摘 要:随着生产技术的不断进步以及对产品质量要求越来越高,用户对压延铜箔的表面质量和板形要求日益严格。针对压延铜箔在X型六辊箔轧机轧制过程中出现的严重板形问题,以宽度630 mm、厚度18 μm的紫铜箔轧制过程为例,着重分析了加工道次、张力控制以及支撑辊辊型对双肋浪、双边浪、中间浪等板形问题的影响,并提出了相应的解决方案。结果表明:① 在总加工率不变的情况下,减少加工道次,可以增加每道次产生的变形热,有利于残余应力的释放,进而改善板形;② 适当的加大张力,并调节入口张力与出口张力相等,可以有效地对板形进行调节;③ 设置支撑辊总凸度值为0.3 mm以及磨削支撑辊二级辊型均可有效改善板形。
关键词:压延铜箔;X型轧机;板形;轧制道次;张力;辊型
1 前 言
随着航空航天、计算机与通信、汽车电子和和高端电子产品等领域的快速发展,铜箔作为电子互联的基础材料,需求量也在日益增加。相比电解铜箔,压延铜箔因其高延展、高挠曲性及超低轮廓而广泛应用于挠性覆铜板(flexible copper clad laminate,FCCL)、印制电路板(printed circuit board,PCB)及锂电池行业[1-3]。随着生产技术的不断进步以及对产品质量要求越来越高,用户对压延铜箔的表面质量和板形要求日益严格,铜箔板形(即平直度)的好坏已经成为评价铜箔质量的一项重要指标,不良板形会造成铜箔与基板的结合不良,导致开裂、褶皱等问题。板形控制是铜箔轧制的核心技术,国内压延铜箔板形控制研究仍处于开发试制阶段,板形控制能力较差,客户投诉板形问题较多,主要问题是严重的1/4浪以及宽幅板形起伏较大。本文从铜箔板形缺陷产生的原因和特点进行分析,结合X型轧机的调控手段,针对不同类型的板形缺陷提出改善措施。
2 铜箔板形缺陷产生的原因
板形是指板带材的平直度,即板带材是否产生波形、翘曲、侧弯,板形的好坏取决于板带沿宽度方向各部分的延伸是否相等。波形是指板带材纵向呈起伏的波浪,有双边波浪、单边波浪、中间波浪等。影响铜箔板形的因素有内因和外因两个方面,内因是指金属本身的物理性能,直接影响了轧制压力的大小;外因是指摩擦条件、轧辊直径、辊形、张力、轧制速度、弯辊力、轧制工艺、磨损、铜箔母材的来料公差与板形等,这些都会影响铜箔最终板形[4,5]。实际的板形控制非常复杂,需要根据来料的规格选择合适的轧制工艺,根据带材的实际情况预设轧制力、弯辊力及张力。
铜箔越薄,板形越难以控制。板形控制的实质是轧件内部的残余应力分布,当不均匀变形时,轧件内的残余应力也呈不均匀分布,当附加的应力超过一定临界值时,就会形成不同形式的弯曲,形成诸如双边波浪、单边波浪、中间波浪、二肋浪等板形缺陷。在实际生产中由于变形的复杂性,要想从原来就有厚差的母材坯料获得优良铜箔板形,同时保证横向厚差是不可能实现的,或多或少都存在一定的不平度。
铜箔轧制时轧辊横向压下一致是保持板带平整的必要条件。压下横向不一致的结果是:微观地、微小地产生内应力,宏观地、严重地产生板形不平整。假设一段带材由许多细长条并排连接而成,带材的轧制变薄即意味着细长条被拉长。当带材沿宽度方向各部分的延伸不一致时,即意味着细长条的拉长程度是不一致的。由于细长条之间彼此是相互连接的,因此延伸较长的细长条会受到压应力,而延伸较短的细长条会受到拉应力,这些应力构成了整个带材宽度上的内应力分布。当细长条所受的应力达到一定的程度时,会产生弯曲变形,这些变形就构成了整个带材宽度上的“波浪”缺陷。
3 铜箔轧制的特点
铜箔与板带的区分主要是厚度,国内是以0.05 mm区分,美、日等国以0.1 mm区分。由于铜箔很薄,所以对厚度的不均匀非常敏感,一般来说,在 0.035 mm以下厚度轧制时使用负辊缝为主体的AGC控制方式。在负辊缝状态下,轧辊的变形已是一个非圆轮廓,压下量与轧制压力的大小已无绝对关系,轧制过程已完全由张力和轧制速度的大小来控制。不能通过轧制力的改变去补偿这个变形,故需采用速度和张力来减薄箔材的厚度。根据最小轧制厚度公式[6]:
Hmin=3.58DμK/E
(1)
4.1.2 张力对双肋浪的影响
为了轧制出更薄的板带材,必须减小工作辊辊径,并采用高效的工艺润滑剂,减小金属的变形抗力,增加轧辊的弹性模量,有效地减小轧辊的弹性压扁。
4 铜箔实际板形案例分析
目前国内4家压延铜箔厂家,3家使用的箔轧机均为日本IHI六辊X型轧机,1家采用米诺六辊UC轧机。与传统轧机相比,X型轧机采用双支撑辊支撑,轧制过程中轧辊不易变形,因此板形控制的稳定性好。X轧机的板形测量方式为16个转子分段测量,板形测量更精确,控制模式有辊缝控制、速度AGC、张力AGC,轧制过程更稳定。X型轧机基于设备本身的设计,板形的控制最突出特点为分段冷却与分段加热控制。下面以X型轧机实际轧制过程中出现的铜箔板形问题为例,探讨具体板形问题的解决方法。
4.1 双肋浪
肋浪是铜箔轧制过程中最难解决的板形问题,其形成原因比较复杂,为了消除肋浪,需协调控制轧制道次、道次加工率、前后张力等工艺参数。
4.1.1 轧制道次对双肋浪的影响
针对X型轧机实际生产中出现的双肋波浪情况,根据实际情况通过调整轧制道次、张力以及支撑辊辊型,取得了良好的板形。以宽度为630 mm、厚度为18 μm的铜箔轧制为例(母材厚度为0.15 mm),对比了不同轧制工艺对板形的影响,轧制工艺参数如表1所示。
3种轧制工艺的总加工率相同,分别采取4道次、5道次、6道次轧制,保持成品的加工率、张力等参数设置一致,观察轧制道次对双肋浪的影响。图1为采用不同轧制工艺轧制后的板形情况,可以看出,4道次轧制后(方案A)铜箔表面有微小的肋浪;当轧制道次为5道次时(方案B),铜箔表面肋浪数目增加;当轧制道次为6道次时(方案C),铜箔表面的肋浪更加明显且宽大。由此可见,轧制道次越少,铜箔的板形越好,原因主要为首道次及第二道次的加工率大,产生的变形热多,有利于残余应力的释放,减小了变形抗力,有利于板形调节。实践表明,铜箔轧制时,变形抗力越大,铜箔的厚度公差越难以控制,为了保证出口厚度公差,系统会自动增大轧制力,会出现厚度公差为负公差,此时系统又会减小轧制力,既而可能导致厚度公差为正公差,如此循环往复,导致出口铜箔板形随着轧制力的波动发生变化,不利于保持板形稳定性。
表1 18 μm厚铜箔的不同轧制方案及其工艺参数
Table 1 Rolling programs and its process parameters for rolled copper foil with thickness of 18 μm
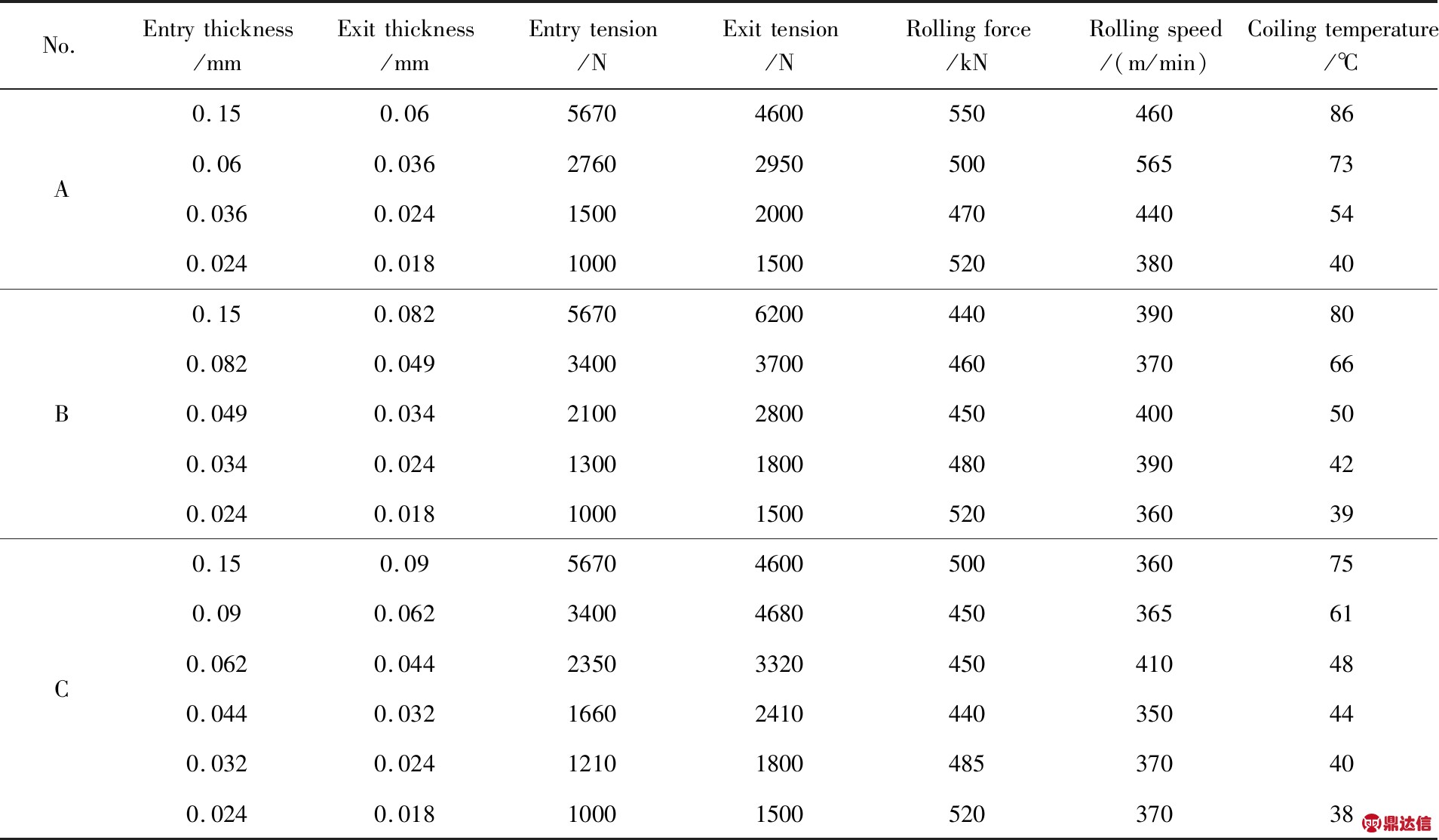
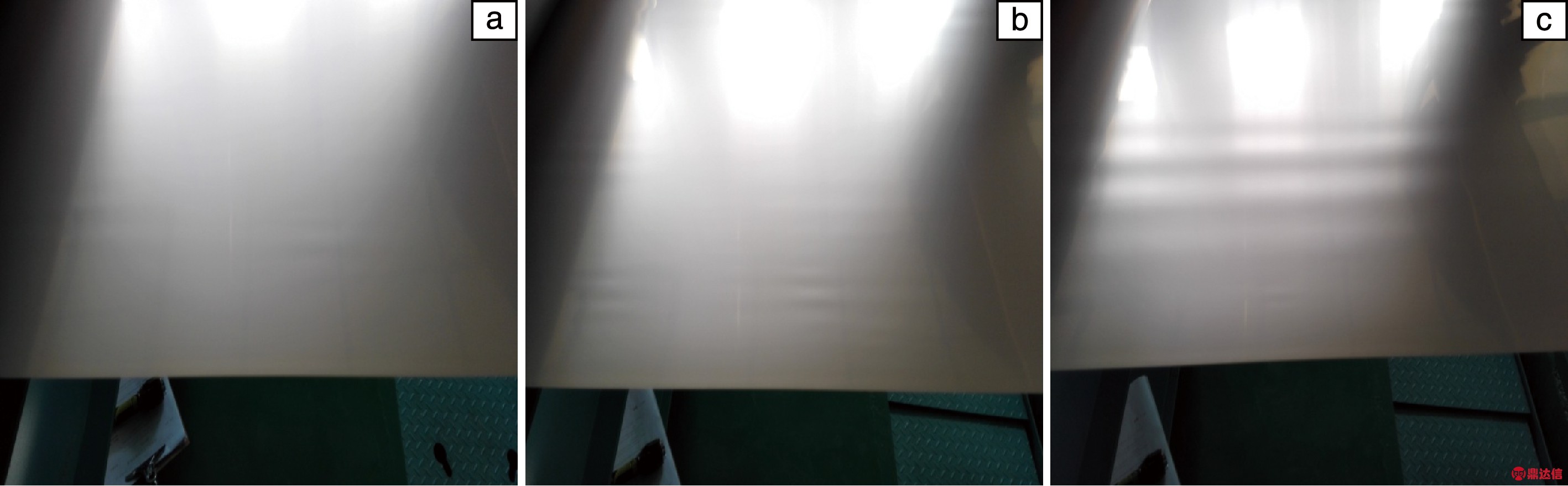
图1 采用不同总轧制道次轧制后的板形情况:(a)4道次,(b)5道次,(c)6道次
Fig.1 Plate shapes under different total rolling passes:(a)4 rolling passes,(b)5 rolling passes and (c)6 rolling passes
持钟剧社成立以来,社务进行,不遗余力,社长何少南剧务干事李广政胡道柞罗质君等,均努力工作,闻已聘定陈鲤庭谢韵心董每戡诸先生参加本校校庆,民立游艺会及中学联联合公演,排演已成白热化。此小小之艺术之花,遂含苞待放,将来戏剧界上必可跃为生力军云,该社所排剧本如下:《战友》(雷蒲芳主演)、《放下你的鞭子》(黄菲主演)、《父归》(顾燕飞张觉民主演)、《姐姐》(王毓侨主演)、《转变》(杜振中主演)。 [23]5
使用4.1.1节第一套轧制工艺,改变张力(具体方案列于表2),探讨张力对板形的影响。实际板形对比发现,张力大且入口张力等于出口张力时板形最好,如图2所示,其中红色圆圈标记处为产生浪形。在箔轧机上是以改变入口张力来进行厚度控制。如图2d所示,当来料厚度H有一个正偏差ΔH时,轧后带材厚度h将产生正偏差Δh。在辊缝不变的情况下,通过加大入口张力,使塑性曲线的斜率减小,由 “曲线B(小张力)”变为“曲线B(大张力)”,曲线A与“曲线B(大张力)”交点的横坐标为h,从而消除厚度偏差Δh使轧后带材的厚度h保持不变。对比图2板形可看出,张力对板形影响是明显的,随着前张力的增加,板凸度呈下降趋势,即板形趋于良好;当前张力不变,后张力增加时,板形改善更加明显。可见无论增大前张力还是后张力对板形改善都是有益的,这是因为张力增加会使轧辊挠度变小,板凸度也随之变小。另外张力的增加可减小金属的变形抗力,有利于金属流动,使箔材沿着板形改善的方向发展,这种现象也被称之为前张力对板形的均化作用。而前张力与后张力相等时板形最好,是因为无论前张力大于后张力还是后张力大于前张力,轧辊都会因箔材前后张力不同的作用产生向前或向后的变形,而轧辊凸度的变化即会引起板凸度的不良变化,导致板形变差。
表2 张力控制方案
Table 2 Tension control plan
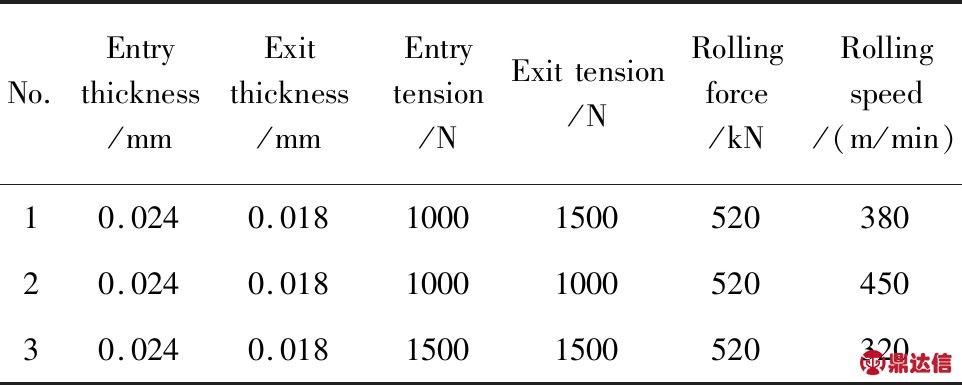
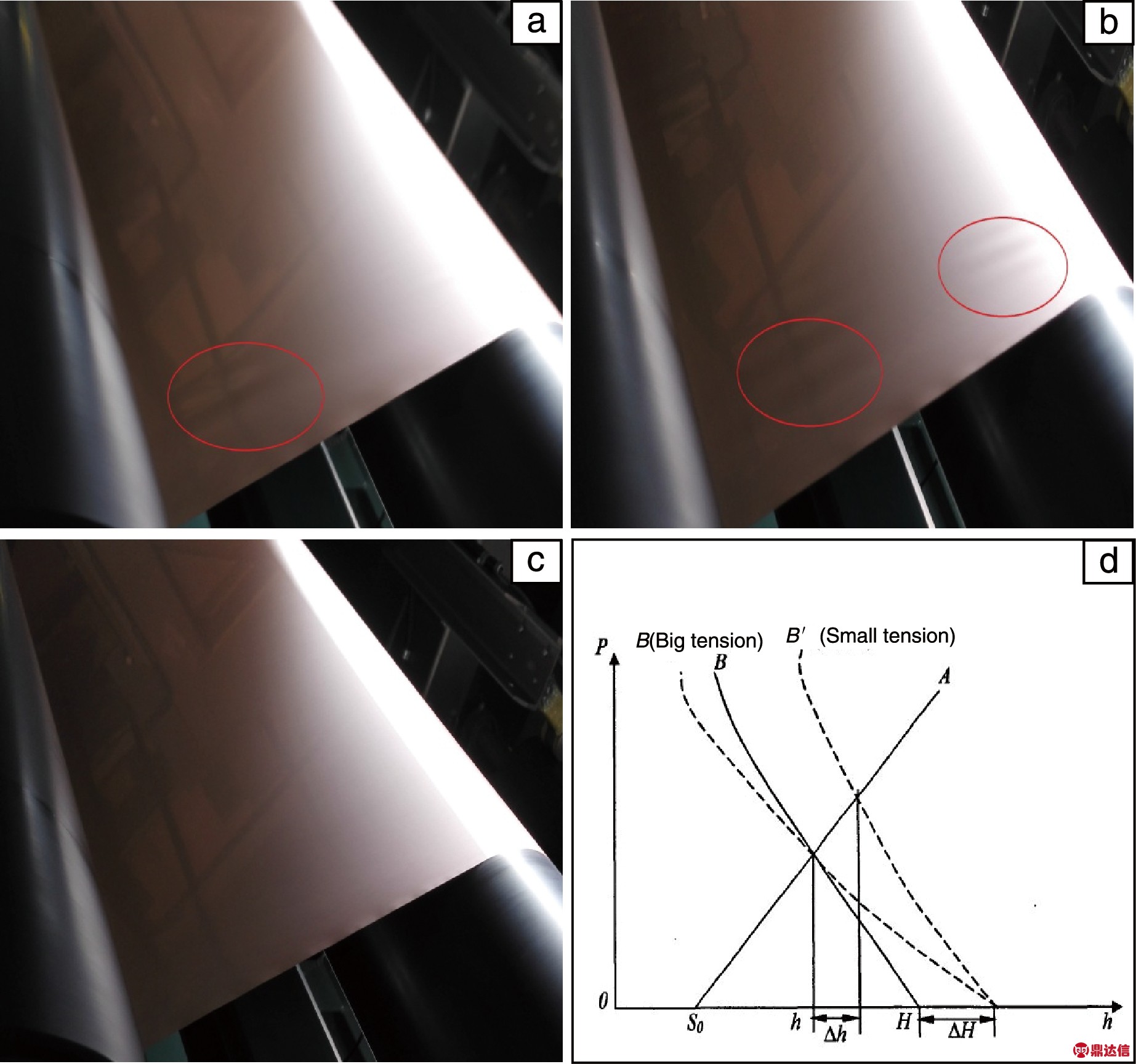
图2 不同张力下轧制后板形:(a)方案1,(b)方案2,(c)方案3。张力调节P-H图(d)
Fig.2 Plate shapes after rolling with different tensions:(a)No.1 program,(b)No.2 program,(c)No.3 program.P-H diagram for tension regulation (d)
4.1.3 支撑辊辊型对双肋浪的影响
为更好地解决双肋浪问题,我们在实际生产中采取了二级辊型方式,通过模拟米诺六辊UC轧机的中间辊锥辊抽辊调节方式,有效地解决了肋浪问题。
4.2 双边波浪和中间波浪
生产初期支撑辊凸度为微凸,总凸度值0.1 mm,轧制过程中出现严重双边浪,边部压折严重,如图3a所示;增大总凸度至0.3 mm时,板形趋于良好,如图3b所示;继续增大支撑辊总凸度至0.4 mm,铜箔出现了严重的中间浪,如图3c所示。分析主要原因为,支撑辊凸度过小,推上缸沽塞作用于支撑辊两端,当轧制力增大时,轧辊两端变形程度大于中间的变形程度,导致箔材边部的受力大,中部受力小,最终使得箔材边部延伸较心部延伸大,产生不均匀变形,形成“双边浪”。调整支撑辊总凸度为0.3 mm后,双边浪消失,板形趋于良好,主要是因为增大凸度后,补偿了轧辊两端的变形,使得箔材横向受力更加均匀,进而获得良好的板形。然而,当继续增大支撑辊凸度时,轧制过程中,轧辊两端变形程度不足以补偿凸度值,造成箔材中间受力较边部受力大,使得其变形不均匀,最终形成中间浪。由此可见,支撑辊总凸度值大小是控制铜箔板形的重要参数,合理控制轧制过程中的总凸度值有利于铜箔板形的改善。
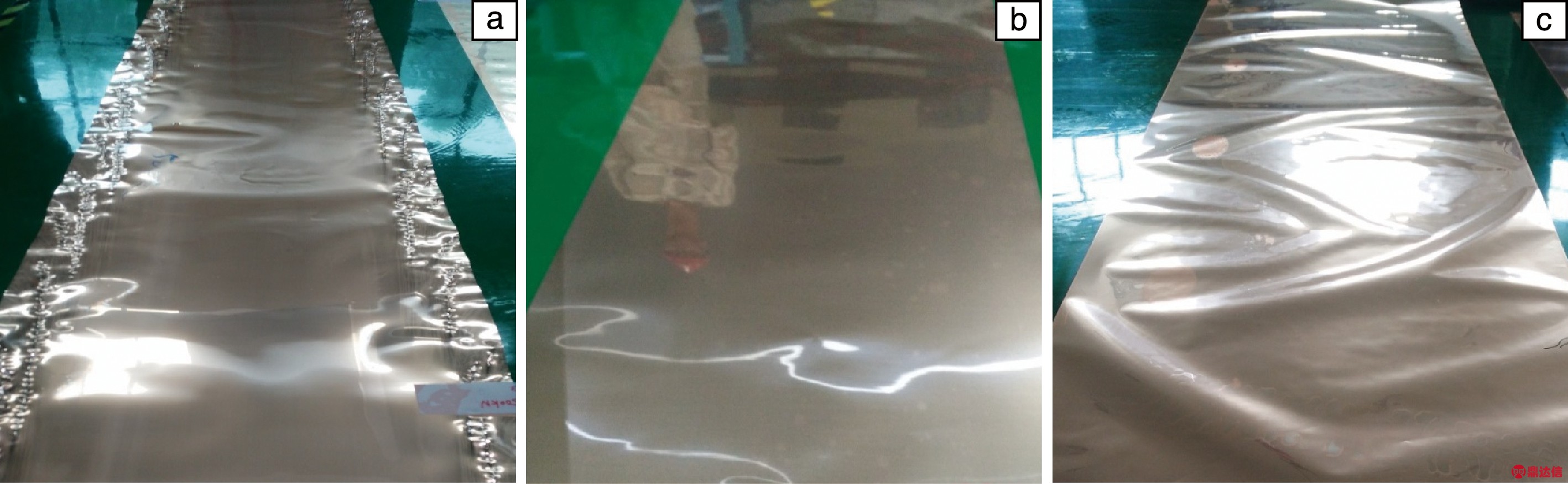
图3 不同支撑辊凸度值下板形情况:(a)0.1 mm,(b)0.3 mm,(c)0.4 mm
Fig.3 Plate shape under different crown value of back-up roll:(a)0.1 mm,(b)0.3 mm,(c)0.4 mm
4.3 单边浪
图4是典型的单边浪板形照片。出现单边浪的主要原因有以下几个:一是铜箔母材存在较严重单边浪,经正常轧制后无法完全消除;二是轧件对中存在偏差,板形调整时出现一边压力过大;三是轧辊偏心或是锥度过大。消除单边浪可通过调整偏调、保证轧件对中与轧辊精度改善。
5 结 论
(1)减少加工道次、磨削二级支撑辊辊型以及设置张力参数为出口张力等于入口张力,可以有效改善18 μm厚铜箔板形;
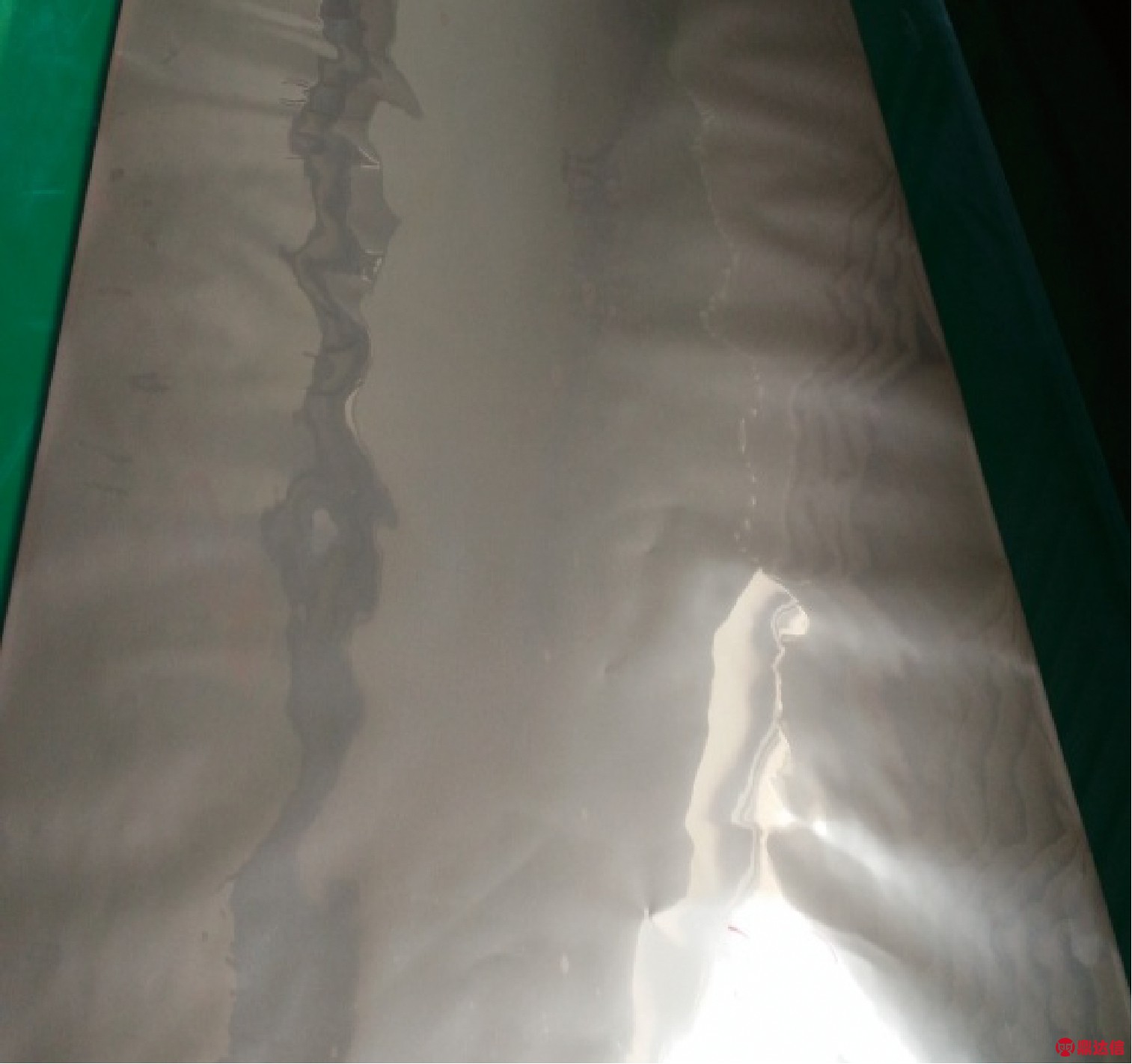
图4 单边浪板形
Fig.4 Plate shape of single waves
(2)支撑辊总凸度值为0.3 mm时,可以有效消除双边浪及中间浪;
(3)良好的母材板形、保证轧辊磨削精度可以获得良好的铜箔板形。