摘要:为了解决零散井站点的天然气和原油在分离过程中,因为不能自动调节和控制分离器内的液位,造成天然气进入储油罐或原油进入气管线的难题,利用分离器现有的部件,通过加装干簧管远传、数显表、记录仪、电磁阀、报警器等仪器,研发制造出了一种分离器液位自动控制系统。该系统具有自动化程度高,实现了分离器自动完成气液分离,连续计量及液位超限报警等功能,避免了现有技术需要人工操作,值班员工24小时盯住液位计进行量油,一旦值班人员精力不集中,将会造成天然气管线内进入液体,储液罐内进入天然气等事故的发生。
关键词:自动控制;信号远传;运行安全;降本增效
中图分类号:TE977
文献标识码:B
在油田开发过程中有大量的区块含油面积小,呈零散分布,区块间生产的油气不能进行汇集处理,只能在井站点自行气液分离,液体进入储液罐,通过罐车外运,天然气除自用外,多余的气量供给附近的用户。通过人工来调节排液阀门的开度,使分离器进、出液量在相对时间内保持平衡,但因油井生产状态及用户用气量的不同,使分离器进、出液量不平衡,当进液量多,出液量少时,就会发生分离器内的液体进入到天然气管线内,堵塞气线,不但损坏设备造成经济损失,而且降低企业的声誉;当进液量少,出液量多,气、液一同从排液阀中排出,进入到储液罐内,使大量的天然气外泄,既损失了气量又对环境造成污染,还造成了安全隐患。针对以上所述的困难,应研发、设计一种具有高度自动化分离器液位自动控制系统,从而解决现有技术中的难题。
一、改进思路及方案实施
1.设计思路。将分离器液体排出阀由普通阀门改为自动控制开关的电磁阀,原来由人工操作控制的分离器液位高度,实现由电信号自动控制,同时该系统具有自动报警功能,在值班室设有报警装置,当分离器计量排液系统不能自动排液,分离器内的液位超过上下警戒位时,报警系统开始启动运行,发出声光警报,提示工人及时进行排除。
通过在现有的计量系统基础上进行改动,在实现以上功能的同时,做到既不违反安全规定,又尽量减少投入。尽量利用分离器现有的磁翻板液位计中的功能,根据磁翻板液位计内的磁浮标随分离器内液位高低发生移动,磁浮标移动到什么位置,就在什么位置发出磁力线的特性,在磁翻板液位计上下计量标高处及在分离器上下液位警戒位处磁感电器元件,当磁浮标达到计量标高时,磁感电器元件在磁浮标磁力线的作用上,通过仪表转换成控制电磁阀的电信号,实现分离器排液阀门根据高度的设定值实现自动开关;如果出现故障不能自行关闭和开启排液阀时,磁浮标将继续上行或下移,到达分离报警高度时,磁感电器元件转变成报警信号,值班室内的警铃或警灯开始运行,警示值班人员去排除故障,故障不排除,警示不停。
2.组成及特征。分离器液位自动控制系统主要由分离计量系统、信号传输系统、自动排液系统、液位报警系统四大部分组成,主要包括磁翻板液位计、干簧管远传、数显表、记录仪、电磁阀、报警器、各种连接导线等部件。
(1)分离计量系统由磁翻板液位计、干簧管远传、数显表、记录仪及导线组成。磁翻板液位计与分离器构成一个连通器,磁翻板内磁浮标随分离器内液位的位置同步移动,始终与分离器内的液位保持同一高度。干簧管远传与磁翻板紧贴在一起,干簧管内的阻值的大小与磁浮标联动。当分离器内的液位在计量下限时,在液位计磁浮标的磁力线的作用下,干簧管远传发出信号,关闭分离器的出液阀门,开始计量油井产量,同时值班室内的数显表显示出罐内液位高度,当液位达到计量上限时,在液位计磁浮标的磁力线的作用下,干簧管内发出不同阻值的远传信号,记录仪根据收到的到量油信息,计算出产油井的产液量,并对量油数据进行储存。
(2)信号传输系统由干簧管远传、数显表、记录仪及导线组成。干簧管远传设有计量下限、计量上限、报警下限、报警上限四个信号传输点。液量计量时,记录仪发出计量信号,分离器内的液位低(高)于计量下限时关闭(打开)排液阀,当分离器内液位达到计量下限时,干簧管远传发出信号关闭分离器排液阀,数显表显示分离器内液位高度,记录仪读取量油信息,计算产液量,值班人员在值班室内就可以在仪器的显示仪上时时观察到各种数据,借助现代化通讯设备还能够实现数据远传,让技术人员随时了解单井点的数据信息。
(3)自动排液系统由干簧管远传、电磁阀、记录仪及导线组成。分离器排液时,当分离器内液位到达计量下限时,干簧管远传在液位计磁浮标磁力线的作用下,发出电信号,导通电磁阀的控制电机,使电子手轮旋转,关闭分离器的排液阀,对油井产量进行第二次计量,记录仪开始工作,当分离器内液位到达计量上限时,排液阀开启排出液量,记录仪根据量油时间计算出液体产量,通过设定,实现全天对油井产液量的计量。
(4)液位报警系统由干簧管远传、报警器及导线组成。当排液阀门不能及时开启,将造成分离器内的液位持续上升,当液位达到天然气出口时,产出液将进入天然气管线内,给天然气用户造成损失。分离器排液时,当液位到达计量液位下限时,排液阀不能自行关闭,液位降到排液口时,气、液将一同进入储液罐内,造成气量损失,严重时还会造成环境污染。为防止出现以上事故,在磁翻板上设有报警下限标记和报警上限标记,当分离器内的液位达到报警上下限标记时,在液位计磁浮标磁力线的作用下,发出报警信号,安装在值班室内的报警器,将会发出声光警报,直至值班人员发现并排除故障后,报警才能停止。
二、分离器液位自动控制系统的构结及原理
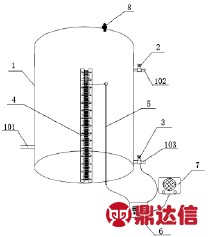
图1 液位自动控制系统结构图
1.分离器进液位2.天然气出气位(阀)3.分离器排液位(阀)4.磁翻板液位计5.干簧管远传6.数显表、记录仪(安装在值班室)7.声控报警器
1.分离器液位自动控制系统的示意图。
2.分离器液位自动控制系统的功能。
功能一:实现了对分离器内液面高度的自动控制,保证了分离器内的液位在适当的范围之内,杜绝了气体进入储液罐和液体进入气管线现象的发生。
功能二:实现对油井产液量全天24小时的计量与记录,为油井产能的变化分析提供了依据。
功能三:具有对分离器内液面的监控功能,当分离器内的液位超过警戒位时,就会通过声控和灯光进行报警,提示操作人员及时进行处理。
3.分离器液位自动控制系统的工作原理。液量计量的工作原理,工作人员通过记录仪6发出计量信号,干簧管远传5通过磁翻板液位计4测出液位的位置,分离器内的液位低于计量下限时,干簧管远传电阻件发出信号关闭出油阀,当分离器内液位达到计量下限时,干簧管远传的电阻组件503发出信号,数显表、记录仪6将收到的阻值信号转变为电流信号并开始记录量油信息,对油井的产液量进行计量。当液位达到计量上限时,电阻组件504发出信号,数显表、记录仪6将收到的信息进行分析,并计算出油井产液量,同时将转信号进行转变为电磁阀的控制信号,打开分离器排液的电磁阀,将分离器的液体排入储油罐内,当分离器内的液位到达分离器下限时,干簧管远传的电阻组件503又发出信号,分离器排液电磁阀再次关闭,进行下一次的液量计量。
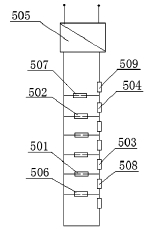
图2 干簧管远传工作原理图
当分离器内的液位高于计量下限时,干簧管远传电阻件发出信号打开排液阀,当分离器内液位达到计量下限时,干簧管远传的电阻组件503发出信号,关闭分离器排液阀。自动控制系统中数显表、记录仪6将开始对油井产液量再次进行计量。当班工人可以根据不同油井的量油要求,对数显表、记录仪6进行设定,确定量油次数,取得精确的油井产量信息。
分禽器内液位高度的控制原理:为了确保分离器连续工作和外供天然气平稳运行,分离器的进液量与出液量要保持平衡,使分离器内的液位保持在一个合理的位置。该系统通过以下原理实现分离器液位的控制,当分离器进液量少于排液量时,分离器内的液位下降,当降到电阻件503的位置时,干簧管远传5发出信号给记录仪6,记录仪6通过计算,将信号转换为分离器排液控制电磁阀的控制信号,调小阀门开度,减小排液量。当进入分离器进液量大于排液量时,分离器内的液位上升,当升到电阻件504的位置时,干簧管远传5发出信号给记录仪6,记录仪6将信号转换成开大分离器气排液电磁阀3的控制信号,调大排阀的开度,加大排液量,使分离器内的液位始终保持在一个合理的位置高度。当排液阀打不开(关不上),分离器内的液位持续上升(下降),当分离器内液位高度到达电阻件509(508)的位置时,干簧管远传5发出信号给数显表、记录仪6,数显表、记录仪6将信号转换后,发给安装在值班室内的报警元件7,报警元件7持续发出声、光预警声信息,提示值班人员进行故障排除,直至故障解除后,预警信息才终止。
三、分离器液位自动控制系统推广应用及创效情况
分离器自动液位控制系统研制成功后,分别在华北油田务3、务4等零散的井站点上进行了使用。经过一年多的应用,不但能够完成对油井产液量的自动计量,而且还实现了根据分离器进液量的变化自动调节出液量的多少,使分离器内的液位保持在合理高度。原来需要通过人工完成的工作,现在通过分离器液位自动控制系统自动完成,不但减轻了岗位员工的劳动强度,而且提高了运行安全系数,降低了液体进入天然管线和天然气进入储油罐内故障的发生率。每套系统每年平均可以减少一个人员的工作量,减少天然气损失5万方,年创效50余万元。该技术应用一年多,已经趋向成熟,具备了进行推广条件,可以向具备条件的油气生产场所进行推广应用。
四、结束语
分离器自动液位控制系统利用电子元器件实现了分离器液位的自动控制,产液量的自动计量及分离器液位警戒线的报警功能。该套液位自动控制系统装置在应用过程中,不但降低了员工的劳动强度,减少了用工量,而且与原来人工操作相比计量准确,运行安全,具有良好的运行前景。