摘 要:针对300 mm单晶片清洗设备,设计开发了一套化学药液温度控制系统。由于化学药液传输系统具有大惯性、大时滞、非线性的特点,采用Smith预估法设计了一种温度控制算法;并基于可编程计算机控制器(PCC)设计实现了化学药液温度控制系统。介绍了该控制系统的硬件组成和控制算法设计,实验结果表明该温度控制系统能够满足清洗工艺需求。该系统现已成功应用于自主研发的300 mm、65 nm铜互连单片清洗设备。
关键词:化学药液传输系统;温度控制;Smith预估法;清洗设备
按照国际半导体技术发展路线图(ITRS)指 引,晶片尺寸进一步加大,器件特征尺寸不断缩小,造成晶片高集成化、器件结构超微小化,从而对晶片洁净程度、表面化学态、微粗糙度等提出更为严苛的要求。而一些新材料的使用和生产工艺的改变也给清洗工艺带来新的挑战,如Low-k材料的应用、更高的选择性、腐蚀的均匀性等要求。因而,高性能的晶片清洗设备是实现纳米级清洗的关键。
化学湿法清洗设备可分为批量槽式和单晶片清洗两种方式。与槽式清洗相比,单晶片清洗方式能有效避免晶片清洗的交叉污染,能够有效清洗晶片的背面、边缘,能够满足多品种小批量的清洗需求,具有清洗药液回收效率高,良品率高等优势。当主流工艺从90 nm发展到65 nm及以下工艺节点时,传统的槽式清洗方法已不能满足极大规模集成电路制造中关键步骤的清洗要求,单晶片清洗设备是大势所趋。
化学药液传输系统是单晶片清洗设备研制的关键系统之一,它为整个设备在线提供满足工艺需求的一定温度、压力、流量的化学药液,从而保证晶片表面腐蚀的均匀性和一致性。
在后道铜互连清洗设备等应用中往往由于化学药液昂贵的价格,需要将药液回收再循环使用以降低成本,而工艺处理中由于化学药液会喷淋在晶片表面,存在着药液与晶片本身以及与空气间的热交换,造成药液温度损失严重,导致回收的药液对化学药液供给管路的温度产生较大干扰;另一方面,不同工艺腔室分时进行工艺处理,时间不同步,回收药液的温度干扰具有不确定性,进一步增加了对化学药液温度控制的难度。
因此,为了实现对化学药液供给管路温度的稳定控制,本文针对化学药液传输系统具有大惯性、大时滞、非线性的特点,采用Smith预估法设计了一种温度控制算法;基于可编程计算机控制器(PCC)设计开发了化学药液温度控制系统,并通过实验验证了化学药液温度控制算法的有效性。
1 化学药液传输系统设计
北京七星华创电子股份有限公司研制的65 nm单晶片清洗设备主要用于铜互连后道工艺中多孔性Low-k介质材料的清洗,清除光刻胶残留、颗粒、通孔内的聚合物。而化学药液传输系统作为单晶片清洗设备的关键子系统之一,为整个设备提供工艺处理所需的化学药液、超纯水、高纯氮气、洁净干燥空气,并具有超纯水冲洗和气体干燥管路等功能。它主要由化学药液供给管路、超纯水供给管路、气体供给管路组成。
化学药液供给管路作为CDS系统的核心,包括化学药液存储罐、工艺泵、在线加热器、温度传感器、压力传感器、超声波流量计、各类阀件等,管路示意图如图1所示。
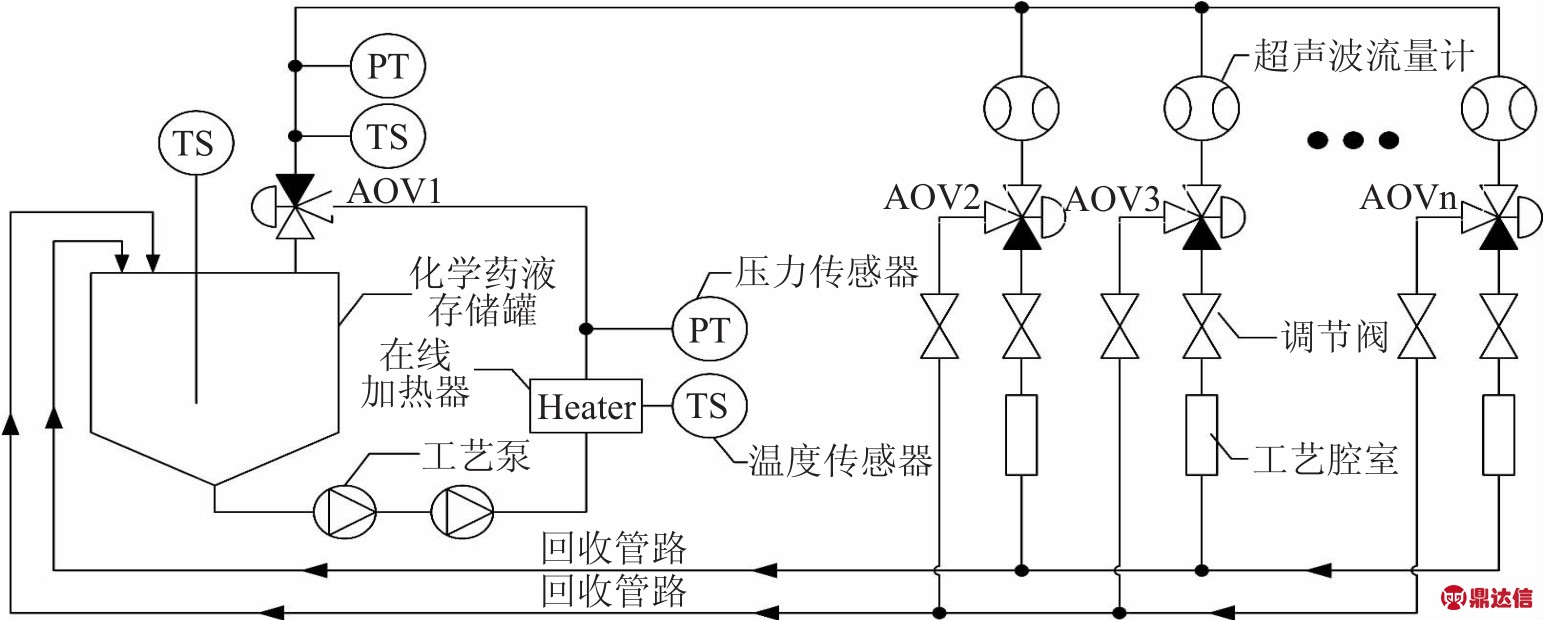
图1 化学药液供给管路示意图
为了缩短工艺等待时间,同时避免化学药液滋生细菌,化学药液供给管路具有本地循环和系统循环两路药液循环管路,两种循环管路的切换通过三通阀AOV1实现。在非工艺时间,化学药液供给管路中的药液通过三通阀AOV1的常开端回流入药液存储罐,在本地循环管路中循环流动,并预加热化学药液至工艺设定温度;在工艺时间,通过三通阀AOV1的切换,使得化学药液进入系统循环管路。当化学药液达到工艺温度,且化学药液供给管路的出口压力到达设定值,可以通过切换流向相应工艺腔室的三通阀AOV2~AOVn,使得药液通过工艺腔室的喷淋臂喷淋至晶片表面,参与清洗工艺处理。喷淋至晶片表面的化学药液再通过化学药液回收管路回流至化学药液存储罐,未作清洗工艺支路中的化学药液则通过化学药液回流管路回流至化学药液存储罐。
2 化学药液温度硬件控制系统设计
化学药液是湿法清洗的主要介质,用于清除晶片表面的光刻胶残留、颗粒、通孔内的聚合物。它的温度作为关键的工艺参数,直接影响到清洗效果。如果药液温度过低,其黏性增加,当低于特定温度时,化学药液中某些组份将处于惰性状态,不能有效去除聚合物;温度过高,则药液腐蚀性过强,造成对晶片的损伤,使得晶片氧化层及铜表面不平整。根据工艺需求,设定温度控制精度为设定值的±0.5%。
化学药液温度控制系统的硬件框图如图2所示。它主要由PCC控制器、SCR功率调节模块、在线加热器、温度传感器等组成。
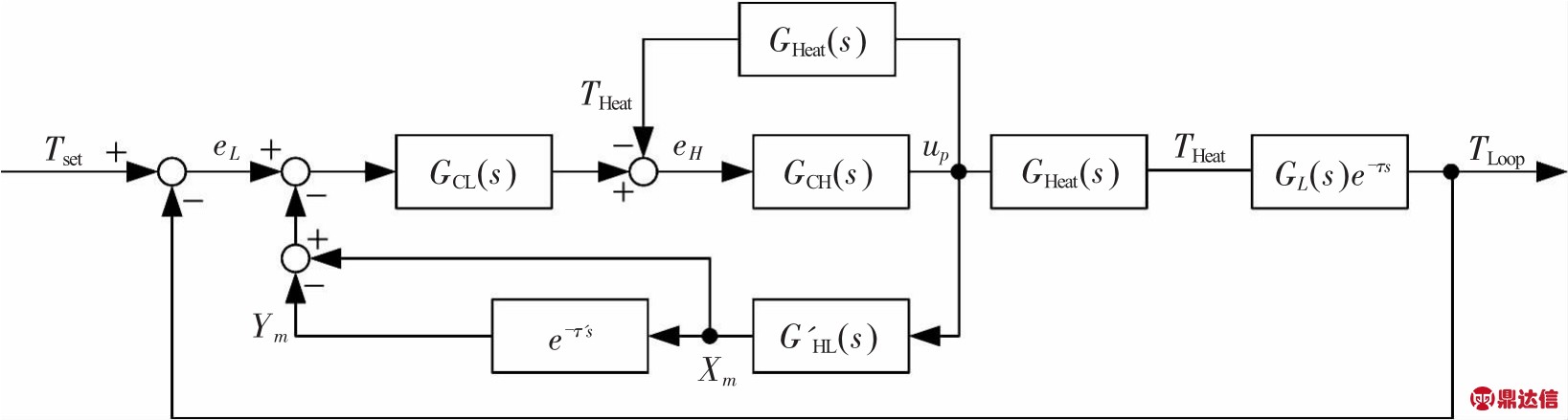
图2 温度控制系统硬件框图
各组成部分具体功能:
(1)PCC控制器:通过温度模块采集存储罐中化学药液的温度、管路出口化学药液的温度,通过AI模块采集加热器出口药液的温度,根据温度控制算法计算出加热器的输入功率,并由AO模块输出模拟控制量至SCR功率调节器以调节在线加热器的加热功率。
(2)在线加热器:在线加热器采用加热丝加热的方式,将混配好的化学药液加热至工艺需求温度。考虑到所使用的化学药液具有一定的腐蚀性,因此对在线加热器有耐腐蚀的要求,这与药液需要快速加热以缩短工艺准备时间的需求相互矛盾。具体而言,加热器产生的热量必须经过耐腐蚀性的特氟龙涂层后再传递给管道中的药液,而特氟龙涂层的导热系数较低,因此在选择加热器功率时,需要兼顾温度指标和升温速度。同时选择的在线加热器内部配有RTD热电阻温度传感器,用于检测其内部加热丝的温度并作为过温保护电路的输入。
(3)SCR功率调节器:通过4~20 mA控制信号的输入,经功率调节器控制串联在主回路中的SCR模块的通断,从而改变主回路供电电压的导通或关断,以达到调节电压或功率的目的。SCR功率调节器具体可分为调压器和调功器两类。
调压器采用相位控制模式调节电压的有效值。输出的电压波形呈正负半周对称,无直流成分,可直接用于感性负载。但是不规则的脉冲负载电流容易引起电网波形的畸变,造成对电网的冲击,同时对其他用电设备造成干扰。
调功器采用零位控制模式控制负载电压的周波通断比,从而控制负载的功率,常应用于阻性负载。采用该控制模式,可有效消除相位控制方式对电网波形和其他用电设备的干扰。
综合上述原因,本系统选用SCR功率调节器以零位控制模式工作。控制SCR功率调节器的控制信号由PCC控制器的模拟量输出模块给出。
(4)限温控制器:监测在线加热器内部加热丝温度传感器的值,当该值超过设定温度时断开接触器线圈,切断SCR功率调节器的交流输入。它作为硬件互锁控制单元,防止在线加热器过热损坏。
(5)温度传感器:用于检测化学药液供给管路出口药液温度、化学药液存储罐中混合回收/回流药液的温度。常用的温度传感器主要有4种类型:热电偶、热敏电阻、RTD热电阻和IC温度传感器。RTD热电阻是中低温区最常用的一种温度传感器,它的主要优点是测量精度高,性能稳定,典型的有铜热电阻、铂热电阻等,其中铂热电阻的测量精确度最高,误差一般在0.01%,被广泛应用于工业测温、标定基准仪。因此,本系统中选用铂热电阻PT1000作为药液温度测量传感器,其测量范围-50℃~260℃。
3 化学药液温度控制系统软件算法设计
本文所研究的化学药液温度控制系统具有大惯性、大时滞的特点,对于此类系统,如果采用常规的PID控制算法,系统容易出现超调量大、稳定性差的问题。因此,文中基于PID串级控制结合Smith预估补偿 [1,2]设计了化学药液温度控制算法。此算法采用管路出口药液温度作为外环反馈,采用加热器出口药液温度作为内环反馈。另外,化学药液在管路传输及工艺过程中存在与传输管路、晶片本身及室温空气的热交换,造成回收或者回流至存储罐中药液温度的下降,对管路出口药液的温度产生干扰;同时,在同一时间段,清洗设备会有不定数量的工艺腔室进入药液清洗工艺造成回收药液温度衰减扰动的不确定性,为此文中采用存储罐中化学药液的温度作为前馈补偿,以缩短系统的响应时间。所设计的温度控制算法具体为:
定义THeat为加热器出口药液温度,TLoop为管路出口药液温度,TTank为化学药液流经各支路回收或者回流至存储罐时的温度,Tset药液的工艺设定温度。
为了提高温控系统的快速响应性,采用THeat为内环控制的反馈量,通过调节加热器输入功率,使得加热器出口的化学药液温度快速跟随前级的输出设定值。内环控制主要起快速随动控制作用,允许存在稳态误差,因此,基于比例调节器设计了内环控制器GCH(s)其具形式为:

其中:比例系数K1通过对加热器内环整定得到。
定义GHeat(s)为加热器输入功率至加热器出口药液温度的传递函数。定义GLoop(s)为加热器出口药液温度到管路出口药液温度的传递函数,可表达为:

其中:GL(s)为被控对象不含纯滞后环节的传递函数,τ为纯滞后时间。由于纯滞后时间τ的存在,使得被控量不能及时反应系统所受扰动,造成系统超调明显,调节时间延长,系统稳定性降低。
定义GUL(s)为加热器输入功率至管路出口药液温度的传递函数,可表达为:

为了改善滞后性对控制的影响,在反馈回路中并联一个Smith补偿回路,以减少滞后环节的影响,与被控对象并联的Smith补偿环节的传递函数为:

系统开环传递函数可以表示为:

其中:up为加热器的输入功率。
基于Smith补偿的串级控制系统闭环传递函数为:

其中:GCL(s)为外环控制器的传递函数,GH(S)为内环闭环传递函数,即:
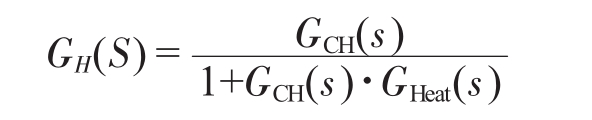
由此可见,若系统模型精确,则系统经Smith补偿后,传递函数的特征方程不含纯滞后环节e-τs,系统不会受纯滞后的影响,从而提高了系统的控制性能。
本文采用一阶纯滞后环节来拟合温控对象,即:

设阶跃输入幅值为△u,则增益K2可按下式求取。根据阶跃响应曲线开始出现变化的时刻来确定延时时间τ。截去纯延迟部分,并化为无量纲形式的阶跃响应TLoop(t),即
利用[t1,TLoop(t1)]和[t2,TLoop(t2)]来确定时间常数t2,则可得到温控对象的传递函数。但所得到的传递函数不是被控对象的精确模型,不同流速下传输化学药液的热量损失不同,增益、惯性时间常数以及纯滞后时间会有所变化,但在同一流速下纯滞后时间常数相对稳定,可以保证Smith预估器对滞后性的有效补偿。
本文采用PID控制方法设计外环控制器GCL(s),其具体形式为:

其中:比例系数K3、积分时间常数T3及微分时间常数Td通过对加热器内环整定完成后对外环整定得到。基于Smith补偿的串级温度控制框图如图3所示。
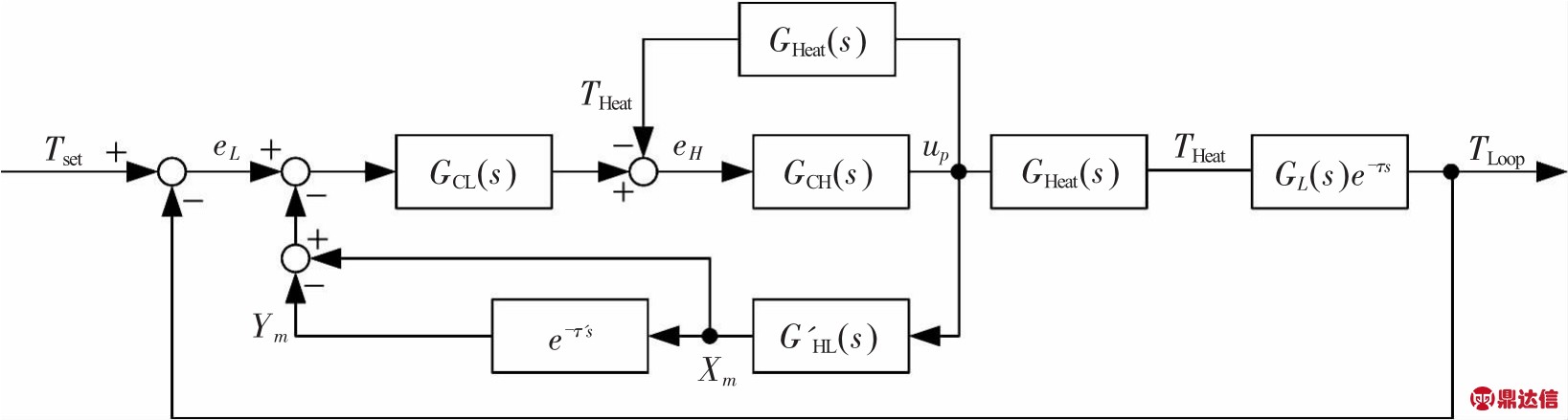
图3 基于Smith补偿的串级温度控制框图
为了补偿化学药液在管路传输及工艺过程中的热量损失造成对管路出口药液温度的扰动,本文根据化学药液存储罐中的药液温度设计了前馈控制器GCT(s),以提高系统的响应速度,具体形式为:

其中:比例系数K4和积分时间常数T4通过试验试凑得到。
整个温控系统的控制框图如图4所示。
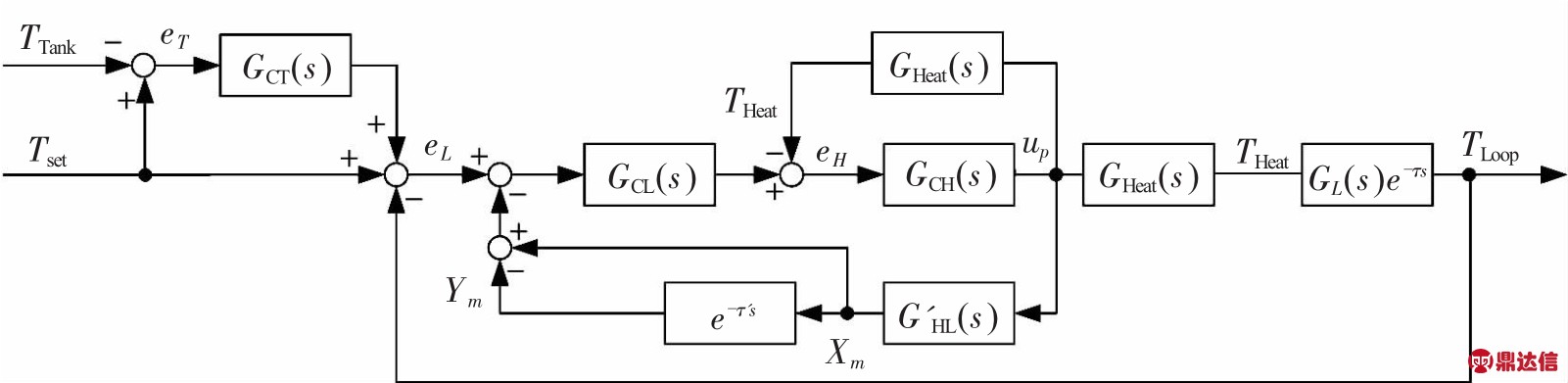
图4 温度控制系统控制框图
具体算法实现时,采用带死区的PID控制方法[3],即在偏差较大时,使得加热器以大功率快速加热,提高温升速度;当偏差较小时,基于Smith预估补偿采用PID调节器进行闭环控制。
4 温度控制实验结果
在所研发的65 nm单晶片清洗设备上对上述温度控制算法进行了实验。实验中设定管路出口化学药液温度为40℃,化学药液供给管路的出口压力为65.5 kPa,此时工艺泵的运行速度为3 335 r/min左右。化学药液温度控制的实验结果如图5所示。实验数据表明采用Smith预估补偿控制方法可以将管路出口化学药液温度控制在±0.2℃以内,调节时间约在8 min左右,基本满足控制要求。
虽然此温度控制系统能够满足系统控制指标,但是该控制方法的控制效果依赖于温控模型的精确性,而不同流量时热量传导模型不同,造成系统纯滞后时间存在差异,将会影响控制效果。因此,该控制方法存在一定局限性,对流量扰动的抗干扰能力稍显不足,需要进一步加以研究。
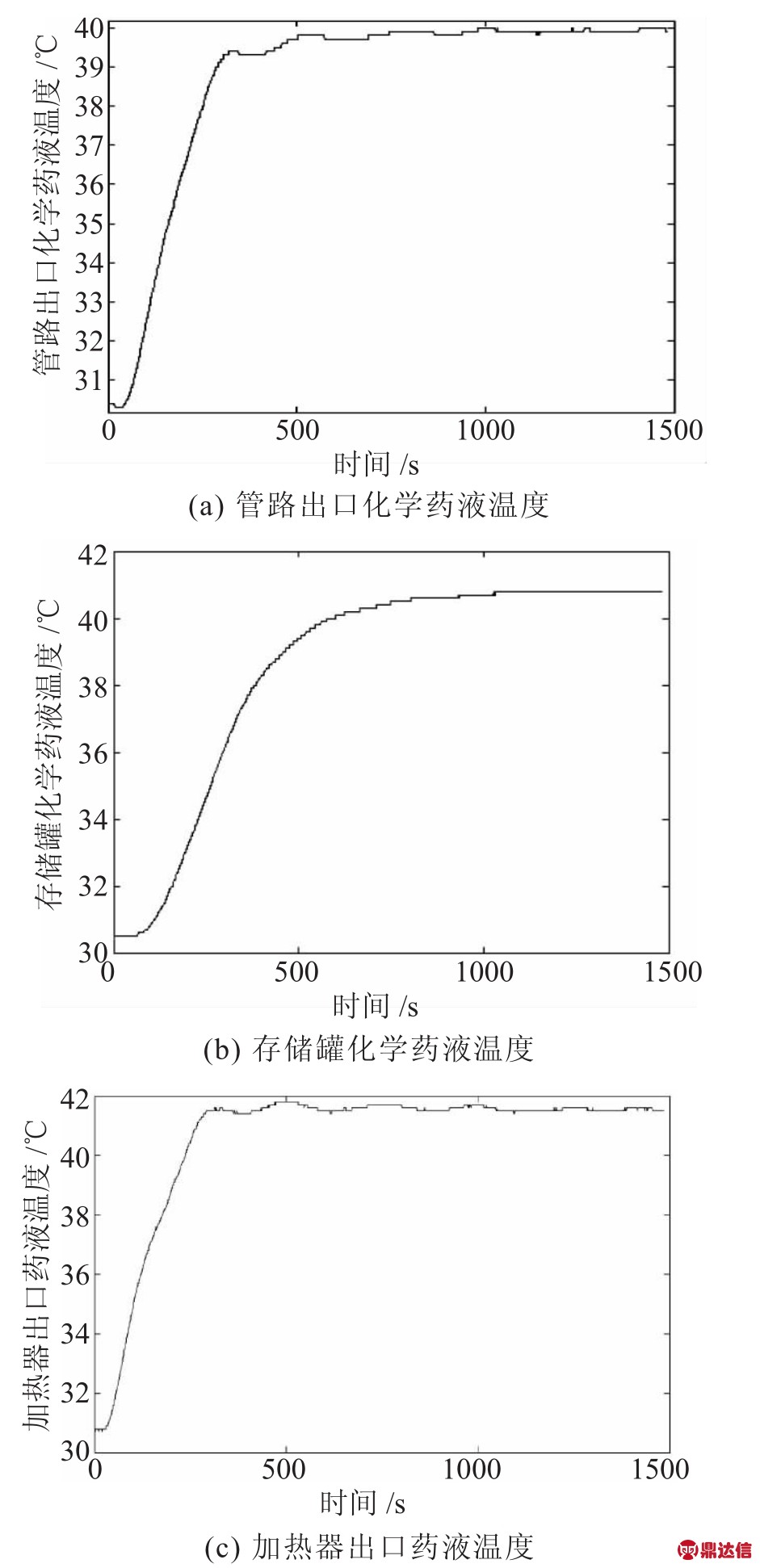
图5 温度控制曲线
5 结 论
本文设计了一种应用于65 nm单晶片清洗设备的化学药液传输温度控制系统。针对管路化学药液温度控制的要求,提出了一种基于Smith预估补偿的串级温度控制方案。在所研制的65 nm单晶片清洗设备上采用了文中设计的化学药液温度控制系统,并在此设备上通过实验验证了药液温度控制方案的有效性。从实验结果可以看出,所设计的控制系统能够满足清洗工艺对化学药液压力、温度的控制精度、响应时间及稳定性的要求,从而为提高设备的工艺效果奠定了良好的基础。