摘 要:为满足横梁系统高速运动要求,需提高其动态性能。分别采用有限元分析和动力学实验对数控转塔冲床横梁系统进行动力学分析与研究,根据动力学分析结果提出优化方案,并验证优化方案的可行性,从而达到提高横梁系统刚性和动力学响应性能的目的。
关键词:横梁系统;位移;加速度;优化
横梁是数控转塔冲床送料系统,其动力学性能好坏直接影响板材加工精度[1],因此,研究横梁动力学性能具有非常重要的意义。动力学分析主要有两种方法:一种是动态测试,主要测试系统的动态位移、动力加速度、固有频率等;另一种是利用动力学模型进行理论分析[2]。本研究采用动态测试与动力学模型分析相结合的方法对横梁系统进行动力学分析,利用分析数据找出系统的薄弱环节,从而对系统进行优化改进,并验证优化结果。
1 横梁结构
1.1 横梁模型
横梁主要由电机、丝杆、导轨、夹钳、横梁方管以及加强筋组成,其中横梁方管是横梁的支撑部件,厚10 mm;加强筋用于增加横梁的刚度,竖直方向加强筋Z1厚8 mm,水平方向加强筋X1厚10 mm。横梁结构如图1所示。
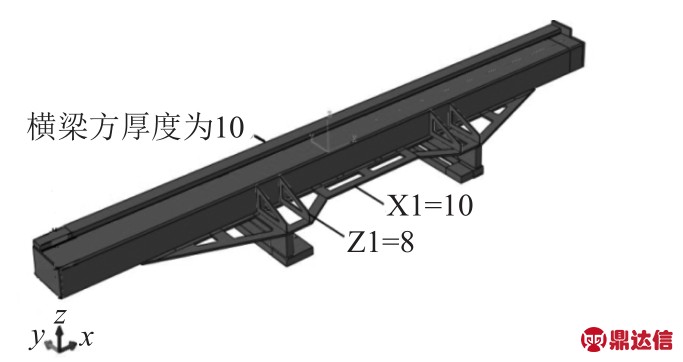
图1 横梁结构图
1.2 横梁有限元模型
对横梁进行有限元分析,需先建立有限元模型。①为减少计算量和防止计算不收敛,对横梁模型进行简化处理,如去倒角、小孔[3];②设定横梁材料,横梁由3种材料组成:Q235A、Q235B及45钢;③划分横梁网格,横梁主体采用四面体和六面体实体单元,丝杆采用横梁单元划分网格[4];④设定横梁各部件约束,横梁主体采用Tie约束,导轨和丝杆采用Connector约束[5],如图2所示。
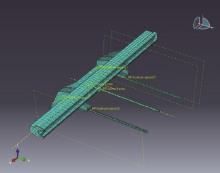
图2 横梁网格划分模型
2 优化前横梁动态性能及优化方案
2.1 动力学模型分析
对横梁主体方管进行轻量化处理,可以减小惯性力,以提高横梁系统的加速度响应。为不影响横梁整体作用,仅对横梁主体方管两侧板材进行处理,将其厚度变为16 mm,优化后横梁由原来的588.57 kg减至553.61 kg。
本研究采用有限元分析方法对横梁系统进行动力学分析,通过有限元分析,得到横梁系统结构模态[7]。模态低阶频率对横梁系统影响较大[8],因此,经模拟分析选取横梁系统前六阶固有频率和振型,如表1和图3所示。
表1 横梁系统固有频率和振型
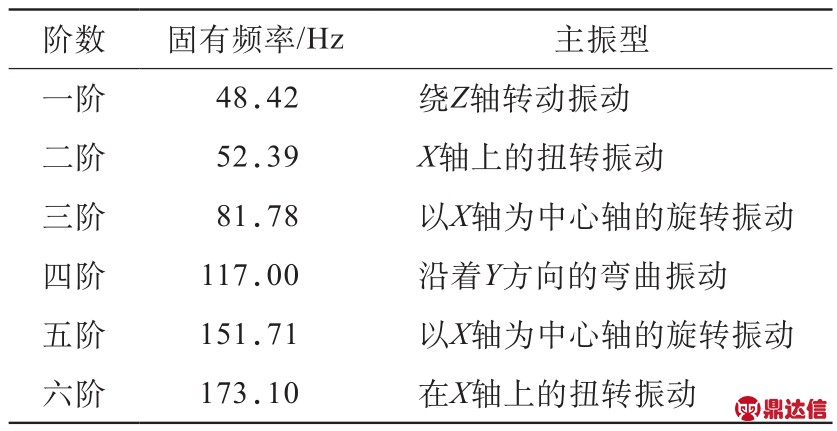
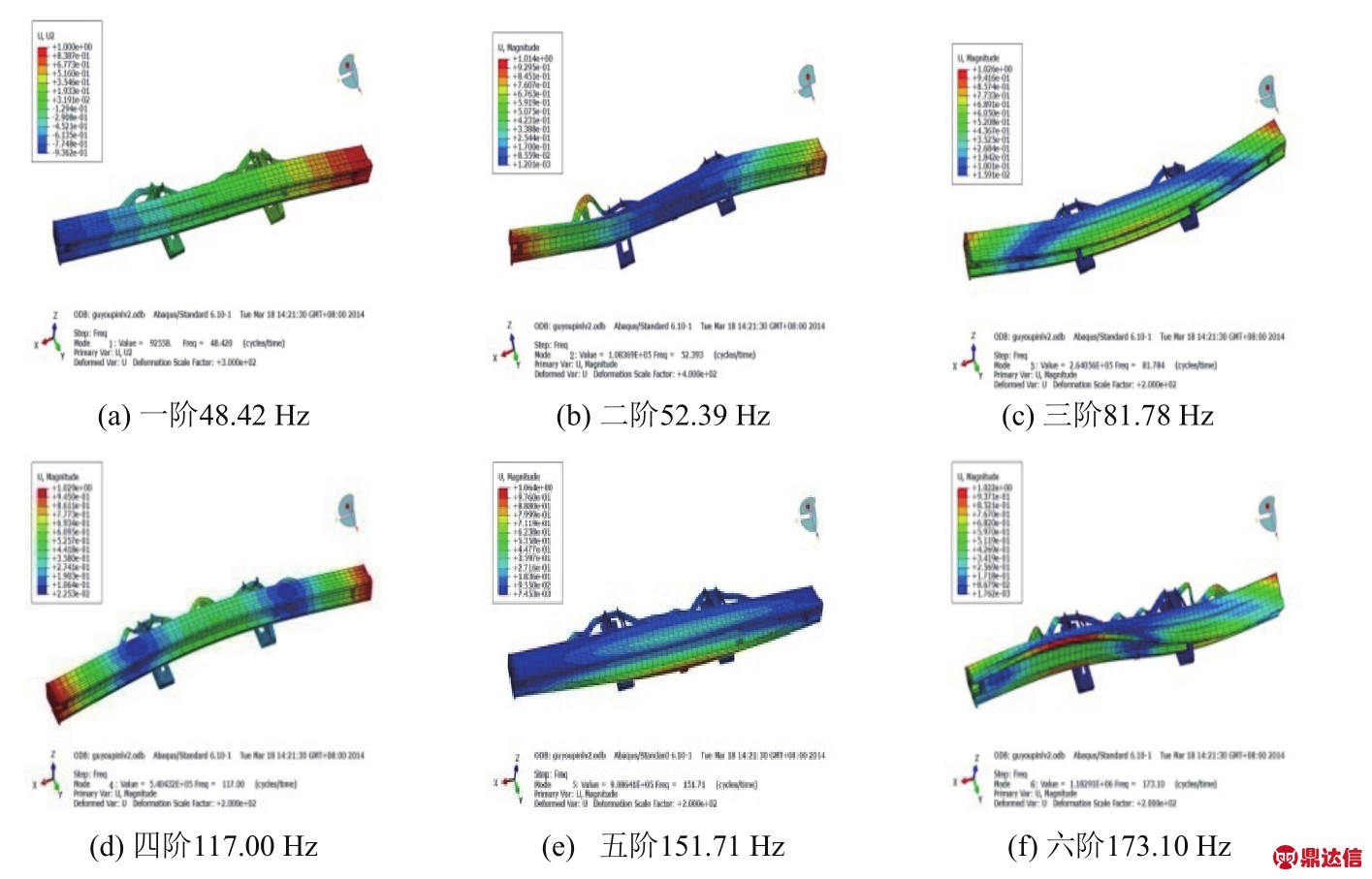
图3 优化前横梁系统振型图
2.2 动态测试分析
动态测试主要研究横梁系统在动态载荷激励下的动态位移和加速度。测试电测法在横梁上布置测点,并获得测点的动态位移和加速度。不同工况下横梁系统所获得的动态位移和加速度各不相同,本研究选取横梁夹持板材位于中间和空载两种工况,横梁以100%(即60 m/min)速度,做1 mm,10 mm,25 mm和600 mm往复运动进行研究。测试所得优化前横梁动态位移如表2所示,优化前横梁加速度如表3所示。
表2 优化前横梁动态位移
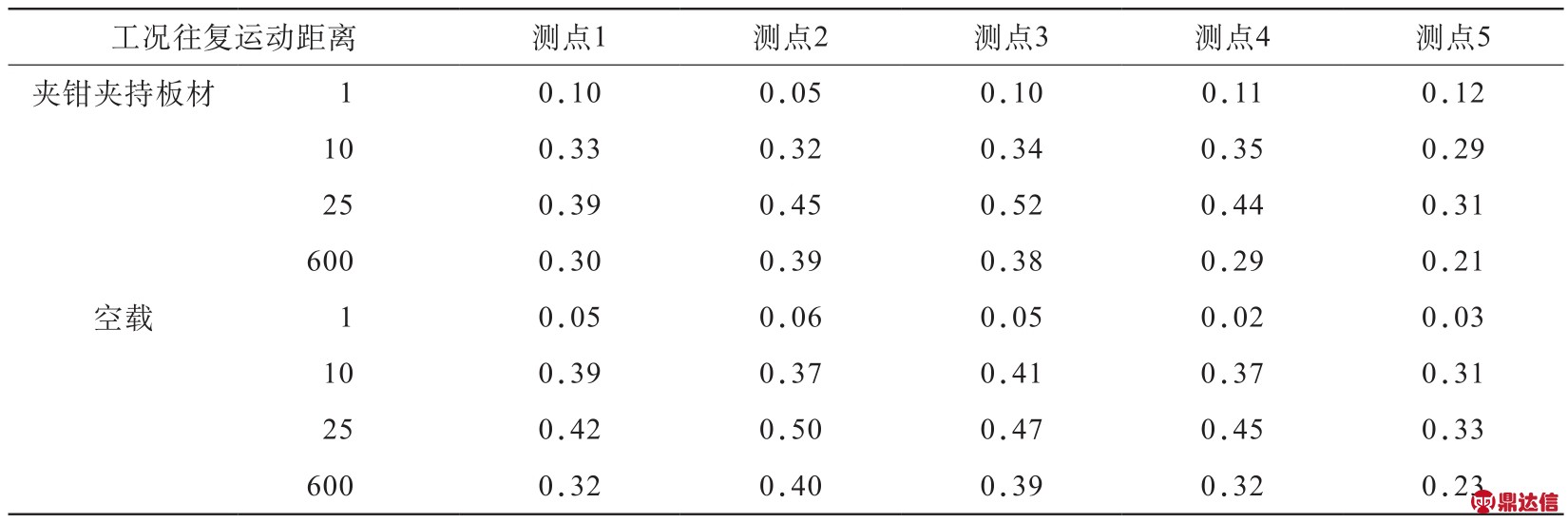
表3 优化前横梁加速度
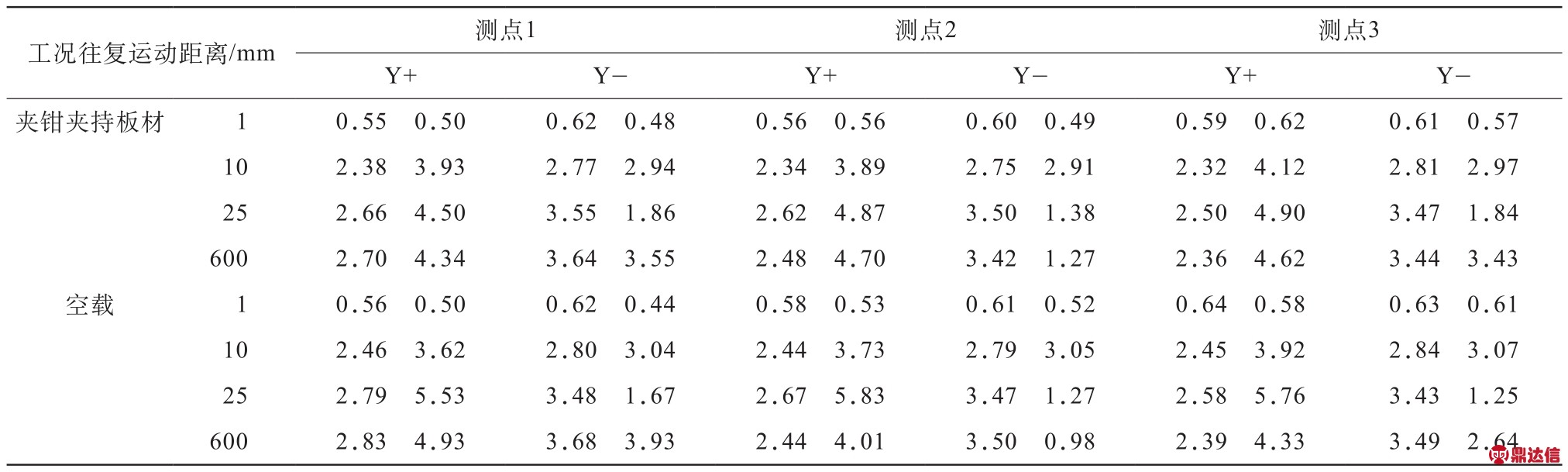
由测试结果可知:①在相同工况下,横梁夹持板材比空载时动态位移要大,如横梁做10 mm运动时测点动态位移如图4所示;同一测点,横梁做25 mm反复运动时的动态位移最大;②在相同速度下,横梁夹持板材和空载时加速度基本相同。
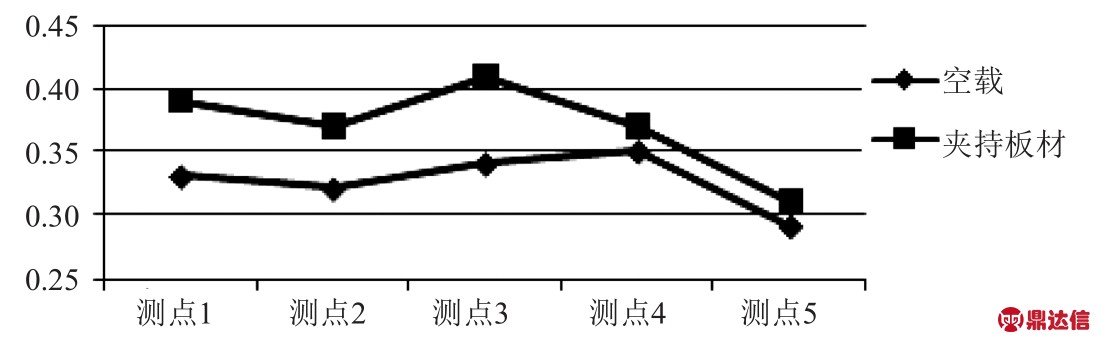
图4 横梁做10 mm运动时测点动态位移
2.3 优化方案
经上述动力学分析可知,横梁系统动力学性能基本能满足现阶段加工需求,但是当横梁高速运动时,会出现高频振动,而高速运动又是冲床今后发展的趋势,因此需优化横梁系统动力学性能。主要从提高横梁刚性、提高加速度两个方面优化横梁动力学性能。
横梁筋板用于提高横梁主体方管的刚度,故增加筋板尺寸可达到提高刚度、减小动态位移的目的。将纵向筋板厚度X1增加为12 mm,横向筋板厚度X2增加为12 mm。
模态分析是研究结构动力特性的一种方法,其分析机械结构的固有振动特性,每一个模态分析具有特定的固有频率、阻尼比和振型[6]。
3 优化后横梁动态性能
3.1 动力学模型分析
横梁系统优化后固有频率如表4和图5所示。
表4 优化后固有频率和振型
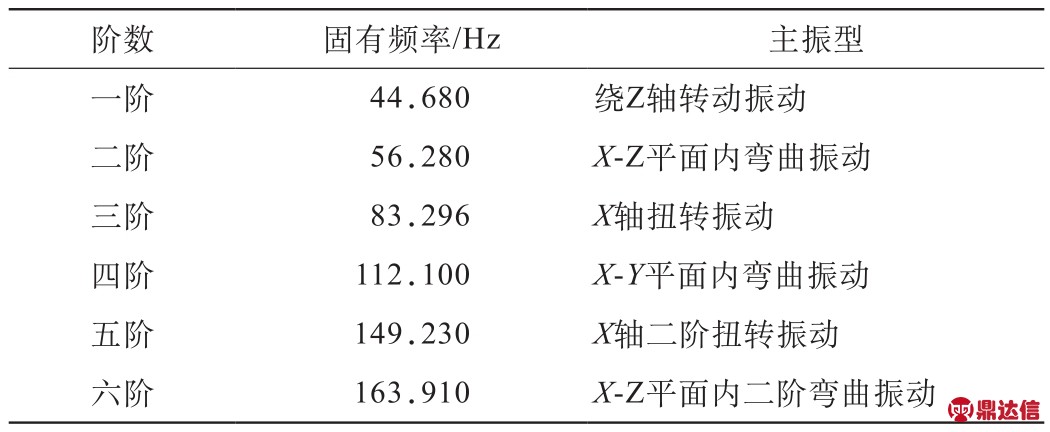
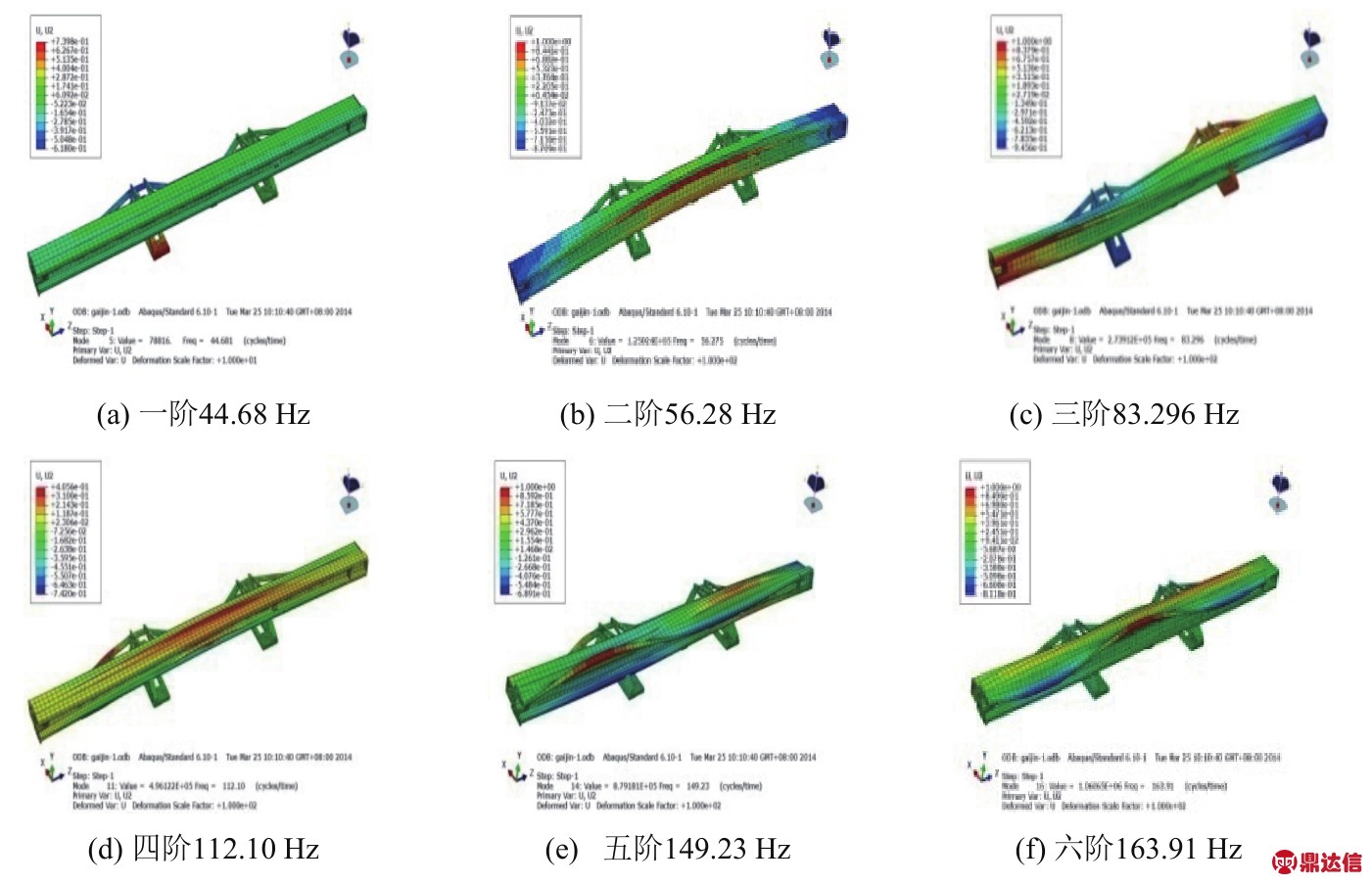
图5 优化后横梁系统振型图
3.2 动态测试分析
横梁系统优化后动态位移和加速度如表5和表6所示。
表5 优化后横梁动态位移
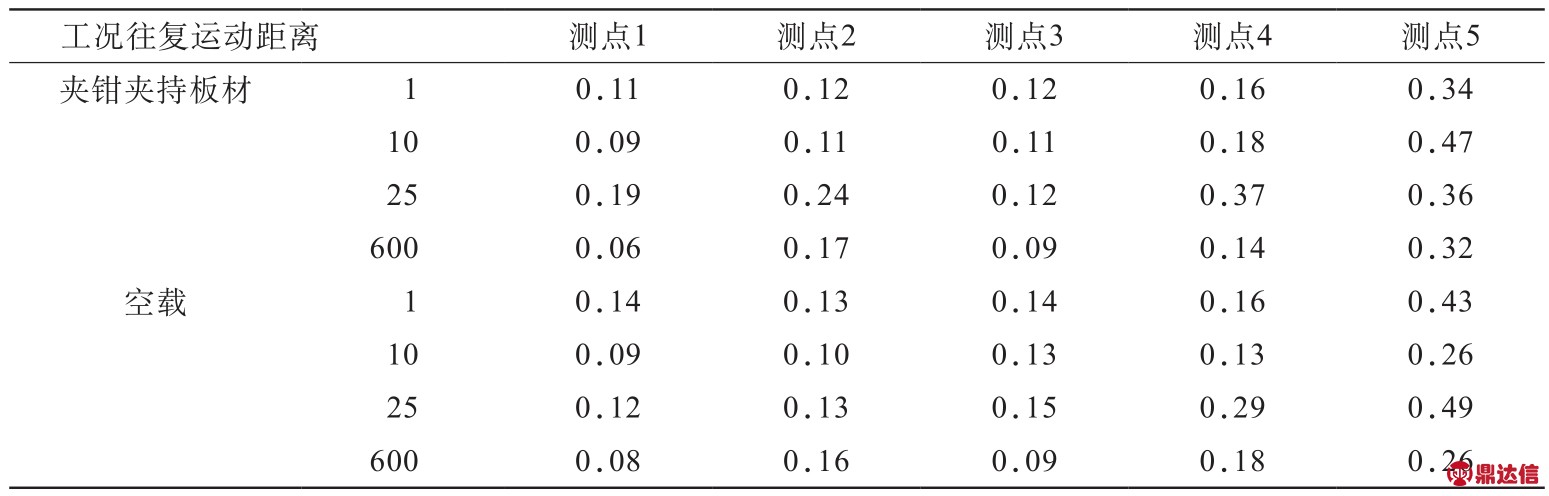
表6 优化后横梁加速度
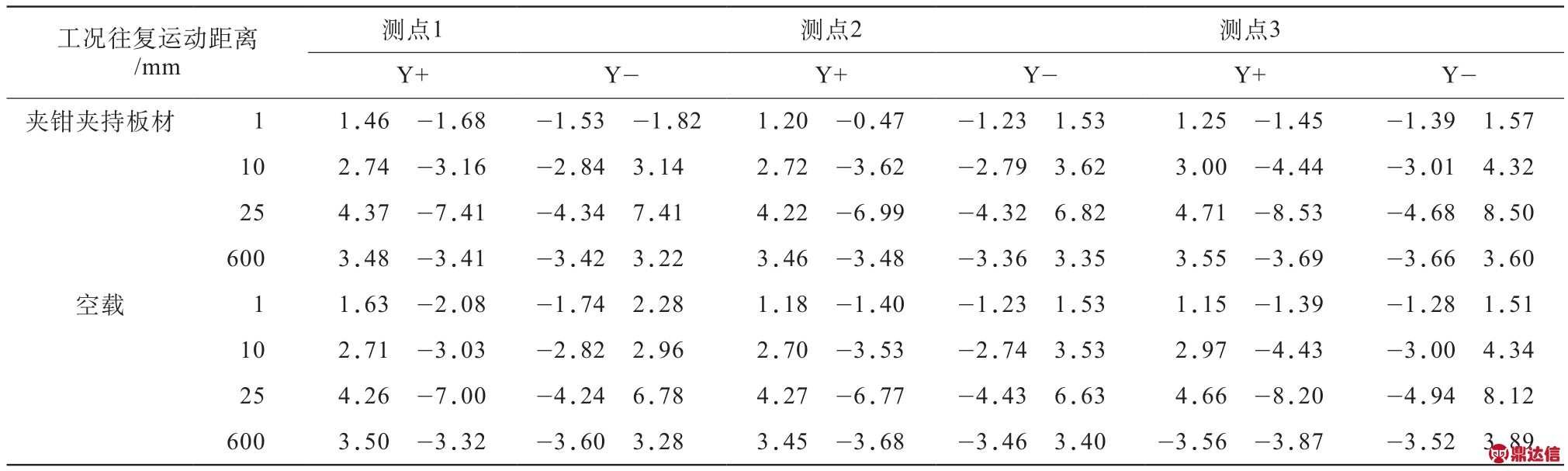
4 结论
对比改进前后动力学模型分析和动态测试实验可知:
1) 优化后横梁系统除二阶、三阶外,其他固有频率都有所下降,达到了轻量化的目的。
2) 在相同工况下,横梁系统改进后动态位移明显减小,说明改进后横梁系统刚性得以提高。3) 在相同工况下,横梁系统改进后加速度变大,响应速度变快。