摘 要:为了解决交通信号支撑结构疲劳裂纹扩展的问题,利用ANSYS软件对已有的信号支撑结构静力和疲劳试验分别建模分析,并用有限元结果与试验结果进行对比。研究表明:静力加载模型中,圆钢管上最大Mises应力为413.7 MPa,有限元结果与试验结果较为接近;裂纹最深点ΔKII和 Δ K I II 值较小, Δ K eff与ΔKI几乎完全相等,裂纹扩展寿命主要受ΔKI值的影响;远离裂纹端点处各点的ΔKI值呈现出M形状;Bowness公式计算得到的裂纹最深点的ΔKI值比有限元结果大,利用该公式预测交通信号支撑结构端板与圆钢管焊接节点的疲劳寿命较为保守。
关键词:裂纹扩展;有限元;静力加载;疲劳试验;应力强度因子
交通信号支撑结构主要用于支撑信号灯、指示牌等交通信号工具,一般由长细比较大的悬臂钢结构构件所组成[1]。风荷载是信号支撑结构所承受的主要荷载,在长期风荷载作用下,该支撑结构容易产生疲劳破坏。
美国的交通信号系统与我国相比使用较早,在常年风荷载的作用下,大量的支撑结构已经发生了的疲劳破坏,造成了一定的经济损失和人员伤亡。因此,从 20世纪八、九十年代开始,美国学者对于交通信号支撑结构的疲劳性能[2]、阻尼减震装置以及风荷载数据等进行了大量的研究。而我国对于交通信号支撑结构的力学性能研究较少。
目前,世界各国对于钢结构疲劳问题均以构造类别S-N曲线为主要的疲劳设计方法[3],然而随着断裂力学以及有限单元法的发展,用有限元方法对钢结构疲劳裂纹扩展寿命进行预估已逐渐成熟[4-5]。
圆钢管是交通信号支撑结构中最常用的结构形式,本文基于已有的带焊缝端板圆钢管结构试件的静力和疲劳试验数据[6-7],利用ANSYS软件进行模拟。由于ANSYS的APDL程序语言可以自动完成不同裂纹深度和长度有限元模型的建立,因此非常适合解决疲劳裂纹扩展的问题。然后,用有限元计算结果与试验结果进行对比,验证利用有限元软件对交通信号支撑结构疲劳裂纹扩展问题进行研究。最后,用有限元计算的应力强度因子结果与Bowness公式计算结果对比,考察Bowness公式对于交通信号支撑结构的适用性。
1 试验简介
圆钢管与端板焊接的静力和疲劳试验在马里兰大学帕克分校结构实验室完成。试件以及焊脚尺寸见图 1。该试件的设计与马里兰州通用的交通信号悬臂结构设计相符,为1∶1足尺试件(仅长度方向截断为靠近端板的1.5 m段)。其中,采用了锥型钢管,圆管直径均匀变化,与端板连接最外侧的外径为 254.0 mm(10英寸),左侧加载端外径为236.2 mm,钢管厚度为 6.35 mm。圆管的长度为1524 mm(5英尺),与水平面的夹角为3°。端板高度为457.2 mm,宽度304.8 mm,厚度50.8 mm。钢管与端板在内外两侧采用角焊缝连接。
总共设计了6组试件,WTJ1~WTJ6,圆钢管均采用ASTM A572钢材,端板采用ASTM A36钢材。首先利用螺栓将端板固定在反力架上,然后用MTS液压伺服加载系统作动器在左侧端部对钢管向下加载,加载如图2所示。加载分为两步:静力加载和疲劳加载。静力加载中,每个试件均加载至29 kN,然后卸载。疲劳加载的极值见表1,荷载幅恒定,当裂纹扩展到最后的破坏阶段停止加载。
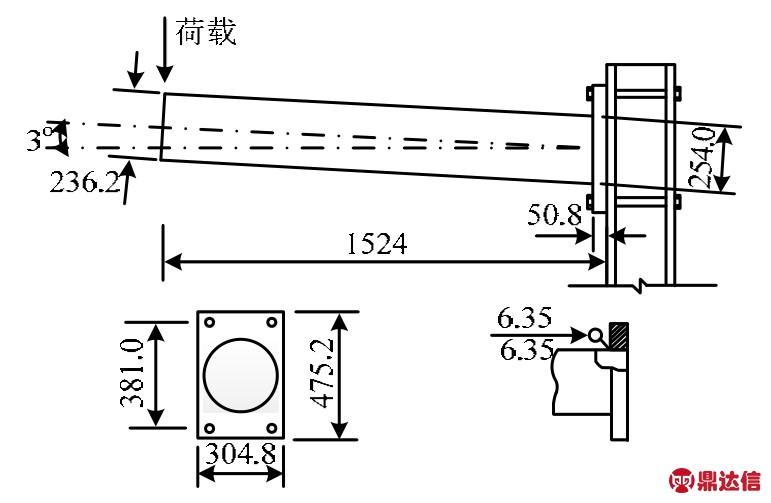
图1 试件及焊缝尺寸 /mm
Fig.1 Specimen and weld dimension
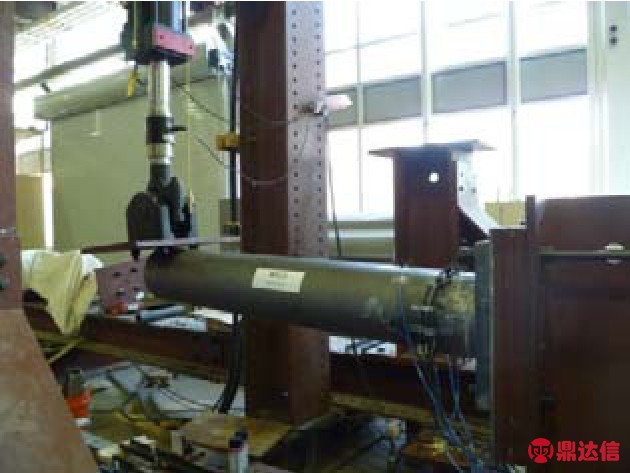
图2 加载装置
Fig.2 Loading device
表1 加载极值和幅值
Table1 Extreme and range values of the load
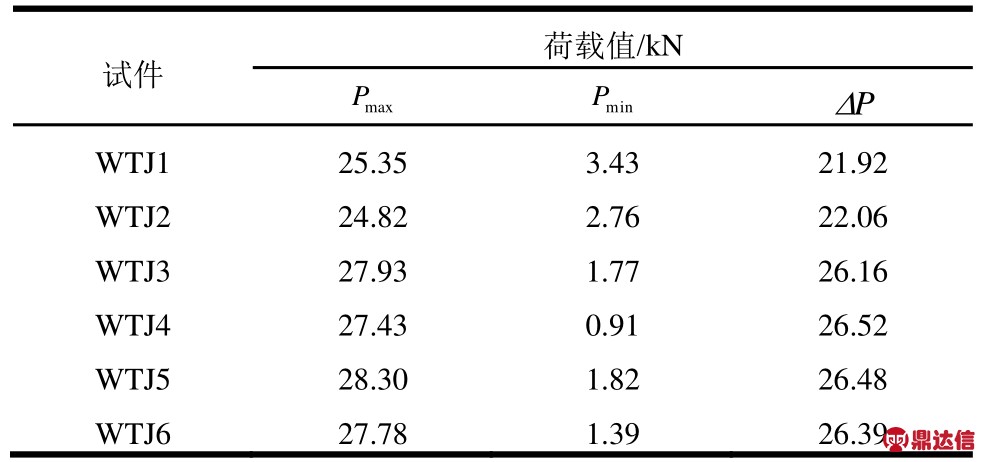
试验中采用应变片测量应力值,应变片的布置见图3。应变片SG1、SG3、SG4、SG5位于截面A上,截面A与角焊缝焊趾的距离为3.84 mm,其中SG1位于顶部。SG2也位于圆管顶部,但是与焊趾的距离为14.06 mm。SG7、SG8、SG9、SG10位于截面B上,该截面与焊趾的距离为305 mm。以上应变片均沿着圆钢管长度方向布置,测量纵向应变,而SG6则位于截面A和截面B之间,测量环向应变。
由于WTJ1、WTJ2、WTJ3试验主要是为了尝试不同的裂纹探测技术,并且摸索不同的加载控制方法,因此在与有限元结果对比时,不考虑WTJ1~WTJ3的试验结果。后文的静力加载有限元模型仅与WTJ4~WTJ6的结果进行比较。对于疲劳裂纹扩展有限元结果,仅与WTJ5试验结果进行比较。
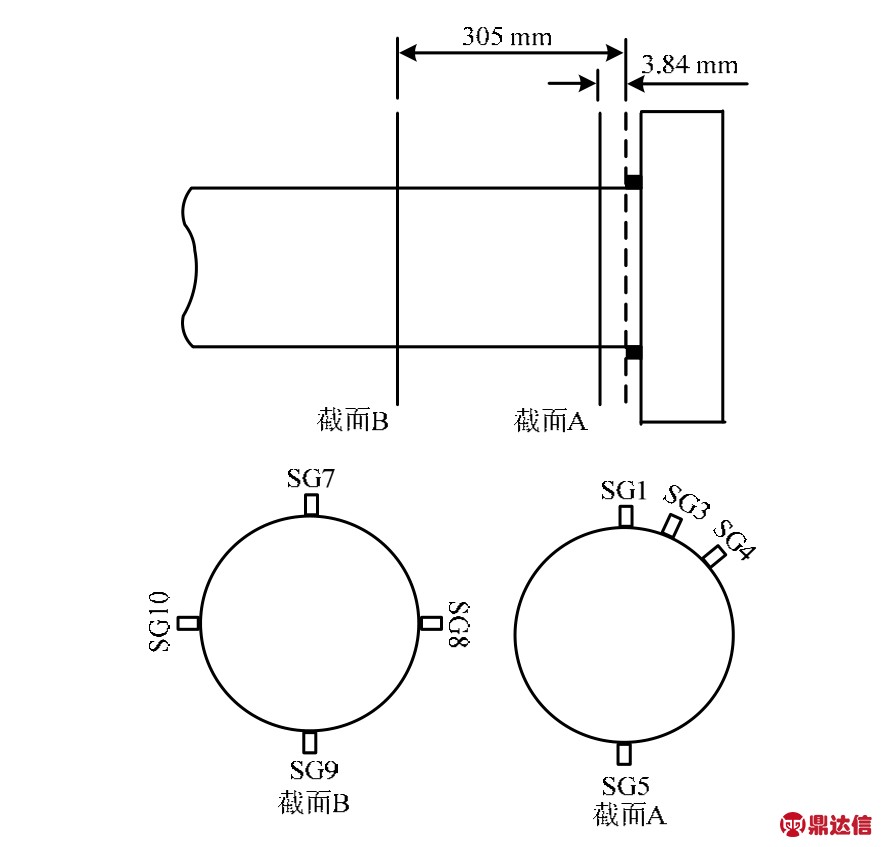
图3 测点布置
Fig.3 Measuring points layout
2 疲劳裂纹扩展模型
2.1 裂纹扩展假定
裂纹往往出现在应力最大的区域,从试验结果来看,试件的裂纹均出现在圆钢管顶端的焊趾处,并且沿着横截面扩展。对于裂纹深度与半裂纹长度的关系(见图 4(a)),本文采用 Vosikovsky等[8]对焊接T型节点疲劳裂纹扩展所提出的模型:

其中:
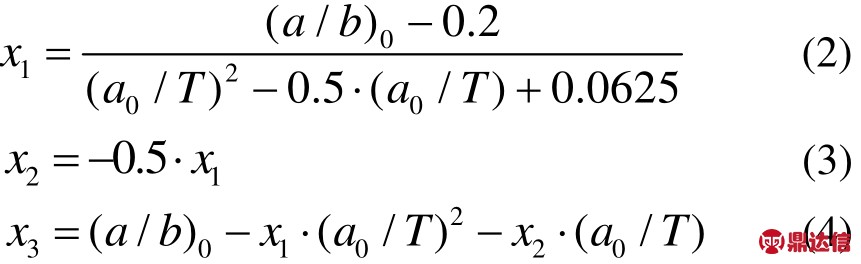
式(1)~式(4)中:T为圆钢管厚度,值为 6.35 mm;(a/ b)0为初始裂纹深度a与半裂纹长度b的比值,对于WTJ5试件,该值为0.4879;a0为初始裂纹深度,值为0.1860 mm。从图4(b)可以看出,在WTJ1试件中,当裂纹深度为 6 mm时,半裂纹长度为31 mm,因此a/ b的值接近于 0.2。此外,观察到的裂纹尖端的形状为圆弧型,因此在后文的有限元建模中,裂纹尖端依然采用圆弧型。
疲劳裂纹扩展的极限裂纹深度也是考虑的重点,有研究表明:初始裂纹扩展阶段对于圆钢管的疲劳寿命影响较大,而最终的临界阶段对于疲劳寿命影响较小[9]。同时,由于本文关注的是裂纹扩展中第二阶段,即线弹性断裂力学适用阶段,因此,本文取用0.9T(5.715 mm)作为疲劳裂纹扩展的极限深度[7]。
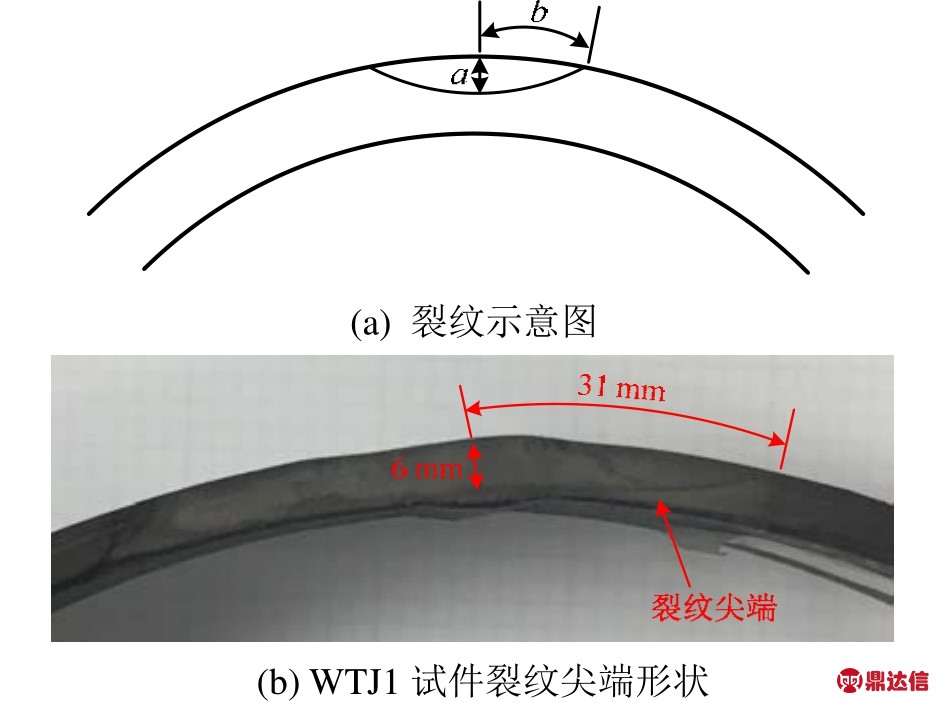
图4 试件中表面裂纹
Fig.4 Surface crack on specimen
2.2 裂纹扩展公式
本文采用Paris公式进行疲劳裂纹寿命的计算,公式如下:

式中:a为裂纹深度;N为疲劳寿命;C和m为材料参数; Δ K e ff 为裂纹尖端等效应力强度因子范围。Keff的表达式为:

式中:v为泊松比;KI、KII和KIII分别为I型、II型和III型裂纹尖端应力强度因子。
由于ANSYS软件无法直接模拟三维裂纹扩展的问题,因此本文的思路是:将裂纹扩展过程分为若干个子步,求解每一个子步裂纹尖端最深点的应力强度因子幅值 Δ K e ff ,利用 Δ K e ff求解此步的荷载循环次数,然后更新裂纹长度,并且重新建立有限元模型,直到最终裂纹扩展至深度为 5.715 mm为止。本文采用的裂纹深度增量约为0.2 mm,当增量足够小时,可假定在每一步内应力强度因子不变),因此裂纹扩展速率恒定,Paris公式变为:

根据此公式可求得下一步荷载循环次数Ni+1。
3 有限元模型
与试验一样,有限元模拟也分为两个部分:静力试验模拟和疲劳裂纹扩展模拟。其中,静力试验模拟主要是为了验证该有限元模型的可靠性。
3.1 静力加载模型
焊缝对于模型的计算结果影响很大,焊趾处一般会产生应力集中,因此该处的应力往往最大。端板左侧与圆钢管连接的角焊缝对模型计算结果会有显著的影响,此处的建模应该精细。然而,端板右侧与钢管端部连接的焊缝只是起到固定钢管的作用,为了简化有限元模型,将距离钢管端部7 mm以内的部分与端板连接来模拟等效焊接连接,简化过程如图5所示。
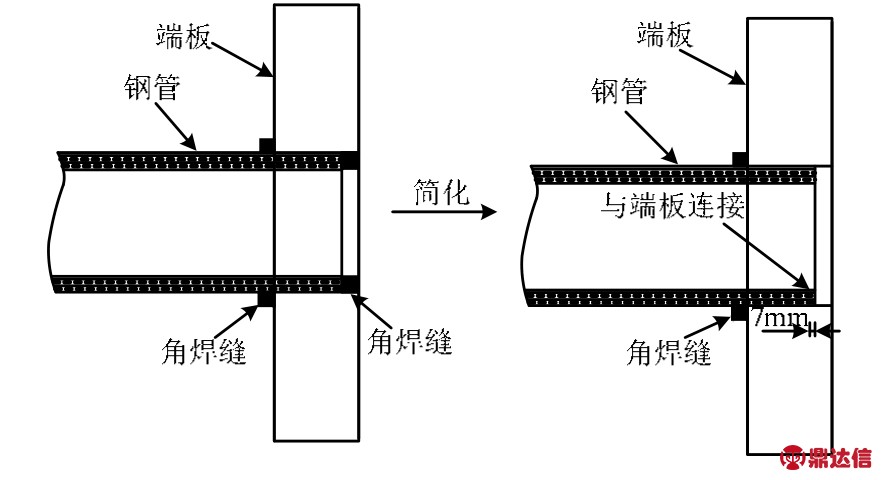
图5 焊缝的简化
Fig.5 Weld simplification
钢管及焊缝均采用ASTM A572材料,本构关系选用双线性模型。弹性模型取为 200 GPa,泊松比为0.3。屈服强度取为453 MPa,塑性阶段的切线模量为620.32 MPa[10]。端板不是本文关注的重点,因此仅采用线弹性本构模型,其弹性模量为200 GPa,泊松比为0.26。
模型中采用两种单元:Solid186和Solid187。Solid186为20节点三维实体单元,每个节点有三个自由度,该单元能很好地模拟应力集中。因此,对于角焊缝附近的区域,采用Solid186单元。Solid186有四种形式:六面体、棱型、金字塔型、四面体。由于本文的试件结构形式不规则,采用六面体、棱型以及金字塔型的单元难以均匀地划分网格,因此选用四面体单元。Soild187是 10节点三维实体单元,该单元只有一种四面体形式。对于远离焊缝的区域,采用此单元进行模拟。
静力加载模型的网格划分见图 6。图 6(a)中边界条件的施加是通过将端板上与螺栓连接处整个横条区域所有节点的自由度进行约束来实现。为了模拟作动器提供的竖向荷载,将钢管加载端所有节点y方向的自由度进行耦合,然后在其中一个节点上施加点荷载。图6(b)为焊缝处网格,此处会产生应力集中,因此网格更密。最终,Soild186单元数量为12981,Solid187单元数量为76530,节点总数为164255。焊缝处Solid186四面体单元的边长约为3.84 mm。
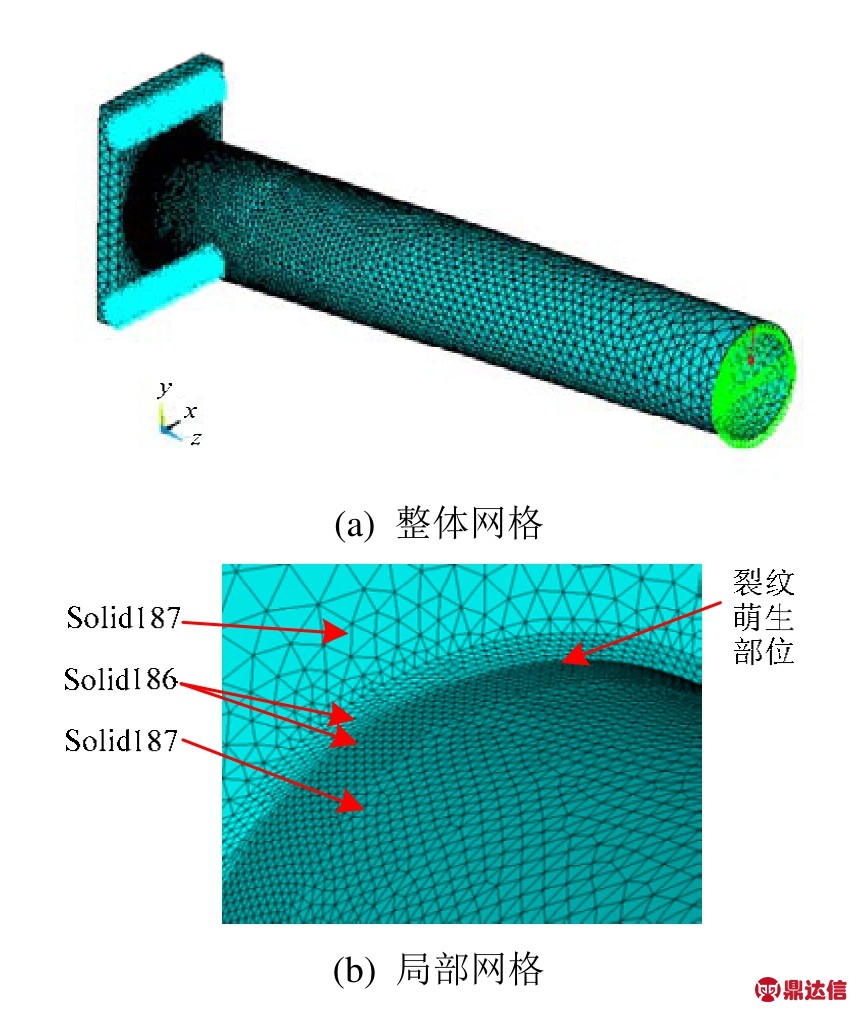
图6 静力加载模型网格划分
Fig.6 Mesh partition for the static model
3.2 疲劳裂纹扩展模型
由于ANSYS软件计算应力强度因子时规定使用线弹性本构模型,因此本文的疲劳裂纹扩展模型中的材料属性均为线弹性。
模型中使用的单元依然为Soild186和Soild187单元,但是与静力加载模型相比,疲劳裂纹扩展有限元模型多了裂纹尖端附近单元的建立。裂纹尖端附近单元环如图7(a)所示,裂纹尖端实际上是由一组节点所组成,位于单元环的中心。该环型体单元是用VSWEEP命令来建立,半径约为0.4 mm。与单元环最外一侧连接的是四面体单元,见图7(b)。裂纹深度为1.4 mm和3.0 mm时裂纹附近的网格划分分别见图7(c)和图7(d)。
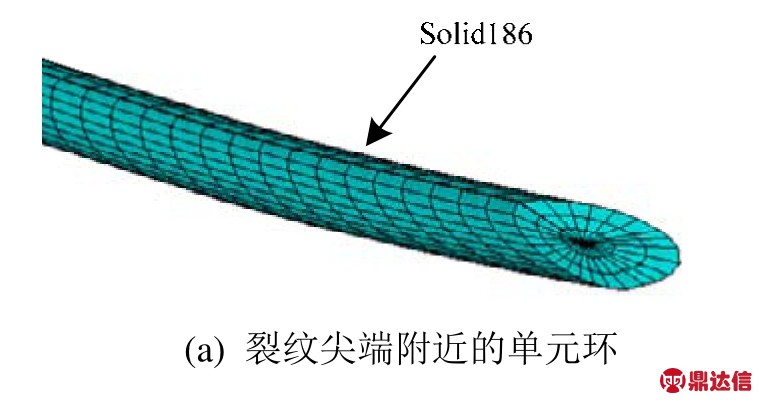
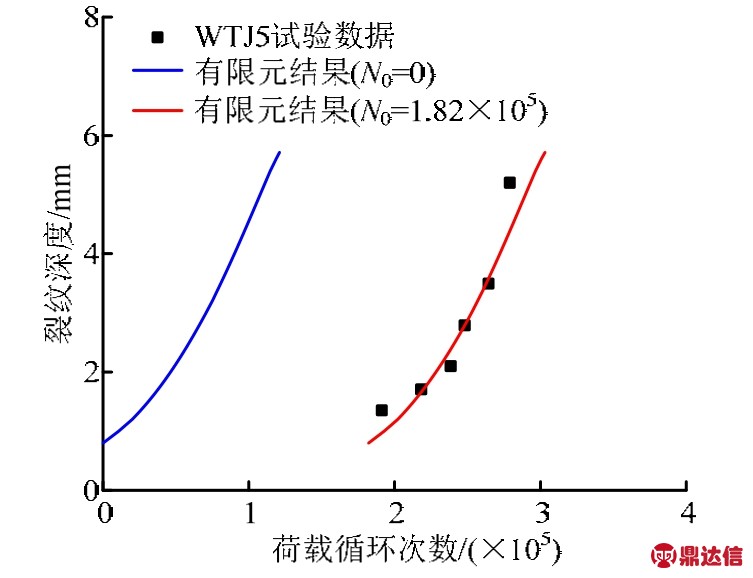
图7 疲劳裂纹扩展模型网格划分
Fig.7 Mesh partition for the fatigue crack gowth model
ANSYS中提供了两种计算应力强度因子的方法:交互积分法(Interaction integral method)和位移外推法(Displacement extrapolation method)[11]。位移外推法为传统的计算方法,是在求解之后计算应力强度因子。该方法往往需要更多的网格,并且其精度依赖于1/4节点的建立。对于平面二维模型,一般可以用KSCON命令建立1/4节点,然而对于三维模型,建立1/4节点往往非常困难。相比之下,使用交互积分法计算更加精确,不依赖于1/4节点的建立,而且使用方便。利用CINT命令,可以定义裂纹参数,其中包括选定计算轮廓值的数量。该方法选用远离裂纹尖端的节点来进行轮廓积分。选取应力强度因子计算值时,建议去掉第一个轮廓值,因为第一个轮廓值的积分路径靠近裂纹尖端,其精度比其他值要低[11]。
4 有限元计算结果
4.1 静力计算结果
静力计算整体Mises应力云图见图8(a),焊缝处局部应力云图加图 8(b)。由图可知,最大 Mises应力出现在焊趾处,为 413.7 MPa。圆钢管上远离焊缝的区域,应力几乎成线性变化,符合悬臂构件的加载特点。
根据计算结果,可以得到模型中任意一点的三维应力状态,从而可以计算出与应变片所测方向相同的应力大小。有限元计算结果与试验结果的对比见图 9,为了简明起见,本文只对比了部分测点。由图可知,试验结果表现出了一定的离散型,但总体上来说,有限元计算结果与试验结果吻合度较高。测点SG7和SG9位于B截面,远离焊缝,该处的有限元结果与WTJ4~WTJ6试验的平均值非常接近。测点SG1位于圆管最上端接近焊趾处,该处的有限元计算结果与WTJ4和WTJ6试验结果非常吻合,稍大于WTJ5试验结果。测点SG4的有限元结果比试验结果均稍大一些,但仍在可接受的范围之内。
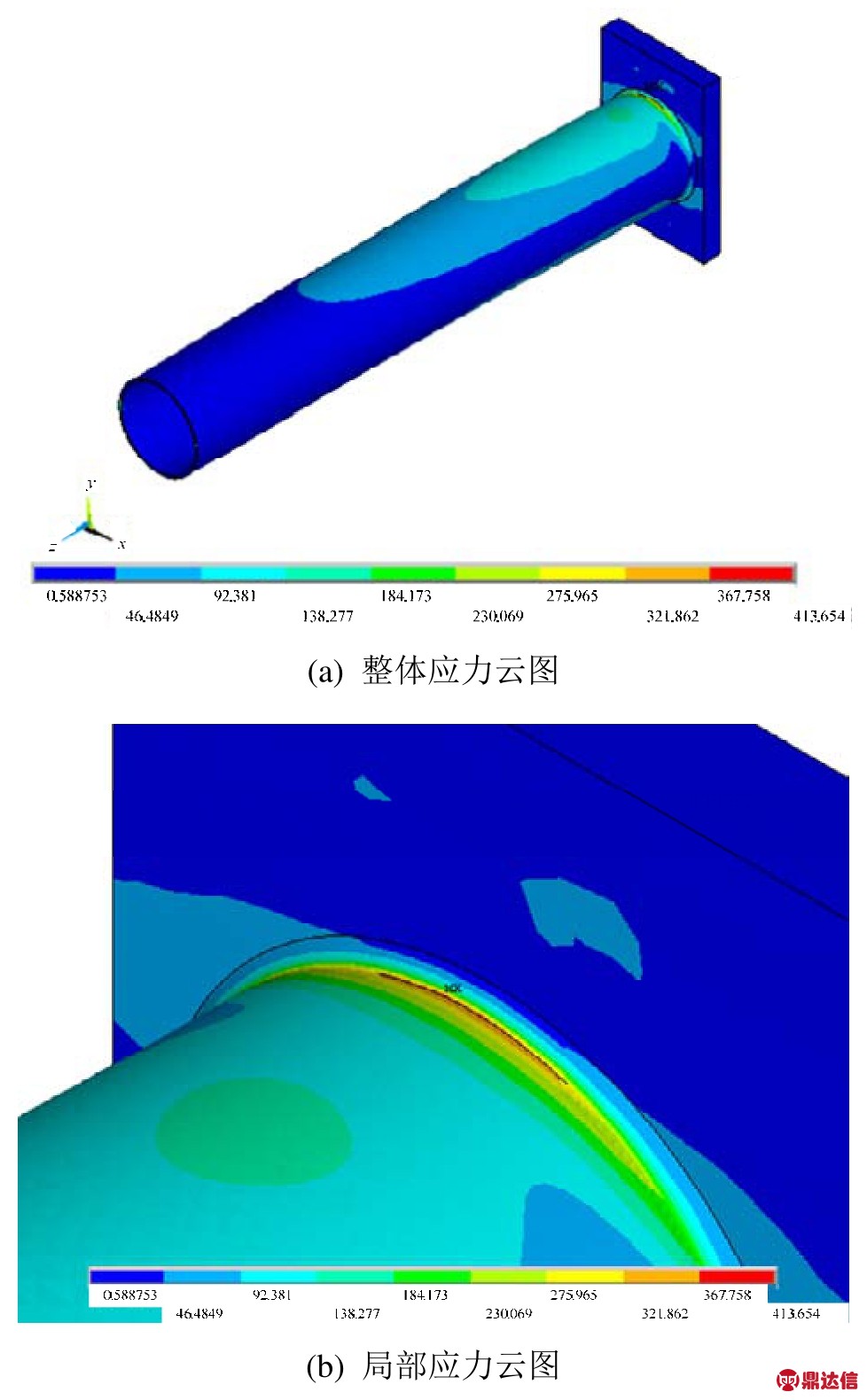
图8 静力加载模型Mises应力云图 /MPa
Fig.8 Mises stress contours for the static model
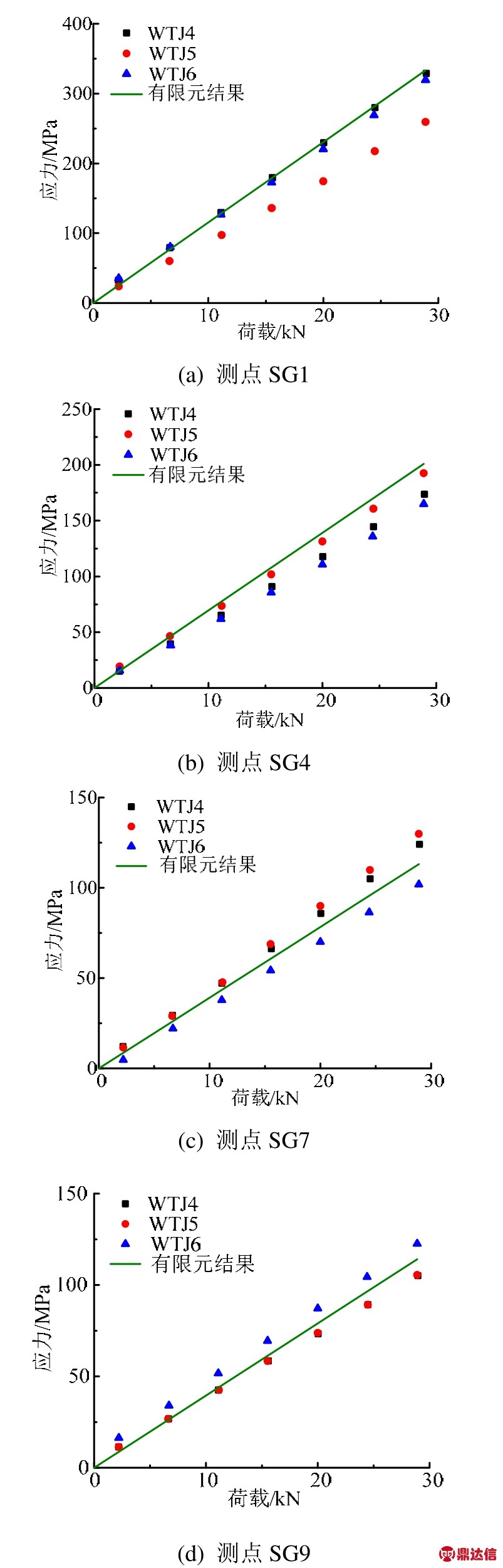
图9 静力加载模型试验与有限元结果对比
Fig.9 Comparison between the static test and FE results
4.2 疲劳裂纹扩展计算结果
为了方便后文的描述,本文定义了裂纹尖端角度φ,见图10。当裂纹深度为4 mm时,裂纹附近的 Mises应力云图见图 11(a),裂纹尖端不同点的ΔK I 与φ/π的关系见图11(b)。从图11(a)可以看出,由于模型中定义的材料属性为线弹性,模型中的最大Mises应力为1289.9 MPa,远超过了ASTM A572钢材的屈服强度,但是屈服面积较小,属于小范围屈服。从图11(b)可以看出,在远离裂纹尖端的区域,应力强度因子的变化较为规则,并且呈现出 M 形状。然而,在裂纹端点处其应力强度因子的值会产生突变,这种突变型是由端点的边界约束效应所造成的[12]。已有学者指出[13]:在裂纹端点与自由面的交界处,应力强度因子的平方根奇异性不再有效,因此利用J积分或者位移外推法计算出的应力强度因子结果不准确。由于本文主要关注裂纹最深点的应力强度因子,因此对于裂纹端点的应力强度因子暂且不做深入的研究。
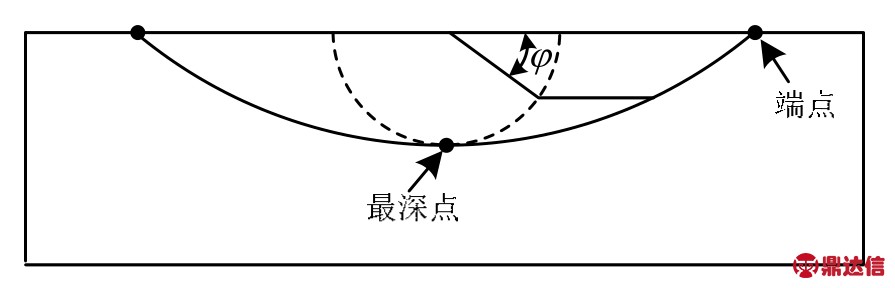
图10 角度φ的定义
Fig.10 Definition of angleφ
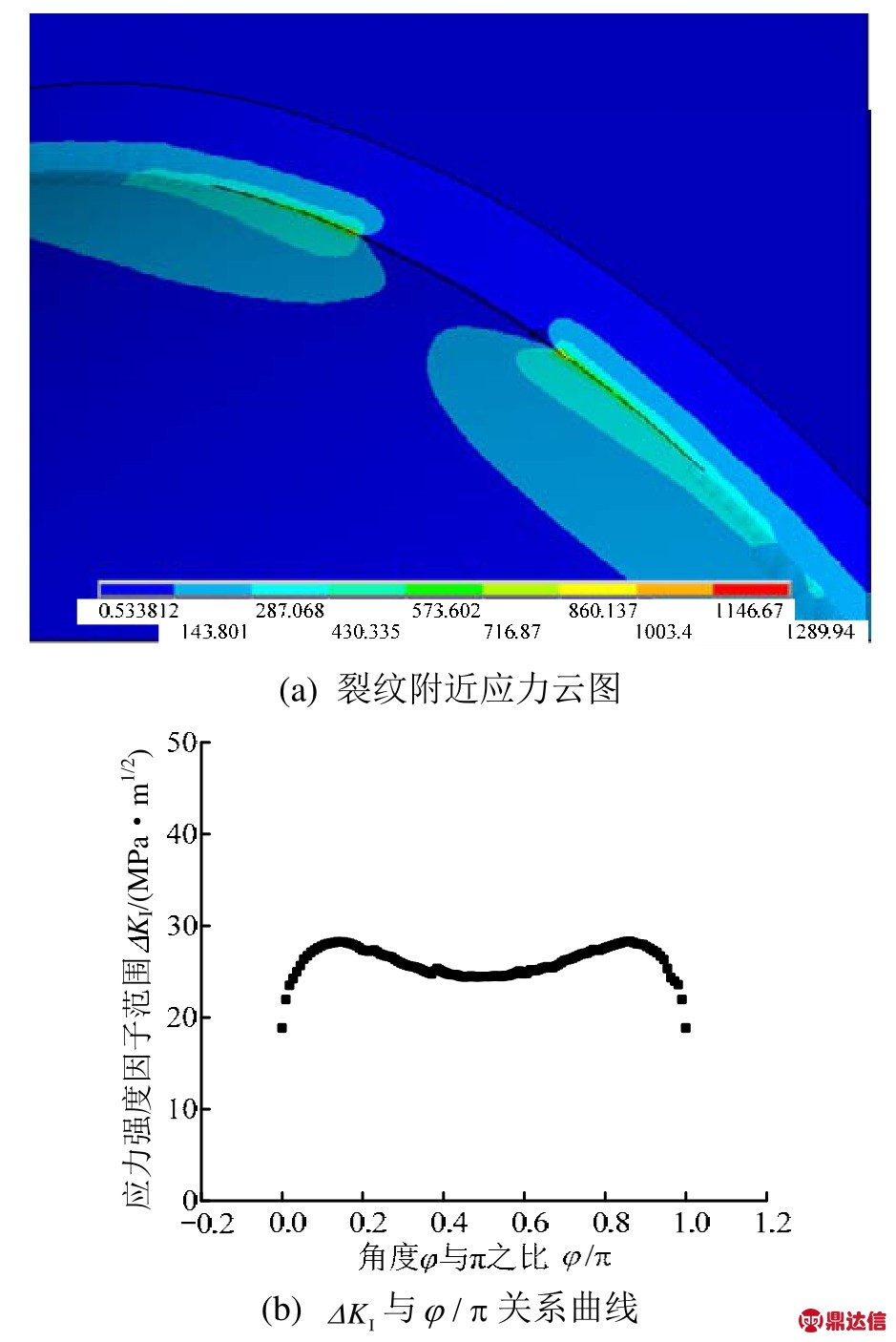
图11 裂纹深度为4 mm时有限元计算结果
Fig.11 FE results for the model with crack depth of 4 mm
裂纹最深点的ΔKI、ΔKII、 Δ K I II、ΔK e ff 与a/ T的关系见图 12。由图可知,裂纹最深点的ΔKII 、ΔK I II 值非常小, Δ K e ff与ΔKI几乎重合,说明该模型的疲劳裂纹寿命主要受ΔKI的影响。
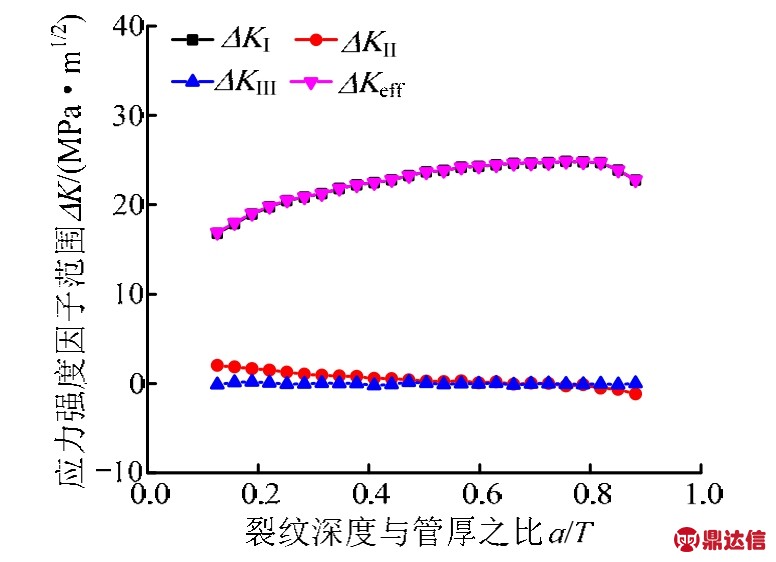
图12 最深点应力强度因子范围与a/ T的关系
Fig.12 Relationship between SIF ranges at the deepest point and a/ T
由于本文并未对试验材料ASTM A572钢材进行疲劳裂纹扩展速率试验,因此无法得知 Paris公式中的材料常数C和m。不同厂家生产出材料的材料常数会有较大的差异,同时由于裂纹扩展区位于焊趾处,焊接对钢材的性能会产生一定的影响,因此其他学者关于ASTM A572钢材试验的所得材料常数结果对于本文并不适用。因此,本文假定C等于 1.2×10-13(mm/cycle)·(mm3/2/N)3, m=3.0。当裂纹深度为 0.8 mm时初始荷载循环次数为 0和1.82×105的计算结果见图13。由图可知,当初始循环次数取为1.82×105时,有限元的计算结果与试验结果非常接近。
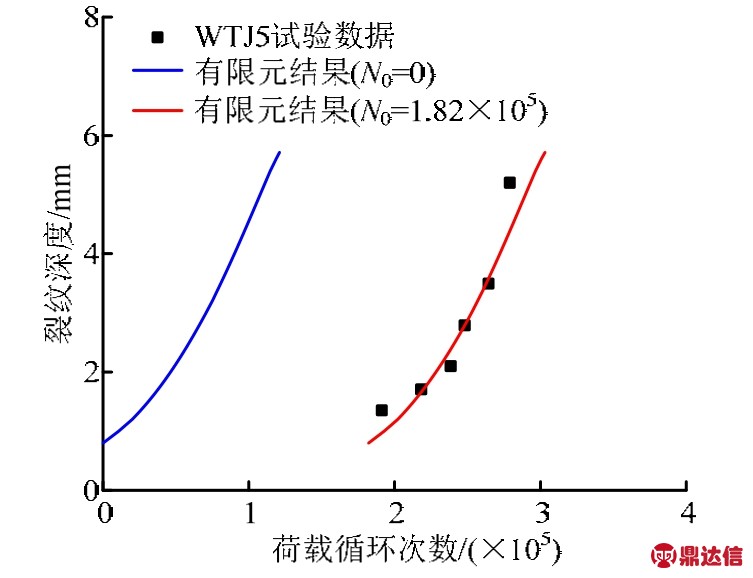
图13 裂纹深度与荷载循环次数关系曲线
Fig.13 Crack depth versus load cycle curves
5 有限元与Bowness公式计算结果对比
为了计算T型节点中半椭圆裂纹的应力强度因子,Bowness和Lee等[14]提出了一个经验公式,该公式也被广泛的应用于求解近海结构管节点中裂纹的应力强度因子。为了考察利用Bowness公式计算交通信号支撑结构焊接圆钢管节点中裂纹应力强度因子的可行性,本节将Bowness公式计算结果与有限元结果进行了对比。
Bowness公式的表达式为:

式中:Mk为焊趾处放大系数;Y为平面板形状系数(参照文献[15]);SCF为应力集中系数;DOB为弯曲自由度;σnom为名义应力;下标m和b分别表示膜加载和弯曲加载。
在裂纹最深点有限元结果与Bowness公式计算得到的ΔKI值的对比见表2。
表2 裂纹最深点ΔKI有限元与Bowness公式结果对比
Table2 Comparison between the SIFs at the deepest point obtained by the FEM and the Bowness equation
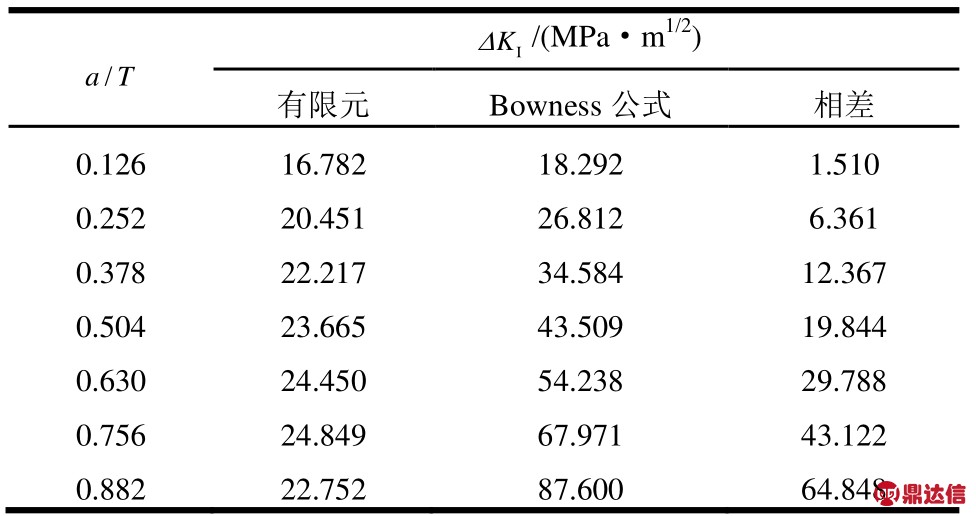
从表2可以看出,在初始阶段,两者的计算结果差异较小。然而,随着a/ T值的增大,两者的差异逐渐明显,Bowness公式计算的结果大于有限元计算结果。因此,对于交通信号支撑结构中端板与圆钢管焊接的节点,利用Bowness公式计算得到应力强度因子从而推测疲劳裂纹寿命较为保守。
6 结论
(1)静力加载有限元模型中,圆钢管上所得的最大Mises应力为413.7 MPa,小于ASTM A572钢材的屈服强度,在焊趾处虽然有应力集中的现象,但是材料仍然处于弹性阶段。有限元计算结果与试验结果较为吻合,说明了有限元计算的可靠性。
(2)由疲劳裂纹扩展模型的计算结果可知,裂纹最深点的ΔKII和 Δ K III 值非常小,Δ K e ff与ΔKI几乎相等。说明本次试验试件的疲劳裂纹扩展寿命主要受ΔKI的影响。
(3)在远离端点处,裂纹尖端的ΔKI值变化较为规则,几乎呈现M形状。在裂纹端点处,由于受到边界约束效应的影响,计算所得的ΔKI有一定的突变。
(4)Bowness公式计算得到的最深点的ΔKI值比有限元结果要大,利用该公式预测交通信号支撑结构中端板与圆钢管焊接节点的疲劳寿命较为保守。