摘 要:将激光切割机横梁组件作为研究对象,以提高横梁组件刚度、横梁组件稳定性为优化目标,且适量降低横梁组件总质量或者保持不变.利用二阶响应面模型分别拟合出正交试验数据中横梁组件各壁厚参数与3 个相关性能指标的函数关系,并建立相应的优化模型.通过对优化设计模型进行求解,最终得到筛选后的最优解.通过最优解对各壁厚参数进行修改后仿真显示激光发射孔处静态变形量下降了8.12%、横梁组件一阶固有频率提高了7.73%,提高了横梁刚度、避开了横梁的共振区间,横梁组件总质量基本保持不变.
关键词:激光切割机;横梁;响应面;优化设计
随着激光的发展与应用,激光切割技术一直受国内外加工行业的青睐.相较于国外,国产激光切割机切割精度与进口激光切割机相比存在差距[1-2].
Marco Troncossi[3]分析了激光切割机移动横梁上激光器的结构特性,对结构进行优化使激光器性能得到改善,提高激光束的稳定性与激光切割的质量.金俊尉[4]利用BP 神经网络和遗传算法相结合的方法对某横梁倒挂式激光切割机横梁优化,降低了横梁质量,提高了横梁刚度,但未考虑到共振对横梁稳定性的影响.J.R Bakera[5]建立数学模型,研究机床结构刚度对加工颤振的影响.濮雍[6]提出以横梁质量和一阶模态固有频率为设目标,优化了激光切割机横梁的动态特性,但未考虑横梁刚度对切割精度的影响.
综上,激光切割机横梁作为激光切割机主要运动部件,承载激光发射器、导轨、齿条等各种零件.激光切割机横梁性能优劣将直接影响激光切割机切割质量.本文研究以提高激光切割机横梁组件刚度和横梁组件稳定性为目标优化横梁组件,且要求横梁组件总质量保持不变,对横梁组件进行优化.
1 龙门式激光切割机模型
1.1 激光切割机模型
龙门式激光切割机主要由激光切割机床身、激光切割机横梁、及其安装于横梁上的激光头和各轴驱动电机装配而成,如图1 所示.
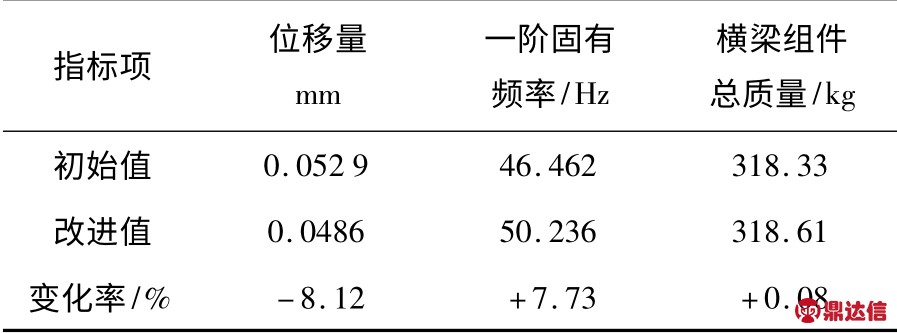
图1 激光切割机的实体模型
激光切割机主要结构参数及横梁初值如下:加工幅面为3 000 mm ×1 500 mm;伺服电机工作转速为2 800 r/min;横梁尺寸为2 200 mm ×180 mm ×187 mm;滑枕侧壁厚t 1为5 mm;横梁上壁厚t 2为6 mm;横梁加强筋壁厚t 3为9 mm;横梁侧壁厚t4 为5 mm;横梁的下壁厚t 5为7 mm;横梁材质为ZL104;横梁初始质量为63.313 kg;横梁组件总质量为318.33kg.
因激光发射器安装于横梁上,横梁刚度将直接影响激光发射器孔位置的精度,从而影响激光机切割精度.
本文为得到横梁刚度和激光发射孔位置的位移量,对横梁整体进行静力学分析.
1.2 激光切割机横梁静力学仿真分析
建立激光切割机横梁CAD 模型,并导入Ansys-Workbench 静力学分析模块,设置材料属性,采用自动网格划分[7].横梁与其支撑座的连接方式采用固定约束,横梁上导轨滑块接触面采用滑动约束.有限元模型如图2 所示.
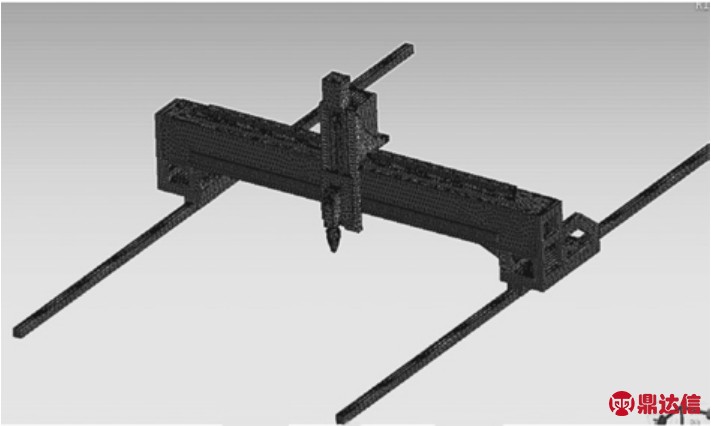
图2 横梁组件有限元模型
激光发射器组件处于横梁中间位置时,横梁挠度最大.此时激光发射孔处位移量最大,该处精度对切割质量影响较大,因此设定为极限工况.对该工况进行静力学分析如图3 所示.
由图3 可得,该工况下激光发射孔处位移量为0.052 9 mm.
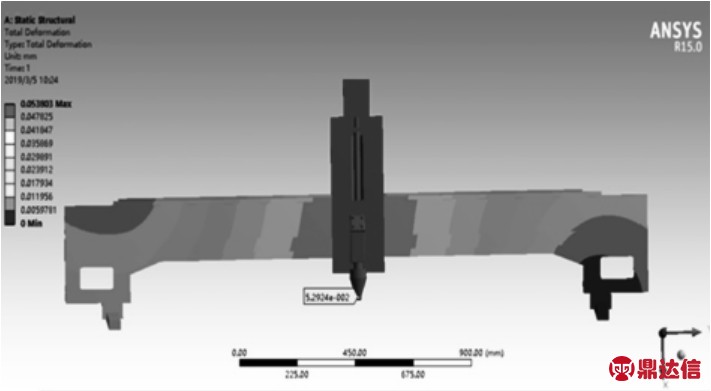
图3 激光发射孔处的位移量
横梁为激光切割机的运动部件,运动时会产生振动.经分析,外部激励与横梁组件一阶固有频率有较大可能性发生共振[6-7].横梁组件经模态分析得到一阶固有频率为46.462Hz,如图4.
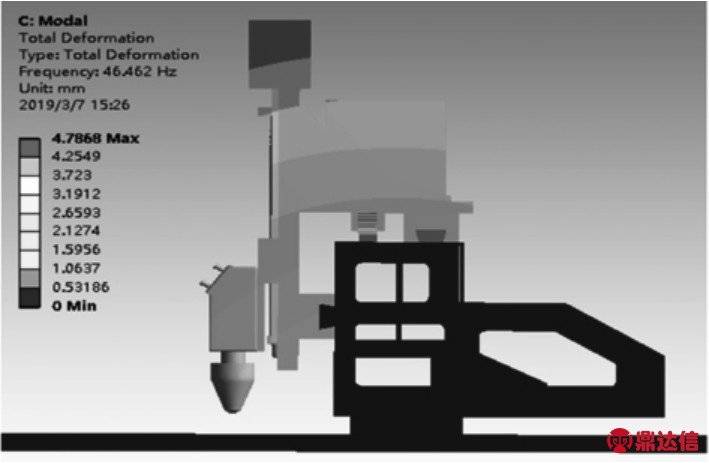
图4 横梁组件一阶固有频率
图3 、4 得到优化前横梁部件结构的各项性能指标.各项指标如下:位移量0.052 9 mm,一阶固有频率46.462 Hz,横梁总质量318.33 kg.
伺服电机工作频率为45 Hz,与横梁一阶固有频率46.462 Hz 相近,容易发生共振.为避开共振区间需要对横梁进行结构优化,将横梁以及激光头组件看成整体,在降低或保持横梁部件总质量不变的前提下提高横梁的刚度,减小横梁变形,提高切割精度.
2 正交试验
激光切割机激光发射孔处的位移量主要取决于其横梁刚度,根据公式:
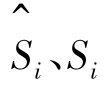
由式(1)可知,当横梁组件质量M 不变时,横梁的一阶频率f0 随横梁的刚度K 增大而提高.但本研究致力于提高激光发射孔处的精度同时降低或保持横梁组件质量,以及避开横梁共振区间.即当横梁组件质量发生变化时,横梁刚度、一阶固有频率也会变化.此时本研究为多目标优化问题.
本文采用二阶响应面法构建优化模型.为得到较准确的响应面模型拟合函数,应对激光切割机横梁各结构参数与激光切割机激光发射器发射孔位移量、横梁一阶固有频率和横梁组件总质量进行多水平、多参数的全面仿真试验,本文采用具有“均匀分散,齐整可比”的正交试验法.
正交试验设计,是一种研究研究多因素、多水平的一种设计方法,利用正交性,从全面试验中挑选有一部分的点进行试验,这些点具有均衡分散和较强的代表性[8-9].
基于正交试验对横梁及其组件结构进行尺寸参数设计,本研究利用仿真分析得到各个结构性能指标情况,为改进设计提供依据.
2.1 试验参数确定
选取横梁及其组件结构5 个主要壁厚参数作为试验因素.5 个试验因素分别是安装于激光切割机横梁上滑枕侧壁厚t1、激光切割机横梁上壁厚t2、激光切割机横梁中间位置加强筋壁厚t3、激光切割机横梁侧壁厚t4、激光切割机横梁下壁厚t5.每个试验因素考察5 个水平.因素水平如表1 所示.
表1 正交试验方案各因素水平 mm
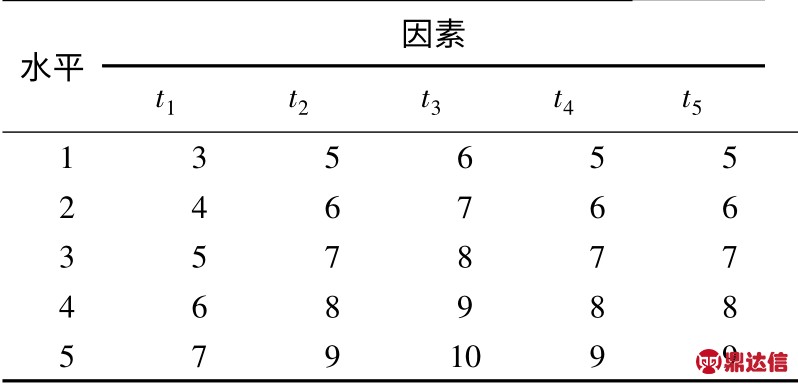
2.2 正交试验方案制定
根据试验目的,选择激光器发射孔的位移量S1、横梁组件总质量S2、一阶固有频率S3 作为试验指标.根据激光切割机的主要参数所研究的问题为包含5 因素,每个因素有5 个水平,故可以选择标准正交表L25(56).根据正交表使用规则,当使用标准正交表L25(56)设计正交试验时,需要进行25 次试验,同时所研究的因素最多不超过6 个,每个因素包含的水平为5 个,当研究的因素小于6时,构建正交表时,减少一列即可.本研究需进行25 次试验,利用仿真分别计算了各试验因素下,激光发射孔处的位移量S1、横梁组件总质量S2、一阶固有频率S3 这三个指标的数值,结果如表2所示.为构建多目标优化设计数学模型进行求解,本文采用响应面法对上述表格的正交试验数据进行函数拟合建立响应面模型[8-11].
表2 正交试验设计方案仿真计算结果
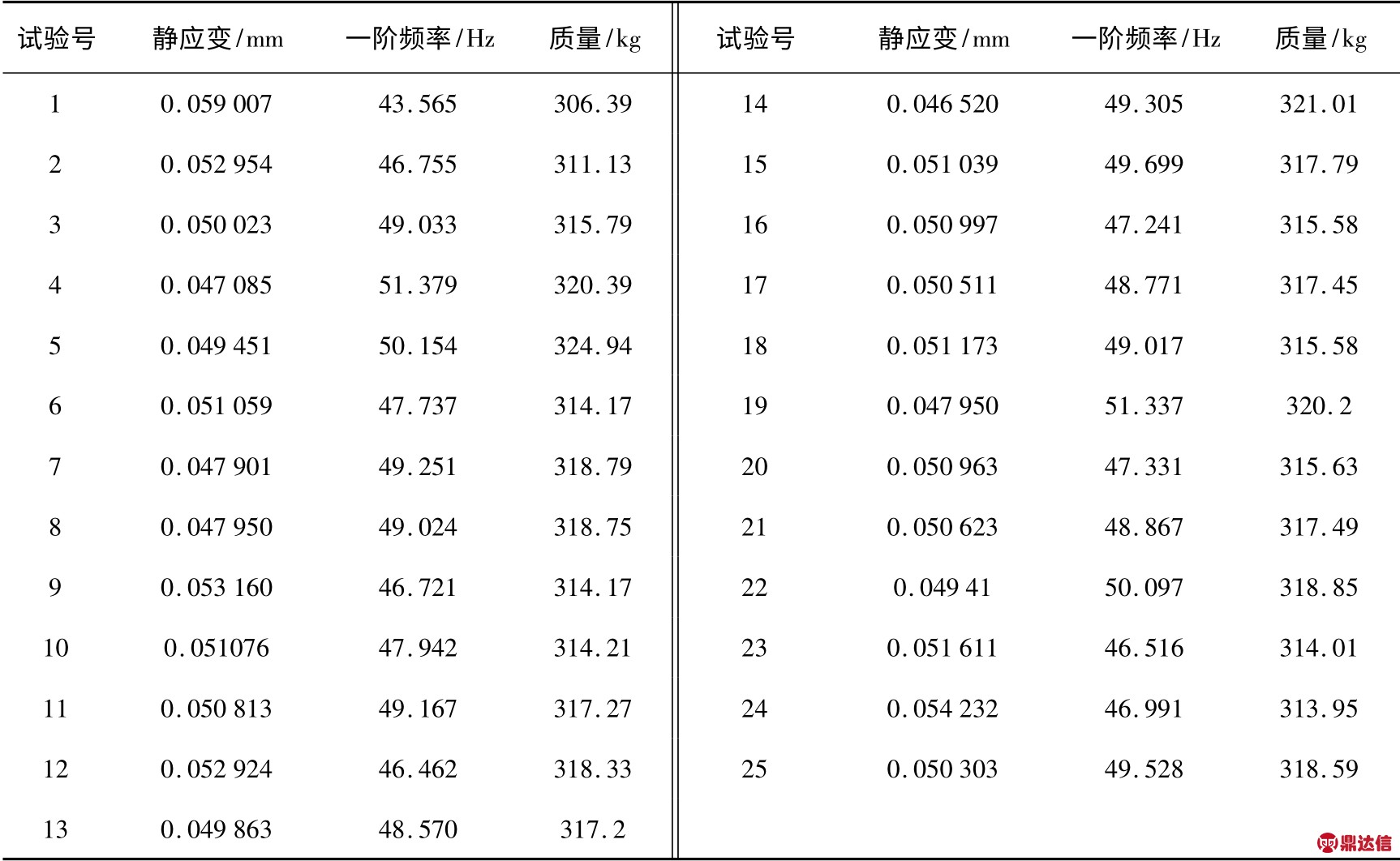
3 建立优化模型与求解
3.1 建立响应面模型
本研究中性能指标为三个,根据正交试验表1[7-8],可知各因素影响对三个性能指标影响情况各有不同,故不能直接用于优化.
为了清楚研究各因素与指标参数之间关系,利用正交试验数据,采用不带交叉项的二次多项式形式的响应面函数[10-11],并采用最小二乘法进行拟合,可以拟合出极限工况下激光发射孔处位移量、该工况模型一阶固有频率
以及横梁组件总质量
的响应面模型:
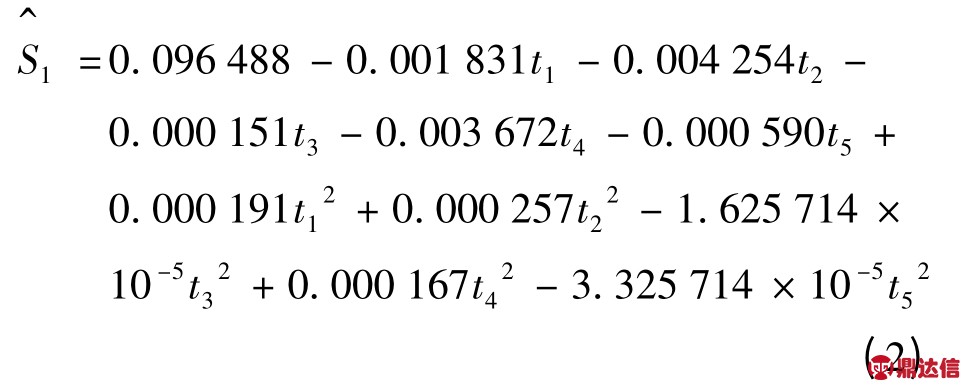
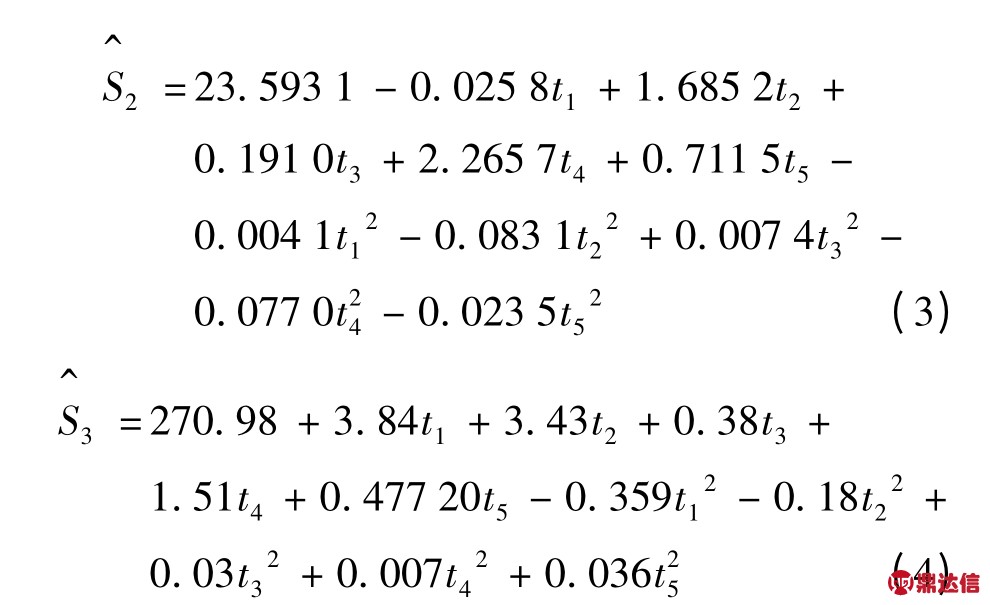
式中,t1、t2、t3、t4 和t5 分别表示横梁及其组件的5个尺寸参数.
将尺寸参数与性能指标拟合为响应面模型时,拟合函数是否接近实际情况应加以考察.故可将视为在N 维空间中的点,拟合值
越接近实际值Si 时,两点之间的距离就越小拟合函数也就越好.函数拟合度指标R 为
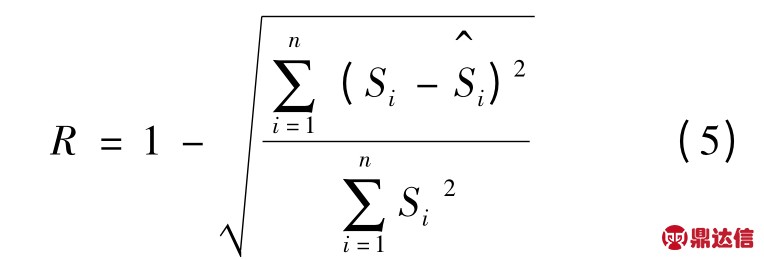
式中,R 为函数拟合度指标,Si 为各项性能指标的实际仿真结果,为响应面模型的拟合函数值.R越趋近1,表示拟合得越好.由公式计算可以得,激光发射孔处的位移量、横梁组件一阶固有频率、以及横梁组件总质量对应的函数拟合度指标分别是:0.987 4、0.982 3、0.989 4,说明拟合精度较高.
3.2 横梁优化模型
优化问题的数学模型,一般有三个基本要素:目标函数、约束条件和设计变量.
3.2.1 目标函数
在保证横梁组件总质量不超过初始实体质量318.33kg 的情况下,横梁的一阶固有频率尽可能最大,同时激光发射孔处的静态位移量
尽可能最小即:
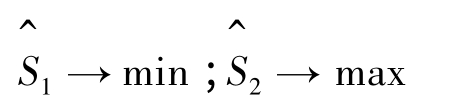
3.2.2 约束条件
尺寸参数发生变化,横梁组件整体质量和激光发射孔处的位移量均会变化.设置横梁组件质量 不超过318.33 kg.即:
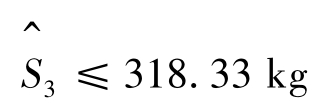
3.2.3 设计变量
横梁组件为机床的主要移动部件和承载部件,故选择横梁作为研究对象,对内部的壁厚尺寸以及安装于横梁上滑枕的壁厚进行研究,共5 个参数,分别是安装于激光切割机横梁上的滑枕的侧壁t1、激光切割机横梁的上壁厚t2、激光切割机横梁中间位置加强筋壁厚t3、激光切割机横梁的侧壁厚t4、激光切割机横梁的下壁厚t5.各设计变量取值范围如表3 所示.
表3 各设计变量的取值范围 mm
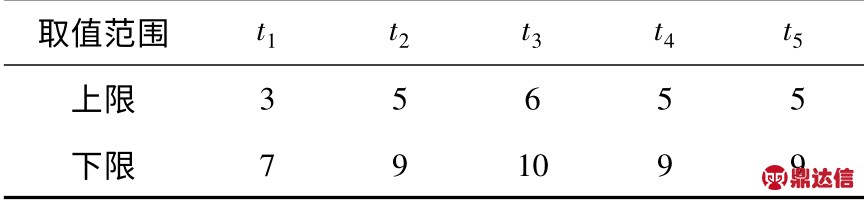
3.3 数学模型求解
本研究横梁及其组件尺寸优化的问题为5 个因素组合问题,需采用全局搜索方法求解.计算得到的优化参数经过圆整后分别为:
3.4 结果分析
根据求解的优化结果,对横梁及其组件原尺寸进行修改后分析,得到改进后的安装于横梁上激光发射孔的位移量和横梁组件总体的一阶固有频率分别如图5、图6 所示.与初始结构对比,如表4 所示.
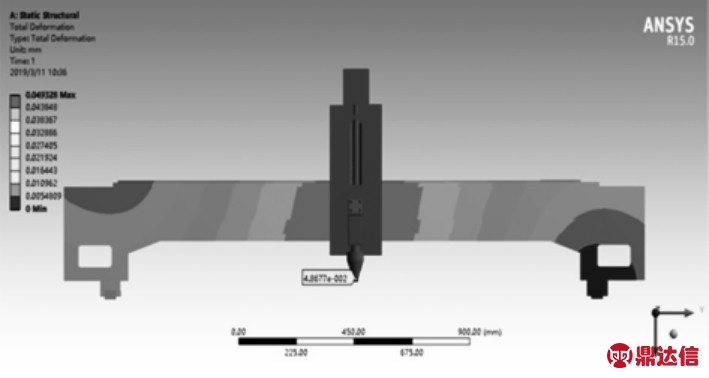
图5 优化后发射孔处的位移量
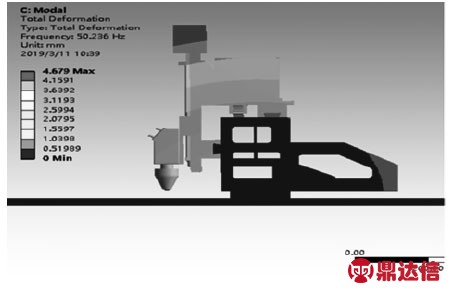
图6 优化后横梁组件一阶振型与固有频率
表4 优化前后仿真计算结果对比
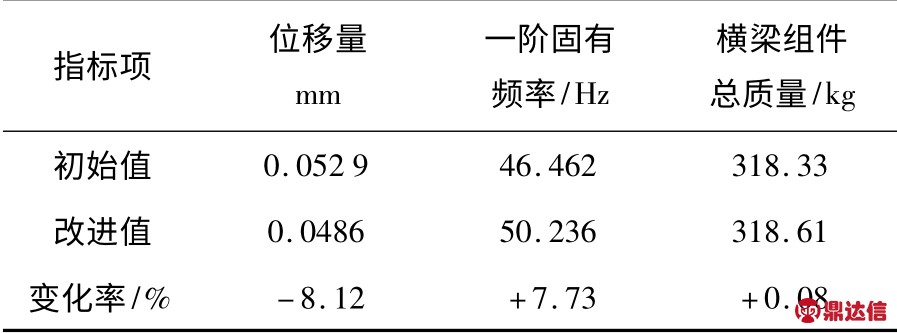
据表4 可知激光发射孔位置位移量下降明显,下降率为8.12%,即横梁刚度得到提高.横梁组件一阶固有频率上升7.78%避开了外部激励频率.且横梁总质量增幅微小,满足初始优化要求.
4 结论
本研究利用二阶响应面模型拟合出某龙门式激光切割机横梁5 个结构参数与3 个性能指标(该激光割机激光发射孔位移量、激光切割机龙门横梁一阶固有频率以及横梁组件总质量)函数关系.利用该函数建立优化设计模型,求解得到最优解,得到优化结构.改进后结构与原结构相比,激光发射孔处位移量降低8.12%提高了横梁刚度,横梁部件一阶固有频率提升了7.73%,避开了共振区间,横梁组件总质量基本保持不变,为优化机床横梁结构提供思路.