摘 要:为了提高1 6 0 0t螺旋压力机横梁的综合力学性能,本着设计理念高起点、设计要求高起点的原则,在不改变横梁外形、长度、宽度、高度的条件下进行优化设计,设计了三种不同的横梁内部结构,通过C A D/C A E集成模拟设计平台,对它们进行了静态动态力学性能分析,根据分析结果选出最佳的设计方案。在改变设计结构的情况下可以提高螺旋压力机横梁的刚度、降低应力,同时应尽量提高横梁固有频率,降低传递打击能量时对机身的破坏,提高机床的使用寿命,同时固有频率的提高能减少振动耦合的发生。
关键词:电动螺旋压力机;C A D/C A E有限元法;静态动态性能;固有频率;振动耦合
1 概述
1.1 目前我国锻造行业设备状况
近些年,我国锻造行业飞速发展,厂家众多,但与国外相比较,大多设备落后,效率低下,虽然一些大的锻造厂拥有一些世界上较先进的设备,但对于大多数中小企业,锻造设备总体水平依然落后,导致材料及能源消耗高,产品质量差,污染严重,严重影响了企业的竞争力。特别一些高档精密锻件的制造与国外还有一定的差距。
1.2 模锻件常用的成型设备
模锻锤:蒸汽(空气)锤、速控全液压模锻锤;机械压力机:新型多工位压力机、曲柄压力机、楔横轧机等;模锻液压机;螺旋压力机:摩擦压力机、电动螺旋压力机、液压螺旋压力机、高能螺旋压力机。
1.3 摩擦压力机介绍
目前国内主要的模锻设备仍然是一次性投资较少的摩擦式压力机,而在国外摩擦式压力机大多已淘汰。在摩擦压力机的使用中,由于能量不能精确控制,所以在很多情况下摩擦压力机都处于超载运行状态,造成机身、螺杆等机械部分的损坏。设备在使用过程中,可靠性差,维护成本高,能耗高,将逐步被电动螺旋压力机所取代。
1.4 电动螺旋压力机原理及特点
如图1所示,电动螺旋压力机是利用飞轮储存的能量,通过螺杆、滑块的传递,最终使工件变形的锻压设备。适用于工件的热态模锻、精压、校正、弯曲、压印等工序,是火车、汽车、拖拉机、船舶、航空、五金工具、医疗器械、餐具等行业理想的锻造设备。具有如下优点:1)结构简单维护方便。电机通过皮带直接带动飞轮正反转,通过螺旋副驱动滑块上下运动,易损件少,维护费用低。2)产品成型重复精度高。电机转速可以任意设置,因此滑块的打击力和打击能量可以在允许范围内任意设置,打击力、打击能量输出稳定,从而保证了批量工件的成型重复精度高。3)高效节能。本机采用开关磁阻电机调速系统直接驱动飞轮,具有最短的传动链。其突出特点是效率高、无起动冲击电流、节能效果好,可节能50%左右。4)自动化程度高。控制系统采用PLC可编程序控制器控制,人机界面(HMI)触摸屏操作,控制精度高、操作方便。5)安全性高。采用电机、机械双重制动,保证滑块在全行程任意位置停止。

图1 电动螺旋压力机示意图
2 电动螺旋压力机横梁的优化设计
2.1 横梁优化设计的原理
横梁是电动螺旋压力机的重要部件,其结构的静态动态性能指标将直接影响到机床的寿命、加工精度、精度稳定性、生产效率等问题,为保证机床高打击力、高效、高精度、高强度和轻量化的设计要求,床身必须具有足够的静态刚度和良好的动态特性。横梁的静态、动态特性与其结构尺寸、形状和筋板布局有着密切的关系。本文研究的电动螺旋压力机的横梁,是在保证装配尺寸,保证不改变横梁外形、长度、宽度、高度的条件下进行设计。图2所示为1600 t电动螺旋压力机横梁结构图。设计出不同的筋板结构对比传统电动螺旋压力机横梁变形、应力、固有频率,筛选出最优的结构方案。
2.2 横梁优化设计的方案
针对1600 t电动螺旋压力机横梁设计了3种不同的筋板结构。方案一(原方案)壁厚70 mm,方案二是在方案一的基础减小壁厚,在拉筋孔处增加筋板,筋板厚度50mm。而方案三在方案二的基础上增加“井”筋板结构,筋板的厚度为50 mm。底座材料牌号为ZG270-500,弹性模量190 GPa,泊松比0.3,材料密度7800 kg/m3。图3~图5分别为方案一~方案三参数化建模后的3D实体模型剖视图。
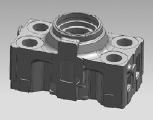
图2 1600 t横梁
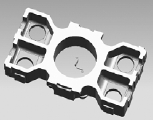
图3 方案一参数化模型
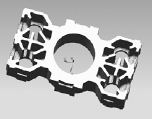
图4 方案二参数化模型
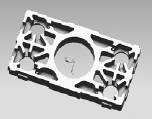
图5 方案三参数化模型
2.3 横梁优化后的有限元分析
利用CAE有限元法进行分析,划分网格单元格大小75 mm,对横梁底面与立柱接触的面进行固定约束。对每个拉筋孔施加螺栓预紧力12 MN,止推轴承接触面施加16 MN的压力。计算求解,静态分析结果如表1所示,动态分析结果如表2所示。
表1 静态分析
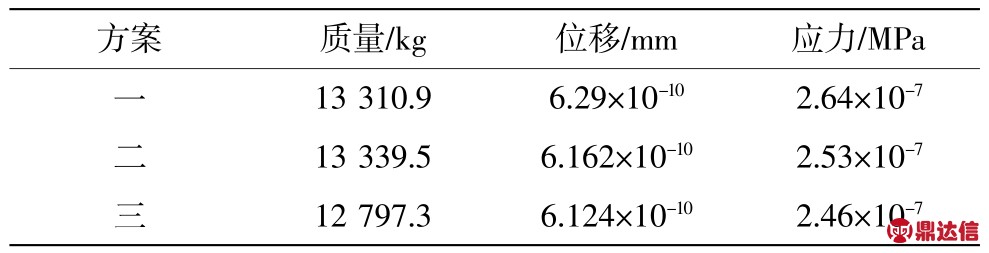
表2 动态分析(阶段4固态频率) Hz

图6~图8分别为方案一~三的位移分析结果视图,图9、图10、图11分别为方案一~三的应力分析结果视图。
从上述静态、动态分析结果可以看出方案一的质量12 797.3 kg,质量最低,应力主要集中在拉筋孔口处,最大变形也主要在拉筋孔口处。方案三应力2.46×10-7MPa、位移6.124×10-10mm均最小。材料ZG270-500的屈服强度270 MPa,锻压机床设计安全系数取2.0计算,许用应力135 MPa,三种方案的最大应力均远远小于许用应力,满足设计要求。从表2动态分析结果可以看出,方案三在阶段4的固态频率576.3 Hz,为3种方案最高。我们知道频率越高在作为能量传播载体的情况下破坏力越低,因此方案三对机床本身的破坏力最低,有力于提高机床的使用寿命。阶段4振型的振幅由下向上逐步增加,该振型影响横梁下底面与底座上平面的平行度,从而影响模具的使用寿命和锻件竖直方向的精度。从表1可以看出方案三的质量12 797.3 kg,质量最低,而静态变形、应力最小,说明刚度在3种方案中最高,无疑是设计方案的最佳选择。图12所示为方案一阶段4位移视图。
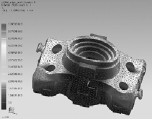
图6 方案一位移视图
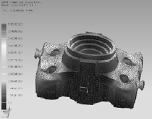
图7 方案二位移视图
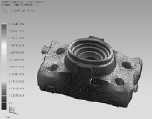
图8 方案三位移视图
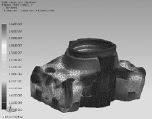
图9 方案一应力视图
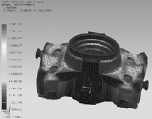
图10 方案二应力视图
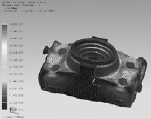
图11 方案3应力视图
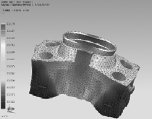
图12 方案一阶段源位移视图
3 结语
本文在保证不改变横梁外形、长度、宽度、高度的条件下设计了3种不同结构的螺旋压力机横梁内部结构。方案二、方案三都设计了筋板,不同的是方案三的筋板比较多、厚度比较薄,而方案一没有设计筋板,壁厚70 mm最厚。通过有限元法对3种结构的静态动态特性进行分析,说明在改变设计结构的情况下可以实现提高螺旋压力机的刚度,降低应力同时应尽量提高横梁的固有频率,降低传递打击能量时对机身的破坏,提高机床的使用寿命,同时固有频率的提高能减少振动耦合的发生。方案三的质量最低有利于实现横梁轻量化的设计。利用CAD/CAE集成化模拟分析软件,我们对电动螺旋压力机的主要部件横梁、拉筋、立柱、滑块、飞轮、螺杆等均进行了结构的优化,提高了部件的刚度、固态频率。有效地保证了机床的打击力,提高了机床的使用寿命。