摘 要:汽车轻量化和绿色制造催生了对高稳定、高强度的铝合金用材需求。针对现有的铝合金车身构件存在着强度不足、稳定性不够等问题,以汽车下托盘铝合金铸件为例,对热处理工艺进行了优化,得到了较佳的热处理工艺路线。结果显示:经该热处理方法强化后,下托盘铸件的力学性能较热处理前有着较为明显的提高,铸件的强度进一步强化,热处理后的铸件组织稳定,内应力较小,结构尺寸稳定,由此得到下托盘铝合金铸件较佳的热处理工艺为520℃固溶并保温2 h,风冷急速降温2 h冷却到室温,人工过时效230℃,保温2 h~5 h。
关键词:铝合金;热处理工艺;人工时效
0 引言
当代新能源汽车正朝着轻量化、高速、安全舒适与节能的方向发展。为实现这一目标,新能源汽车材料及技术的进步与发展起着举足轻重的作用,而使用轻质材料则是减轻车重的一个重要措施[1-2]。
由于铝合金密度低,能够很好地满足车身材料轻量化的用材需求,其强度高,接近或超过优质钢,加上塑性好,容易加工成型,且具有优良的导电性、导热性和抗蚀性,目前已被广泛应用到汽车生产制造领域,是目前汽车领域使用量仅次于钢的合金。但由于现有的铝合金车身构件存在着强度不足、稳定性不够等问题,易导致汽车局部变形从而影响汽车性能及寿命。目前铝合金构件的制造方法主要有锻造和铸造,铸造铝合金因其原材料及加工成本比锻造铝合金具有优势,且铸造铝合金经热处理工艺后可以得到强化,能够满足汽车铝合金构件的使用性能要求,因而在汽车领域铸造铝合金得到较为普遍的应用。对于铸造铝合金的热处理强化,饶晓晓[3]以A356铸造铝合金轮毂为研究对象来研究固溶工艺参数对力学性能的影响规律;沈健等人[4]对6005A铸造铝合金的淬火方式研究发现A6005A铝合金要满足性能要求必须要有较高的淬火条件和较短的停放时间;张德恩等人[5]采用正交实验法对铸造铝合金的力学性能影响因子进行分析并得到最佳的热处理工艺路线。为了进一步强化铝合金铸件,因此,寻找有效的铝合金热处理工艺显得十分重要,对于提高汽车整体性能也有着非凡的意义。
本文以汽车下托盘铝合金铸件热处理工艺为例,通过合理的热处理工艺设计来提高铝合金的力学性能,为生产制造企业及相应的人员提供一定的参考。
1 铝合金热处理的特性
1.1 热处理目的
经压铸成型后的铝合金铸件通常情况下还不能够直接使用,主要原因在于压铸后的铝合金车身构件的机械性能还满足不了实际的使用要求,铸件内部还存在着内应力,使得铸件组织结构不稳定,从而会导致铝合金车身铸件尺寸不稳定。为了进一步提高铝合金铸件的强度及尺寸稳定性,有必要对形成后的铸件进行热处理。
根据文献[6],铝合金车身构件热处理的目的具体有以下三个方面:
(1)可以强化合金,改善铝合金金相组织,提高铝合金铸件的机械性能,改善铝合金的切削性能及焊接性能;
(2)可以消除因铸件壁厚不均、转接处壁厚过大等原因造成铸件结晶凝固时因冷却速度不均匀所造成的内应力,稳定铝合金铸件的组织及零件轮廓尺寸;
(3)防止和消除高温相变而使体积发生变化,消除晶间和成分偏析,使组织均匀化。
1.2 热处理特点
铝合金材料的成分对铝合金构件的力学性能有着直接的影响,同时也对铝合金铸件的热处理工艺产生十分重要的影响。
由于铝没有同素异构转变,所以铝合金的热处理强化方法与钢不同,其利用溶体化处理和时效硬化处理来强化铝合金,通过固溶处理,使合金元素和第二相固溶于基体,并通过时效处理均匀析出细小的强化相,以此达到强化目的[7]。
正是由于铝合金的这种热处理强化机理,并非所有的铝合金都可以进行热处理强化,故在实际生产应用中,除了ZL102(Al-Si系)、ZL302(Al-Mg系)及ZL401(Al-Zn系)等铝合金因铸造性能优良、铸造过程无热裂及疏松倾向、气密性较好等特点而不可热处理强化之外,其余的铝合金铸件必须要经过热处理来达到强化合金,提高铸件的机械性能及其他的使用性能,进一步改善切削加工和焊接等加工性能。
2 试验材料与热处理工艺
2.1 铝合金锭材料成分
本文试验采用Al-Si系合金铝锭AlSi10MnMg,参考标准GB/T 20975.25-2008,用电感耦合等离子体原子发射光谱仪对三个试样进行检测,材料成分如表1所示。
表1 铝锭材料成分(%)
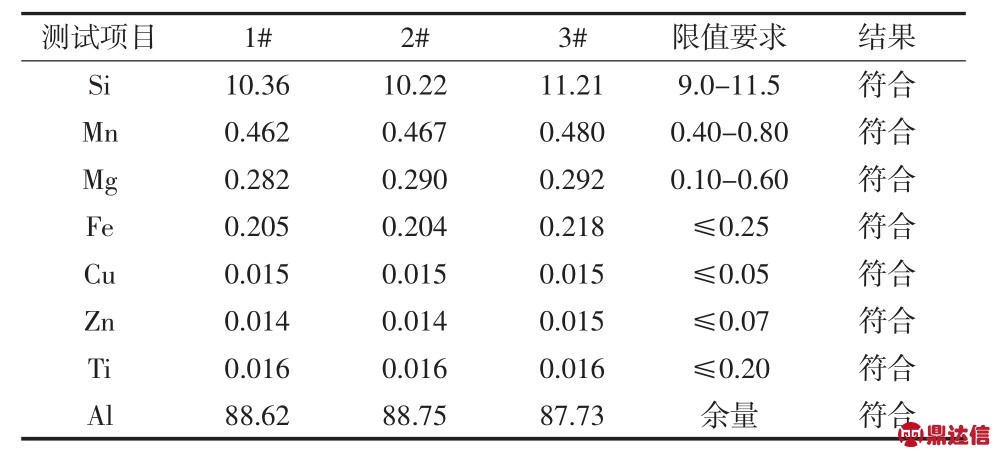
2.2 铸件存在的问题
图1所示的为高真空压铸铝合金下托盘构件试样,未经热处理前,铸件力学性能为抗拉强度小于230 MPa,屈服强度小于180 MPa,延伸率不足5%;在负载气密测试中,气体泄漏速率达到0.35 kPa/min,与使用要求严重不符,表明铸件因强度不足出现较大的变形;铸件螺纹孔螺纹强度不足,提供不了产品所需要的锁紧力,在装配过程中,容易出现螺纹牙破烂,且容易松动。
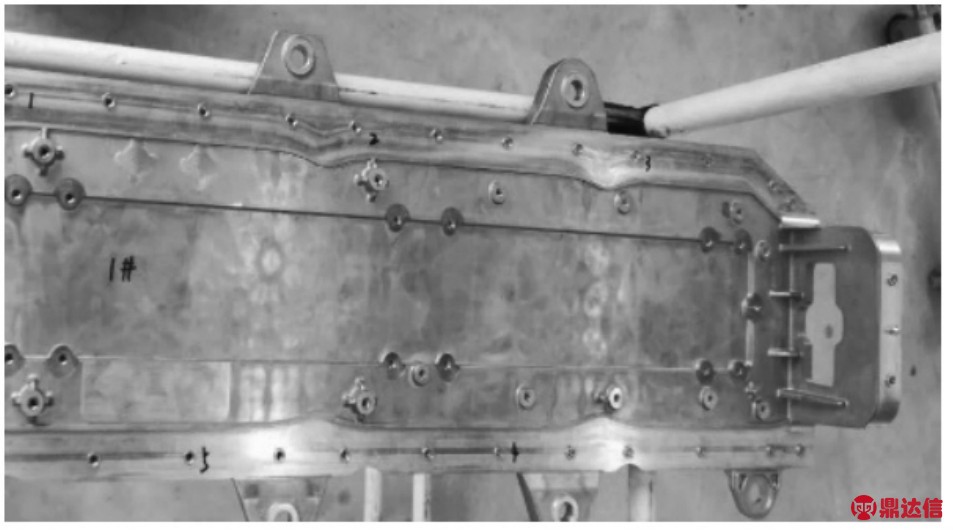
图1 下托盘铝合金铸件试样(局部)
为了提高上述铝合金铸件的使用强度及尺寸稳定性,有必要通过热处理工艺的优化来达到强化铸件目的。
2.3 热处理工艺
经多次反复试验验证,确定下托盘铝合金热处理工艺为:将下托盘铝合金铸件放入固溶电阻炉中固溶,固溶温度为520℃,固溶时间为2 h,使合金内的可溶相充分溶解。然后采用风冷方式对铸件进行2 h冷却到室温,使铸件急冷,目的在于使得强化后的组元在合金中得到最大限度的溶解,强化铝合金铸件。最后进行人工过时效,将铸件重新加热到230℃,保温2~5 h,使强度略有下降,提高塑性,以此使得铝合金铸件获得较好的力学性能。下托盘铝合金铸件热处理工艺温度变化曲线如图2所示。
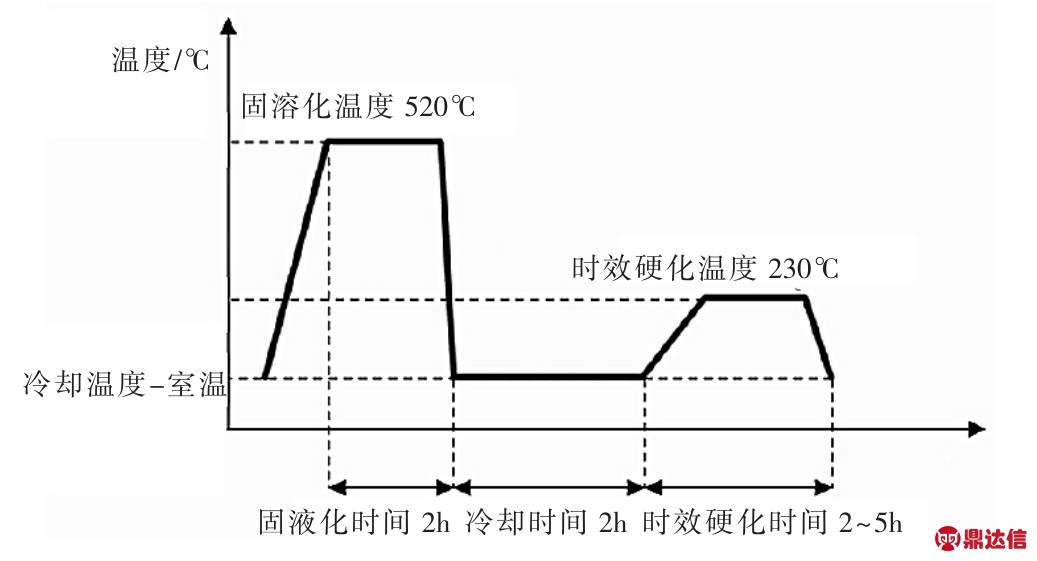
图2 下托盘铸件热处理工艺温度变化曲线图
3 性能检测与结果分析
3.1 力学性能检测
在经热处理后的下托盘铝合金铸件上截取三个试片(见图3(a)),利用300 kN电子万能试验机对试片进行力学性能检测,采用ASTM B557-15检测标准,得到试片检测结果如表2所示。
表2 下托盘铝合金铸件主要力学性能
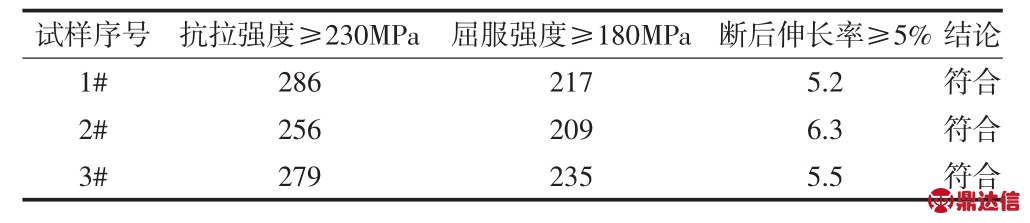
由表2可知,通过热处理工艺操作后,铸件抗拉强度远大于230 MPa,屈服强度超过180 MPa,延伸率大于5%,较之前有着较为明显的提高。在材料的承受极限内,多次的载荷测试,试片没有明显的变形(见图3(b)),铸件力学性能得到使用要求。
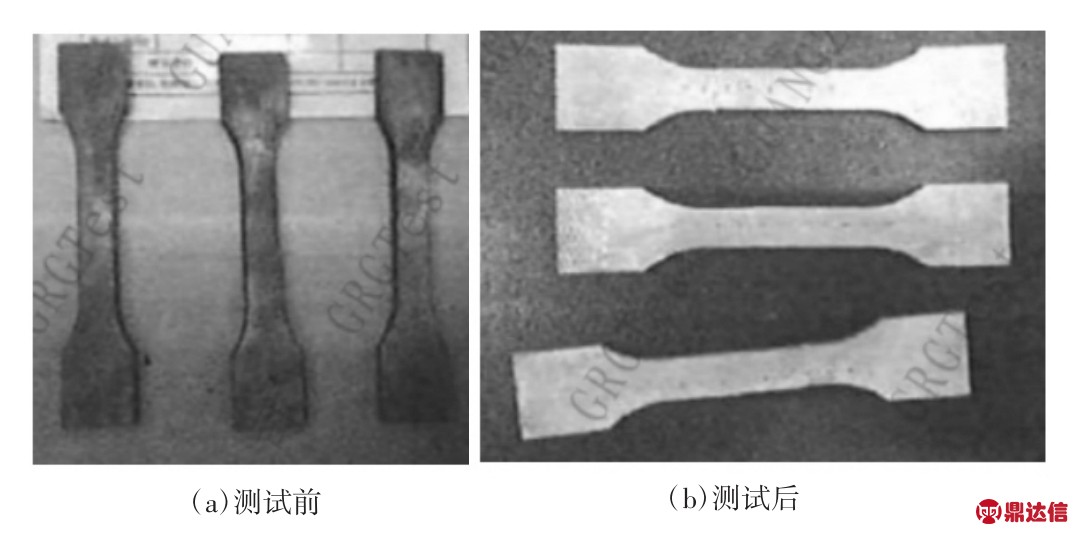
图3 下托盘铝合金铸件试片
3.2 扭力测试
随机选取3个试样,在每件铸件上随机选取其中的6处螺纹孔做钢套/牙套的紧固力矩测试,要求安装孔螺纹的机械性能满足安装力矩≥15 N·m,并且要满足10次以上拆装而不得出现功能失效,同时要求打紧螺栓至15 N·m后,反向打力矩至8 N·m时,钢套不得与本体发生旋转或脱离。扭力测试结果如表3所示。
表3 下托盘铝合金铸件扭力测试结果
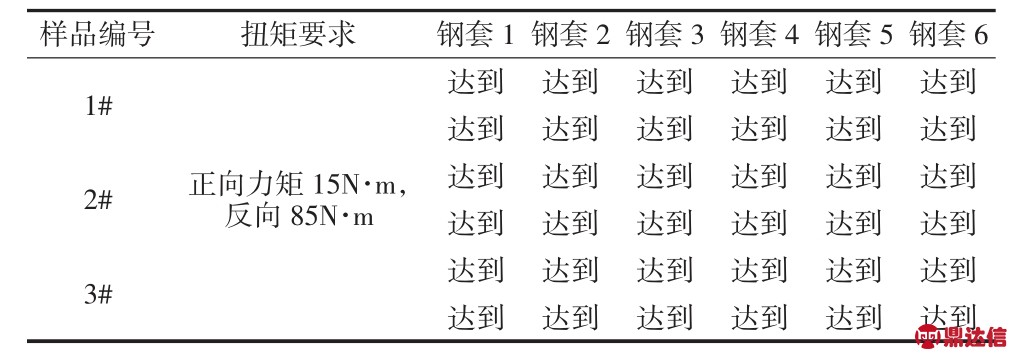
从表3可以看出,随机选取的3个试样,任意6处螺纹孔的钢套/牙套的紧固力矩测试达到检测要求,表明下托盘铝合金铸件强度达到使用要求。
3.3 气密测试
铝合金铸件的气密测试是衡量铸件变形程度最为直观的检测方法,也可以用来评估铸件热处理后尺寸的稳定性,检测是否存在较大的内应力。下托盘铝合金铸件气密测试,要求保持通入气压≥20 kPa,保压1 min,观察泄露速率,泄露速率≤0.1 kPa/min的情况下为达标。在同一批次产品中随机选取10个试样,其气密测试结果如表4所示。
表4 下托盘铝合金铸件气密测试结果
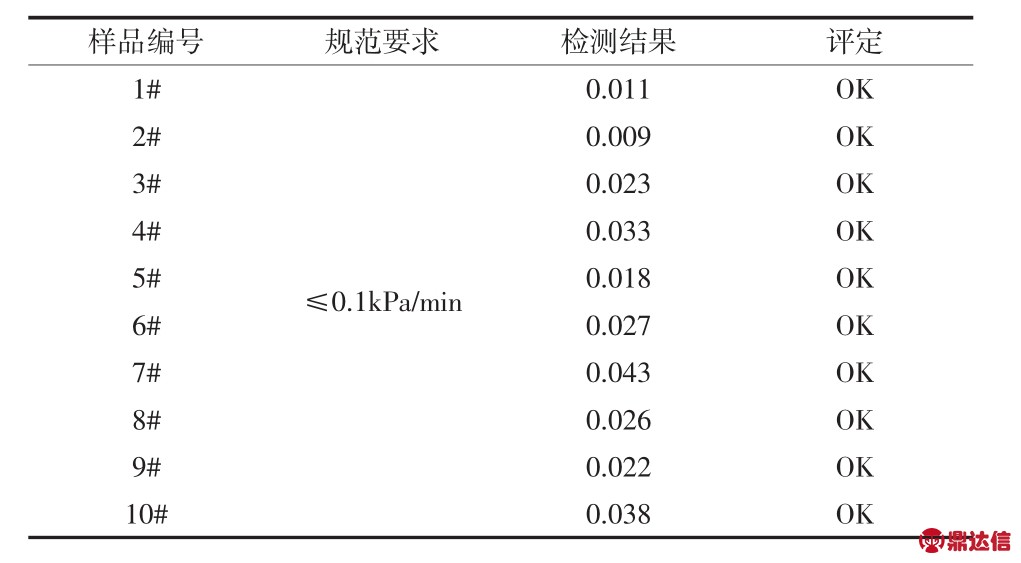
由表4可知,该批次下托盘铝合金铸件气密测试达标,表明了铸件热处理后稳定性较好,铸件变形量在要求范围内。
4 结束语
本文针对汽车用压铸铝合金构件存在强度不足、残余内应力以及组织尺寸不稳定等问题,以汽车下托盘铝合金铸件为例,对其进行了热处理优化,并对铸件进行了力学性能检测、扭力测试及气密测试分析,以此评估热处理后的铸件的使用性能,结果显示:经过该热处理工艺处理后,铸件较热处理前力学性能有着较为明显的提高,大大提高了铸件的强度,热处理后的铸件组织稳定,内应力较小,结构尺寸稳定,表明了下托盘铝合金铸件较佳的热处理工艺为520℃固溶并保温2 h,风冷急速降温2 h冷却到室温,人工过时效230℃,保温2~5 h。