摘 要: 通过Fluent软件对滚塑成型托盘的模内冷却过程进行了数值模拟,目的是为了研究托盘上进气孔和出气孔的间距、个数、布置方式以及出气孔的直径对模内冷却时间的影响。结果表明,增大进、出气孔的间距可以缩短模内冷却时间;为得到较好的模内冷却效果,进气孔的总面积不能小于出气孔的总面积;在只有1个进气孔和1个出气孔的情形,当出气孔直径减小到进气孔直径的79 %时,模内冷却时间最短,如果继续减小出气孔直径,模内冷却时间反而急剧增大。
关 键 词: 滚塑成型;托盘;模内冷却;数值模拟;Fluent软件
0 前言
目前几乎所有的滚塑工艺在冷却过程中,都是利用外界空气或者水雾等冷却介质与模具外壁面进行对流换热以带走模具和塑料制品的热量。这种传统的冷却方式有2个缺点:一是传热效率比较低,致使冷却过程所花费的时间乃至整个滚塑工艺的成型周期都比较长;二是塑料制品在冷却过程中其内外壁面的温度差较大,从而生成显著的残余应力,使得塑料制品变形较大,无法满足尺寸精度[1]。
模内冷却技术是指在滚塑的冷却阶段开始后,当外部环境对模具进行冷却时,将空气或其它冷却介质以一定的压力打入塑料制品的内部空腔,这样塑料制品可从内、外两侧同时受到冷却,使得冷却效果比较均匀。这就减小了塑料制品内部的温度梯度和残余应力,因此变形也就受到抑制。另外冷却过程所花的时间以及滚塑成型周期也会缩短。文献[2]给出了1个采用压缩空气对塑料制品进行内部冷却的实验装置示意图,并认为模内冷却可以将滚塑的成型周期减少大约14 %。文献[3]展示了现有研究中采用空气、液氮、冷却水进行模内冷却的示意图,并分析比较了在这些研究里滚塑成型周期减少的百分比以及每种模内冷却方式的优缺点。
从以上文献可以看出,目前的滚塑模内冷却主要是集中在实验研究,而很少有基于数值仿真的理论研究。究其原因是如果要得到准确的计算结果,所建立的理论模型比较复杂,数值计算量很大。从传热机理来看,此时外界环境与模具外壁面之间的对流换热、模具自身的导热、模具内壁面与塑料制品外壁面间的接触导热、塑料制品自身的导热、塑料制品内壁面与模内冷却介质之间的对流换热需要耦合起来求解。而且同时还要考虑塑料制品自身的冷却结晶过程引起的相变换热。目前本文只发现Sun等[4]对滚塑模内冷却进行了数值仿真,他们将内部空气的温度设置成一个恒定值,然后假定一个塑料制品内壁面与内部空气间的对流换热系数。通过这种简化处理,计算区域就不再包含塑料制品的内部空间,即不需要考虑在内部空间里空气的流动与换热,塑料制品内壁面与内部空间之间的对流换热只要在该内壁面上设置第三类热边界条件即可得以实现。所以数值计算的难度和工作量都大大下降。但实际上在模内冷却进行的过程中,模内冷却介质的温度随时间总是在变化的,因此该传热模型与实际情况差异较大,而且也无法得出模内冷却效果与滚塑制品内部结构之间的关系。
本文为滚塑成型托盘的模内冷却过程建立一个简化的流动与传热模型。通过数值仿真来研究托盘上进气孔和出气孔的间距、个数、布置方式以及出气孔的直径对托盘模内冷却时间的影响,所得计算结果可为托盘上进气孔和出气孔的结构优化设计提供理论依据,以得到最佳的模内冷却效果。
1 流动与传热模型
本文所研究的托盘是1个通过滚塑工艺制造出来的中空的塑料制品。图1所示的是该托盘内部空腔所占据的空间区域。为进行模内冷却,需要在滚塑模具上对应托盘底面的地方开出一些进气孔和出气孔,然后将室温的空气以一定的压力从进气孔打入托盘的内部空腔,在其中流动,最后再从出气孔流出并带走热量。
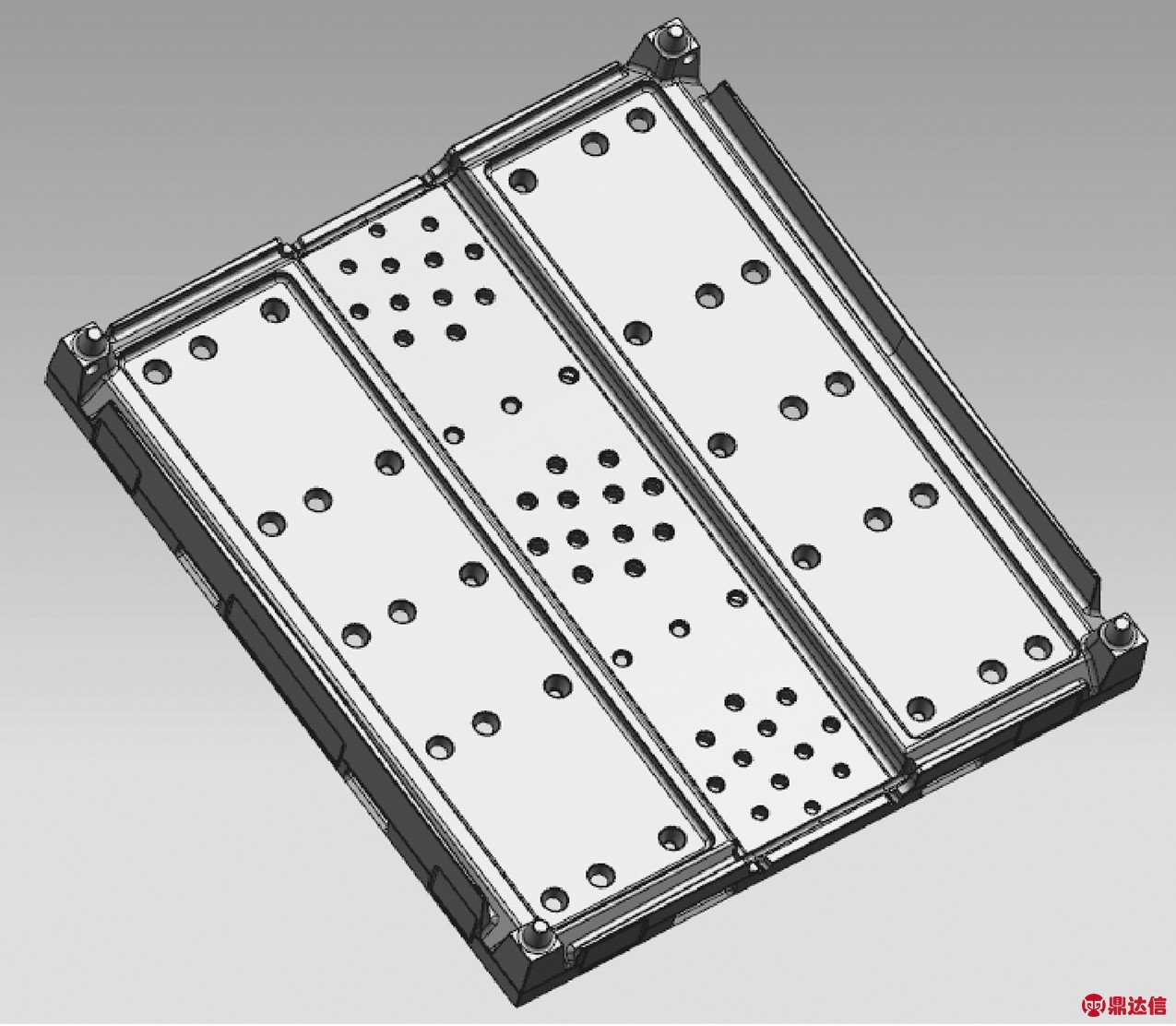
图1 托盘的内部空腔所占据的空间
Fig.1 Space occupied by internal cavity of the pallet
在本文的流动与传热模型里假设托盘内部空腔的表面—托盘的内壁面是绝热的,因此数值仿真的区域就是图1所示的托盘内部空腔所占据的空间体积,不包括托盘本身,也不包含模具。由该简化模型仿真所得的模内冷却过程所花费的时间与实际值相比肯定会有较大的差异。但因为本文只研究模内冷却时间与托盘上进气孔和出气孔的个数、位置、大小的关系,而不研究外界环境、模具、托盘这三者间的换热对模内冷却时间的影响,因此这个简化假设带来的误差只会影响模内冷却时间的绝对值,而不会影响模内冷却时间随上述进、出气孔结构因素的变化趋势。
如图2所示在托盘底面上开出的进气孔和出气孔的位置A、B、C、D、E。如表1所示,由这5个位置组合出本文所研究的7种情形。在表1中,对应于某一情形,在进气孔位置和出气孔位置的栏目里均未出现的英文字母表示在图2里该字母所指示的位置处是封闭的,没有开任何孔。
表1 与不同进气孔和出气孔的位置对应的7种情形
Tab.1 Seven cases corresponding to different locations of air inlets and outlets
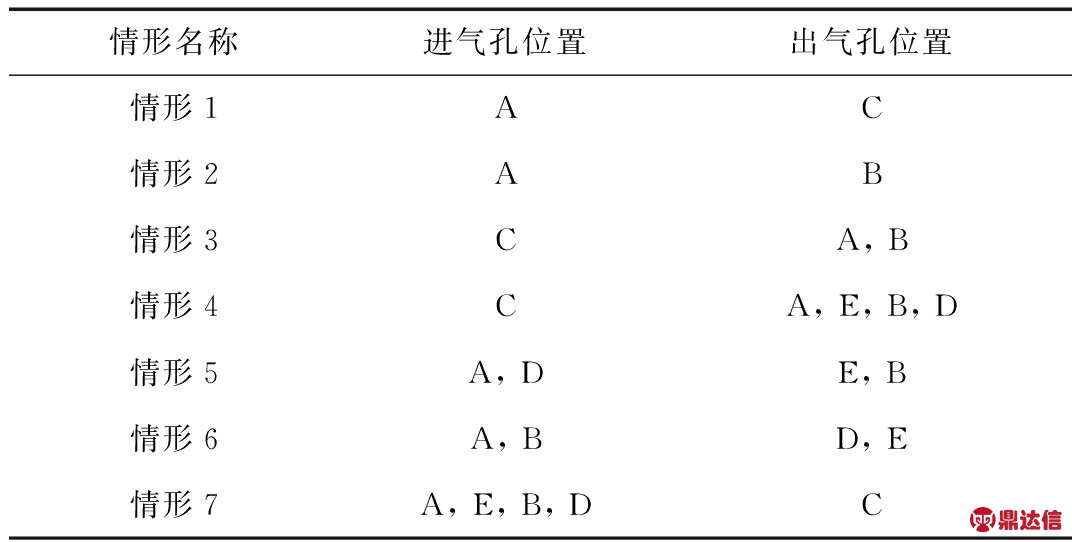
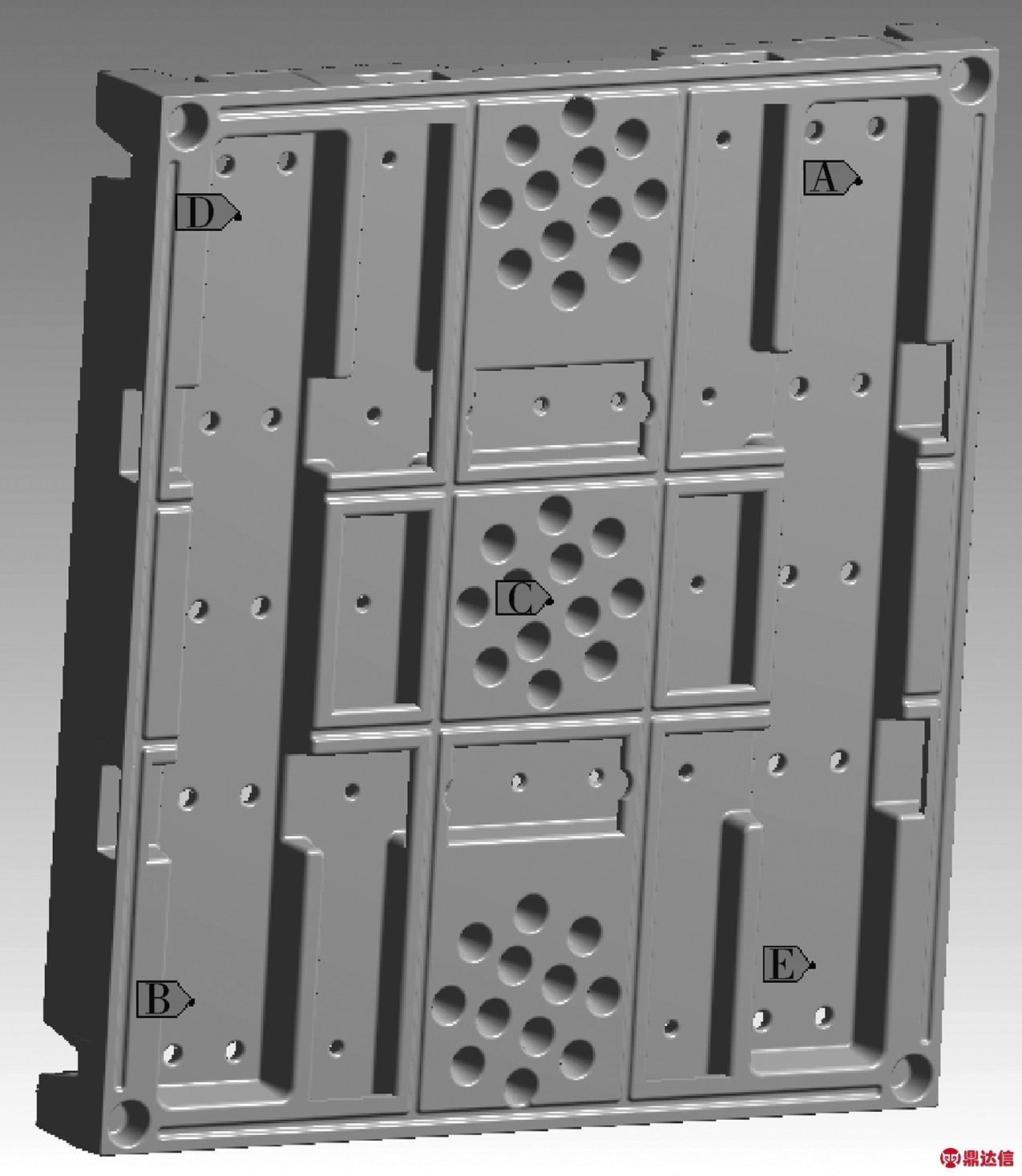
图2 在托盘底面上进气孔和出气孔的位置示意图
Fig.2 Schematic of locations of air inlets and outlets at the bottom of the pallet
进气孔的直径保持为14 mm,进气流量保持为40 L/min,进气温度保持为27 ℃。托盘内壁面的初始温度为200 ℃。托盘内部空腔里空气的初始速度为0 m/s,初始温度为200 ℃。这是因为研究表明当内部空气的温度达到200 ℃时开始进行冷却,滚塑制品可以获得较好的力学性能[5]。模内冷却时间定义为托盘内壁面的平均温度从200 ℃下降到60 ℃时所花费的时间。在情形2,出气孔的直径会发生变化以研究模内冷却时间随其的变化规律。而在除此之外的其它情形,出气孔的直径都保持为14 mm。另外,在情形5、6、7,多个进气孔是平均分配40 L/min的进气流量。这是非稳态的不可压缩空气的三维流动与传热问题,本文将通过Fluent软件并采用湍流的k-ε两方程模型[6]对其进行数值仿真计算。
2 数值计算结果及分析
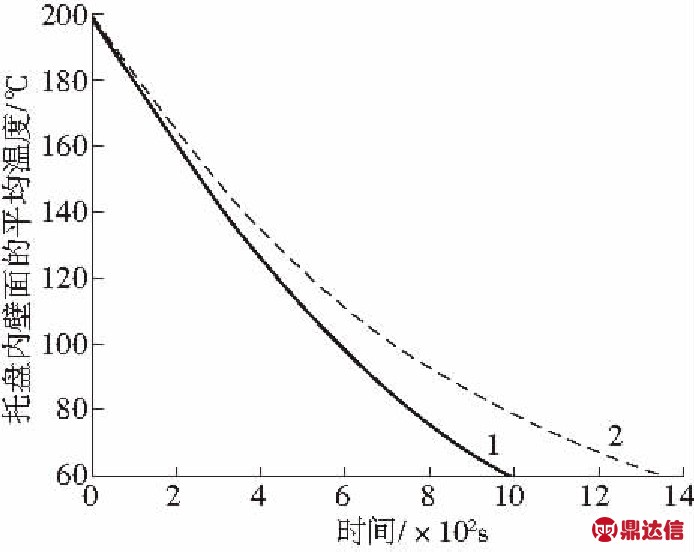
1—情形2 2—情形3
图3 在情形2和3托盘内壁面的平均温度随时间的变化
Fig.3 Variation of average temperature at inner wall of the pallet with time in case 2 and 3
如图3所示给出了在情形2、3托盘内壁面的平均温度随时间的变化规律。可以看出,刚开始的时候托盘内壁面的平均温度随时间下降的速率较大,但随着时间的延长,随时间下降的速率越来越缓。另外可以看出在模内冷却开始后比较短的时间内,这2种情形的托盘内壁面平均温度随时间的变化曲线相差不大,但随着模内冷却过程的进行,它们之间的差异越变越大。也就是说越到模内冷却过程的后期,进气孔和出气孔的结构设计对模内冷却效果的影响就越显著。
如表2所示给出了在表1中所示的7种情形的模内冷却时间,下面对其进行比较分析以说明前述诸因素是如何影响模内冷却时间的。
表2 在不同情形的模内冷却时间
Tab.2 Internal cooling time in different cases
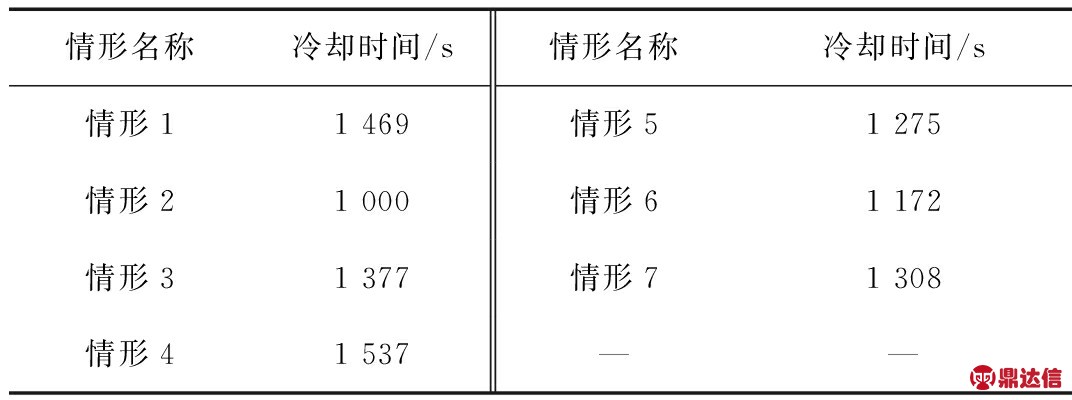
2.1 进、出气孔间距的影响
比较表2中的情形1和2可以看出,增大进气孔和出气孔的间距,可以有效地缩短模内冷却的时间。这是因为进气孔与出气孔离得较远,意味着冷空气可以在托盘的内部空腔里流动较长的距离,这样冷空气就能与托盘空腔内更多的热空气充分混合,从而在流出空腔时能带走更多的热量,相应提高了模内冷却的效率。这一点也可以由能量守恒原理来证明。根据能量守恒原理,每单位时间托盘空腔内空气热力学能的减少量等于每单位时间从出气孔流出的空气热量与从进气孔流入的空气热量之差,如式(1)所示:

(1)
式中 ρ——空气的密度,kg/m3
Va——托盘内部空腔的体积,由几何模型得知Va=0.584 m3
cp——空气的定压比热容,J/(kg·K)
Ta——托盘内部空腔里空气的平均温度,在初始时刻,Ta =27 ℃
t——时间,s
QV——进入托盘内部空腔的空气的体积流量,QV= 6.67×10-4 m3/s
Tin ——在进气孔处空气的平均温度,Tin = 27 ℃
Tout——在出气孔处空气的平均温度, ℃
因为托盘内壁面假设为绝热,同时托盘内部空腔的横截面比较狭窄,所以内部空腔里的空气平均温度Ta应该与托盘内壁面的平均温度Tw相差很小,可认为近似相等。再将式(1)两边从初始时刻积分到模内冷却过程结束,可得式(2):

(2)
式中 Tw(Δt)——在模内冷却结束时托盘内壁面的平均温度,Tw(Δt) = 60 ℃
Tw(0)——在初始时刻托盘内壁面的平均温度,Tw(0) = 200 ℃
进气孔处的空气在模内冷却过程的时间平均温度,
℃
出气孔处的空气在模内冷却过程的时间平均温度, ℃
Δt ——模内冷却时间,s
代入已知数据,由式(2)可得出模内冷却时间的表达式(3):
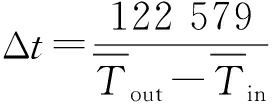
(3)
由式(3)可以看出,要想缩短模内冷却时间,就要使得出气和进气在模内冷却过程的时间平均温度相差越大越好。一般来讲,如果进气孔和出气孔离得比较远,就能使得表达式(3)的分母比较大,从而缩短模内冷却时间。如果由于结构或工艺的原因,进气孔和出气孔无法布置的相隔较远,可以在设计模具的时候有意在二者之间设置1个隔板,使得进入托盘内部的冷空气在与更多的热空气充分混合之前无法轻易流出托盘,这样就能增大出气在模内冷却过程的平均温度以减少模内冷却时间。在极限情形下,空气流经出气孔时可达到的最高平均温度为内部空腔里空气的初始温度200 ℃,代入方程式(3)可算出理论上最短的模内冷却时间为709 s。也就是说在其他条件不变的前提下,无论怎么优化进气孔和出气孔的位置、个数和大小,模内冷却时间都不可能少于709 s。
2.2 进、出气孔个数的影响
比较表2中情形2、3、4的计算结果可以看出,当进气孔的个数为1个,增加出气孔的个数会使得模内冷却时间变长,即模内冷却效果变差。这主要是由2个原因造成的。一是在情形3和4,进、出气孔的间距比情形2要小,进入托盘内部空腔的冷空气来不及与原来的热空气充分混合就从出气孔流出去了。第二个原因是在进气流量一定的前提下,出气孔的个数越多,从出气孔流出的热空气的平均速度就越低,因此在出气孔附近区域空气湍流的程度就会变弱,使得进入托盘内部空腔的冷空气与原来的热空气混合得不够充分,无法有效地将内部空腔里的热量带出,致使模内冷却效果变差。也就是说如果出气孔的总面积大于进气孔的总面积,那么托盘空腔里的气流扰动就会变弱,模内冷却时间就会变长。
情形5和6的模内冷却时间都比情形3的要短。在情形5和6中,进气孔和出气孔是分散开来布置的,即二者的间距比情形3要大,另外情形5和6比情形3多1个进气孔。这2个原因使得进入托盘内部的冷空气与原来的热空气有更多的机会充分混合,提高了冷却效果。由此可见如果可以将进、出气孔分散布置,增加进气孔的个数能减少模内冷却时间。
2.3 进、出气孔布置方式的影响
在情形5和6,所开的4个孔的位置和大小都一样。区别是在情形5,两列进、出气孔是平行布置;而在情形6,进、出气孔是交叉布置。表2的仿真结果表明情形6 的模内冷却时间比情形5要短。这是因为在情形6,交叉的气流运动方向增强了托盘空腔内气流扰动的程度,更有利于冷、热空气的充分混合以带出更多的热量。在情形4和7中,所开的5个孔的位置和大小也都是一样的,区别只是将进气孔和出气孔的位置对调,因此这两种情形的气流方向是相反的。在情形7出气孔处的流速比情形4的大很多,从而在托盘空腔内造成了较强的气流扰动,提高了冷却效果,缩短了模内冷却的时间。
由此看出改变进、出气孔布置的方式本质上是改变了托盘内部空气流动的方向和状态,从而最终影响了模内冷却时间的长短。另外以上的分析比较也说明了为保证较好的模内冷却效果,进气孔的总面积一般应大于或等于出气孔的总面积。
2.4 出气孔直径的影响
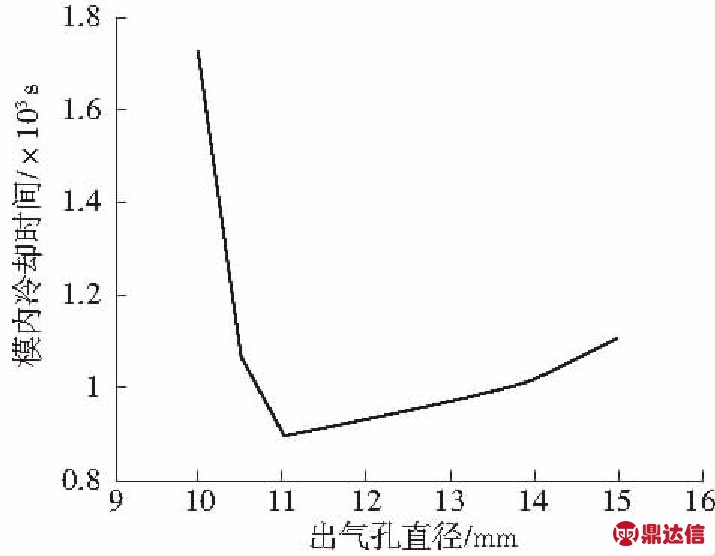
图4 情形2的模内冷却时间随出气孔直径的变化
Fig.4 Variation of internal cooling time with outlet diameter in case 2
图4表示了在情形2,当进气孔直径保持为14 mm,托盘的模内冷却时间随出气孔直径的变化规律。可以看出在刚开始的时候,模内冷却时间随着出气孔直径的减小而缩短。当出气孔直径减小到11 mm,即进气孔直径的79 %时,模内冷却时间达到最小值。此后如果继续减小出气孔直径,模内冷却时间反而急剧增加。在进气量一定的前提下,出气孔处的空气流速随着出气孔直径的减小而增大,因此在出气孔附近区域的空气湍流的脉动程度增强,托盘空腔内冷、热空气可以混合得更充分,从而提高了冷却效果。计算结果表明与进、出气孔直径都为14 mm的情形2相比,通过减小出气孔直径最多能缩短12 %的模内冷却时间。
图5比较了在出气孔直径分别为14 mm和10 mm的情形2,当模内冷却结束时出气孔上的气流速度分布。可以看出随着出气孔直径的减小,更高速的气流越来越集中在出气孔的中心区,也就是说高速流动的冷空气与其周围靠近壁面的热空气越来越难于充分混合,致使模内冷却效果变差。虽然前面说过减小出气孔直径有助于增强气流的扰动和冷、热空气的充分混合,但当出气孔直径过小时,继续增强气流扰动对冷、热空气充分混合的促进作用已不再显著,而由此产生的高速气流向出气孔中心靠拢对冷、热空气充分混合的不利影响开始占主导地位,故此时模内冷却时间随出气孔直径的减小反而增加。所以当采用减小出气孔直径的方法来提高模内冷却效果时,要特别谨慎。
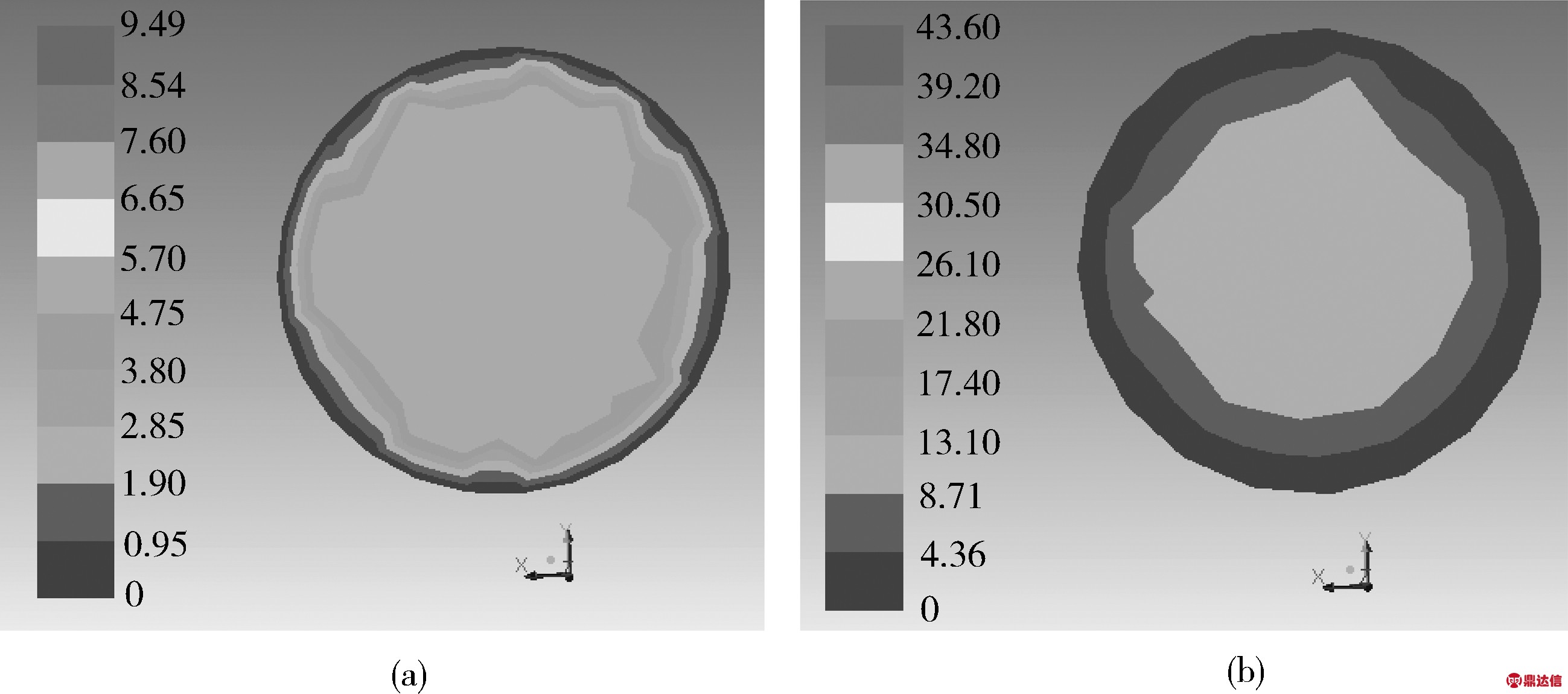
出气孔直径/mm:(a)14 (b)10
图5 当模内冷却结束时在情形2出气孔上的气流速度分布(m/s)
Fig.5 Air velocity distribution at outlet in case 2 when internal cooling ends
如图6所示,随着出气孔直径的减小,在情形2模内冷却结束时进、出气孔间的压差会快速增大,即在托盘内部空腔里空气的流动阻力急剧增大。因此为保持一定的进气量,随着出气孔直径的减小,需要消耗越来越多的机械能,这也可以看作是为提高托盘空腔里气流扰动程度所必须付出的代价。
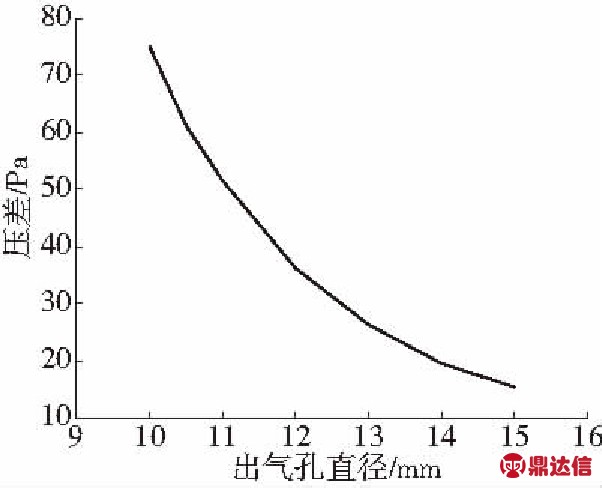
图6 在情形2当模内冷却结束时进、出气孔间
压差随出气孔直径的变化
Fig.6 Variation of pressure difference between inlet and outlet in case 2 when internal cooling ends with outlet diameter
3 结论
(1)随模内冷却过程的进行,托盘内壁面的平均温度减小的速率变得越来越慢;
(2)为减少模内冷却的时间,应使得进入托盘内部的冷空气与原来的热空气有更多的机会充分混合,同时应增大托盘内部气流的扰动强度;因此进、出气孔的间距应尽可能的大,进、出气孔应尽可能交叉布置,另外进气孔的总面积不能小于出气孔的总面积;
(3)在只有1个进气孔和1个出气孔的情形,模内冷却时间随出气孔直径的减小而减少;当出气孔直径减小到进气孔直径的79 %时,模内冷却时间最短;如果继续减小出气孔的直径,模内冷却时间反而急剧增大。