摘要:本文阐述了硅晶片金刚线多线切割原理,并对自主研发的硅晶片多线切割机及其工艺作了介绍。
关键词:硅晶片 多线切割 金刚线 切割机 工艺
0 引言
随着世界常规能源供应短缺问题的日益严重和化石能源的大量开发利用造成的自然环境污染与人类生存环境恶化的问题日益突出,寻找新型能源已成为世界热点问题。在各种新能源中,太阳能光伏发电具有无污染、可持续、总量大、分布广、应用形式多样等优点,受到世界各国的高度重视。硅晶片不仅是微电子信息(IC 即Integrated Circuit)产业的重要元件,更是太阳能光伏(PV 即Photovoltaic)产业的重要元件。图1 表明,其国内外市场前景总体看好。
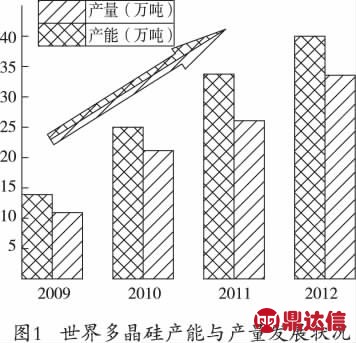
硅晶片的生产成本在整个光伏发电系统建造成本中占有相当的比例,严重制约着光伏企业的发展和光伏发电的商业应用步伐。硅晶片的生产加工一般是采用专用切割机床(多线切割机),以砂浆切割工艺方式进行加工生产。这种工艺生产效率不高,能源消耗较大,工艺辅料(切割砂浆和切割钢线等)用量多、环境污染严重。为改善上述不足,近年来,一种新型的硅晶片切割技术——金刚线多线切割工艺正悄然兴起,成为一种发展趋势。
1 金刚线多线切割原理
1.1 砂浆多线切割原理
为便于读者的了解,先介绍一下硅晶片砂浆多线切割原理。
硅晶片多线切割机的切割原理是:以高速运动的钢线为载体,以SiC 颗粒(砂浆)为切割刃,通过硅锭与钢线的相对运动实现对硅锭的切割加工,以获得一定几何形状的硅片(图2)。
缠绕在导轮上的切割钢线以13 m/s 左右的速度(切割速度)携裹砂浆做水平运动,硅锭则以(0.2 m/s ~0.4 m/s)的速度(进给速度)做垂直运动,从而实现切割。
切割钢线规格一般为φ0.10 mm ~φ0.18 mm,抗拉强度≥880 MPa,表面镀铜。钢线沿导轮轴线方向按一定的间距排布(实现多线切割)。
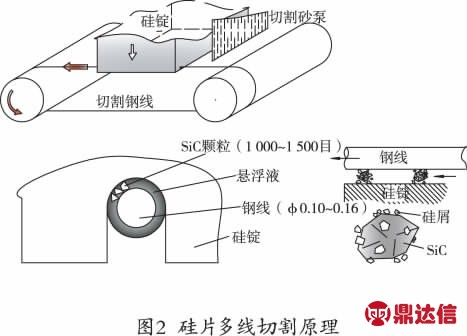
导轮直径一般为φ300 mm,长度520 mm,表面挂胶,按一定的几何形状要求开有沟槽。
砂浆是按一定比例的SiC 颗粒和悬浮液充分搅拌而配置的。SiC 形状为多菱体,颗粒度为1000 ~1500 目(图3)。悬浮液为油性介质。喷淋装置将砂浆喷淋到切割钢线上,并通过过滤系统重复使用(2-3 次)。
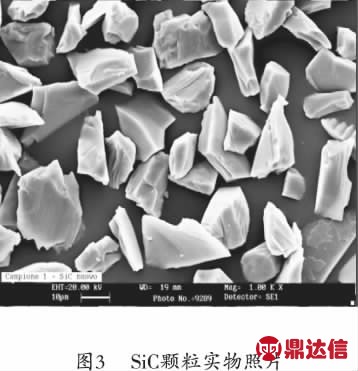
切割结束后,由于切屑(硅粉)混合于粘度较高的砂浆中,分离比较困难,造成原材料的浪费和对环境的污染。
1.2 金刚线多线切割原理
金刚线(图4)按其金刚颗粒的粘附方式的不同分为树脂金刚线(把持力低)、电镀金刚线(把持力高)和钎焊金刚线(生产难度较大)。由于电镀金刚线具有开刃和耐磨性能好,把持力强,切割速率快以及较为经济的等特点,目前用于硅晶片切割的一般都为电镀金刚线(以下除非特殊说明,本文所提及的金刚线均为电镀金刚线)。金刚线的线径为0.14 mm,母材直径为0.12 mm,破断力大于30 N。由于在电镀过程中会诱发拉应力造成母材脆化,所以在其生产过程中必须采取相应技术消除这种现象。
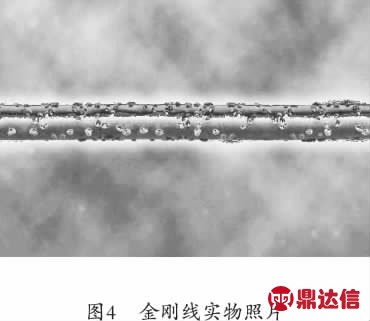
金刚线硅片多线切割原理则与之不同,它是以固接在母材(钢线)上的微小的金刚石颗粒(磨料)为切割刃具(俗称金刚线),金刚线高速运行(约12 m/s),通过硅锭与金刚线的相对运动,来实现切割的。砂浆切割是一个复合的磨削过程,金刚线切割则更接近于是一种刚性切削过程(图5)。
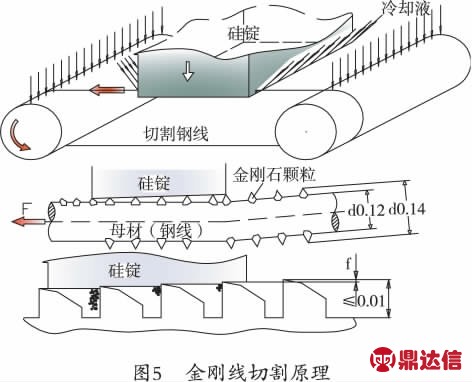
金刚线切割采用多进少退的进线方式,实现往复切割以节省金刚线的消耗,降低硅晶片制品的单位成本。返线率k 是指回线长度与进线长度的百分比,其值一般为90%≤k <100%。
金刚线切割所使用的导轮与砂浆切割使用的导轮类似开有多道沟槽以实现多线切割。但由于金刚线与普通砂浆切割所使用的钢线不同,所以对其沟槽等形式和尺寸有所不同。
金刚线切割过程中,必须采取一定的冷却方式对金刚线进行冷却(同时起到金刚线与硅锭之间的润滑和对金刚线上硅屑的冲刷作用)。冷却液一般采用低粘度的水溶性冷却液,切割完成后对切屑(硅屑)的回收处理较为容易,从而也就实现增效和节能环保的目的。
2 金刚线多线切割机的基本构造和特点
本文以笔者所在公司自行研发的金刚线多线切割机YL-DQ-T2156 为对象,对其基本构造和特点做一介绍。
2.1 机床性能指标
切割方式:正反
工件尺寸:156 mm×156 mm/125 mm×125 mm
可切割工件长度:480 mm
可切割工件数:2 根
切割工件层数:1
切割线直径:0.14 mm ~0.16 mm(指包络外径,母材直径0.12 mm ~0.14 mm)
切割线速度:Max12.5 m/s
返线率:85 ~97%
注:返线率k 的计算公式:
k=[反向回线长度/正向进线长度]×100%
切割线张力:15N ~30 N
工作台升降行程:Max200 mm
工件进给速度:0.2 ~0.6 mm/min
导轮数量-长度×直径:2—510 mm×280 mm
冷却缸容积:320L
冷却液流量:90 ~160 kg/min
冷却液温度控制精度:±1℃
最大负荷:100kW
冷却水(7-15℃)流量:2 m3/h
气压与耗气量:0.6 ±0.06 MPa/0.1 m3/min
外形尺寸:4 000 mm×2 060 mm×3 030 mm
总重量:12 000 kg
2.2 基本构造
T2156 按其功能区域划分为六个组成部分:
1)切割室(包括切割座、导轮、升降系统、硅夹持系统等,工件的切割在切割室内完成);
2)收放线室(包括收线轮、放线轮、张力控制摆轮、导轮等,张力控制在收、放线室完成);
3)冷却室(包括冷却缸等,提供硅块切割所需的循环冷却液);
4)水气路集成室(水路系统和气路系统分别提供设备各系统所需的机械冷却水和压缩空气);
5)电控柜(包括PLC 模块、电机驱动器、电源开关、接触器等电器控制元件);
6)机顶(包括质量流量计、板式热交换器等)。
其总体结构如图6 所示。
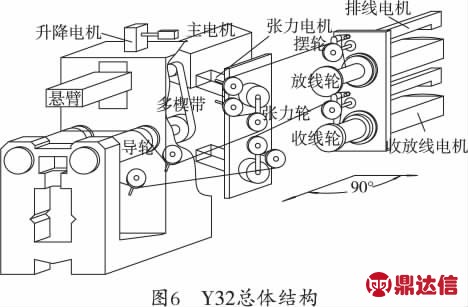
①金刚线缠绕在导轮上(按一定的间距开有沟槽)。主电机通过多楔带驱动导轮,从而带动金刚线做往复运动。
②硅锭装夹在悬臂上。升降电机通过丝杠副带动悬臂做上下垂直运动,以实现硅锭相对于金刚线之间的切割运动。
③放、收线轮分别由排线电机和收放线电机驱动。金刚线通过摆轮机构改变其运动方向,并通过进、出口处的两个张力轮(各自通过张力电机控制)调整金刚线切割过程中张力的大小。
④硅晶片的切割生产中,最为突出的质量问题是断线(即在切割过程中由于某种原因造成切割钢线断裂,造成切割中止)。一旦出现断线容易造成整块待切硅锭的报废,损失较大。即使人们仔细操作,重新将钢线焊接继续切割,硅晶片的质量也大打折扣,造成质量损失,况且金刚线的焊接十分困难。断线的原因是多方面的,钢线运行的平稳性是其一个重要原因。金刚线切割因为要往复运动,运行距离不能太长,否则容易出现跳线(即钢线脱离滑轮的轮槽),从而造成断线故障。T2156 在总体结构上采用了收放线轮与张力轮之间相互垂直的布线方式(图7),大大缩短了钢线的运行距离,从而为提高其运行质量创造了条件。同时使得设备的结构更加紧凑。
2.3 操作系统
T2156 采用了全汉化的操作界面,直观、简洁、易掌握。进入主界面(图8)即可对机器操作。主界面既可实时监控设备的运行情况,又可根据需要进入各个子界面对金刚线速度、工件进给速度、冷却液的供应量以及进线张力和出线张力的大小等相关工艺参数等进行重新设定、修改,或进一步细致地了解、检查设备详细的工作状况。
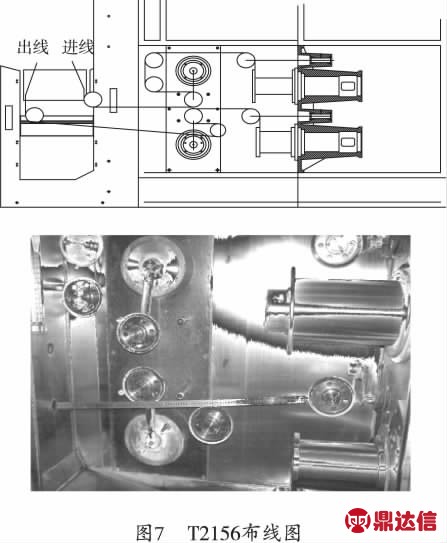
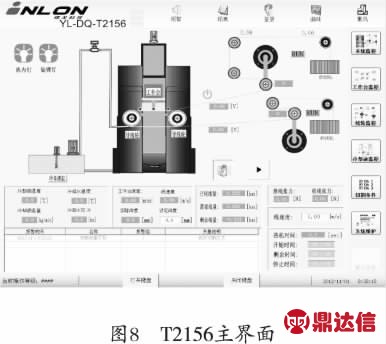
主要子界面(全屏)包括:①工件台界面;②线轮监控界面;③线轮高级参数界面;④冷却液监控界面;⑤切割准备界面;⑥系统监控界面;⑦配方界面;⑧实时曲线界面(图9)。
3 切割工艺
对于多线切割制片,其质量指标包括与原料冶炼有关的电化学指标(电阻率和少子寿命等),而与切割工艺有关的主要质量(形状)指标则包括:
1)总厚度偏差(Total Thickness Variation,简称TTV)——指切片的最大与最小厚度之差值,如图10(a)所示。对于光伏硅晶片,TTV≤0.04 mm。
2)翘曲度(Warp)——指切片中心平面与假想参考平面之间的距离(绝对值),与其厚度变化无关,如图10(b)所示。对于光伏制片,Warp≤0.10 mm。

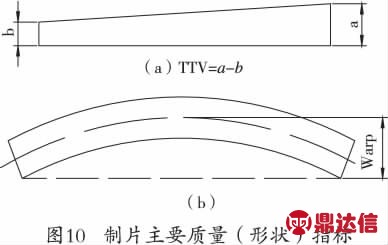
3)外观——切片崩边、缺口和线痕现象轻微。对于光伏硅晶片,容许存在小于0.5 mm 的崩边和缺口,线痕≤0.015 mm。
金刚线切割的主要工艺参数包括:①线速V;②台速S;③张力值F;④返线率K;⑤冷却液流量q 和⑥加速度a。其中影响TTV、Warp 和线痕的主要因素是线速V、台速S 和张力值F;用户应在厂家推荐的参数值基础上通过调试确定合适的工艺参数。
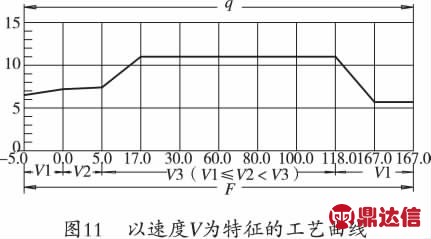
4 结语
金刚线多线切割由于其工效高、节能环保等优点,愈来愈为人们所重视。实践表明,该切割技术的推广目前还存在几个问题:一是金刚线制作成本较高;其次,切割杂质、位错密度较多的多晶硅块时断线风险较高;再者,与之配套的电池工艺中硅片清洗和制绒工艺要同步作出调整。随着技术的发展和环保意识的提高,相信不久的将来,金刚线多线切割一定会成为类似于光伏硅晶片这样的脆性材料切割加工的主流技术。