摘要:采用吸附材料进行油水分离是经济且非常有效的方法。吸附材料主要有无机材料、合成高分子材料和天然有机纤维材料等。相比较而言,天然有机纤维材料为可再生生物质资源,来源广泛、生物降解性好,可有效防止二次污染,具有良好的发展潜力,备受关注。本文首先简要介绍了油水乳液稳定性的影响因素,然后综述了油水分离材料的分离原理、构建方法和分离性能等研究进展,并总结了油水乳液分离材料的表征及其分离性能的评价指标。特别地,重点总结了天然有机纤维基吸附材料分离油水乳液的研究进展。最后指出研究智能响应型天然有机纤维基油水乳液分离吸附材料是重要的发展方向。
关键词:生物质;乳液;分离;吸附;多孔介质
工业化的快速发展和海洋漏油事件的频发,导致较为严重的资源浪费和环境生态破坏,也给人类生命健康带来严重危害[1-2]。处理油水污染的方法有许多,但综合来看,采用吸附材料的吸附分离法更为经济有效。但是,对于油水乳液,因为乳液分散相粒径(通常小于20μm)小于油水分离材料的孔径大小(通常为数十上百微米)[3],而且乳液体系更加复杂且稳定,诸如乳液类型,组成成分是否含乳化剂,还有乳液粒径、pH、电荷、油品等众多因素的影响,给油水乳液分离带来了极大困难[4-5]。
基于润湿理论和油水分离原理,吸附材料可分为两大基本类别,即超疏水-超亲油材料和超亲水-水下超疏油材料,而智能型油水分离材料则是在此基础上发展起来的一类新型材料。其中,超疏水-超亲油材料研究较早,至今已发展成熟,但由于自身润湿特性导致的易被油污染及因油堵塞孔隙导致循环利用率低等缺陷,限制了进一步发展;而超亲水-水下超疏油材料[6],克服了超疏水-超亲油材料的上述缺陷[3]。至于智能刺激响应型油水分离材料[7],可以随外界刺激条件(如光照[8]、温度[9]、电场强度[10]、pH[11-12]等)的改变实现超疏水和超亲水两种润湿性能的转变[13-14]。
基于吸附材料形态的不同,油水分离材料可分为2D膜材料和3D吸附材料。前者通过过滤分离油水混合物,需要额外的收集设备,且分离效率受通量影响;而后者不仅可以分离,还可以直接储存分离后得到的油,但也受到吸油倍率等因素的限制。目前,以无机材料为基质的油水分离材料,其改性涂层易被破坏,导致较差的循坏性和低的使用寿命。而合成高分子材料使用普遍,其优势是合成工艺简单和性能优良,劣势是大多难以生物降解。但天然高分子材料具有高的生物降解性、不易造成二次污染等优点。近年来,棉纤维[15]、纤维素[16]和胶原纤维[17]等环境友好可再生天然有机纤维材料用于油水分离备受关注,它们廉价易得,可生物降解,而且含有大量功能性基团,有利于改性处理。本文作者课题组在总结了天然有机纤维改性方法和油水分离性能影响因素[18]的基础上,运用疏水亲油改性技术、超疏水表面构筑技术和可控制孔技术,合成了具有3D多孔结构的疏水-亲油型胶原基吸油材料,可生物降解,具有良好的油水混合物分离效果[17,19]。考虑到胶原纤维富含羧基、氨基等活性基团,通过疏水改性赋予表面疏水亲油性、纳米粒子构造表面粗糙度、冷冻干燥等可控制孔技术获得孔径大小适宜的多孔结构,可以进一步制备用于油水乳液分离的pH响应型油水分离材料。
油水乳液分离吸附材料的分离效能取决于吸附材料的表面润湿特性(与表面能和表面微观粗糙度相关)[20]和油水乳液的稳定性(反映乳液破乳难易程度)。为此,本文在简要介绍油水乳液稳定性影响因素的基础上,讨论了各种类型油水分离材料的分离原理、构建方法和分离性能等,也总结了油水乳液分离材料及其分离性能的表征评价指标。特别地,重点探讨了以棉纤维、纤维素纤维和胶原纤维等为代表的天然有机纤维基油水分离材料在油水乳液分离的研究进展。最后,展望了油水分离材料对油水乳液进行分离的发展前景,以期对环境友好型天然有机纤维基油水乳液分离材料的研究与开发提供指导。
1 油水乳液体系影响油水分离效果的因素
1.1 乳液类型
影响油水分离效果的因素首先是乳液类型。油包水(W/O)型乳液,油是连续相,不需要破乳过程即可直接被吸附分离,这一类型的油水乳液分离难度相对较低。只要构筑好超疏水-超亲油表面和构建孔径大小适宜的多孔结构,就可依靠材料表面亲油性和毛细管作用力实现油水分离,因此超疏水-超亲油材料普遍用于分离W/O型乳液。而水包油(O/W)型乳液,油是分散相,以小液滴的形式分布于水中。此类乳液分离时需要先破乳,使材料表面接触到油滴之后,分离过程才得以进行,因此O/W型乳液主要采用超亲水-水下超疏油材料进行分离。
1.2 乳液稳定性
乳液稳定性也是影响油水乳液分离的重要因素。油水乳液稳定性越好,破乳过程越难进行,分离难度越大。
1.2.1 乳化剂
乳化剂会显著提高乳液的稳定性,使分散相粒径远小于20μm,而且由于乳化剂分子覆盖在分散相粒子表面,形成稳定的保护层,乳液破乳的难度极大提高,给分离工作带来极大困难。Peng等[21]通过羟胺诱导相转变的方式,合成了超亲水-水下超疏油聚丙烯腈膜用于分离O/W型乳液,无乳化剂存在下通量最大可达3806L/(m2·h·bar)(1bar=105Pa),但有乳化剂存在时通量大幅度下降。Chen等[22]通过蒸汽诱导相转变的方式合成超疏水-超亲油聚偏二氟乙烯凝胶用于W/O型乳液的分离,乳化剂存在时通量为220L/(m2·h),无乳化剂下时通量接近 1240L/(m2·h)[通量单位为L/(m2·h·bar)时,分离过程施加了额外压力;为L/(m2·h)时,则没有施加额外压力]。
1.2.2 电荷及pH
电荷及pH是影响乳液稳定性的重要因素。对于离子型乳液来说,主要是通过静电作用使体系处于稳定状态,一般来讲,电荷强度越大,乳液体系越稳定。但在目前油水乳液分离的研究中,普遍使用司班(Span)系列或吐温(Tween)系列等乳化剂制备非离子乳液,使用离子型乳液的文献几乎未见报道,这将是今后研究的一个方向。对于非离子乳液,pH的变化会影响乳液中油成分的溶解性,从而导致乳液的稳定性变化。Wang等[23]研究了不同pH下单宁改性胶原纤维膜油截留率的变化,发现低pH下,分离非离子O/W型乳液时,油截留率下降,随pH的增加,油截留率呈现上升趋势。原因是在低pH条件下,乳液中的油成分邻苯二甲酸二丁酯的水溶性增加,油成分粒径更小,不易在膜表面形成过滤层,因此截留率较低。
1.3 油品类型
油品的黏度、极性和表面张力等因素均会影响油水乳液的分离效果。对于3D吸附材料而言,油的黏度越大,吸油分离效率降低,但保油性提高。油水乳液的黏度越高,一般乳液的稳定性越高,分离难度越大。Bu等[24]使用微流体技术合成超疏水-超亲油磁性石墨烯/多壁碳纳米管微粒,将其沉积在尼龙膜上用于分离有乳化剂存在的O/W型乳液,发现油的黏度越低,通量越大。一般情况下,极性和表面张力的影响规律与黏度相似,越高则油水分离的效率越低。对于低表面张力的油[15],可以更好地润湿亲油性材料的表面,大幅度提高了油的吸收速率。Chen等[22]合成了超疏水超亲油聚偏二氟乙烯凝胶,对正己烷、环己烷和甲苯等不同W/O型乳液进行分离,发现油品的极性越高,油水乳液的分离效率越低。
2 油水分离材料研究进展
2.1 超疏水-超亲油材料及原理
超疏水-超亲油油水分离材料的发展时间较长、研究较为完善,主要用于油水混合物及W/O型油水乳液的分离。分离原理主要基于材料超疏水超亲油表面性能,当材料与油水乳液接触时,水被排斥在外部,油却可以进入;同时,通过构建适宜大小的孔径结构,利用毛细管力和分子间作用力实现油水分离。但是它易被油污染或堵塞,不仅影响分离效率,而且严重限制使用寿命。
依据基质材料的不同可分为三类,即无机材料、合成高分子材料和天然有机纤维材料。无机材料主要为铜网、不锈钢网、碳纳米管等。纳米金属网材料可以根据所分离乳液分散相粒径的不同,选用适宜大小的孔径结构。但由于金属材料难以发生化学反应,所以材料表面结构易被破坏,从而导致循环利用能力不足,使用寿命不长。同时,碳纳米材料也常被用于油水乳液的分离,Shi等[25]通过真空过滤制造了一种超薄独立的单层碳纳米管(SWCNT)网膜,通过化学组分和粗糙度的有机结合具有超疏水和超亲油性能,可以有效分离无乳化剂存在和有乳化剂存在的W/O乳液,分离效率大于99.99%,且通量为100000L/(m2·h·bar)。
合成高分子材料因合成工艺成熟、性能优越被大量使用,如聚氨酯(PU)海绵[26]、聚丙烯(PP)[27]、聚偏二氟乙烯[22]等,但难以降解,易于造成二次环境污染。如Chen等[22]通过蒸汽诱导相转变的方法,制造的超疏水超亲油聚偏二氟乙烯凝胶材料,分离无乳化剂的W/O型乳液,最高纯度可以达到99.99%,通量可达1240L/(m2·h)。同时,用于分离有乳化剂存在的W/O型乳液,纯度依然可以达到99.99%,通量220L/(m2·h)。
天然有机纤维材料属于环境友好型材料,如棉纤维[15]、纤维素[16]、胶原纤维[18]等。棉纤维和纤维素纤维属于天然植物纤维,具有来源广、成本低、生物降解性良好的优势。而且含有大量羟基功能性基团,具有易于改性的基础,近年来广泛应用于油水乳液分离研究中。Wang等[15]通过一步热液法用硅烷改性棉纤维,用于分离无乳化剂存在的O/W型乳液,不仅具有良好的分离性能、可循环性,而且在腐蚀液和热水中具有极好的稳定性。Meng等[16]合成了纤维素和壳聚糖复合气凝胶,利用壳聚糖自组装的方式构建表面粗糙度,通过静电作用和离子交换用硬脂酸钠进行改性,赋予了材料疏水的性能。可以有效分离有乳化剂存在的W/O型乳液,并且可以多次循环利用。相较于天然植物纤维,天然蛋白纤维的研究较为少见,而且研究主要是针对油水混合物体系的分离。特别需要注意的是,在油水乳液分离的研究方面,天然蛋白纤维分离材料的研究几乎未见文献报道。以胶原纤维为代表的天然蛋白纤维材料,具有上述天然植物纤维的优点,富含羧基、氨基等反应性基团,易于改性。在之前的研究中,本文作者课题组[17]使用有机硅对胶原纤维进行了疏水改性处理,合成了具有疏水亲油性能的胶原纤维基质吸油材料,吸收硅油、机油和植物油的能力分别高达13.60g/g、12.50g/g和11.92g/g。在此基础之上,研究胶原纤维材料应用于油水乳液分离势在必行。该方面的研究不仅可以有效利用制革等工业产生的大量废弃物,而且可以拓宽油水乳液分离材料种类,有助于进一步完善油水乳液分离机理的应用基础研究。
2.2 超亲水-水下超疏油材料及原理
来自于鱼鳞特性启发的灵感[6],科学家制备出超亲水-水下超疏油材料并应用于油水分离领域,可以有效分离O/W型乳液[28]。因为材料具有水下疏油的性能,可以很好地防止被油污染[29],使用寿命大大提高。分离基本原理主要是依靠超强的亲水性能,水可以顺利通过材料内部的孔隙结构和缝隙,并在材料表面形成一层水合层,能够阻止油通过[30];此外,大量的微孔、小孔及高比表面积产生的毛细管力可以使乳液发生破乳过程,有利于乳液的分离[29]。Wu等[31]通过硫醇-烯烃点击反应,使用3-巯基丙酸改性纤维素海绵,合成超亲水-水下超疏油改性海绵,分离乳化剂存在的O/W型乳液,第一次分离效率可达98.6%,6次后分离效率仍可达到95.0%。Peng等[21]合成的超亲水-水下超疏油聚丙烯腈膜分离O/W型乳液,通量可高达3806 L/(m2·h·bar)。不仅如此,聚丙烯腈膜还具有良好的防污性能以及可循环利用的能力。
2.3 pH-响应型智能材料及原理
pH-响应型智能材料在近几年有大量的研究成果涌现,可分为羧基-响应型和氨基-响应型两类。其原理是在不同pH下,材料的内部构象变化和静电效应导致材料表面润湿性能的转变[32]。通过不同pH下的超润湿性能智能型的转变,不仅可以分离W/O型乳液,也可分离O/W型乳液,而且还具有优良的防污性能和自清洁作用。
羧基-响应型智能材料是通过引入含大量羧基聚合物或化合物的方式来改性基质材料而制得。此类聚合物主要有聚甲基丙烯酸[33-34]、聚丙烯酸 (PAA)[35]、HS(CH2)10COOH[36]等。通过调节pH,使羧基基团发生质子化/去质子化作用,导致相应的构象伸展/崩塌,从而实现材料润湿性能的智能型转化。Zang等[33]通过单轴电纺技术,以聚甲基丙烯酸为亲水性外壳,乙酸纤维素为内核构建了超亲水-水下超疏油性能的纳米纤维水凝胶膜,可以分别在酸性和碱性的条件下处理无乳化剂存在和有乳化剂存在的O/W型乳液,实现油水分离,且通量随pH的上升而下降。
氨基-响应型材料是通过引入含有大量氨基的聚合物或化合物的方式来改性基质材料而制得。聚合物主要包括吡啶类[37]、含氨基丙烯酸酯类[38]等。其响应性原理与羧基-响应型的相似,也是通过调节pH引起相应的基团发生质子化作用/去质子化作用,从而导致相应构象的变化。Xiang等[39]通过原位聚合和非溶剂致相分离技术的方法,使用N,N-二甲基氨乙基甲基丙烯酸酯作为改性单体,乙烯基三乙氧基硅烷(VTES)作为交联剂,合成了具有pH-智能响应性的聚偏二氟乙烯(PVDF)膜,在不同环境中拥有不同的润湿性能。该材料暴露在空气中时:在酸性条件下,内部的叔胺基团发生质子化作用,由于静电排斥的原因导致构象伸展,从而具有亲水的性能;在中性条件下,叔胺基团则会发生去质子化作用,导致构象崩塌,进而转变成亲油的性能。同时因为PVDF具有亲油性,该材料在空气中具有亲油性。当材料在油中时,材料表现出超疏水的性能,并且与水的pH没有关系,可以分离W/O型乳液。当在水中时,中性条件下具有水下亲油的性能;酸性条件下具有水下疏油的性能,可以分离O/W型乳液。
3 油水乳液分离材料的构建方法
性能良好的油水分离材料,首先必须具有低表面能的表面组成和复杂的微观表面形貌[20]。仅仅依靠降低材料表面能很难达到超疏水[水控触角(WCA)>150°]的程度[40],由 Wenzel和 Cassie模型理论可知,必须提高材料表面粗糙度才可以获得超疏水、超亲油的性能。其次,油水分离材料的孔径大小及其多孔结构也至关重要,对于油水乳液的分离而言,尤其如此。当分离材料的孔径过大时,难以产生可以促进有效破乳的毛细管力,从而影响分离效率;但当孔径远小于乳液分散相的粒径时,由于液滴过大无法通过孔径,易于堵塞材料表面,油水乳液难以分离。因此油水乳液分离材料的孔径大小应当适宜,既不能过大也不能太小[41]。在此,分别针对低表面能、表面粗糙度和多孔性结构3个方面介绍构建方法。
3.1 构建低表面能的方法
将具有低表面能的化合物或聚合物引入基材构建低表面能的方法,主要有浸渍法[42]、气相沉积法[43]、喷涂法[44]和原位化学反应法[45]等。浸渍法是首先将低表面能的有机单体或聚合物溶解形成稳定的溶液体系,然后通过浸渍方式施加进入到基质材料中,随后干燥处理。如采用硬脂酸通过浸渍法改性PU海绵[42],相较于未改性的PU海绵,水接触角提高到150°左右,用于分离O/W型乳液效果极好。浸渍法是一种溶剂法,简单实用,适用于各种不同基质,也常用于天然有机纤维材料的改性处理。如将棉纤维浸入有机硅(十二烷基三甲氧基硅烷)溶液中发生反应,赋予低表面能,改性棉纤维具有超疏水超亲油的性能[15]。
气相沉积法(CVD)适用于多种基质材料。与溶剂法相比,气相沉积法避免了脱溶剂过程,使得涂层更加规整紧密[43]。这种方法应用在合成高分子油水分离材料中较为普遍,而在天然有机纤维油水分离材料合成中应用并不多。
喷涂法简单、高效,多应用于工业生产。在喷涂过程中,具有低表面能的聚合物溶液(如有机硅与甲基丙烯酸甲酯共聚物)[44]首先雾化成微米尺度的液滴,然后借助气流的作用施加到基质材料表面,最后干燥处理,形成了具有微纳尺度结构的低表面能表面。此种方法适用于多种基质材料,但在油水乳液分离研究的相关文献中少见报道。
上述3种方法是基于改性物与基质材料接触方式不同而划分的,而原位化学反应法是基于改性物与基质材料结合方式的不同而划分的,侧重于化学结合的一种方式。原位化学反应法可以同时有效控制化学组成和表面微观形貌两种因素[45],具体方法常常是将基质材料浸没于前体反应溶液,在基质表面发生化学结合,形成粗糙的低表面能表面,稳定性强。至于天然有机纤维,含有大量的功能基团,很容易发生化学结合,所以制备天然有机纤维基油水分离材料,普遍采用这种方法。如有机硅改性棉纤维[15]、聚二乙烯苯基改性滤纸[46]等。
3.2 构建表面粗糙度的方法
主要有蚀刻法[47]、微粒修饰技术[27]、相分离法[21]以及原位增长法[47]等。蚀刻法是使用物理或者化学方法从基质材料中除去部分成分的一种方法。Gu等[47]先在Al2O3基板上均匀附着碳纳米管(CNTs)后,通过自引发光接枝聚合法合成疏水聚苯乙烯(PS)聚合物刷,然后通过蚀刻法从Al2O3基板上分离获得PS-g-CNTs膜。扫描电镜和透射电镜观察发现,膜材料表面具有良好的粗糙度。此种方法多适用于无机基质材料的处理。
微粒修饰技术是采用等离子沉积、物理气相沉积、浸渍等方法将微粒引入到光滑的基质材料表面,构建微观粗糙度。Kansara等[27]通过浸渍法使用烷基三氯硅烷改性聚丙烯材料,获得纳米二氧化硅涂层,从而增加表面粗糙度,该改性材料在油水乳液分离中表现出极高的效率。此种方法几乎适用于所有基质材料。通过此法,天然有机纤维材料的表面粗糙度可以在原有基础上大幅度提高。如Xu等[48]使用SiO2纳米微粒与癸酸改性处理棉纤维后,可以有效分离油水混合物。
相分离法[49]分为热致相分离和非溶剂致相分离两种。热致相分离法是将熔融的聚合物溶于高沸点、低挥发性的溶剂(又称稀释剂)中,形成均相溶液。然后降温冷却,从而体系会发生相分离。非溶剂致相分离法是首先将聚合物和溶剂组成的膜液涂在一支撑板上(如玻璃或无纺布),然后刮膜或者纺丝后,膜液中溶剂和凝胶浴(非溶剂)相互扩散,逐渐分层发生相分离。由于新相的沉积过程是自发无序的,因此使用相分离技术可以显著提高材料表面的粗糙度[21-22]。此种方法多适用于合成高分子基质材料的处理。
原位增长法,其原理与上述构建低表面能的原位化学反应法类似,可在光滑基质表面构建粗糙结构。如Cheng等[50]使用原位增长法在铜网表面构建了一层均匀的Cu(OH)2纳米棒涂层,提高了铜网表面的粗糙度。天然有机纤维含有大量的功能性基团,这种方法十分适用,不仅可以增强材料的机械性能,更可以显著提高材料(如棉纤维[48])表面的粗糙度。
3.3 构建多孔性结构的方法
构建多孔性结构的方法很多。针对天然有机纤维材料来说,主要有冷冻干燥法[22]、冷冻超临界干燥法[51]等。但是由于冷冻超临界干燥设备价格昂贵,故主要介绍经济适用的冷冻干燥法。天然有机纤维本身大多属于多孔性材料,但多孔结构较为紧密,采用冷冻干燥法可以使其多孔结构更加松散,有利用油水分离。
冷冻干燥是利用升华原理进行干燥的一种技术,即将材料在低温下快速冻结,然后在适当的真空环境下,使冻结的水分子直接升华成为水蒸气而逸出,构建多孔结构。合理控制材料预浸水的时间可以有效控制孔径的尺寸大小,这是合成油水乳液分离材料的关键。Wu等[31]通过冷冻干燥法在合成的超亲水-水下超疏油纤维素海绵上构建了适宜大小的孔径结构,实现了有乳化剂存在的油水乳液的高效分离。
基于以上阐述要点,将近几年来的油水乳液分离2D膜材料和3D吸附材料汇总于表1和表2。
4 油水乳液分离材料及分离性能的表征
油水乳液分离材料及分离性能的表征是研究其结构与性能之间关系的重要依据。分离材料的表征内容主要包括材料改性前后的化学组成和微观结构及其变化,油水乳液分离性能主要包括通量和分离效率等。
4.1 油水分离材料的表征
油水乳液分离材料的表征内容,主要有官能团结构、表面微观形貌、孔隙结构、力学性能、热稳定性和生物降解性等。相关内容在本文作者课题组之前发表的综述文献中已经详述[18],故此处不再赘述。
但需要特别注意的是,孔径大小是决定油水乳液分离材料分离性能的重要因素。因为油水乳液的分离过程与材料内在孔径的毛细管力有着重要的联系,材料的孔隙结构直接影响其破乳、吸油、分离等过程。油水乳液分散相的粒径一般处于微米至纳米级水平,故所用分离材料孔径大小需要处于微米纳米尺度范围内,分散相才易于通过。但是分离材料孔径过小又会导致分离速率降低,甚至在材料表面发生堵塞,故适宜大小的孔径尺寸是需要的。
孔径的测试方法主要有气体吸附法[57]、显微分析法[56]等。通常需要根据孔径的大小、形状等因素选用合适的测试方法。孔率测定方法主要有气体吸附法[57]、液体置换法[56]和显微分析法[56]等。对于微、介孔材料,多采用氮气吸附法进行测量,精确度很高,但成本较高。Khosravi等[56]通过气相沉积法采用棕榈酸和聚吡咯对PU海绵进行双重改性处理,合成了可以分离O/W型乳液的亲油疏水性改性PU海绵。采用液体置换法测定了该材料的孔率,并使用光学显微镜观察了孔径大小。
表1 油水乳液分离2D膜材料
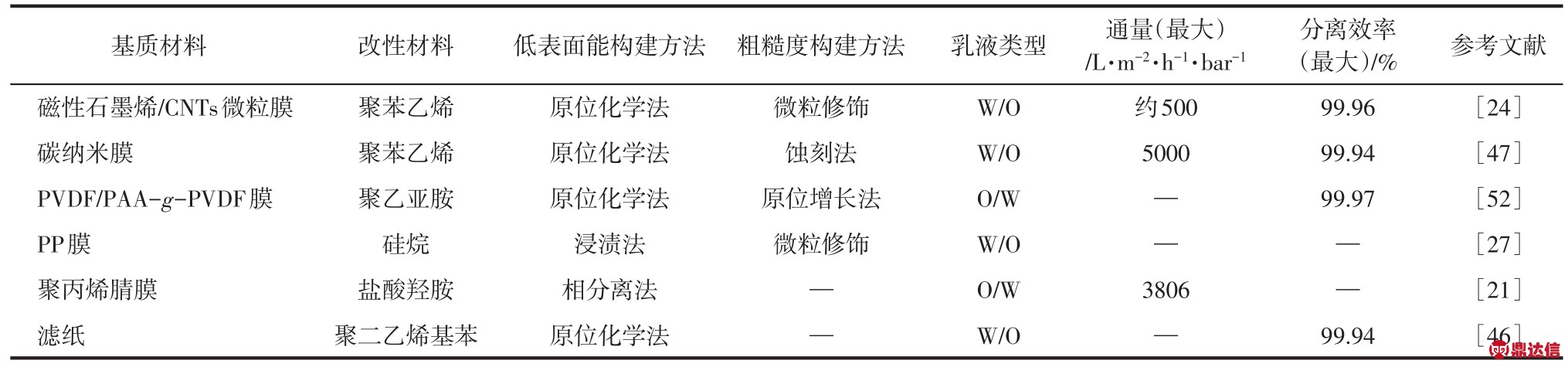
表2 油水乳液分离3D吸附材料

①在油水乳液分离过程中施加了额外压力下,故其通量单位应为L·m-2·h-1·bar-1;②其材料使用吸附分离的方式分离油水乳液,因此没有通量的指标进行表征。
4.2 油水乳液分离性能的表征
油水乳液分离2D膜材料和3D吸附材料的表征方式有所不同的。前者是2D膜结构,纯油体系吸油及油水混合物分离的表征方法不适用,吸油倍率以及保油性等指标无法准确描述膜类过滤材料的油水乳液分离程度,故主要通过通量和分离效率两个指标来评价其油水乳液分离性能。后者3D吸附分离材料的表征则依据材料的分离方式分为两类:一是如上述2D膜材料般的过滤分离方式,则表征方法如上所述;二是吸附分离方法,如硬脂酸改性PU海绵[42]、棕榈酸和聚吡咯改性PU海绵[56]、硅烷改性棉纤维[15]等。这种方法是将吸附材料放入乳液中进行搅拌吸附油或者水,从而使乳液分离,因此无法使用通量指标进行评价。而主要采用分离效率进行评价,同时还会使用纯油体系和油水混合体系分离的指标(如吸油倍率等)表征。另外,重复利用率则常用于评价材料分离的经济适用性。
4.2.1 通量
通量为固定时间内流过有效膜面积的流量体积。在单位时间下,流量体积越大,表明分离效率越好。在此基础上,由于油水乳液的分离过程有着是否使用额外压力的区别,其单位也因此有所不同。当分离乳液的过程加了额外压力,则其单位为L/(m2·h·bar);当没有施加额外压力时,其单位则为L/(m2·h)。
4.2.2 分离效率
通过测量一次分离后的水/油质量分数进行计算,或者直接采用光学显微镜进行观测。还可以采用分离前后油水乳液透光率的比值对分离时间作图所得的曲线和气相色谱法等方式进行间接分析。分离效率主要用来判断材料的有效分离程度,水(油)纯度越高则表明有效分离能力越强。
4.2.3 重复利用率
重复利用率是判断环境友好型材料的重要标准,也是材料本身经济价值的重要体现之一,直接影响材料的使用寿命。主要采用挤压/收缩循环或直接烘干等方式进行多次循环油水乳液分离实验,直至材料本身分离能力丧失或是严重下降,计算其实验次数。实验次数越多,则材料的重复利用率越好,利用价值和经济价值越高。
5 结语
关于油水乳液分离的相关研究,由早前的超疏水-超亲油材料,到现在的超亲水-水下超亲油材料,以及在两者基础之上发展起来的智能响应型材料;从无机材料和合成高分子材料基材的应用,到现在正蓬勃发展的天然大分子生物质材料的应用;从分离微米级的油水乳液,到分离有乳化剂存在的纳米级乳液。其研究进展十分迅速,成果不断涌现,油水乳液分离领域的研究发展在不断深入和拓宽,整体的理论框架渐渐完善。在此基础上,总结认为此领域中未来的发展主要有以下3个方向。
(1)天然有机纤维油水乳液分离材料的研究。此方面的研究尽管已有一些研究成果,如棉纤维、纤维素等基材的应用,但大多局限于油水混合物的分离,对于乳液体系的研究较少;且大多局限于天然植物纤维材料,天然蛋白纤维材料的研究相对较少。
(2)pH-响应智能型油水分离材料。作为一种新型材料有着广泛的潜在应用价值,但目前研究仅限于聚甲基丙烯酸、聚4-乙基吡啶、HS(CH2)10COOH、N,N-二甲基氨乙基甲基丙烯酸酯等几种pH响应型材料。因此拓宽响应型材料的种类,以及在上述基础上拓宽其响应性的pH范围,应用前景良好。
(3)在上述两者的基础上,发展新型的pH-响应智能型天然有机纤维油水乳液分离材料。属于环境友好型材料,对环境发展有利,不会产生二次污染;而且可以实现智能型转变,在油水乳液分离的应用中,可适用于各种不同的环境,而且材料的使用寿命将会有极大提高。