摘 要:针对某自卸车驾驶室后悬横梁开裂问题,在Hyperworks软件中建立后悬置有限元模型,并对其进行了有限元分析,找到了横梁开裂原因。分析了系统结构参数对后悬支架载荷的影响,通过调整后悬置系统结构参数,减少了后悬系统结构载荷;通过添加加强筋块、改变连接位置关系的方式增加了横梁局部刚度。对改进后的结构进行有限元分析,与改进前相比,结构应力情况明显改善,有效解决了横梁开裂问题。
关键词:自卸车;悬置横梁;开裂;改进
调控温度是发菌期“重中之重”。以暖棚保温宜,发菌期控温要严,在保证菌丝体生长的前提下,尽量降低温度。出菇期,要提供足够的温度刺激。
1 结构介绍及问题陈述
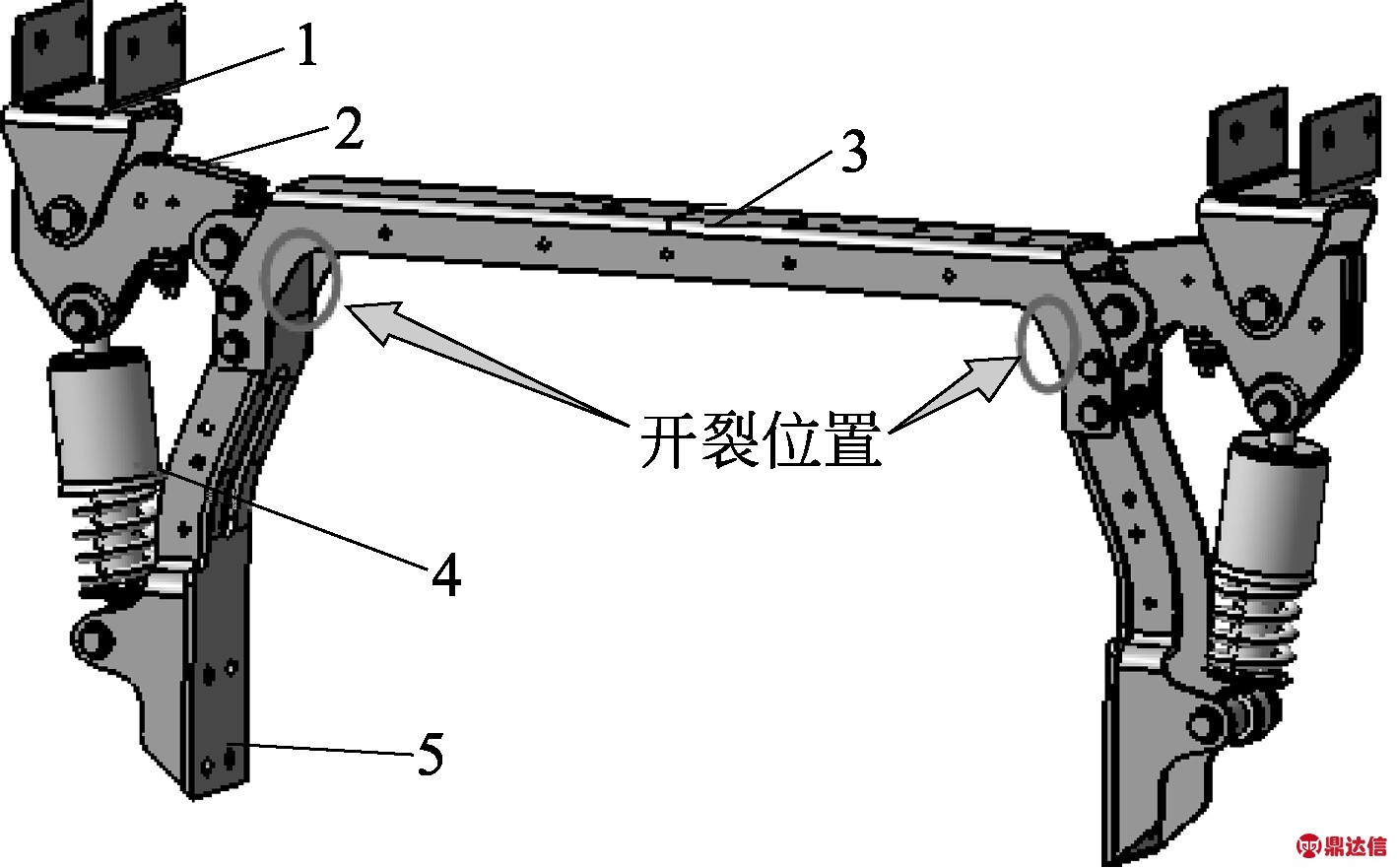
1.上托架 2.摆臂 3.横梁 4.螺旋弹簧总成 5.下支架
图1 驾驶室后悬置
自卸车驾驶室后悬置是位于驾驶室尾部和车架之间的二级减振系统,图1为自卸车整体式后悬置结构,其主要由左右下支架、横梁、螺旋弹簧总成、摆臂、上托架组成,下支架与车架固定连接;上托架与驾驶室固定连接;空气弹簧总成与下支架铰接,上托架、空气弹簧总成分别与横拉杆三者铰接,螺旋弹簧总成以较小的角度倾斜放置,起承载、缓冲、及减振的作用;摆臂与下支架铰接,主要起导向作用,在汽车转弯行驶、侧向风等工况下,承受侧向力,提高驾驶室横向稳定性。
该车在进行强化道路试验过程中,横梁拐弯处出现断裂,如图1所示,可能是结构强度不足造成的结构开裂;也可能是卡车在复杂路面行驶过程中,驾驶室上下跳动,在横梁上循环往复的周期性载荷作用下而产生的疲劳开裂,此时应力峰值虽没达到其屈服极限,但交变应力造成的疲劳损伤累积到一定程度继而产生裂纹[3]。
2 原结构有限元分析
在Hypermesh中建立后悬置有限元分析模型,对原结构在两种极限载荷条件下,运用Hyperworks中的Optistruct求解器对模型进行计算,分析结构应力情况,以找出横梁开裂原因。
2.1 有限元模型建立
驶室驾后悬置由冲压板件通过焊接和螺栓连接装配在一起。悬置材料为T52L钢,屈服极限为355 MPa。因冲压板件长度和宽度尺寸远大于厚度尺寸,故在进行有限元建模分析时可对其抽取中面,用二维四边形以及少量的三角形壳单元Shell进行结构离散,以获得更准确的分析结果,网格大小为4 mm,模型中的工艺倒角、过渡圆角、方便安装附属设备的小圆孔对结构应力没有太大影响,予以简化[4],在螺栓孔等连接处,通过添加Washer的方式提高螺栓孔周围的网格质量,采用RBE2单元模拟螺栓孔连接,主节点为圆孔中心,从节点为孔圆周两圈节点,载荷和约束都施加在圆孔中心的主节点上,这样布置考虑了实际结构中螺母、螺帽的作用,更能准确反映螺母、螺帽与所连接板的受力关系,从而消除部分应力集中现象[5],悬置的约束施加在支架和车架连接的8个螺栓孔上。该有限元模型有22 969个四边形单元,449个三角形单元,48个刚性单元,24 338个节点。
对于驾驶室悬置横梁,最大载荷往往发生在驾驶室上下跳动到极限位置时所产生的载荷,为简化计算,结合具体车型,在ADAMS软件中,给驾驶室一个偏离平衡位置上下移动的强制位移,以模拟驾驶室上下跳动过程中各跳动位置的载荷。上止点载荷:强制驾驶室向上移动到上止点,移动量为驾驶室设计最大跳动量35 mm,此时横梁受最大拉力,悬置上支点和下支点的载荷分别为23 230 N和562.5 N;摆臂水平时的载荷:当驾驶室向下跳动到摆臂成水平位置时,横梁受最大压力,悬置上止点和下止点的载荷分别为4 738 N和3 589 N。横梁受最大拉力的有限元计算模型如图2所示。
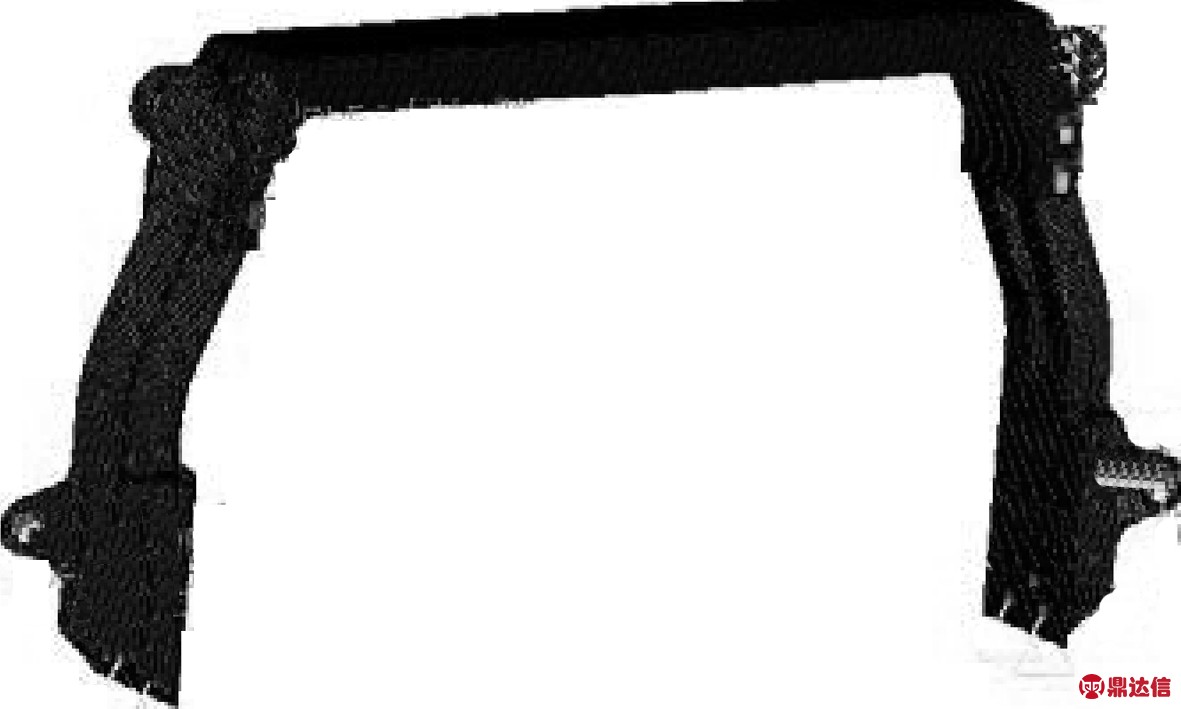
图2 悬置支架受最大拉力时有限元计算模型
2.2 结果分析
在两种载荷条件下,分别求得后悬支架的应力云图,如图3、图4所示,其中当摆臂处于水平位置时,横梁左右承受最大压力,对应的最大应力为69 MPa,远低于材料屈服极限。而当驾驶室向上跳动到最大位置时,最大应力出现在横梁拐弯处,为320 MPa,非常接近材料的屈服极限355 MPa,因在分析过程中考虑的是横梁受到的最大静力,但在实际运行过程中,汽车转弯行驶工况下,横梁还承受巨大动载荷,同时当卡车在路面情况较差的道路上行驶时,驾驶室上下跳动不可避免地会对横梁造成大于静载荷的冲击载荷[6],在此种载荷作用下非常容易造成横梁开裂,这与上述分析的开裂情况相符。
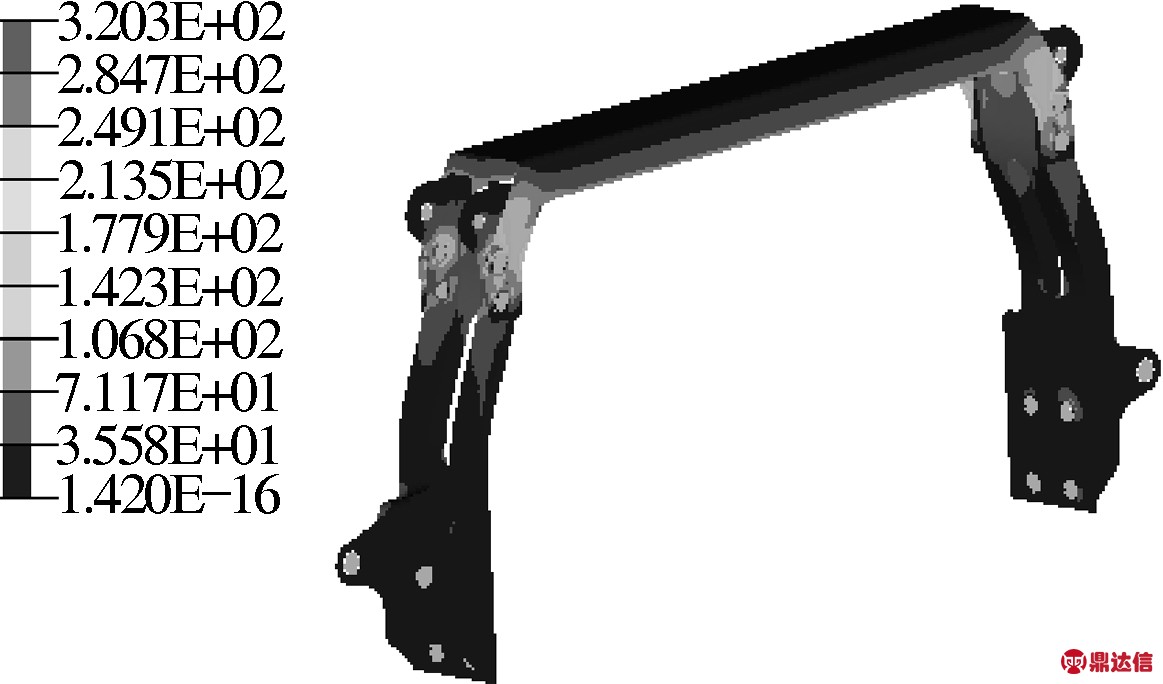
图3 驾驶室上跳最大位置时后悬置应力云图
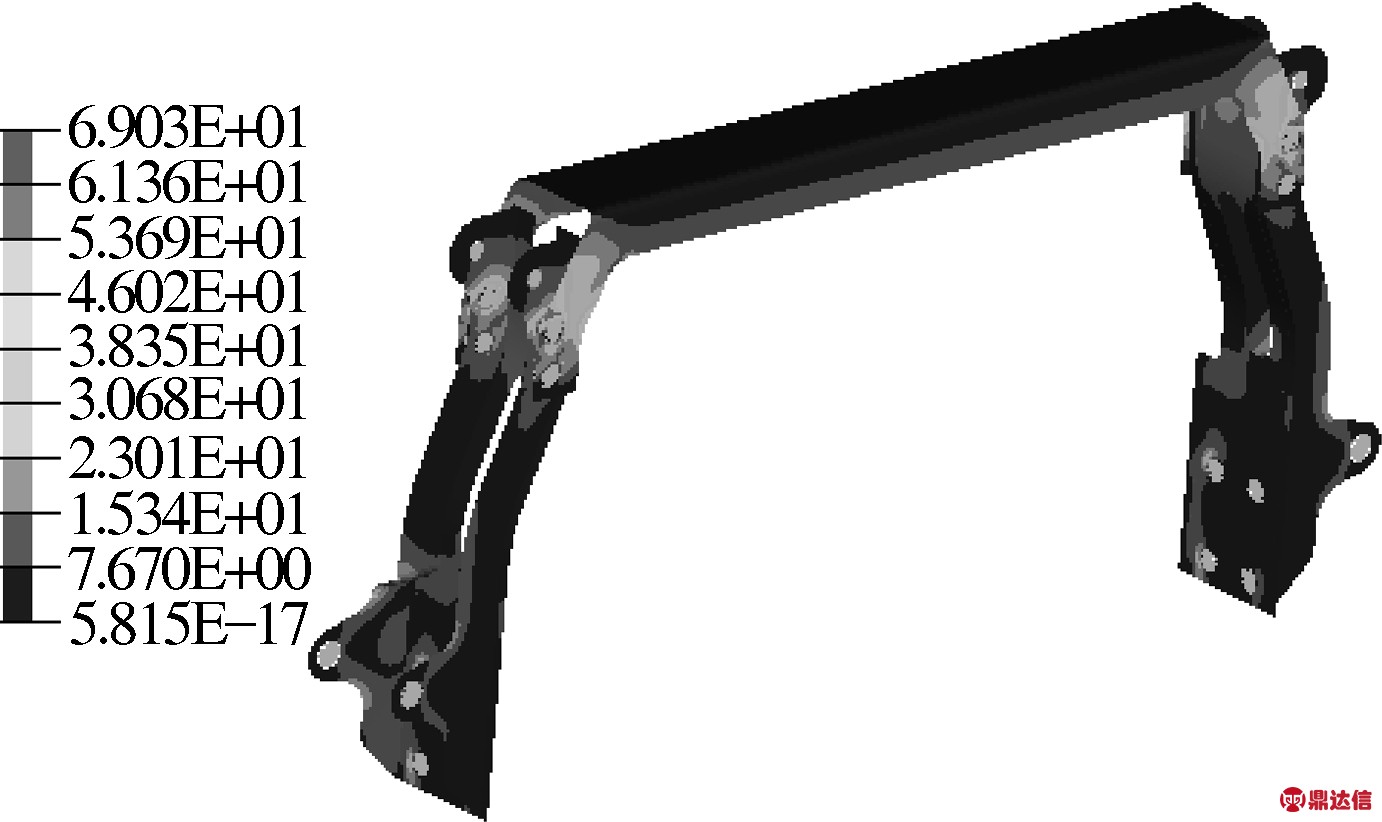
图4 横摆臂处于水平位置时后悬置应力云图
3 后悬置结构改进
随着卡车技术的不断发展,为了提高重型卡车的舒适性,国内外多数重卡厂商纷纷采用四点全浮式悬置系统连接驾驶室和车架,对悬置结构的强度与刚度提出了更高的要求[1],同时为了节能环保,轻量化思路贯穿于汽车产品整个设计过程中,但盲目追求轻量化可能会削弱产品的性能[2],容易造成安全隐患。本文针对某自卸车在强化道路试验过程中,驾驶室后悬横梁(以下简称横梁)拐弯处出现断裂的问题进行分析,找到其开裂原因,并从两方面着手对其进行改进设计:一方面,优化驾驶室后悬置整体结构,以减小驾驶室强制位移下横梁的结构受力;另一方面,通过添加加强板、增加连接件、改变结构几何形状等手段以加强横梁拐弯处的局部刚度。在同等工况下,利用有限元法对横梁改进前后进行对比分析,结果表明,横梁应力峰值下降了48.5%,有效解决了横梁开裂问题,对类似设计具有一定的实际参考价值。
3.1 系统整体结构改进
3.1.1 结构受力分析
如图5所示,在驾驶室上下跳动时,驾驶室在垂直方向上运动,而摆臂以摆臂和横梁的交点为圆心运动,显然二者之间运动轨迹不重合,造成运动不协调[7]。因悬置下支架和驾驶室的刚度较大且不易控制,摆臂一端驾驶室上托架在锁销处刚性铰接,另一端与支架通过橡胶衬套柔性铰接。此种不协调只能由摆臂和横梁连接处的橡胶衬套的变形来弥补,橡胶衬套变形越大,施加在横梁上的力越大。图6为摆臂运动到不同位置的示意图,H为驾驶上跳至极限位置时摆臂两连接点垂直方向距离,b为摆臂水平方向长度。根据几何关系,施加在横梁上的静力

(1)
式中:k为橡胶衬套径向刚度。
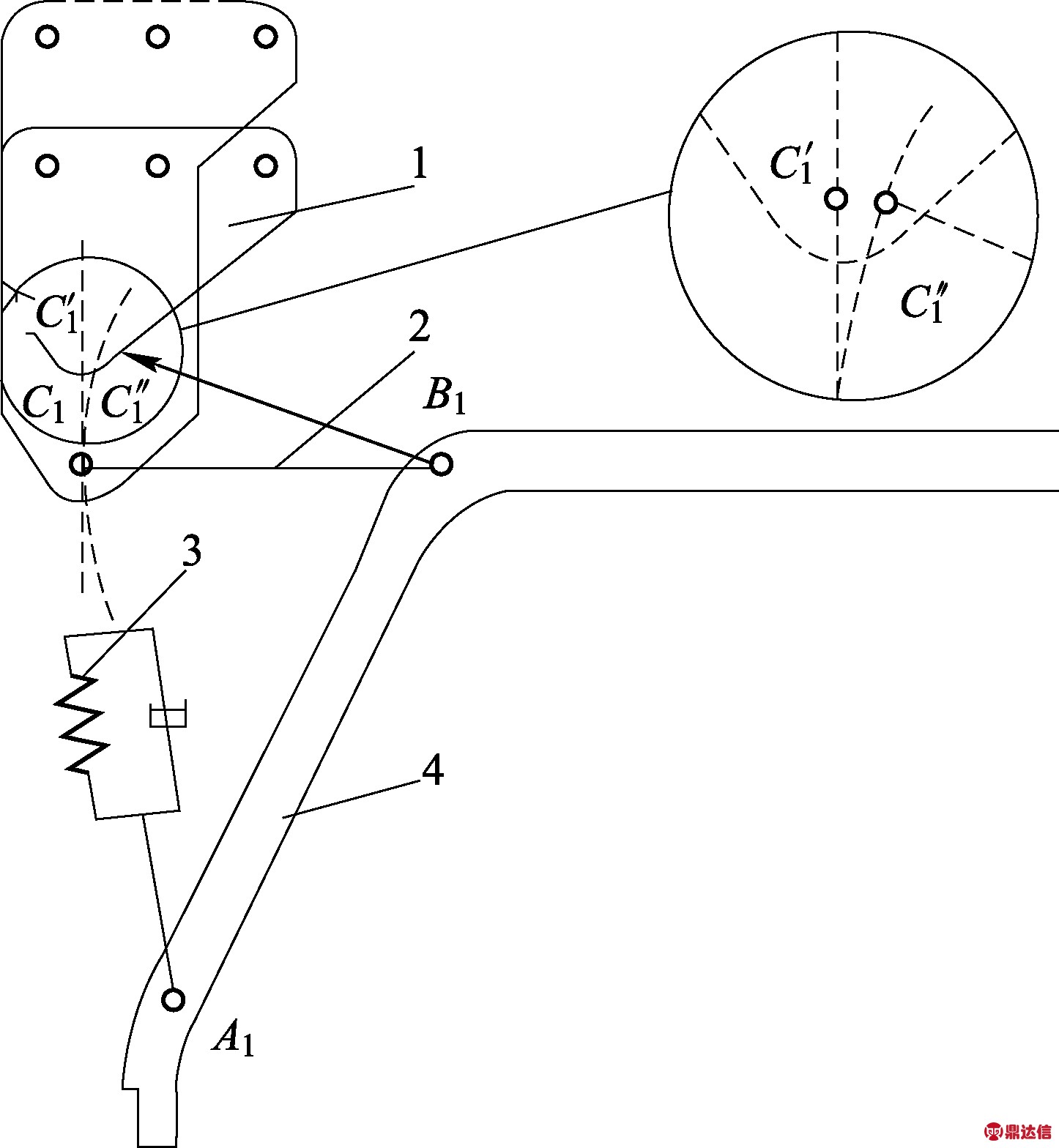
1.上托架 2.摆臂(横拉杆) 3.弹簧减振器 4.下支架
图5 后悬置结构示意图
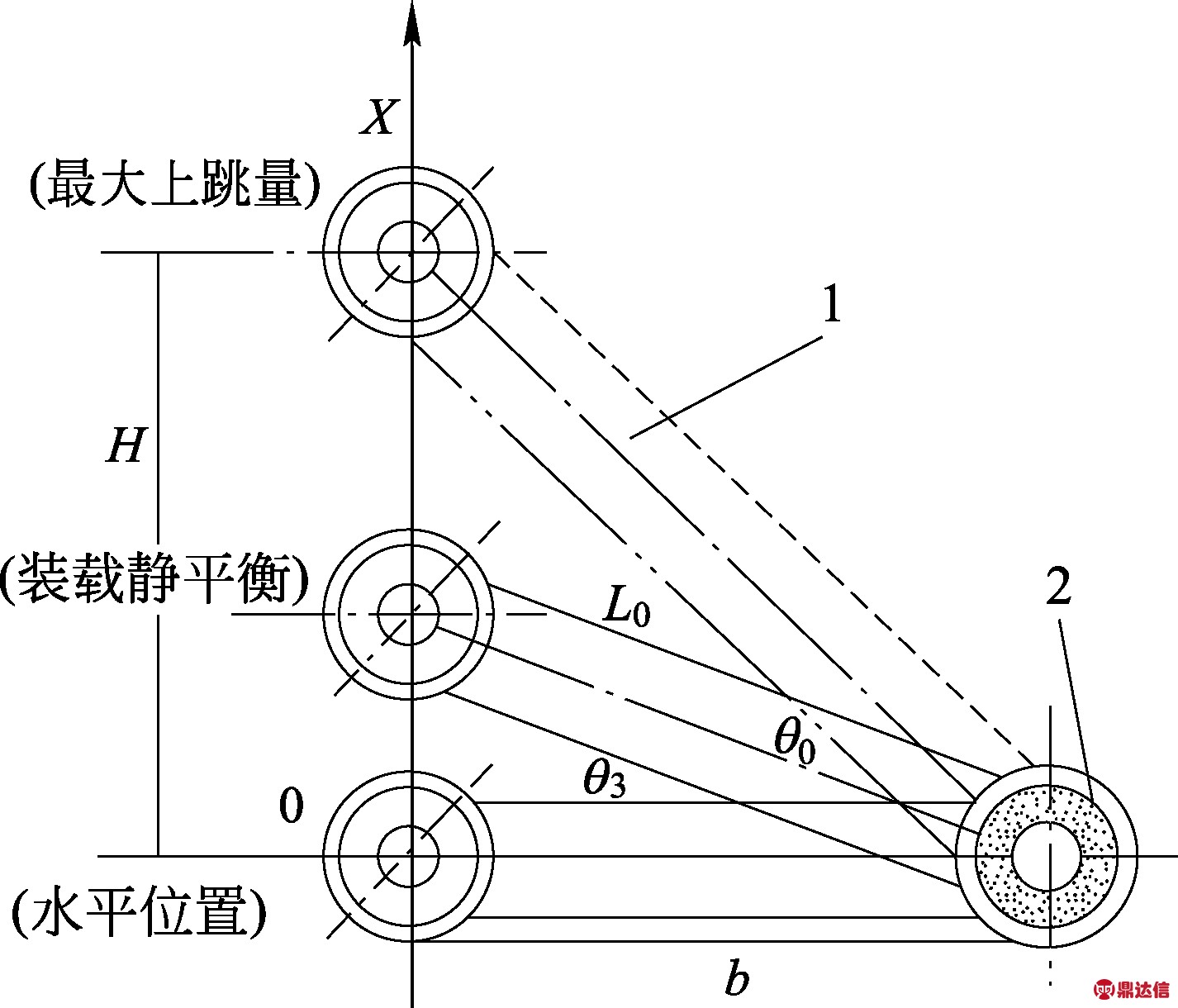
1.摆臂 2.橡胶衬套
图6 摆臂跳动示意图
3.1.2 改进前后载荷对比
根据式(1)可知横梁受力与摆臂长度、驾驶室跳动量和橡胶衬套刚度有关,由于驾驶室的最大跳动量和其他结构相关,不便修改,本文通过调节摆臂长度和橡胶衬套刚度来改善横梁的受力情况。该商用车满载时总质量1 090 kg,后悬置单侧悬置载荷为225 kg,螺旋弹簧刚度为65 N/mm,驾驶室向上最大跳动量为35 mm。表1为后悬置改进前后参数对比,改进后当驾驶室跳动至上极限位置,横梁承受的最大拉力降低了32.9%;当摆臂处于水平位置时,横梁承受的最大压力降低了40%。此外,摆臂的改进设计将对悬置整体刚度造成影响,继而影响驾驶室的舒适性,研究表明该影响是有益的。
表1 改进前后结构参数对比
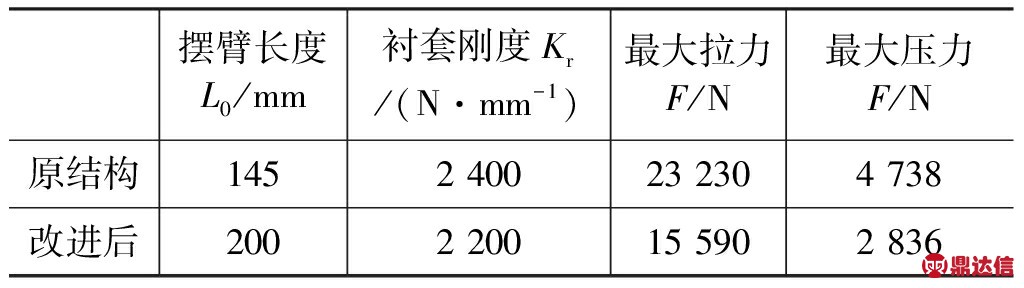
3.2 悬置局部刚度改进分析
3.2.1 局部结构改进
原结构横梁拐弯处钢板较窄,且下支架连接螺栓孔接近,局部刚度不足造成横梁应力过大,进而引发开裂问题。为此在横梁拐弯处添加一加强筋块,将横梁上端和侧端通过缝焊焊接在一起,增加拐弯处局部刚度;在原结构中,摆臂和支架连接销与支架和横梁的连接螺栓是分开的,两者之间有一定距离,来自摆臂的力作用在连接销上,会产生杠杆放大的作用,施加在横梁上的载荷会相应的放大。为此在改进后的结构中,将横梁、下支架与摆臂三者在一点用销轴连接,消除因连接点之间的距离造成载荷杠杆放大的作用。并且原结构为整体式下支架,虽然包含的零件较少,便于装配,但其加工时浪费材料较多。考虑到加工的可行性、物料成本以及工作效率,将原整体式下支架改为断开式,支撑减震器的吊耳通过螺栓与下支架一起连接在车架上,以提高材料利用率、节约成本,并提高生产效率。改进前后对比如图7所示。
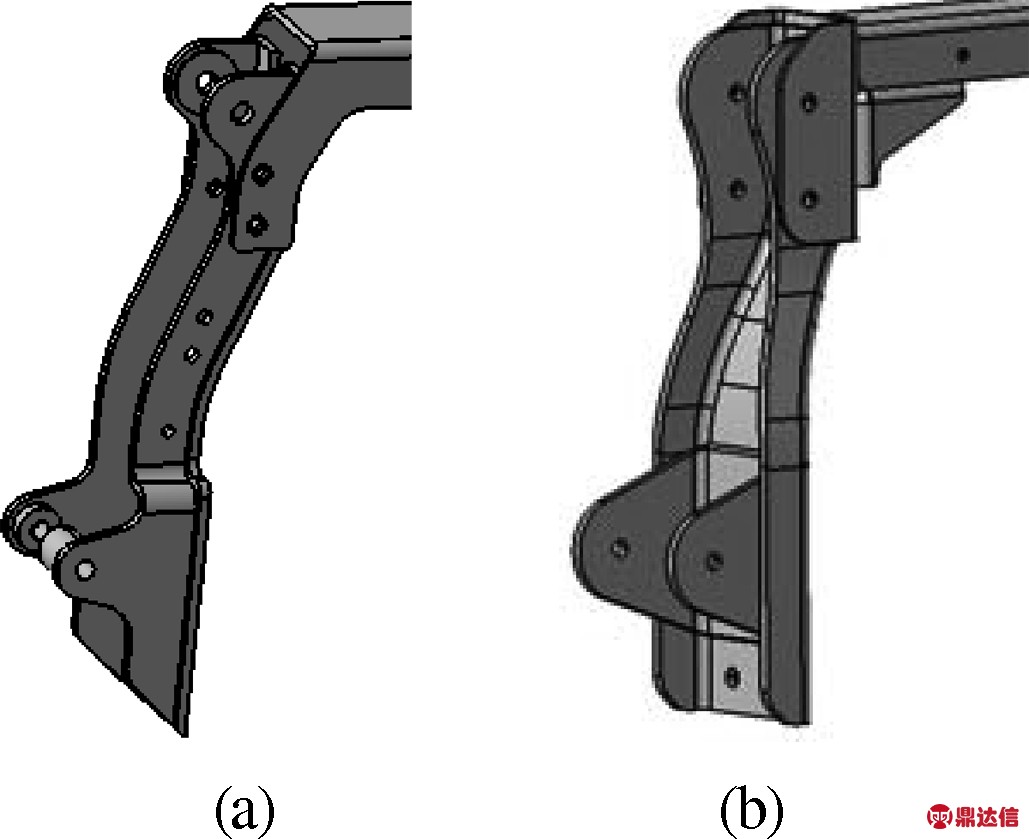
(a)原结构 (b)改进后
图7 改进前后结构对比
3.2.2 悬置改进后有限元分析
为确定后悬置结构改进后的可靠性,运用Hyperworks软件对改进后的结构进行有限元分析。改进后的结构比原结构增加了焊缝单元,为此在建立有限元模型时采用Bar单元模拟焊接结构,Bar单元可以在节点与节点之间建立连接关系,结构几何处理、网格划分参数选取以及约束条件与改进前的结构一致。因横梁受最大拉力时更易造成结构开裂,所以这里只需要对改进后的结构在横梁承受最大拉力时进行有限元分析。改进后的悬置有限元计算模型如图8所示。
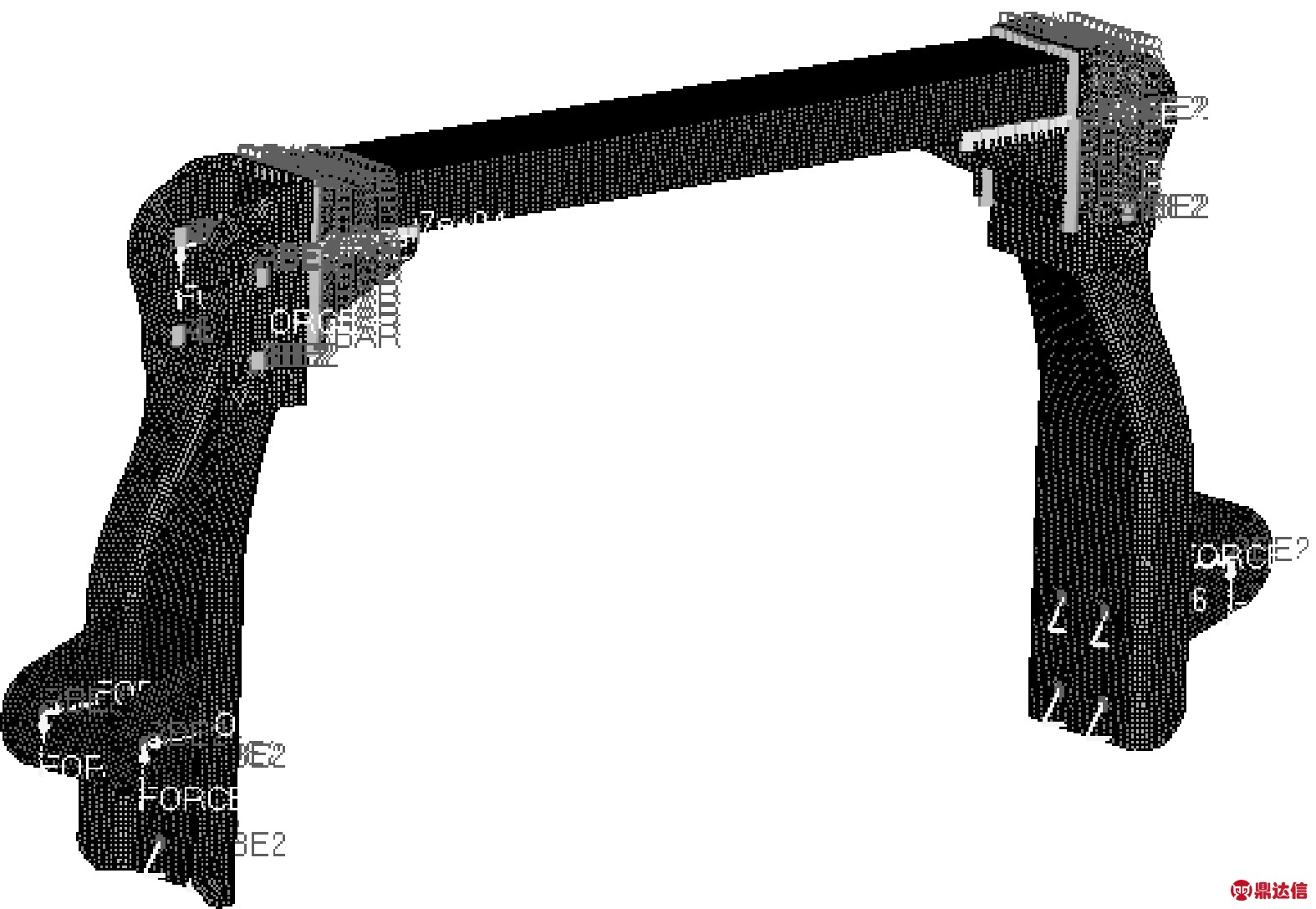
图8 结构改进后有限元计算模型
图9为悬置结构改进之后的应力云图,结构最大应力出现在横梁和支架连接的螺栓孔处,由原来的320 MPa减小为164.9 MPa,相对于材料的屈服强度355 MPa,安全系数为2.15,完全能满足工程应用要求[8]。与改进前相比,最大应力减少了48.5%,能有效解决横梁开裂问题。
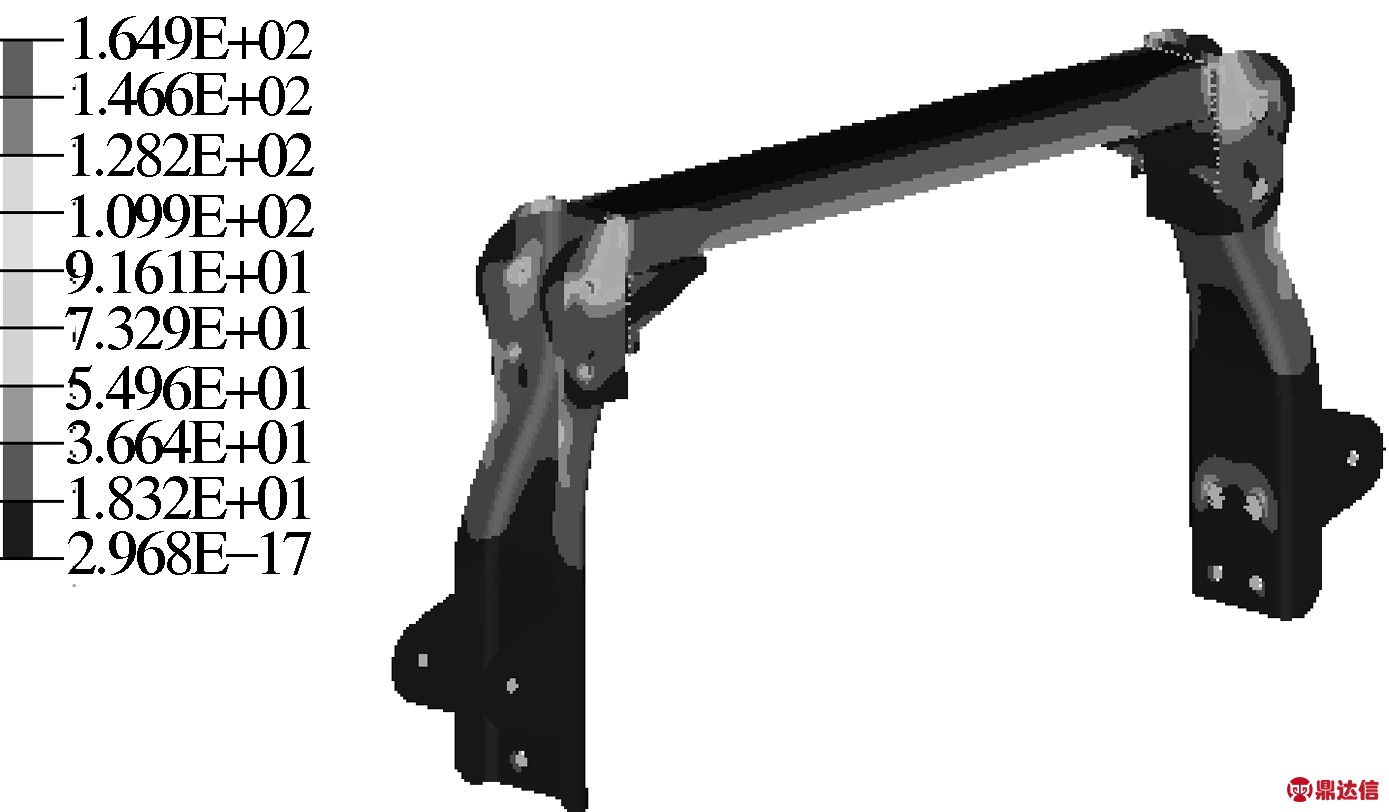
图9 改进后结构应力云图
4 结论
针对某自卸车驾驶室后悬置横梁拐弯处开裂问题,首先,在Hyperworks中对其进行有限元分析,找到了开裂原因;其次,对后悬置结构进行了分析,通过改进整体系统结构,降低了驾驶室后悬置最大载荷;然后,通过调整后悬置局部结构,加强了后悬置拐弯处局部刚度;最后对改进后的结构进行有限元分析,最大应力情况得到明显改善,对改进后的结构进行了样车道路试验,未产生上述横梁开裂问题。在以后的工作中可采集路面振动谱获取动态载荷对该车驾驶室模型进行多体动力学分析,能更准确反映悬置的受力情况。