摘要:某些特殊电子设备的短时高功耗运行往往会引起急剧温升,进而导致设备失效。文章采用膨胀石墨/高碳醇复合相变材料(PCM)作为热沉,针对某高功耗模块进行了散热仿真,并与传统铝热沉进行了对比,结果表明无主动散热平台下PCM热沉显著优于铝热沉。同工况温箱实验进一步验证相变热沉散热特性,并与仿真结果进行对比,结果表明实验结果与仿真结果具有一致的温度变化趋势,但由于相变温度范围的差异导致不同时间段温升速率不同。分析了二者的差异及原因,为严酷条件下应用相变材料进行热设计和热管理提供参考。
关键词:复合相变材料;热管理;电子设备;热沉;仿真分析;实验研究
0 引言
随着电子及通信技术的飞速发展,电子设备及元器件微小型化和高度集成化逐步成为主流发展趋势,而微系统形态下实现相同甚至更强功能必然导致电子设备和元器件功率密度急剧增加。如果各种发热功能元器件的发热量不能及时有效地释放,热量的积聚会造成元器件的温度超过其承受极限,从而降低其可靠性,甚至失效[1]。文献[2]表明,电子设备的失效有55%是由温度超过限定值引起的。在某些严酷环境下,虽然电子设备只需要在几十秒到几分钟内短时工作,但往往其芯片热流密度极高,同时平台无法提供主动冷却散热条件,这对设备的温控提出了更高要求[3]。相变材料(phase change material, PCM)在特定相变点发生相变过程中具有吸收/释放大量潜热同时保持等温或近似等温等优点,已逐步在航天器热控领域得到广泛应用[4-6],因而也是无主动散热条件下实现高热流密度电子设备热控的一种可行方案。
PCM按相变方式可分为固-固型、固-液型、固-气型和液-气型4类。固-气型和液-气型相变潜热很高,但相应会发生较大的体积和压力变化,对电子设备要求很高;固-固型相变体积变化最小,但其相变潜热小,且可选材料品种少,较大程度上限制了其应用[7];对于无主动散热环境平台而言,固-液型相变材料体积变化较小,相变潜热较大,属于比较合理的选择,但相变产生流态液体对封装可靠性要求较高。
本文针对高度集成的某电子设备模块,安装固-液型膨胀石墨/高碳醇复合PCM热沉,比较了其与铝热沉的瞬态散热性能差异,并通过实验对该复合PCM热沉的散热效果进行了验证和比较,为无主动散热环境平台应用PCM进行瞬时温控设计提供参考。
1 结构布局
1.1 模型结构布局
图1为本文所采用模型结构组成示意图,分为模块本体和相变热沉2部分,其中模块本体包含盒体、印制电路板(PCB)、功率器件及相应连接器;相变热沉为封装结构,即在热沉盒体中填充复合PCM。同时,本文目的是验证复合PCM的散热效果,因此对模块本体中无关器件和结构进行简化处理:模块本体仅保留主要功率器件,并将功率器件紧贴复合PCM热沉对应凸台。
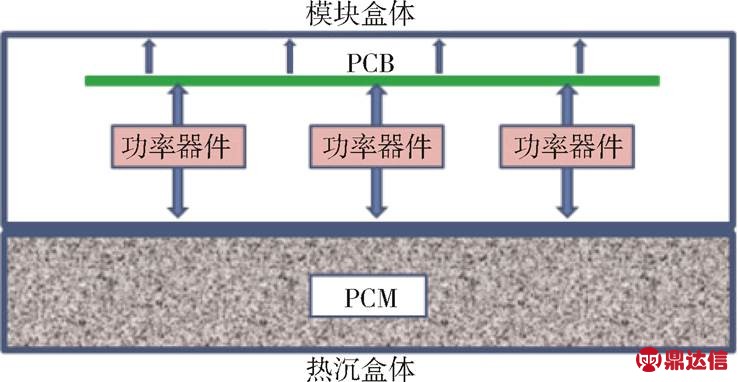
图1 模型结构示意图
Fig. 1 Schematic diagram of the module structure
1.2 模块热耗分布
模块热耗来自PCB上的各功率器件,计算模型中设置总热耗约为57W,功率器件热耗分布及对应热沉位置如图2所示,表1为各功率器件参数。
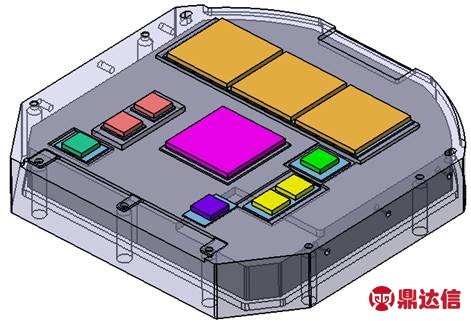
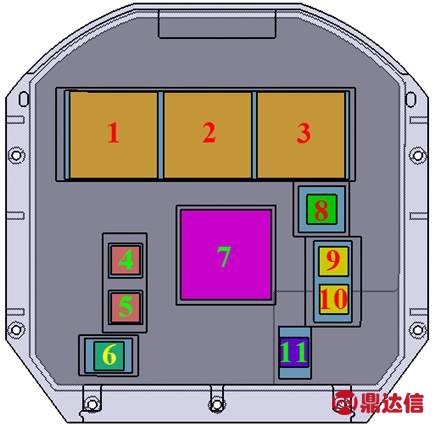
图2 芯片热源分布
Fig. 2 Chip heat source distribution
表1 芯片参数
Table 1 Chip parameters
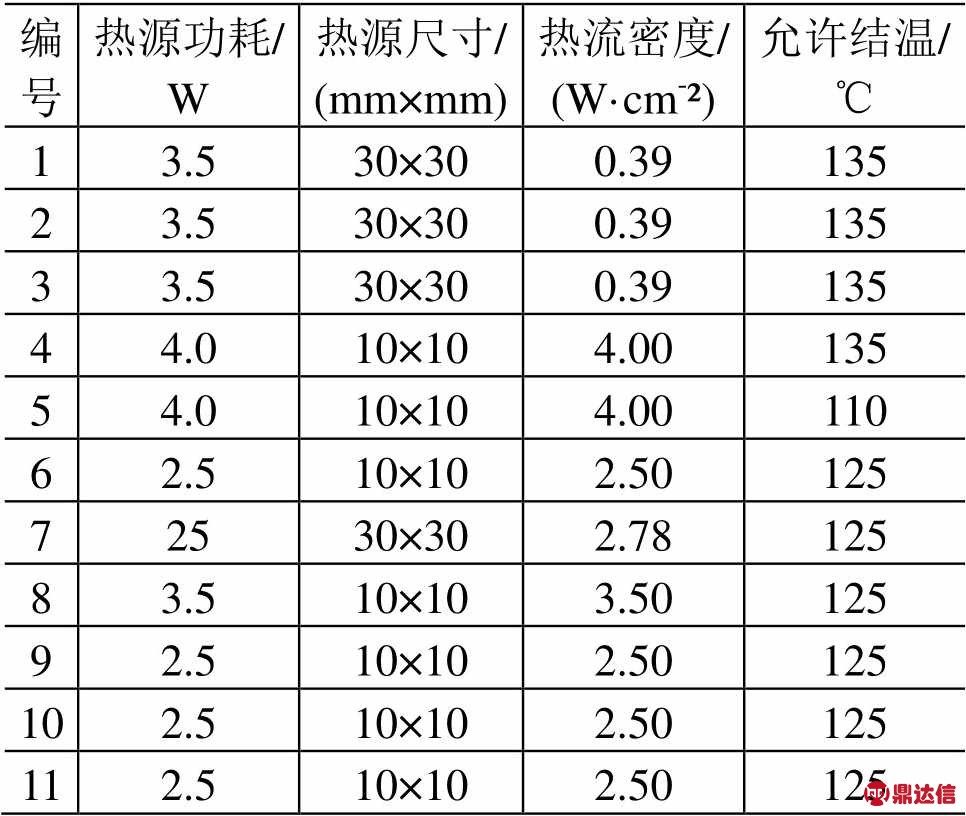
2 热控方法
2.1 相变材料选择
由于平台无法提供主动散热条件,但工作时间不长,所以一般都采用热沉散热。相较于金属热沉,PCM热沉重量轻,同时其巨大的相变潜热使其储热性能非常优越,因而被广泛应用于缺乏主动散热条件的电子设备瞬态热控领域。然而PCM热沉导热性能较差,通常需要采用高导热骨架材料或金属隔筋来增强其综合导热性能。本方案针对环境条件及热控要求,采用膨胀石墨骨架/85#高碳醇复合PCM,其相变潜热高,导热性能好,同时膨胀石墨具有良好吸附性能,能有效降低液体流动和泄漏风险。表2是85#高碳醇与膨胀石墨不同封装率下的热物性参数。
表2 85#高碳醇与膨胀石墨不同封装率下PCM热物性参数
Table 2 Thermal parameters of PCM with different encapsulation efficiency of 85# higher alcohol and expanded graphite

2.2 相变散热数学模型
本次仿真采用Mentor Graphics公司开发的针对电子设备内热流流动和散热的工程热分析软件FloEFD,其采用有限体积法对芯片级到系统级三维散热问题进行计算和分析。针对热流流动和散热问题,将复合PCM等效成均匀材料,假设其相变前后密度保持不变,则其控制方程(包括连续性方程、动量方程和能量方程)为:
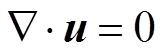
; (2)
。 (3)
式中:为矢量微分算子;ρ、μ、cp、k分别表示材料热物性参数中的密度、动力黏度、比热容和热导率;P、T、S分别表示压力、温度和源项。
针对固-液型复合PCM,文献[3,8-10]主要介绍并对比了界面追踪结合VOF方法、焓-多孔介质法和等效比热法3种建模方法,结论显示,前2种方法模型复杂且消耗资源极大,而等效比热法消耗较低资源的同时计算精度能够满足工程需求,故以上文献均最终采用等效比热法进行仿真分析。
等效比热法是将PCM的相变潜热等效成比热容。对于理想PCM,相变发生在特定温度点,其对应比热容为无限大值,而实际上相变发生在一个温度区间内,这就使得在这个温度范围内的等效比热容为有限值。等效比热法数学表达式为
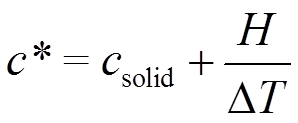
式中:c*为等效比热容;csolid为固态时PCM的比热容;H为PCM的相变潜热;ΔT为相变温度范围。
本文采用的PCM为封装率85%的膨胀石墨基85#高碳醇(相变峰值点85℃),利用差示扫描量热方法(DSC)得到其相变特性,其相变温度范围为76~87℃,等效比热容可表示为分段函数:

将上述等效热导率、等效比热容和密度导入FloEFD工程数据库,为进一步计算做准备。
2.3 物性参数及边界条件
假设初始和环境温度为70 ℃,只能提供局部空气自然对流条件,模块腔体材料采用铝合金5A06,芯片与热沉间采用热导率为1.5W/(m·K)、厚度为0.5mm的导热绝缘垫进行非稳态计算。
3 仿真分析与讨论
针对以上初始和边界条件,分别采用复合PCM热沉和铝热沉进行散热仿真对比。
3.1 温度云图
图3为31min后的热沉模块和芯片温度云图,可以看出,铝热沉对应温度明显高于PCM热沉,说明铝热沉的热容能力显著小于PCM热沉,而铝热沉的导热性能显著优于PCM热沉,温度均匀性更好。
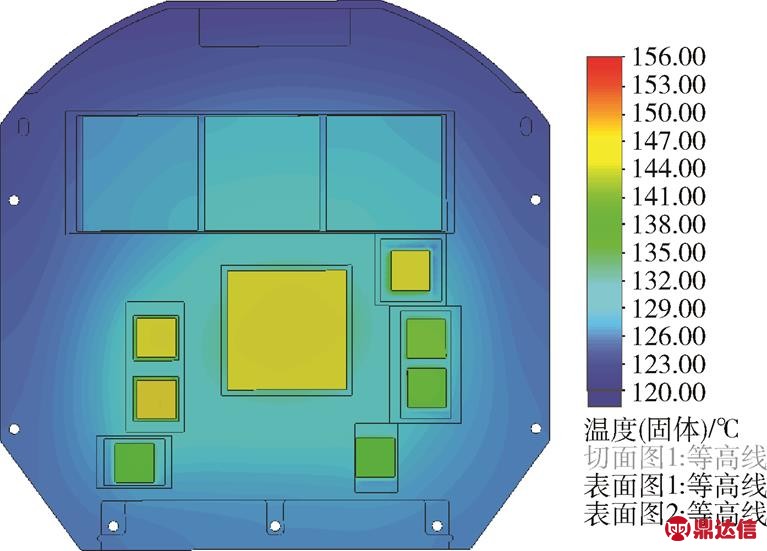
(a) PCM
(b)铝
图3 PCM热沉和铝热沉温度云图
Fig.3 Temperature distribution of PCM and Al heat sink
3.2 温度变化趋势
图4为铝热沉和PCM热沉在31min内的温度变化曲线。可以看出:在最开始的4min内(黑色分隔线左侧区域),由于铝热沉材料更均匀、导热系数更高,使得其散热性能优于PCM热沉,从而芯片温度更低,在这一工作时间内,铝热沉性能更优;4min后,铝热沉对应芯片的温升速率几乎保持不变,而PCM热沉内开始发生相变,吸收大量的热量,导致对应芯片温升曲线趋于平缓,温度显著低于铝热沉;20min后,PCM已经全部融化,相变潜热用尽,对应芯片温升速率又高于铝热沉,但计算结束,芯片温度仍低于铝热沉工况,充分说明了PCM热沉的总体散热性能优于铝热沉。
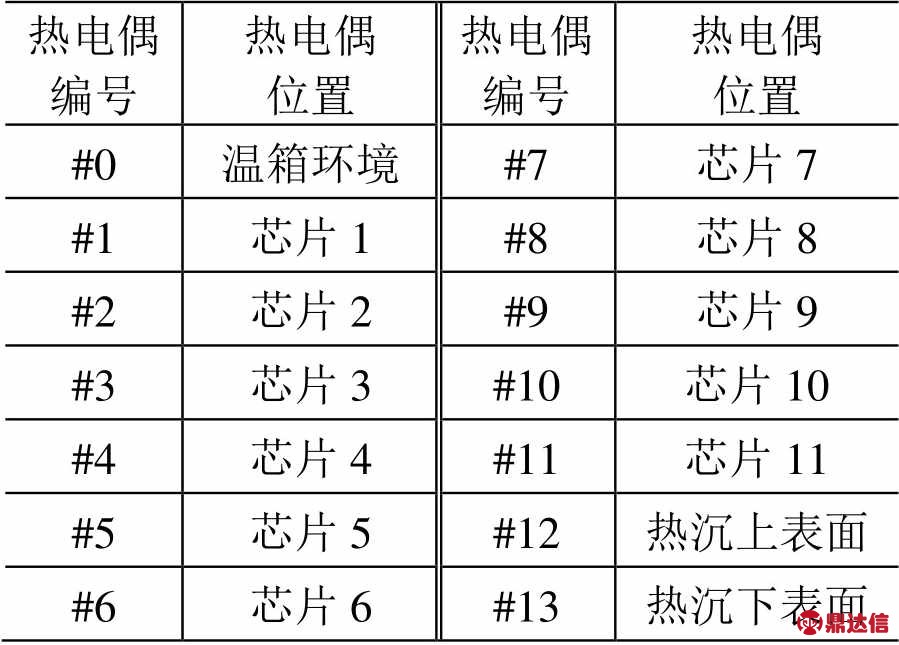
图4 PCM热沉与铝热沉温度变化曲线比较
Fig.4 Comparison of temperature tendency between PCM and Al heat sink
对于常用芯片而言,其最高允许结温约125℃,从图4中可以看出,在此温度范围内PCM热沉可使用时间约为铝热沉的2倍,重量却仅约为铝热沉的1/3,对平台而言,具有极大利用价值。
4 实验验证
4.1 实验方案
为验证PCM热沉的散热特性,并与仿真结果进行比较,用陶瓷模拟热源代替真实功率器件,通过导热绝缘垫将模拟热源紧贴热沉,在对应监测位置贴上OMEGA的T型热电偶(见表3)后采用高温胶带进行压紧和隔热处理,热电偶测温精度为0.5℃。将实验件放入70℃温箱进行保温和加电测试,采用NI数据采集仪实时记录监测点温度,如图5所示。
表3 热电偶编号和对应位置
Table 3 Thermal couple number and corresponding position
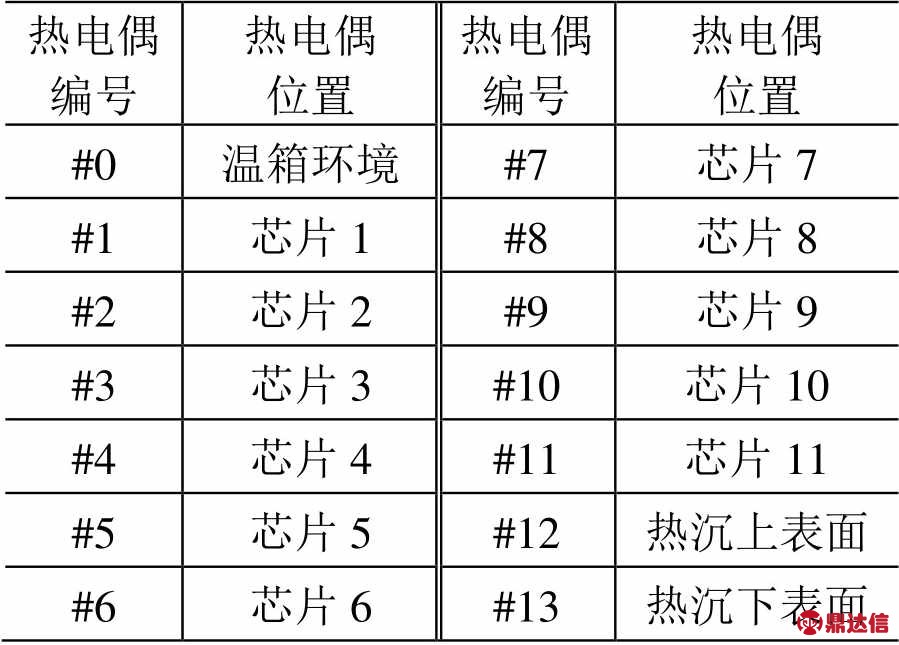
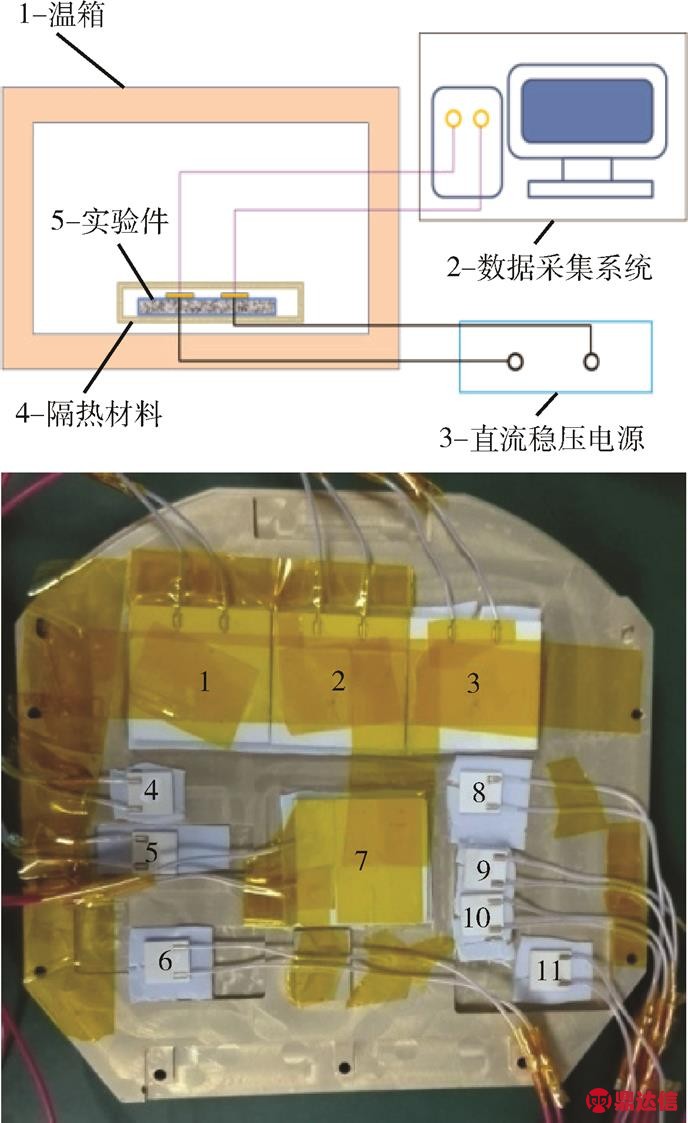
图5 实验系统及热沉样件
Fig.5 Experiment system and heat the sink sample
4.2 实验结果
实验结果如图6所示,整个散热过程仍可以分为相变前温升段、相变温升段和相变后温升段3段,相变温升段温升速率显著低于其他2段。
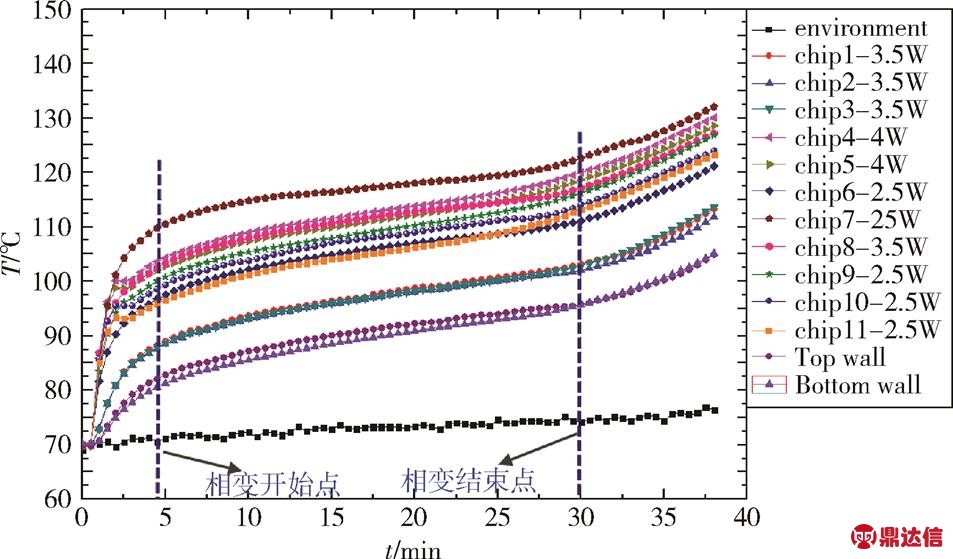
图6 实验芯片温度变化曲线
Fig.6 Chip temperature tendency during experiment
除去热沉上下表面和环境温度,温度曲线可分为3组:第1组为Chip7,由于其功率高,初始温升速率最快,并迅速领先其他芯片达到最高;第2组为Chip1、Chip2和Chip3,由于其热流密度最低,温升速率最慢,温度最低;其他芯片为第3组,由于芯片热耗相近,故曲线比较集中,但趋势仍是功率(热流密度)更高的芯片温度更高。以大部分工业芯片最高结温125℃为限,使用PCM热沉芯片可持续工作大于30min,满足平台的短时工作需求。
4.3 实验与仿真对比
图7(a)~(d)为实验和仿真结果对比。
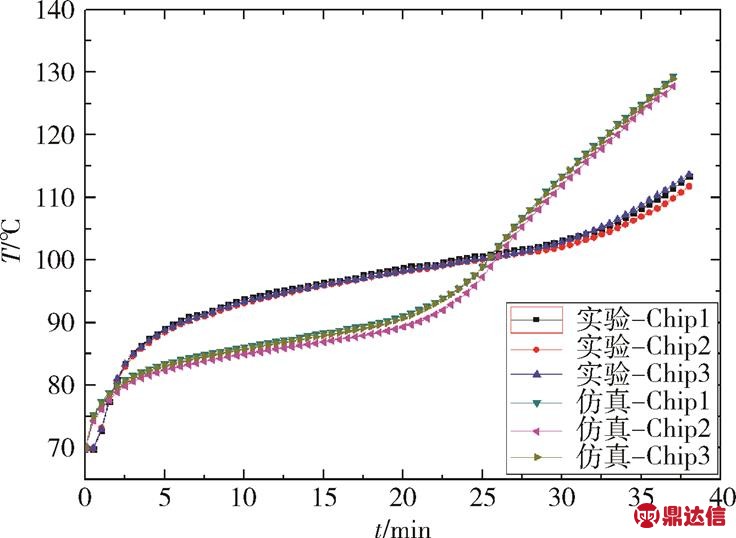
(a)
(b)

(c)
(d)
图7 实验与仿真结果对比
Fig.7 Comparison of simulation and experimental result
可以看出,实验曲线和仿真曲线温度变化趋势一致,均分为明显的3段,但在不同时间段温升速率有较大差异,从而出现了分化:25min之前,实验得到芯片温度低于仿真结果,而之后出现相反的趋势。经分析,这是由于实验采用的PCM发生相变更晚,同时实验过程中存在导热绝缘垫压紧力不足而产生更大接触热阻等干扰因素,导致前半段温度高于仿真结果;相反,仿真中PCM相变完成时间早于实验PCM,从而导致相变后温升段提前,温度迅速上升并超过实验结果。
对比结果表明,膨胀石墨基复合PCM实际相变温度范围与仿真模型有差异,其原因可能包括:1)仿真模型采用等效比热法无法反映多孔介质内部工质流动和传热的复杂机理,且等效法未完全覆盖真实温变范围,因而方法本身存在一定误差;2)PCM实际存在一定程度非均匀性,使得DSC测得的样品参数具有局限性;3)测温点少,无法反映热沉平均温度水平。为提高仿真准确度,后续需要改进仿真方法,并得到更准确的材料属性参数。
5 结束语
本文使用FloEFD软件对膨胀石墨基复合PCM热沉和铝热沉散热性能进行了仿真对比,并进行了PCM相变热沉的同工况温箱实验,证明了PCM热沉在无主动散热平台中的应用优势。在后续的研究工作中需要针对具体温控对象,合理选择相变材料并准确测试材料热物性参数,同时改进仿真方法,充分考虑材料的非均匀性和不同工作条件下多孔石墨骨架内工质相变过程中的对流效应,并尽量减小与实际工况边界条件的不一致性,提高仿真精度和准确性,以加强对工程设计和应用的指导性。