500#的金刚石砂轮,轴向进给速度为100~500 mm/min,磨削深度较大,一般为0.5~1 mm。目的是迅速地去除硅片背面绝大部分的多余材料(加工余量的90%)。精磨时,加工余量几微米直至十几微米,采用粒度2000#~4000#的金刚石砂轮,轴向进给速度为0.5~10 mm/min。主要是消除粗磨时形成的损伤层,达到所要求的厚度,在精磨阶段,材料以延性域模式去除,硅片表面损伤明显减小。
1.2 晶圆减薄机磨削原理
当前主流晶圆减薄机的整体技术采用了In-feed磨削原理设计。为了实现晶圆的延性域磨削,提高减薄质量,通过减小砂轮轴向进给速度实现微小磨削深度,因此,要求设备的进给运动分辨率小于0.1 μm,进给速度最小1 μm/min。另外,为了提高减薄工艺的效率,进给系统在满足低速进给的前提下,要尽可能实现高速返回(见图2)。
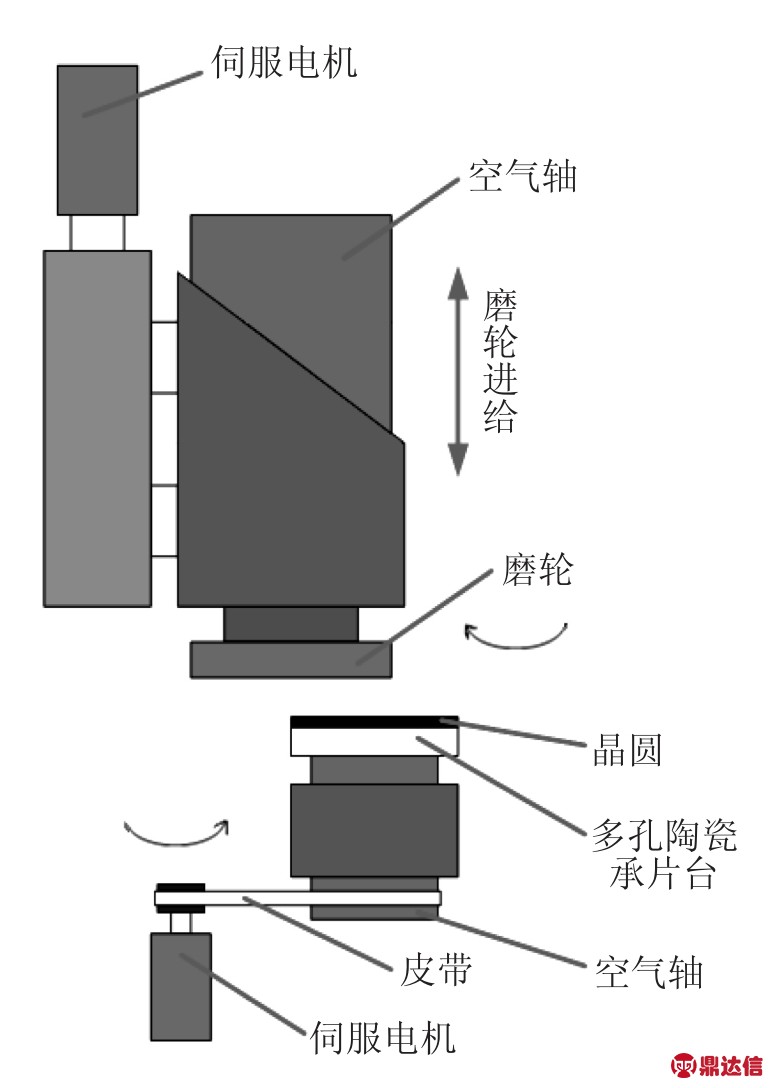
图2 晶圆减薄原理示意图
2 实验研究
2.1 实验设计
准备20片φ200 mm(8英寸)晶片,进行减薄试验,记录减薄时的各项工艺参数及最终所磨削晶片的TTV值,磨削实验用JB-802晶圆减薄机(见图3)。

图3 JB-802晶圆减薄机
2.2 工艺操作步骤
将20片φ200 mm(8英寸)晶片,2片一组,分10组放置到片盒1中,运行自动磨削过程,晶片经过粗磨和精磨后,将其放置于片盒2中。晶片的初始厚度为540 μm,设定的目标厚度为170 μm,减薄后的晶圆片见图4所示。
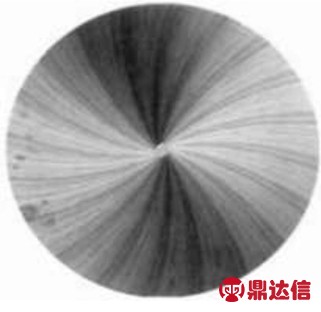
图4 减薄后的晶圆片
2.3 测量设备及方法
通过星纳多功能晶片检测系统MS203测试,读取五个点晶圆片数据,测量方法如图5所示。
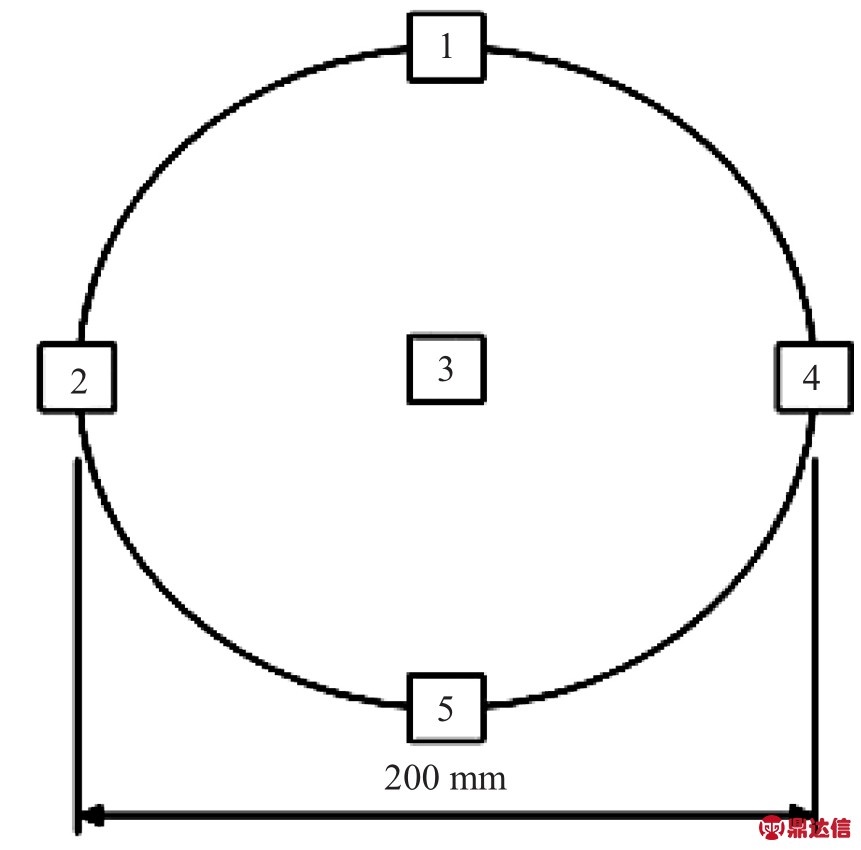
图5 晶圆厚度检测位置示意图
2.4 实验结果
将片盒2中晶圆片置于星纳多功能晶片检测系统MS203平台上,读取五个点晶圆片数据,如表1所示。
表1 晶圆片TTV值
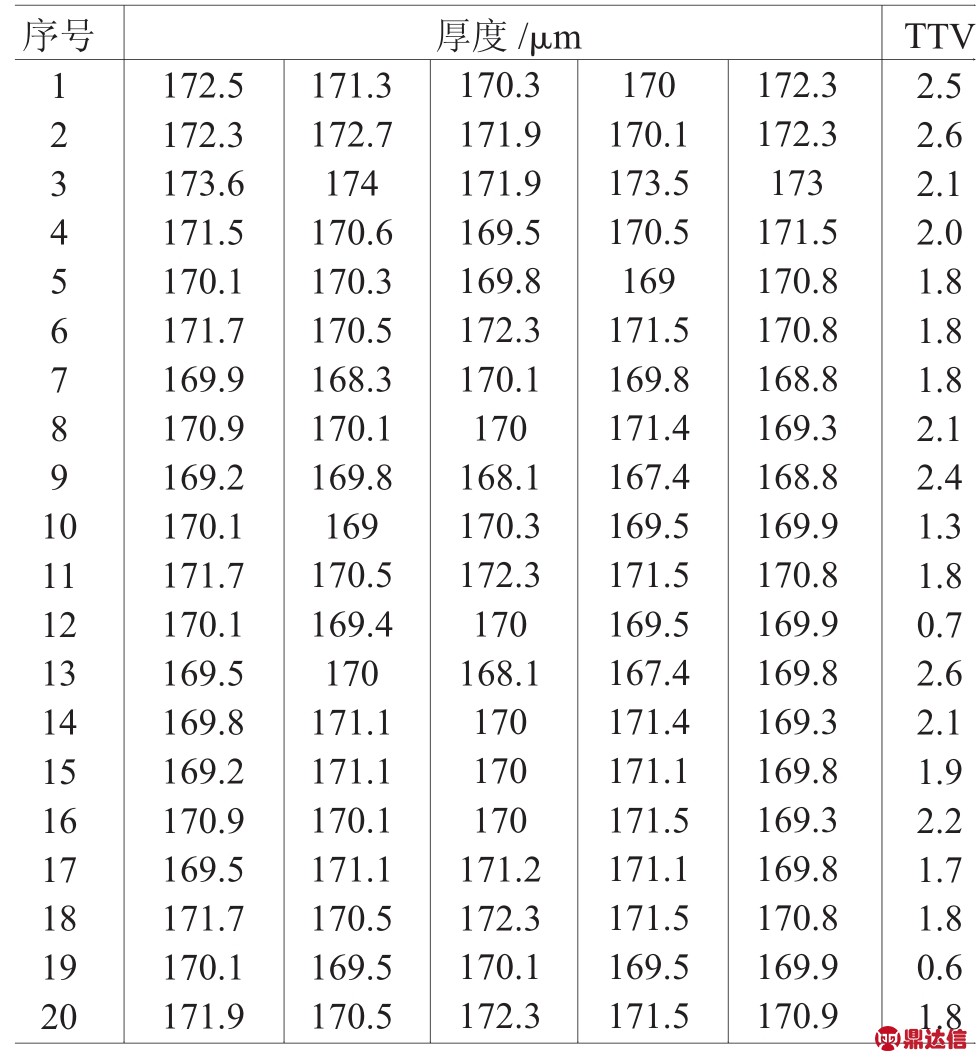
20片晶圆TTV值分布图分别见图6和图7。
我们取4号片进行晶圆表面模拟,如图8所示,晶圆中间区域产生凹陷。
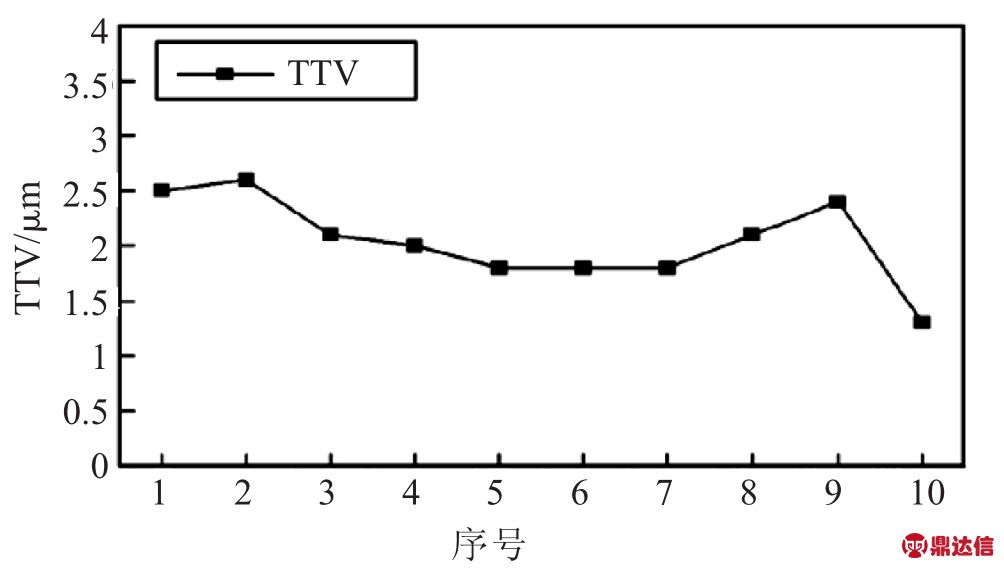
图6 晶圆片TTV变化图
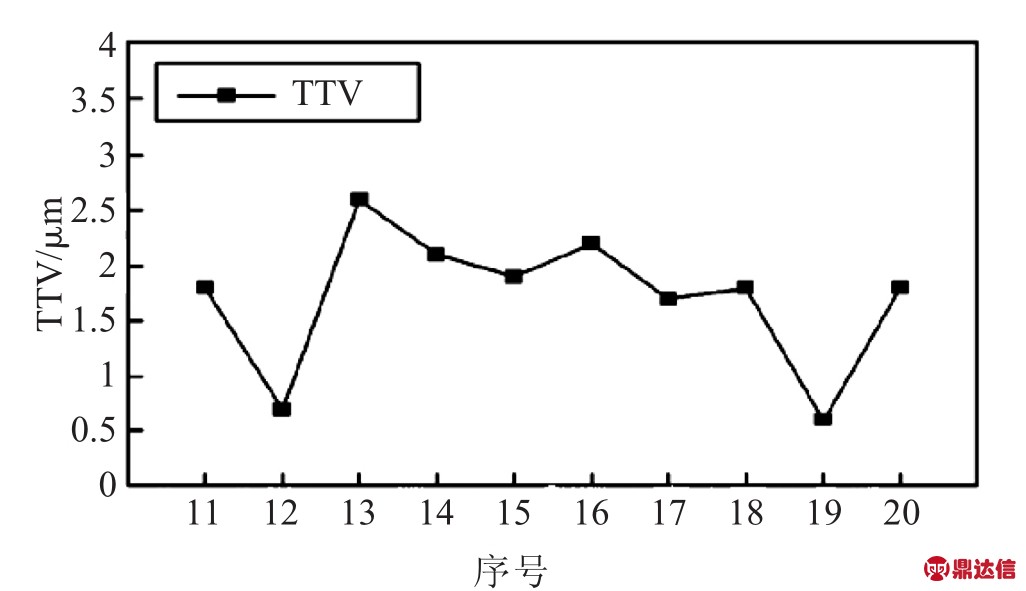
图7 晶圆片TTV变化图
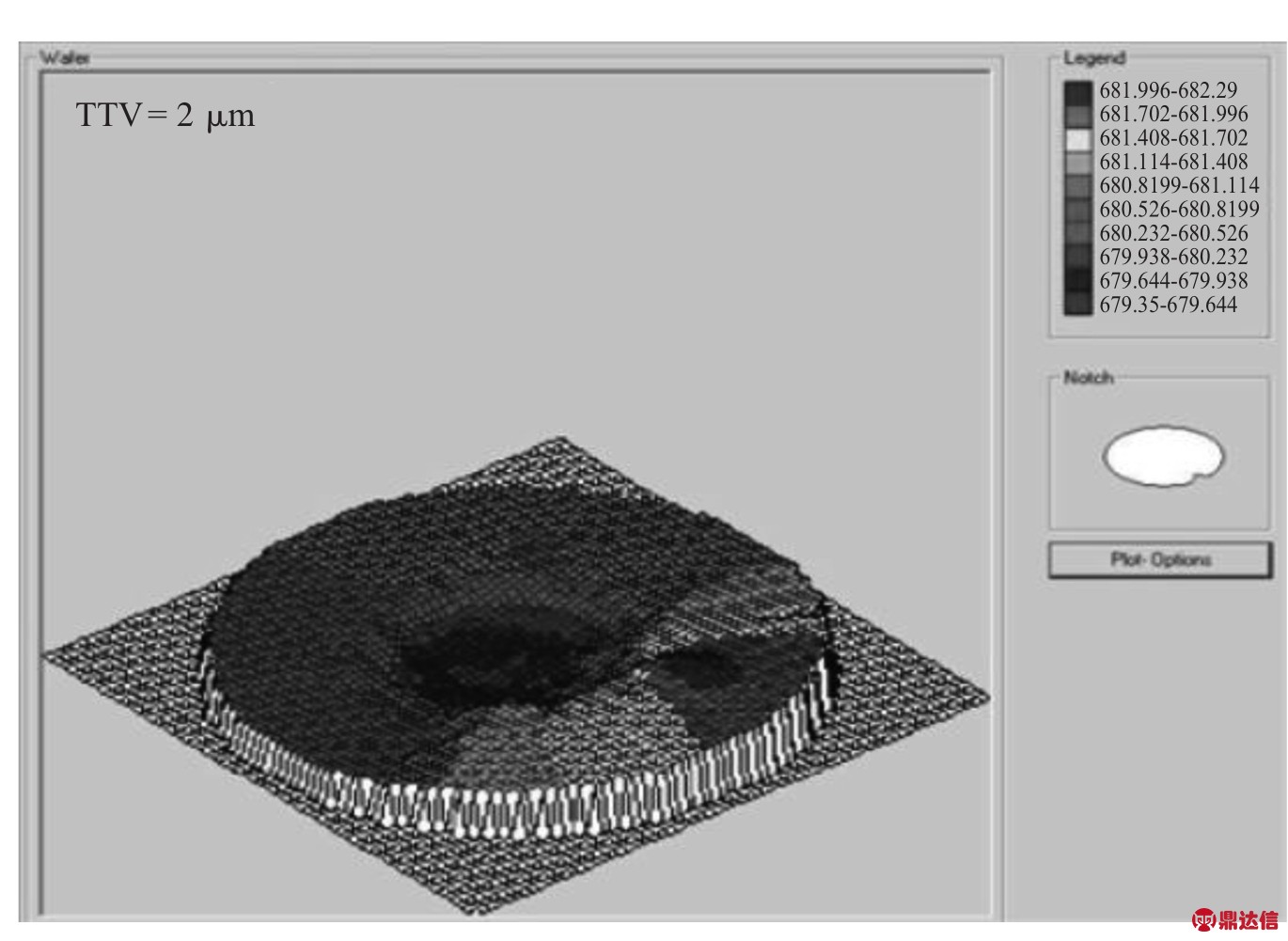
图8 晶圆减薄后之TTV(中间区域产生凹陷)
2.5 结果分析
为了研究砂轮进给率、砂轮转速、工作台转速对硅片TTV的影响规律,分别对它们进行试验研究。
通过实验得出如下结果:
(1)当其它磨削参数不变时,硅片的TTV值随着砂轮进给率的增大而增大,且TTV值增大的很快。因为砂轮进给率增大而转速不变时,砂轮磨削深度增大,从而对硅片表面的切削力和挤压力也增大,单位时间内去除的材料增多,材料脆性断裂的趋势增大,损伤深度也增大。因此,为了降低硅片的TTV值,就要在一定范围减小砂轮进给率,不过这样会降低材料的去除率,延长了加工时间,增加成本。
(2)当其它磨削参数不变时,硅片的TTV值随着砂轮转速的增大而减小,这是因为随着砂轮转速的增大,砂轮每转的磨削深度减小,从而损伤深度也就减小。因此,为了降低硅片的TTV值,砂轮转速要最大化。但砂轮的转速并不能无限制地增大,一方面是由于磨床自身主轴性能的限制,另一方面与砂轮本身的强度也有关,砂轮转速增大,则砂轮轮齿受到的离心力也相应增大,对砂轮的强度要求也就越高。
(3)在其它磨削参数不变时,TTV值随着工作台转速的增大而减小,但是变化的幅度很小,相对于砂轮进给率和砂轮转速来讲,工作台转速对硅片TTV值的影响最小。
3 结 论
综上所述,砂轮进给率、砂轮转速、工作台转速对硅片TTV的影响巨大。因此,在晶圆磨削过程中,对砂轮进给率、砂轮转速、工作台转速等工艺参数的合理设置,有助于降低晶圆的TTV值,从而提高磨削后晶圆的表面质量。