【摘要】探讨提高托盘式自动络筒机插管效率的技术与方案,找出了影响插管速度的基本因素,如管纱的质量、大小头检测传感器的检测准确性、振动盆剪刀的使用寿命、空托盘的供应速度以及各个工位传感器检测的稳定性等。
【关键词】托盘式自动络筒机;插管;管纱
随着劳动力成本的不断提高,愈来愈多的纺织企业采用了托盘式自动络筒机。该自动络筒机是将原来由挡车工完成的管纱生头插管交由机器自动完成,可以降低75%以上的用工。
托盘式自动络筒机一般由插管装置、生头装置、输送装置、单锭卷绕装置和落筒小车装置等组成。一般情况下,一台自动络筒机具有60~72个单锭,单锭的卷绕速度在1200~1600m/min,所纺的纱线支数通常在9.7~58tex,一个管纱的重量在 50~80g,折合纱线长度一般在 1300~5000m,这样一个管纱单锭卷绕的时间在1.2~4.0min,加上换管时间、切疵重新捻接等,平均一个管纱占用单锭的时间最少在1.4min,如果是72锭的自动络筒机,每分钟需要供应的管纱数就是72÷1.4=51.4个。再加上生头不成功、卷绕不完全等因素,这样CBF的管纱供应能力必须大于51.4×(1+15%)=59。如果管纱供应不上就会造成部分单锭停止工作,直接影响络筒机的生产效率。所以插管速度和生头速度以及生头成功率是影响络筒机产量的主要因素。以往的单插管速度只有35~40个/min,所以许多国外设备都采用了双插管,一套插管35个,两套预计就能达到70个,但实际上没有达到,插管问题解决了,新的瓶颈就变成了振动盆对管纱的输送速度。目前稳定的管纱输送速度在50~55个/min,两套插管并不能得到充分发挥,结构也复杂成本也高,并都申请了专利保护。
我公司优化改进了供管系统并研制了一套高速单插管装置,插管速度可以达到55个/min以上,属于单插管国际领先水平。下面就如何提高插管速度的一些措施做一些探讨。
1 插管的工艺流程
细纱机落纱到管纱小车内→管纱小车推到大纱库铲车上→管纱小车在液压缸的作用下将管纱翻倒在振动平板上→振动平板通过振动(振动电机)将管纱输送到振动盆内→振动盆将管纱振动(振动电磁铁)成单列排列方式→通过大小头检测传感器检测出管纱的大小头→通过插管装置插到下方的CBF托盘上。大纱库组件示意图见图1。
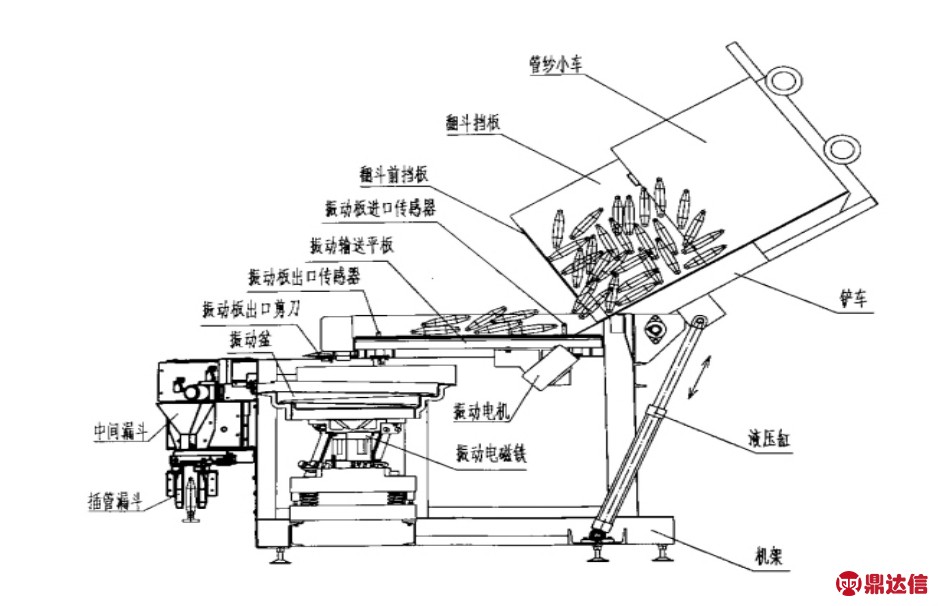
图1 大纱库组件示意图
2 插管速度的影响因素
影响插管效率的因素一般是插管的各个流程中的最高速度和故障率,这2个因素影响了插管的平均速度,两者缺一不可。要提高插管速度就要提高各个流程的最高速度,在整个插管流程中只有振动盆输送和插管是一个一个管纱进行的,是影响效率的关键流程。而影响振动盆输送管纱的因素则是振动盆的振动频率、振动盆内管纱的数量和管纱回丝缠绕的状态。
振动盆的振动频率可以调节,比较容易控制。振动盆内管纱太多,回丝缠绕就会很严重,沿振动盆螺旋上升的管纱经常会被下面的管纱给拖下来重新排队,原来的管纱队伍中就会出现空位,影响管纱输送效率。
管纱的相互缠绕还会造成振动盆出口堵塞,引发插管故障。如果振动盆内管纱太少,管纱就不容易迅速进入螺旋上升通道,在振动盆中间游荡,也会造成输送效率降低。要平衡两者之间的矛盾,就是找到一个合适的管纱数量,并让这个数量一直稳定下来,不应该一会多一会少。
分析认为,振动盆内的管纱从振动平板上过来,振动平板是根据振动盆内管纱数量检测传感器的信号控制平板的振动,振动输送管纱的数量取决于振动平板上管纱层的厚度和振动时间。在时间设定不变的情况下(可以设定但不能自动改变),管纱层的厚度就是唯一的因素了。再往前推,振动平板上的管纱是从液压翻斗来的,大纱库的液压翻斗和汽车的自卸车厢原理相似,刚开始向上翻时,只是翻斗表面的管纱向下滚落,等翻斗翻倒到一定角度时,管纱就会瞬间倾泻而下,造成振动平板上管纱厚度前面薄后面很厚,所以首先要从解决翻斗供纱的问题开始入手。翻斗加挡板示意图见图2。
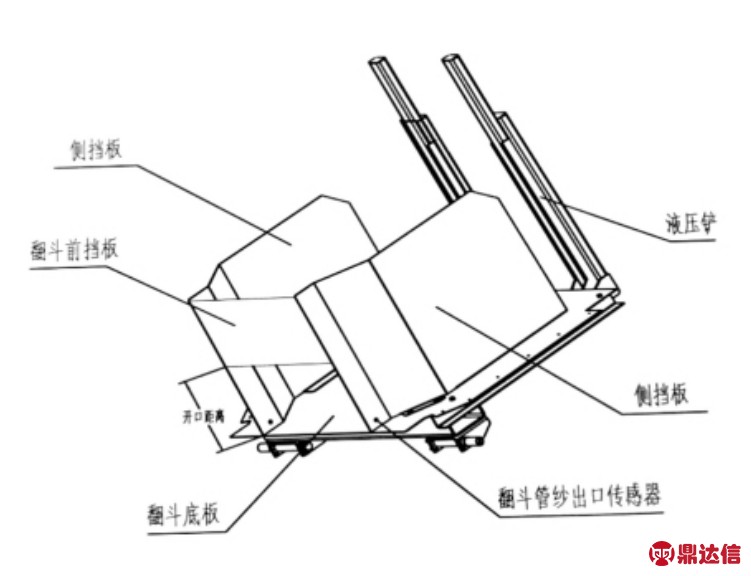
图2 翻斗加挡板示意图
3 翻斗供纱装置
3.1 翻斗改进前
采取液压缸间断举升的方式,当管纱小车在液压缸的举升作用下,管纱小车的倾斜度越来越大,管纱在重力的作用下就会沿液压翻斗的斜面滑落,在振动平板的进口处设有传感器。当此处的传感器检测到管纱时,液压缸就会自动停止。但由于液压缸及翻斗的惯性以及时间的延迟作用,仍会有大量的管纱倾倒在振动平板上。当采用间断举升的方法时,举升一定角度即使振动板进口传感器没有检测到管纱,也要停下一定时间等待管纱下落。如果这个时候管纱下落也不会下落太多,因为液压缸这时是停止的,如果停止一定时间后管纱还没有下落则液压缸继续举升一定角度再停下来,直至管纱下落传感器检测到管纱。这种方式虽然好,但并不能彻底解决问题。
3.2 翻斗改进后
在管纱小车出口下方增加翻斗前挡板,减少管纱的下泄数量,如图2所示。加上翻斗前挡板后,管纱只能从侧板、前挡板及底板围成的口子倒出,多余的管纱就会被前挡板挡住,这样就不会有大量的管纱落在振动平板上,但也可能出现管纱堵在出口处无法下落,即翻斗管纱出口传感器检测有管纱但振动平板进口传感器无信号。可以采取液压缸下降一段距离,堵在出口处的管纱就会自动解开,然后液压缸再自动向上举升,通过实践证明这个方法是稳定可靠的。翻斗改进后供纱示意图见图3。
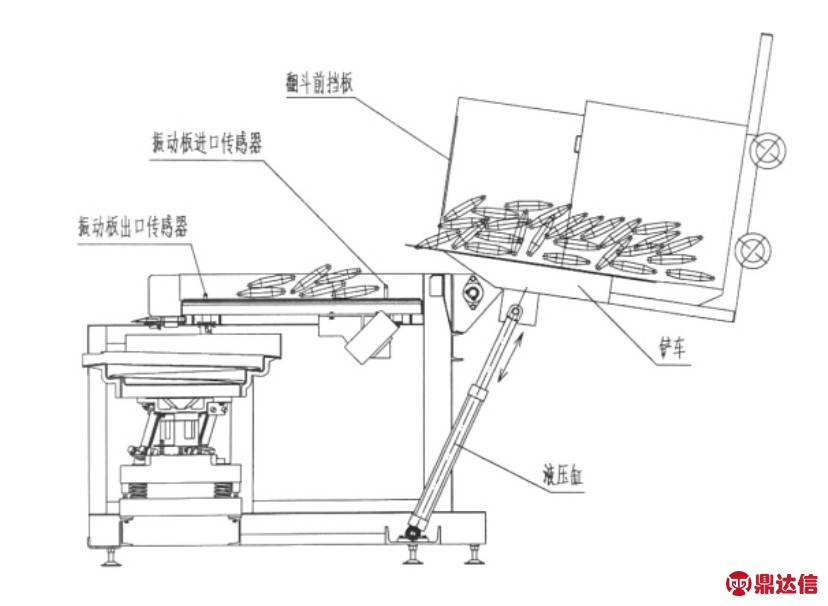
图3 翻斗改进后供纱示意图
3.3 振动平板的调节要求
振动平板的时间调节判断原则:每一次振动下落到振动盆内的管纱数量控制在15~20个,振动平板振动的起始条件是振动盆内底面漏出一半以上的面积,振动设定的时间后停止。如果振动盆内管纱太多就会造成振动盆振幅太小影响管纱输送速度,同时管纱之间也会相互缠绕,管纱太少就会造成管纱断断续续,浪费时间,降低振动盆的输送效率。也可以在振动平板出口处设置三个管纱厚度检测传感器,根据此处管纱厚度的不同而自动采用不同的振动时间。振动盆内管纱数量示意图见图4。
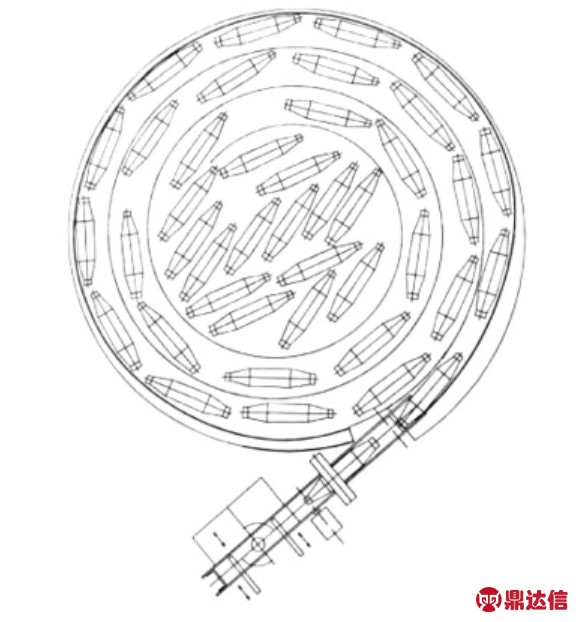
图4 振动盆内管纱数量示意图
3.4 振动盆的调节要求
振动盆振动频率的调节,一般在45~55Hz左右,管纱在振动盆内要匀速前进,不能出现管纱原地不动甚至倒退的现象。管纱之间最好要留有间隙,每个管纱都能够自己独立向前爬行。振动时管纱输出速度要达到55~60个/min,振动电磁铁上下部分之间的间隙为0.8mm。距离太大振动幅度会减小,管纱速度会慢;距离太小,振动噪音会比较大(可以用一张纸塞进振动电磁铁上下部分之间,当电磁铁振动片刻后,拿出纸后看看这张纸是否有打击的痕迹,如果有痕迹就说明振动电磁铁上下部分之间的间隙太小)。
振动盆输出导板的调节,管纱在进入振动盆剪刀之前,即在弧长A的位置(见图5),轨道上只能存放一个管纱,此处导轨的水平宽度必须小于管纱的直径,多余的管纱必须被挤入振动盆内重新排队,否则管纱会在振动盆出口处卡死。振动盆出口图见图5。
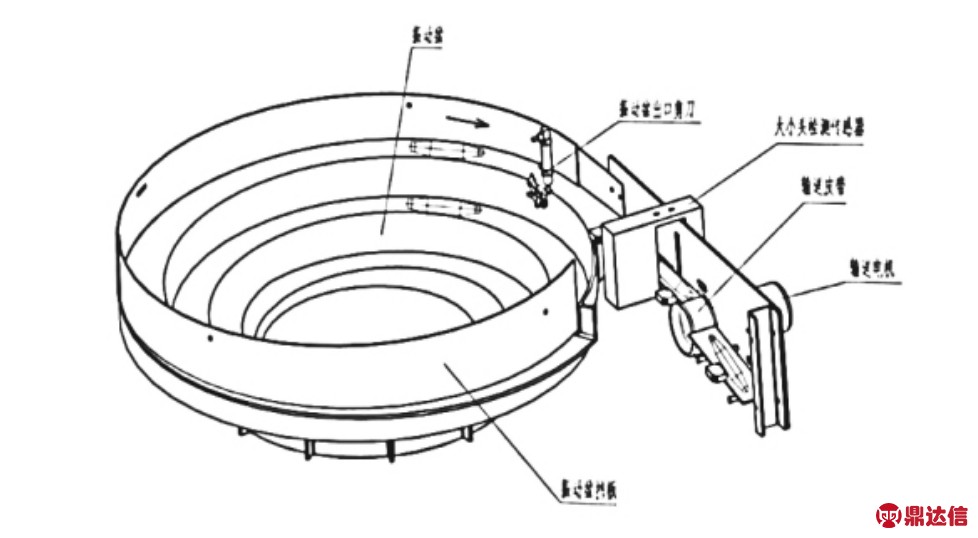
图5 振动盆出口图
当管纱拖着纱头经过出口处时,纱尾必须被剪断,否则容易造成管纱阻塞。原设备为了保证每个纱尾都被剪断,当振动盆振动时,管纱随时有可能通过剪刀处,剪刀必须快速反复动作几次,这样剪刀动作的次数可达到每分钟五十多次,每天达七万多次,严重影响剪刀的使用寿命。为此在剪刀处增加了纱线检测传感器,只有当管纱拖着纱尾经过出口处时,纱尾才会被传感器检测到,剪刀只要动作一次就会将纱线减断(大约只有百分之二十的管纱拖着纱尾),大大降低了剪刀动作的次数,有效延长了剪刀的使用寿命。
振动平板的管纱向振动盆输送时,在振动平板出口处增加剪刀,当管纱到达振动盆内纱尾仍在振动平板上时,剪刀必须将该纱尾剪断,否则管纱的纱尾会越来越长,造成管纱的相互缠绕。
4 插管装置
为了提高插管的速度,首先分析一下影响插管速度的因素:一是管纱的大小头检测;二是管纱根据大小头检测的结果由横向转变为大头朝下的纵向;三是管纱下落插到托盘上的时间;四是各工位之间的协调。
如图6所示,管纱通过振动盆螺旋输送到图中的第一工位,由传感器11检测到,振动盆停止,再由输送皮带1将管纱2通过门式传感器3输送到第三工位的插板6上,如果插板6上有管纱存在,则管纱停在第二工位,由传感器4检测,通过门式传感器的检测就已经知道了管纱的大小端方向,如果第三工位有管纱就在第二工位等待,此时传感器 4检测到管纱的到达,皮带1停止运转,当中间漏斗9内没有管纱时(由传感器14检测),插板6和销轴7或者销轴8迅速回撤(如果管纱大端在后则销轴7后撤,如果是管纱大端在前则销轴8后撤),管纱在自身重力和销轴7或8的共同作用下,大端向下落入中间漏斗9,如果漏斗10下方有空托盘12等待时,中间漏斗下方的插板13抽开,管纱落到漏斗10,最后插在托盘12上完成插管整个动作。高速插管装置见图6。
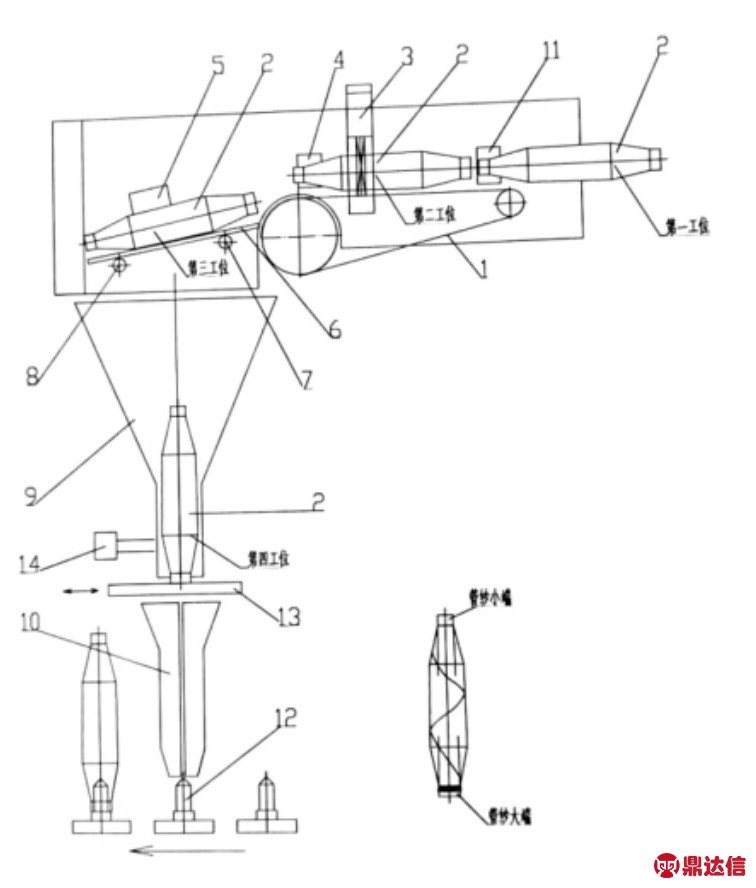
图6 高速插管装置
1-平皮带、2-管纱、3-大小头检测传感器、4-平皮带出口传感器、5-传感器、6-管纱支撑平板、7-管纱挡杆一、8、管纱挡杆二、9-中间漏斗、10-插管漏斗、11-平皮带进口传感器、12-托盘、13-插板、14-中间漏斗传感器
在整个插管过程中将整个插管动作分成了4个工位,每个工位都是独立的并都传感器检测状态,以保障每个工位随时都有管纱,减少了时间的浪费。甚至把管纱的下落过程分成两段,如果管纱直接由第三工位下落插到托盘上,管纱由水平状态变为垂直状态要与漏斗壁发生多次碰撞,下落时间很长,通常需要0.6~0.7s的时间,这个时间对于完成一个插管循环的时间来讲是太长了。如果采取管纱分步下落,将减少整个插管循环时间 0.3~0.4s。
具体实施方式:在漏斗9和漏斗10之间增加插板13,当漏斗9内没有管纱时(由传感器14判断),由第三工位释放一个管纱,管纱由水平状态变为垂直状态与漏斗壁发生多次碰撞稳定后垂直的立在伸缩挡板13上,被传感器14检测到,处于等待状态,当漏斗10下有托盘12等待插管时,伸缩挡板13迅速回撤,管纱通过活动漏斗插到托盘上。由于管纱在下落过程中始终处于直立状态,所以下落速度较快,同时下降距离缩短,节约了时间,提高了插管效率。
5 结语
通过以上分析找出了一些影响插管速度基本因素,如管纱的质量,大小头检测传感器的检测准确性,振动盆剪刀的使用寿命,漏斗下面空托盘的供应速度,各个工位传感器检测的稳定性等等。经过近几年的生产试验,插管效率、稳定性和可靠性都有了较大的提高,插管失误率在万分之一以下,单插管速度可以达到55个/min,属于国际领先水平,已经获得多项国家发明专利,同时也申请了日本、德国和意大利的国际发明专利。