摘 要:针对重型牵引汽车在使用过程中出现的车架横梁异常断裂问题,文章采用有限元分析的方法对其进行结构及强度分析校核。根据有限元分析结果,车架横梁异常断裂现象是梁连接部位应力值大于材料的屈服强度引起的,这与实车车架断裂结果吻合,再对其结构进行改进设计,并通过对比分析验证了改进设计的合理性。
关键词:牵引汽车;车架;异常断裂;有限元分析
引言
车架是汽车各总成零部件的安装基体,它将发动机和车身等总成连成一个有机的整体,组成一辆完整的汽车。要求有足够的强度:保证在各种复杂的受力状况下,车架及底盘上的各总成不致因变形或疲劳而早期损坏或失去正常的工作能力。有适当的扭转刚度:当汽车行驶在不平路面时,为了保证汽车对路面不平度的适应性,提高汽车的平顺性和通过能力。车架横梁作为车架的关键零部件,横梁的主要作用是连接纵梁,构成一完整的框架,保证车架承载性能,具有足够的强度和抗扭转刚度。
针对某重型牵引车车架第二横梁在使用过程中出现断裂的情况如图1所示,分析横梁的故障模式和故障原因,对横梁结构进行改进设计,通过有限元分析的方法对两种结构最大等效应力进行分析比较[1],并通过分析验证改进的合理性。
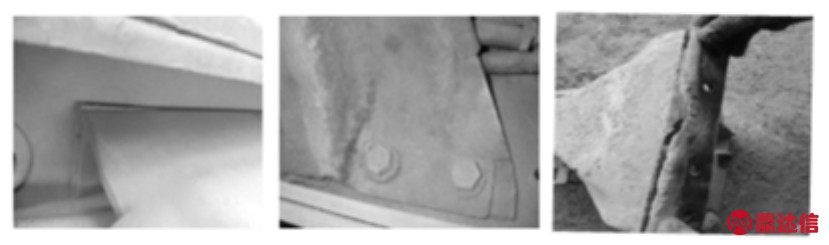
图1 横梁的故障模式
1 两种结构的有限元模型的建立
1.1 两种结构介绍
根据横梁的开裂模式对横梁进行优化设计,老结构如图2(a)所示,新结构如图2(b)所示。
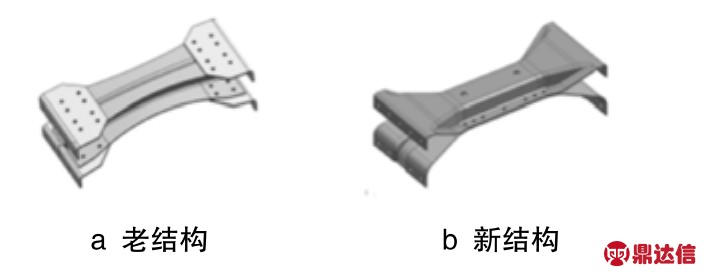
图2 第二横梁结构优化前后的对比
1.2 有限元模型的建立
某重型牵引汽车车架为U型断面梯形边梁式结构,主要由2根主纵梁、2根副纵梁和6根横梁组成,其中横梁与纵梁通过铆钉和螺栓连接。将两种结构整体横梁放在整个车架里计算。车架几何模型较为复杂,采用NX软件建立车架三维模型,通过BatchMesher和HyperMesh软件进行网格划分,将划分好的网格文件导入HyperMesh软件,利用Nastran定义的有限元模型的材料属性及边界条件,提交到 OptiStruct进行计算。各横梁、纵梁和侧翼板的划分采用边长为 10mm的四边形板壳单元(Shel1);圆管梁划分采用边长为5mm的四面体单元(Solid)。车架各构件通过铆钉或螺栓连接,构建装配关系时,先采用刚性单元在装配孔边缘与装配孔中心间建立约束关系,再对装配孔中心点进行刚性连接。
在铆接以及螺栓连接位置进行模拟时,用刚性体单元Rbe2以及Cbeam单元联合模拟,在约束以及驾驶室和发动机重力施加位置采用RB2单元进行连接,在结点施加力和约束,可得有限元计算模型如下图3所示:
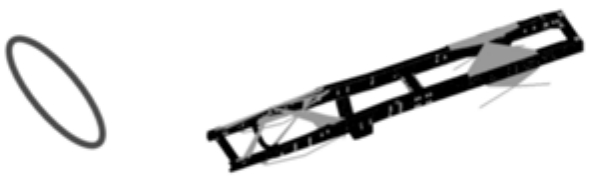
图3 有限元模型(线框内为目标横梁)
1.3 计算的载荷工况边界条件
在有限元分析计算中用到的材料参数见附表1。
表1 材料参数
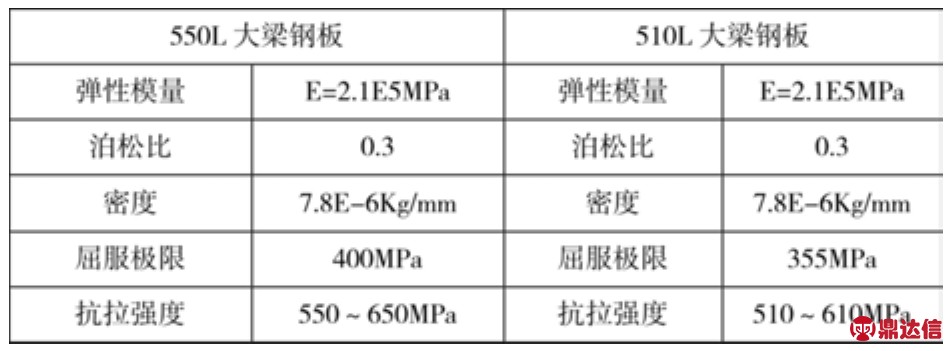
1.3.1 弯曲工况
车辆满载时,作用于车架的载荷包括动力总成的重量 、驾驶室总成的重量、及牵引器所承受的拉力等。在施加载荷时,动力总成的重量按照 800kg,在动力总成重心位置施加力均布于动力总成在车架上安装的悬置点 ,驾驶室总成的重量按照 900kg,在驾驶室重心位置施加力均布于驾驶室总成在车架上的安装点,牵引器施加向后的牵引力和竖直方向的压力。
1.3.2 扭转工况
扭转工况的边界条件及承载情况计算时,约束前悬弹簧接地处的所有自由度,承载情况和弯曲工况一样,将左侧纵梁的后悬弹簧的刚度降低至原来的1/3,使两边纵梁受力不同,形成扭转。
2 有限元计算结果及讨论
2.1 弯曲工况
2.1.1 整车受力情况
弯曲工况下车架总成的受力趋势如图4所示,更换横梁前后对车架总成的总体受力趋势影响不大。老结构横梁状态下车架最大应力值 355.9Mp更换新结构状态横梁后车架最大应力值为354.6Mp。横梁更换前后车架总成最大应力值下降1%。
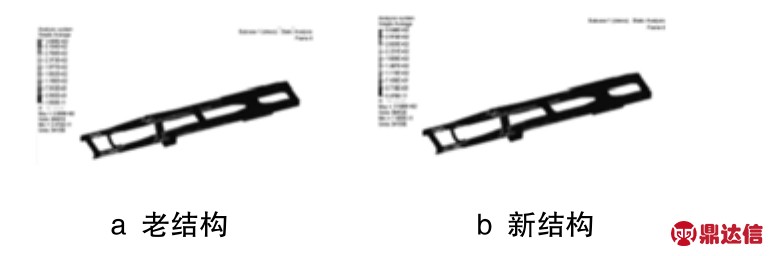
图4 车架总成受力趋势
2.1.2 横梁受力情况
在弯曲工况下老结构横梁受力趋势如图5(a)所示,横梁的最大应力值为341.8Mp,在弯曲工况下新结构横梁受力趋势如图5(b)所示,横梁最大应力值为334.6Mp。新结构横梁相对老结构横梁最大应力值下降3%。
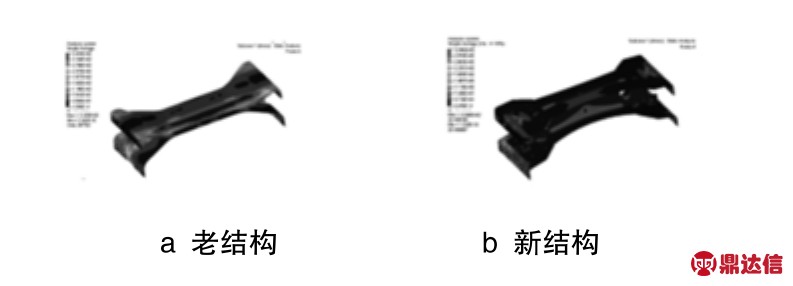
图5 横梁受力趋势
2.2 扭转工况
2.2.1 整车受力情况
在扭转工况下车架总成的受力趋势如图6所示,更换横梁前后对车架总成的总体受力趋势影响不大。老结构横梁状态下车架最大应力值369.3Mp,更换新结构状态横梁后车架最大应力值为340.3Mp。横梁更换前后车架总成最大应力值下降8%。
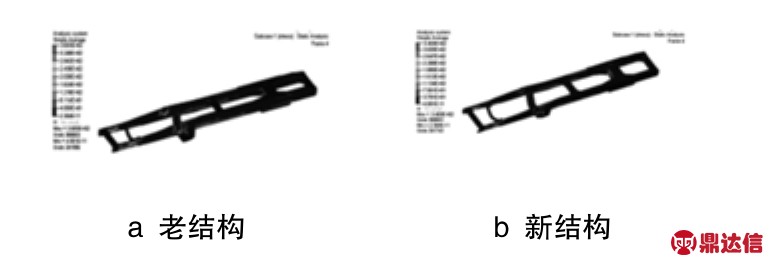
图6 车架总成受力趋势
10.16638梁受力情况
在扭转工况下老结构横梁受力趋势如图7(a)所示,横梁的最大应力值为361.8Mp,在扭转工况下新结构横梁受力趋势如图7(b)所示,横梁最大应力值为320.3Mp。新结构横梁相对老结构横梁最大应力值下降12%。
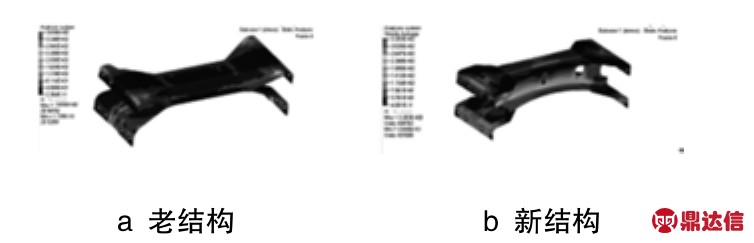
图7 横梁受力趋势
2.3 分析结果讨论
把不同工况下整车和单个横梁的受力趋势详见表 2,可以更加直观对整车和单个横梁的受力趋势做详细的比较和分析。
表2 受力情况
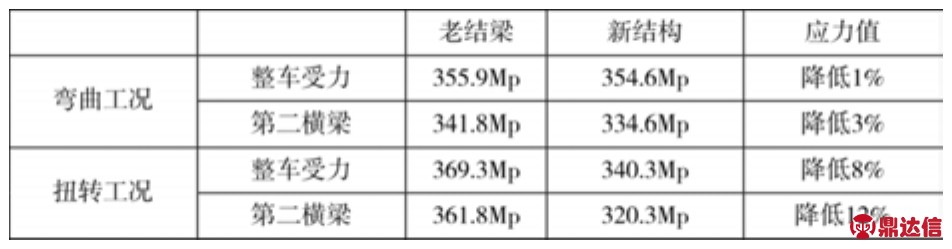
通过表格数据发现,新结构横梁对整车的弯曲工况受力影响较小,最大应力点在大梁上,大梁材料为 550L屈服强度为 400MPa,整个车架受力在合理的范围内。第二横梁材料为的屈服强度为 355MPa,新老结构横梁均满整车的使用工况。
扭转工况下整个车架受力在合理的范围内,满足使用要求,老结构横梁应力值超过横梁材料的屈服极限,在使用过程中因多次扭转达到疲劳极限产生开裂。而新结构横梁抗扭性能好,能很好的适应扭转工况。
从表格中可以看出老结构横梁的抗弯性能较好,新结构的抗扭性能较好。重型牵引车由于装载原因无法上高速公路行驶,只能跑省道路况相对较差,第二横梁的位置位于中桥前,主要承受扭转应力。新结构横梁更适合重型牵引车的使用工况。
横梁结构改进后,应力的在整车和第二横梁的应力分布较合理,同时新结构横梁目前在市场验证已经有1年多的时间,表现良好,很好的解决了市场上重型牵引车第二横梁的开裂问题。市场验证结果也证明了该结构改进的可行性 。
3 结论
在本次优化设计时借助了应用软件 NX、HyperMesh、HyperView等软件。对车架的结构强度分析结果表明,车架第二横梁断裂现象是由于横梁在折弯位置因拉伸产生变薄,且所在使用工况的应力值超过横梁材料的屈服强度引起的。有限元计算结果与实车车架横梁断裂结果和位置相吻合,表明本论文研究采取的建模方法和分析方法可行,可为车架结构及横梁改进设计提供依据。
新结构横梁在各种工况下的等效应力均小于老结构,整体车架结构在受力方面有较大的改善,新结构横梁代替旧结构在强度上有很大的改善,解决市场问题切实有效。