[摘 要] 山东某电解铝企业400 kA电解槽采取适当加高阳极炭块的方法降低阳极毛耗,该厂一系列23万t产能所用的阳极炭块高度均由原来的595 mm提高到620 mm后,换极周期由30 d调整为32 d,阳极毛耗降低了4.2 kg/t-Al,节约成本总计约174万元,为企业带来较大的经济效益。
[关键词] 电解铝; 阳极高度; 电解槽; 换极周期; 经济效益
1 概述
2013年工业和信息化部发布了《铝行业规范条件》,其中对新建和现有铝电解企业的有关物料消耗提出了要求:新建和改造的电解铝系统,炭阳极净耗应低于410 kg/t-Al;现有电解铝企业,炭阳极净耗应低于420 kg/t-Al。对此,各电解铝企业从改进阳极结构降低阳极消耗入手,开展降低成本的工作。尽管国内外不少学者和机构在进行这方面的研究,但大多集中在理论计算上,缺少实践案例与成本分析。
阳极组主要由铝导杆、钢爪和炭块3部分构成,其中铝导杆和钢爪通过铝-钢爆炸焊片连接,钢爪和炭阳极通过磷生铁浇铸黏接[1]。国内外针对阳极组结构节能降耗的研究见表1。
近年来,国内各大铝厂无论在前期设计还是设备的后期改造,均有对阳极尺寸做过优化,以降低阳极单耗。表2为国内部分铝厂400 kA电解槽使用的预焙阳极现状。
从表2可以看出,大部分铝厂阳极高度大于600 mm,最高达650 mm。对于阳极高度的设计,各设计院结论不尽相同,但主流仍是以增加阳极高度为设计原则。部分设计院曾计算过,阳极理论高度可达到1 m以上。对于电价低廉的地区,增加阳极高度非常有效。另外,劳动力成本上升,人员流动性大,造成换极的各项损失增加,尤其对于低电压,这种影响会更大。
阳极炭块的高度决定着换极周期、阳极毛耗、阳极本体电压降、阳极散热与保温、劳动强度等。理论上,当残极高度不变时,阳极毛耗随阳极高度的增加而降低,换极周期随阳极高度增加而延长[2]。所以,在充分考虑压降、操作和经济成本的基础上,研究探讨预焙阳极炭块高度对铝电解过程中阳极单耗的影响具有一定的实际意义。
某公司结合400 kA电解槽系列和炭素生产线的实际,通过采取适当加高阳极的方法以期降低阳极毛耗、降低生产成本及减轻员工的劳动强度,减少换极对电解槽的扰动。另外,该公司原换极周期为30.6 d,阳极加高后换极周期达32 d,是倒班天数(8 d)的整数倍,可实现定时定区换极。
2 阳极使用周期计算
阳极使用周期是指预焙阳极在铝电解槽中的使用时间。计算公式及推导过程如下[3]:
单块阳极使用周期:
表1 国内外对阳极组结构的研究内容及方法
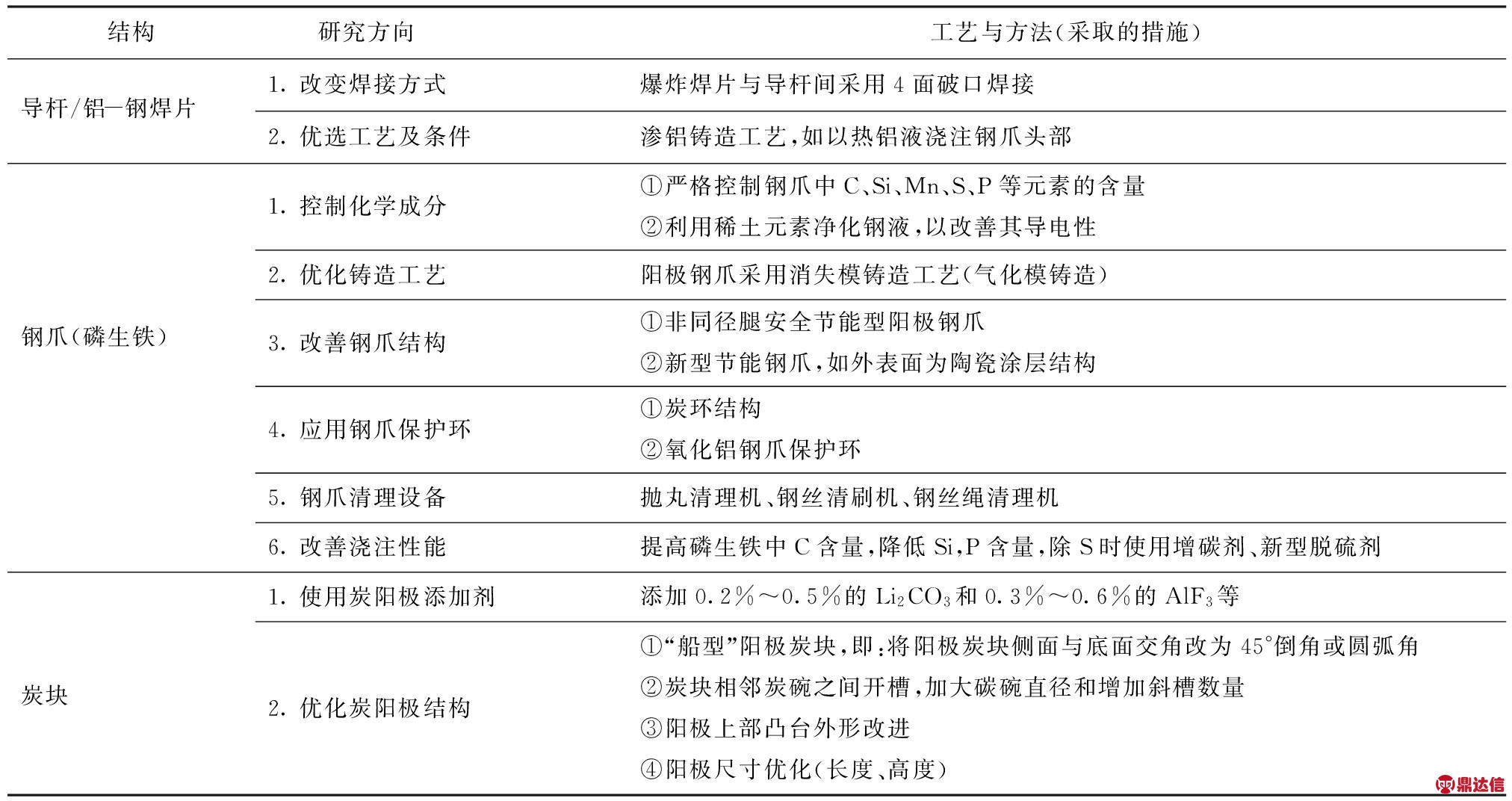
表2 国内大型预焙槽阳极尺寸
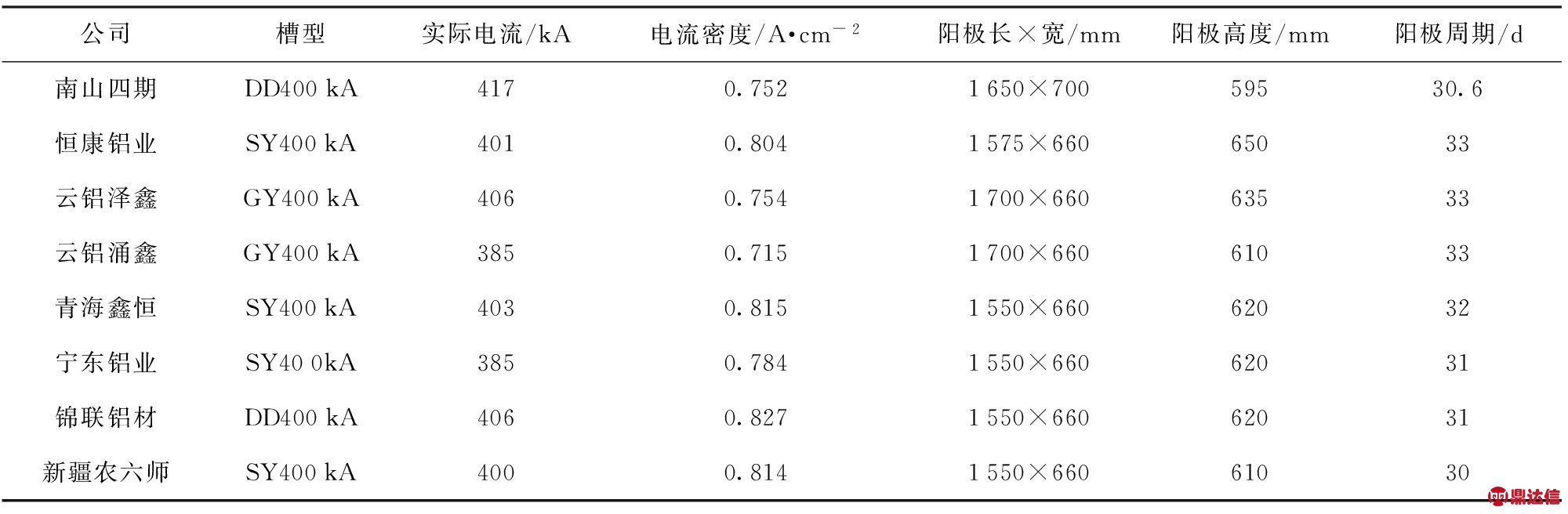
Tz=(HA-H残)/HC
(1)
式中:Tz——单块阳极使用周期,d; HA——阳极高度,cm; H残——残极高度,cm; HC——阳极消耗速度,cm/d。
阳极消耗速率:
3.2.1 阳极的电能消耗
(2)
式中:Hc——阳极消耗速度,cm/d; I——阳极电流密度,A/cm2; η——铝电解电流效率,%; C净——阳极净消耗,kg/t·Al; d——阳极体积密度,g/cm3。
把(2)式代回(1)式得:

(3)
某公司400 kA电解槽,实际电流效率91.1%。若将目前的换极周期由30.6 d延长到32 d,则可通过公式计算出阳极高度。表3中为计算阳极周期的原始数据。
通过计算可知,若该电解车间换极周期延长至32 d,则应将阳极加高到620±5 mm较为经济合理。
3 经济效益分析
与原预焙阳极生产相比,阳极高度增加后,在整
表3 阳极使用周期计算的原始数据及公式
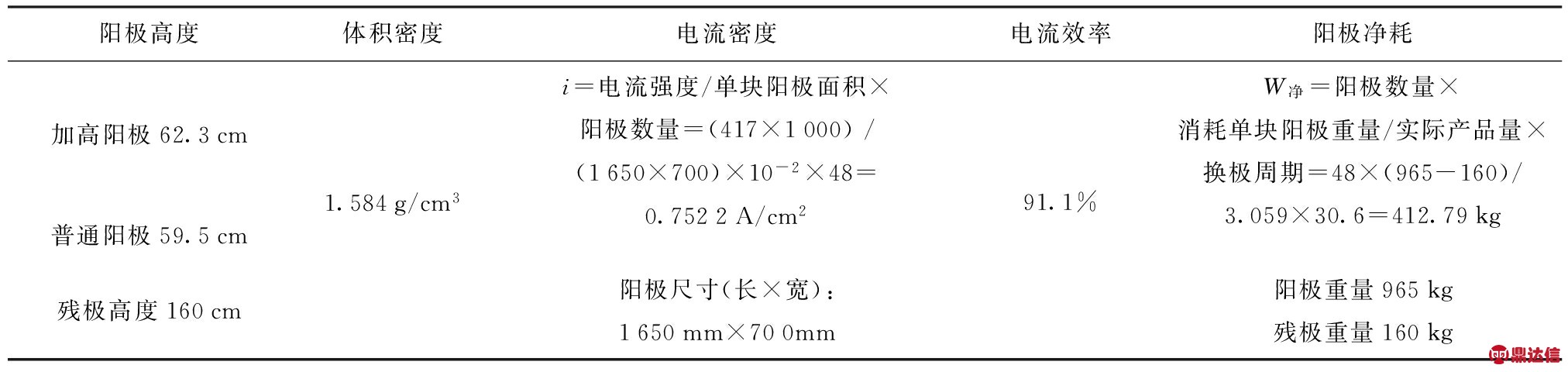
体电解器产量不变的情况下,减少了阳极炭块生产数量,焙烧和阳极组装工序成本大幅下降,降低了电耗,减少了换极操作对电解槽的扰动。
3.1 阳极生产成本
Hc=8.054 ×I×η×C净×d-1 ×10-3
3.1.1.1 阳极炭块数量
假设该电解厂一个系列产铝量为a万t,阳极毛耗为b(t/t-Al)(熟块),则需生产阳极ab万t,加高前后阳极的重量分别是H0(t)和H1(t),阳极加高后少产炭块为:
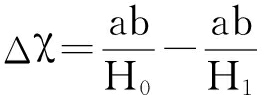
(4)
2015年该厂平均阳极毛耗为501.79 kg/t-Al,按照一个系列23万t产能计算, 加高前后阳极重量分别是965 kg和1 015 kg,则实际少产炭块:
890块
按每块平均重965 kg,则少生产的炭块量为:
890×965/1 000=5 683.85 t
若每天消耗的量不变,阳极使用周期延长,由于残极率减小,则毛耗b下降,那么实际生产中减少阳极量应多于5 890块(2 945组)。
3.1.1.2 阳极毛耗
加高阳极的换极周期为32 d,单块重量1 015 kg,炭块使用量48×1 015=48.720 t。32 d出铝量为:
32×0.3356×417×24×0.911=97.912 t
炭耗为:
48.720/97.912=497.59 kg/t-Al
降低炭耗:
501.79-497.59=4.2 kg/t-Al
3.1.2 天然气消耗
该电解厂配套的炭素生产系统,焙烧车间2015年天然气平均单耗76.19 m3/t-C,天然气单价约2.67元/m3,则每吨炭阳极消耗天然气的费用为204.10元。若采用加高阳极,按全年可少生产5 890块炭块,其重量为5 683.85 t,节约的天燃气价值:
D1=5 683.85×204.10=1 160 073.79元
3.1.3 焙烧车间耗电量
焙烧车间主要用电设备的功率及每天运行时间为:多功能天车(325.15 kW,17.5 h),堆垛天车(114.25 kW,19 h),编解机(169.5 kW,17.5 h),碳碗清理机(30 kW,12 h)。按上述设备各一台每天正常运行工作,则1 d的耗电量为:
Q=P多功能天车×t1+P堆垛天车×t2+P编辑组电机×
t3+P碳碗清理机×t4=
325.15×17.5+114.25×19+169.5×17.5+30×12=6 118.25 kW·h
工作1 d所产生的电费为:
6 118.25×0.43=2 630.84元
按焙烧车间每月产量20 000 t计,即每天产量约666.67 t,则全年少生产5 683.85 t炭块节省的时间为:
5 683.85÷666.67=8.5 d
每年节省的焙烧电费为:
D2=8.5×2 630.84=17 542.64元
3.1.4 减少磷生铁的用量
组装阳极时,在中频炉熔铁和浇铸过程均存在铸造烧损[4]。该炭素厂阳极组装烧损约为5 kg/t-C(熔铸损失率按5‰计算),5 683.85 t阳极生铁补充量约为:
5‰×5 683.85=28.42 t
按照目前钢铁市场价格2 100元/t,则每年可节省生铁成本约:
D3=28.42×2 100=59 680.43元
3.1.5 减少中频炉电耗
由于阳极加高后将减少磷生铁用量,因此中频炉的工作时间也会缩短,由此电耗将减少。根据四炭素厂阳极组装的生产实际,一炉次熔化的磷生铁水可浇注20组阳极,若全年少生产2 945组阳极,则少熔化147炉次磷生铁。按照1台中频炉(额定功率800 kW)正常工作,熔化均匀需要2 h,则147炉全部熔化消耗的电量为:
800×2×147=235 200 kW·h
当前电价为0.43元/kWh,则共节省的费用为:
D4=235 200×0.43=101 136元
3.1.6 残极清理费用
目前残极采用人工清理,清理费用为每组17元,少生产2 945组阳极,则每年可节省的残极清理费用为:
D5=2 945×17=50 065元
3.1.7 阳极组其他用电
阳极组车间旋链系统、导杆校直、压脱设备等一系列设备运转需要大量电能,若少生产5 683.85 t,除去公共用电,其所节省电能约占整个阳极组车间电能的1/3(经验值),所以可根据该车间电耗对此进行估算。
阳极组车间平均月产19 344 t阳极,每吨耗电35.40元,则总耗电:
19 344×35.40=684 777.6元
按加高阳极生产占阳极组用电量的1/3,则节省电费为:
D6=1/3×5 683.85×35.40=67 069.4元
综上,根据实际生产情况及相关近似计算,炭素生产加高阳极节省的费用可分为上述6个部分,总计:
D1+D2+D3+D4+D5+D6=1 455 567.26元
3.2 电解生产成本计算
3.1.1 阳极炭块的数量及炭块毛耗
炭块压降的计算公式[5]:
V炭=ρ炭dh
(4)
式中:ρ为热态炭块电阻率,900~1 000 ℃时约为55 μΩ·m(热态时比冷态时偏低);d为阳极理论电流密度,电流417 kA时,为0.752 2 A/cm2;h为阳极组平均高度。
其中,h1=h新-h钢爪深度;h2=h残极-h钢爪深度;h=(h1+h2)/2+h残,通过公式(4)即可计算出V炭为184 mV。
VΔh=V炭×Δh/h新(Δh为新极增加高度),进而计算加高后阳极压降增加8.54 mV。但是实际中阳极加高后,将保持设定电压不变,主要是阳极自身放热,几乎不影响电解槽热量平衡,即使影响也非常小。换句话说8.54 mV将转化为消化极距。理论上每1 cm极距电压为330 mV,那么增加阳极高度后,其将消化0.02 cm极距。若能量保持平衡,稳定性好,极距大于4.5 cm时,0.02 cm对电效几乎不构成影响。但如果极距小于4.5 cm,或者电解槽偏冷,则0.02 cm会有一定的影响,但影响也很有限。
3.2.2 换极电能消耗及损失
换极对电解槽影响较大,如果没有换极,电解槽物料平衡和热平衡波动会非常小。目前,该厂换极后经常出现电压波动,电解槽稳定性较差。换极的电能消耗和电效损失如下:
(1)换极附加电压最小电能消耗
W换极=0.43(电价,元)×2 945(阳极组数)×417(电流,kA)×100(附加电压量,mV)×1(附加电压时间,h)/1 000=52 806.80元
(2)针摆最小电能消耗
W针摆=0.43(电价,元)×2 945(阳极组数)×417(电流,kA)×30(附加电压量,mV)×1(针摆最小时间,h)/1 000=15 842.04元
(3)针摆期间铝的最小损失
2015年该厂槽日产量为3.079 t,则每小时产铝量为128.3 kg。若针摆1 h,电流效率损失2%,则针摆期间铝量损失为3 kg。更换2 945组阳极,铝价为12 000元/t时,其铝的损失为:
W铝损失=2 945×0.003×12 000=106 020元
(4)多功能天车消耗
设多功能天车换极全过程(包括换极前后的相关工作)平均功率为150 kW,换极时间30 min,则每换一组天车耗电75 kW/h,更换2 945组阳极的电费为(此项不包括天车自身维护保养):
W天车=2 945×75×0.43=94 976.25元
综上,采用加高阳极在电解生产中,特别是换极过程中节省的费用总计:
∑W电解成本=W换极+W针摆+W铝损失+W天车=
52 806.80+1 584.04+106 020+94 976.25=
269 645.09元
3.3 阳极运输费用
若一年少生产5 890块(2 945组)阳极,则阳极组装车费用及往返运输费用将大大减少。该厂运输阳极组有四辆阳极拖车和两辆叉车同时作业,叉车将成品阳极叉入到大箱车内,大箱车将成品阳极运送到各电解车间。
运输车每次运2组阳极,2 945组阳极减少运输1 472次。阳极拖车、叉车每天(平均)共用柴油448.38 L,每天四个车间运输阳极总数为:
Q=84×4=336块
运回的残极总数也为336块(往返运输)。运输每块极耗油为:
C=448.38/(336+336)=0.67 L
每块极所需的运费为(目前柴油单价4.182 5元/L):
Z1=0.67×4.182 5=2.81元
一年内所产生的运输费用为:
Z总=5 890×2.81=16 550.9元
综上,该厂400 kA电解槽采用加高阳极可产生的直接经济效益来自三个部分,炭素生产成本、电解成本及运输成本,总计1 455 567.26+269 645.09+16 650.9=1 741 763.25元。
4 结论
(1)采用加高阳极具有重要意义。从电解生产的角度看,阳极保持适当高度,可减少电解槽扰动,降低工作量,保持平稳生产;从经济效益考虑,加高阳极可节省生产成本及运行费用,通过估算每年约174万元。
(2)理论计算表明,该电解厂400 kA电解槽若将目前的换极周期调整为32 d,炭块高度应为620.02 mm。如能将阳极高度由现行值增高到最佳值,将可取得明显的经济效益。